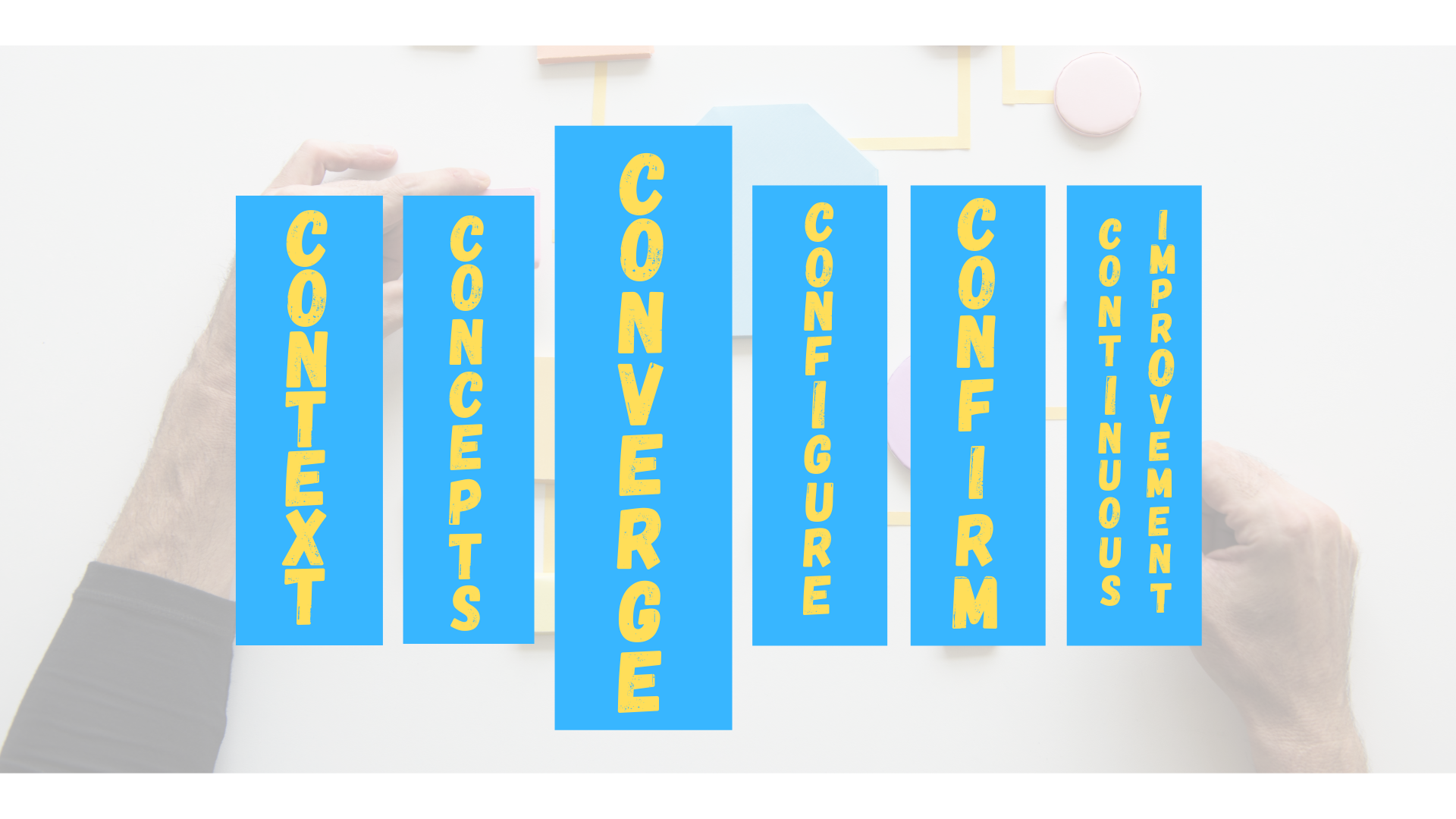
Learning to say “No” on the way to “Yes”
SERIES – The authors discuss the third of six elements in their process development model – Converge – using experiments to test key aspects of different ideas, while objectively working towards a single design concept slated for refinement and implementation.
