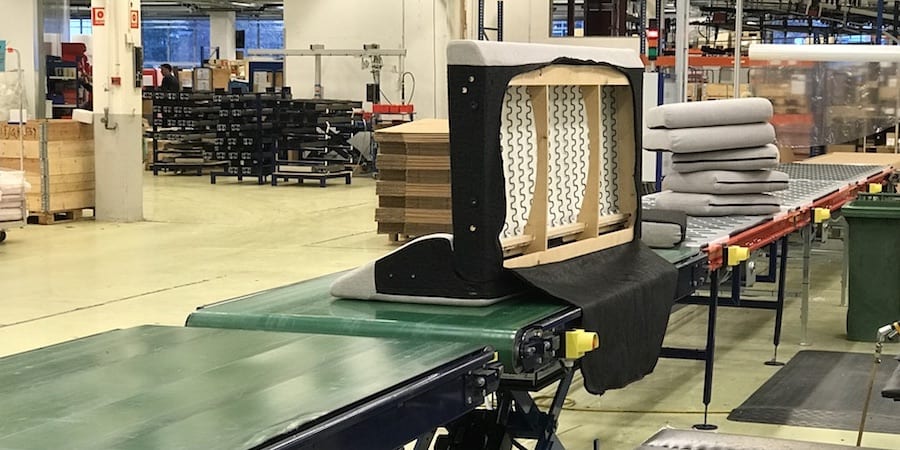
A single experiment changed how we produce furniture
FEATURE – Sometimes all you need to change minds is a successful experiment. This is how a Norwegian furniture manufacturer managed to transform the way it thinks about its sofa production.
Words: Eivind Reke, Organizational Secretary, LOS Norgeand Marcin Gaarden, Improvement Coordinator, Ekornes
The manufacture of furniture has been present in the area around Sykkulven, on the West coast of Norway, since the 1960s. Ekornes, a company famous for its Stressless brand of adaptable chairs and sofas, has two assembly plants here – one in Ikornes, and a smaller sofa plant in the town of Aure, right opposite Ikornes, across Storfjord.
Ekornes started its lean journey in 2010, when every manager went through formal off-site training with a large Norwegian consultancy firm. For the first while, lean in Ekornes meant using tools and techniques, such as 5S and visual boards, but not much more. The company was still producing and moving products in batches from production cell to production cell. The sofa plants in Hareid (now closed) and Aure experienced large variation in operational methods and cycle times, and there were large amounts of buffer stock between workstations. Even though the plant was working with lean tools and strived to continuously improve, they still struggled with a rather uncompetitive delivery time to customers. Similar to many other companies starting off on their lean journey, Ekornes was experiencing difficulties with legacy systems (in particular a long-standing piece pay system where workers get paid per piece produced), a superficial understanding of the problems lean was supposed to solve, and frustrated lean facilitators with more drive than patience.
In 2016, during a research project led by master student Laura Lazar – the soon-to-be-closed Hareid plant involved everyone in a value stream map of their entire process. As they worked on this together, managers and operators began to get a deeper understanding of the overall production system in place at Hareid, and to see how their own work was connected to the overall process.
In the furniture industry, cell and batch production is still prevalent, but at Ekornes people were starting to feel the need to do things differently, maybe even testing line production as a countermeasure to the long lead-times. The closing of the Hareid plan and the subsequent move to Aure was the change in circumstances that allowed Production Manager Ole Andre Småge, Department Manager Stein Arve Rise, engineer Arne Christian Jensen and the lean coordinator Marcin Gaarden to establish a line and start experimenting with one-piece-flow.
