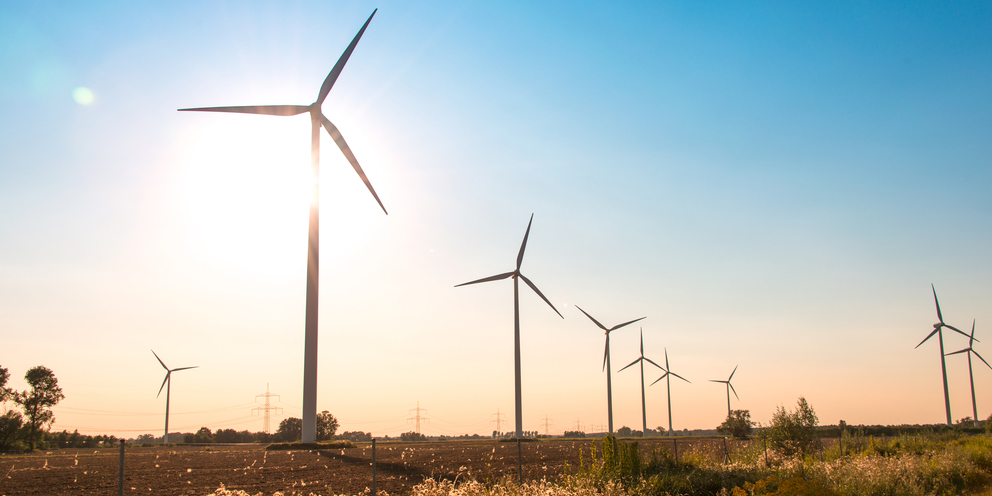
Eight practices to put more green into lean
FEATURE – The planet is warming at an unsustainable rate, pollution is increasing, wildlife populations and arable land areas have plummeted, and our oceans are filling with plastic. Can Lean Thinking help?
Words: John S. Hamalian, Lean Global Network – Southeast Asia
“How can you be running a lean transformation exercise and have waste streams that go into landfills?” nudged Marty Neese, COO of solar panel maker SunPower in this 2016 post. Lean thinkers love a good challenge, and Marty sure has given us one! In light of the accelerating dangers the people of this planet collectively face, are we in the Lean Community doing enough to make a difference?
The idea of “Lean and Green” is not new, but perhaps we need to do a better job at institutionalizing “green” into Lean Thinking. We could think of this as “Green Lean”, the systematic incorporation of environmental sustainability into the daily work of lean practitioners around the world to help unlock the green passion and potential that lie within each of us.
In this article, I’d like to frame this conversation by outlining eight enablers of “Green Lean”. Here they are.
1) GREEN TRUE NORTH
Where do we start? Here, Jim Womack has pressed us “to apply Lean to ‘big problems’ rather than the little problems most folks focus on”. When it comes to big problems in sustainability, unfortunately, we are spoiled for choice – from the $1 trillion of food wasted globally every year to the 12 million hectares of land lost annually or the fact that our oceans will contain more plastic than fish by 2050.
In a bid to contribute to the resolution of such big problems, companies like Nestlé, IKEA, Unilever and Patagonia have incorporated sustainability into their business models. Toyota, for its part, has been investing heavily not only into green products, such as the Prius and Mirai, but even in a Green City (the ‘Woven City’).
The green revolution can provide Lean Thinking many new (big) problems to solve, breathing a new sense of purpose into our work.
2) GREEN HOSHIN
Lean practitioners can take the lead on integrating sustainability into Hoshin Kanri, Daily Management and other key processes. In fact, some organizations have already added the “environment” as a category of their hoshin, thus building “green” into their strategy. Not surprisingly, Toyota is way up front here: the Toyota Environmental Challenge 2050 is a series of six high-level, long-term stretch goals that are deployed throughout their organization via the Hoshin process.
