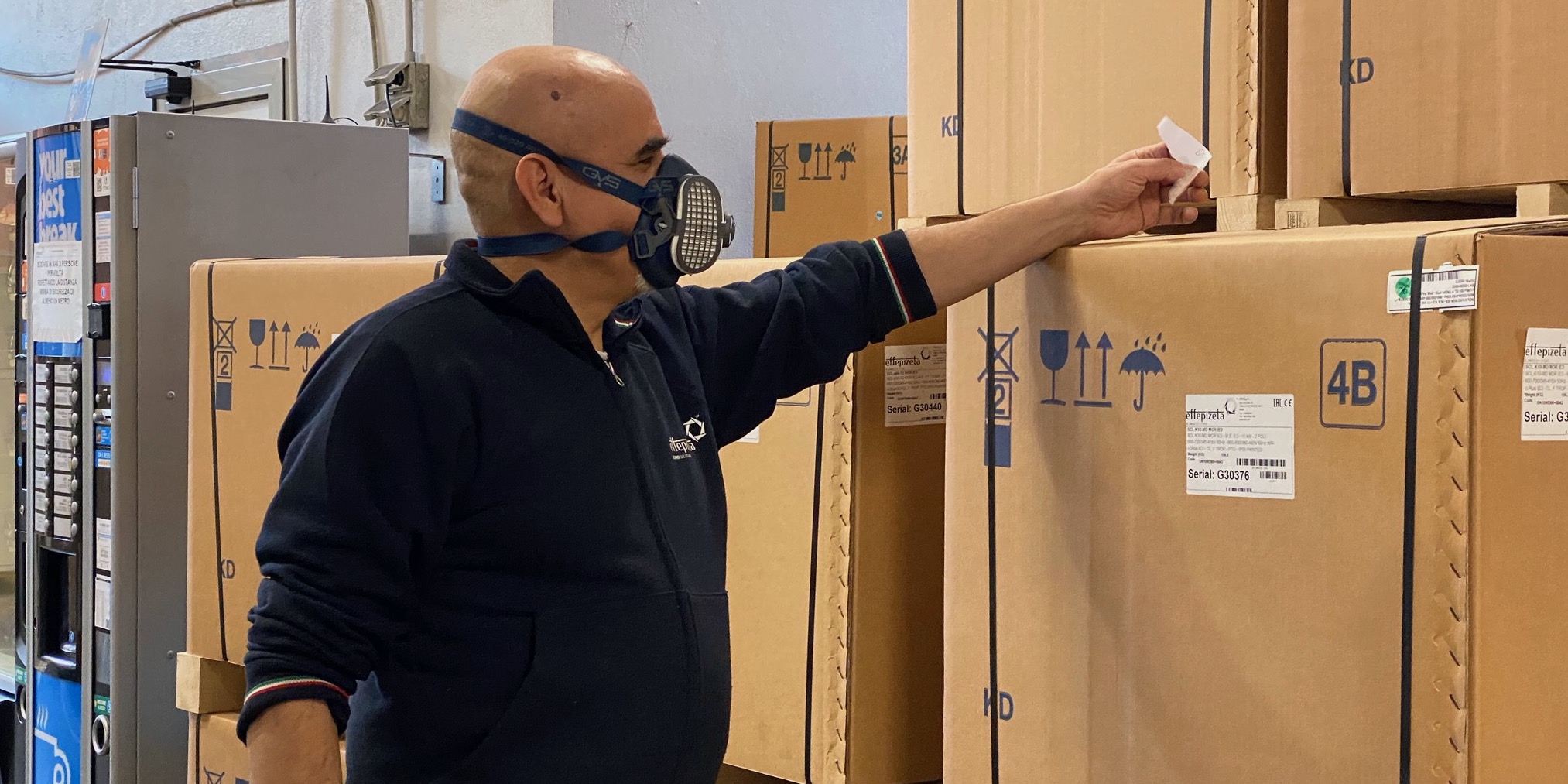
Immunity
CASE STUDY – This Italian manufacturer has found in lean a way to ensure business continuity and provide support to a distraught workforce in the midst of the coronavirus outbreak.
Words: Sergio Ferigo, Gianni Lorenzani and Matteo Consagra
Extra support and information provided by: Paolo Mauro, Susanna Cecchi, Georgiana Ceausu, Andrea Lazari and Mauro Mantovanelli.
On February 21st, the first case of Covid-19 in Italy was discovered in Codogno, in the province of Lodi – some 70 kilometers from where we are. We all know what happened since then, in Italy and in the rest of the world. Within days, our lives have changed beyond recognition and we are not sure for how long.
In the article he published on Monday on Planet Lean, Michael Ballé reminded us that in the face of a crisis, one can react in two ways: with a fixed mindset or with a growth mindset. At FPZ, we have chosen the latter. In this crisis, we have chosen to continue learning and improving; we have chosen business continuity; in a word, we have chosen to fight.
We realize we have a duty to fulfill, as a key element in an important supply chain. The components we produce are used in industrial automation, for dosing substances in chemical, pharmaceutical and food processes, in ventilation systems, industrial cleaning, and so on. Without products like ours, making staple goods would become difficult and eventually impossible.
We are very much aware of our role in this health crisis. If healthcare workers are on the front line and those providing services – like distributing food and drugs – are on the second line, we are contributing to this collective effort from the sidelines. It’s this awareness that encourages us to allow our company and the people working in it to continue to operate, in full safety of course.