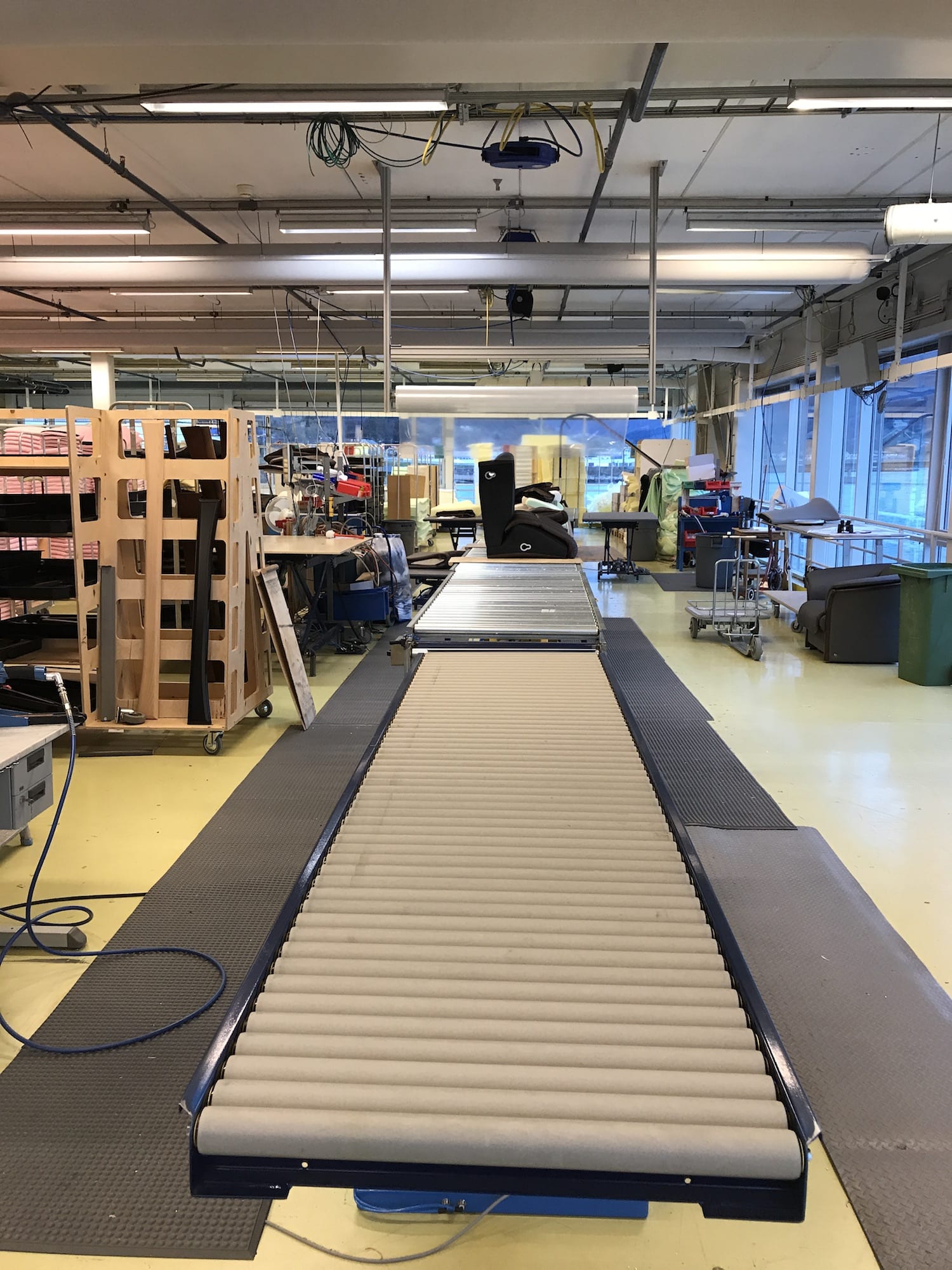
Before the move, the team had started working on the experiment. The first step was to set up a line for final assembly of a popular product that already had a relatively stable lead-time. Marcin, a Polish native who had worked for Ekornes since 2010, calculated the takt time and set up the heijunka schedule. The work was led by Marcin and Stein Arve along with Arne Christian, and it was done with the blessing and total support of the factory manager. At first, the suggestion to set up the line was met with laughter, but the results were eye-opening: production lead-time was halved and final assembly, which used to be split into multiple cells, saw a lead-time reduction of 94%. The team also saw a reduction in buffer stock from 1.5 to 0.5 days between sawing and final assembly. The amount of safety stock in the kanban system was reduced, and defects in production between operations of assembly were eliminated. And let’s not forget that all these extraordinary results were achieved by a dedicated team working in a factory that would soon close. With the planned move, many of the workers at the Hareid plant hada to relocate with their families to Aure or travel up to four hours each day to get to work. Some decided to look for work elsewhere.
