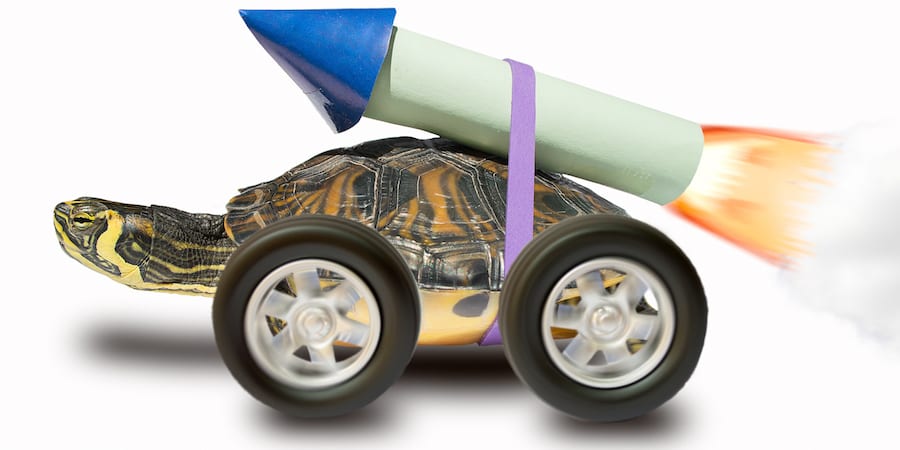
Jim Womack shares insights on how to help lean spread faster
WOMACK'S YOKOTEN – How it is that some ideas and innovations spread like wildfire while others are slower to take roots? It is clear that lean thinking belongs to the latter category, but how can we speed up its diffusion?
Words: Jim Womack, Founder and Senior Advisor, Lean Enterprise Institute
On October 16, 1846, at the Massachusetts General Hospital – as it happens, in line of sight across the Charles River from my desk at LEI – Dr. Henry Bigelow performed the world's first operation under anesthesia (using ether). His findings – that for the first time in history patients felt no pain during surgery – were published in a scientific journal in November and by June 1847 surgeons around the world were using ether. A fast idea.
By contrast, Edinburgh surgeon Joseph Lister discovered in the 1860s that the use of a disinfectant (carbolic acid) on instruments, sutures, and the surgeon's hands and garb, plus a fine spray of carbolic acid over the operating field, dramatically reduced the rate of surgical infections, which at that time killed about half of patients undergoing major surgery. He published his results in 1867 and within a few years... nothing happened. Indeed, it was more than 30 years before Lister's ideas were commonly adopted by the world's surgeons. A slow idea.
Atul Gawande's wonderful article, "Slow Ideas", published on The New Yorker of July 29, 2013, provides the details, and I urge you to read it. Gawande concludes that the difference in acceptance of these ideas was that anesthesia could be administered with quick results, with no discomfort to the surgeon and great comfort for the patient. "Listerism", by contrast, required surgeons to completely reorganize their activities and slow their rate of production (the number of procedures per unit of time) in order to change their instruments and clothes and even wash their hands (!) after every procedure. Most of them didn't believe that their practices were causing infections in the first place, given that these only emerged days after surgery. For Lister's methods to gain widespread acceptance surgeons eventually had to change their professional self-image from fearless sawbones in dark rubber smocks doing what had to be done in the midst of chaos to scientists in white gowns systematically trying new methods and measuring outcomes.
We have witnessed something similar with the spread of lean practices. Most of the tools in the lean toolkit – 5S, single-piece flow in cellular layouts, production to takt time, pull systems, rapid improvement events – were fully developed by the 1960s at Toyota in Japan and were being widely deployed outside of Toyota in kaizen events across the world by the late-1970s. That's still a case of slow ideas compared to anesthesia. But lean management methods – notably hoshin planning to gain agreement on the important problems to tackle, A3 analysis to deploy on important initiatives, and rigorous daily management to stabilize every value-creating process so that kaizen results can be sustained – were also fully developed at Toyota by the mid-1960s yet are only being applied widely with sustainable success 50 years after their first application. A case of very slow ideas compared even with Lister's countermeasure for infection.
