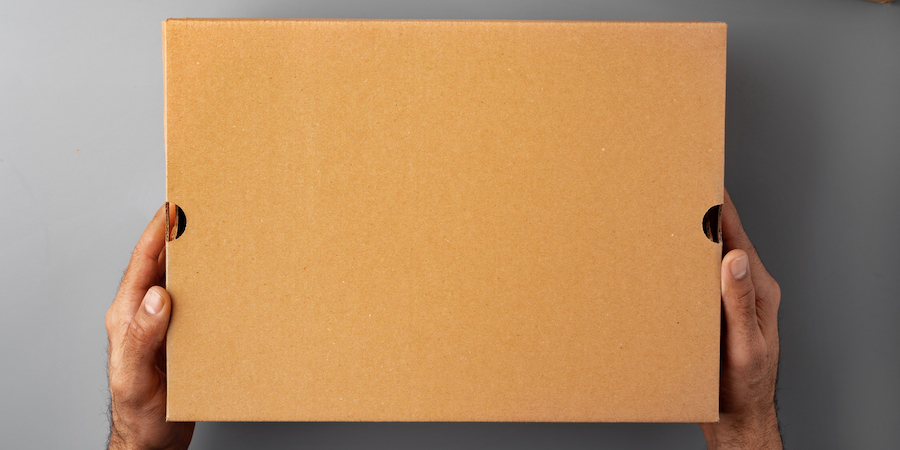
Don’t just watch my hands!
FEATURE – The author shares a story from a training session at the gemba, which contains a couple of important lessons on the Training Within Industry method.
Words: Csaba Barhács, Lean Coach, Lean Institute Hungary
Background
During a recent TWI training practice at one of our partners, one of the employees was given the task of creating a job breakdown sheet for the process of taking samples from the production line for quality control purposes. Boxes on the line move at a speed of 500 units per minute. This makes the job of collecting samples challenging even for an experienced worker, let alone a new employee.
When creating a TWI job breakdown sheet, three main elements need to be considered and defined:
1. Major steps - What do we do?
2. Key points - How do we do it?
3. Explanations - Why do we do it?
What's the problem?
When the first version of the job breakdown sheet was completed, I noticed it included definitions such as “with one hand”, “from above”, or “with a quick motion” among the key points.
Since the training of a new employee was also underway, I asked how he was doing with the job breakdown sheet and with the task itself. I was told, “The new employee is not really getting the hang of it yet, but that's something that requires a lot of practice.”
So, I asked the worker to show me the process and try to teach me how to perform it, too. I must admit that, throughout the learning process, my heart was pounding: it was so stressful to intervene in a line moving at full speed and try to take out one of the 500 boxes passing through every minute. I tried multiple times, but always failed. At one point, I even had to stop the line because I knocked over a few boxes.
Observations
After numerous failures, I asked the colleague to show me how once again it’s done. I tried to observe as many details as possible. Initially, I only focused on their hand, trying to pick up that critical motion that would ensure success. However, I didn't see any significant difference from my own practice.
I then noticed where they were looking, and that was the moment I understood the key to the process. The focus of the worker's gaze was about one meter ahead of the extraction point. They looked at an incoming box, followed it with their eyes until the extraction point, and then, with the appropriate hand motion, grabbed the box.
Experiments and the solution
I asked if what I saw was correct, that they were looking at the box before taking it out. They confirmed this with enthusiastic nods, seeming not to understand why I asked such a basic question. It was clear to them! After that, I tried the same practice: eye contact, tracking, and extraction. Miraculously, it worked flawlessly for me as well.
At the end of the practice, we agreed that the work breakdown sheet needed to be supplemented with one additional step and its corresponding key point:
Selecting the box (what) - Approximately 1 meter from the extraction point, choose the box and visually track it to the extraction point (how).
With these additions, the key points related to grasping the box were now working perfectly.
Conclusion
This short story provided both me and the operator with two valuable lessons:
1. Often, experienced workers overlook trivial details in their work, and we tend to superficially examine a process.
2. In addition to hand motions, it's worth observing head and eye movements, as well as movements of the feet, torso, and shoulders, which can also be crucial (e.g., stepping sideways, turning, etc).