Words: Eric Ethington and Matt Zayko
“We are trying to prove ourselves wrong as quickly as possible, because only in that way can we find progress.”
- Richard Feynman -
The word “converge” conjures up the typical definitions you would find in Merriam-Webster: 1) to tend or move toward one point or one another; and 2) to come together and unite in a common interest or focus.
In the context of lean process creation, however, the idea of converging is more nuanced. We were recently talking with Jim Morgan, author of the books Designing the Future and The Toyota Product Development System, discussing convergence as a development concept. “To start, we already need to be looking broadly at multiple alternatives,” remarked Jim. If you’ve been following this series on Planet Lean, you’ll know that last month we talked about the idea of “concepts” and the need to consider multiple alternatives. So, we have that covered.
But what Jim said next about converging really gets at its purpose, “convergence is about deselection, not selection. Folks tend to want to pick out what they think is best, they want to jump to a conclusion.” He continued, “This means having a strong understanding of the critical attributes, running experiments and deselecting parts of the alternatives that do not meet the attributes.”
There are many ways to run process development experiments, and one of the simplest is to create a rough mock-up of the process. How rough? Only as elaborate as you need to test the attribute(s) you are exploring. If you are trying to understand the best shape for your cell, then get some moving boxes and tape from Home Depot and a few days later, for a few hundred dollars, you will have a better understanding of which configurations are not meeting your needs. Trying to understand different options for flowing materials between areas? Perhaps a simple queuing simulation can help or a layout with post-it notes. Looking at alternative fixture concepts? Can you create something with foam? What about a quick 3D printed model? To quote Einstein, “As simple as possible, but no simpler.”
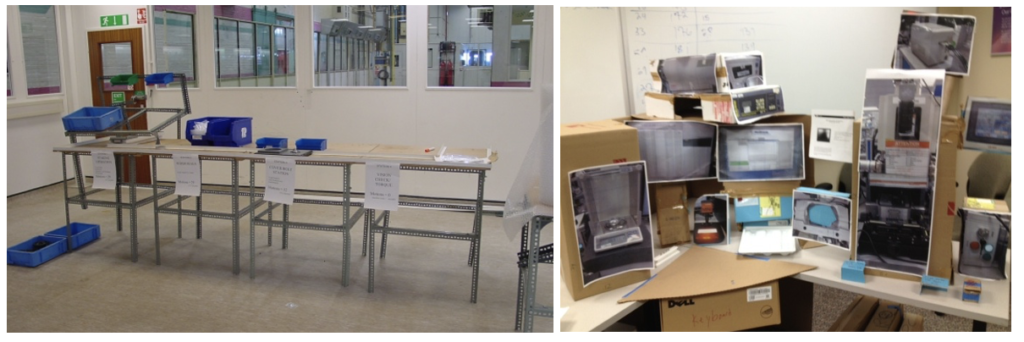
If a concept does not fulfil a critical attribute, it is not necessarily completely deselected. In this case, only the portion that does not meet the attribute is removed. “You can take parts of ideas and combine them with others, run more experiments and deselect again,” Jim said.
To aid in putting some boundaries on the concepts under consideration we like to stress the phrase “creativity before capital”. In other words, don’t attempt to spend your way to the optimal process design – invest when it makes sense, but only when it makes sense. When does it make sense? That is what the experiments are helping you determine. Why spend capital investment on equipment when a simpler and cheaper alternative achieves the same results? Of course, this implies that some sort of investment limits should be one of the critical attributes. (See last month’s article.)
This reminds us of another key point Jim made during our discussion. “You have to be very clear about what you are trying to create, about your value. And there must be constraints. The toughest problems in the world to solve are those that are unconstrained,” he said.
In our book we share something we learned from our mentor years ago: O1S2I3.
O1 = Observation. All improvement begins with observation, and in the case of convergence, observing the experiments.
S2 = Standardize & Stabilize. This has application well beyond converge, into the areas of configure, confirm, and continuously improve. But for the sake of converge, our standards will be our experiments and through learning we will stabilize our ultimate design. One way to do that is to acknowledge three levels of improvement in a specific order.