In the lean case the situation has actually been worse because lean tools and lean management are linked – unlike anesthesia and sterilization. We now know that the fast-to-spread lean tools don't produce sustainable results without the organizational context created by the slow-to-spread lean management. It's small wonder that many in our Lean Community feel frustration with our progress.
To think creatively about this problem, we need to begin by asking about the factors determining the ease or difficulty of spreading ideas in organizations. In general, we know that ideas that do not disrupt organizational structures or routines, that require little practice to master (e.g., new technologies that simply need to be plugged in), that can be implemented by experts (often consultants) as line managers watch, and that produce dramatic, instantaneous results are relatively easy. High-speed kaizen – the fabled four- or five-day blitz – led by experts and producing instant payback on effort and expense is a perfect case.
By contrast, ideas that require the rethinking of organizational structures, that need practice to master, that must be implemented and sustained by line managers busy dealing with constant disruptions, and that produce results only over an extended period, are hard and likely to be slow to gain acceptance. Lean management, which requires managers not only to change their methods but to change their fundamental ideas about what managers do (e.g., give orders and measure results with KPIs vs. ask questions and enable workers to be more successful by removing barriers), is surely not the hardest idea ever diffused but it is certainly plenty hard. Hence our steady but very slow progress.
What can we do with these insights? How can we change our thinking to increase the velocity of our ideas?
First, we can get out of denial by admitting that lean tools alone cannot produce sustainable results. I recently witnessed a great example of this change in mindset at a company where I accompanied the CEO on a gemba walk to see the results of a large kaizen campaign designed and led by consultants and supported by a large internal operational excellence group. In the course of the walk it became apparent that the front-line workers were willing to work in new ways but that the modern management system did not facilitate or sustain the new practices. The evidence of backsliding was clearly evident, both to the eye and on the daily production board.
The CEO asked the leader of the internal operational excellence group what needed to be done and got the answer that the number of kaizen activities needed to be dramatically increased. He then asked the mindset-changing question: "Are we simply doing – and re-doing – kaizen on top of chaos? And, if so, why would we expect a better result with more kaizen?" After a long pause, one of the line managers suggested that maybe their time would be better spent creating basic stability through rigorous daily management (which they were just embarking on) before doing more kaizen. The CEO then wrapped up the discussion by asking how they could conduct an experiment on the hypothesis that rigorous daily management would make sustainable kaizen possible. I wish I went on more walks with this result!
Second, we can rethink the role of lean consultants, external and internal. Going all the way back to Frederick Taylor and "scientific management", there has been a belief that process improvement is done to front-line workers, usually by consultants or staff experts with superior knowledge, and without much need for managers at all. Hence, the big operational-excellence focus of recent years. But going down this path means two things in practice: Line managers believe they can't improve processes themselves by coaching their teams. And they feel certain they don't have time to coach even if they know how, because all their time goes to managing exceptions generated by unstable processes. So they try to outsource their problems to consultants, who are happy to help because kaizen on top of chaos produces steady repeat business!
In my experience the most productive role for consultants is to help create line managers who can establish stable processes through rigorous daily management. And they should do this before they focus on helping managers improve every process from the current baseline. This path inherently shows slower results than just fixing problems right now, but it creates the stability and line responsibility that can sustain improvement in the long term.
Third, we can stop thinking that a lean management system can be put in place in the same time frame as lean tools through kaizen – in other words as another fast program. This is because new management methods and mindsets need repeated coaching (in my experience as a manager, a very large amount of coaching!) in order to become second nature. Thus, coaching line managers is a continuing practice, not a one-time event. Given this fact, higher-level managers need to be patient, while asking questions about the coaching process for their managers rather than focusing on short-term improvement results.