THE AUTHOR
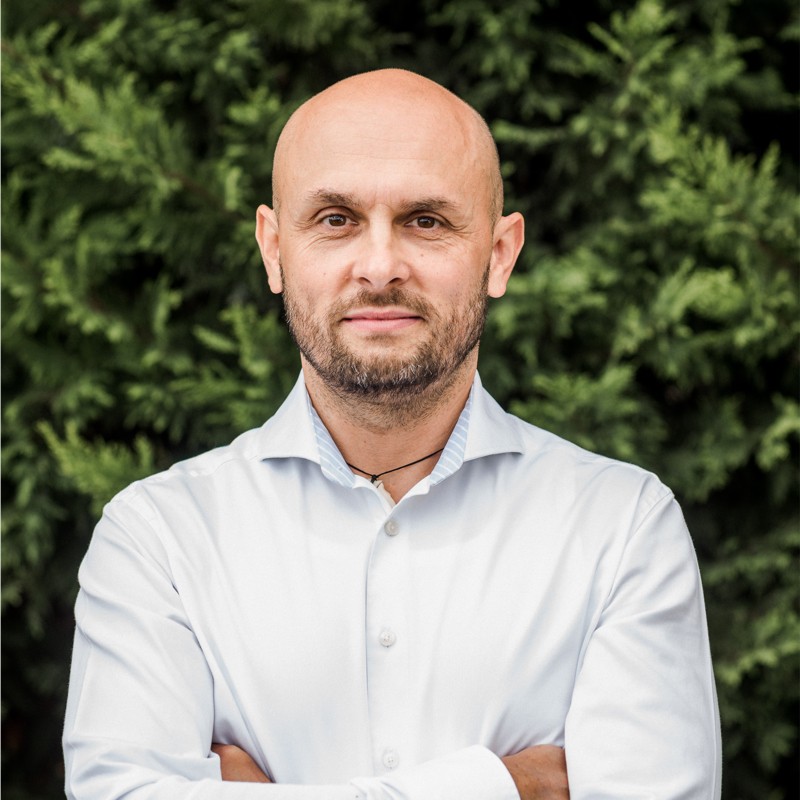
Read more
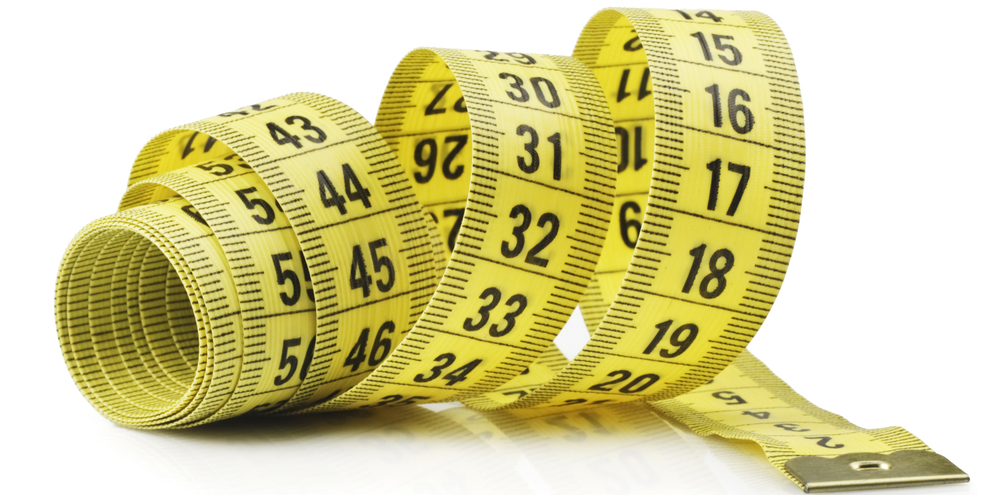
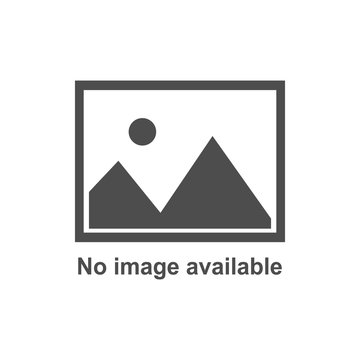
FEATURE – Pure and simple management by indicators can be a trap leading us to make decisions that are inconsistent with the real needs of a company. The balance between facts and data is key.
