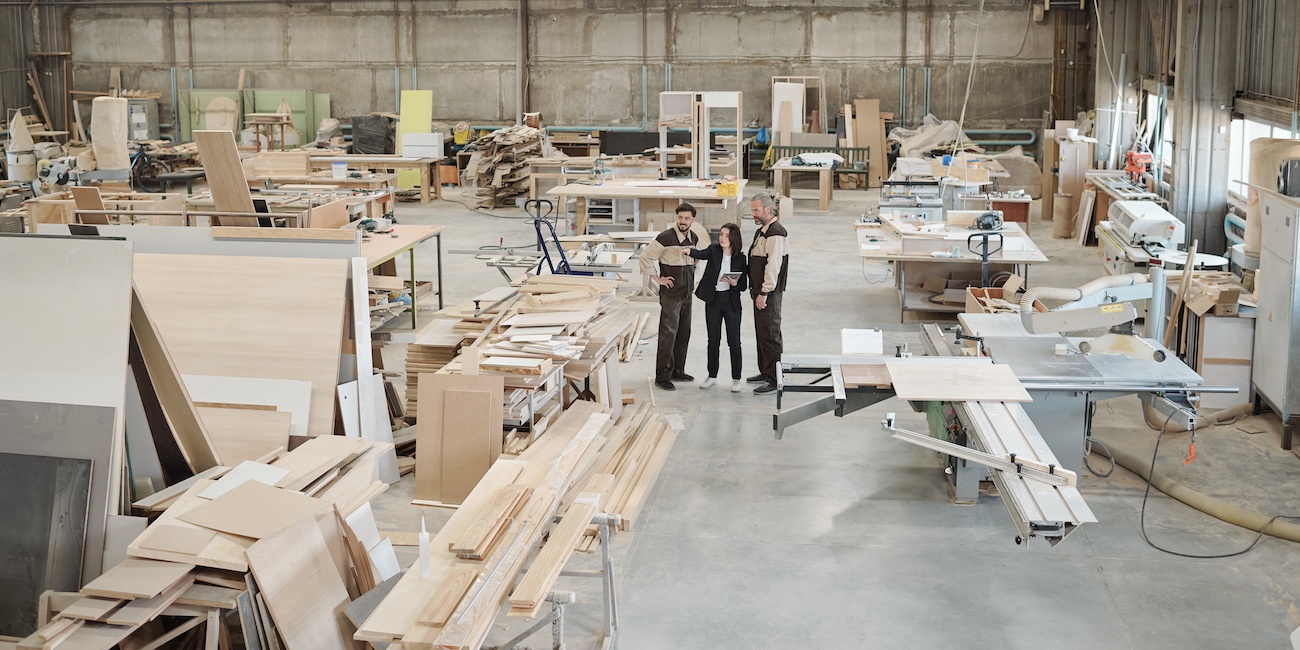
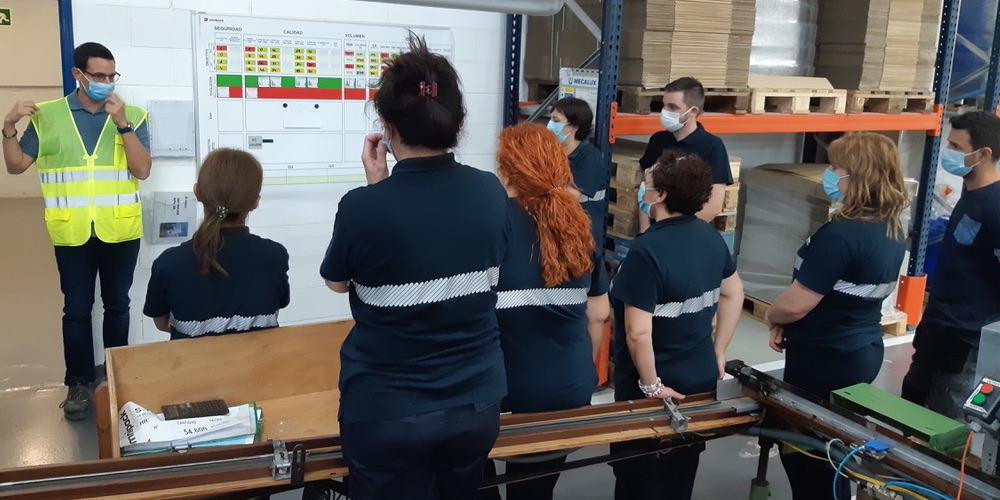
NOTES FROM THE GEMBA – What’s kaizen for? Improving quality? Generating a flow of ideas? Challenging a method? All of the above, so long as the underlying goal is to make people’s lives easier.
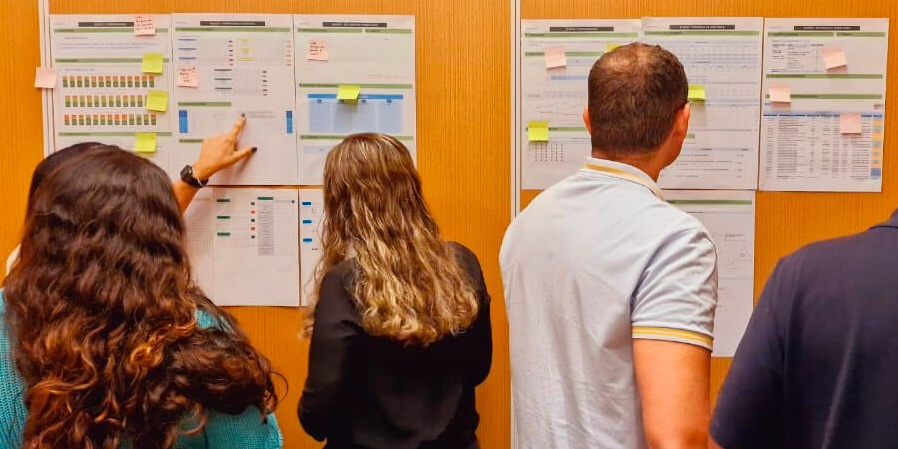
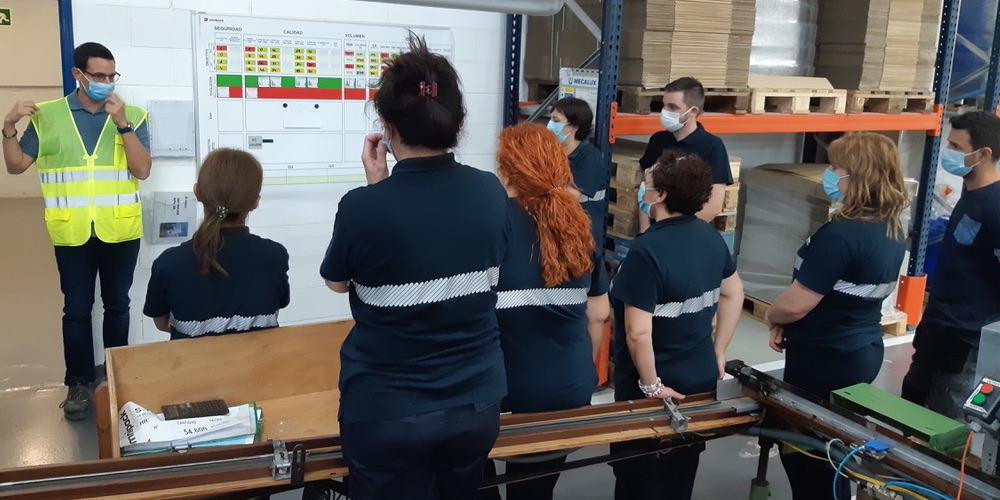
CASE STUDY – Learn how Knauf, a global provider of prefabricated materials, regained its sales leadership in Brazil, impressively optimized its performance indicators, and transformed people's mindset and behaviors.
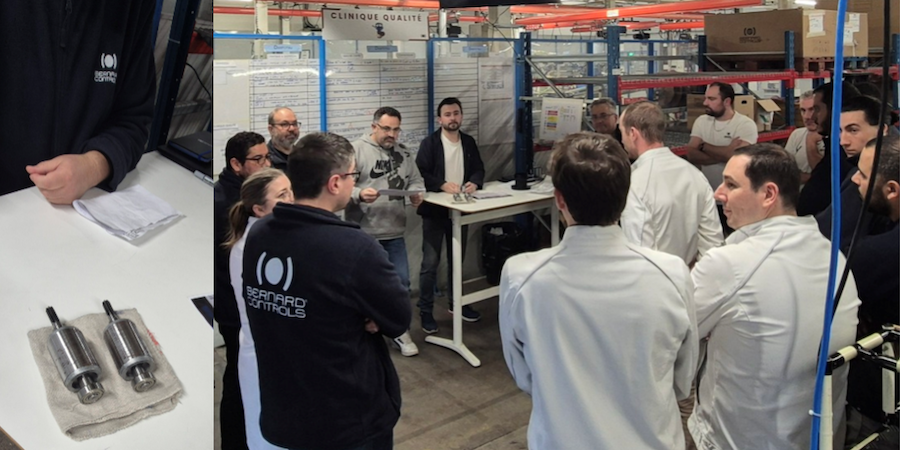
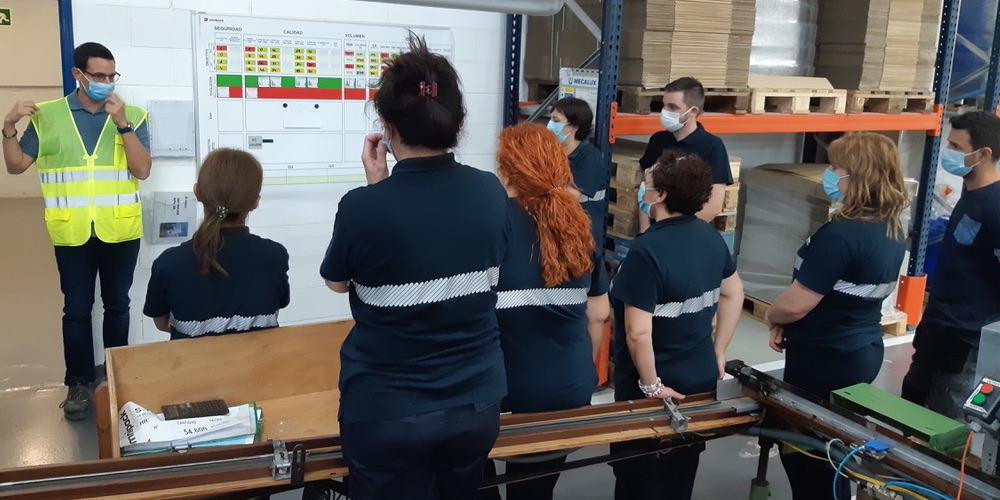
CASE STUDY – Lean Thinking helped Bernard Controls Europe improve efficiency, reduce lead times, and enhance quality, fostering resilience in the post-pandemic industrial landscape.
