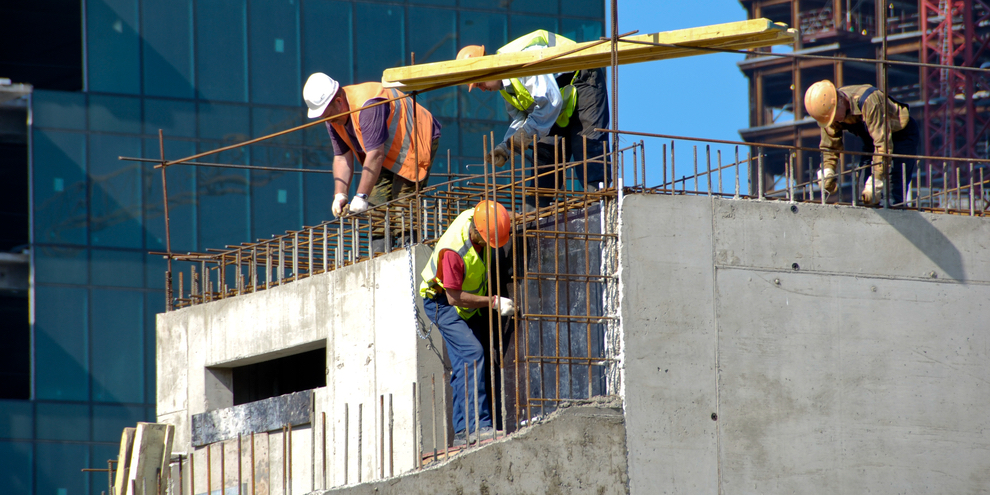
Improving the front-line work in construction
FEATURE – What is the key to improving the front-line construction work? Our lean construction coaches pull their experience together to shed a light on the subject.
Words: The LGN Lean Construction Working Group
Lean was introduced to construction almost at the same time as in manufacturing. And yet, decades after it first appeared, the construction industry continues to lag in key metrics, such as safety and productivity.
Why is that? Over the years, important tools and methods have been introduced in the sector (for example, Last Planner System), bringing greater stability to construction projects. Unfortunately, there hasn’t been enough of a focus on studying and improving the value-adding front-line work.
One reason behind this might be the way in which the industry itself is structured: in most construction projects, the actual work is not performed by the general contractor but by subcontractors. General contractors plan, coordinate, and engineer, but they do not participate physically in the actual construction of the building. Because they are not doing the work, they seem to have lost the ability to improve it. With the means and methods left entirely to them, subcontractors typically become much more experienced than the general contractors in performing the daily work – and harder to coordinate. A disconnect creates between the parties that has come to represent one of the most common problems in the industry.
To address this situation, we need to focus on the following:
- Support owners in developing contracts in which lean is required as a project strategy, and bring owner, general contractor, and subcontractors together to share the responsibility of the work.
- Support owners in learning how to understand and evaluate general contractors’ actual lean capabilities.
- Help general contractors to understand that a lean transformation requires addressing the five dimensions of the Lean Transformation Framework (moving from a tool-oriented approach to a culture-oriented approach).
- Putting at the heart of lean construction the improvement of the value-creating work through the engagement of front-line workers.
PROPERLY CATEGORIZING THE WORK
Before we discuss how to improve the front-line work, we believe it is useful to spare a few words on how this should be categorized and studied. We find that, in lean, the focus of work study can be broken down into something we call the “3Cs of Work”. Traditionally, companies in the construction industry have not studied the work using this framework, but those who do find great value in it.
First, we look at the “Characteristics” of the work. As the team member does the work, does he or she experience overburden? Is the work difficult to physically do? Is there waste in the person’s work? Is there unevenness (they are quite busy at one time, not so much at another)? In Lean Thinking, we typically refer to this s the 3Ms – Muri, Muda, Mura. The reason we focus on the characteristics of the work first is that the construction industry has traditionally looked sideways at overburden: it is a commonly held belief that the work in construction should be hard.
