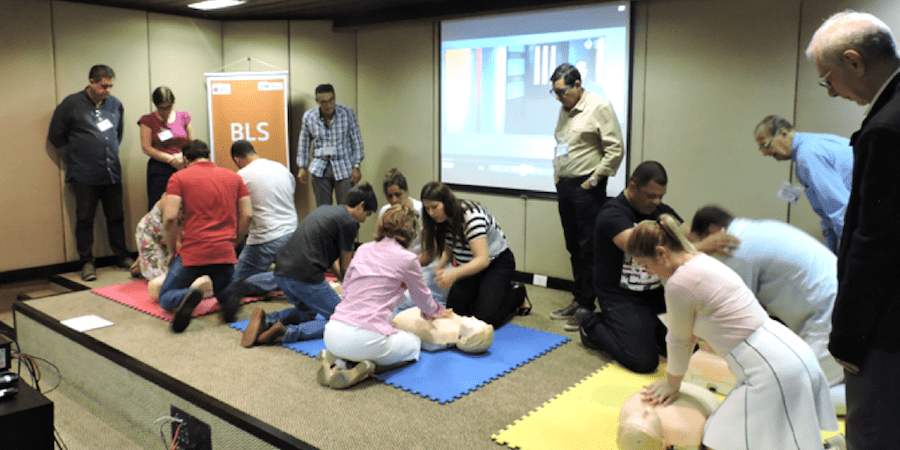
Creating a dedicated pathway for heart patients
INTERVIEW – A cardiologist from a hospital in Salvador de Bahia explains how his department was completely transformed following the introduction of a dedicated pathway for heart patients.
Interviewee: Eduardo Novaes, Cardiology Line Coordinator, Hospital Aliança – Salvador de Bahia, Brazil
Planet Lean: What was the situation in the Cardiology Department when lean was first introduced?
Eduardo Novaes: In Brazil, one person dies of heart attack every five minutes – that’s 80,000 deaths each year, 60% of each occur in the first hour. This makes it really important to treat heart patients as quickly as possible, which is one of the reasons why, in May 2016, Hospital Aliança decided to introduce a dedicated multi-disciplinary pathway for them. This involved professionals from different areas (like doctors, nurses, social workers, etc).
The problem that convinced us to give lean a try was that the fact that the Cardiology department had state-of-the-art technology and very capable staff available, but a high idle rate. There was no standard way of managing the provision of care, and we didn’t monitor any KPIs.
Assisting heart attack patients using the new multi-functional protocol was the first challenge we chose to tackle on our lean journey. We needed more than just a theoretical protocol to consult, however. We wanted a system that would cover the entire flow of a heart patient, from the moment he or she arrives with chest pain, through to the ER team and Hemodynamics to clear the obstructed artery, and finally to the ICU.
There are stringent time-to-care international standards for each stage of this process. Implementing such protocols is a challenging task, because we depend on those at the front line to know what exactly we need to do and when. This was the first time these set of actions took place in a coordinated way.
PL: How did lean help you?
EN: People working on the newly-established “Cardiology Line” were all care professionals with no experience with management, and the hospital didn’t have a proper toolkit that could guide them. As the doctor managing the new clinical path, I felt completely unprepared for this role and thought I didn’t have enough qualifications. For a while, I even considered giving up.
But then the hospital provided us with some lean training to develop our capabilities, and as a team, we immediately realized how strong a connection we felt with this alternative way of thinking. The introduction of lean at Hospital Aliança gave us a chance to modify our approach to providing care, redefining processes, creating standards, and developing the capabilities of our people. Lean gave us a method we could follow, and the support from top management that our people needed to succeed in this undertaking.
The results we achieved thanks to the lean-based protocol were tremendous. They included a 23% reduction in the time between a patient’s admission and the angioplasty procedure, as well as an overall improvement in our performance. For more on how we started our lean journey and the results we got, read this other article I co-wrote for Planet Lean.
PL: As it often happens in a lean journey, you began by preparing an A3. What can you tell us about that experience?
