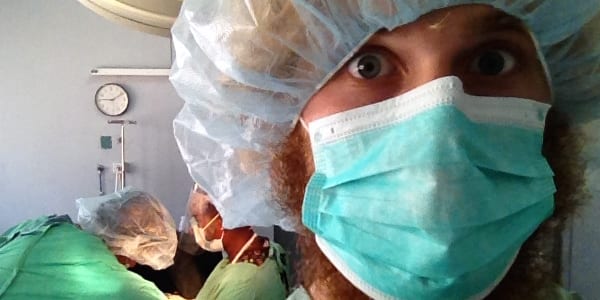
Lean leadership and the opportunity for developing countries
ARTICLE – While supporting the adoption of lean in a Mozambican hospital, a young engineer learned a number of valuable lessons on leadership and what it really takes to help developing countries to grow.
Words: Colin Emerson, Industrial Engineer and former Director of Quality and Process Improvement at Chicuque Rural Hospital, Mozambique
In November 2013, I boarded a plane from Atlanta to Johannesburg. I would soon make my way to a 100-year-old hospital in the rural fishing village of Chicuque, in southern Mozambique.
I was 23, exuberant, and petrified. I had just graduated from college with a degree in Industrial Engineering but had no idea how to actually improve a real world process or solve a problem. I had no real experience with lean, and no leadership skills. All I had was a copy of Mark Graban's Lean Hospitals, and a reliable Internet connection to read as many online articles about lean and leadership as I could find.
Chicuque Rural Hospital was a brilliant and brutal training ground for an aspiring lean healthcare improvement professional. The utter difference in everything between the United States and rural Africa is almost unimaginable for a Westerner who has never intimately experienced it. I tried to go into the experience without any upfront expectations so that I could treat every new thing as objectively as possible. Nevertheless, my understanding of normal had to adjust quickly.
My initial lack of language skills (Portuguese is the national language of Mozambique along with 60 some other nationally recognized local languages) was a very obvious and formidable hurdle. Yet the complexities of the history and local culture, which themselves would laugh at my ignorant Western notions of simplistic African life, presented the most interesting and complicated obstacles.
However, those difficulties made experimentation and learning for everyone involved that much richer.
To my knowledge, a lean transformation in that kind of setting had never been attempted before, and I did not have anyone to guide me through it. A good sensei is certainly a necessary relationship to have through one's personal lean journey, and I am grateful I have been taken in by a spectacular sensei since returning from Mozambique.
Still, being at the mercy of my own leadership was a vexing and prolific experience I would never trade.
I could only ever look at myself when improvement plans failed, which was typical and good. It was frustratingly beneficial to try something new, fail, reflect, and repeat throughout the year. Through that cycle I learned how I lead, how I needed to improve as a leader, while the people in the organization learned how good change can be.
What small victories we did gain were monumental for the local staff. We were not successful with very many tools outside of 5S, but the simple act of clearing out decades of junk and organizing work spaces eventually had an uplifting effect among line staff who bought in.
Chicuque and other smaller hospitals across Africa, which are hotbeds for international aid and development work, are among the most extreme examples of non-lean environments. Not only is African culture itself generally very adverse to change and humorously opposite of JIT, but local staff have grown accustomed to seeing outside development agencies, embassies, and charities come for short periods, give wads of money and do the projects for the local staff. All of this creates dependency and apathy.
For reasons like these, bringing lean principles into Chicuque went against the grain as is typical and expected, but the contrast after improvement orchestrated by the people in the organization for a change was all the more brighter.
I came away from my time in Mozambique with a few life lessons, which I think apply beautifully to practicing lean, especially in the context of a developing economy. I will hold onto these lessons throughout my career wherever in the world I am practicing lean. I think they are good lessons for anyone considering doing any type of work in a developing country, though I will describe them in the context of practicing lean.