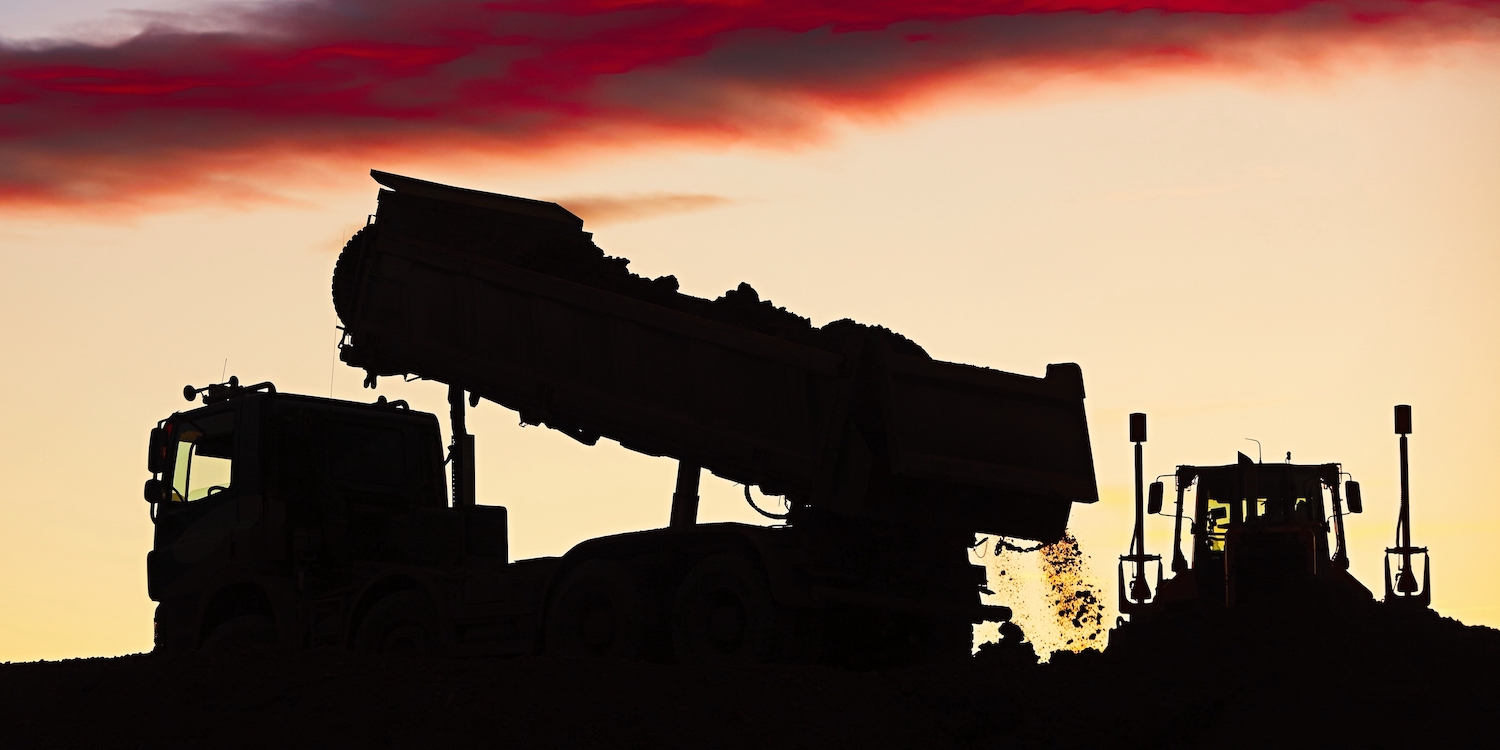
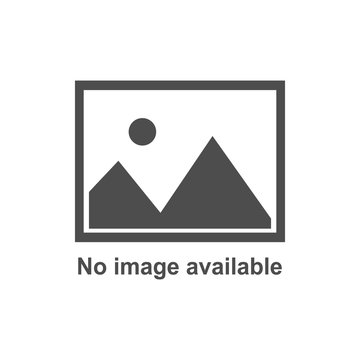
INTERVIEW – Drawing on 33 years of experience working in product development at Caterpillar, the interviewee reflects on lean in engineering.