EN: At the beginning, building that first A3 felt pretty logical and straightforward, but the content of the work was immense and, before too long, mapping the process of treating a heart attack (which involves several people, processes and a lot of information) in one page started to feel like an impossible task. As healthcare professionals, we are used to manuals hundreds of pages long!
There were many iterations of the A3, but when we finally got it, it felt amazing. The impact was huge, for both our employees and patients: the former developed a better understanding of the process (which they could then standardize), while the latter could get treated most speedily.
PL: What’s the role of the IT system at the hospital? How do you ensure it facilitates the work, rather than get in its way?
EN: It’s not easy, but the golden rule is that IT has to work with and for the doctors and other professionals. The two have to be perfectly aligned, so that clinical thinking can somehow be built into the IT framework in use at the hospital.
PL: Did you meet resistance when you first introduced lean? How did you eliminate it?
EN: I have to say resistance wasn’t a huge problem for us: people appeared to be open to collaborating as soon as they learned about lean. In those instances in which we did encounter some resistance, we relied on empathy and started to put ourselves in other people’s shoes. Doctors would go to reluctant nurses or reception staff and told them they would make an effort to look at things from their point of view. Along the way, we all learned to put ourselves into the patient’s shoes, which is the most important thing we can do as healthcare professionals. At the end of the day, we are all humans and it’s important we learn to listen to one another.
PL: What is the biggest lesson your journey has taught you so far?
EN: There are several, actually. The first and most important is that lean is an excellent approach for improving healthcare, one that allows you to dramatically reduce waste and solve recurring systemic problems. We also learned that the people who are best placed to improve the process are those carrying it out day after day, at the gemba.