HUMILITY
Lean thinkers are used to acknowledging that processes and systems are broken, but we need to also acknowledge human brokenness all around us. We are all broken human beings with broken relationships in this world. I do not mean a nonchalant, "Nobody's perfect." I mean the same brokenness that spreads AIDS in horrific ways or convinces a Mozambican janitor/nurse-aid that it is okay to not wash their hands in between cleaning a bathroom and feeding a patient. That brokenness is alive in me and you; it just manifests itself differently. Didn't you believe some backwards things about organizations before you learned to see? Isn't much of your existence as a practitioner changing inefficient or even harmful ways of thinking across organizations that many practice as religion because they had never seen another way?
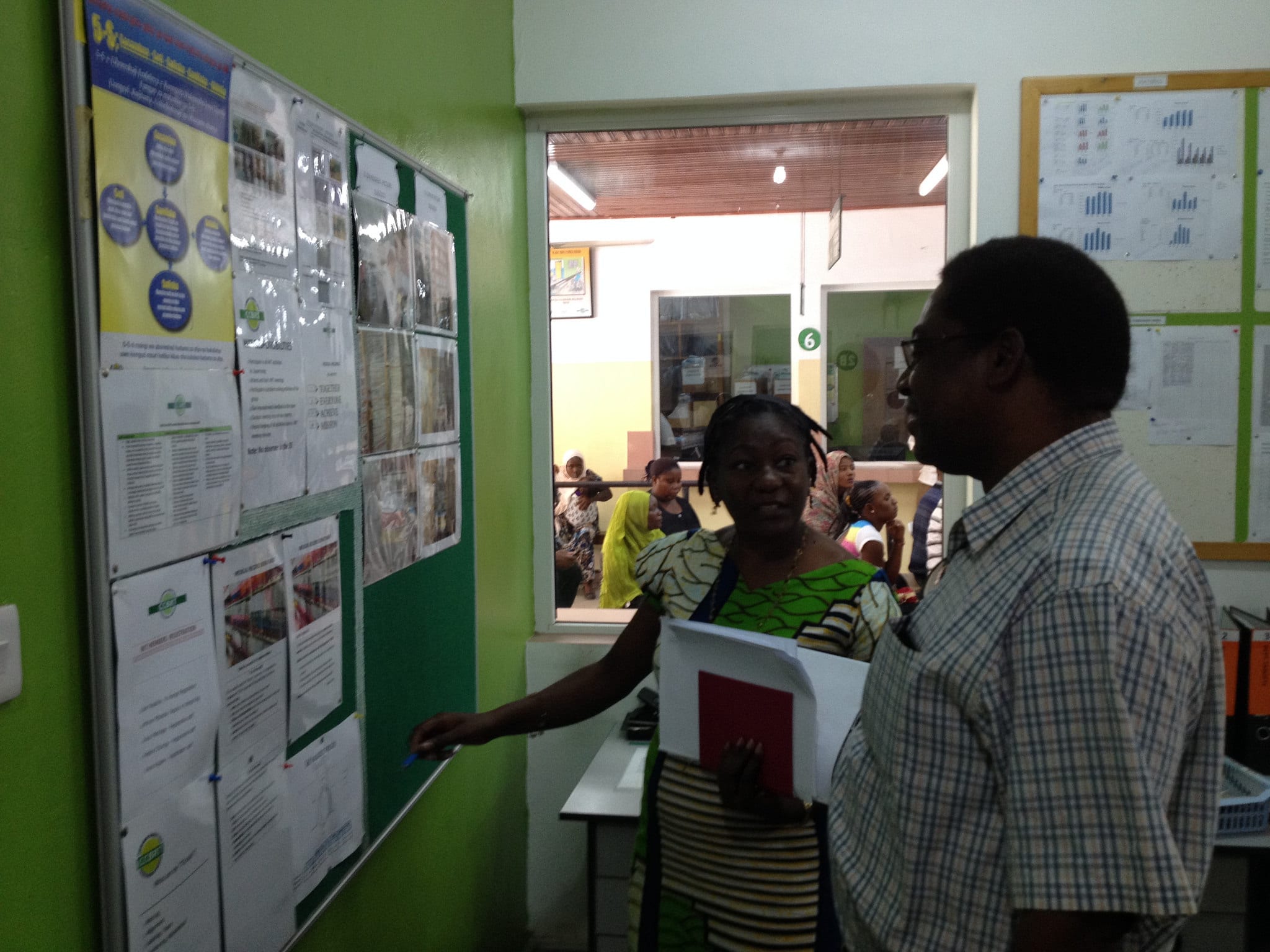
The most challenging, but most effective way to address this brokenness is with humility. Pride is a characteristic of the human condition, which does not need to be translated to be communicated across languages or cultures. Just as a practitioner sees the problems in an organization, anyone can easily see the pride in another person, especially when that person is trying to change their work! Pride is a stout impediment to lean improvement and organizational development. In the face of so many real, abstract differences, humility gave me the clearest avenue to relating with locals and ultimately getting things done, because authentic humility also transcends language and cultural barriers.