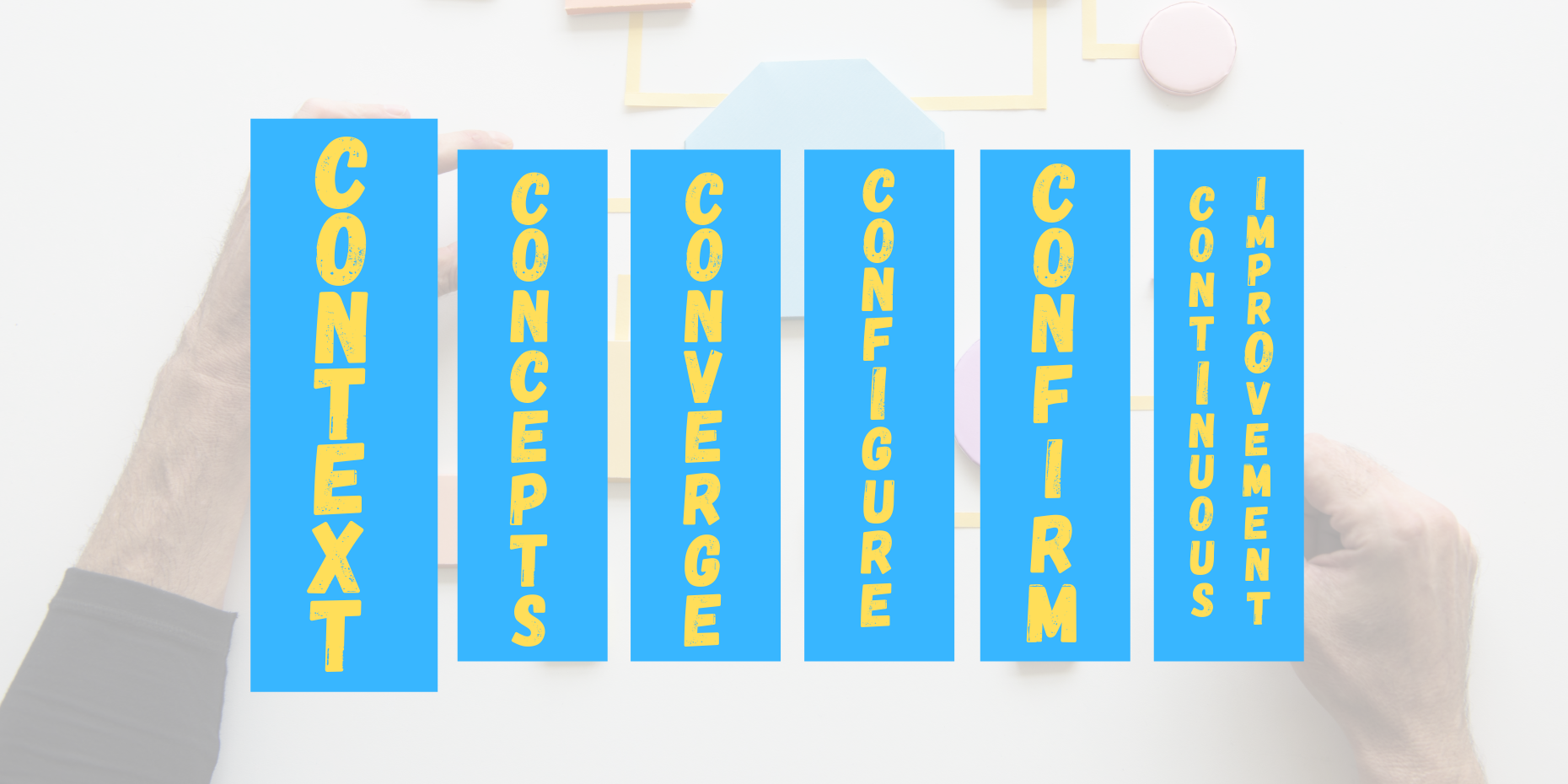
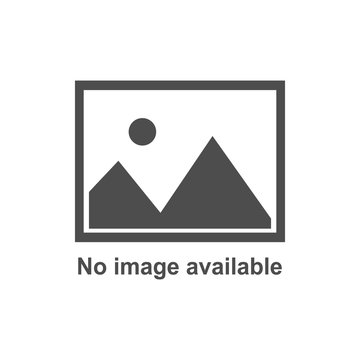
SERIES – The authors discuss the first of six elements in their process development model – Context – highlighting the importance of gaining clarity on the objectives of the process being created.