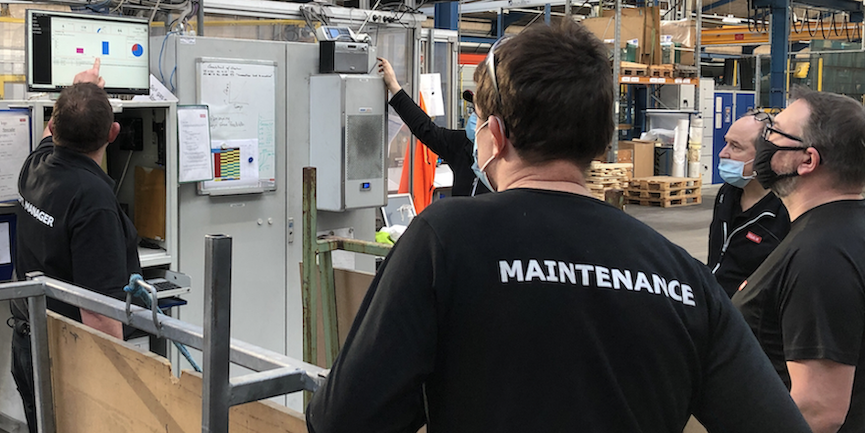
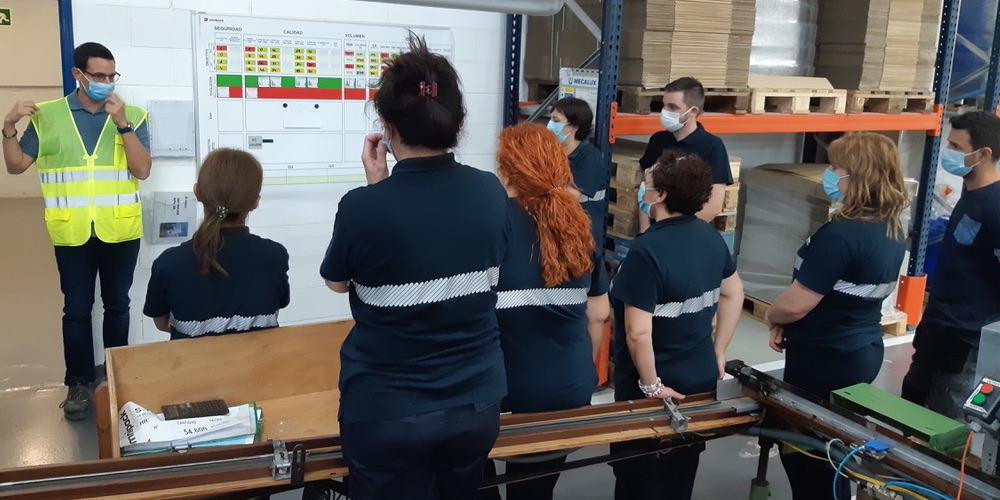
CASE STUDY – The authors discuss how rooftop window producer VELUX harnessed Lean Thinking and Industry 4.0 to empower shop floor workers, after rediscovering the kaizen spirit following a digitalization initiative that didn’t work out.
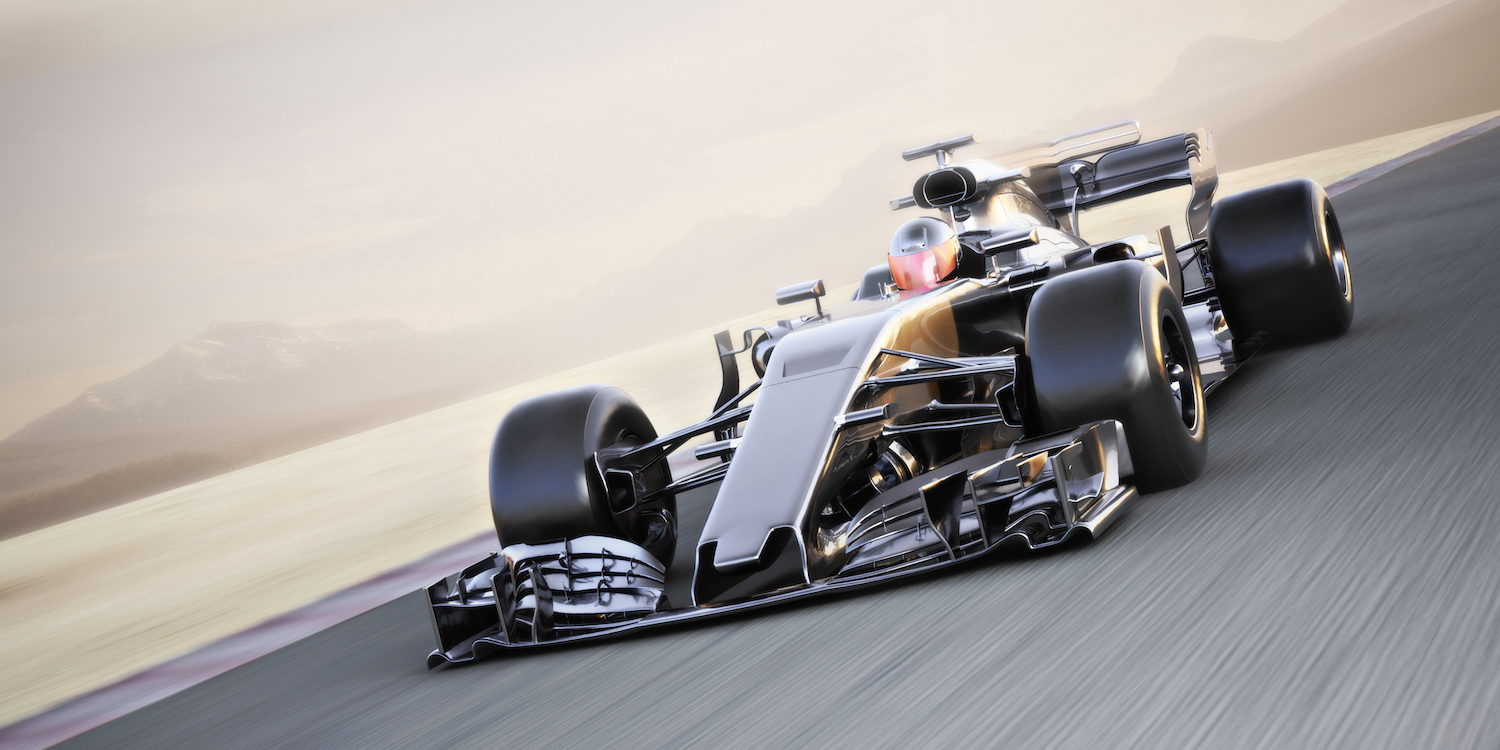
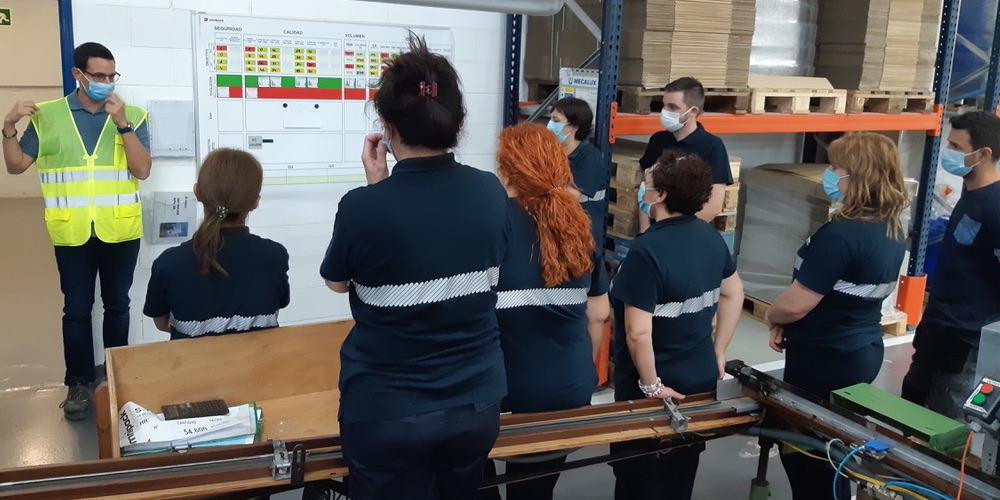
FEATURE – In part 2 of his article, the author unveils an improved process that allows this Hungarian company to replace machine parts with minimal production downtime.