Green Hoshin Tip: Bring tools from the sustainability community into your strategy design process – such as the Materiality Matrix – so that lean and green are not seen as two separate activities.
3) GREEN MUDA
It’s interesting to see how all of the seven wastes can somehow be tied to the environment. Some are relatively obvious, like Transport and Defects, while others are somewhat deceptive – like Over-processing, even though it can lead to all kinds of solid, liquid and gaseous waste (excess run-off or gas emissions for example). It’s hard to deny, for example, there is substantial over-processing in the manufacturing of one T-shirt, which requires a staggering 2,700 litres of water.
And let’s not forget another “hidden waste” the Lean Community can help address: digital waste. According to Kelly Singer, “Digital technology now accounts for as much carbon release as all air travel.” (More here.) As one example, mining Bitcoin currently takes three times the energy than physical mining!
We also may want to look closer at Over-production. Should we reframe its general definition of “more than is required, before it is required by the customer” to include more than can be borne by the customer? (In this case, the “customer” can be our society or community, even our planet.) This may help us think more deeply about current critical issues, such as overstretched landfills, polluted waters and overtourism.
Green Muda Tip:To help us tie muda with environmental impact, borrow a term used by Purdue University – ‘W.A.S.T.E’: Water, Air, Solids, Toxins and Energy. It may be a useful way to highlight “green” in lean and a reminder that process inefficiencies (muda) lead to resource inefficiencies.
4) GREEN GEMBA
Do we consider the environment when we are out there at the gemba? What does a green gemba walk look like? In this post, Sasha Neser suggests putting on a “green lens”. A “Treasure Hunt” at GE, for example, led to greenhouse gas emissions savings of 700k metric tons. One particularly interesting type of green gemba walk is a “Dumpster Dive”: sifting through solid waste streams to understand exactly what is being disposed and then trace it back to the source. Sunpower did a Dumpster Dive and found that the bulk of the residue came from their food waste, leading them to use a composter on their land and even using their own panels to power it! More here.
Green Gemba Walk Tips:
- Find a green partner: leverage EHS experts during your green gemba walks.
- Use “green” tools, such as a System Boundary Map, to help identify current resource usage.
- Reference EPA guidance for Identifying Environmental Wastes and other materials.
5) GREEN VALUE STREAMS
“We need a re-boot of our supply chain,” said Lucas Glanville, Director of Culinary Operations for Hyatt Hotels in Southeast Asia, when discussing sustainability at the 2019 Sustainable Tourism conference in Singapore. Embracing the Circular Economy concept is key to making our world more sustainable, but it does require a shift from linear thinking to systems thinking. Clearly, this is another instance in which Lean Thinking is particularly well-placed to make a difference. For example, Laura Mottola and Kelly Singer have developed a Circular Lean Mining concept to help reconnect the battery raw material suppliers with the end consumer through lean practices. For more on the idea of cradle-to-cradle, check out this article on Sunpower.
Chef Lucas went on to say: “We need to have an overview and understand the situation.” The Extended Value Stream (EVS), as explained in the Seeing the Whole Value Stream, could help here. The EVS method is a wonderful way to see both the upstream and downstream impact of a product or service, a key to achieving a circular economy (or should we say a circular value stream?).
Green Value Stream Tip: Go beyond the typical value stream scope and do an entire EVS analysis
6) GREEN VSM
Learning to see (green) is fundamental. Since most environmental impact is either physically hidden (like CO2) or virtually hidden (that landfill tucked away in the middle of nowhere), what better way to see “invisible” environmental waste than to use green Value Stream Mapping?
Here are a few ideas on how to make this happen, many contributed by some brilliant green lean pioneers:
- Highlight environmental issues on our maps. Just like we may call out Quality issues with a ‘Q’ (in the SQDC framework), so we can use an ‘E’ for Environment.
- Include environmental resource usage to the VSM data box, for example food, water and energy used in a process step (in a case I have come across, this technique helped highlight that 195 pounds of a resource were used to make a product, when only 110 pounds were needed).
