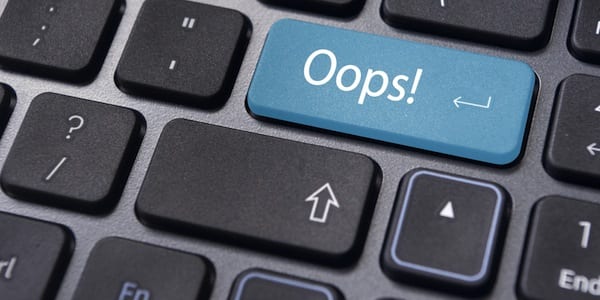
Looking at waste from an IT point of view
COLUMN - For those working in the I.T. world, identifying waste can be tricky. However, starting by tackling over-production will help you to eliminate every other form of waste.
Words: Rodrigo Aquino, Lean Institute Brasil
In 1937, while working at Toyoda Automatic Loom Works, Taiichi Ohno heard a man say that the productivity of an American worker was nine times higher than a Japanese worker’s.
When, in 1945, Kiichiro Toyoda said the organization would catch up with the United States in three years (the car industry in Japan would not have survived otherwise, he claimed), Ohno found himself thinking about that gap in productivity. It was clear to him that the Japanese were doing something wrong and there was too much waste in Toyota’s processes.
If that waste could be eliminated, production would increase at once. This was Ohno’s assumption, which represented the moment the Toyota Production System was conceived.
As we know, Ohno saw seven types of waste: over-production, waiting, transportation, over-processing, inventory, motion, and defective products. He was certain that the complete elimination of these wastes would increase the efficiency of operations. To start, Toyota started to produce only what was necessary – that is, it tackled over-production before anything else.
There are certain environments, however, where the seven wastes are hard to detect. Unfortunately, IT is one of them. So what to do?
In his book Lean IT, Steve Bell adapted the seven wastes to information technology, also comparing them to manufacturing and office environments, as shown in Figure 1 (at the end of the book, you can find more specific examples that can help to clarify these concepts).
{popup}
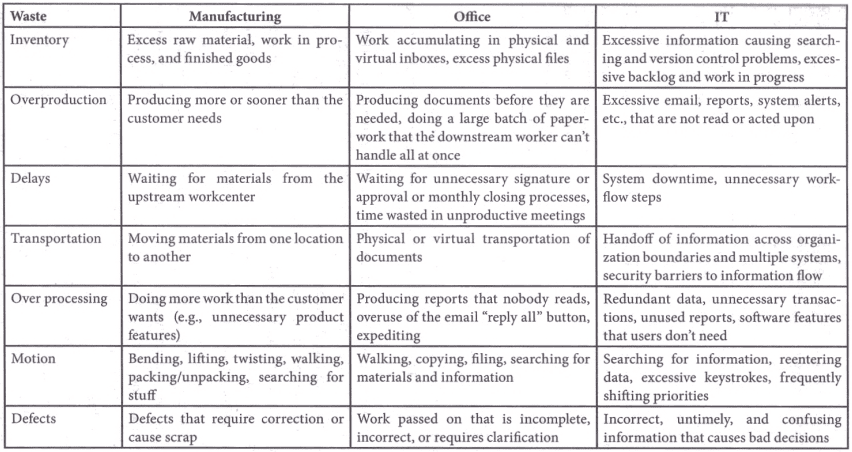
Comparing waste in manufacturing, office and IT. Source: Bell, C. S. and Orzen, A. M. (2011), Lean IT - Enabling and Sustaining Your Lean Transformation (p. 57). New York: CRC Press
Steve also describes lean IT as based on two dimensions: one is outward-facing, to improve management and business processes, while the other is inward-facing, using principles and tools to improve operations, services and software development.
It is important to clarify this separation in order to understand in which area of IT the wastes are occurring. In the box below I present some examples of waste, categorized as inward or outward.