What surprised the team the most, however, was an almost immediate change in how the operators worked together. For years, the piece pay system had cemented silo thinking and stifled teamwork: working in cells, operators didn’t pay much attention to their colleagues, and found it hard to understand the purpose of continuous improvement work. With the new line, they found themselves working together as a team on a daily basis. They were solving problems together on the line, as they occurred, making suggestions on how to improve flow, standardize operations, etc, without anyone telling them how to do it. The team saw Taiichi Ohno’s quote – “Let the flow manage the process, don't let management manage the flow” – come to life. By connecting operations that were previously separate, the flow on the line encouraged a new type of behaviour: problems previously hidden immediately became visible when the buffer between operations was removed.The operators also found themselves speaking with a common voice, raising issues together that had previously felt as individual problems. The “lean team” – Stein, Marcin and Arne – were now forced to face these issues head on and frame them for the rest of the plant, so that they could find the countermeasures together.
Since the introduction of the final assembly line, there has been a palpable sense of excitement at Ekornes. What started as an experiment now seems to have a life of its own and it is clear there is no turning back. Of course, the team still face serious problems that need to be solved, but with the piece pay system gone, they are now extending the pull system to the whole of the manufacturing process. They are also setting up kanban systems with cards and two or three box systems wherever possible, and supermarkets whenever necessary.
For the managers and operators at the Aure plant the story has just begun, and the journey ahead is still long – filled with both excitement and frustration. So much learning to do! For now, it is interesting to see how an experiment that people made fun of at first has ended up transforming the way Ekornes thinks about its sofa production.
