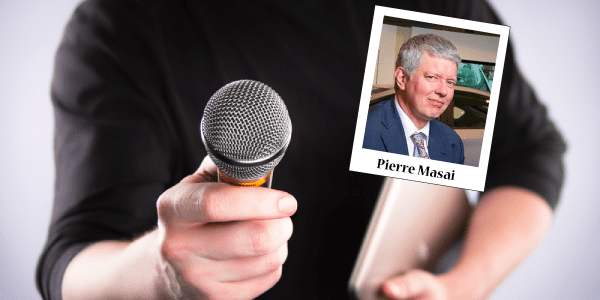
How Toyota integrates IT across its European operations
INTERVIEW - Pierre Masai, CIO of Toyota Motor Europe, discusses IT across the company's operations in Europe, highlighting the importance of people engagement and experiments.
Interviewee: Pierre Masai, CIO, Toyota Motor Europe
Planet Lean: The market that Toyota Motor Europe serves is extremely diverse – how does IT help you to tackle this challenge?
Pierre Masai: What I have been doing since joining the company nine years ago is to gradually build pan-European IT with groups of IT that were already in place around the continent.
Even before I got here, we had started with manufacturing, bringing together IT in different factories. We began in the UK. Then the headquarters for manufacturing moved to Brussels, where we had a European IT and Sales IT, which we merged in 2007.
I then started to bring TPS principles from manufacturing IT to sales IT. We recently started to integrate the IT of National Marketing and Sales companies.
We also have a number of smaller IT functions in different countries. They work closer to the gemba and to the customer. Two of these lean I.T.s are in France and Spain, where I moved somebody from my team. There needs to be a direct hierarchical responsibility to ensure my input is not required at all times. So I put somebody in those two countries who knows the process very well and who can pull help from me when needed.
Once we have completed the process for UK and Germany, we will decide whether to integrate other teams further.
PL: Why do you think it is so difficult to make lean and IT work together sometimes?
PM: One of the reasons is that in lean we explain that IT comes at the very end, and if you work in I.T. you probably don’t like to hear that. But if your main focus is lean rather than IT, it’s easier to integrate the two. Too often people are only interested in the technology and the tools.
PL: What is the purpose of the European IT Kaizen Meeting?
PM: There are different purposes actually. For our employees, whose relentless work on improving is quite invisible to senior management, the meeting represents an opportunity to show their activities to the European president. He in turn engages with them and gives his comments.
But there is also a component of development for the managers, who have to learn to put people on the fore rather than themselves.
The whole meeting happens at the gemba, except for a short “setting the scene” meeting at the beginning and a few closing comments at the end, after shop floor observation. This is another way to put people who do the work in the spotlight. Senior managers are expected to make comments on what they see. It’s a different type of development, which raises the level of motivation.
In short, the European IT Kaizen Meeting helps in terms of alignment, professional development and engagement.
PL: Would you say that what sets Toyota’s IT apart is the fact that the organization has a strong focus on trialing before the development phase begins?
PM: Absolutely. We don’t always do it properly, and when we don’t we generally fail, which is a great learning. We have very different business units, some more experienced than others: my guys may feel under pressure, but looking at what others are doing and doing tests really helps (no matter how difficult it might be to do it).
There is always a way to carry out a trial, maybe just with three customers. If you cannot think of a way to do a trial, you probably shouldn’t be developing a system.
PL: This calls for a question about the lean startup movement. What do you think of its principles?
PM: A former employee of my team decided to start her own company and she of course applied TPS principles to it before realizing there was actually a movement called the lean startup. Without a doubt, their principles and ours go hand in hand.
