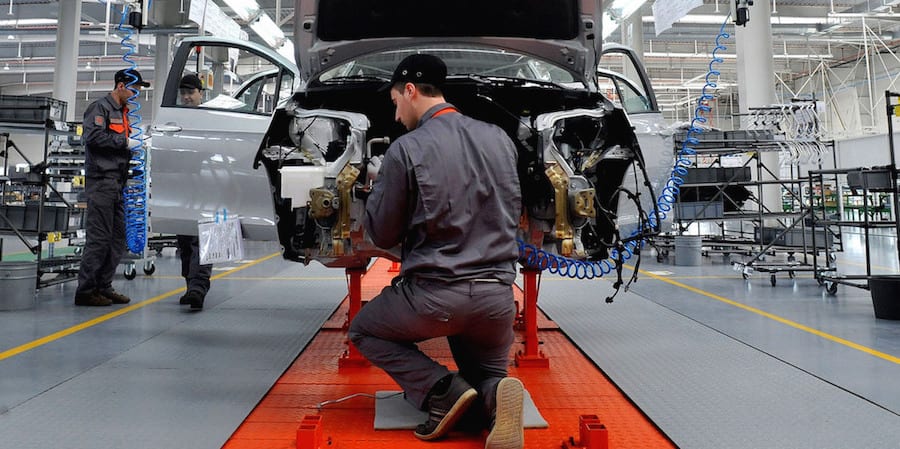
Toyota considered heijunka critical to improve. Do you?
FEATURE - The original TPS "house" had levelled production at its foundation because Toyota understood that establishing and sustaining continuous improvement is impossible without creating stability in production first. What about your transformation?
Words: Ian Glenday, lean coach and author
Photo credit: Ju1978 / Shutterstock.com
My previous article for Planet Lean covered how ERP planning systems based on EOQ's (economic order quantities) or batch logic are guaranteed to produce a different plan every time – which then often changes. In addition, this logic causes peaks and troughs in the supply chain that has nothing to do with real demand. It creates instability, yet it is the logic used by most companies in their planning processes.
How did Toyota avoid this instability? What did they do that created stability and as a result provided a foundation for achieving sustainable continuous improvement?
I was fortunate to go to Japan in the late 1980s to study under a master sensei, Yoshiki Iwata from Toyota Gosei – a rubber component manufacturer. Toyota Gosei was one of the first supplier companies to be taught the Toyota Production System by Toyota. Iwata showed me this diagram of the TPS "house" which was originally drawn by Fujio Cho of Toyota.
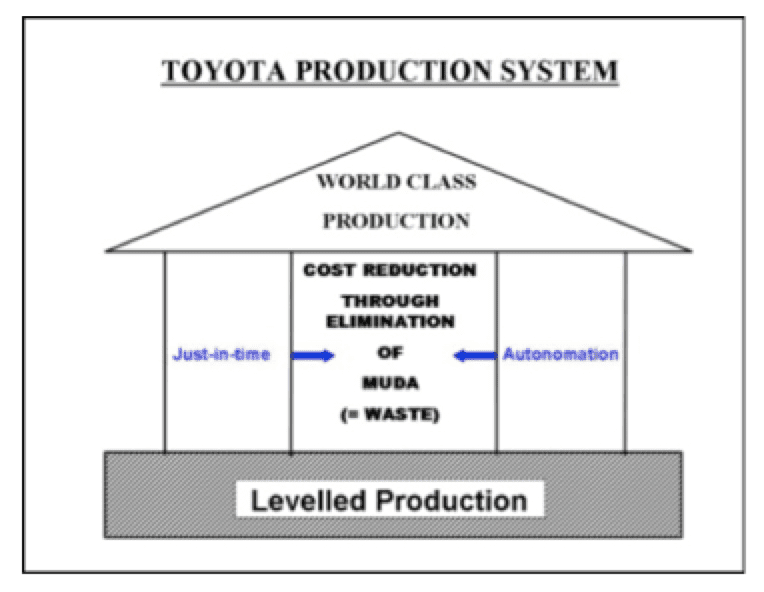
Levelled production forms the foundation of the house – also known as "heijunka," a term coined by Toyota to describe the process. Most companies "doing lean" produce their own version of the TPS house, but I have never seen one – and I have seen a lot – where levelled production is shown as the foundation, as in Toyota's original version. Organizations put lots of good things in their foundation: examples I have seen include leadership, people empowerment and lean fundamentals, but never levelled production. Why is this? Perhaps it is because levelled production is not well understood or, if it is understood, then maybe it seems just too difficult to do. Probably it is a bit of both. What is certain is that it is the foundation of the Toyota Production System and that if you want to be truly lean you have to do it.