I3 = Three levels of improvement
- Workplace
- Equipment
- Total Layout / System
Let the workplace improvements and the basic elements of the simplified work inform what equipment is needed to perform the work. And let the combination of the workplace elements and equipment inform the best layout. We have found this simple hierarchy to drive creativity and enhance employee engagement all the while minimizing risks and reducing costs.
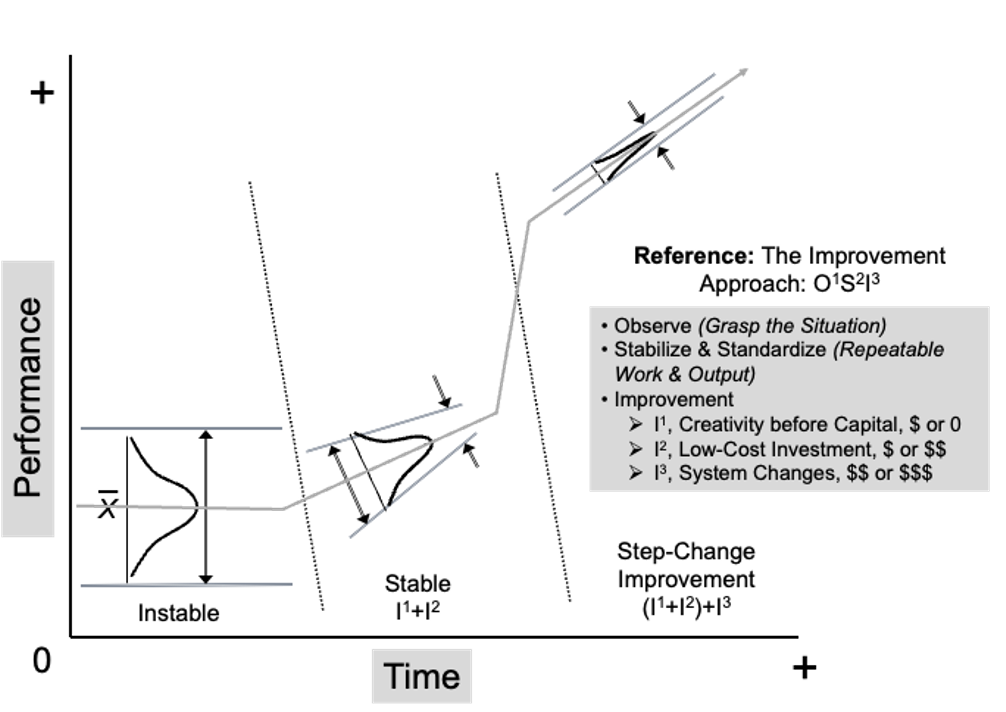
©2022 Zayko & Ethington, The Power of Process, Productivity Press
One final thought Jim shared with us was, “Don’t get wedded to any concept too soon – it may impact how you test.” Great process design is not about being right or wrong. We are trying to create our best known method and process. The output of converge will continue to morph as we move into configure, confirm, and continuously improve.
“We are lucky to live in an age in which we are still making discoveries.”