THE AUTHORS
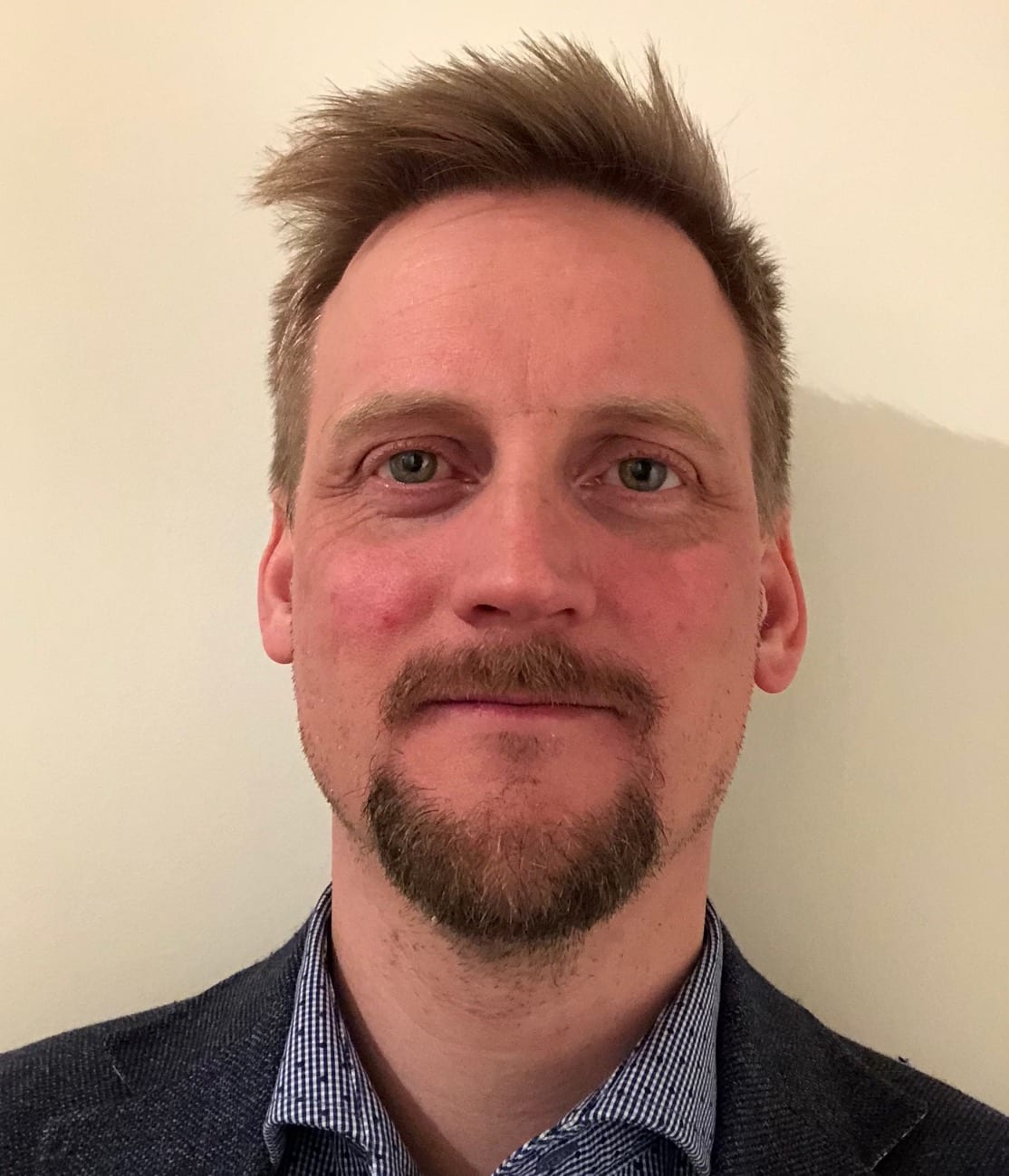
Eivind Rekeis the Organizational Secretary of LOS Norge, a knowledge-sharing network of learning organizations in Norway. The network has over 60 lean and agile thinkers and practitioners working together to develop learning organizations based on the Norwegian model of work life. Eivind learned about the Ekornes case as part of his master research project on lean in Norway.
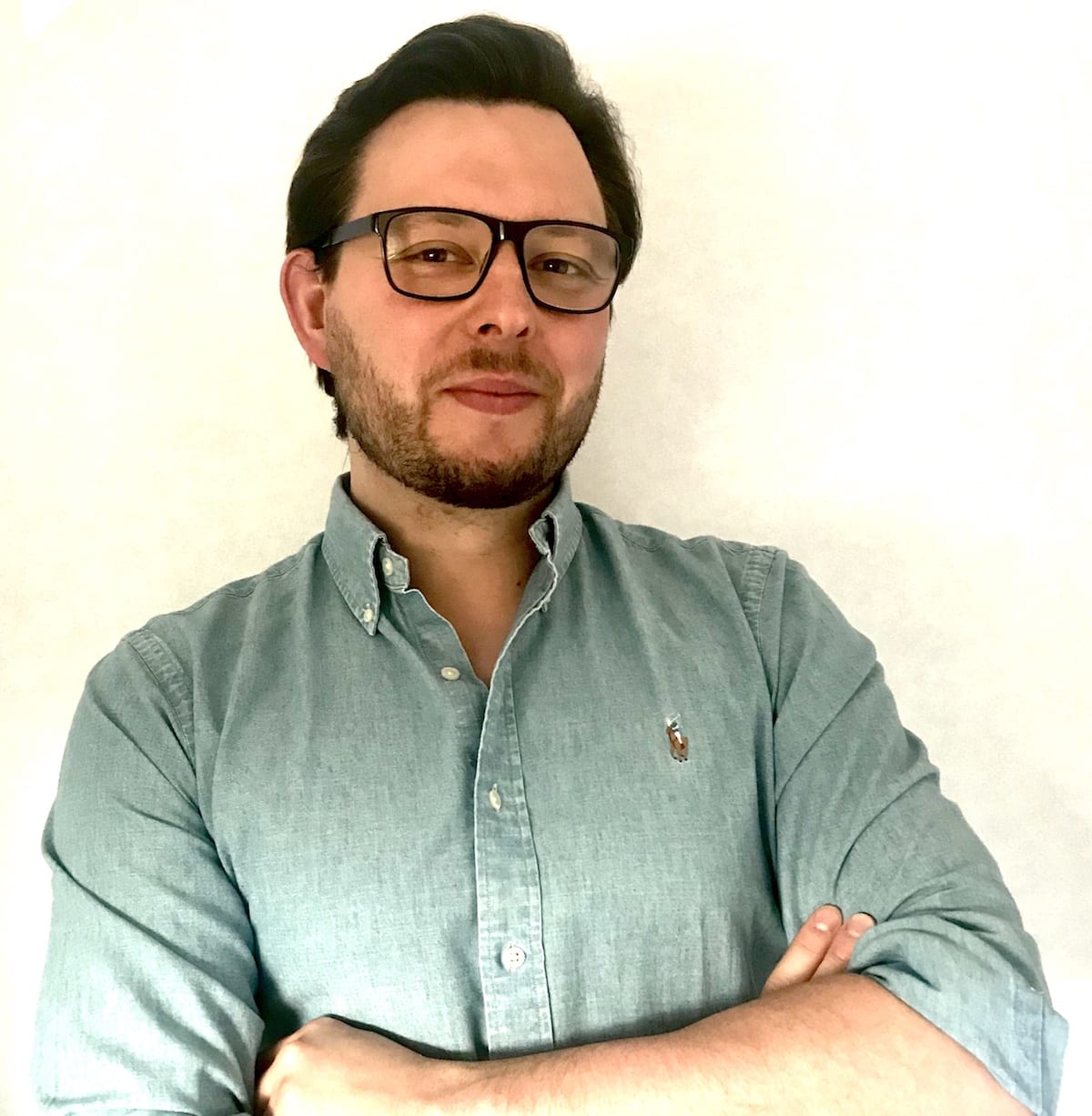
Marcin Gaarden is a lean coach and Improvement Coordinator at the Ekornes plant in Aure. He is a lean six sigma black belt and holds a Master’s degree in economy and foreign trade. Marcin has worked at Ekornes since 2010 and is a member of the LOS Norge network.
Read more
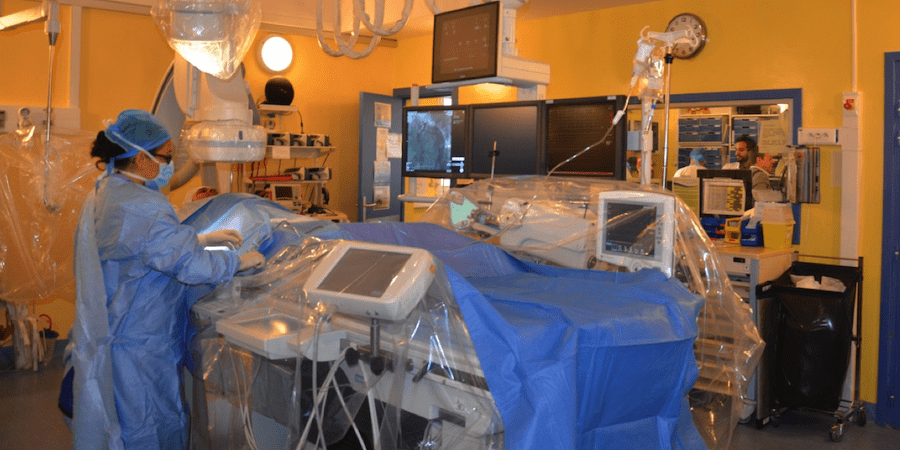
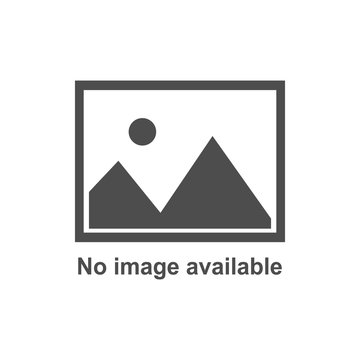
NOTES FROM THE GEMBA – On this gemba walk in the cardiology department of a Parisian hospital, the author discovers how the team is changing its internal dynamics and processes to make lean their way of thinking.