I had to face many instances of my own brokenness and lack of experience. I was the only person in the hospital working on process improvement, and I wasn't even confident in what I was doing. Where do you start when everything is broken and nobody seems to care? The locals do care, a lot; but for many reasons, mainly lack of resources, the problems were never solved. Here I was to actually address these problems, by changing the culture and helping these people see how they could solve their own problems.
Before I went to Chicuque, the hospital director asked me to spend a lot of my time fundraising for the hospital's many needs. I said no. I hate fundraising. I felt that fundraising for new infrastructure was an excuse to doing the real hard work of developing people and designing elegant process solutions that needed no capital, like the stories from Lean Thinking. Anyone can do anything with enough money I thought. I wanted to make Chicuque Rural Hospital great with the very limited financial resources it had.
However, I realized early in my time there that the most crucial problems, water and electricity shortages, could only be addressed with large capital investments. All of the improvement initiatives I tried in the early months initially failed and were met with disgruntled resistance. I conceded that the local staff did not want to trust me until I gave them something they wanted (money), and that the water shortage was the genesis of many other process and quality problems. So I had to humble myself and do the very obvious thing I should have done upon arrival. I applied for a grant for a borehole.
While the borehole is still not complete to this day, after people found out that we had won some money for it, the attitude around the hospital changed towards improvement. It was not like we had crested over the first big climb of a roller coaster and everything was fun and easy from then on out, but the hospital staff would work with me on some process changes.
LEADERSHIP
I personally think the greatest need for all of Africa is homegrown, integrity-driven leadership.
Any lean transformation requires bold, capable change agents. In impoverished settings such as rural Africa, the need for leadership is even more obvious because quality leaders are so few. Cycles of poverty do not break themselves. If good leaders were present, the cycle would not have started in the first place. Without leadership, the cycle will never break. But it is important to remember that these leaders must be indigenous and willing to look inward rather than blame others or remain apathetic.
Africans do not need Western saviors just like your company does not need a "Lean Messiah." Rather Africa needs its own people to rise up and lead them in integrity. Lean provides a powerful organizational practice for building an economy that will have to be shared with developing countries. But speaking from experience, you will only embarrass yourself if you presume that you personally have anything to offer the people you work with. Obviously you may indeed have much to offer, but humility must be at the forefront of your leadership and work, and it cannot be faked.
Another common difficulty for leaders, whether they are running an organization from the top or introducing improvement at the front line, is that not many others are likely to be able to relate to your situation or dilemmas. I certainly felt isolated in just about every area of life during my time in Mozambique. Relentless reflection was something I stumbled into by necessity. I simply did not have many people to talk about anything, let alone rural hospital improvement. But I did have a sunrise to contemplate in front of.