The second C refers to the “Content’ of the work. As lean thinkers, we are all familiar with this. Is it waste, incidental, or value-added work? Striking the nail with the hammer is value added, swinging the hammer is incidental, and walking around, searching for the hammer is waste.
The final C is the “Categories” of work. In this case, we want to understand what the team member’s cyclical work is (like pounding the nail or installing a piece of dry wall), what their periodic work is (like going to gather supplies), and what in their work is abnormal (tasks that cause a problem and take them out of their cycle).
By categorizing the work this way, we can create workflow, thus making the work consistent, repeatable, and smooth. This is the first step to improving the work.
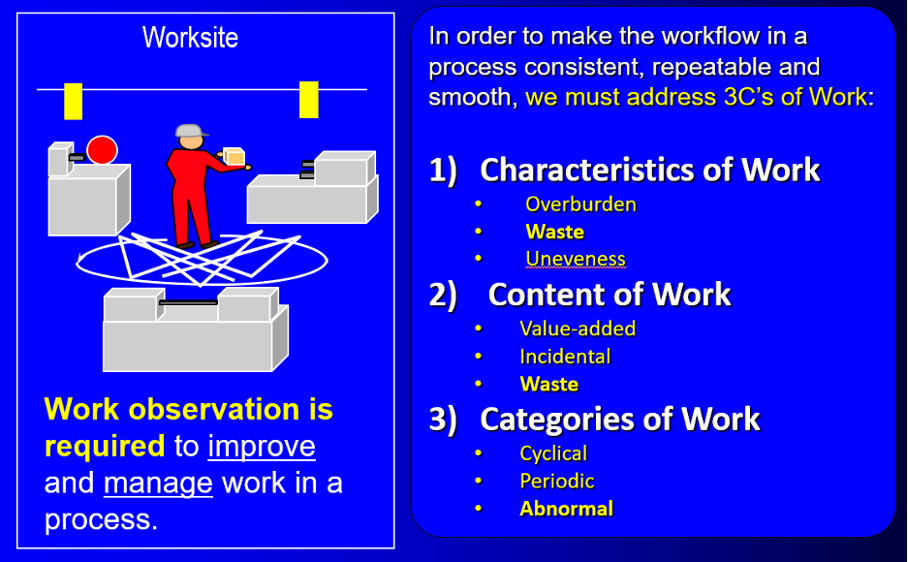
IMPROVING THE VALUE-CREATING WORK
Work in construction is typically organized around “getting the job done” to meet the schedule, too often with very little regard for safety and quality. Whenever a problem occurs, the “solution” that is implemented is simply to increase manpower, add overtime, use more equipment, or change the work specifications.
If we are to transform the construction industry, we must find a way to challenge this approach and prove that the exact opposite is true: it is by making the work easier, reducing hard labor (in all its forms) and increasing safety and quality “right first time” that we’ll be able to see the improvements in productivity and lead-time that we are seeking. As we become more productive, we’ll of course be able to reduce the duration of our projects, too.
Brazil-based construction company Habiarte, for example, was able to harness the power of Lean Thinking to achieve the basic stability necessary to establish standardized work and, therefore, a framework for improvement. This allowed the company to increase the productivity of its projects by 15 to 30% and eliminate cost and time deviations. As a result, Habiarte is now able to complete projects within budget and in a shorter time (on average, 6% faster than before). Standardization became part of the company culture: today, 30 days before each trade kicks off, the company creates a standard work involving the site team and subcontractors.
Do we need to engage people to improve the work, or do we improve the work to engage the people? The answer to the chicken-and-egg question is found in the way gemba-based improvement works. Bringing people from the owner, general contractor, and subcontractors together repeatedly on the site to observe and improve the work activates a process that develops engagement while enabling further improvement. Engagement and improvement are, in this sense, the two sides of the same coin.
Sometimes, the improvement process starts from a very simple question we can ask the workers: “What can we do to make your day better?” Creating an environment in which workers can share their experience and share the problems they see is a powerful enabler of change. Starting from there, we believe that the process of work improvement should be standardized and contain the following key points:
- Go to gemba, observe the work, study the project.