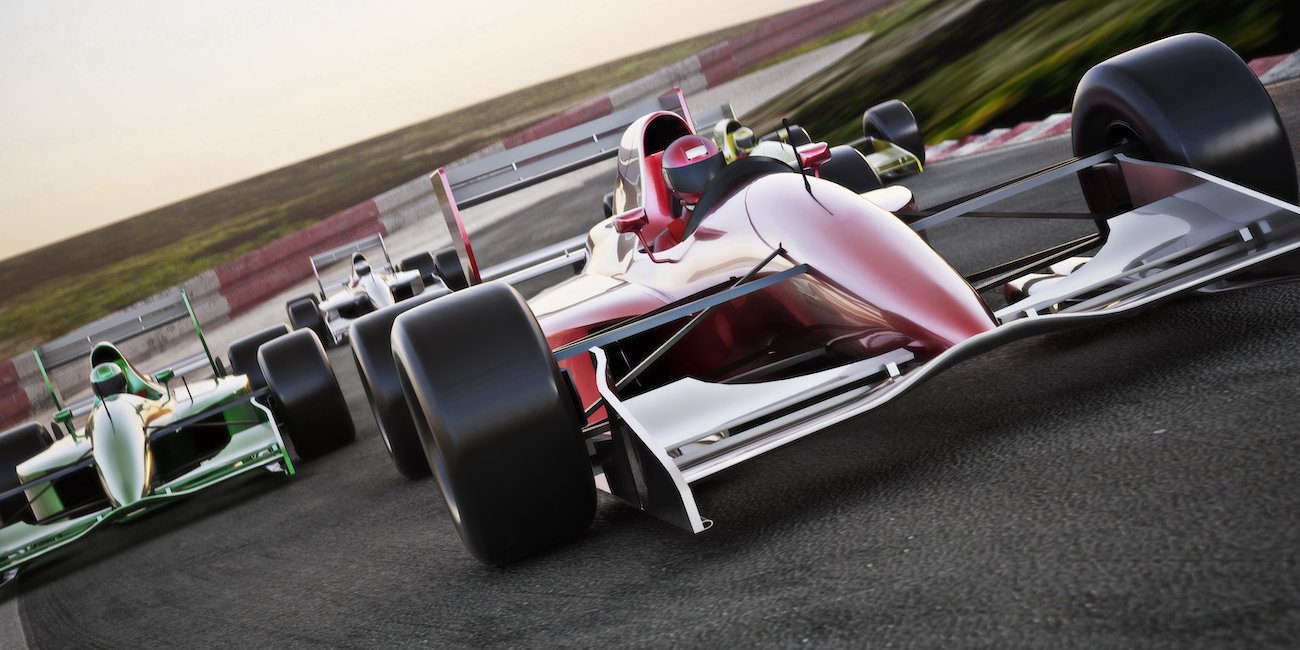
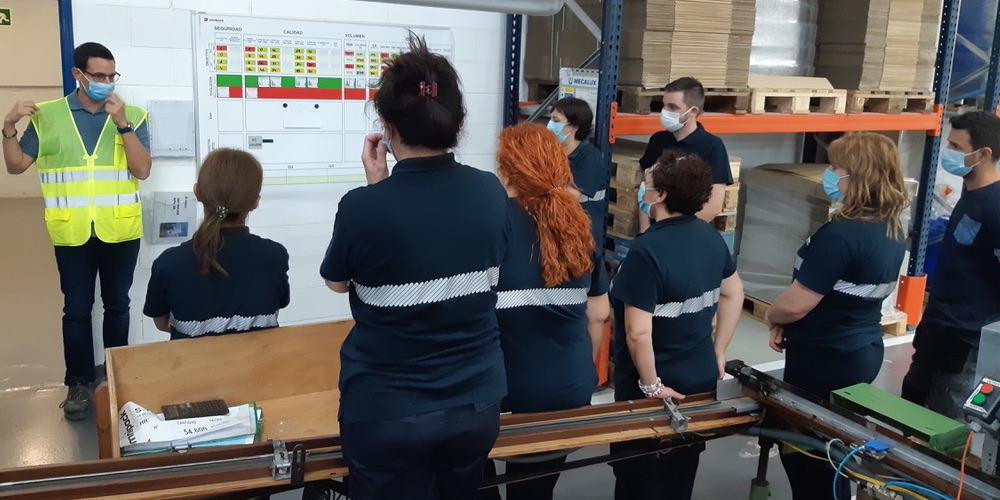
FEATURE – A situation that would be unthinkable in a sports context is an every-day occurrence in many of our organizations. Should we change our way of thinking about our machinery?
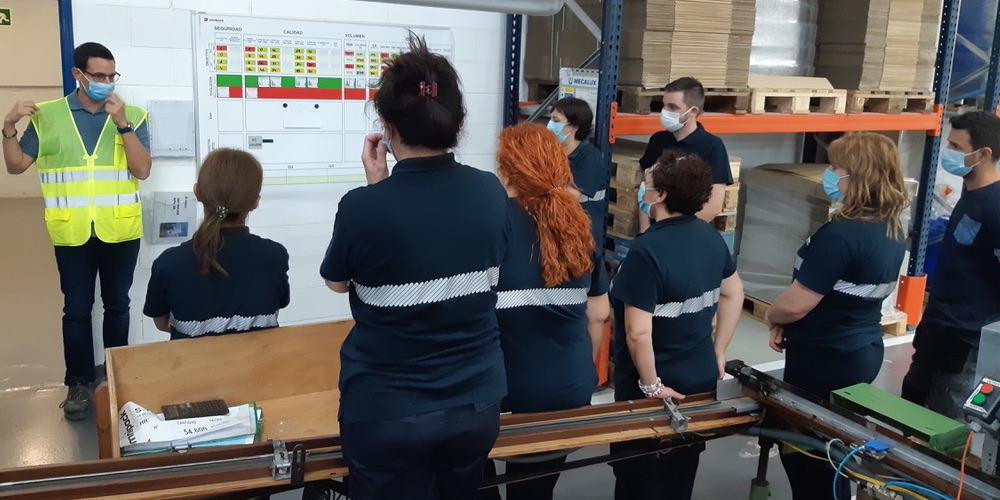
CASE STUDY – Faced with safety and quality issues, this Brazilian manufacturing plant installed a dojo, and the results are very promising.
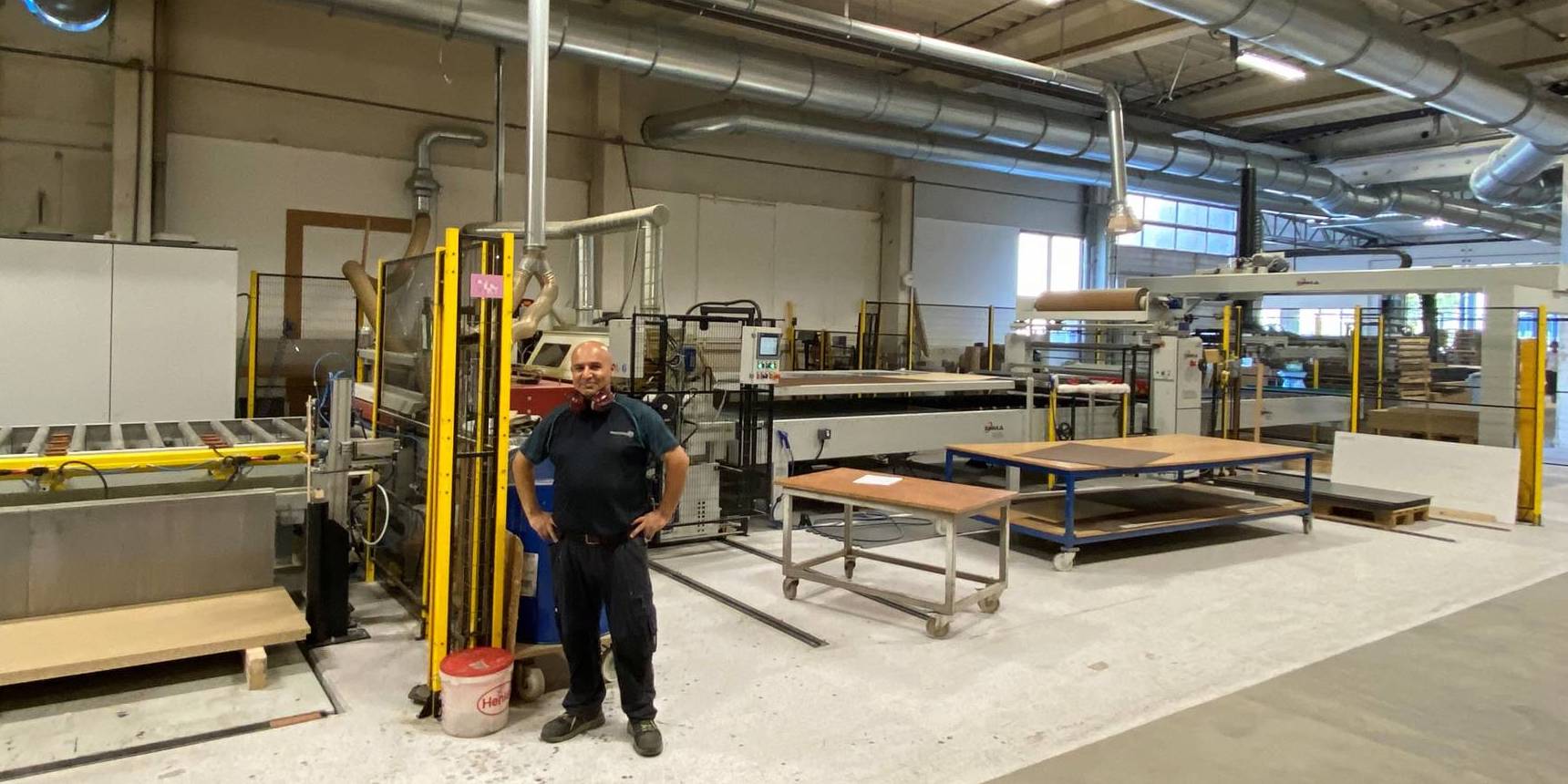
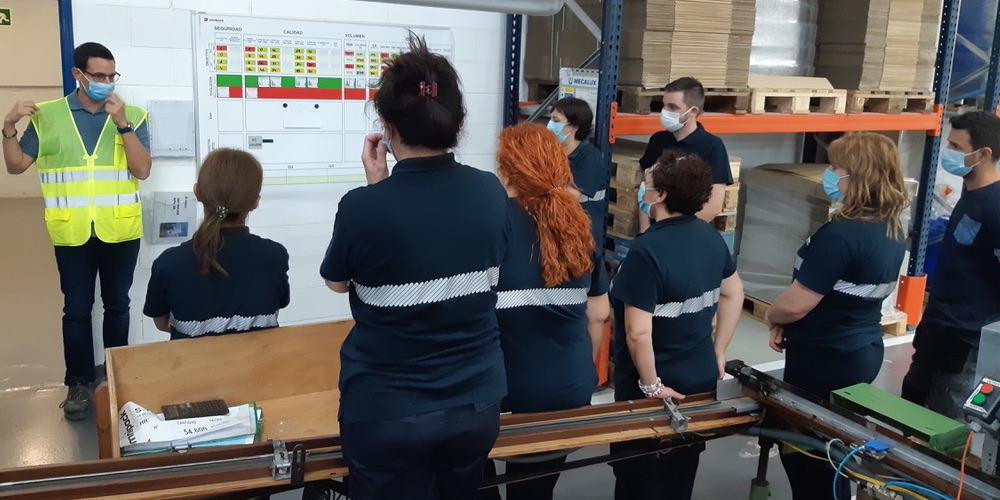
CASE STUDY – The story of Norwegian furniture manufacturer Haugstad Møbel that, thanks to Lean Thinking, was able to transform its culture and unlock the potential of sustainable growth.