So what is levelled production?
Iwata described it as an evolution of five steps. Generally people are aware of the fifth and final step, known as "one piece flow." This is the ultimate objective of levelled production resulting in perfect flow, flexibility, responsiveness and zero waste. However, it is very hard for most people to see how to achieve one piece flow in their company. Especially if they do not understand the other four steps of levelled production.
As a matter of fact, the objective of the first three steps is completely opposite to that of the fifth step. These initial steps were designed to create stability as the foundation for achieving sustainable continuous improvement leading to better performance and reliability. As these are realized it is possible to increase flexibility and responsiveness to demand – the objective of steps four and five. This sequence of steps is vital. Stability must be created first to eliminate the short-term plan changes and firefighting that are endemic in most companies. Then one can progressively match output more closely to actual demand.
The aim of the initial three steps of levelling is to produce products in a fixed schedule that is rigorously followed. Same products, same volume, on the same equipment, at the same time and in the same sequence every cycle. Step one: in a twice a month cycle. Step two: in a weekly cycle. Step three: daily cycles. These fixed schedules would run for 6 to 8 cycles before being re-calculated for another series of 6 to 8 cycles. It led to the term "every product every cycle" (EPEC).
This seems absurd to most people. Firstly they think more changeovers and shorter runs will not make them more efficient – far from it. It flies in the face of conventional wisdom on how to improve performance – it is completely counter-intuitive. Secondly, being able to have the same fixed schedule for 6 to 8 cycles is seen as totally impossible. Not with the level of demand variability people think they have. No wonder so few companies have the five steps of levelling as part of their lean programme.
Yet it is what Toyota did and it is critical to TPS and lean.
The key objective is to create stability first because stability is the foundation that makes it easier to carry out continuous improvement, standardization and root-cause problem solving. Then improvements can be invested in faster and faster cycles. Progressively faster cycles means production gets closer and closer to actual demand. Step four and five of levelled production focus on producing exactly to actual demand. First in very small fixed batches, then just one item at a time – one piece flow – the ultimate objective of levelled production.
I had an exchange of emails with John Shook on the subject of levelled production or heijunka to check that my understanding from Iwata was indeed correct. John was the first American to work as a regular employee of Toyota's global manufacturing HQ in Toyota City. Here's what he said:
"Many meanings are contained in the term heijunka. Unfortunately, translation often forces the translator to focus on just one aspect. You will hear Toyota sometimes refer to heijunka as the 'objective' of system improvement, showing it at the culmination of a series of steps and evolution. Other times you will hear Toyota say heijunka is a 'pre-requisite' for attaining lean that must be incorporated at the beginning. In fact, a 'first stage' heijunka is something we sometimes call 'pattern production.' A pattern of running each part number repetitively, perhaps using an 80/20 rule to differentiate high from low runners, is established. It is remarkable that so few industries, companies, and people have arrived at this understanding of heijunka."
Patterned production! Perhaps if Toyota had used this term more widely people would have understood the steps of levelling and how the first three steps created stability.
Is levelled production part of your approach to lean , including the first three steps where a fixed schedule is rigorously followed for 6 to 8 cycles to create stability?
