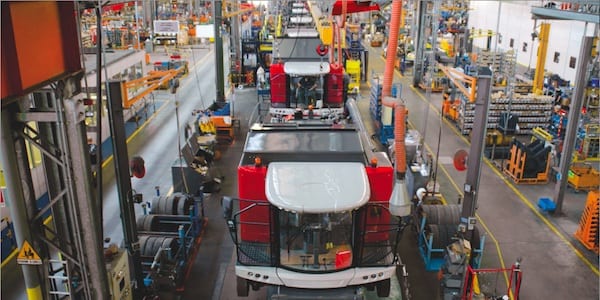
The lean journey of a manufacturer of combine harvesters
CASE STUDY - An approach based on Lean Daily Management System and experiments in a model area led an Italian manufacturer of combine-harvesters to become one of the leanest organizations in the Veneto region.
Words: Roberto Priolo, Managing Editor, Planet Lean
It’s just after 5am, and Laverda’s combine-harvester production facility is warming up in preparation for another day. Along the line, an operator reaches his working station, but right before starting his shift he notices that his machine won’t start.
He immediately tells his Coordinator, who wishfully thinks that the reason for a machine not starting is sometimes very simple. After having checked all the possible causes for the breakage, he concludes he is not able to fix the problem himself, and decides to call maintenance. But the intervention of the maintenance team, however prompt, is not enough to restart the faulty piece of equipment.
At this stage, when everything has been tried, there is nothing else to do but bringing the problem to the attention of the Team Leader at the 7.30 meeting, during which the Coordinator explains what the issue is and what has been done to try to solve it.
The issue is analyzed again, as the Team Leaders of maintenance and production continue the discussion, until a new countermeasure is identified.
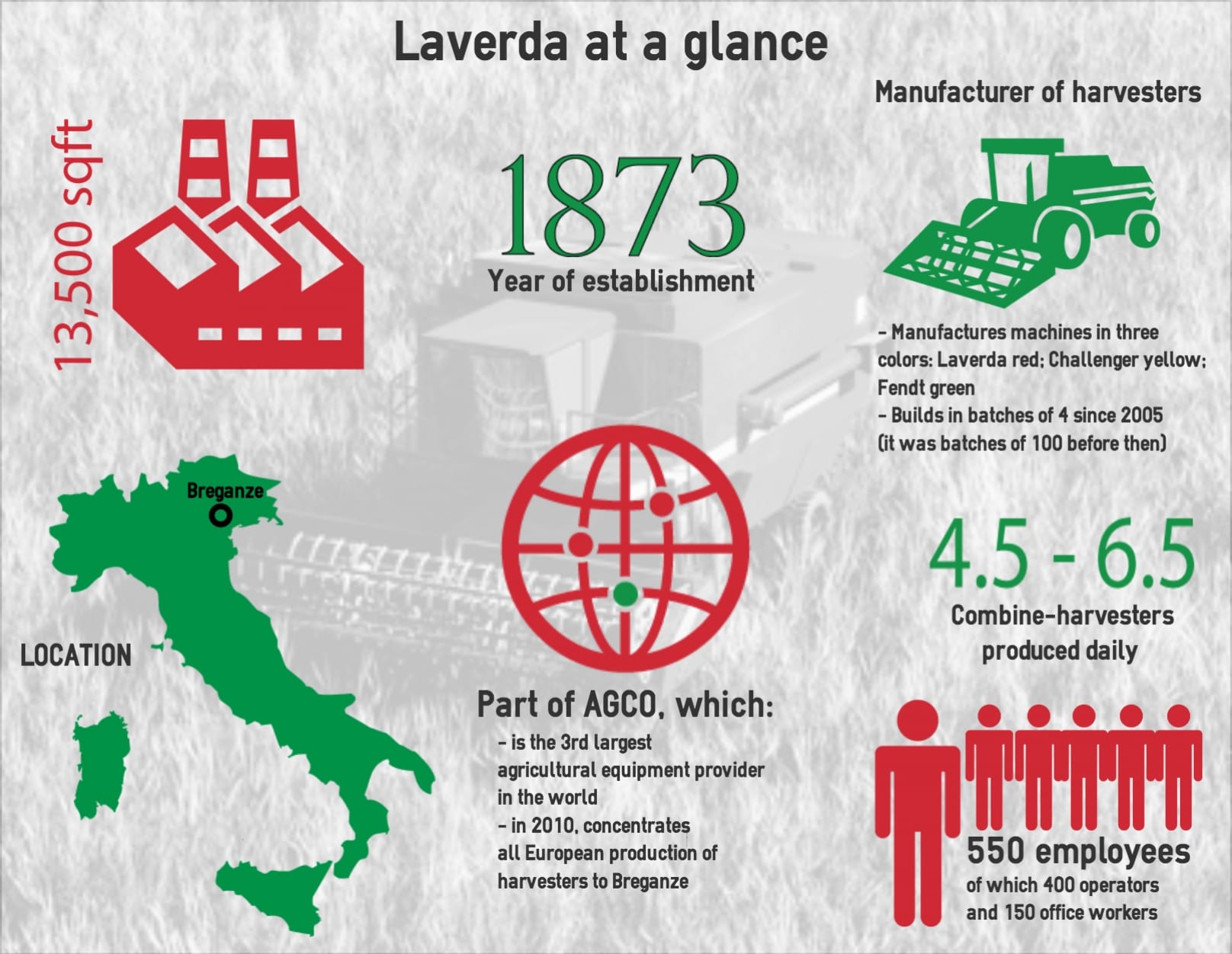
The team leader calls the electrician, but he can’t solve the problem either.
More reflection follows and the problem is then brought to the attention of the Area Manager at the following meeting (it’s now 8.30am). The Team Leader explains all that was done trying to address the problem and, based on his input and suggestions, the Manager decides to call the supplier and to order a new part.
During his meeting with the Operations Director (which happens daily, between 9 and 9.30am, at the end of the combine-harvester production line), the Area Manager says that there is a machine that is not working, that the root cause has been identified (a faulty part), that a new part has been ordered and that the problem is being dealt with.
This system of tiered meetings is one of the elements of Lean Daily Management System, the first technique Laverda implements whenever it starts to expand its improvement efforts to a new area or process. Today, LDMS is in place throughout the Breganze facility, including some of the offices.