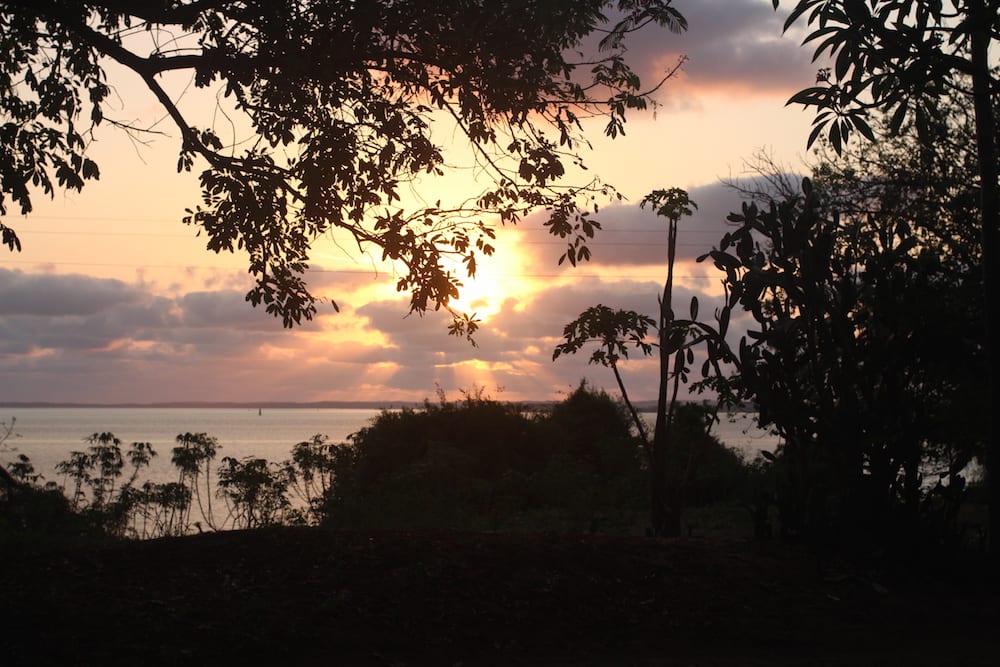
Relentless reflection was an outlet, a sounding board, and an idea factory for all my trials, in and out of work. I imagine many lone lean evangelists out there struggle with isolation, not knowing who to turn to or where to ask for advice. I think the idea of kaizen, having the people who do the work come up with the ideas to improve it, also applies to problems improvement specialists face through relentless reflection. There may be real and surprising barriers to a complete solution, like our extreme financial shortcomings or the fact that many of our patients did not know the translation of the Portuguese word "mosquito" into their own local language. But reflection enables leaders to reconsider the problem from different perspectives and get to partial solutions as stepping stones on the way to a complete solution, like tweaking public health education seminars on malaria to clarify the translation and make the connection with an actual insect.
POSSIBILITY
The obstacles facing lean thinking leaders in developing countries are significant. Miniscule budgets, cultural stagnation, and all manner of humorously ridiculous adversaries to improvement and systemization all around. However, the possibilities for lean in developing countries are limitless, and the results that can be achieved are persuasive. Amid the obstacles, it is always worthwhile to allow yourself to be optimistic and remember that anything is possible if you provide the leadership and right environment.
After several months of stalling improvements and battling immigration services, I consigned that I might not ever make this lean thing happen in Chicuque Rural Hospital. I had failed in several improvement attempts, and the ones that did come through only happened because I did the majority of the manual labor myself. I needed fresh perspective and I needed to bring my director up to speed much more rapidly.
I brought the hospital director on a visit to Comprehensive Community Based Rehabilitation (CCBRT) in Dar Es Salaam, Tanzania where lean coach Michael Grogan led the executive team into a new way of thinking. I witnessed possibility actively transforming into reality when we walked the gemba and met with their leadership and frontline staff. I remember the matron saying, "Our returning patients think the way we've improved things around here is magic. There's nothing magic about it, it (Lean) is just a better way of doing things." After the trip to CCBRT, my director had a clearer understanding of the necessary strategy for improving his own organization and I had renewed faith that we could make this work. We did not overhaul the hospital overnight, but we did lay the groundwork of a long sustainable trek toward lean. If lean can work in Dar Es Salaam, Tanzania and in Chicuque, Mozambique, it can work anywhere. Anything is possible.
Although I am back in the US now, I plan to remain involved with Chicuque Rural Hospital for many years to come and I hope to pass this rich experience on to other young, adventuresome lean thinkers. If you or anyone you know might be interested in practicing lean in a radically different environment, taking bucket baths (kidding... kind of), and enduring a profound life lesson every day, please contact me. I would love to speak with anyone interested in learning more about serving in any capacity in a developing country.