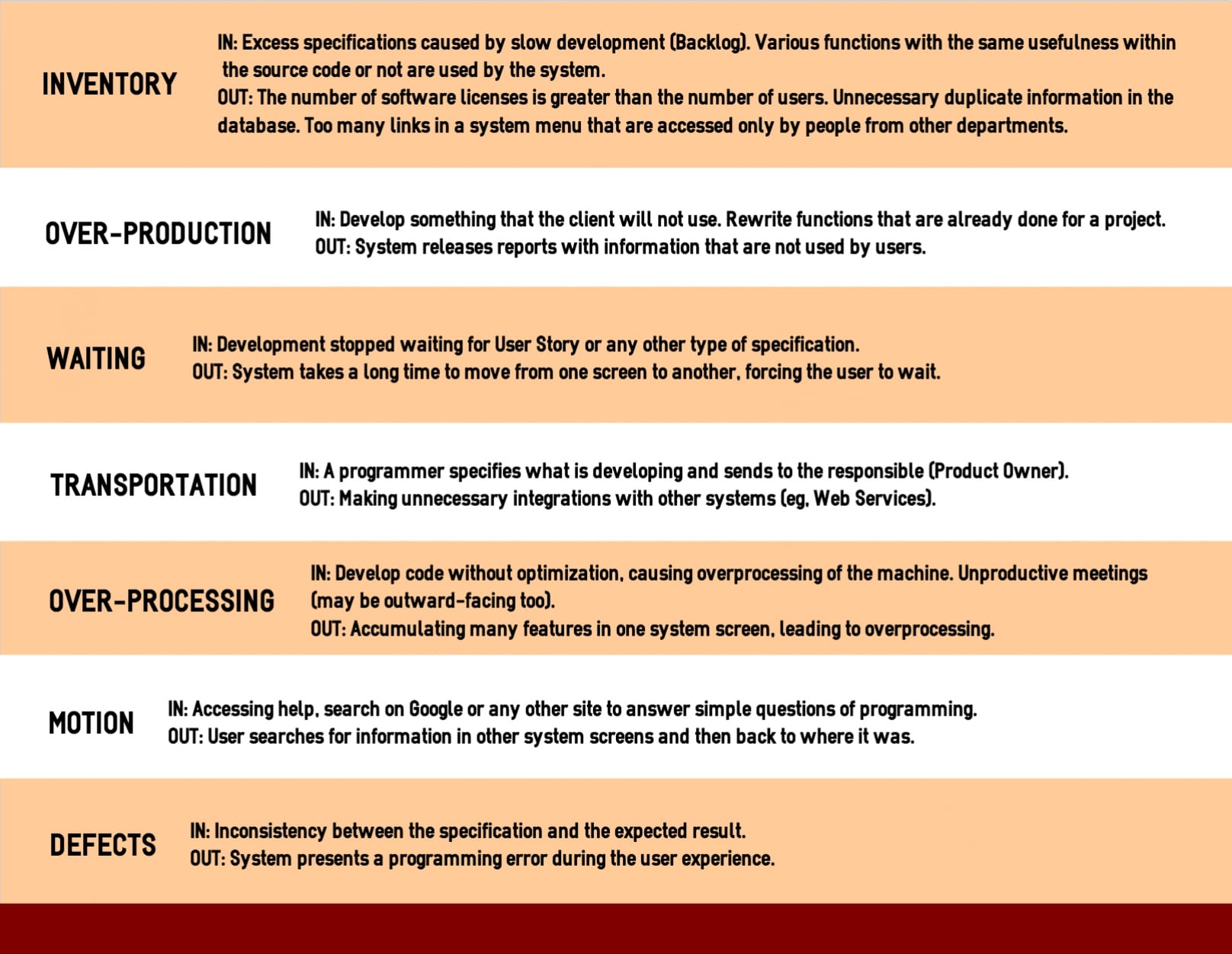
The worst waste in IT, manufacturing or office is indeed over-production, because with it come all the others.
Over-production is the first step towards creating awareness in people and towards facilitating the evolution of an organization. It’s what Toyota did when TPS was first introduced: starting with over-production, it tackled each one of the wastes.