Mirandola, APS Manager at the plant, says: “The idea is that nobody knows a machine better than the operator working with it, and that same person will be best placed to know how to solve a problem the machine experiences. That’s why problems are talked out at the gemba. Root cause analysis has to happen closer to where the action is, which makes operators responsible for their work. It’s not about knowing the solution, but understanding the problem.”
LDMS allows us to manage the flow of information within the organization in a standard way.
THE HISTORY
Just over 140 years ago, Pietro Laverda set up a workshop in San Giorgio di Perlena, a small village in Italy’s Veneto region, manufacturing farming equipment and wine machinery to support the local agricultural firms.
Mr Laverda couldn’t have imagined that a few decades later his small business, which moved to nearby Breganze in 1905, would produce the first Italian self-propelled combine-harvester and that a century and a half down the line it would become part of one of the largest agricultural equipment providers in the world.
As it’s often the case with successful organizations, good results come from two important elements: innovative products and forward-looking leadership that knows what the customer wants. Laverda has benefited from both these aspects.
Mr Laverda was not just a fine mechanic, but also a businessman who was well aware of the importance of understanding customer needs: as early as 1890 he published a product catalogue, something of a pioneering marketing move.
After Mr Laverda’s death, his nephews, Pietro Jr and Giovanni Battista, inherited the business and, it seems, their grandfather’s entrepreneurial spirit. This marked the beginning of a phase characterized by innovation and extraordinary technological breakthroughs that made Laverda a major organization in Italy’s agricultural industry.
In 1934 and 1938 respectively, Laverda produced the first Italian drawn mower and the first Italian reaper-binder. In 1956, the M60 was launched, the first Italian-made self-propelled combine-harvester. With this machine Laverda started its expansion in the Italian market and abroad (similar machines had been present in other countries for decades, but Italian agriculture did not start its modernization process until after World War II).
The organization developed a compact, light, and easy to handle machine that perfectly suited the needs of the customers, agricultural businesses working on small lots. The product was an instant success, and forced Laverda to invest in a production line and in a metal sheet working department.
The M60, the first self-propelled combine, in 1956 and the M100 AL, the first self-leveling combine, in 1971 determined the expansion of Laverda into the Italian market and beyond.