The flexibility afforded to us by our lean culture, our commitment to problem solving and our determination to always have a contingency plan ready for our critical resources enabled us to quickly communicate with our key suppliers and enable internal measures aiming to ensure continuity in production. What is lean management if not structured problem solving to always satisfy customers while minimizing waste? In this sense, business continuity allows us to keep on delighting our external customers without interruptions, while providing our internal ones with the necessary direction at a time of painful uncertainty. Since this crisis began, the quality of our working life has remained as high as the level of service we provide to our customers.
We never could have imagined having to deal with a situation like this, not even within our emergency plans. However, our work to develop managers and front-line staff, which is based on the belief that it comes down to every individual to ensure the safety of the system, has made everyone at FPZ ready to act swiftly and intelligently – moving the business in the direction outlined by the World Health Organization and the Italian government.
OUR RESPONSE
The day after the first Covid-19 case in Italy was announced, we created a Safety Committee on WhatsApp to coordinate our response. It was a Saturday and, by Monday, the first measures were already in place. These included allowing people to only drink water from a bottle or using disposable cups, cancelling our business trips and participation in fairs (those that were not cancelled), suspending all visits, and giving sick leave to those employees with preexisting conditions making them particularly vulnerable to the virus.
We leveraged the great adaptability of our IT system to equip people with the tools they need to effectively work from home – be it access to company servers or phone lines – and to keep them connected and aware of the progress of all activities. Two years ago, we implemented new standards in our IT Department to enable any workstation at FPZ to convert into a remote working space through any interface (PC, a laptop or a smartphone). When the Covid-19 crisis began, therefore, all we had to do was roll out the protocol: on Monday, February 24th, 65% of our office staff were already working from home (now it is 90%). For the past three weeks, we have seen no negative impact on our service to customers – which has been our focus since the very beginning.
Unable to visit clients, the Sales and Marketing Department is using this time to work on the company’s image and plan for the moment things go back to normal. They, too, have been smart working since day one of this crisis, and immediately found their feet: at least once a day, they have an alignment call and the quality of their work is as high as ever. They have also completed activities that had been work-in-progress for a while and started projects they never had time to kick off.
At a time like this, reaching everyone within FPZ is critical, which is we have been working hard to boost our internal communications – especially using videoconferencing, the company social network, and cloud services. We created several WhatsApp groups, with maximum six participants each, to share relevant information. People are also encouraged to share light-hearted content, like the thousands of memes circulating on the internet these days, but we ask them not to do it in these groups. It’s important to distinguish what’s serious and what’s fun.
Unable to meet face to face, we have found different ways to feel close to one another in these strange times and give people a voice. For example, we are creating short videos showing how each of us are dealing with the current working arrangements and the country’s lockdown. Here’s an example:
And check out this tutorial we use to teach people how to use videoconferencing tools [starring Sergio’s children].
To guarantee continuity of supply, we are also utilizing some of our extra capacity to produce standard products that we transfer to a number of warehouses located outside of the Lombardy region (Italy’s most affected in this emergency).
As soon as the coronavirus appeared in Italy, we started tracking the state of each supplier and opened emergency channels of communication with the most critical ones. We think it’s important to share best practices with them and ensure they too implement all the safety measures necessary to continue operating.
Other companies in the FPZ group have also been taking on the measures established by the Safety Committee – like extra cleaning and sanitation (see below). Day after day, every business in our group adapts to the new restrictions introduced by the Committee or, nationwide, by the government. In the mother company, in Arivent (our industrial fans company) as well as Doseuro (our metering pump company), the teams have prepared a Risk Assessment document. All our companies are mapping the situation of their key suppliers to know who’s scaled down production, who’s working at a normal pace, and who’s shut down.