- As a general contractor, make sure you involve owner, subcontractors, and safety team.
- Get people’s support by explaining that improving front-line work is key to their own success, not just the project’s.
- Include quality control in any work method.
- Organize control measures so that front-line workers can carry out the checks and problems (deviations) can be visualized and discussed directly on site.
- Teach and use easy problem solving directly on site to fix problems and improve standards.
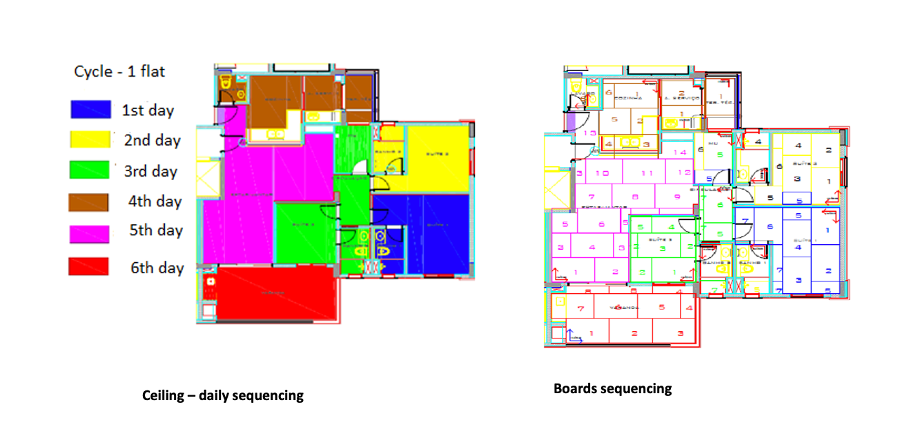
THE ROLE OF LEADERSHIP
Getting the improvement of the front-line work going starts with management. Leaders should develop their ability to enable this process and focus on three main aspects.
First, they should model behaviors. People often take pride in working hard rather than in doing value-adding work, and that mindset has to shift: easier, safer and first-time quality work is what we should strive for. Once front-line people understand this is the main objective of a lean transformation, they become willing to contribute. For that to happen, however, managers need to be at the gemba, acting as servant leaders and carefully observing the work.
Secondly, coaching needs to happen at the gemba, where the problem occurs. Showing respect, a core tenet of Lean Thinking, means to go out and talk to people, to listen to their problems, to challenge them to always go deeper in their analysis of the work to find ever better solutions, and to give them the support they need to follow the working standards that have been created. In other words, using coaching to show respect on one side and help people develop their problem-solving solving skills on the other.
Finally, managers need to encourage the use of A3 Thinking on the site. Involving management int the improvement work can be challenging (it is hard to change deeply rooted habits), but their guidance can be extremely useful – especially when dealing with complex problem-solving exercises. Spain’s Instituto Lean Management has trained several managers and guided them through A3 Thinking with great results: the following A3 shows how a construction company was able to reduce concrete quality problems (surface cracks) by a staggering 95%.
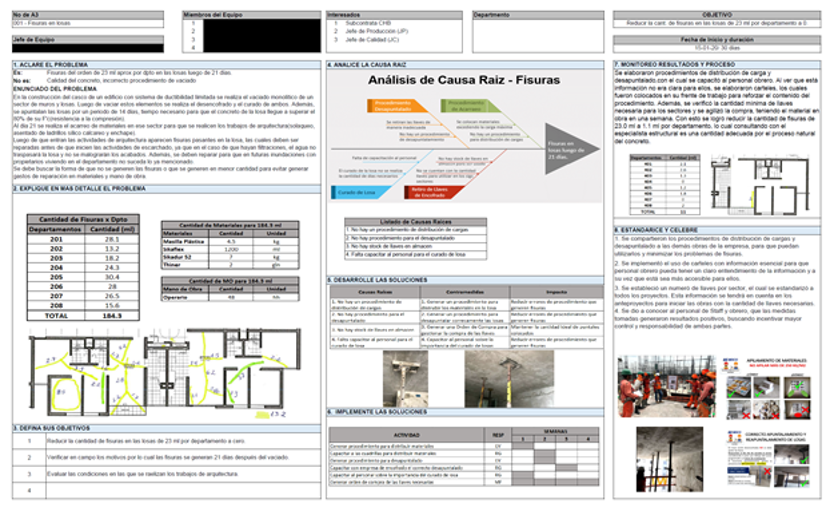
DEVELOPING PEOPLE IS CRUCIAL
Before kickstarting any improvement activity, we need to ensure that people are given the knowledge and tools they will need to do it successfully. For this reason, training and people development represent a step a construction company really can’t skip if they want to create a context in which new behaviors can take shape.