The company’s successful evolution, which made it an attractive partner for FIAT for two decades starting in 1981 and for Argo Tractors, which relaunched the Laverda brand starting in the year 2000, culminated in the acquisition, in 2011, of Laverda by one of the largest agricultural equipment manufacturing groups in the world, US-based AGCO Corporation.
THE JOURNEY
Laverda’s lean journey started in 2005, with the decision to revolutionize the production line, moving from batches of 100 combines, all of the same model and color, to batches of four.
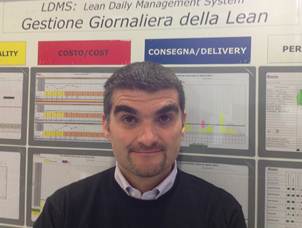
The lean transformation picked up pace after agricultural machine and equipment manufacturer AGCO acquired Laverda and moved all European combine manufacturing operations to Breganze, making this plant as its centre of excellence for this business area in the EMEA markets. The facility faced increased complexity, which translated into further need for change: production soon started to switch colors between batches. It even managed to bring the setup time down to zero.
Marco Mirandola says: “We needed to become more flexible and eliminate defects and downtime in the face of increased complexity coming from an extra family of products moving to our plant. Moving to smaller batches and bringing setup time to zero represented big obstacles, as did kanban cards and other tools at first.”
AGCO’s contribution to Laverda’s journey also meant that more consistency was brought to the application of lean. Laverda is a seasonal business, producing in the first part of the year and selling until August. Production volumes drop September to December, and that is when the majority of the lean efforts, like kaizen weeks, took place.
AGCO introduced the APS (AGCO Production System) and established the APS Office, with two full-time individuals - rigorously coming from within the business - tasked with implementing continuous improvement year-round.
Mirandola is one of them (he previously worked in production), and there is somebody like him in every AGCO plant around the world.
BENCHMARKING FACILITIES
Plants are regularly assessed by the Lean Learning Center, which uses a checklist based on WCM. The score resulting from the assessment allows each facility to benchmark itself against others within AGCO and understand where in the five levels of the APS it is.
The Breganze plant aims to move to Level 3 in the next two years, which means concentrating on lean leadership and lean office activities.
Mirandola explains: “It’s important to know where we are to understand where we are going. All plants are required to reach Level 3 by the end of 2015, and Breganze is one of the highest scoring ones, despite having started the APS implementation in 2011.”
Moving to Level 3 reflects the move from a mere understanding of processes and tools to the more cultural aspects of a lean transformation.
DAILY MANAGEMENT IS KEY
To embed lean principles in employees’ DNA, Laverda puts a lot of effort into capability development.
Learning to dig up the root cause goes through learning how to solve problems, and that’s what education at Laverda is organized around. The aim of the company is to fundamentally change the mindset of people, which is too often focused on the solution, rather than the problem.
Accountability is one of the greatest benefits that Laverda has gained since it started to use LDMS, but certainly not the only one: the speed at which information flows across the organization has proved to be one of the most critical factors supporting the process of transformation.
Mirandola shares another example: “We recently identified the need to encourage people to wear their safety glasses. One evening last month, the Facility Safety Manager met with all the team leaders for 10 minutes and emphasized how important safety glasses are for us. The following morning at 9 o’clock, the information had already reached everybody on the floor via the team leaders. It’s incredible how fast information travels.”
But there’s more. LDMS also allows for the gathering of very high-quality and useful data that will increase the visibility over the state of things in the plant. An operator will know whether machines are being produced to schedule and to the right specifications, or whether production targets are being met thanks to visual boards (one of the fundamental elements of LDMS) that are updated constantly.
There are six pillars on which LDMS is based: Safety, Costs, Deliveries, Quality, People, and Continuous Improvement. According to Mirandola, the first five pillars capture the current state of the plant, while the sixth (continuous improvement) is the one that sets the vision for what the future might look like, sharing the different ideas for improvement coming from operators.
“The best part of the boards is that print-outs are extremely rare. People hand-write these sheets and go back to them all the time. They are quite weathered pieces of paper – you wouldn’t be able to use them in a presentation, but their value is great,” explains Mirandola.
Laverda has decided to establish a rule by which the Coordinator (who is a figure between the operator and the team leader) changes every week or two, to give as many people as possible the opportunity to self-develop.