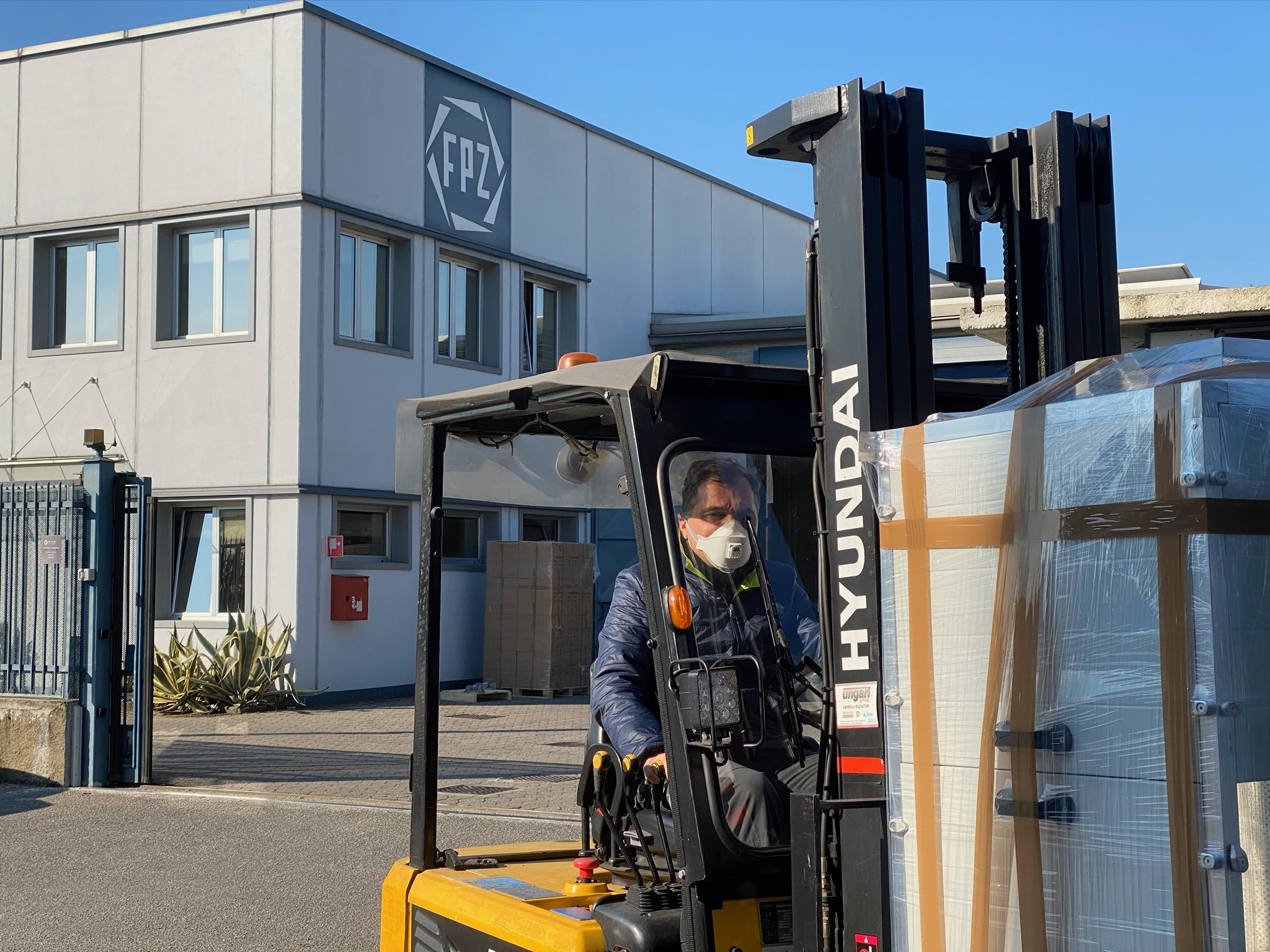
SAFETY ALWAYS COMES FIRST
Effectively managing safety depends on how well we can predict the risk. In our globalized world, it was inevitable that the Covid-19 would not simply remain confined to China. This means that, when the news came that the area around Codogno had been quarantined, our safety measures had already been prepared. It was just a matter of applying them. To not be caught unprepared, forecasting is key – coupled with an ability to “read” external dynamics and internal requirements.
The speed in our response was a result of the FPZ team’s extraordinary ability to work together to find solutions to a common problem. Our people are used to openly giving their contribution to the improvement of the business.
The aggressiveness of this virus and the experience of the Chinese people had already taught us that the only way to effectively stop or at least slow down the spread of Covid-19 would be to physically keep people apart. We’d have to avoid any contact between workers, but at the same time had to ensure this information was communicated in the right way.
So, we took all the necessary measures to reduce the risk of infection from day one. On the production floor, we have compartmentalized working groups to eliminate contact between people in different areas of the production floor. We have two sites (one opposite the other) that are almost completely separate at the moment: only two warehouse workers are allowed to enter both, wearing an FFP2 mask. To further limit the chances of interaction, we have physically separated the assembly and finishing areas. The new organization of the space has already taught us something new: the importance of only transferring critical information from one area to another and of better synchronizing communication among different areas.
Only three operators at a time can enter the changing room, to ensure they can keep the recommended safety distance of one meter and to prevent potentially infected individuals (who might not present any symptoms) from passing the virus on to their colleagues. From day one of this crisis, we have doubled the times the changing rooms are cleaned and sanitized, because every shift has a right to a clean and virus-free environment.
We have taken measures in our break room, as well. Here, too, no more than three people at a time can go in and they must maintain the safety distance at all times. To make this possible and avoid overcrowding and lines by the coffee machines, we have arranged for different break times throughout the day. We have also reviewed our schedule and shifts to give most of our operators the opportunity to have lunch at home with their partners and kids (schools are closed in Italy at the moment). We have also been able to order enough masks – we are not sure of when we’ll receive them, yet – for our people to bring home to their families.
We also sanitize all equipment, measuring instruments and machine tools after every use and at the end of the shift – to ensure everyone can work in safety. Operators regularly disinfect keypads, too. People are even more aware than before of the need to care for the equipment they share with their colleagues.
As the situation continues to evolve, we are learning to be patient and how important it is to continuously invest in the education of our people in the face of this threat.
WE CARE FOR EACH OTHER
We are touched by the strength and determination that our people are showing, and we are committed to doing everything in our power to continue to protect them as they perform their jobs. Most of them are doing fine, but some – understandably – are feeling anxious and stressed out.
They might live alone and be struggling to cope with the social isolation; or they might have family far away or vulnerable relatives. Sadly, one of ours has suffered the loss of an uncle. We strive to help everyone in need through dialogue and psychological support provided by our in-house counselor Aldo Terracciano via video sessions (he’s worked with us for a long time and people trust him).