Fourth, we can stop discouraging ourselves by obsessing about the simple fact that most of us – CEOs, internal consultants, line managers, even lean columnists – don't know exactly how to introduce lean management in our organizations and that there aren't enough external sensei with the right skills to teach us. The most fundamental activity – in fact, the whole point of lean thinking – is to run experiments. (We call it PDCA.) We are used to running them on value-creating processes. Many readers do this every week. Now we need to run them on management processes by trying different things and coaching each other. We need to grasp the current situation of our management processes (in particular with regards to creating the basic stability that makes kaizen sustainable), try new management methods, see what works to stabilize operations and enable improvement, share insights in order to make adjustments, and try more new methods, all in a conscious, systematic manner with everyone observing everyone's successes and set-backs.
The good news: If we can act on these insights as a Lean Community I'm confident that the diffusion of lean ideas going forward can be more like instant ether and less like slow-acting carbolic acid.
THE AUTHOR
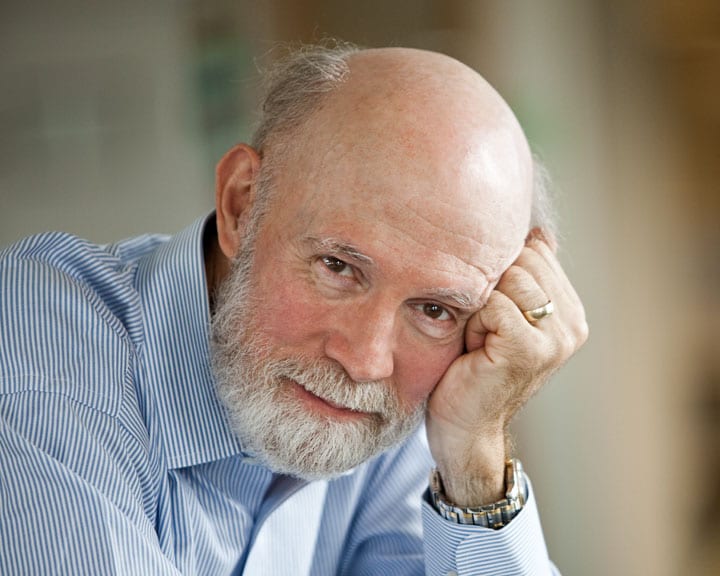
Read more
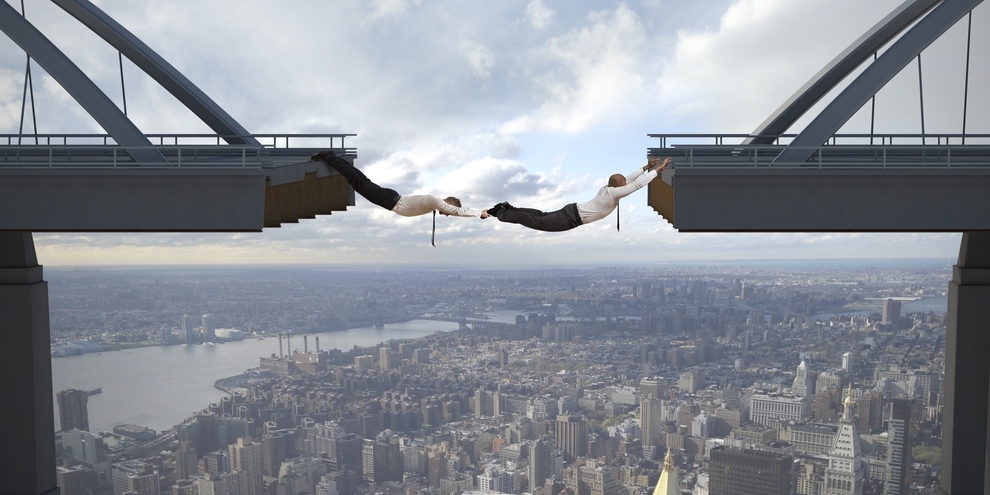
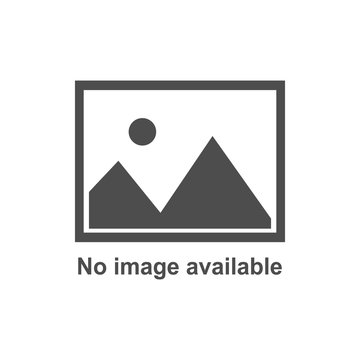
FEATURE – What is the role of middle managers in a transformation and how can we ensure they can fulfil that role – instead of being blamed for the failure of the initiative and even excluded from it?