Workers should be educated in understanding Lean Thinking, how it applies to construction and how it can lead to the creation of a different culture. They also need to be taught how to recognize and eliminate the waste that exists in the process and the standard that has to be followed to improve the work at the gemba (improving is not just about will, but also about method).
Improving the work is about creating standards and practical knowledge for the organization. In this sense, managers should promote the development of skills matrixes to understand what competences the company considers important and to map their actual presence and pursuit within the company. The goal of any training initiative should be to create a shared knowledge base that will support the improvement process across the company.
IMPROVING HOW THE WORK IS DONE
Lean is about creating the right conditions and environment for workers to produce value for the final customer. What workers are experiencing in terms of hard work and safety should always be at the heart of any improvement activity. When Lean Thinking becomes an answer to worker’s need and helps them in their daily work, the positive effects will be felt naturally across the process.
Several construction companies are implementing lean management tools – such as pull, flow planning and daily and weekly management – often with very good results. The logical next step is to dive deep into how the work is done, becoming very granular in the improvement of productivity, quality, and safety with the participation of subcontractors and front-line workers. This is necessary to progress in a transformation, to sustain results, and to improve continuously.
The Lean Global Network’s Lean Construction Working Group aims to contribute to the development of the industry. We have witnessed and supported several experiments in lean construction and believe that our global and multi-industry experience might contribute ideas and concepts that until now have not received the attention they deserved.