But what is it about fixed schedules over 6 to 8 cycles that creates a performance improvement when most people think the reverse will happen? This will be the subject of my next article.
You can find out more about levelled production in Lean/RfS: putting the pieces together.
THE AUTHOR
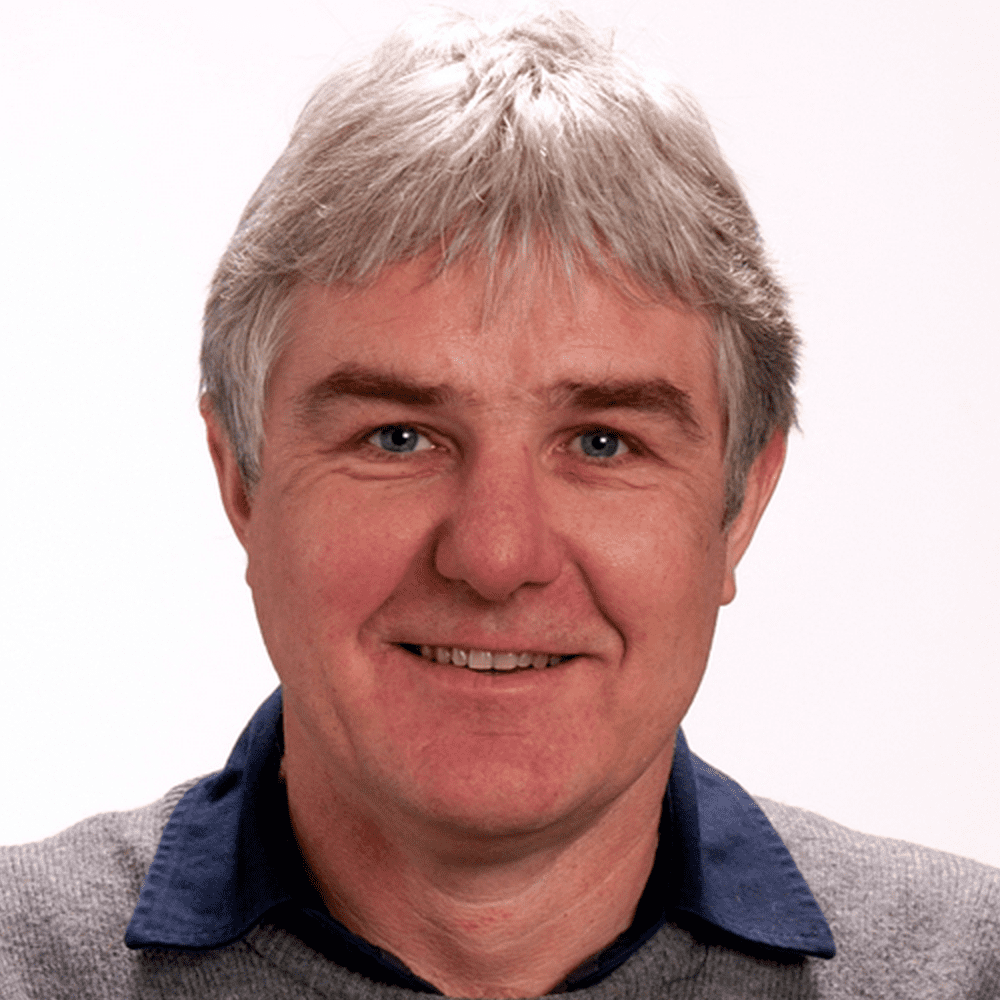
Read more
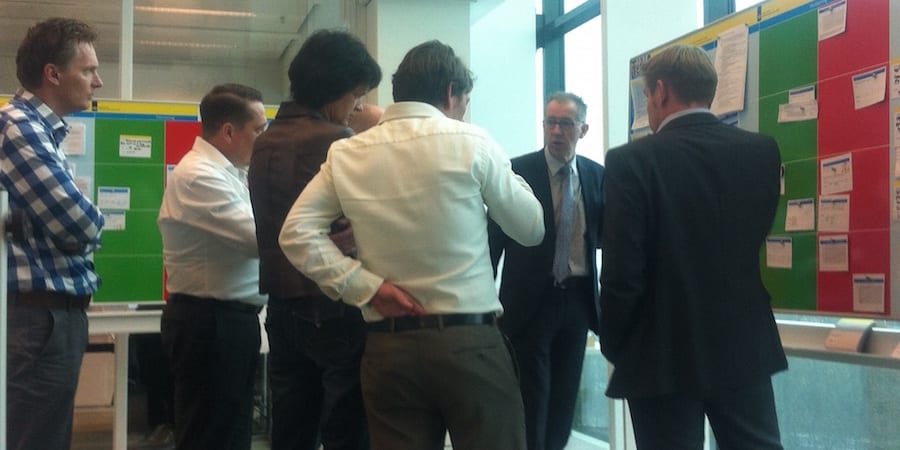
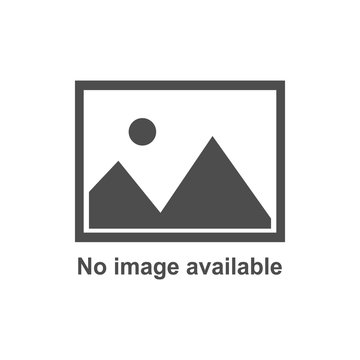
