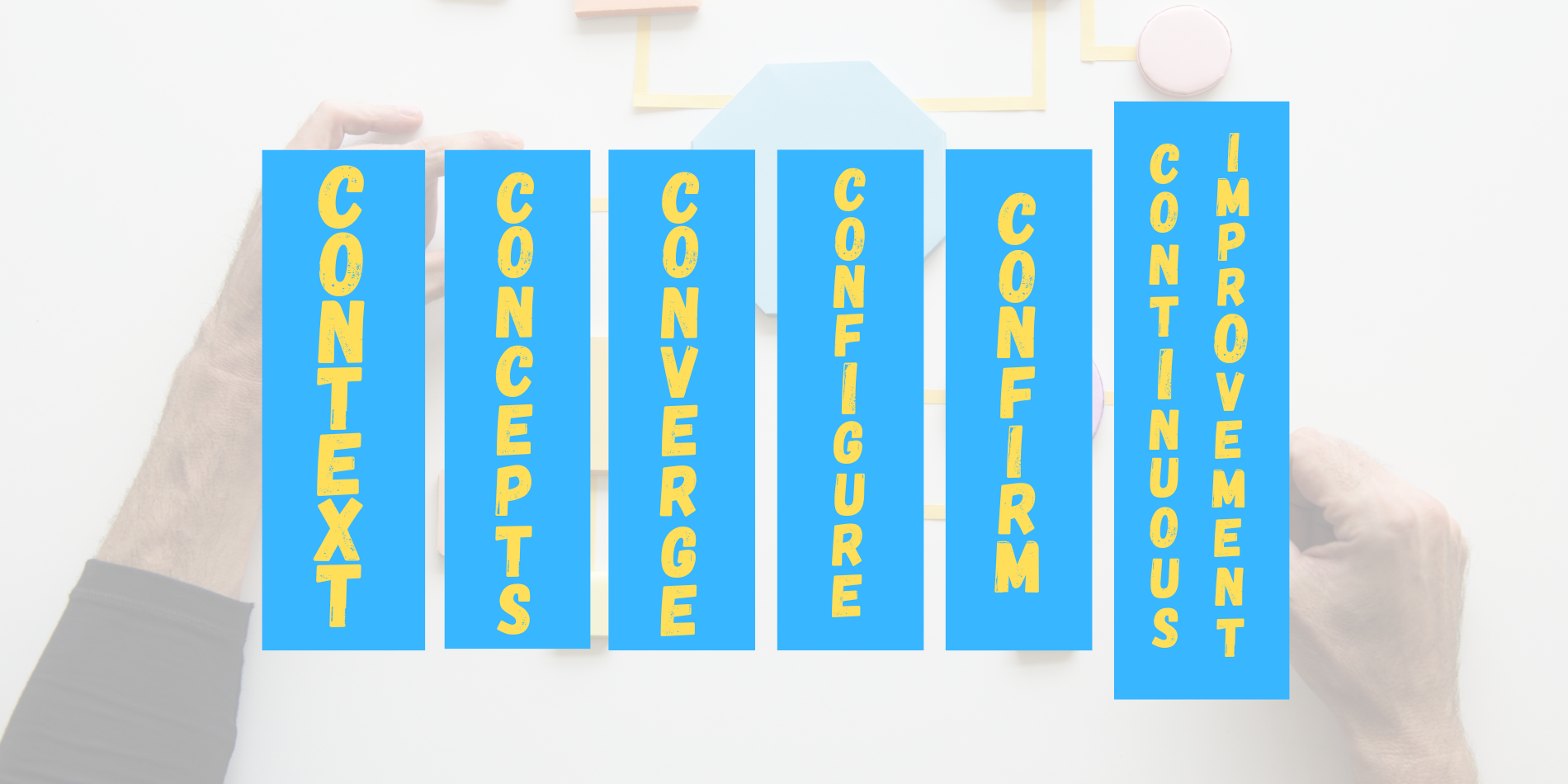
4 leadership considerations for better process development
SERIES – The authors discuss the final elements in their 6CON process development model – CONtinuously Improve – making and sustaining consistent improvements over time that will produce even higher levels of performance.
Words: Mark Zayko and Eric Ethington
“Continuous Improvement is better than delayed perfection.”