- Capture solid/liquid/gaseous waste as an output of a process step, by showing it in between data boxes.
- Add an entirely new ‘flow’ to your VSM, for waste. This would enable us to visually see (via arrows, etc) where streams of environmental waste are flowing to, say, e-waste to a landfill. This might, for example, help farmers see the downstream impact of fertilizers on drinking water due to Nitrogen run-off.
- Broaden the definition of “suppliers” and “customers” to all kinds of “providers” (mines, lakes, etc) and “recipients” (landfills, the air, etc).
Green value stream maps have proven to be effective. In one case, Baxter Healthcare Corp used one to discover opportunities to save a whopping 170,000 gallons of water per day.
Green VSM Tips:
- Leverage ‘green’ techniques such as Sankey Diagrams to better and more visually show critical resource flows.
- Learn from materials such as the EPA training module on VSM
- Use simple online tools such as the EPAs ‘Greenhouse Gas Calculator’ to convert our newly visible resource measures to CO2 (wouldn’t “Total CO2” be a nice addition to a VSM’s measures?)
7) GREEN KAIZEN
Typically, environmental impact reduction efforts center around outputs and end-metrics, often resulting in the implementation of pre-made, end-of-pipe solutions, such as installing solar panels or LED lighting. Lean’s focus on the process, rather than just the result, and improving it through significantly re-thinking and re-designing work can be a big contribution to the Green Movement.
One simple example of this is a food caterer in Singapore that was making plans to increase their warehouse capacity by shifting to a larger building. With some basic lean techniques the work was re-thought and the layout re-designed. Not only did the current space now meet all the requirements, it averted relocation to a place farther from their central kitchen, saving utility and gasoline usage for a net lower carbon footprint.
And of course we have our lean farmer, Ben Hartman, and his case of fundamentally re-thinking agricultural work here.
8) GREEN 5S
Like most restaurants, XiBei, a large chain in China, normally discards returned food during the hustle and bustle of their daily rushes. Inspired by the lean “red bin” concept of highlighting damaged products, XiBei decided to install a “Red Fridge”, a small refrigerator painted bright red and used for the sole purpose of storing returned or otherwise “defective” food. The team does regular reviews around the Red Fridge for reflection and problem solving, driving towards a zero-defect (and zero food waste) performance capability. These kinds of simple actions can have a positive effect on carbon emissions in the whole supply chain.
Speaking of carbon reduction, Tokheim has one of the best Green 5S stories to tell here.
For some tips on how to make your workplace greener, check out this post by Brion Hurley or this EPA document.
A CAUTIONARY GRAIL (AND A CALL TO ARMS)
In one of his Yokoten columns for Planet Lean, Jim Womack has warned us that “lean is not inherently ‘green’”. A key question is what do we do with the resources freed up by lean. Since Lean Thinking teaches us to do more with less, it is imperative that we not only strive for reduced resource usage, but also look at innovative ways to increase value by unlocking opportunities unearthed through our lean improvements. By reducing waste, we free up resources that can be used to make us greener (there is perhaps no better example of that than the Toyota Prius).
The drive and the passion to produce less waste and create more value is strong in any lean thinker. But what can we do today to help? In my mind, we can partner with the Sustainability Community to form a “Lean Green Alliance” and jointly solve the world’s most pressing issues, practice “green lean” in our daily work (and share our learnings with the community), and promote our mission to help inspire the world to change course through our lean actions and practices .
Taiichi Ohno once said, “Progress cannot be generated when we are satisfied with existing situations”. When it comes to sustainability, we shouldn’t be satisfied. We cannot be! If we don’t do this, who will?