To help a business improve, there is no need for supposedly revolutionary pieces of software or elaborate management systems. An unwavering resolve to tackle waste in its every form first will bring in the results.
As an example, imagine a factory that produces 200,000 pieces per month and manages to save two seconds per piece produced. The saving would be a staggering 111.11 hours: that would translate in less manpower deployed, less energy expenditure, and so on. After decreasing waste, cost reductions tend to follow naturally.
The same principle can be applied to an IT company if we take into consideration the amount of time wasted each day with unproductive meetings, phone calls, emails, etc. Calculate how much time this would be times the number of employees, consider a month's work, and you’ll see how big a number we are talking about.
No matter what type of organization you work for, understanding and eliminating waste is the core activity of any transformation.
THE AUTHOR
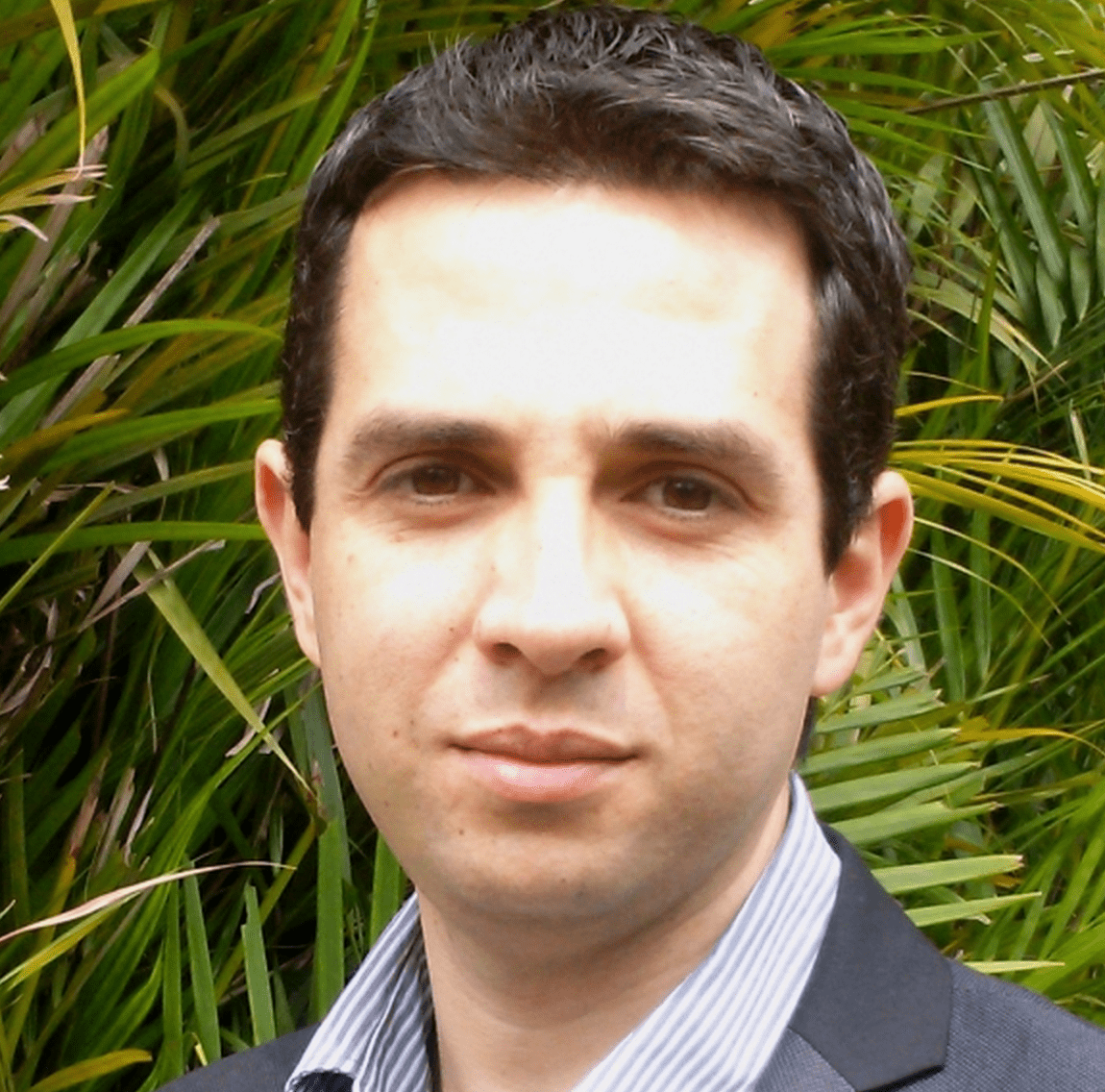
Rodrigo Aquino has worked in I.T. for 16 years. He holds an MBA in Software Engineering at University of São Paulo and is a graduate in Computer Science at the Pontifícia Universidade Católica de São Paulo. He's held the role of Coordinator of Information Technology at Lean Institute Brasil for over three years. He has worked with organizations including ICEC, Totvs, Wunderman, and Petrobras.