THE INTERVIEWEE
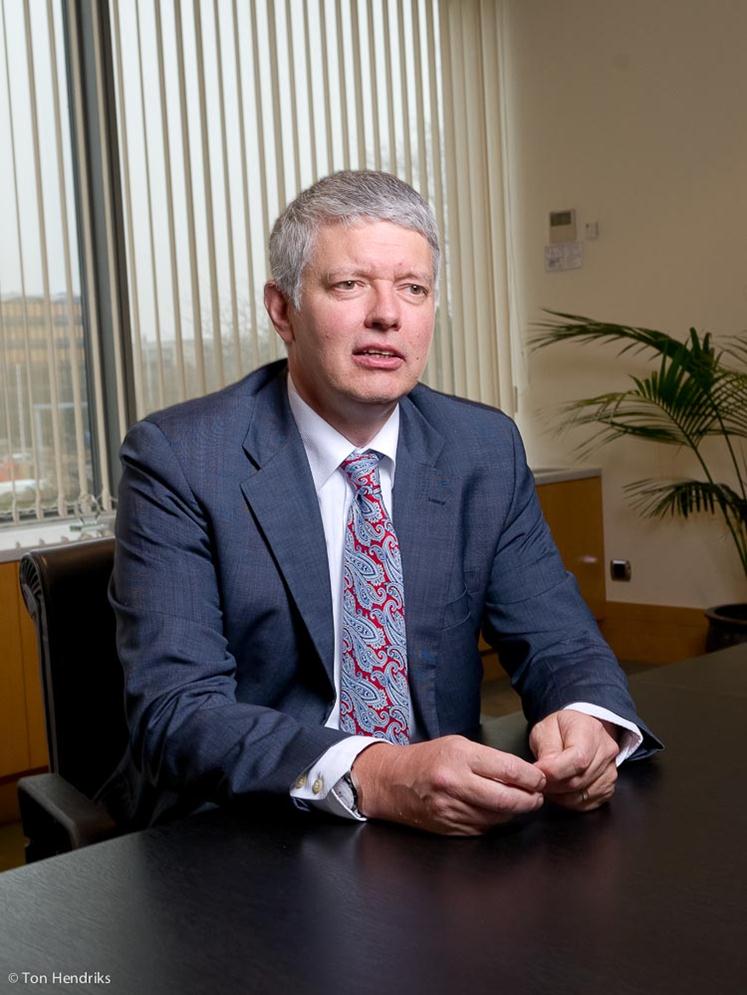
Read more
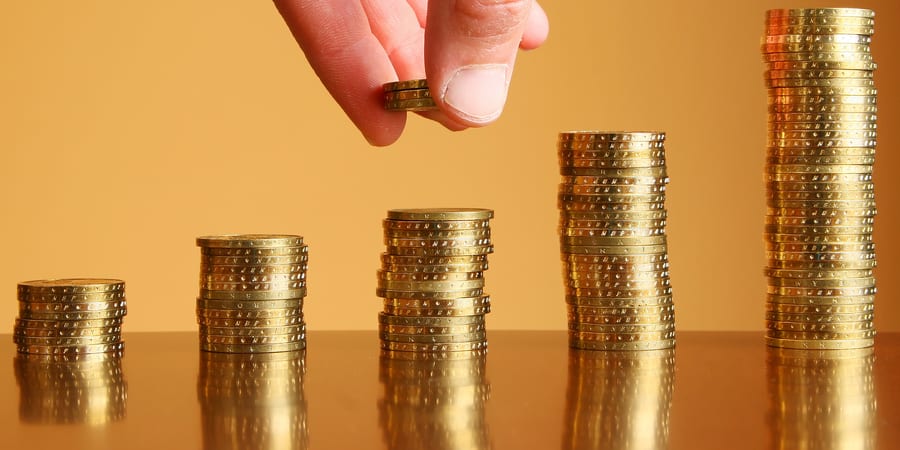
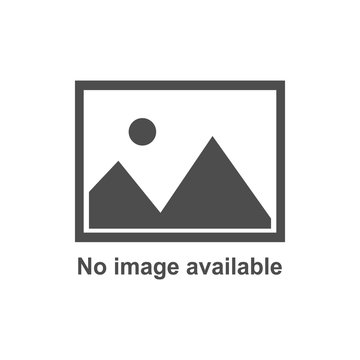
RESEARCH – What kind of financial results can a SME owner expect from a lean transformation? To find out, the author of this interesting research analyzed the performance of 100 Italian small and medium-sized companies.