FEATURE – The theory of hoshin kanri is clear, but how can you adapt it to a government organization structured in departments where making A3s is not a daily practice? A Dutch ministry shares its experience.
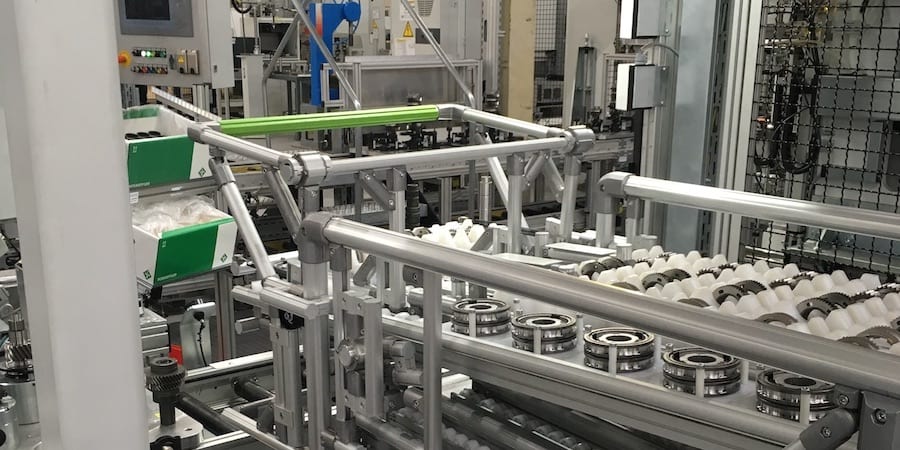
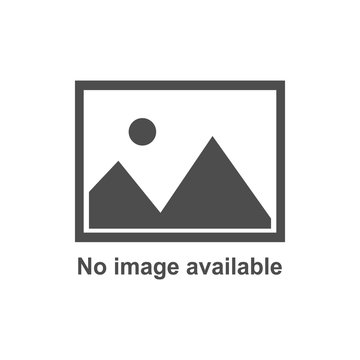
NOTES FROM THE GEMBA – If you need proof that kaizen leads to real innovation, look no further than AIO. This French Tech company that reinvented itself as a karakuri kaizen coach.