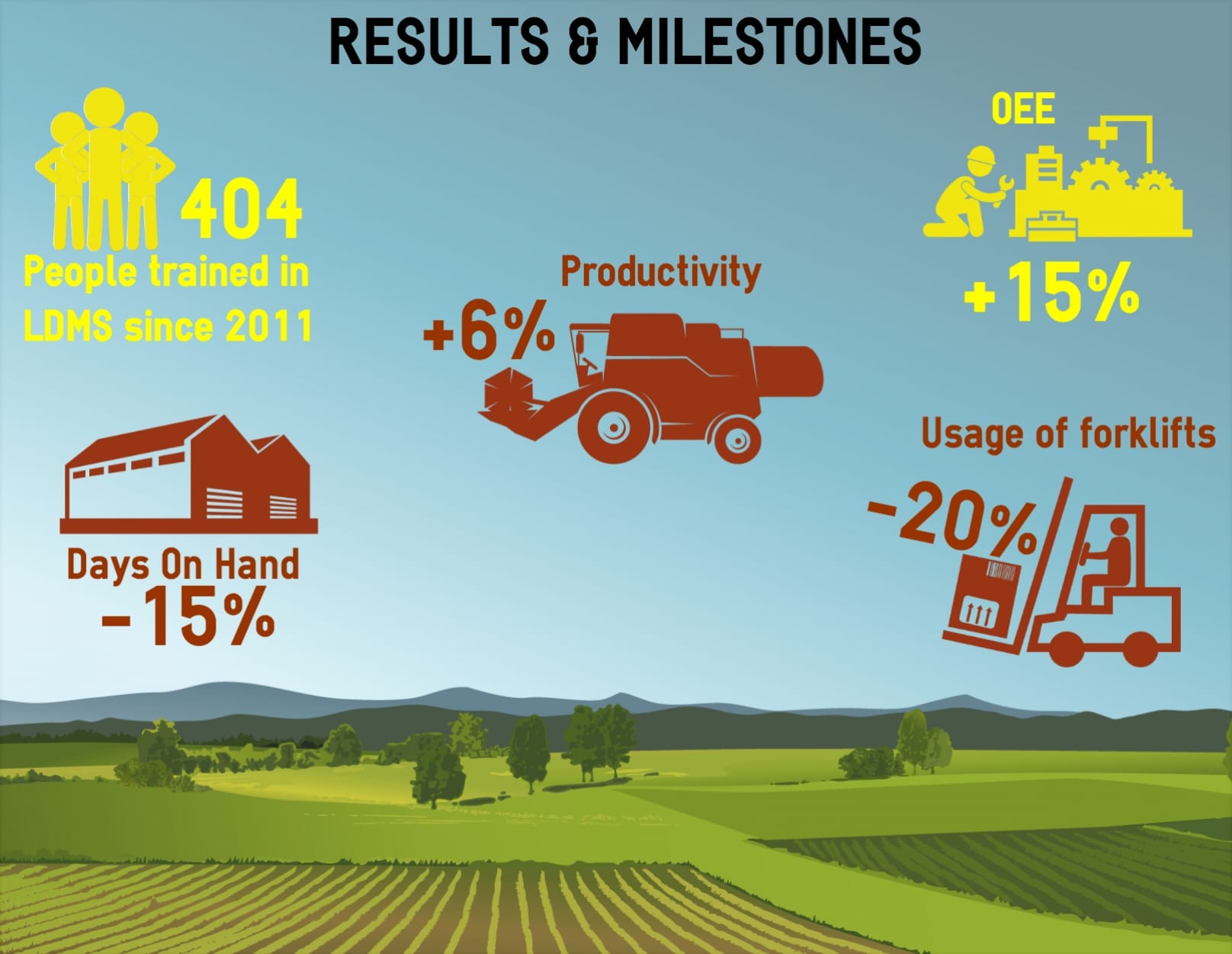
“If you have a KPI you need to comment on in front of your colleagues, you need to know that KPI inside out,” says Mirandola. “Education at Laverda happens in the classroom for only an hour; the rest is all at the gemba, to test and improve the operators’ knowledge of KPIs. If you know them, you can manage them. And that learning happens by working on paper, reflecting, amending, reflecting some more, and so on.”