THE AUTHOR
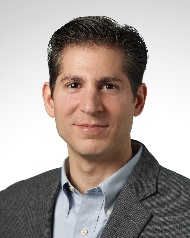
Read more
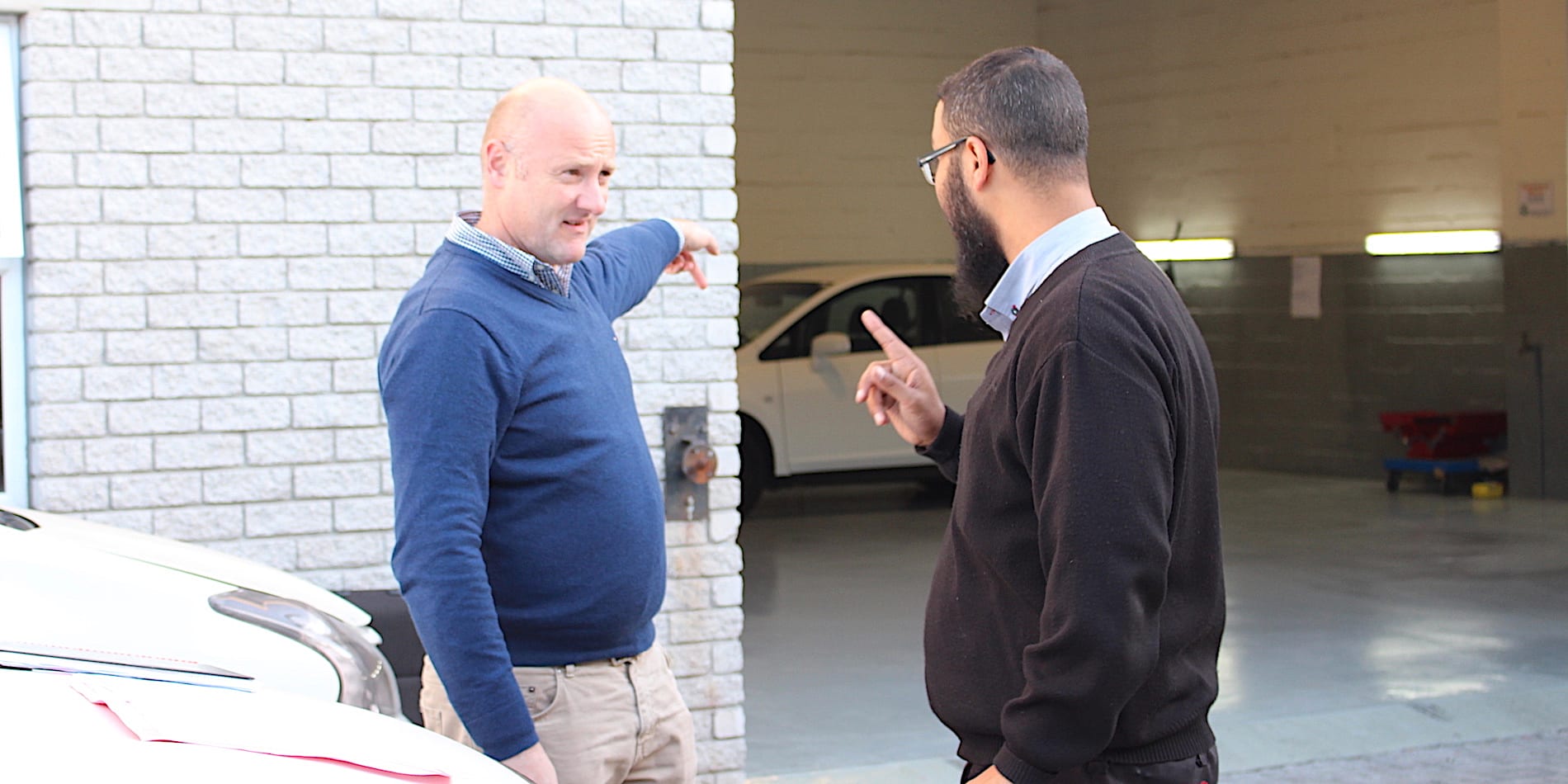
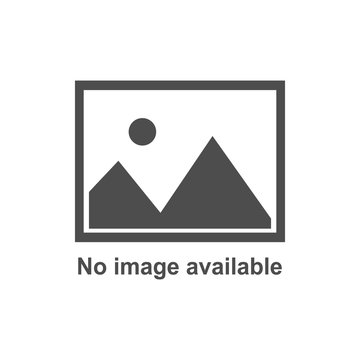
FEATURE – The role of the coach in a lean transformation is an often-debated topic. The author discusses his experience building the architecture of the Halfway turnaround.