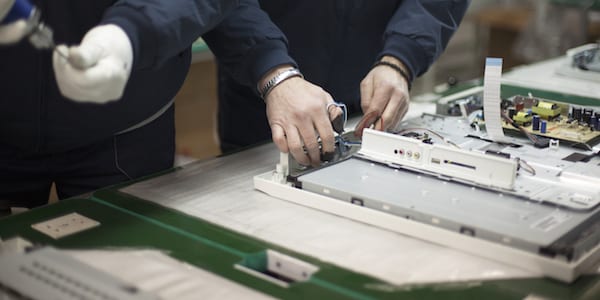
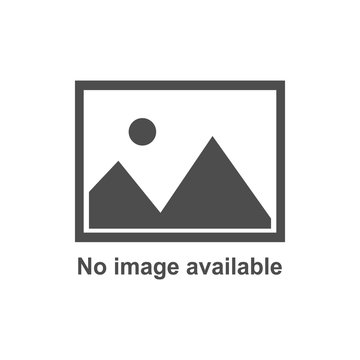
ARTICLE - We always talk about going to the gemba, but we often don't understand what that entails and what changes it can bring to our companies. In this article, we hear about the experience of Thales.
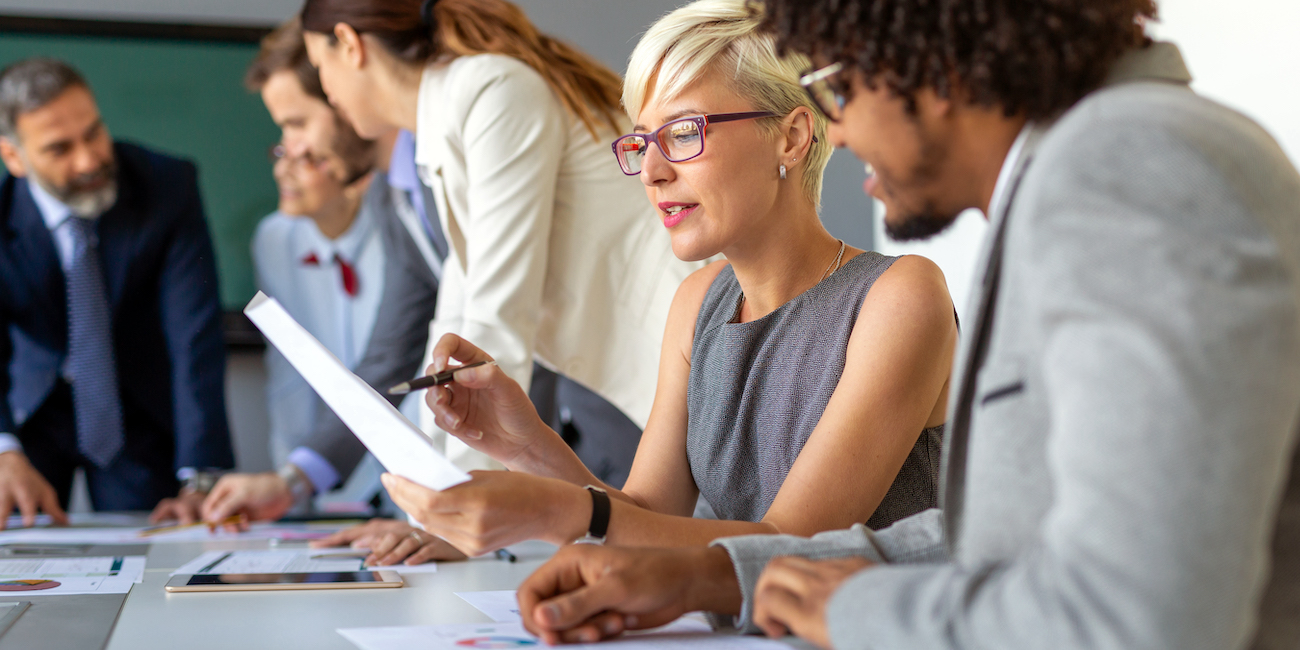
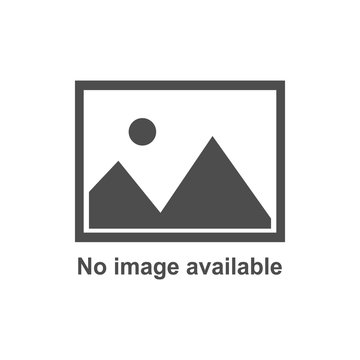
FEATURE – Variety in sensei approaches can cause a lot of confusion. The author sheds light on the subject by describing a sensei’s five modes of interacting with individuals and teams.