Read more
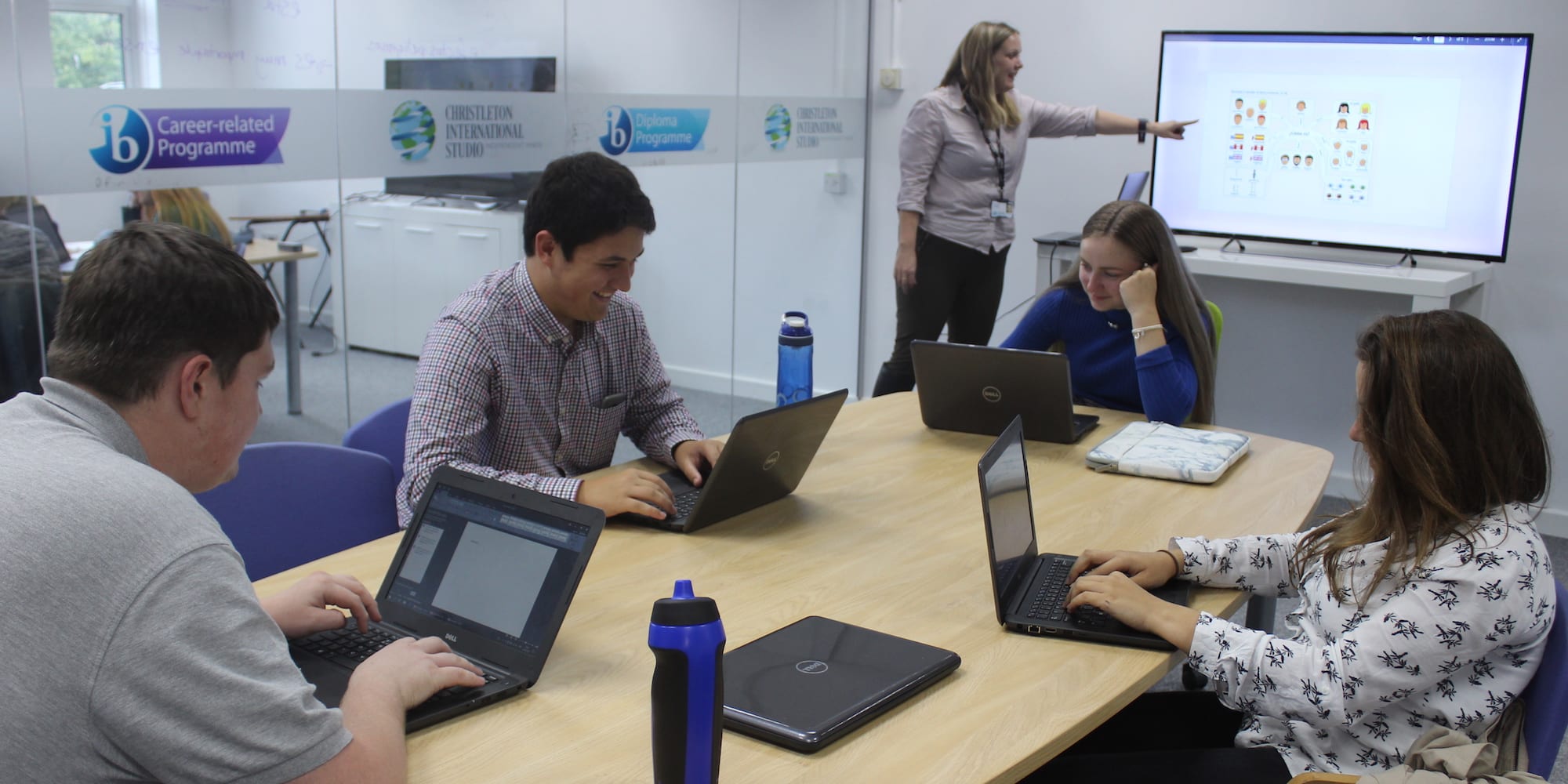
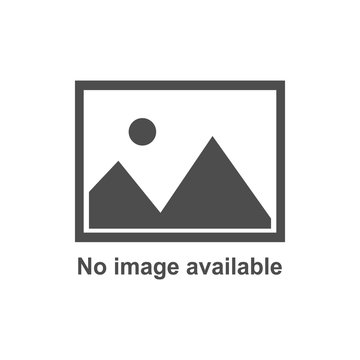
FEATURE – The application of lean management to education is not new, but we all know how hard changing legacy systems is. This greenfield lean school aims higher, trying to rethink learning altogether.