In many ways, this emergency is bringing out the best in our people. A few people have told me they feel privileged to be able to leave the house and come to work, because it’s hard to kill time at home and watching the news only generates more stress in them. This is the right spirit, which we commend. Even more commendable are those FPZ workers who are working from home while caring for their children.
We find that looking to the future with a common goal is a great morale boost, and that there is value in treating this situation like another challenge we can learn from: rather than simply putting up with what’s happening, our people are finding comfort in working to increase safety at work or to guarantee continuity in production.
Until now, FPZ hasn’t seen a drop in the number of orders. Even though we know this situation is bound to hit the whole economy pretty hard, we are not worried because we are in a solid financial situation and can swiftly react to changing circumstances. We will continue to monitor our KPIs and parameters and to adapt our production capacity to customer demand. In the past, before engaging the whole of FPZ in continuous improvement, we would have had no choice but to keep producing. Today we know that we generate value by producing, but also by improving, strengthening our processes and learning.
It’s inspiring to see how quickly our company has been able to act in this incredibly challenging situation, by making level-headed choices and coming up with shared countermeasures. In a way, we saw a perfect example of PDCA here, with every new government decree being absorbed into the FPZ ecosystem like a new adjustment in an improvement cycle.
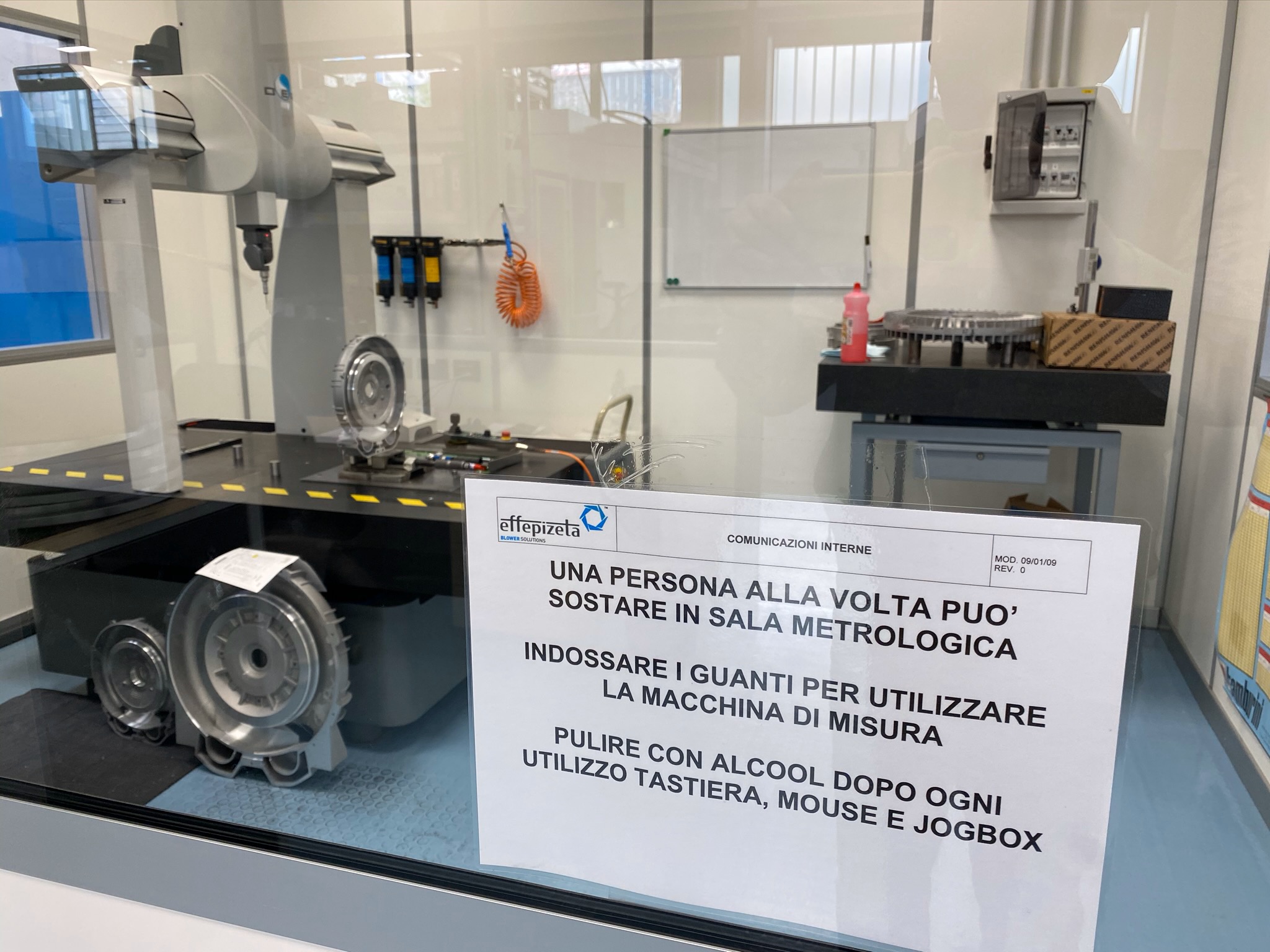
SOME OF THE THINGS WE LEARNED
We’d like to share with you some of the things we have learned over the past three weeks:
- The captain of the ship needs to be frank but positive, without belittling the risk. In these difficult times, we need to take care of the mood of our people more than ever.