Another way to develop people and increase quality is to invest in skills (there is only so much that can be automated in the manufacture of combine-harvesters). Laverda does so by means of the 3x3 system: there must be three operators able to perform each activity and each operator must know how to perform three activities.
When asked how LDMS changed his working day, one operator at the Breganze plant said: “My day has changed radically. Now there is time, every day, for us to discuss the problems we are going to face and to solve them, whenever possible, in a standard way. And we talk about safety and potential risks.”
A MODEL TO BEGIN WITH
Material flow is critical for the company, as only 30% of components are produced internally. In order to improve it (and therefore improve flexibility in production), Laverda implemented the plan for every part (PFEP) method in a pilot area, which had all the main characteristics present in the plant.
Once the problems were understood in the pilot area in January last year (half-empty containers; a lot of materials present by the line; production areas not optimized; excessive handling in the receiving area; and supermarket layout unsuitable for picking activities), the project was expanded to two more areas in the plant.
Following re-layout and rebalancing and the implementation of PFEP, Laverda will extend the reach of its lean program to the supply chain.
Mirandola says: “We like to call our suppliers ‘partners’. Not only do we visit them, but we often have them over here. We try to involve them in our activities, from milk runs to PFEP. They must be aligned if we are to succeed in our undertaking to become a lean organization.”
Read more
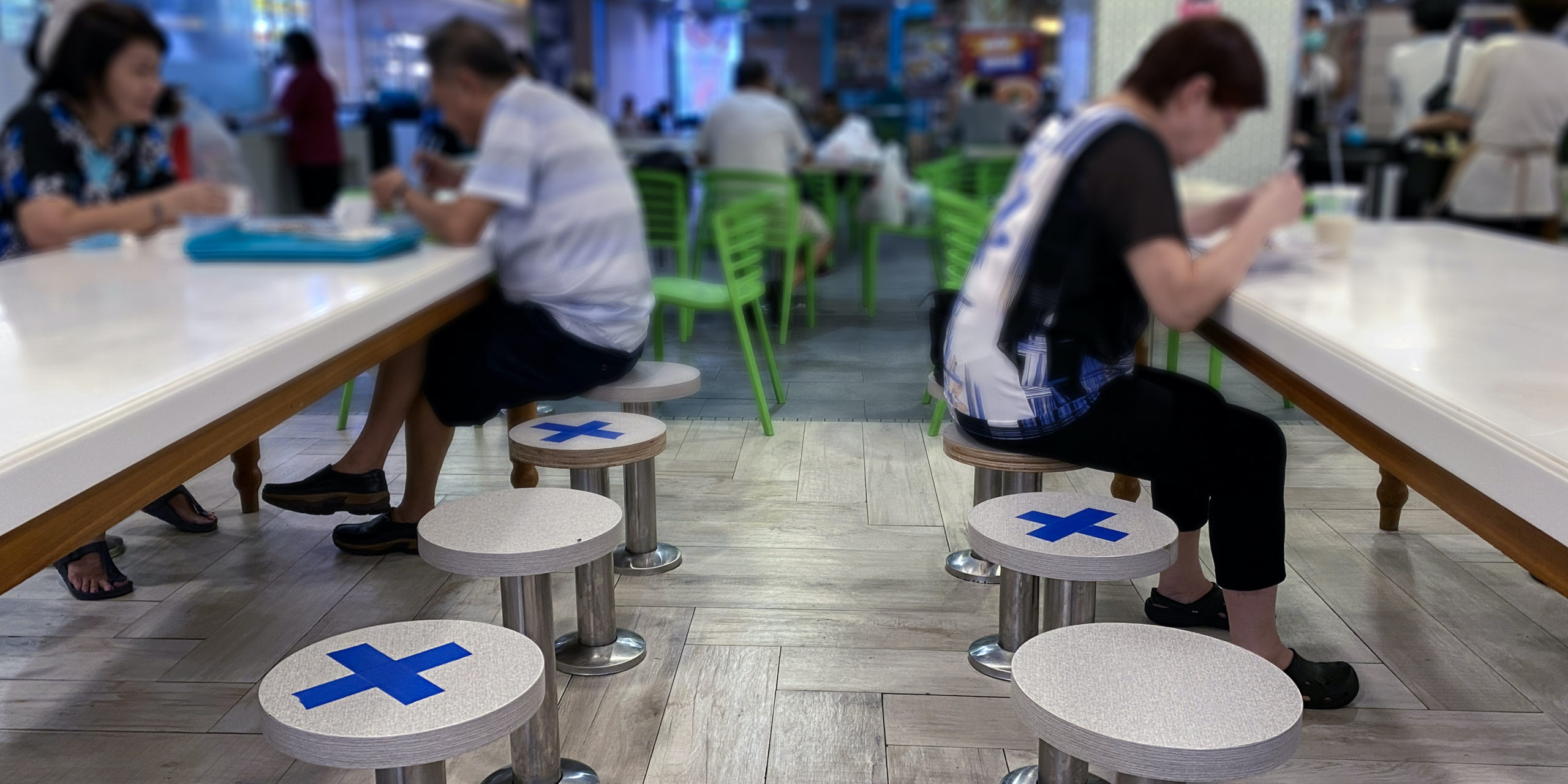
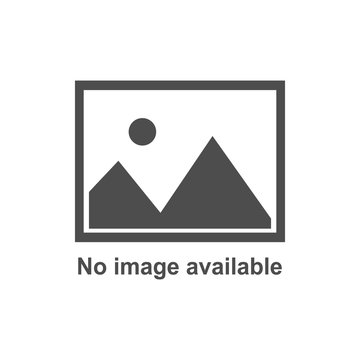
FEATURE – The future has never looked more uncertain for restaurants and cafes. The authors share a set of practical lean tips that can guide these organizations navigate the storm.
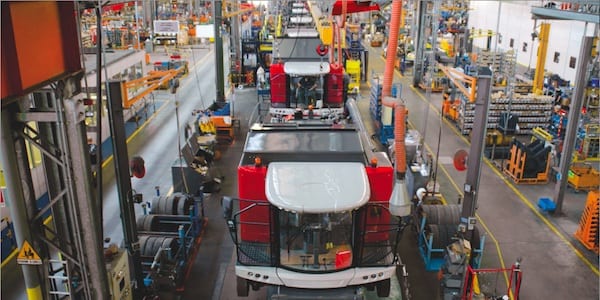
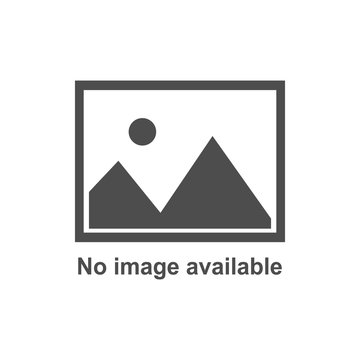
CASE STUDY - An approach based on Lean Daily Management System and experiments in a model area led an Italian manufacturer of combine-harvesters to become one of the leanest organizations in the Veneto region.
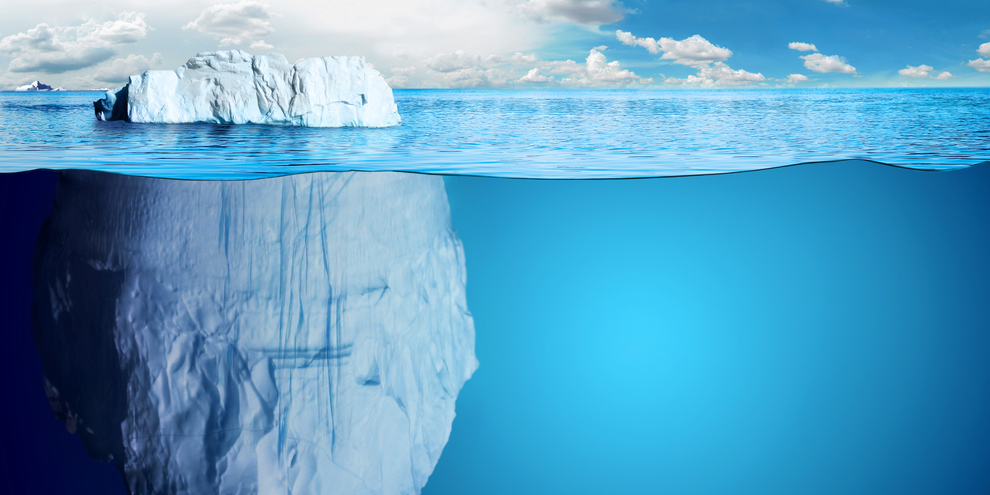
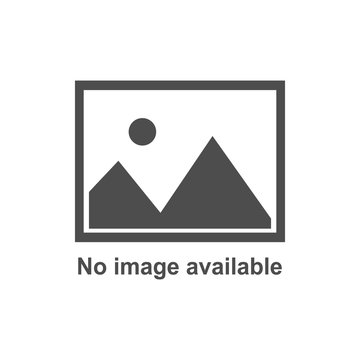
FEATURE – A real understanding of Lean Thinking can only stem from an exploration of its tacit aspects, not just its most explicit, easy-to-grasp elements.