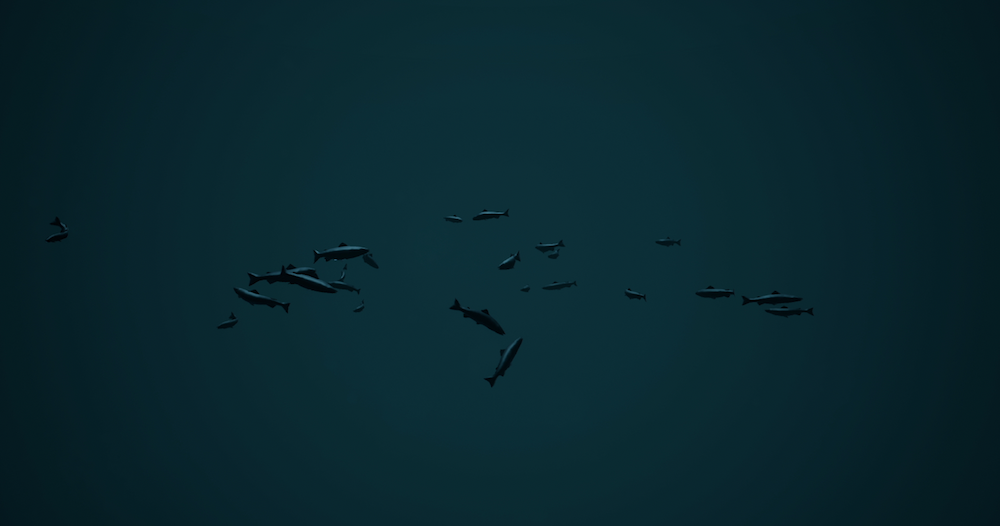
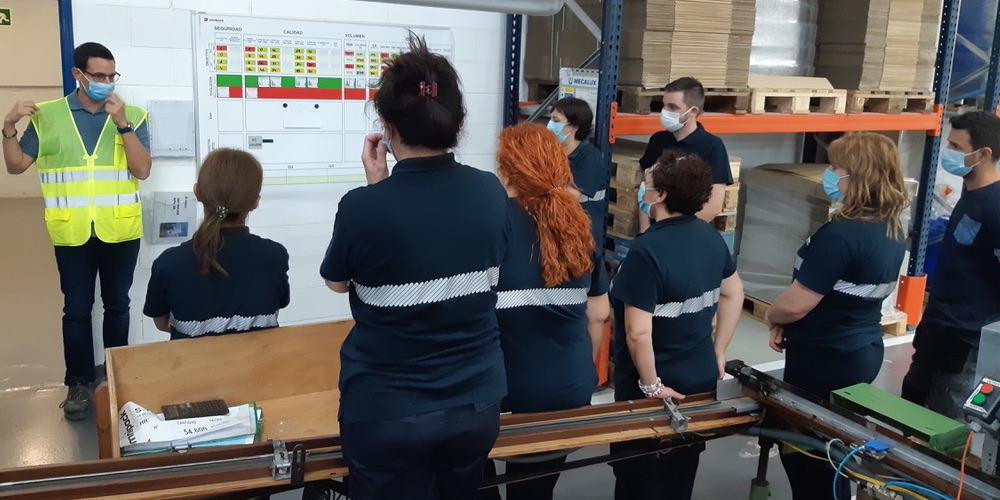
WEB SERIES - In this episode, we head to Chilean Patagonia to visit a manufacturer of fish feed that turned to Lean Thinking to improve yield and eliminate inventory gaps and stock-outs.
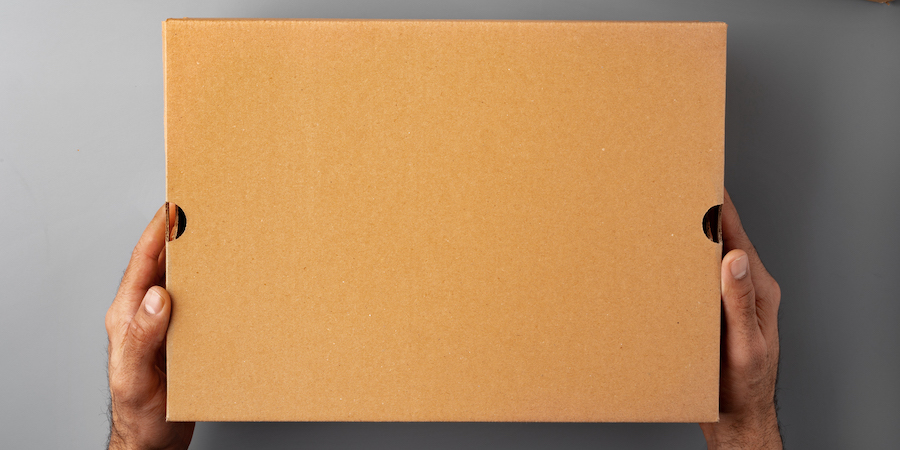
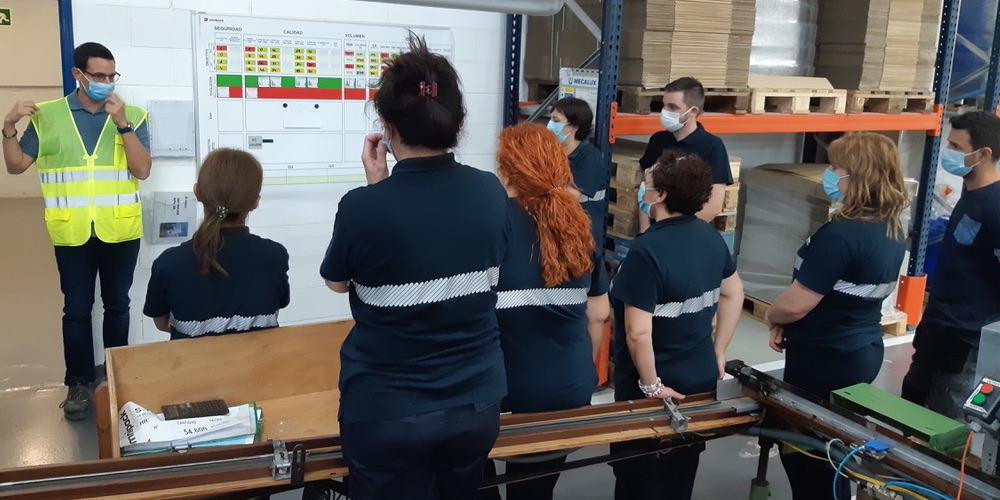
FEATURE – The author shares a story from a training session at the gemba, which contains a couple of important lessons on the Training Within Industry method.