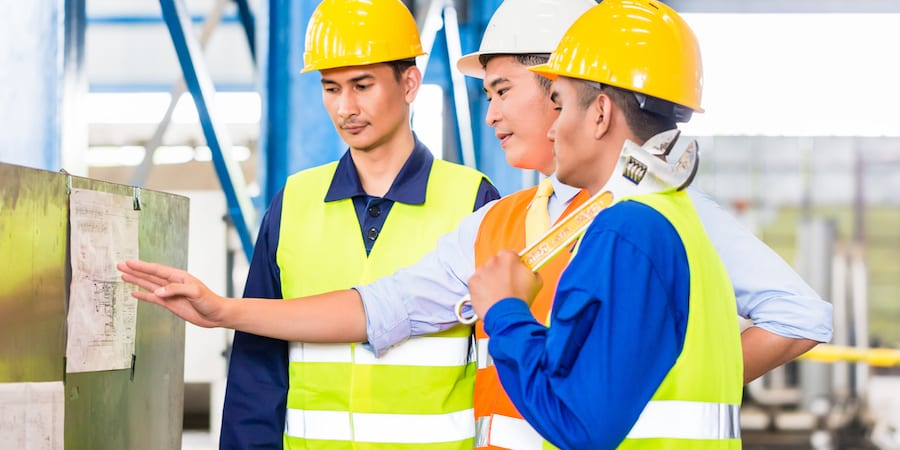
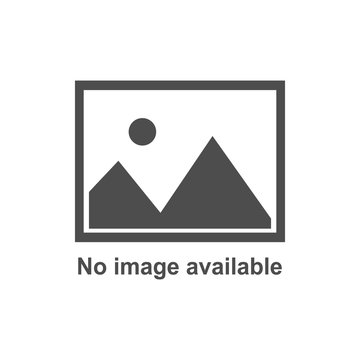
FEATURE – The use of TWI is widespread, but course material doesn’t tell us much about rolling out programs and ensuring their sustainment over time. The authors come to the rescue, discussing how we can ensure the success of TWI.
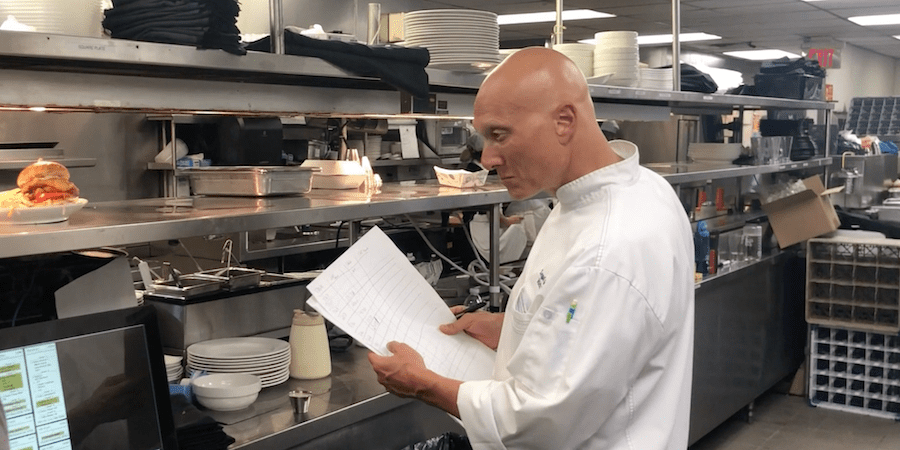
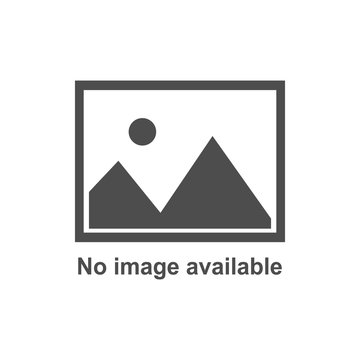
PROFILE – In an industry dominated by star chefs and big egos, meeting a humble leader who has made people development his battle cry is a breath of fresh air. PL interviews Legal Sea Food’s Richard Vellante.