THE AUTHORS
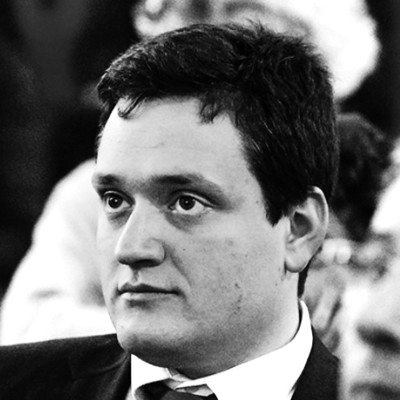
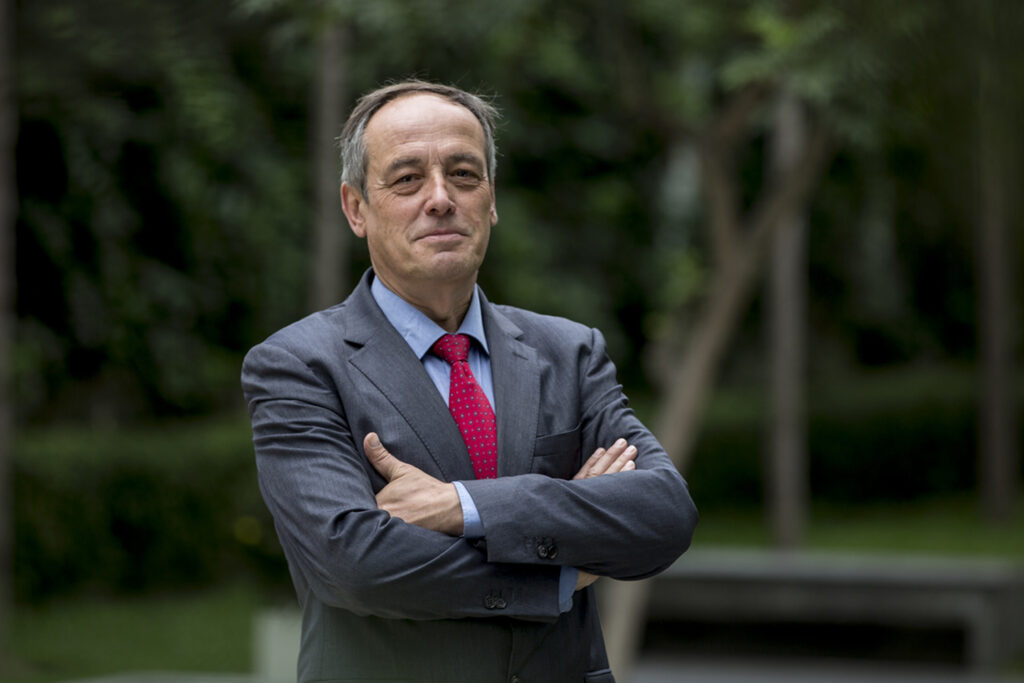
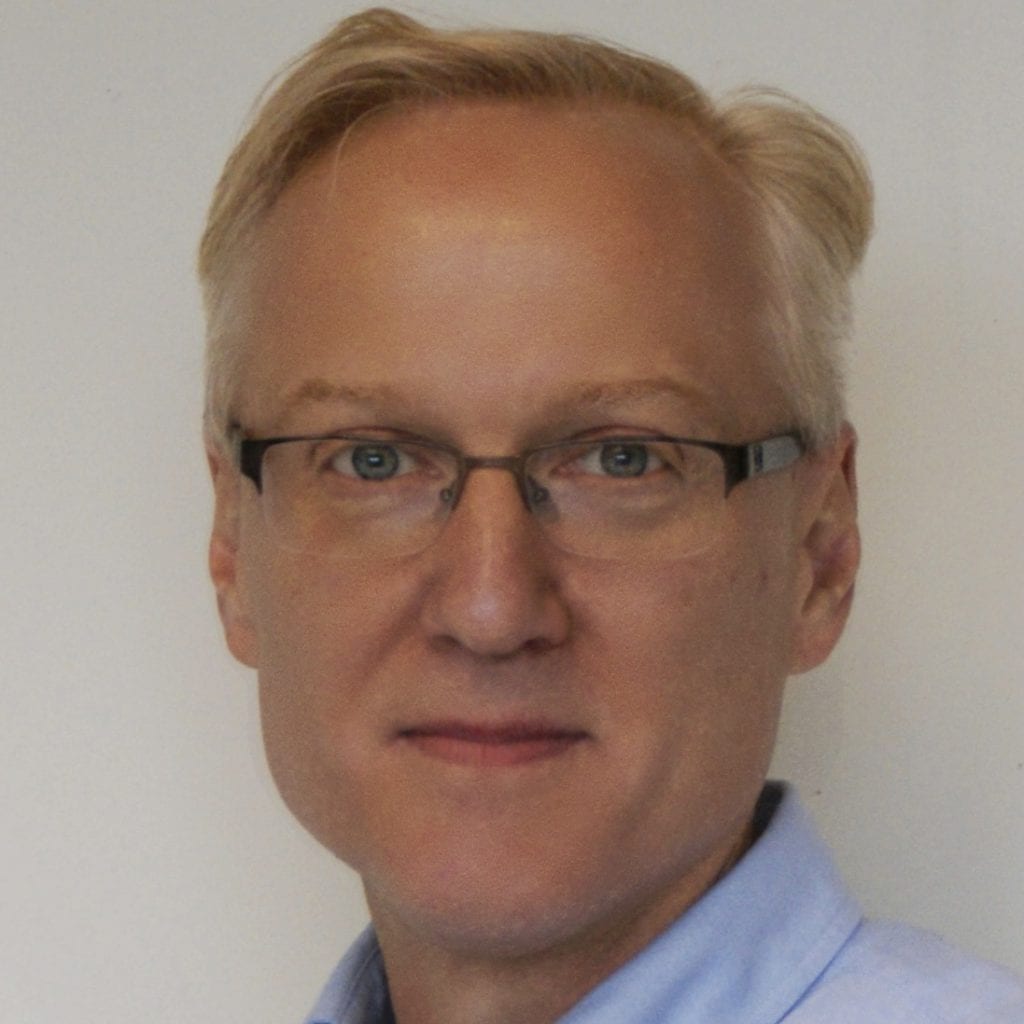
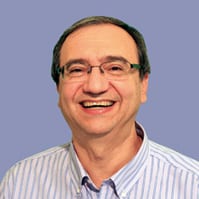
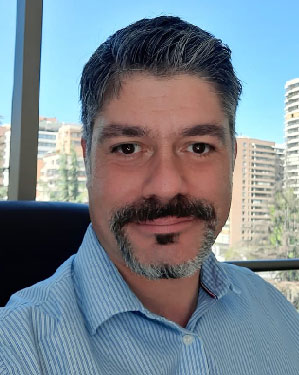
Read more
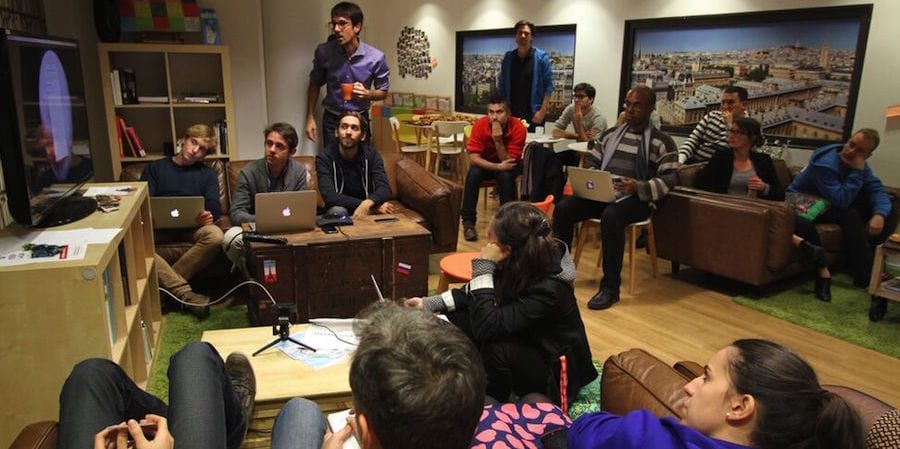
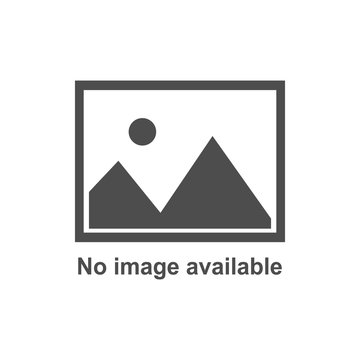
INTERVIEW – At the recent Lean IT Summit, Planet Lean spoke to BlaBlaCar, a Paris-based company that has managed to keep the startup way of thinking alive in the face of the hypergrowth it experienced in the past four years.
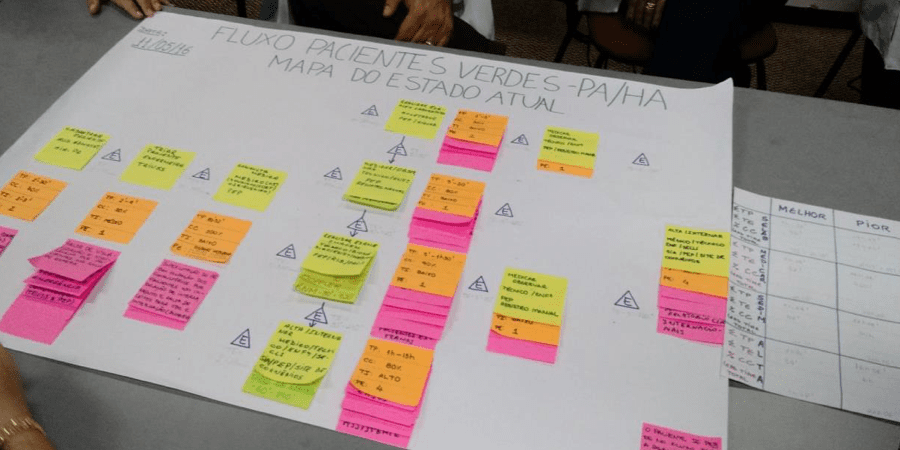
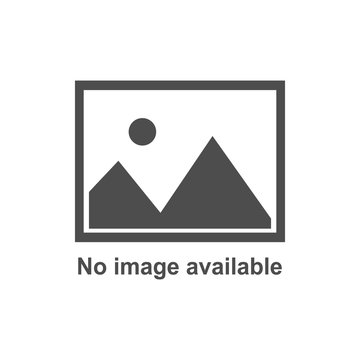
FEATURE – Long waiting times are bad for both patients and hospitals, but when we talk about heart attacks reducing them becomes a moral imperative. Here’s how Hospital Aliança in Brazil is doing it.