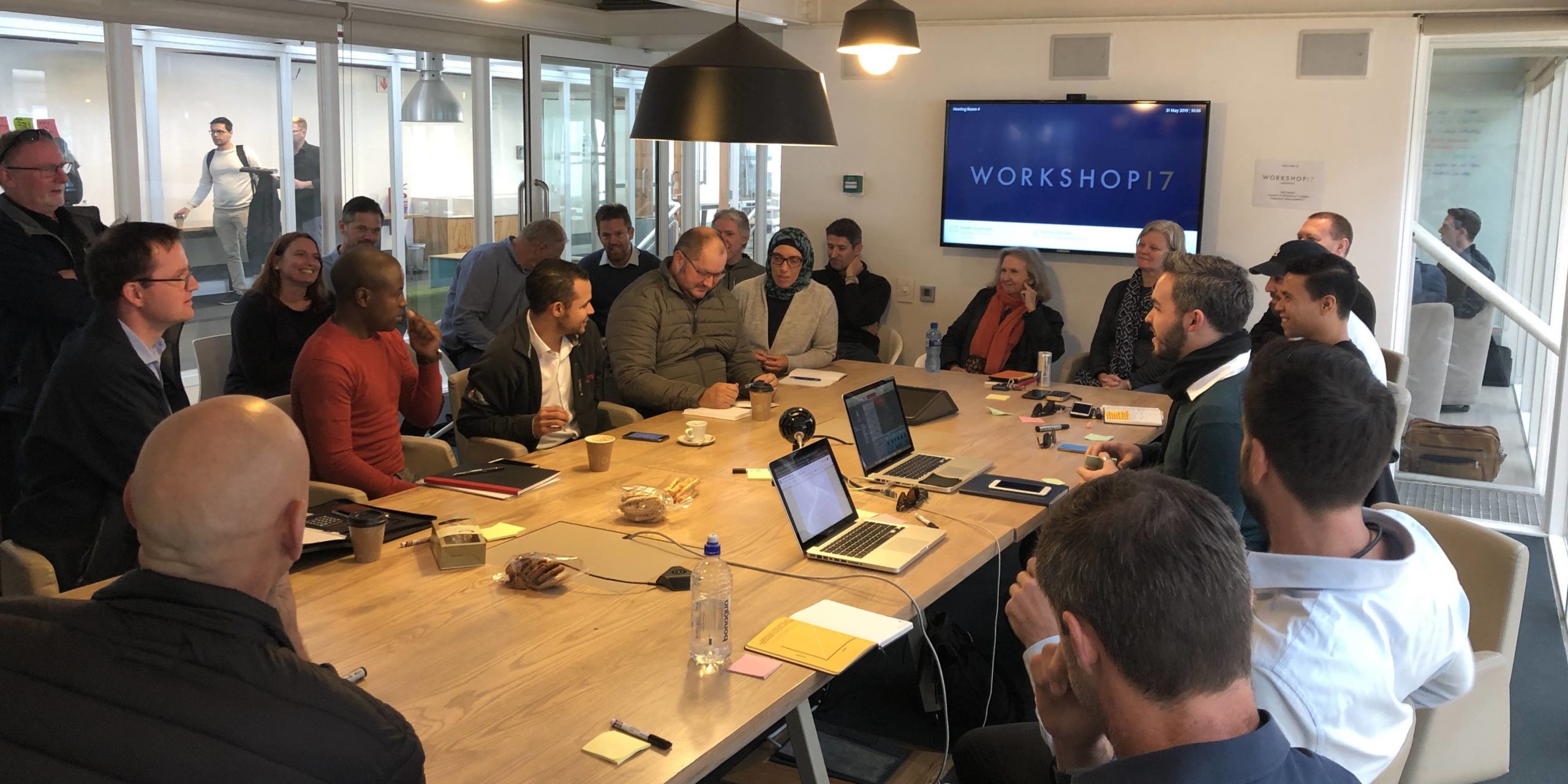
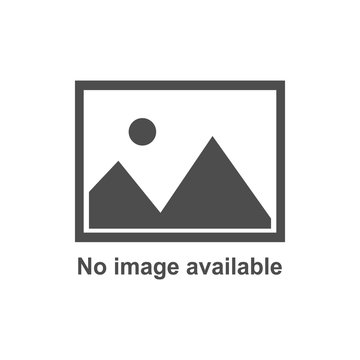
FEATURE – What started as the idea of two friends to meet up and discuss their lean journeys turned into a regular get-together of lean practitioners in the Cape Town area. Another example of the importance of sharing.