- Humans are social beings and getting them to interiorize unpleasant, but necessary isolation measures has been hard. You can never stress them enough.
- You can never give people enough information, even on the behaviors they should follow when they come to work or leave to go home (avoid public transport and carpooling, etc).
- The message doesn’t always reach everyone in the same way. Despite our best effort, some colleagues continued to underestimate the threat of the virus.
- Whenever we involved people in the decision-making process (for instance on how to reorganize the shifts in production), we always saw active participation and experienced no resistance.
- When instability looms, the message going out to people has to be clear and impossible to misinterpret.
- Collaboration between departments and office is critical to help each other out in a difficult time.
- Always focus on the learning, because only by sharing and co-creating ideas can we achieve the personal growth of all those involved.
We want people at FPZ to follow us out of their own will, because they share our ideas and vision – not because they are afraid not to. In uncertain times like this, people need to be given safety on the job and job security, which are both key to their well-being. They need to know that our actions are meant to help them, always; and we management team need to understand that our legitimacy to lead them stems from our will to listen to their needs and our ability to reassure them.
Lean management has allowed us to succeed as a business so far, no matter the crisis we encountered. It’s made us resilient and adaptable, and it’s allowing us to respond to the coronavirus emergency quickly and effectively. It may look like the world is turning upside down, but things at FPZ are still remarkably business-as-usual – with just a little foresight and a few extra rules.
We believe that our company – and indeed, our country – will come out of this tragic chapter stronger than it ever was. As we Italians discover the air we breathe is cleaner, fall in love with the newly-found