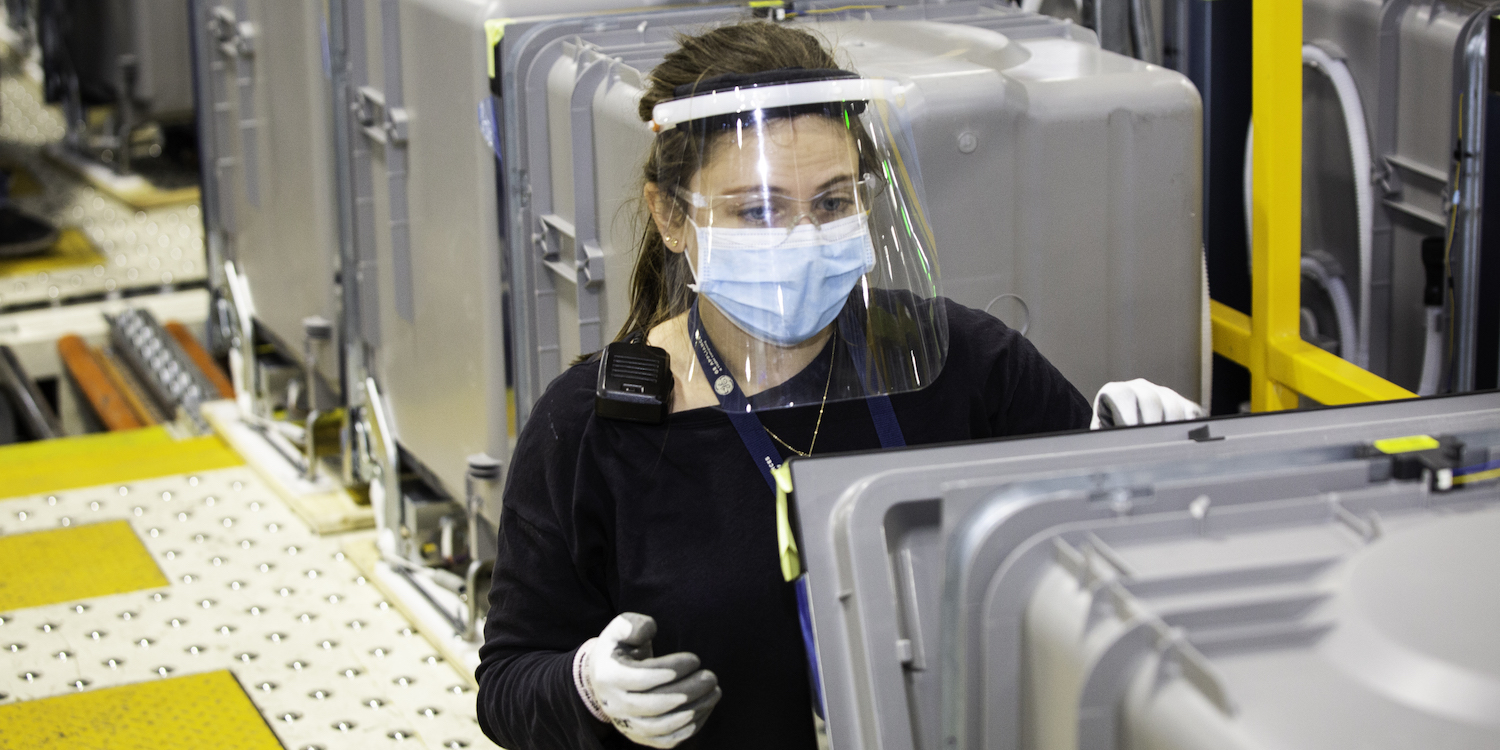
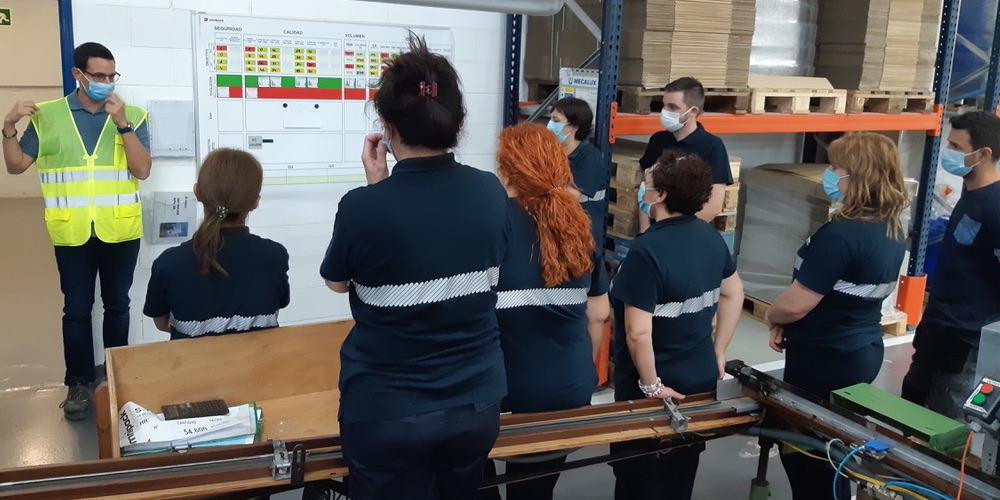
INTERVIEW – In 2020, GE Appliances had to stand up a brand-new assembly process for a new dishwasher. The leader responsible for the program explains how LPPD helped them to get it right.
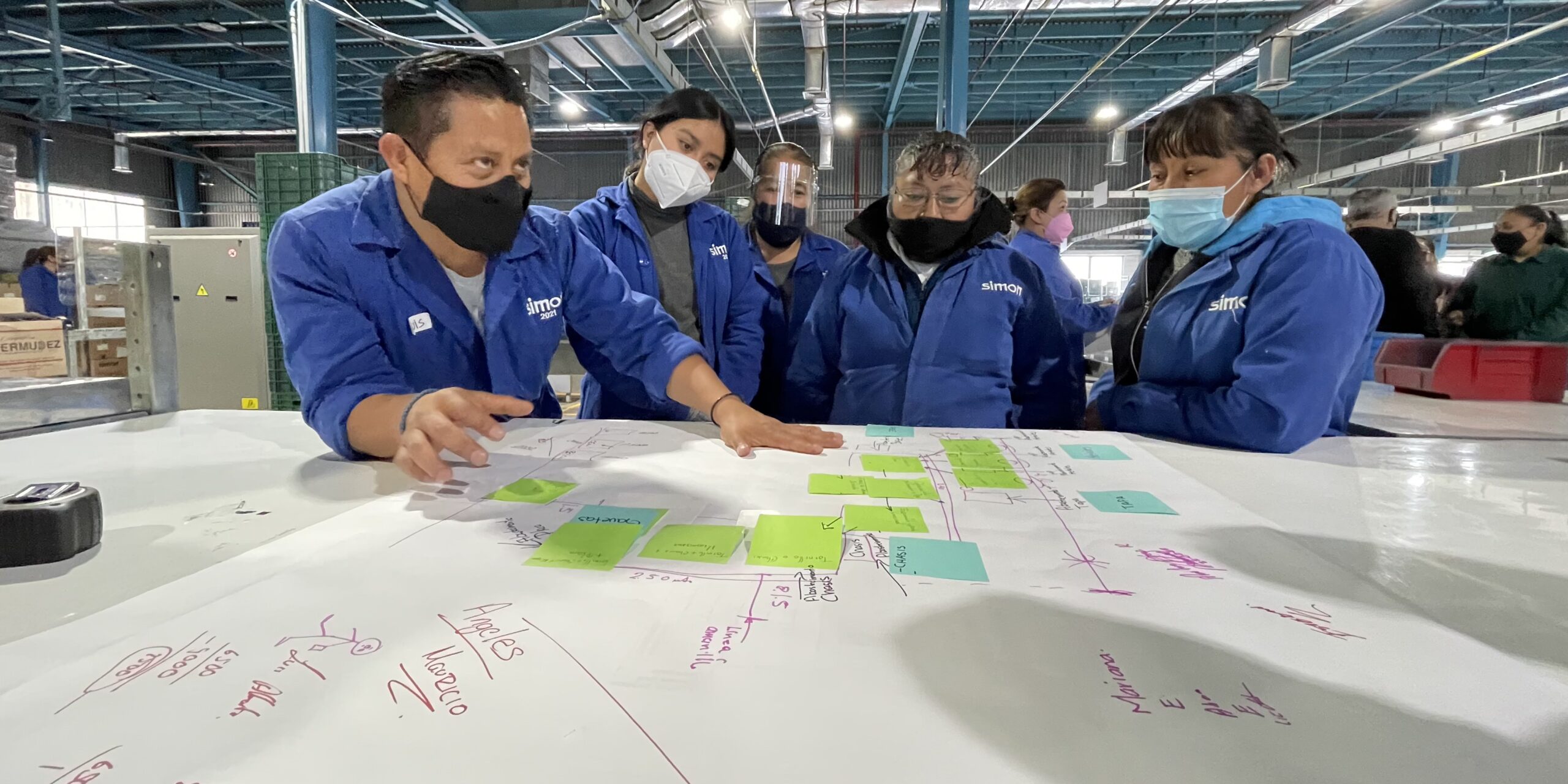
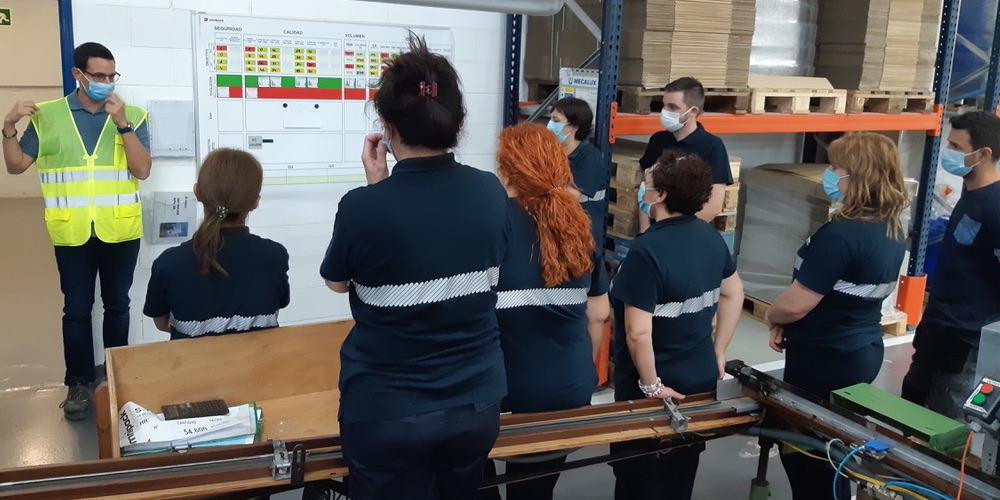
CASE STUDY – Starting in January this year, the Mexican plant of this manufacturer of lighting and electrical solutions has initiated a lean transformation that has already led to impressive results in terms of productivity.