Personally, I have to say I have changed a lot: I am no longer solely involved in providing care to patients; I am a more complete professional, with managerial capabilities. These two functions, I have now learned, complement each other, and I believe this approach to the work has to be shared with the rest of the hospital. The benefits for the organization as a whole would be incredible.
THE INTERVIEWEE
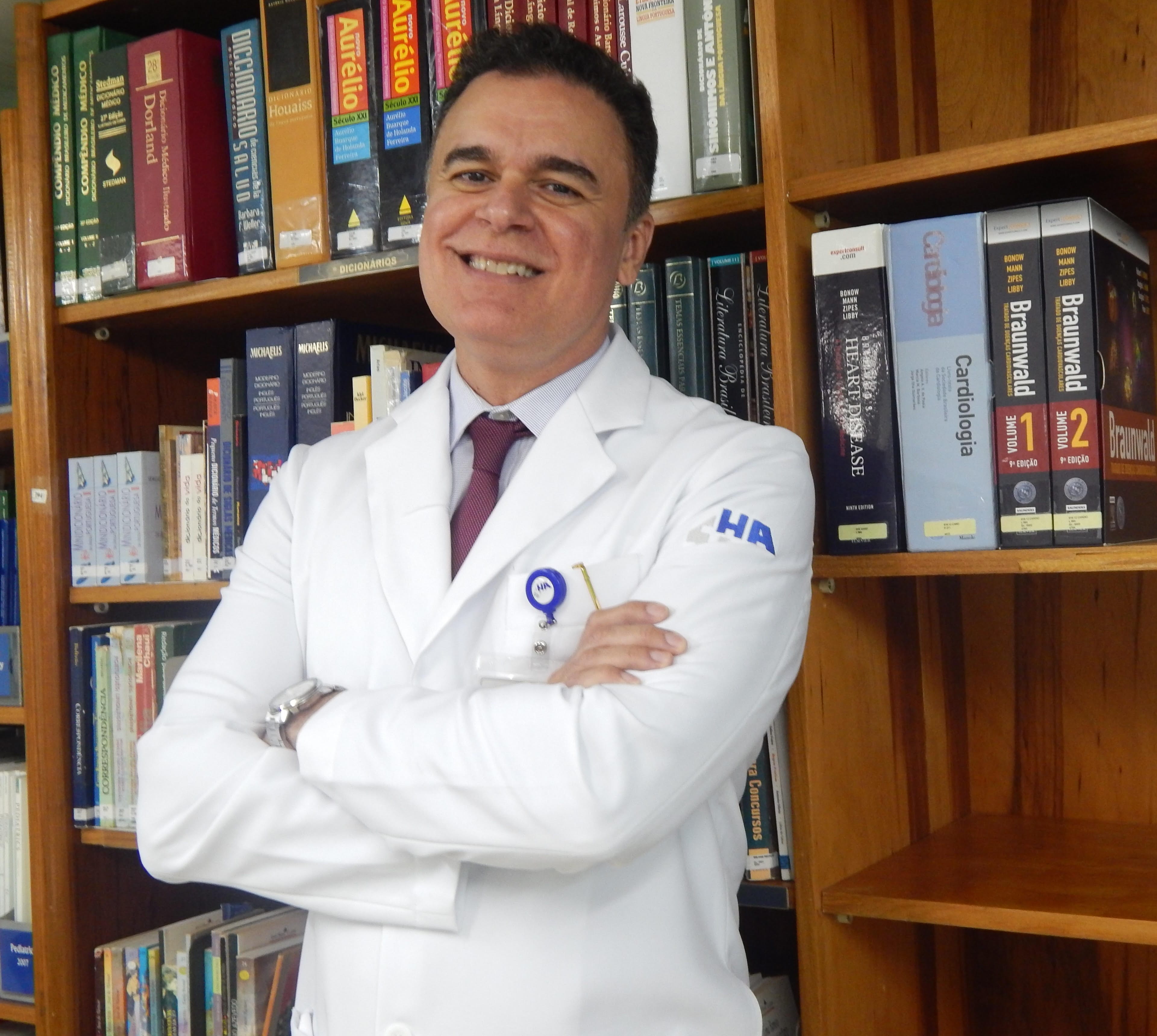
Read more
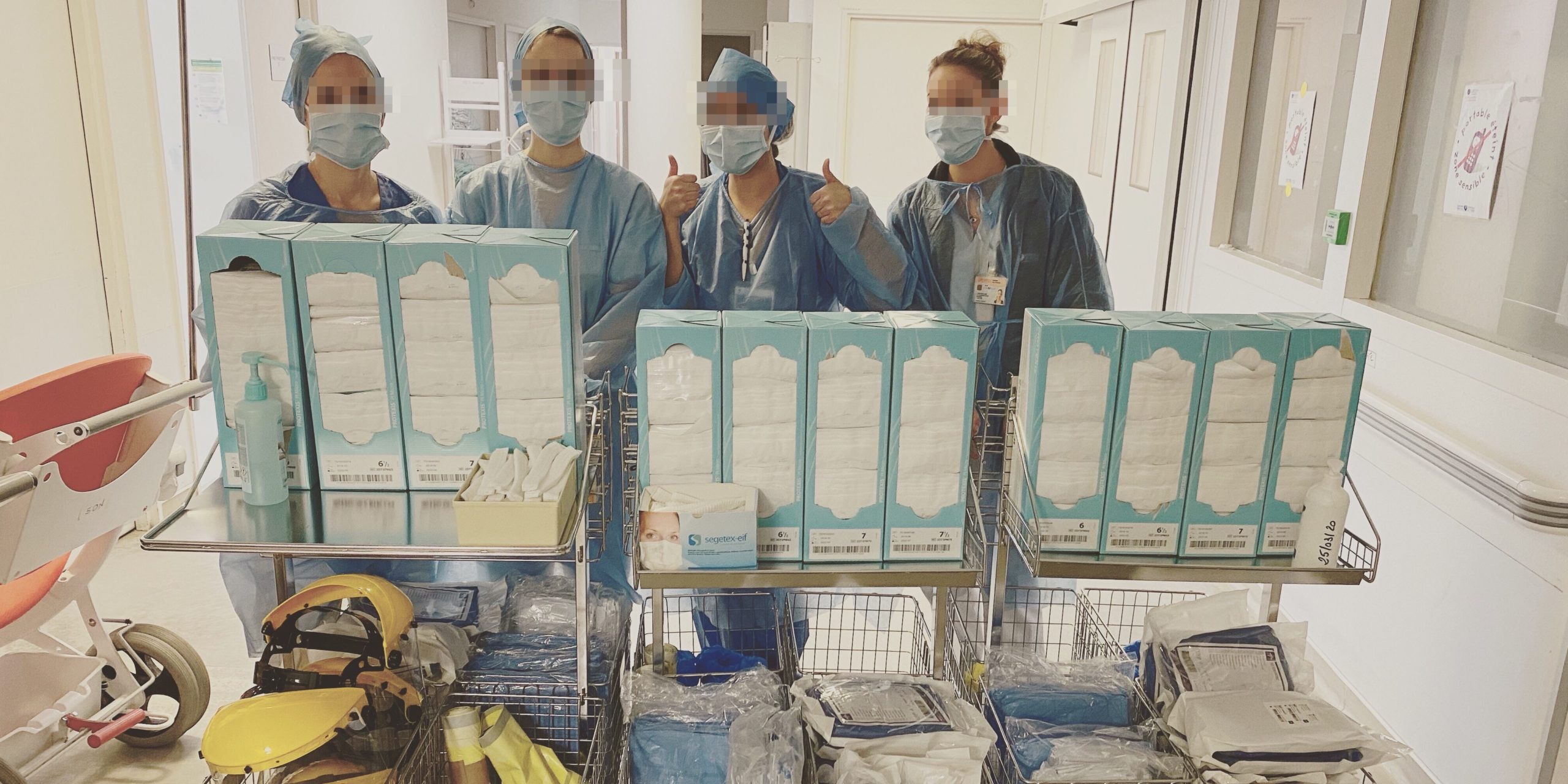
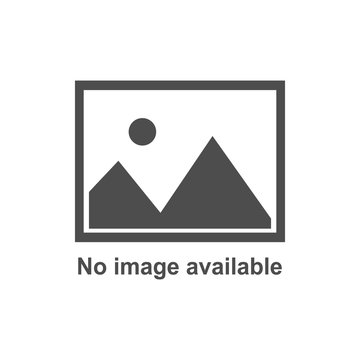
NOTES FROM THE (VIRTUAL) GEMBA – This small manufacturer is relying on Lean Thinking to keep the business running during the Covid-19 crisis, overcome the disruption in its supply chain, and even innovate.
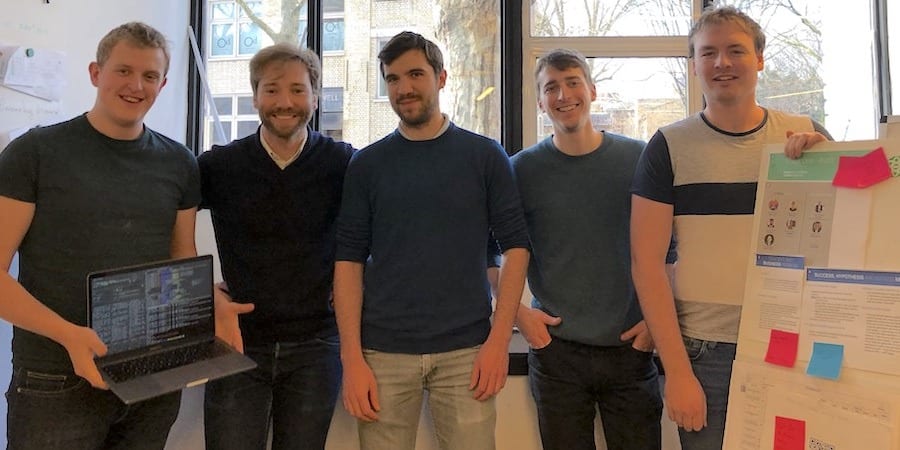
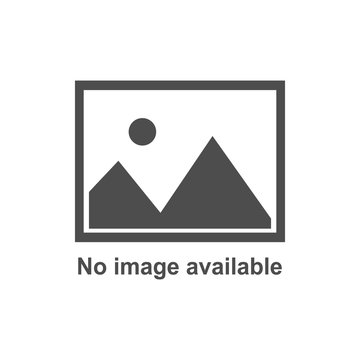
BUILDING BRIDGES – Struggling to scale a new product past its MVP phase, Theodo tried a number of things before realizing that the only way to retain quality and speed is kaizen.