THE AUTHOR
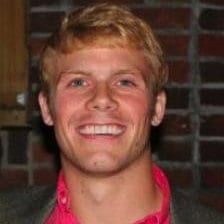
Colin Emerson is an Industrial Engineer based in Atlanta, Georgia. Between December 2013 and December 2014, Colin served as Director of Quality and Process Improvement at Chicuque Rural Hospital in Maxixe, Mozambique.
Read more
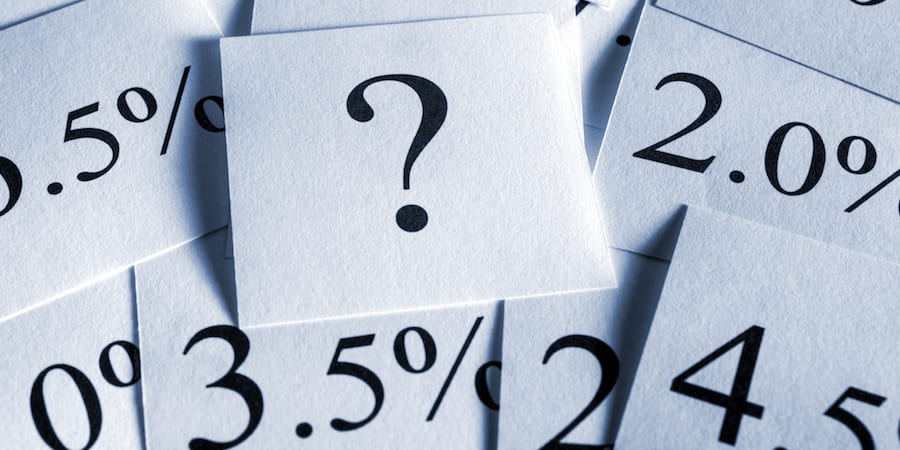
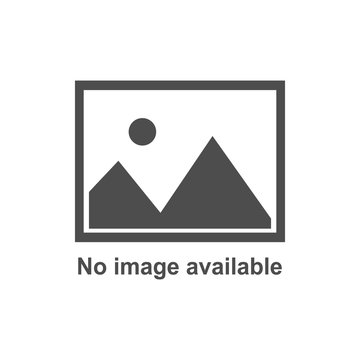
FEATURE – In the latest article in his series on how to effectively