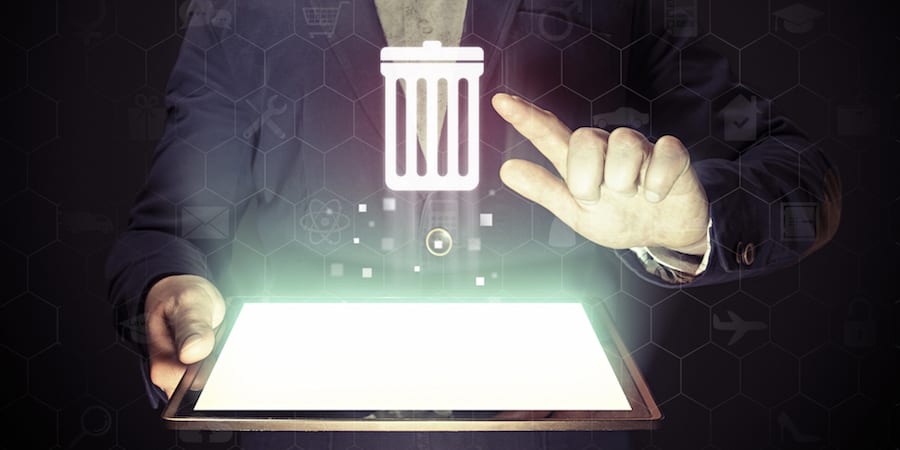
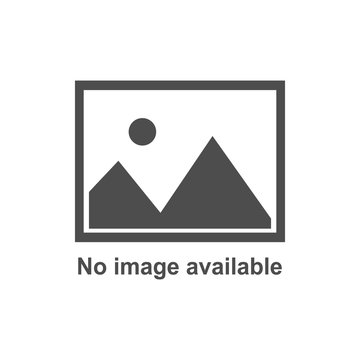
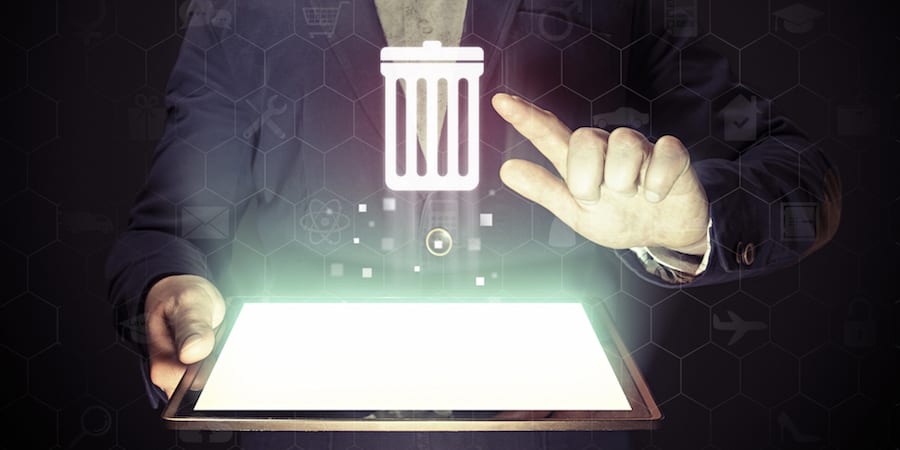
FEATURE – Not many people know that digital technology and the IT industry are rife with environmental waste. Discovering it and eliminating early can have beneficial effects on both the business world and the planet.