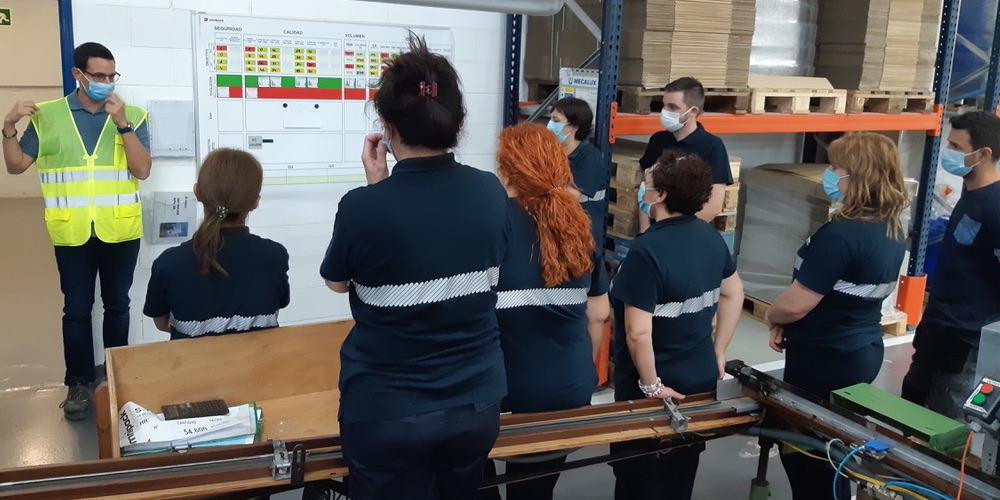
INTERVIEW – At last month’s International Lean Summit in Hungary, our editor sat down with the manager of a CooperVision site that is gradually converting its operations to make them leaner.
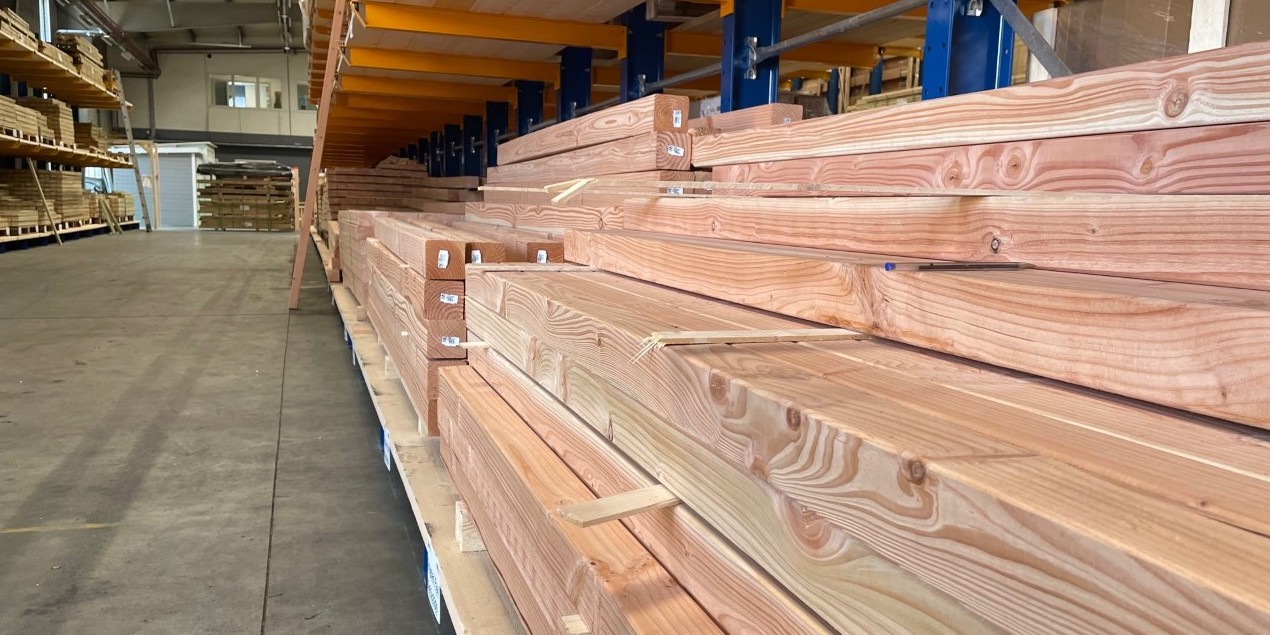
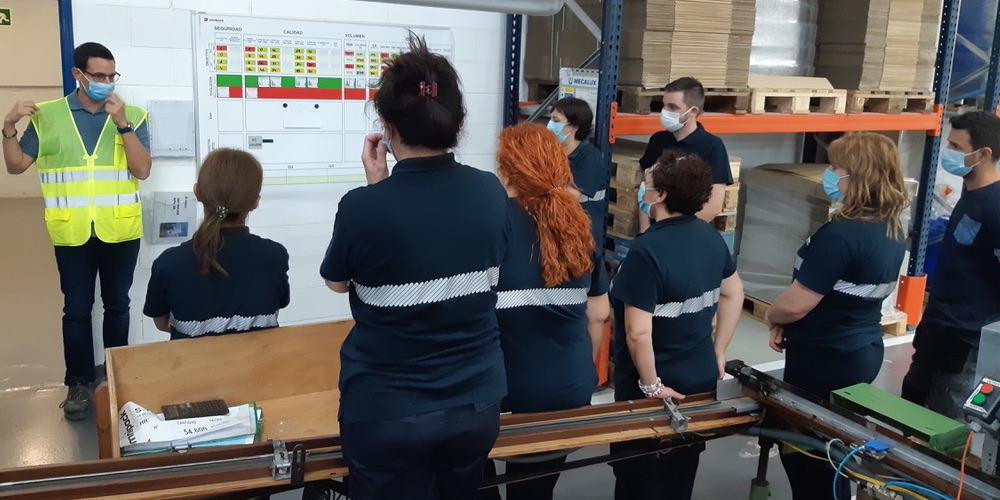
CASE STUDY – This Dutch SME is transforming its picking operation – partly with the introduction of a U-shaped design – to increase the number of orders it can fulfil every day.
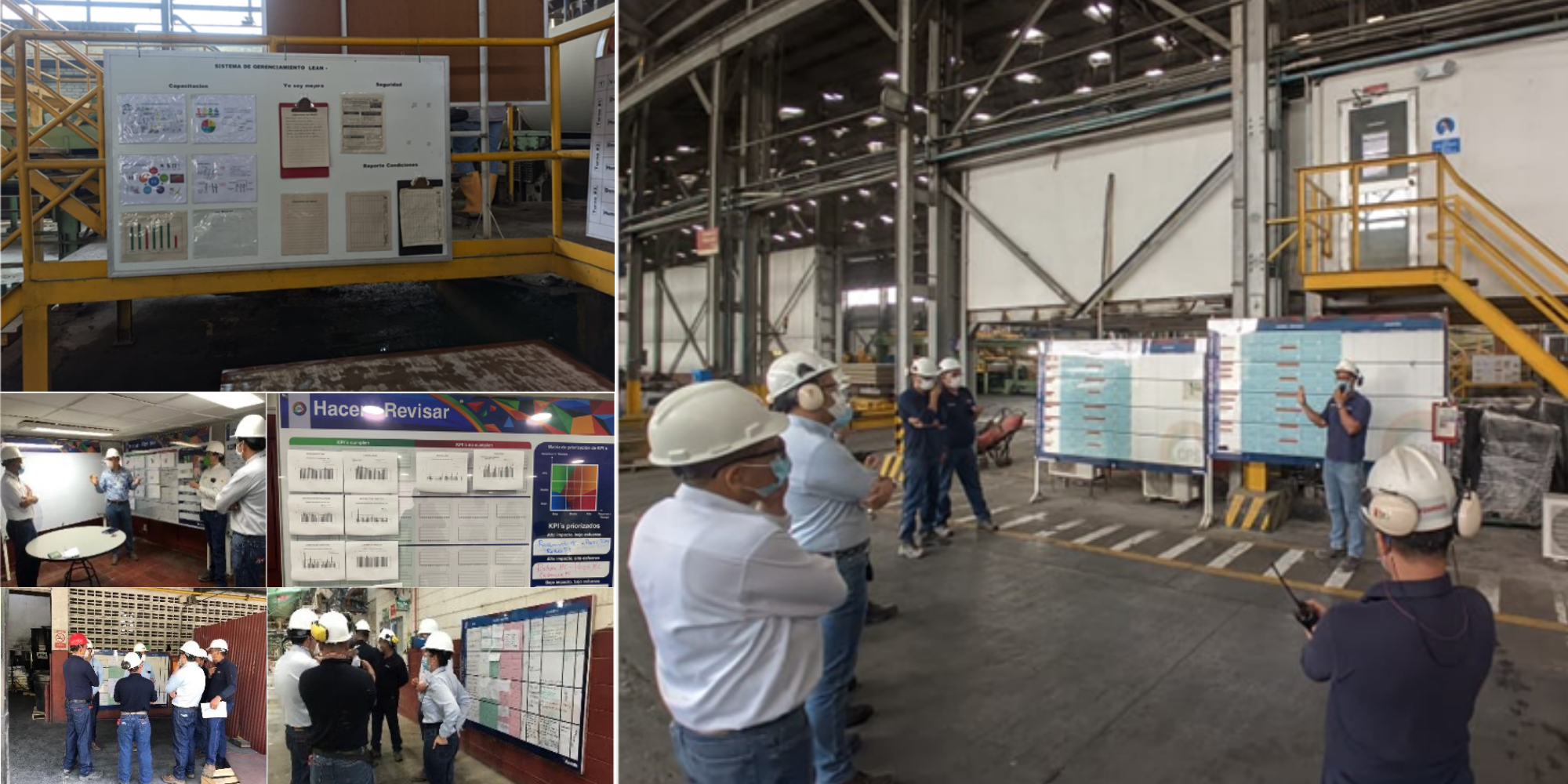
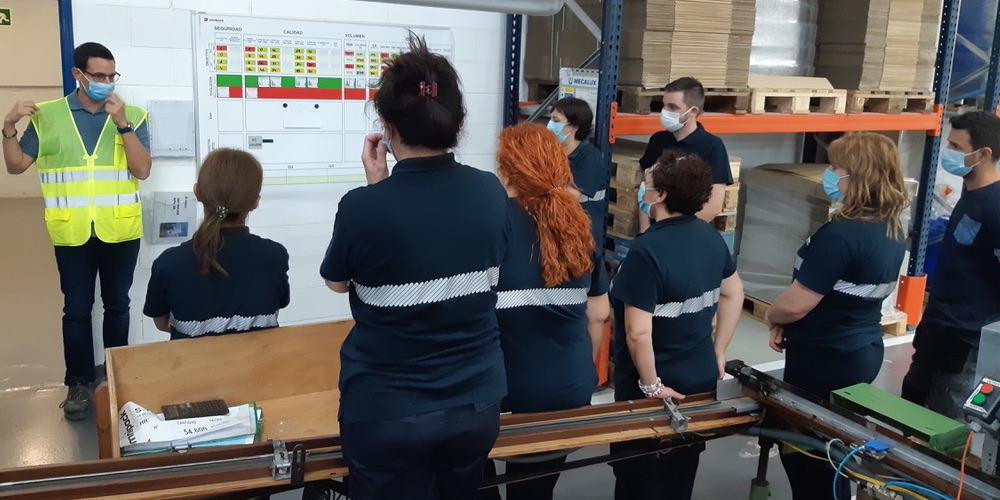
CASE STUDY – For the past year, Elementia Materiales, a producer of materials for the construction industry, has begun a lean journey that’s already brought impressive quality results.