Mark Twain
For the 6th CON, CONtinuously Improve, we are deliberately shifting focus from the work of the team developing lean processes to the overarching leadership supporting the development efforts. Throughout this series, there has been an underlying assumption that leadership has been engaged and supportive of the team. To boost this support, we would like to offer four areas of consideration:
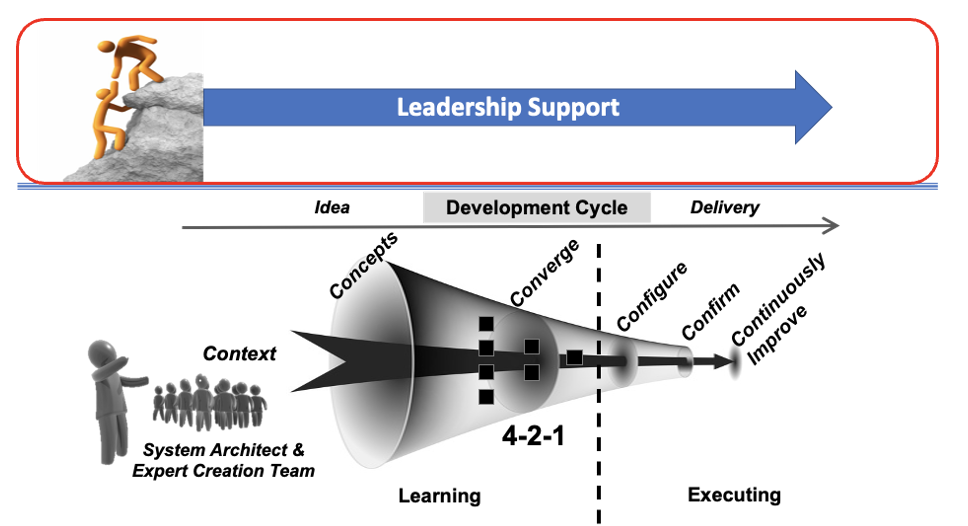
- Leadership support should be part of a process, not merely a declaration
Have you ever been in the situation of heading up a new initiative where your leadership publicly declared their support for what was to come and told you to just let them know if you ran into any problems or needed help? This is a nice gesture, but it can be frustrating when you need the help and the leader is not around, is not well informed about the initiative, or is making decisions that are counter to the direction of the initiative.
In the book Designing the Future, co-author Jim Morgan proposes the idea that a management system is equal to the product of the operating system and leadership behaviors. Or, written as an equation: MS = OS x LB. The idea is purposely written as a mathematical product to illustrate that if either element is missing or zero, the whole equation goes to zero and there is no management system. Here, we are directly addressing the operating system (to learn more about this whole equation, see this article by Jim Morgan).
Great process creation requires a clear role for leadership with regular engagements and a clear escalation path for highlighting and resolving issues, as well as developing the next generation of leaders. Additionally, these regular engagements should fall into at least two categories:
- Amongst the leaders – providing an opportunity to understand the roll-up of issues from various teams and to drive the ongoing improvement of the process of process creation.
- With the teams – providing an opportunity for communications, issue escalation and resolution, capability building, and a deeper understanding of the state of the specific programs under development.
- Make leadership’s work visible
Former Ford CEO Alan Mulally has been noted as saying, “You can’t manage a secret.” And that is where the idea of an obeya comes in. Obeya simply means “big room” in Japanese, and has become a frequently used project management approach. But it also has application in the overarching work of management. Just as we expect the process creation team to have an obeya, management should have one as well that will drive an aligned understanding of the situation, show normal from abnormal, and encourage collaborative problem solving. The obeya should be a reflection of the vision of the lean process development initiative. This may include the schedule and status of the programs in work, escalated issues, and key process performance metrics. Do not expect the obeya’s development to be “one and done” – it will and should evolve as the leadership’s team understanding evolves and their needs change. A few years ago, LEI faculty member John Drogosz wrote an excellent article that explores the common stages of obeya evolution.
- Schedule reflection
We remember working at a site in the late 1990s where a couple of the plant managers told us that they were “too busy to improve”. Yep, you read that right. And in some ways they were correct: the battles of the day consumed them and when the end of their long days rolled around, there was not any time or energy left to focus on improvement. Since there are always post-launch issues and there is always another program or two to get started on, it is easy for a process development leadership team to find themselves in this same situation. So, as you are setting up your obeya, build reflection points into the schedule. Not sure how many or where? Try one shortly after the initiation of the lean process development efforts, one in the middle of the development cycle, and one at the end. This provides a couple of opportunities for major course corrections and time for a post-mortem at the end.