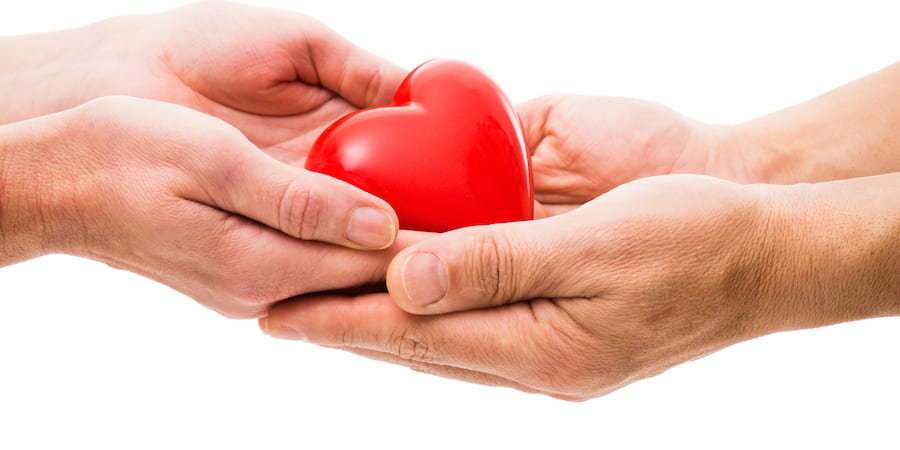
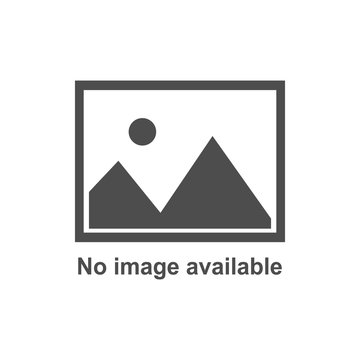
FEATURE – A Michigan NGO that facilitates organ and tissue donation shares its experience with value stream mapping, reflecting on people coming together to understand the gap between current and future state.