Read more
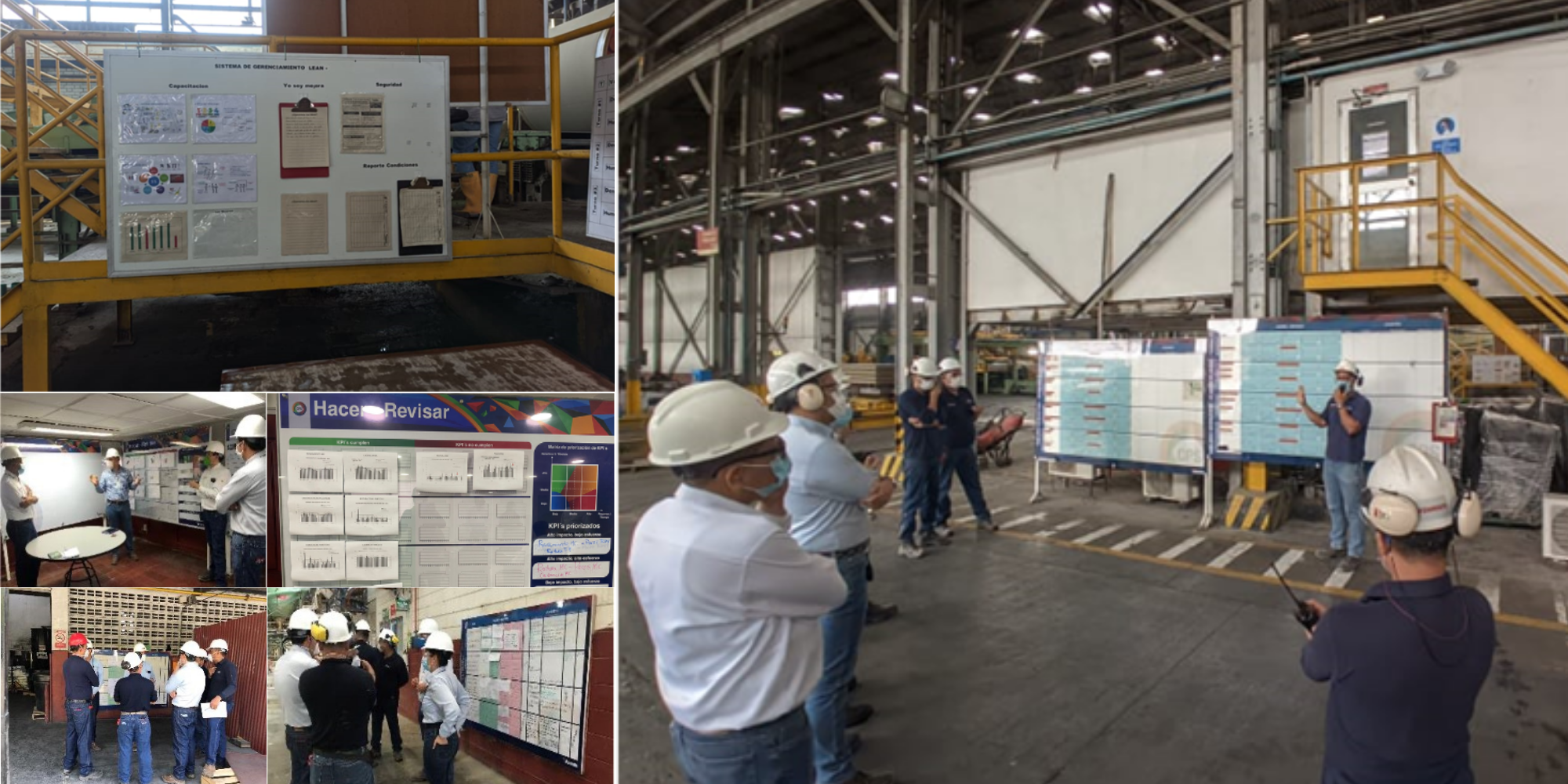
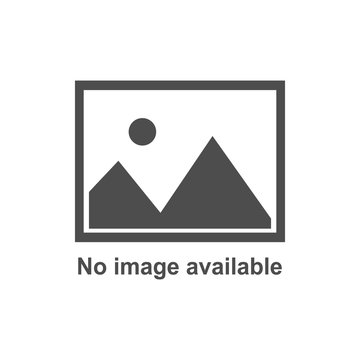
CASE STUDY – For the past year, Elementia Materiales, a producer of materials for the construction industry, has begun a lean journey that’s already brought impressive quality results.