level production, Ian Glenday discusses why the perceived high variability of our demand is actually the result of a misconception… think about it in percentage terms!
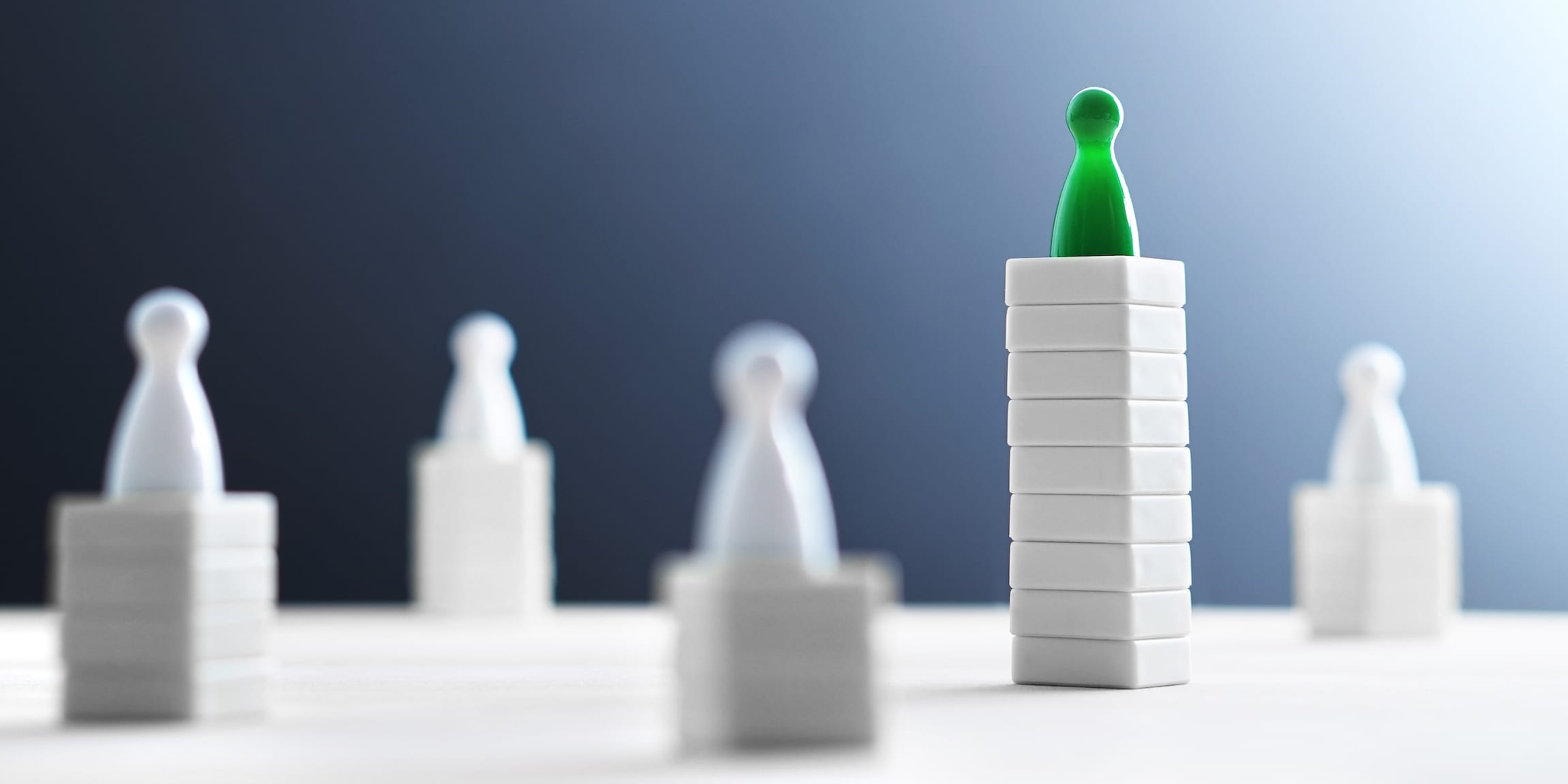
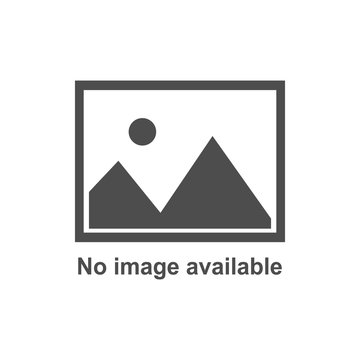
FEATURE – To really embrace lean thinking means to ensure the bureaucratic structures in our organizations enable our people to excel, rather than constrain their creativity.