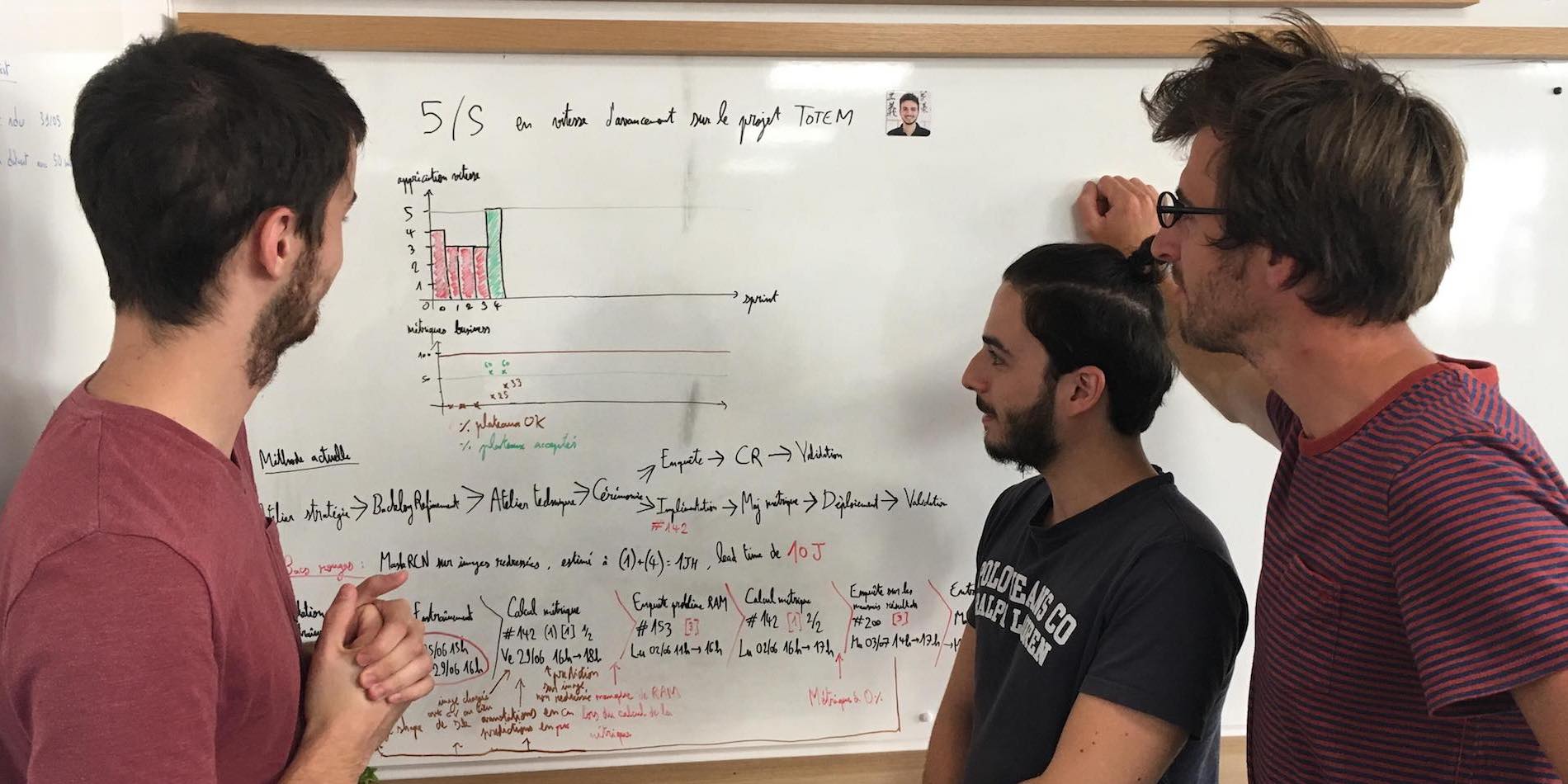
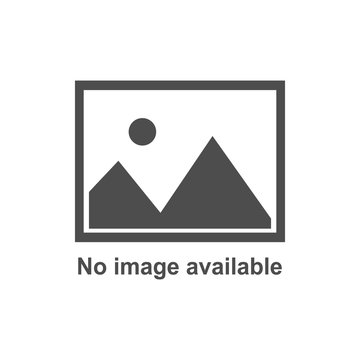
BUILDING BRIDGES - This month, we hear how addressing work-in-progress led a startup specialized in AI to productivity gains on their machine learning projects.