- Richard Feynman -
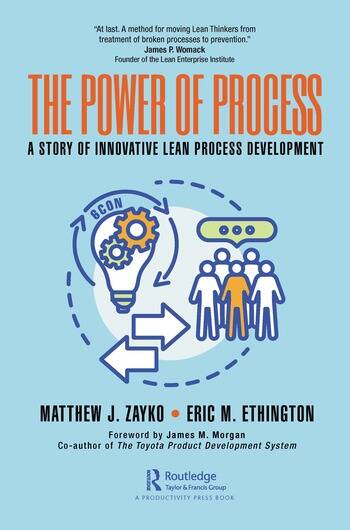
For more details, please visit www.thepowerofprocess.solutions
THE AUTHORS
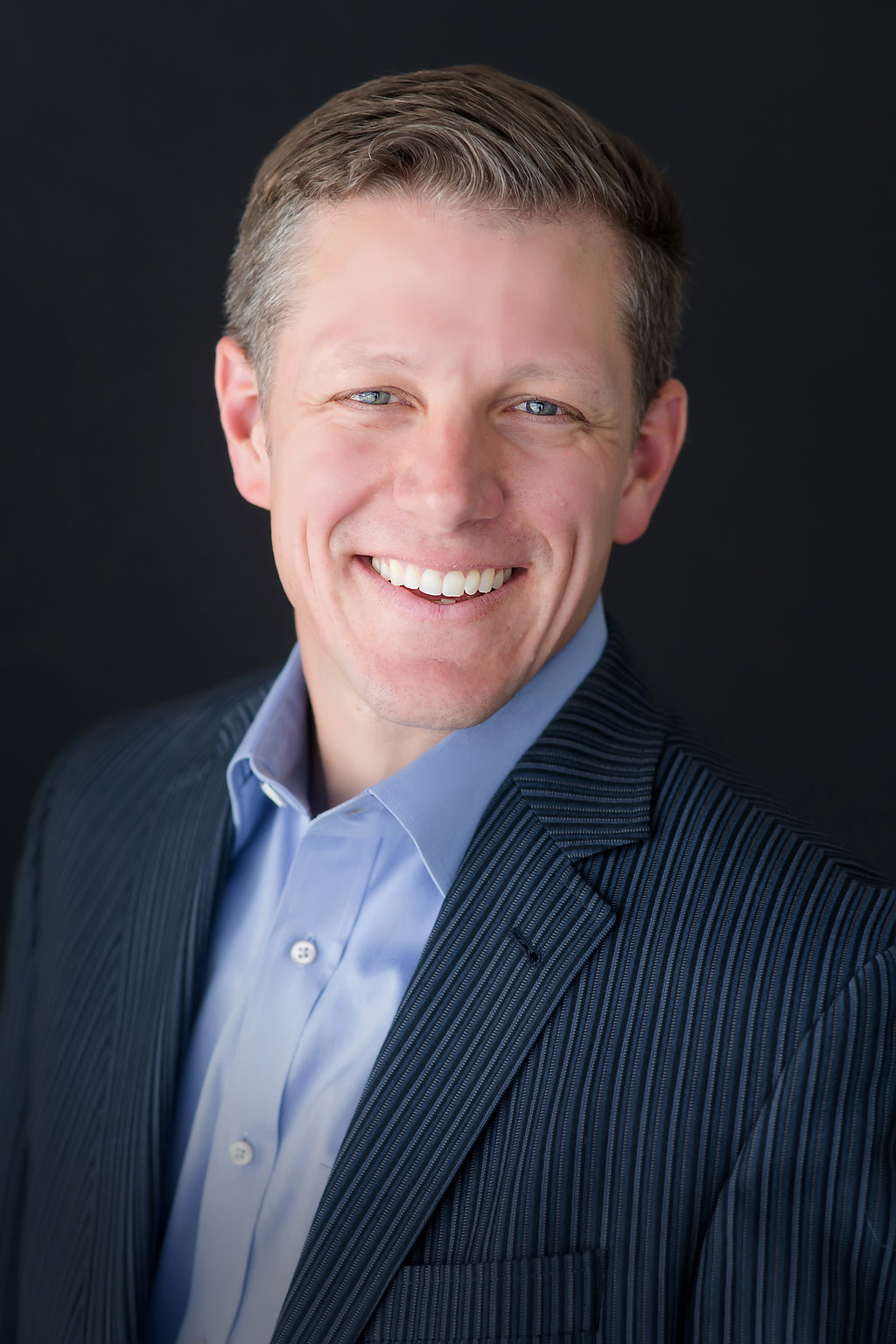
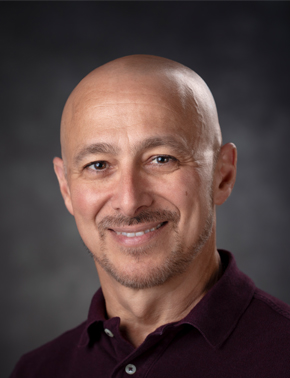
Read more
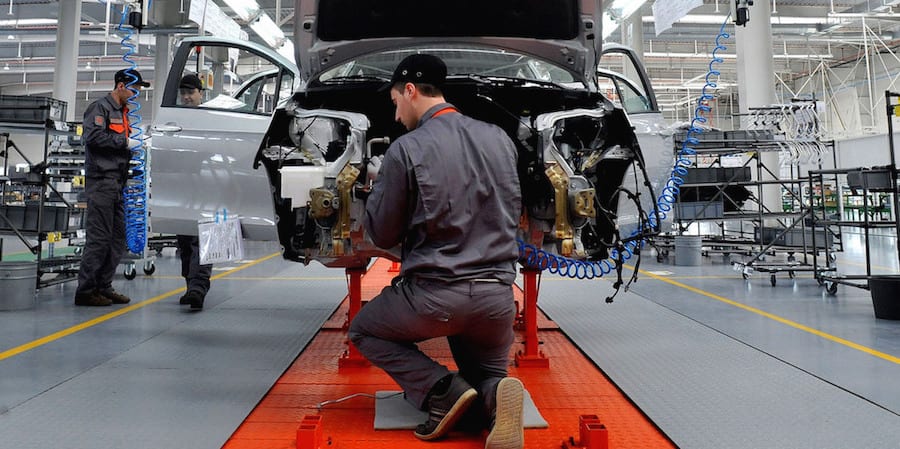
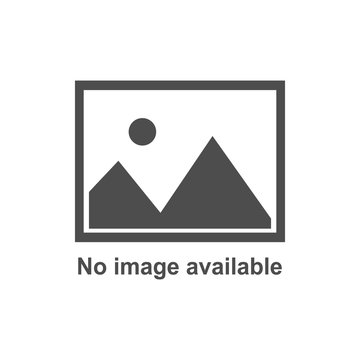
FEATURE - The original TPS "house" had levelled production at its foundation because Toyota understood that