- Deliberately target and develop system architects
Have you ever been on a tour where you are proudly shown the “lean cell” or “model area”, but there is no evidence that any of the lessons learned have spread beyond that one area? It is an oasis of efficiency in the middle of a desert of bad practices. To avoid this situation, the practice of “yokoten” (or deployment across an organization) is utilized.
A key enabler of great process development is the role of the system architect. Think of them as the conductor of the process: they do not play all the instruments, but they are familiar with their capabilities and coordinate them to make music.
Do not take the success of your first attempt at lean process creation for granted. Each of the team members may have been masters of their functions (just like the virtuoso musicians), but without the coordination and vision of the system architect, the results may have been far different. To replicate and expand on this success you will need more system architects. The idea of yokoten should be extrapolated into this space.
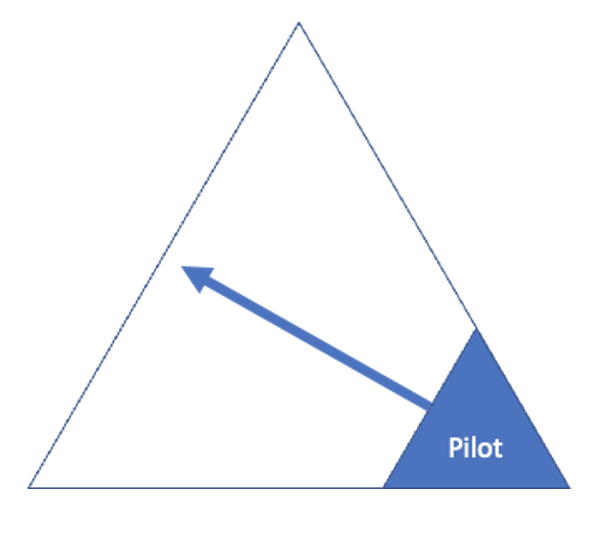
As for developing more system architects, ask yourself, “Was there someone on the pilot team who showed promise?” “Can they co-lead the next process development cycle?” “Is there someone who has been identified as a future system architect?” “What role can they play to gain experience?” There are many paths you can take to develop system architects, but you need to identify and pick one, then learn from it.
There are many dimensions that can be continuously improved for any process, but we feel that one key enabler is the leadership team and their sustainable engagement, support, and involvement in developing great processes which only comes from great teams and great people working together.