clearness of the Venice canals, and admire the beauty of a smog-free night sky, we are learning what’s perhaps the most important lesson of all: that we all share a common destiny. We are understanding the importance of belonging (to a community, a business, a family), of speaking the same language, of eliminating conflict by thinking about the whole rather than just ourselves.
THE AUTHORS
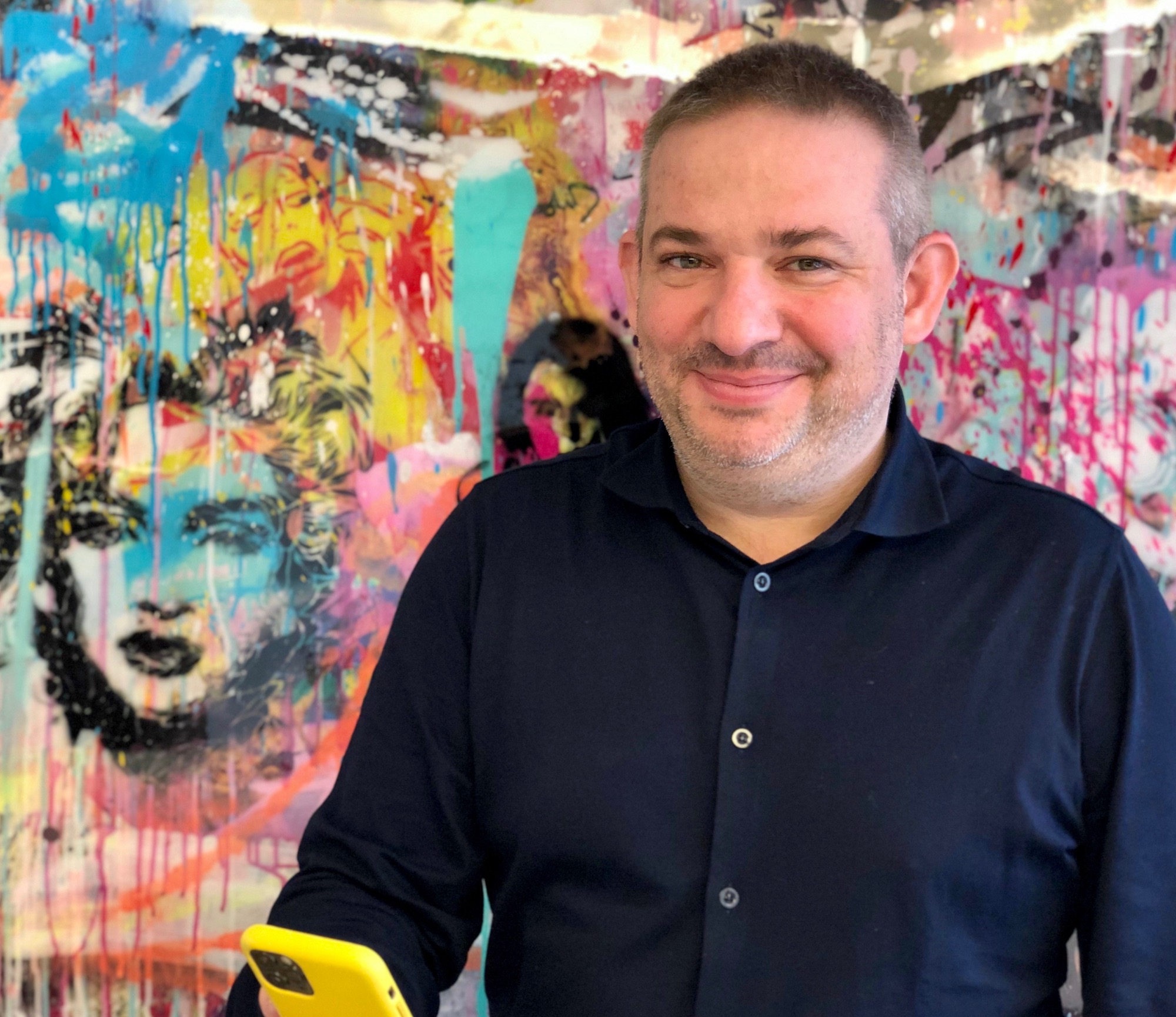
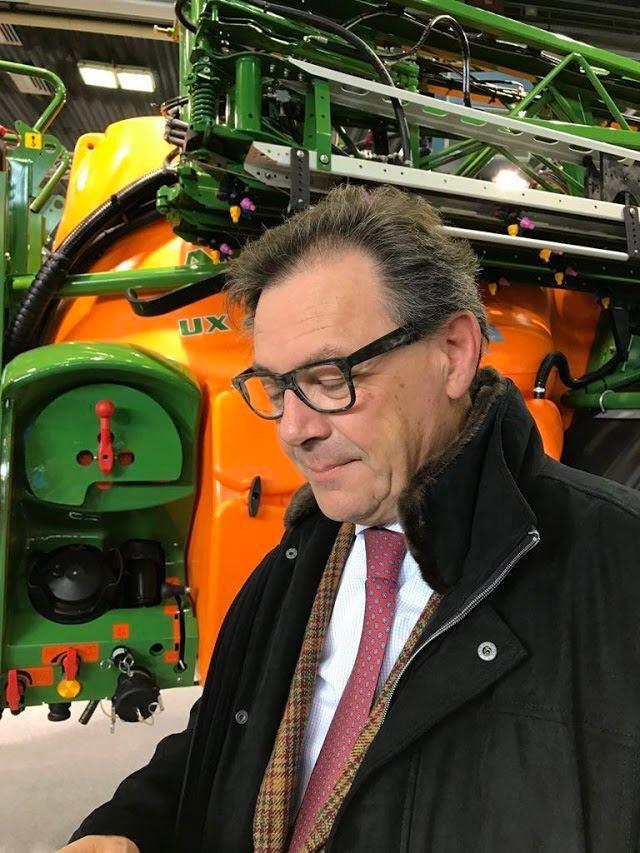
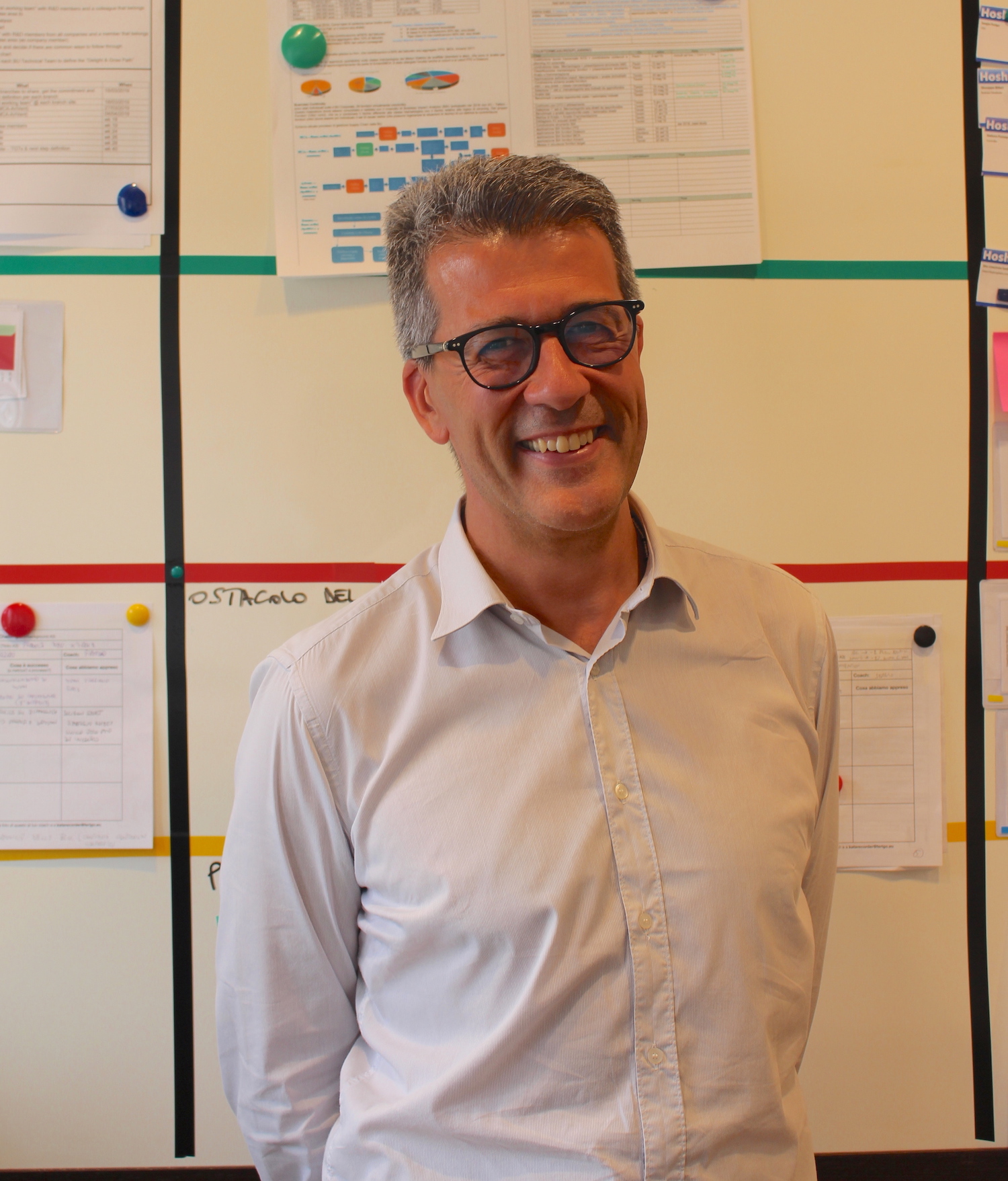
Read more
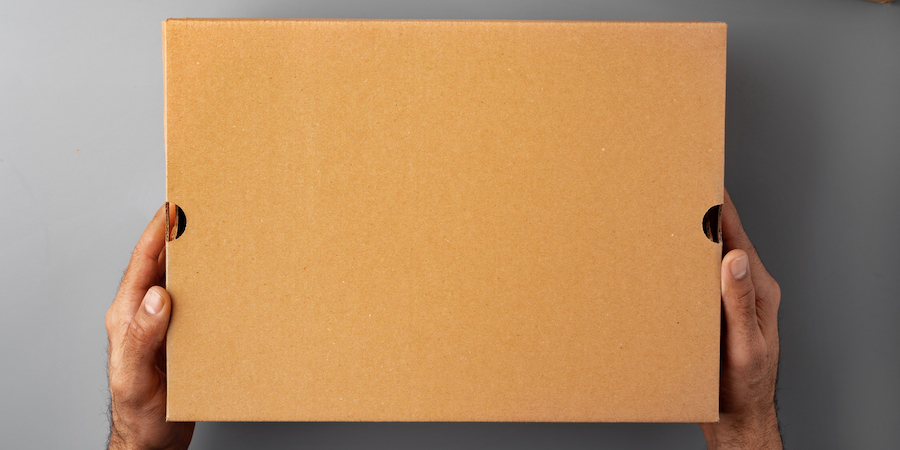
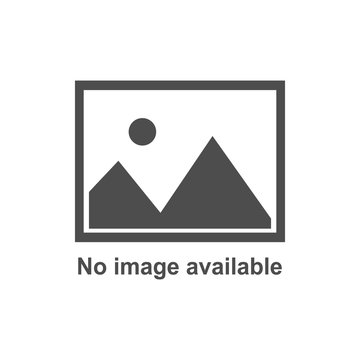
FEATURE – The author shares a story from a training session at the gemba, which contains a couple of important lessons on the Training Within Industry method.
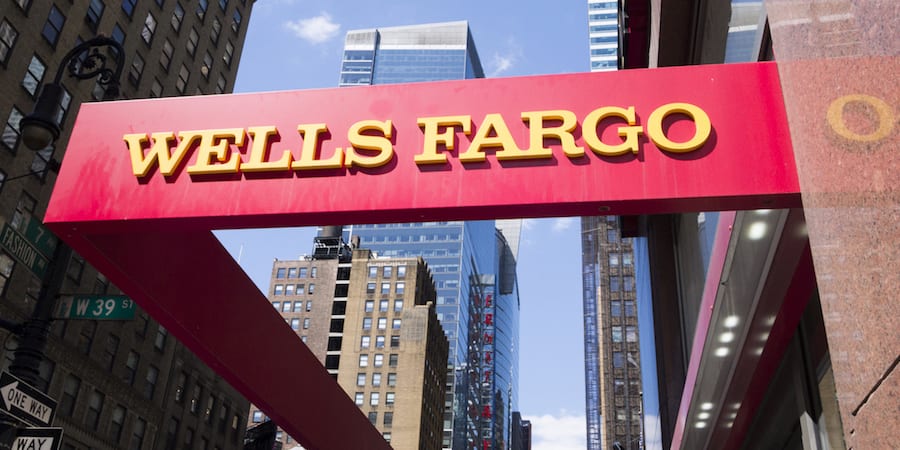
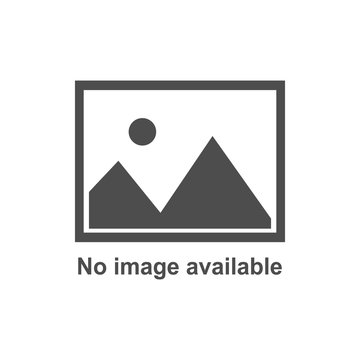
OPINION – The latest banking scandal had us all wonder whether Wells Fargo has lost its way. But how does a pioneering bank that once had lean at its heart betray its core values so profoundly?