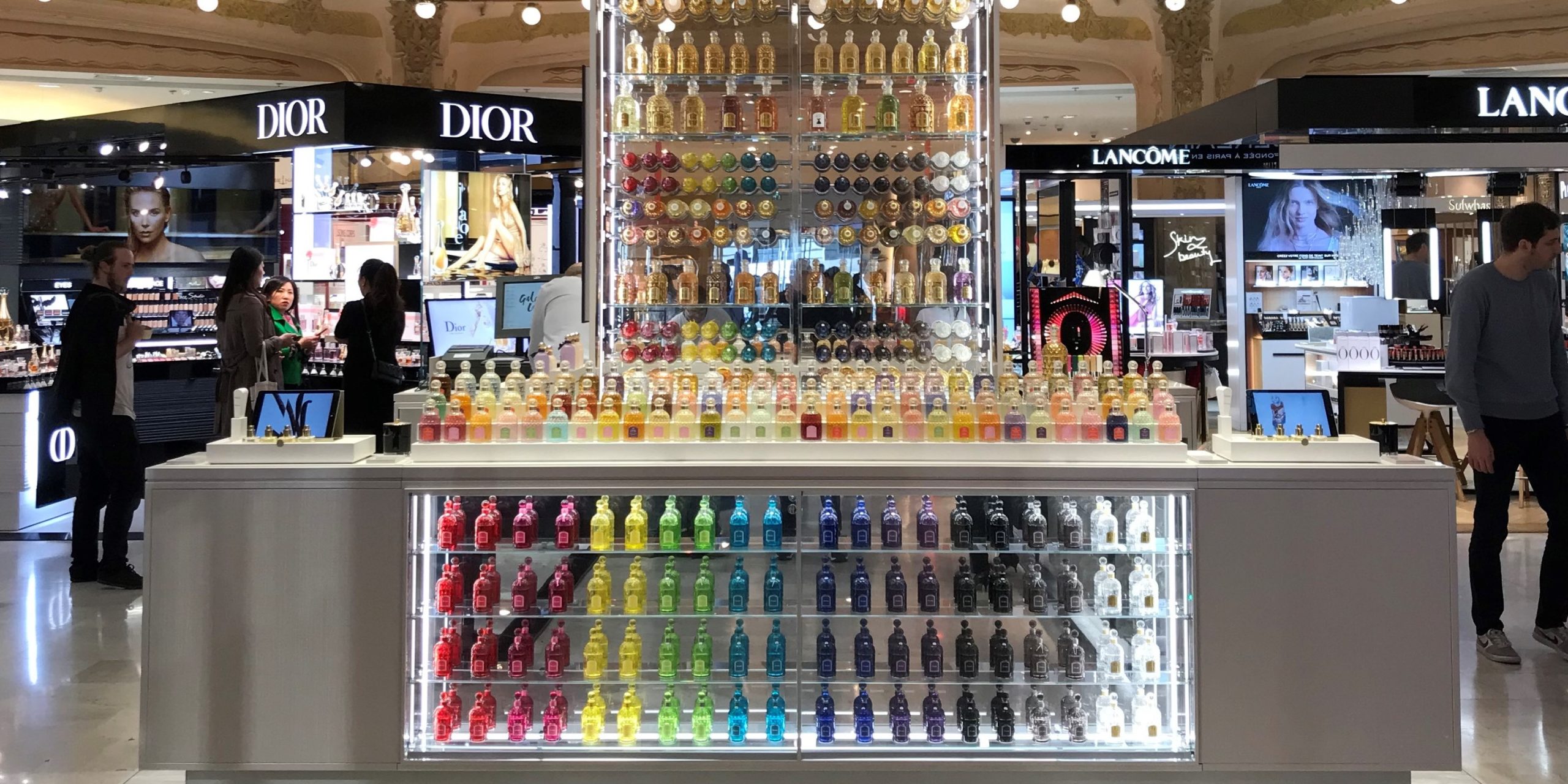
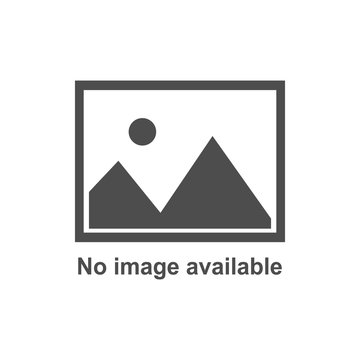
NOTES FROM THE GEMBA – How do you kick off a lean journey? This French company has chosen to begin by analyzing and tackling each customer complaint.