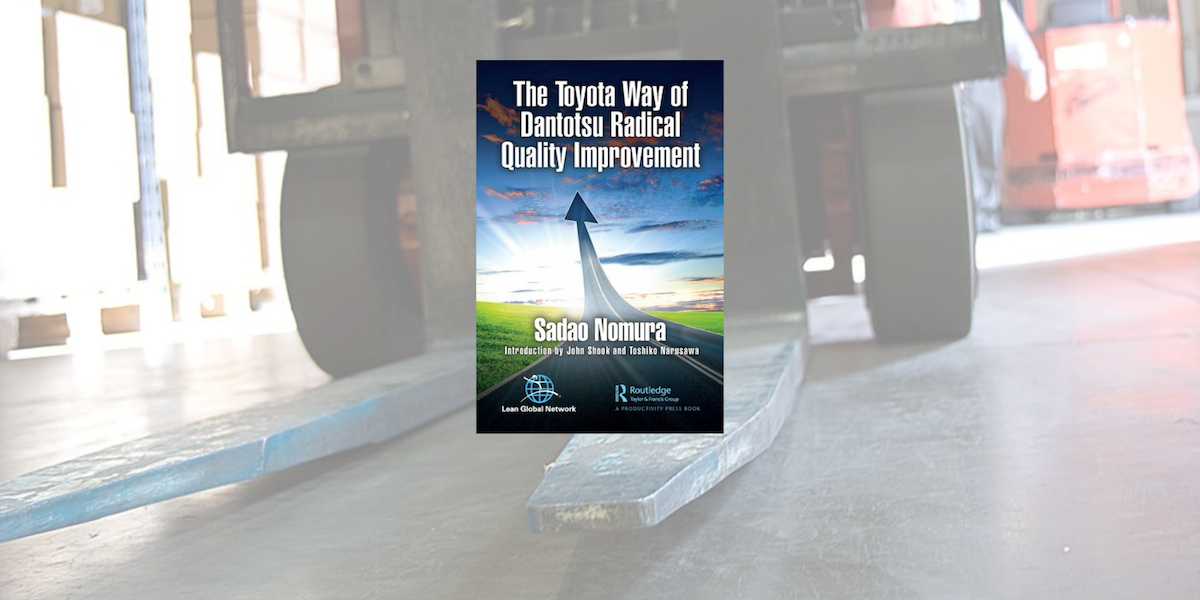
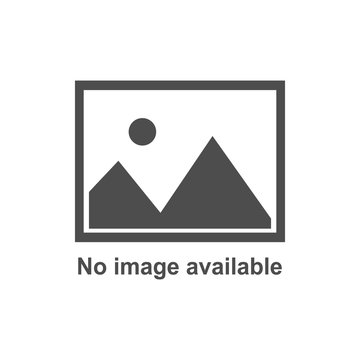
FEATURE – The authors discuss radical quality improvement at Toyota and introduce a new book by Sadao Nomura that the Lean Global Network has just co-published.
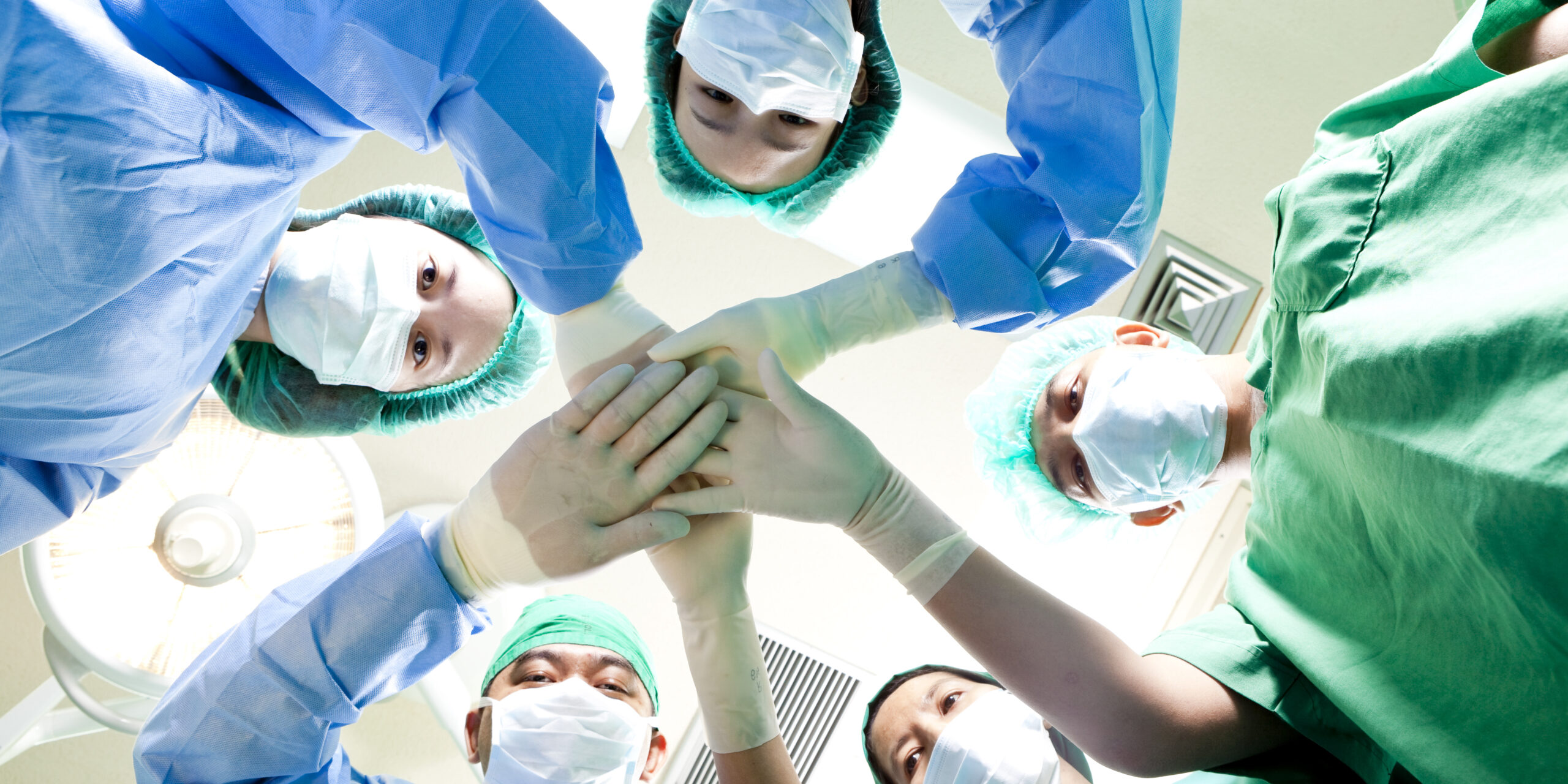
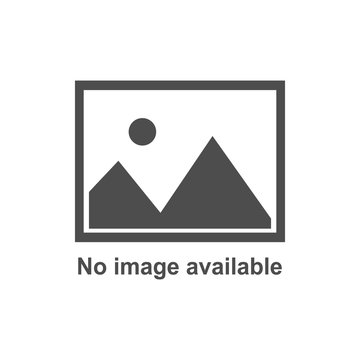
FEATURE – To facilitate the transition to a new organization of the