establishing and sustaining continuous improvement is impossible without creating stability in production first. What about your transformation?
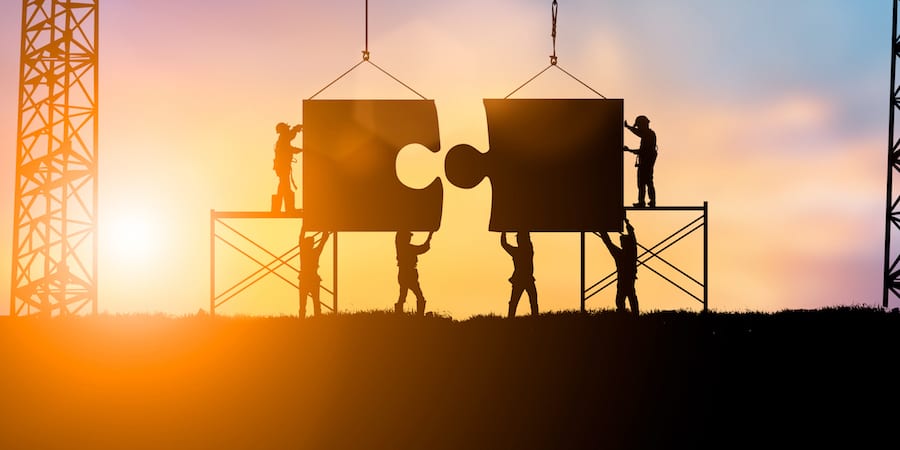
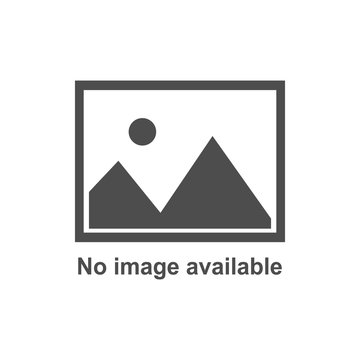
FEATURE – Using Carol Dweck’s distinction between fixed and growth mindsets, the author discusses how leaders should think and act to make lean possible. Looks like no fixed mindset is beyond saving.