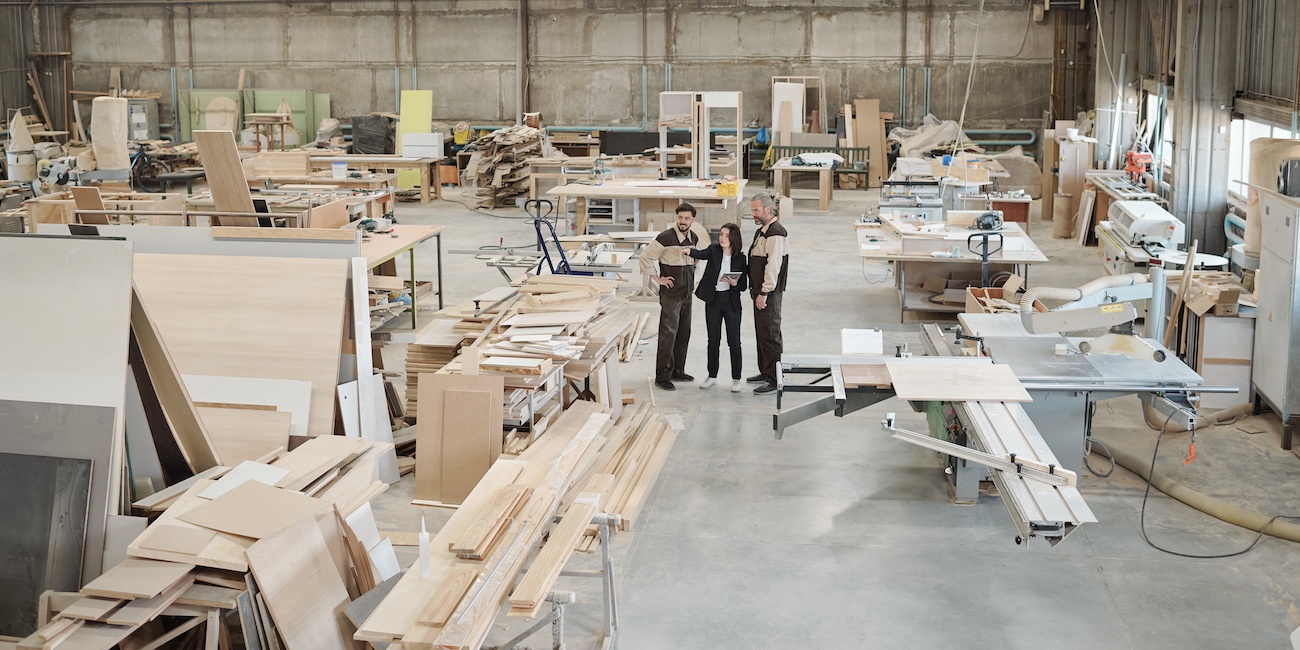
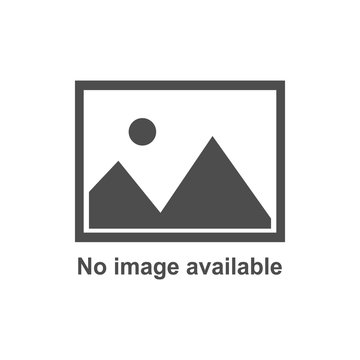
NOTES FROM THE GEMBA – What’s kaizen for? Improving quality? Generating a flow of ideas? Challenging a method? All of the above, so long as the underlying goal is to make people’s lives easier.