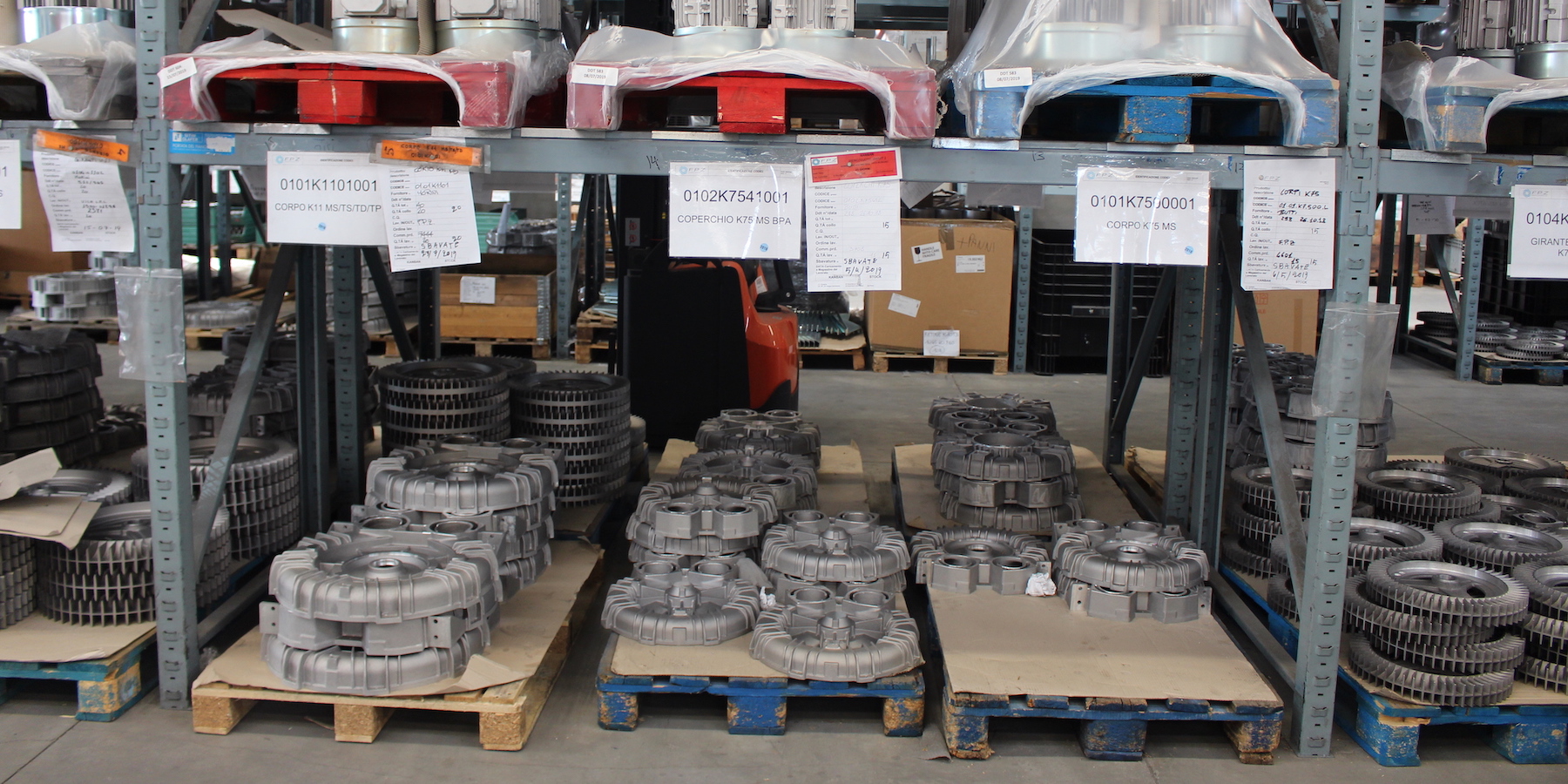
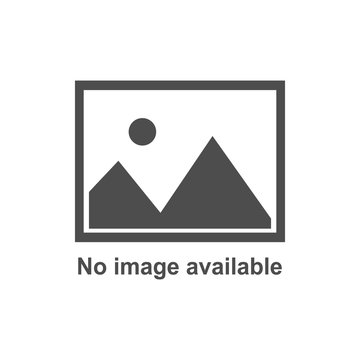
CASE STUDY – Seven years ago, this Italian manufacturer ran an experiment to reduce inventory in its warehouse. Today, lean thinking permeates every aspect of life at FPZ.