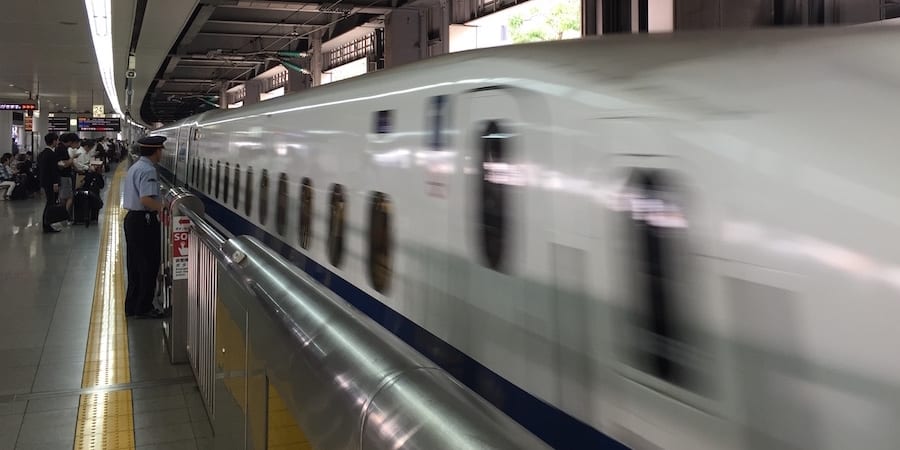
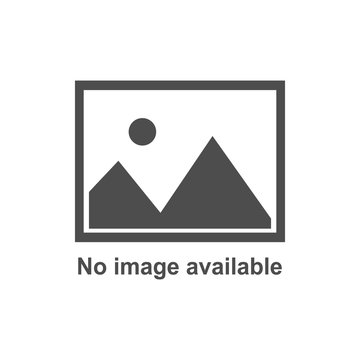
FEATURE – How many times do we hear people say lean is not for them because “it’s a Japanese thing”? After spending 18 months in Japan, the author explains why the country’s culture is not necessarily "lean by nature".
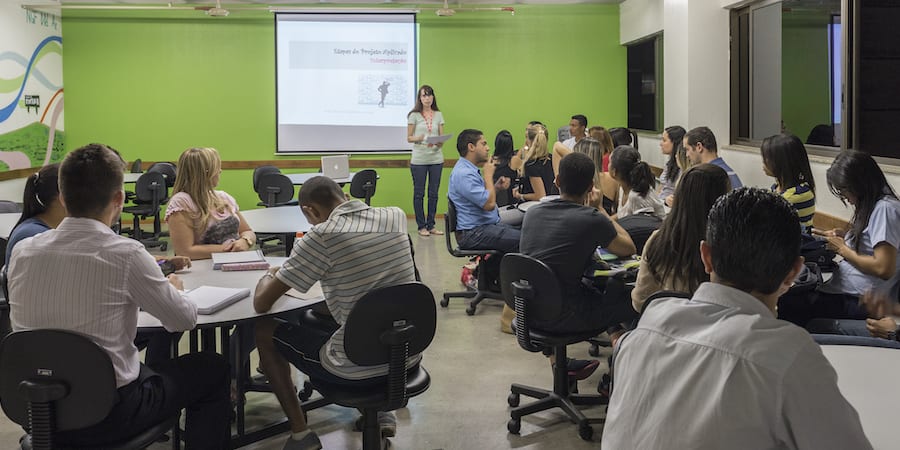
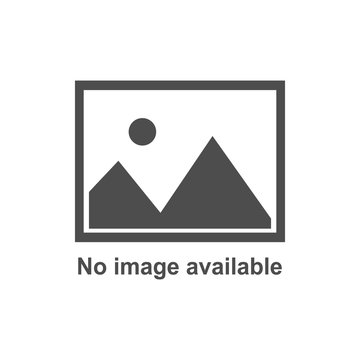
INTERVIEW – Grupo Anima, a Brazilian private education organization with almost 100,000 high-school students enrolled, has revolutionized its culture since introducing lean. But it all started with one project…