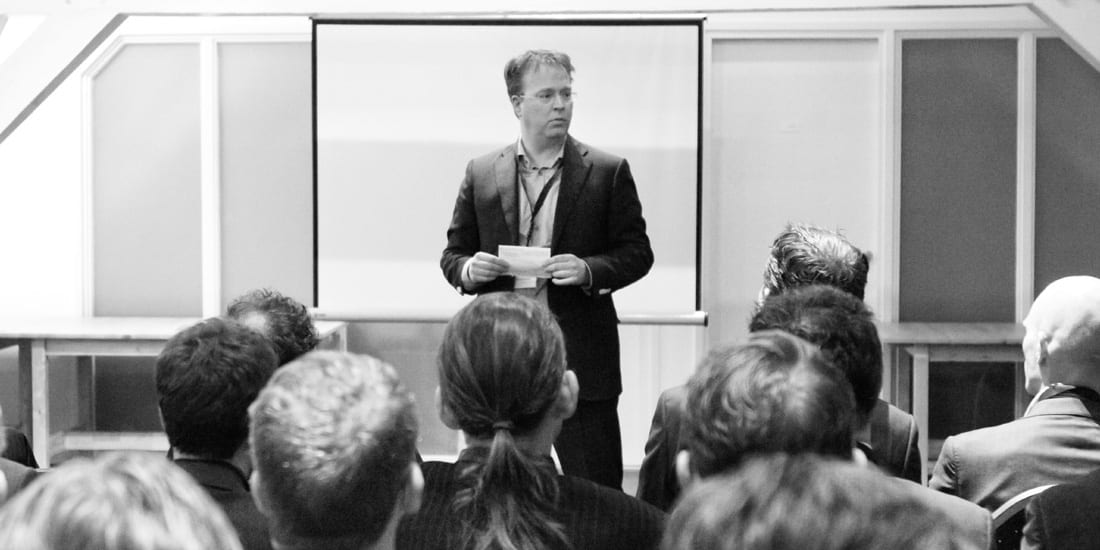
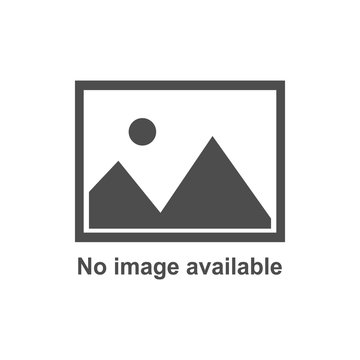
GETTING TO KNOW US – We continue our series of interviews with key Lean Global Network people with a chat with the President of Holland-based Lean Management Instituut.