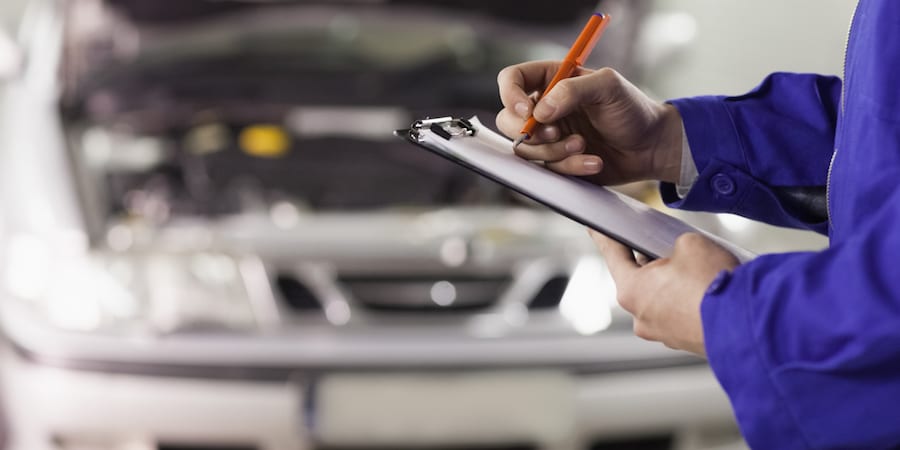
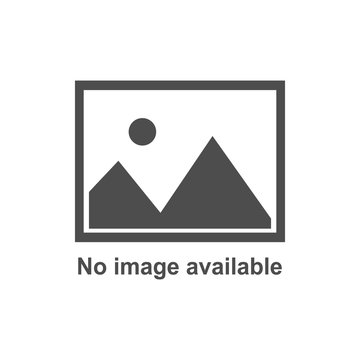
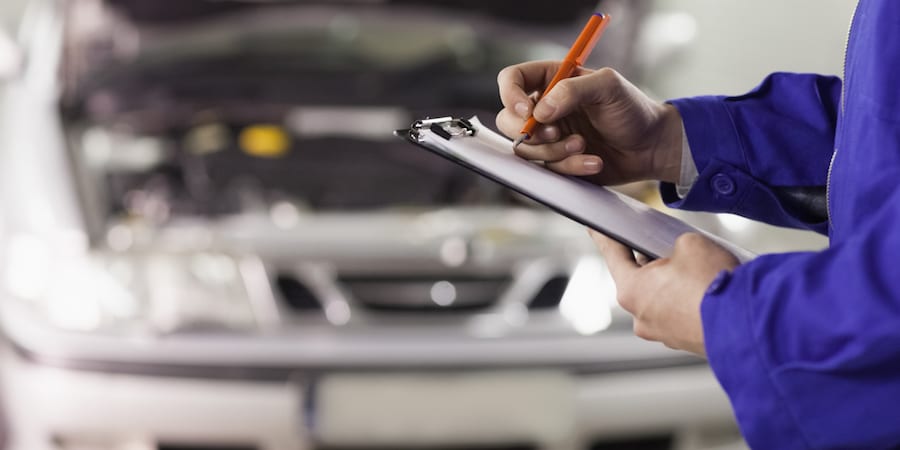
WOMACK'S YOKOTEN – In our lean journeys we spend so much time on improvement (kaizen) and innovation (kaikaku) that we often forget to address the issue of how to maintain our gains. Do you know iji? Perhaps you should.