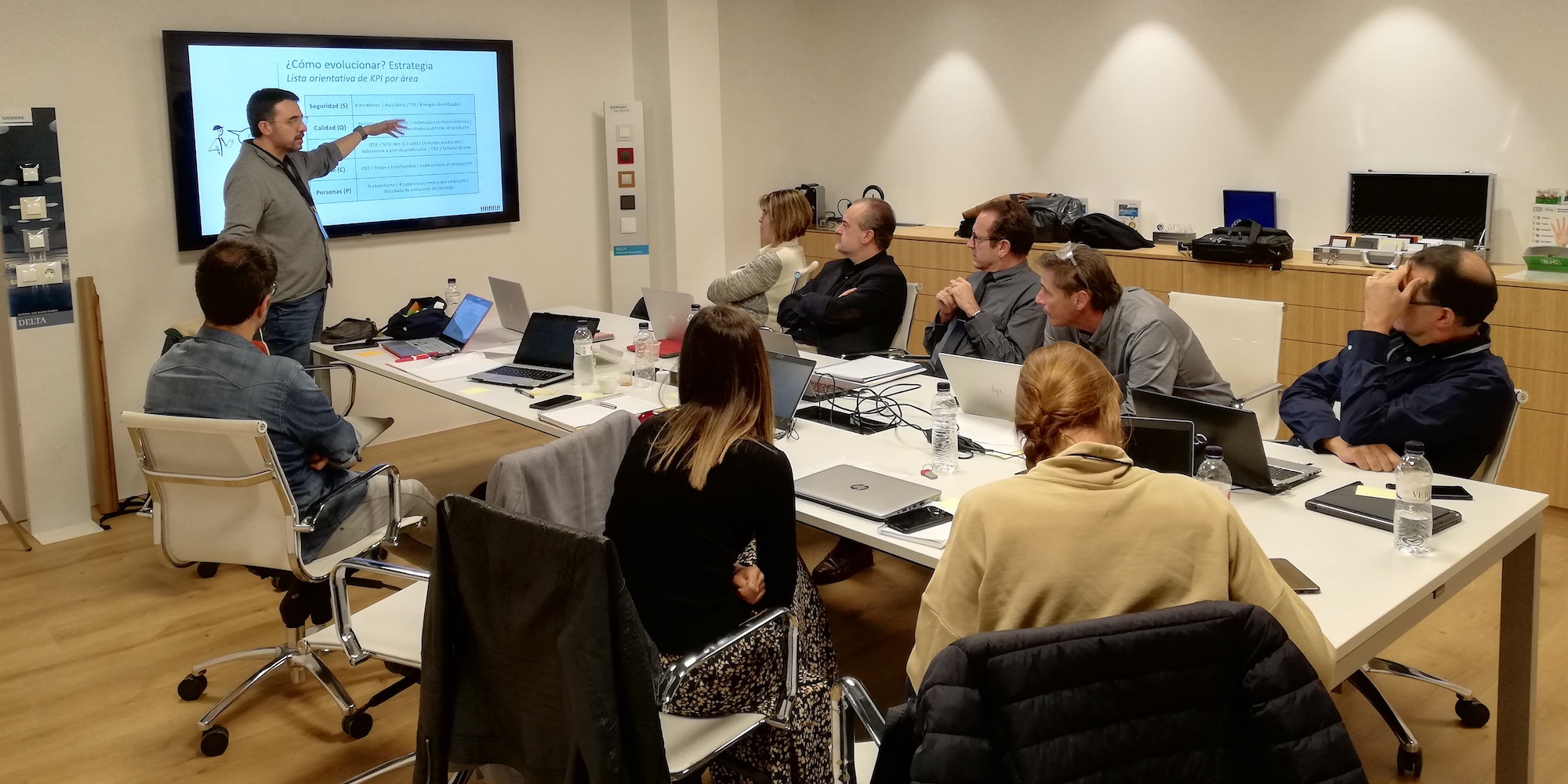
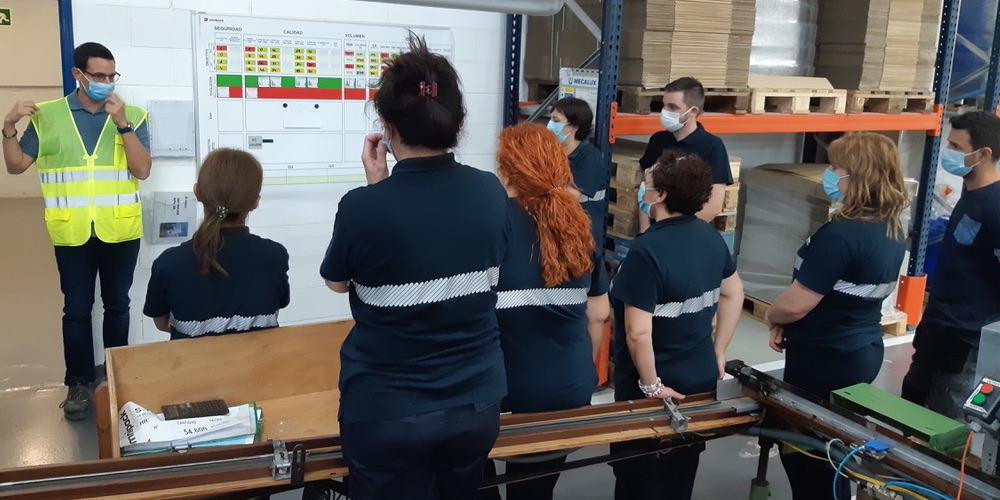
FEATURE – This Siemens Group-owned medium-sized manufacturer of electrical low-voltage devices has been experimenting with hoshin kanri. In this article, they share their experience and lessons learned.
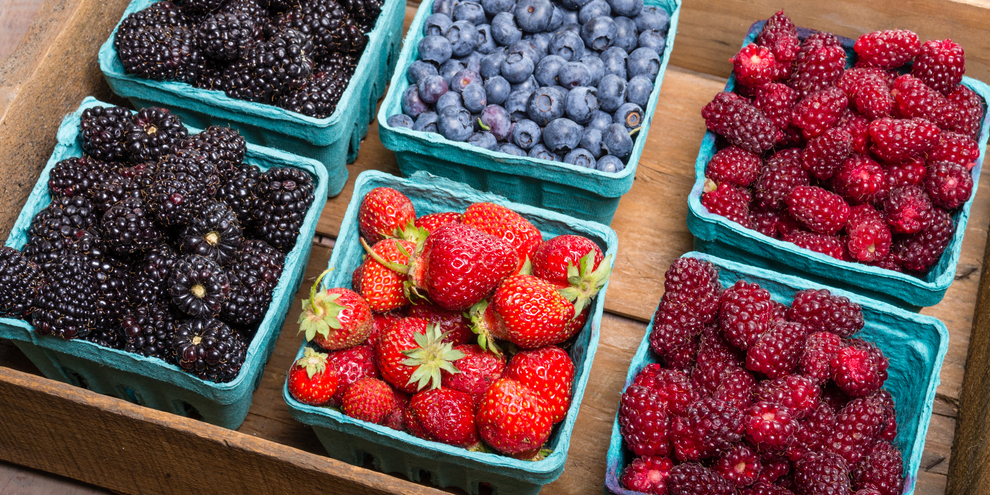
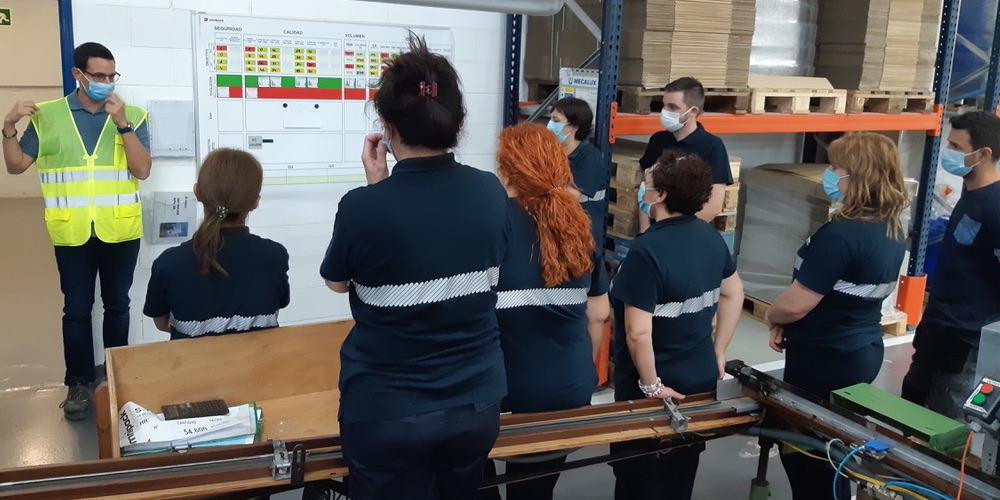
CASE STUDY – This Chilean agrobusiness company achieved great results in a very short time by applying lean to standardize its processes and improve its productivity. They are now berry fond of the methodology.