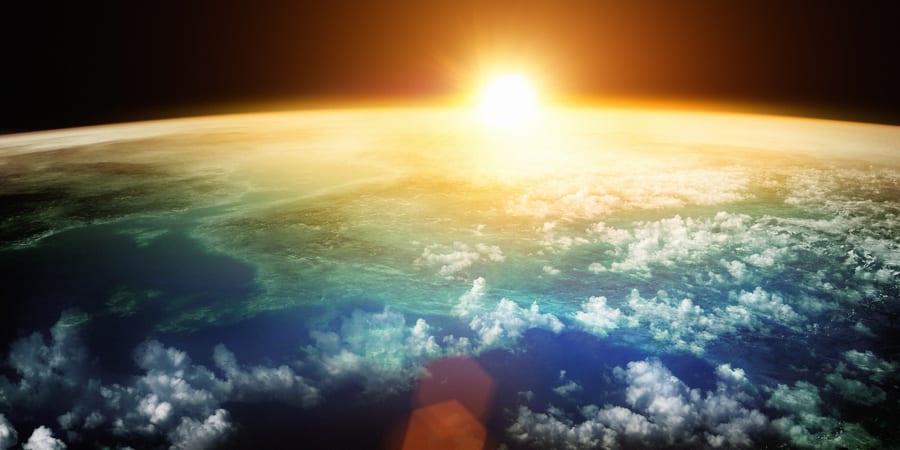
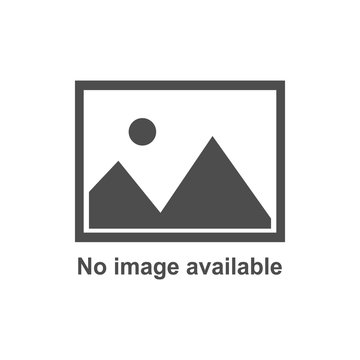
FEATURE – If we see lean thinking as a paradigm, which we do, then we should be able to define a set of values this paradigm is built on. So, are there lean ethics? Michael Ballé identifies 10 undisputed lean values, plus one.
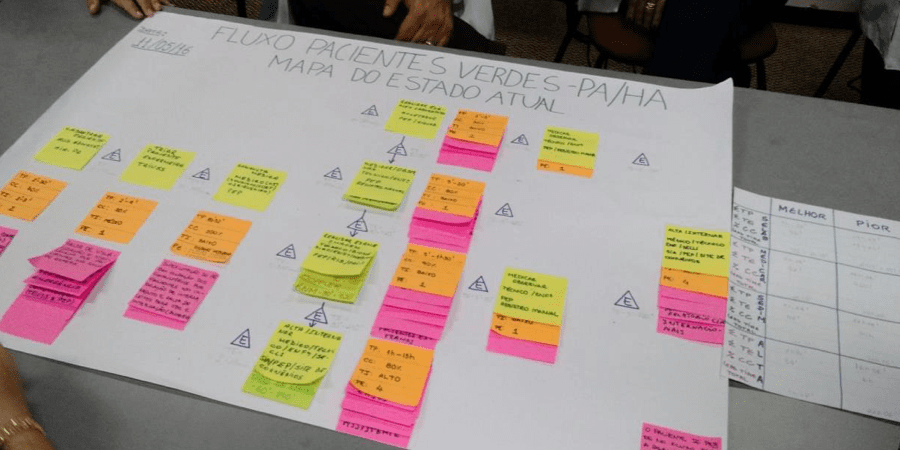
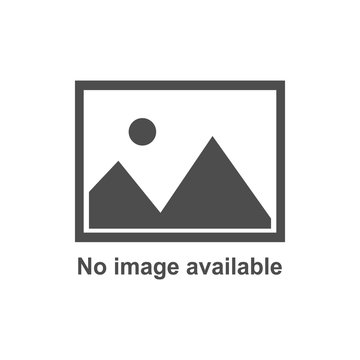
FEATURE – Long waiting times are bad for both patients and hospitals, but when we talk about heart attacks reducing them becomes a moral imperative. Here’s how Hospital Aliança in Brazil is doing it.