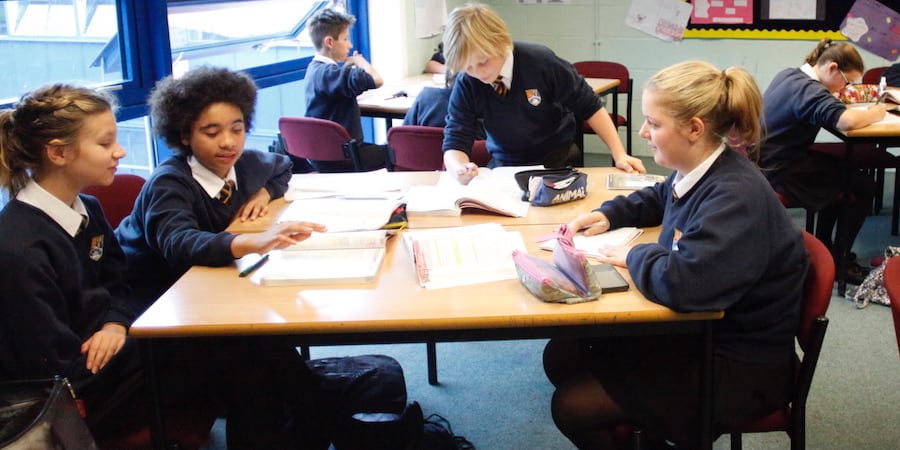
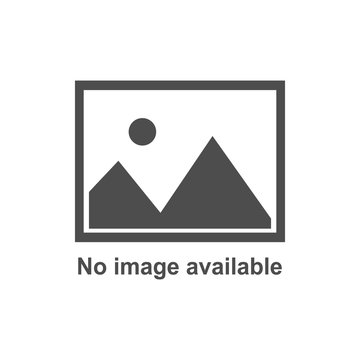
INTERVIEW – Christleton Learning Trust in the UK is running several lean experiments across its three schools. We spoke with its CEO, who told us how coaching is supporting the transformation.
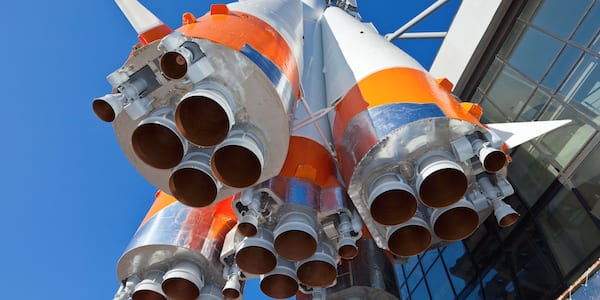
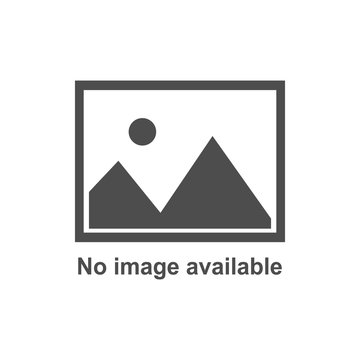
FEATURE - What do Toyota and Procter&Gamble have in common? A passion for developing people, a focus on customer satisfaction, and... enviable results that are sustained over time.