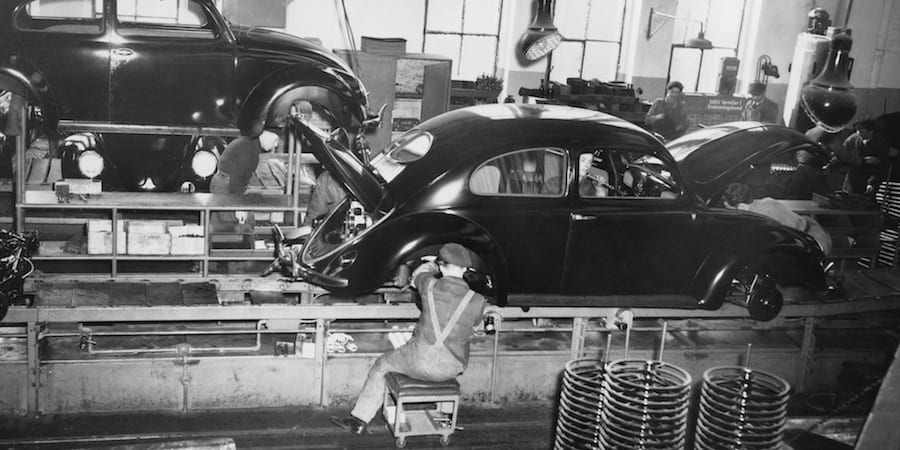
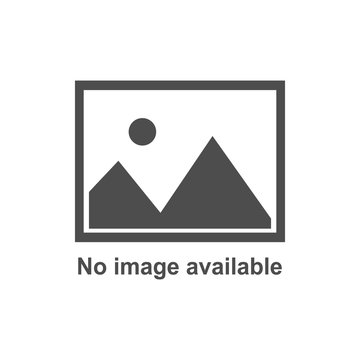
WOMACK'S YOKOTEN – The author reflects on how the legacy of Taylor and Ford still poses challenges to the lean movement, and why critics should move past a simplistic view of lean as mere standardization.
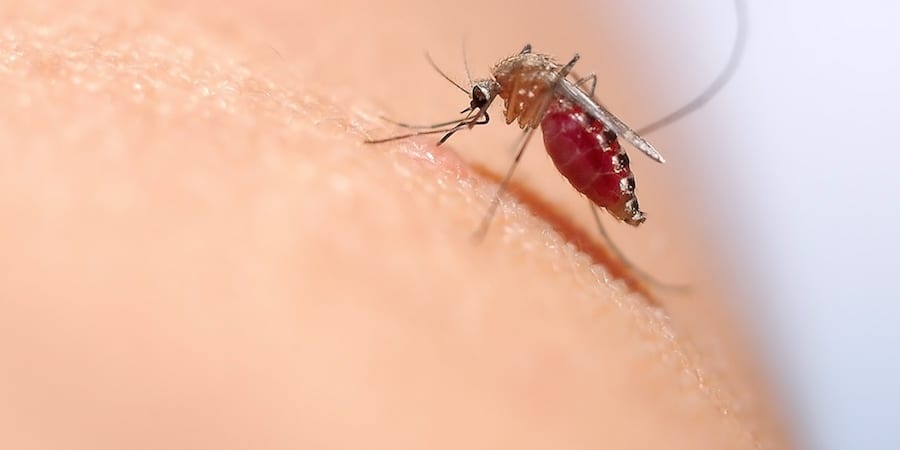
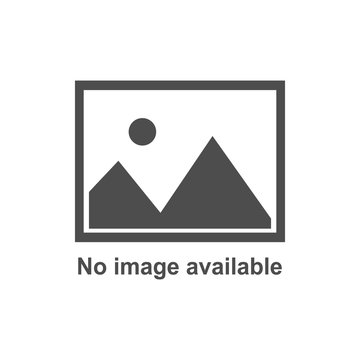
FEATURE – By using lean management, the Hospital São Francisco (HSF) near São Paulo, Brazil, has improved its ability to deal with dengue epidemics – treating patients more quickly and efficiently.