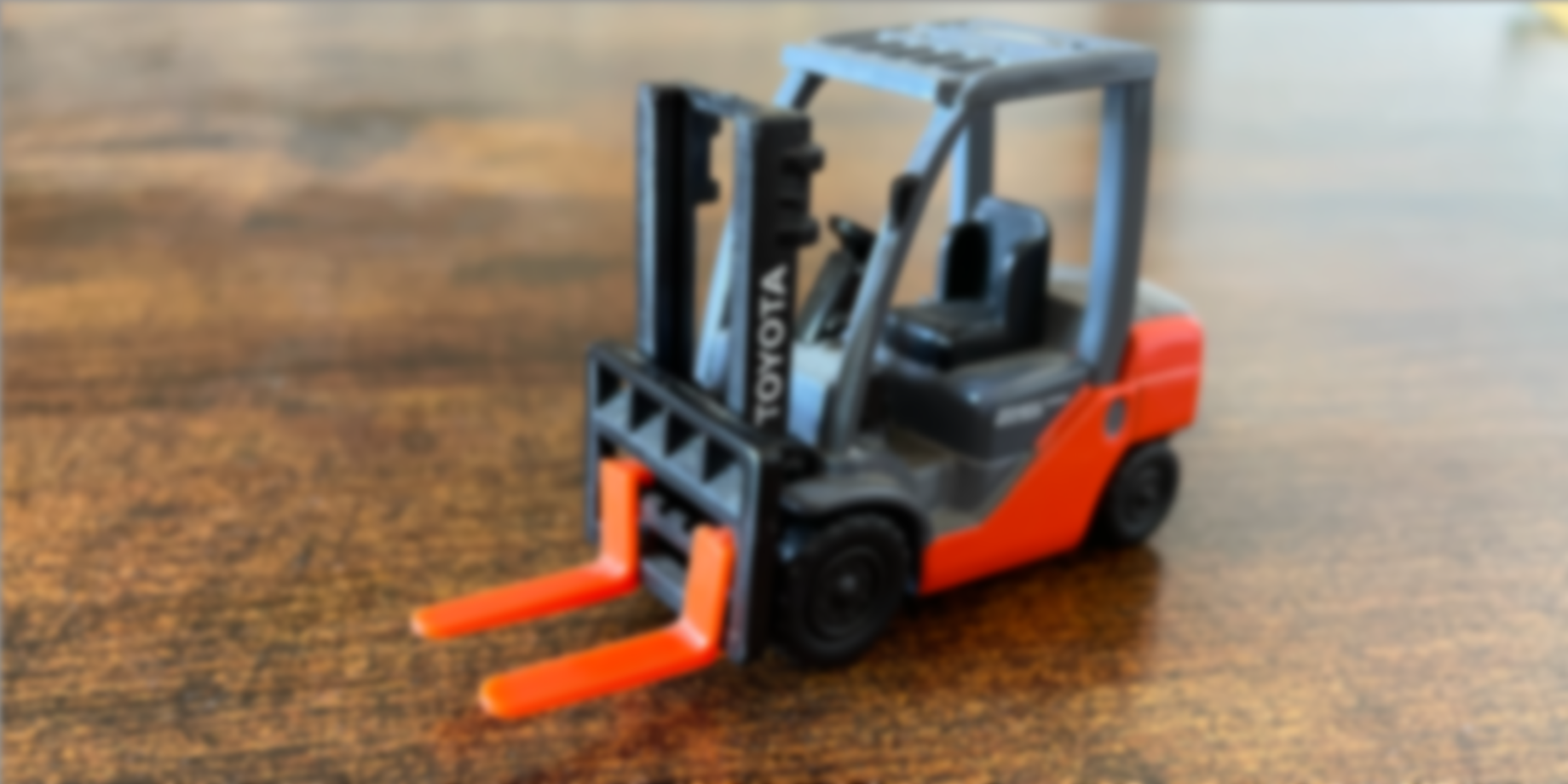
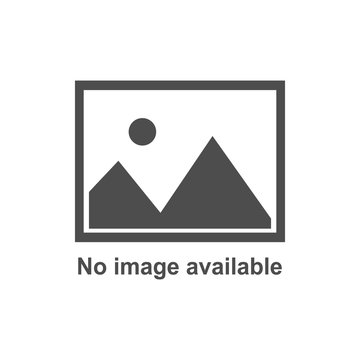
INTERVIEW – The former executive of the Toyota Material Handling plant in Italy reflects on how Sadao Nomura’s “Dantotsu” method helped them to drastically improve quality.