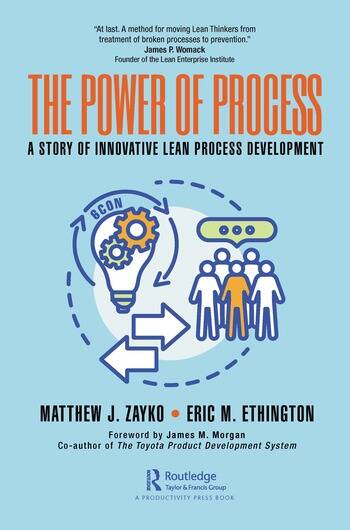
For more details, please visit www.thepowerofprocess.solutions
THE AUTHORS
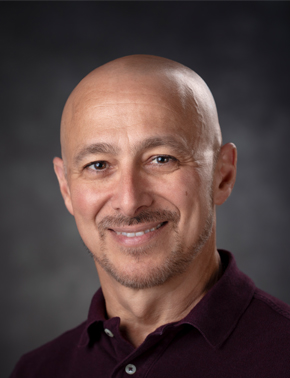
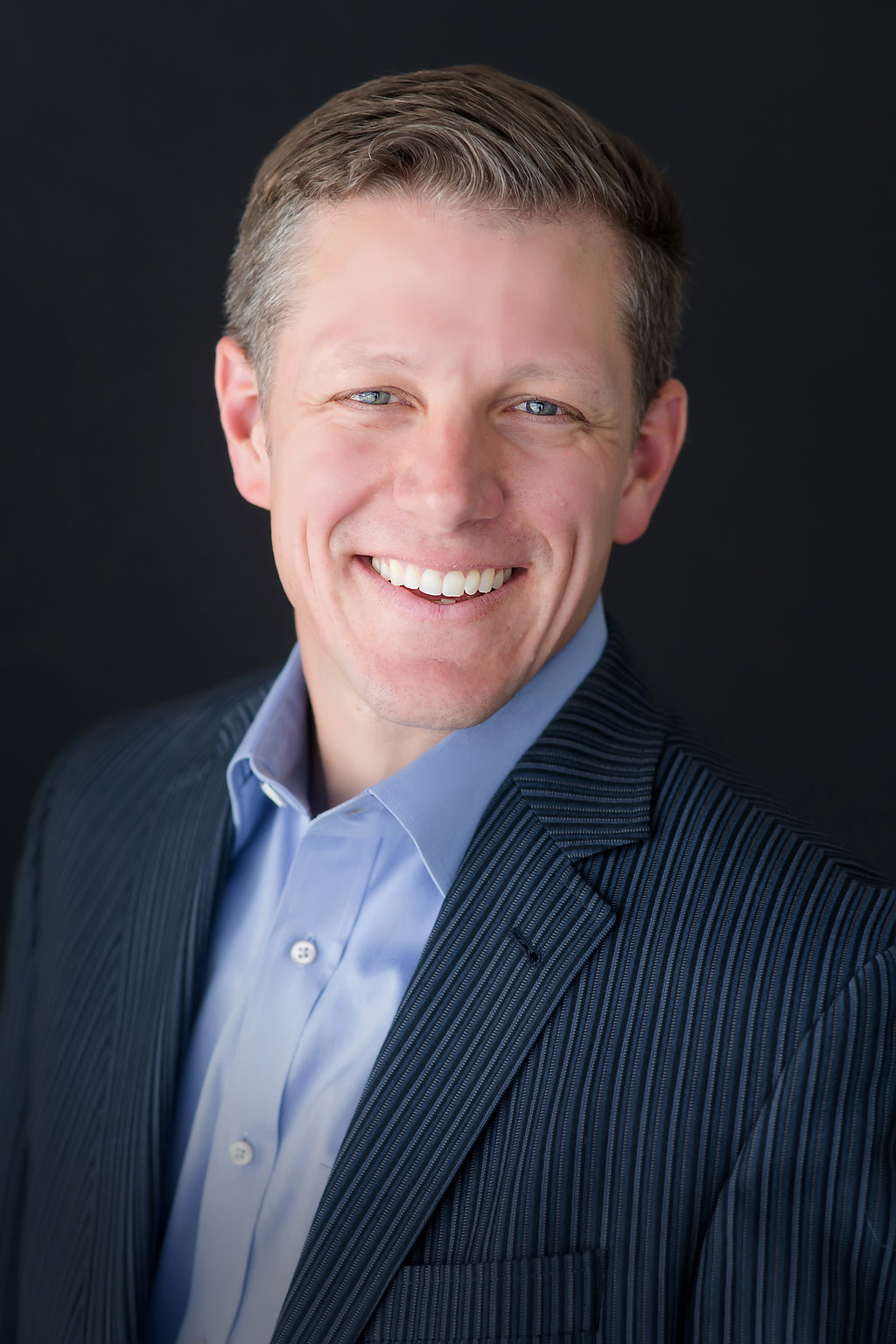
Read more
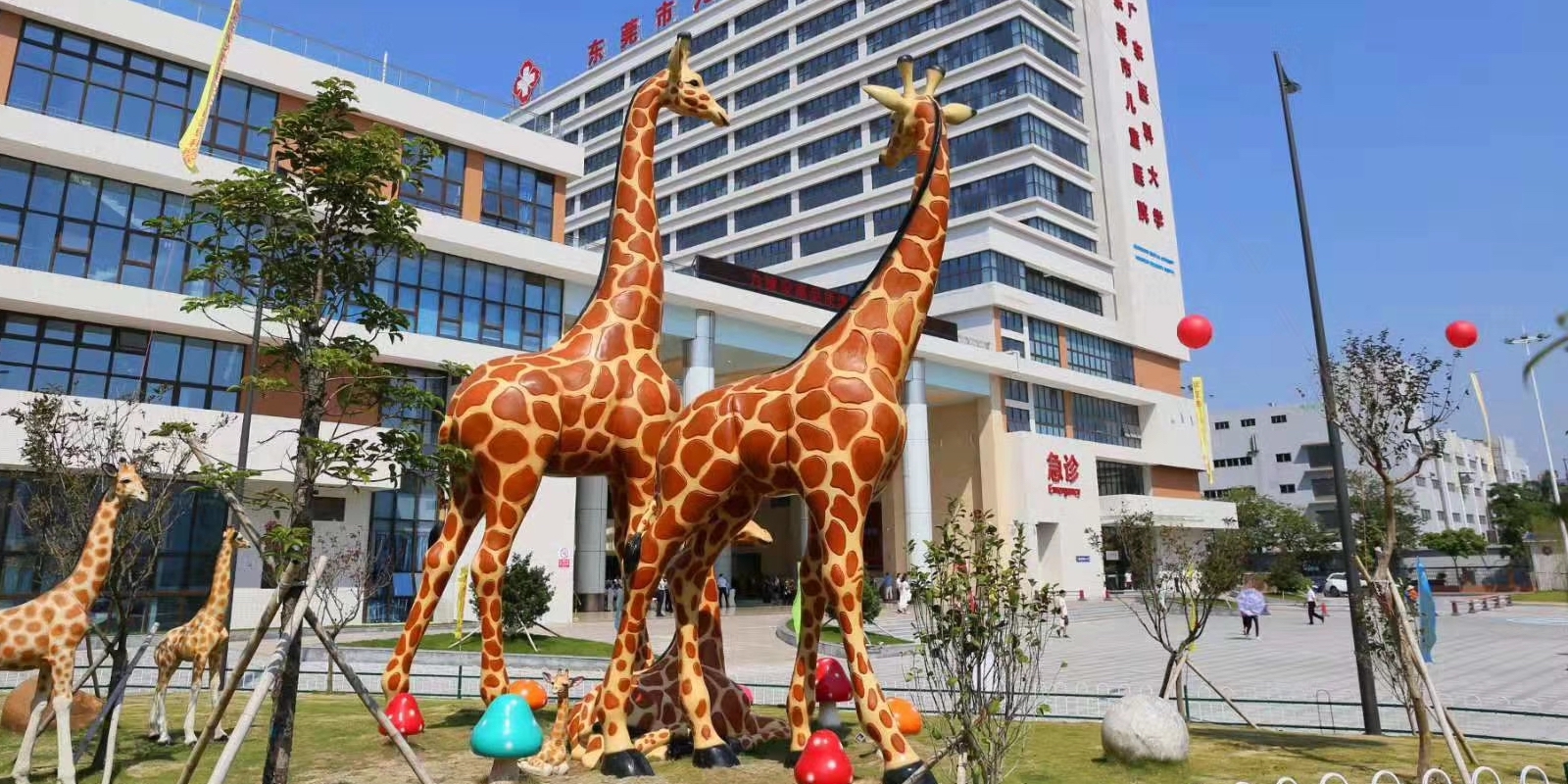
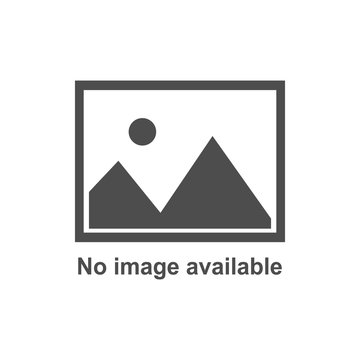
FEATURE - This story from a Chinese children's hospital reminds us that the lean healthcare improvements we make can have remarkable results on both patients and staff.
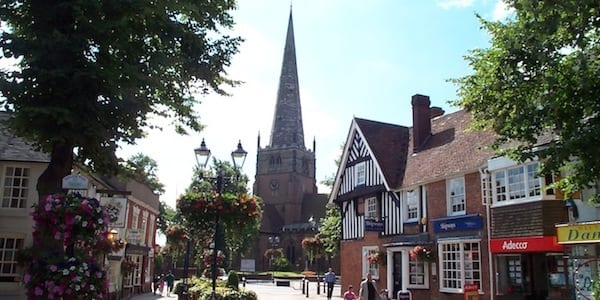
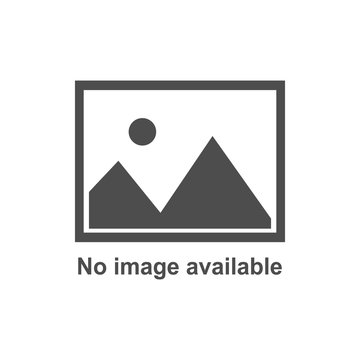
CASE STUDY - In November last year, a town in the West Midlands made the headlines after a survey named it the best place to live in the United Kingdom. Lean may not be directly responsible for the achievement, but there is little doubt it gave its contribution.