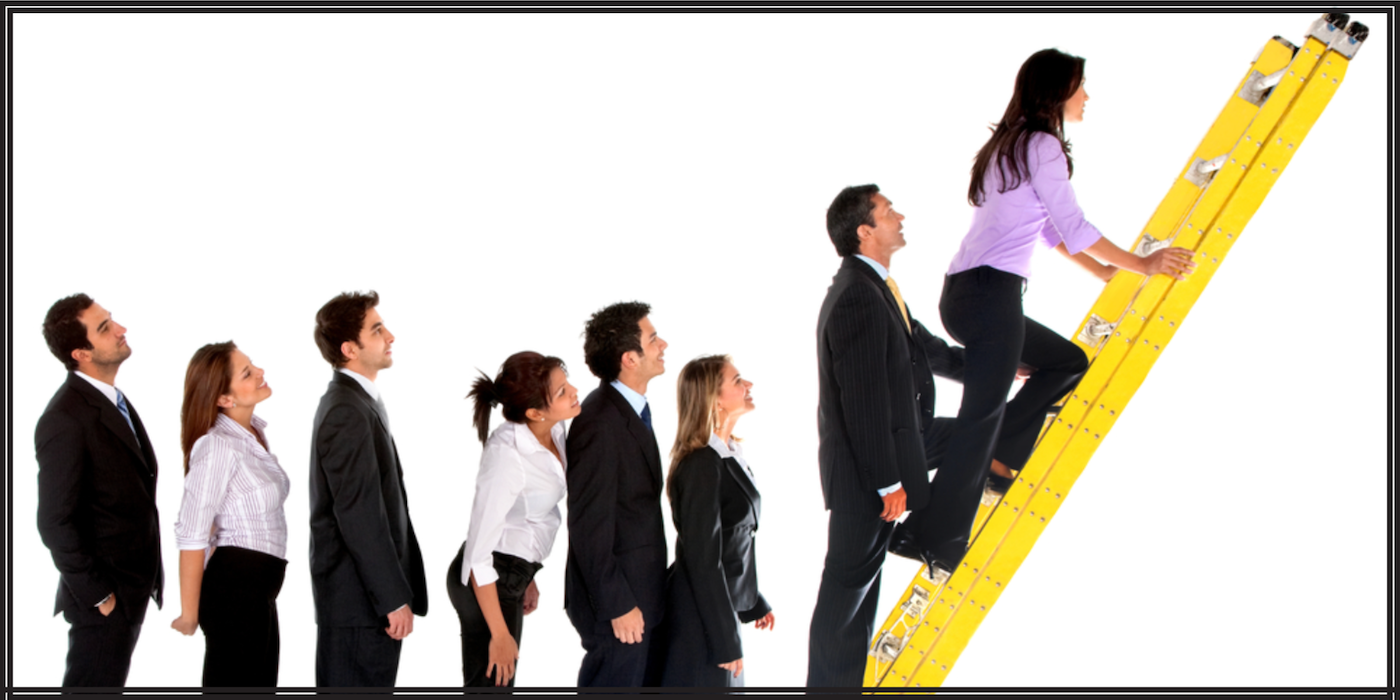
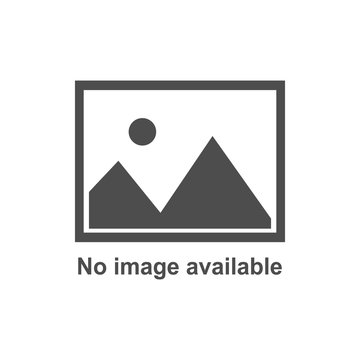
FEATURE – If you think one is born a leader, think again. Leadership can be learned and, in this article, the author provides a four-step guide to developing it.
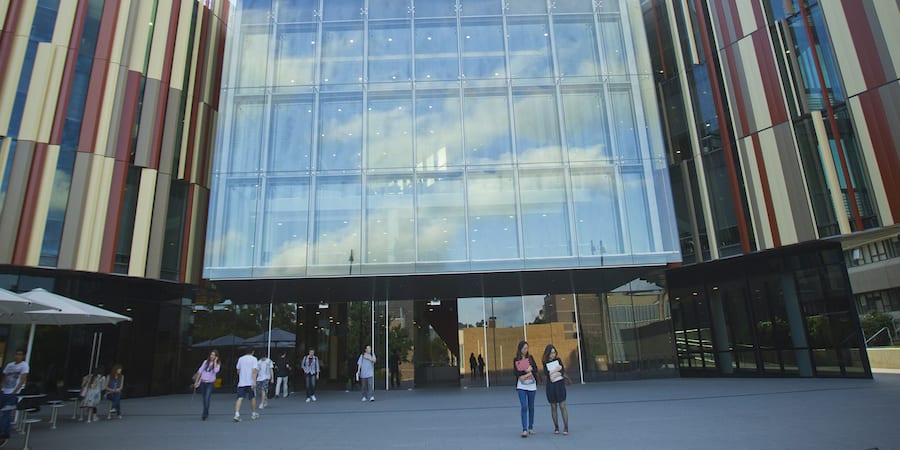
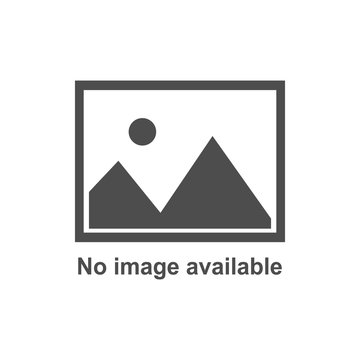
CASE STUDY – An Australian university has been applying lean to streamline and improve its processes, discovering along the way how big a change the methodology can affect in the organization's culture.