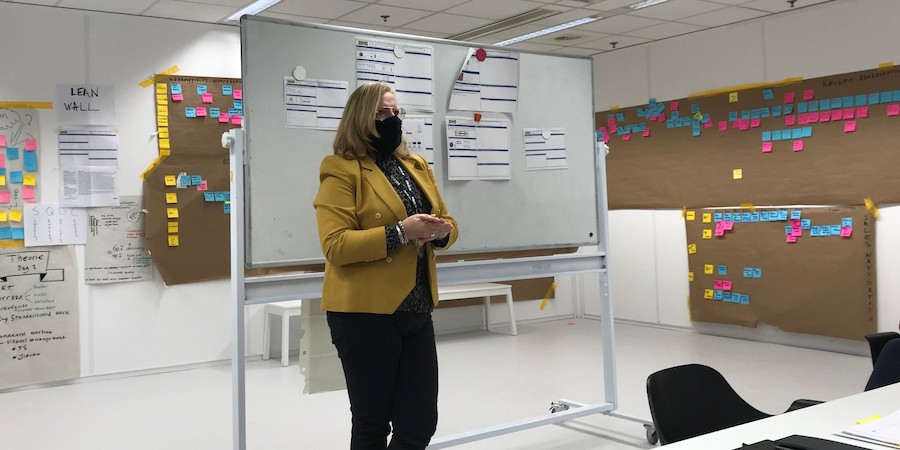
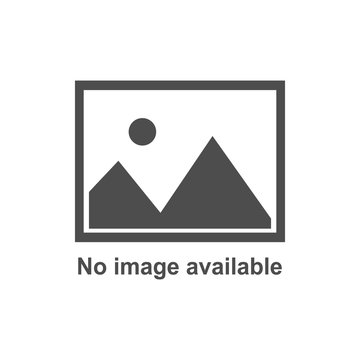
FEATURE – A former ops manager now tasked for improvement across IKEA looks back at what she learned in one of the company’s stores and explains how she hopes to take lean to the whole group.
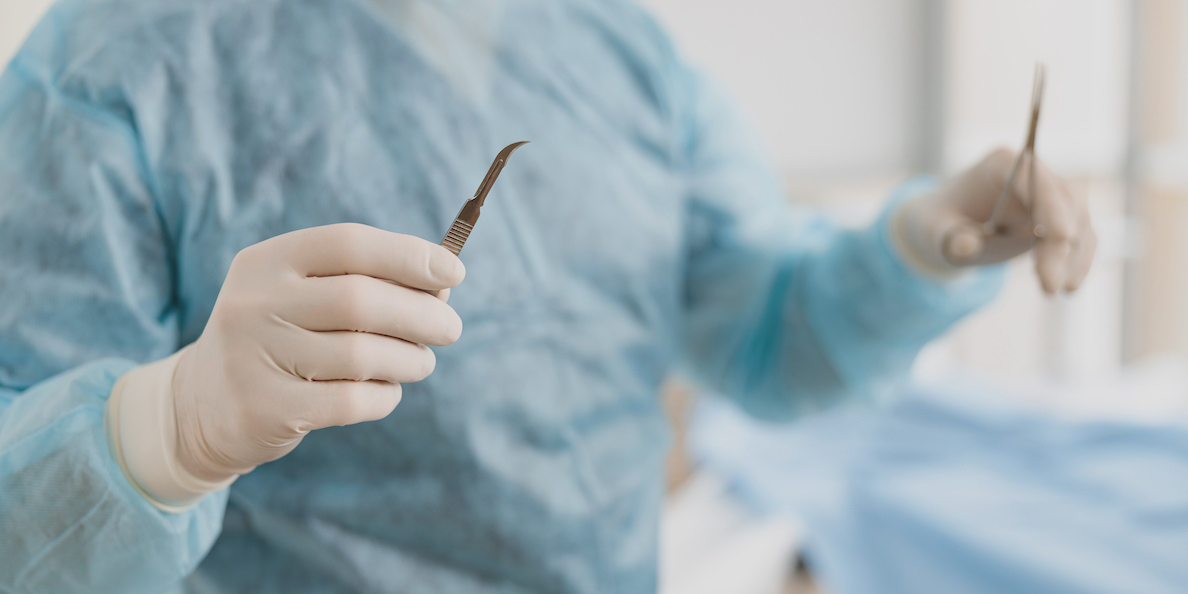
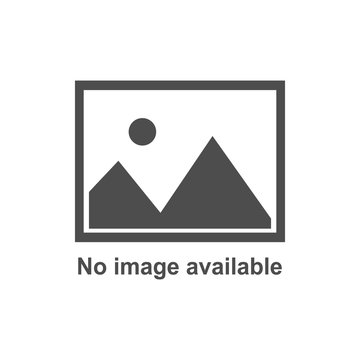
FEATURE - This surgery department was among the first areas in this hospital (maybe in the whole of Spain) to adopt Lean Thinking. Here's what their lean journey is focusing on more than 10 years after they started.