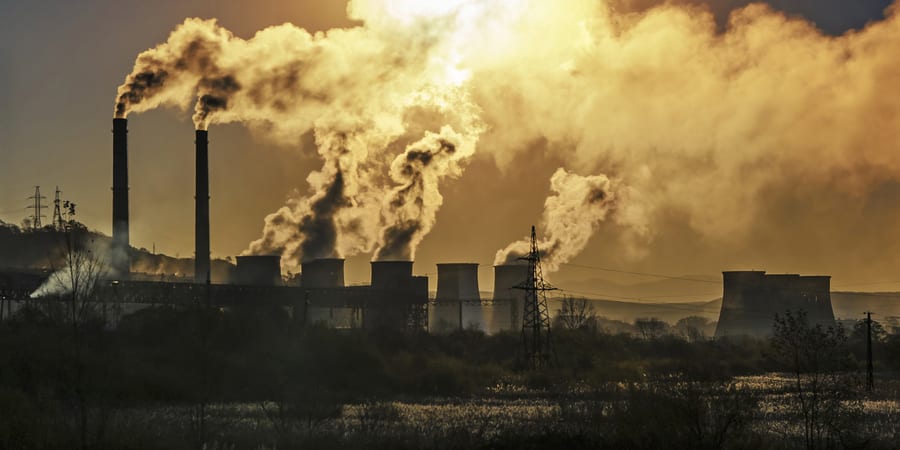
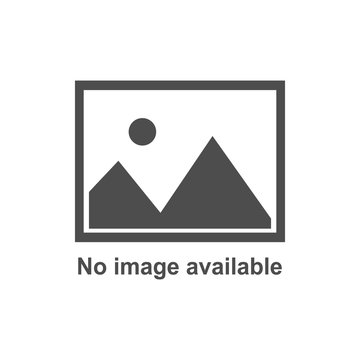
WOMACK'S YOKOTEN – Last month nations signed a greenhouse gas emissions deal – on paper, an insurance policy against climate change. But if action is to follow promises, the cost of the insurance premium, as perceived by voters and governments, must be lowered. Lean thinking can help.
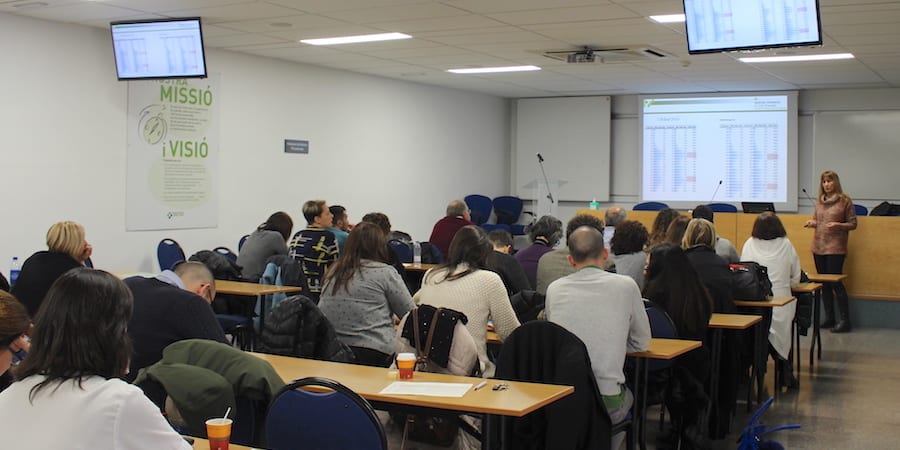
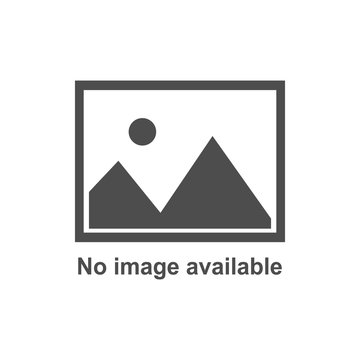
FEATURE – By bringing organizations together to regularly share updates on their lean journeys, Instituto Lean Management has managed to create a flourishing lean healthcare community in Catalunya. But hospitals aren't the only ones benefitting.