work in their department, a group of nurses at Erasmus Medical Center have been using Training Within Industry.
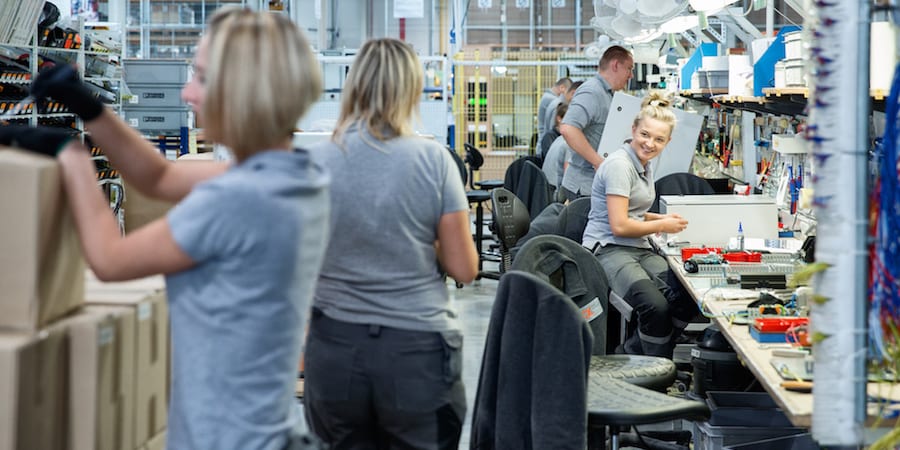
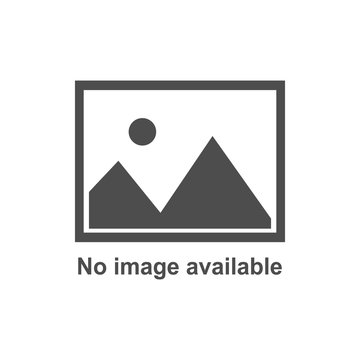
FEATURE – When you are hiring 20-30 people in a week, getting them up to speed with the company’s way of working becomes critical. But how to do it effectively? A Polish factory found the answer in TWI.