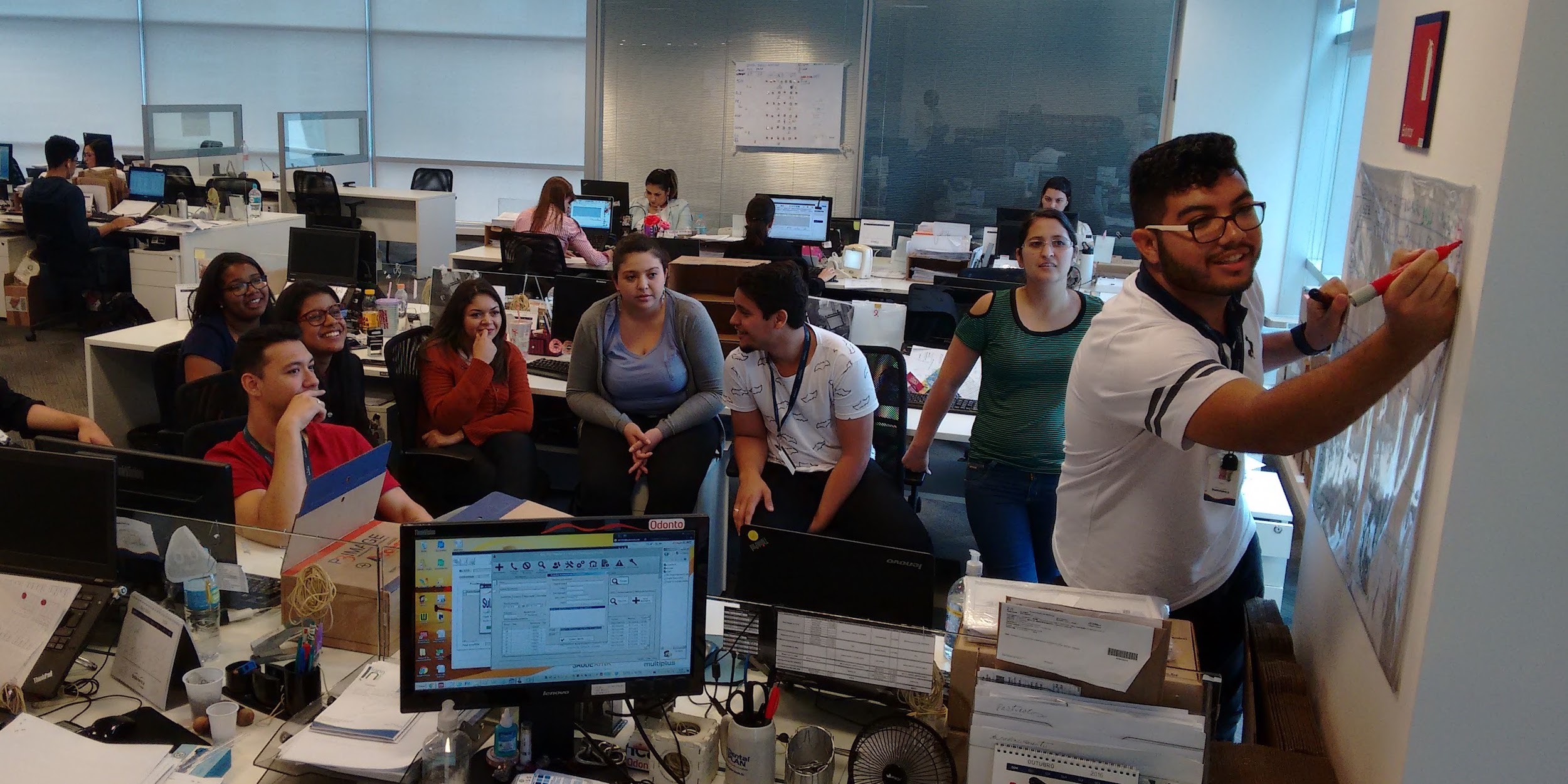
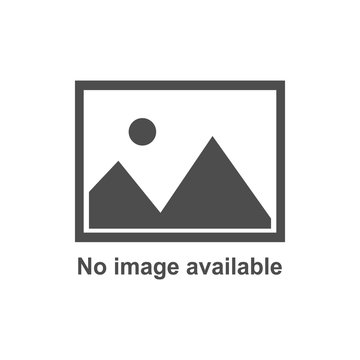
CASE STUDY – In a Brazilian insurance company, a team worked hard to streamline the revision of dental claims – a great example of Lean Thinking in an administrative process.