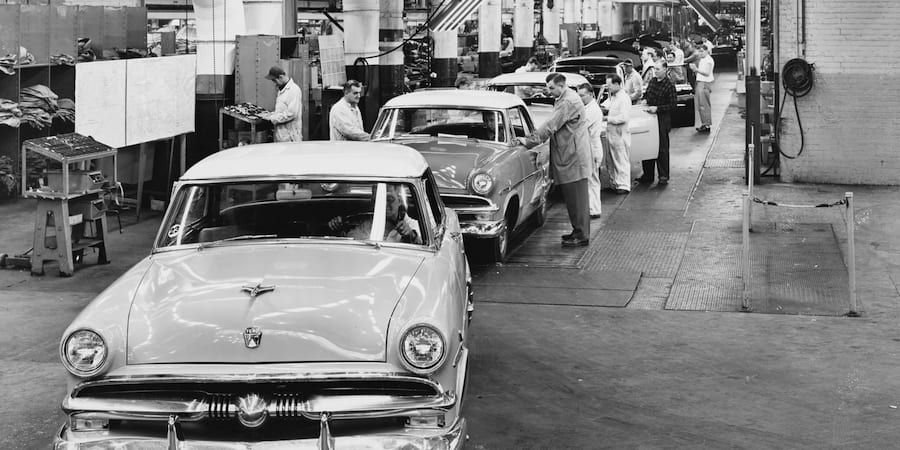
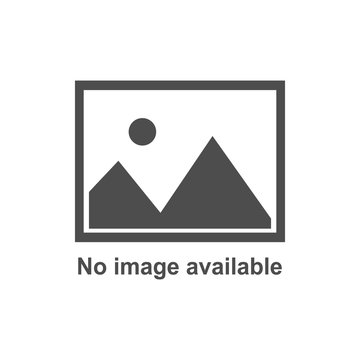
FEATURE – By offering an alternative approach to management, lean thinking has disrupted the business world in the past three decades. But in what way has it really innovated?
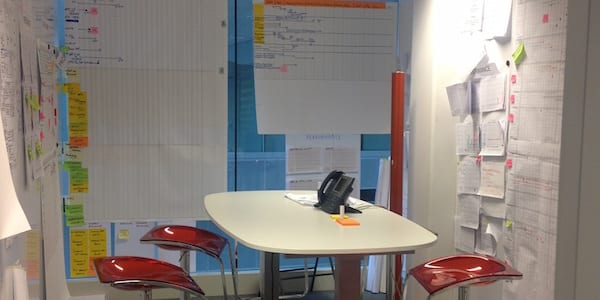
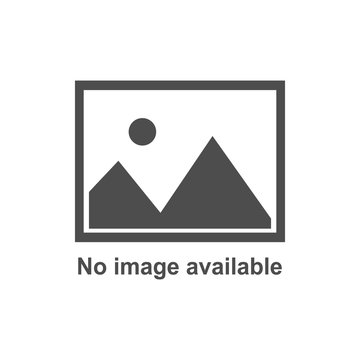
INTERVIEW – The CIO of a French pharmaceutical company gives us a sneak peek of her presentation at the upcoming Lean IT Summit, focused on using the obeya to change the IT department.