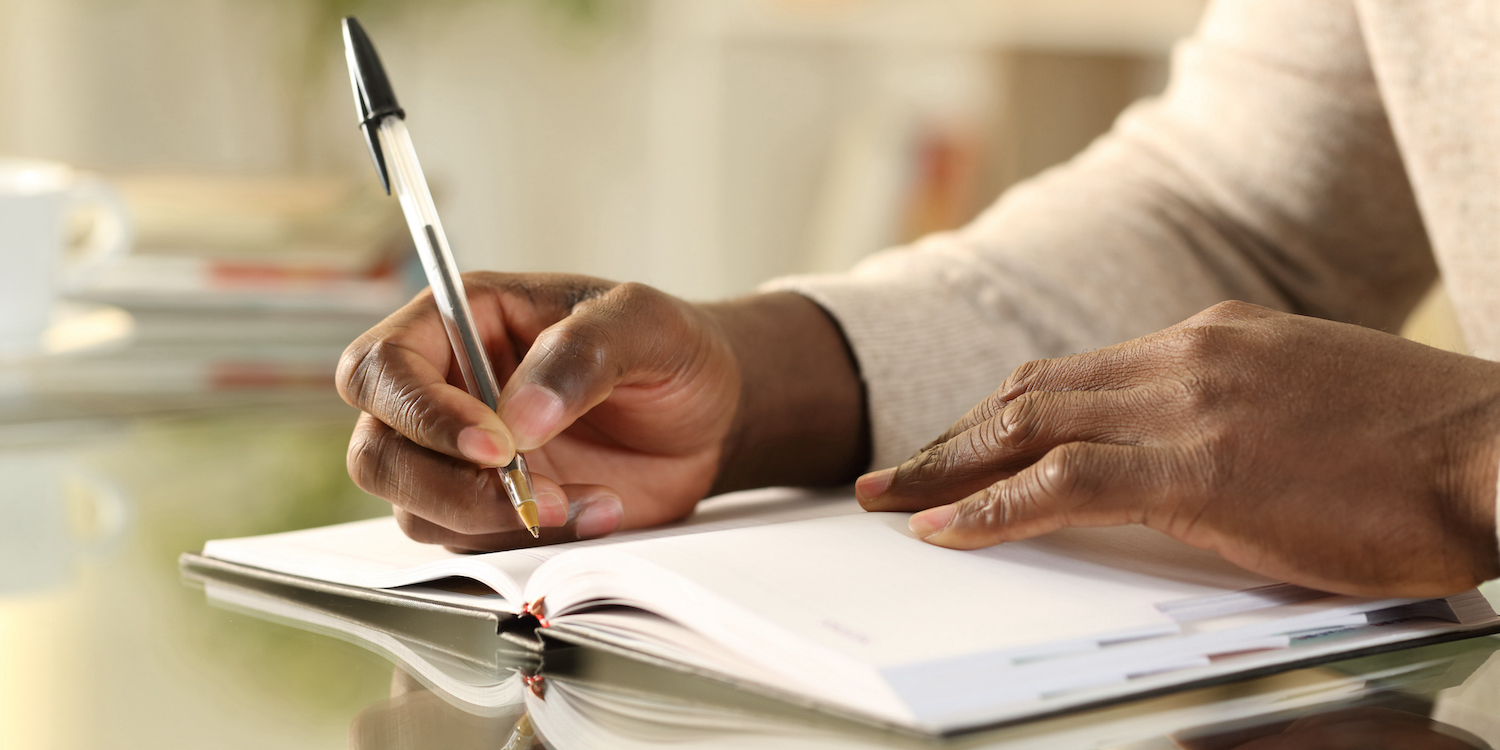
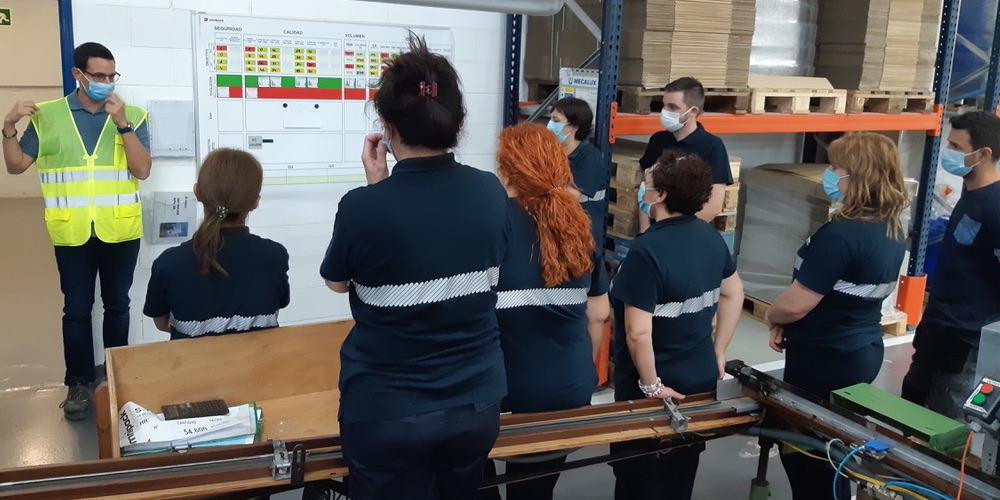
FEATURE – This Brazilian manufacturer was able to achieve significant improvements in its processes in just one week thanks to kaizen.
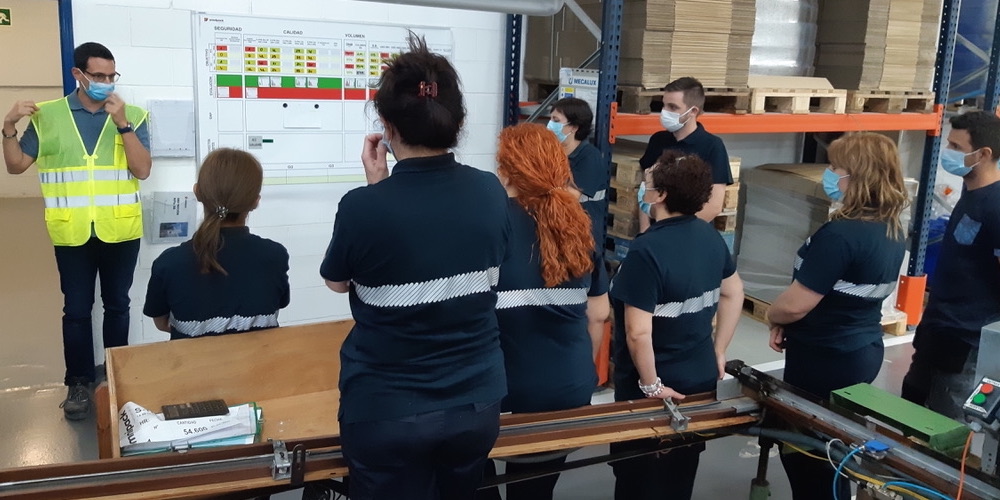
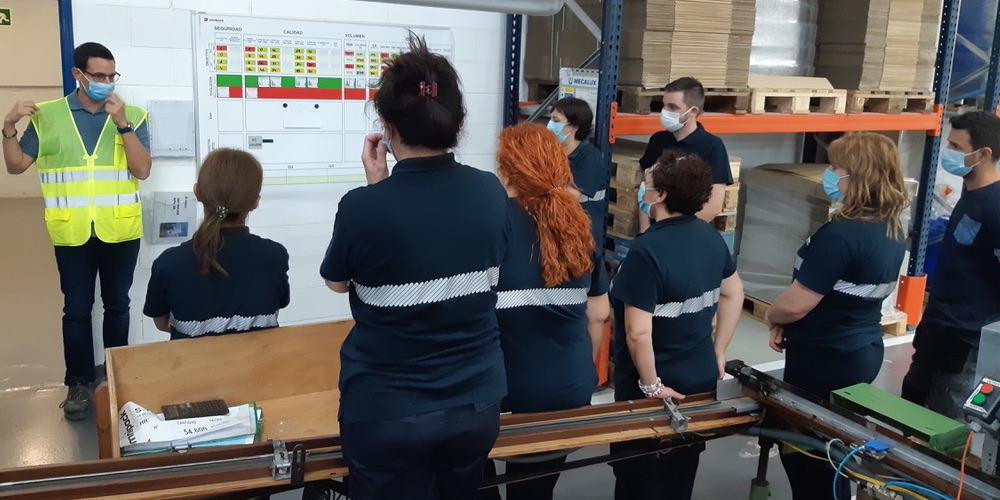
CASE STUDY – This packaging company in Catalonia has been able to cleverly balance the resolution of urgent problems and the advancement of the lean transformation. But what to do when the burning platform is no more?
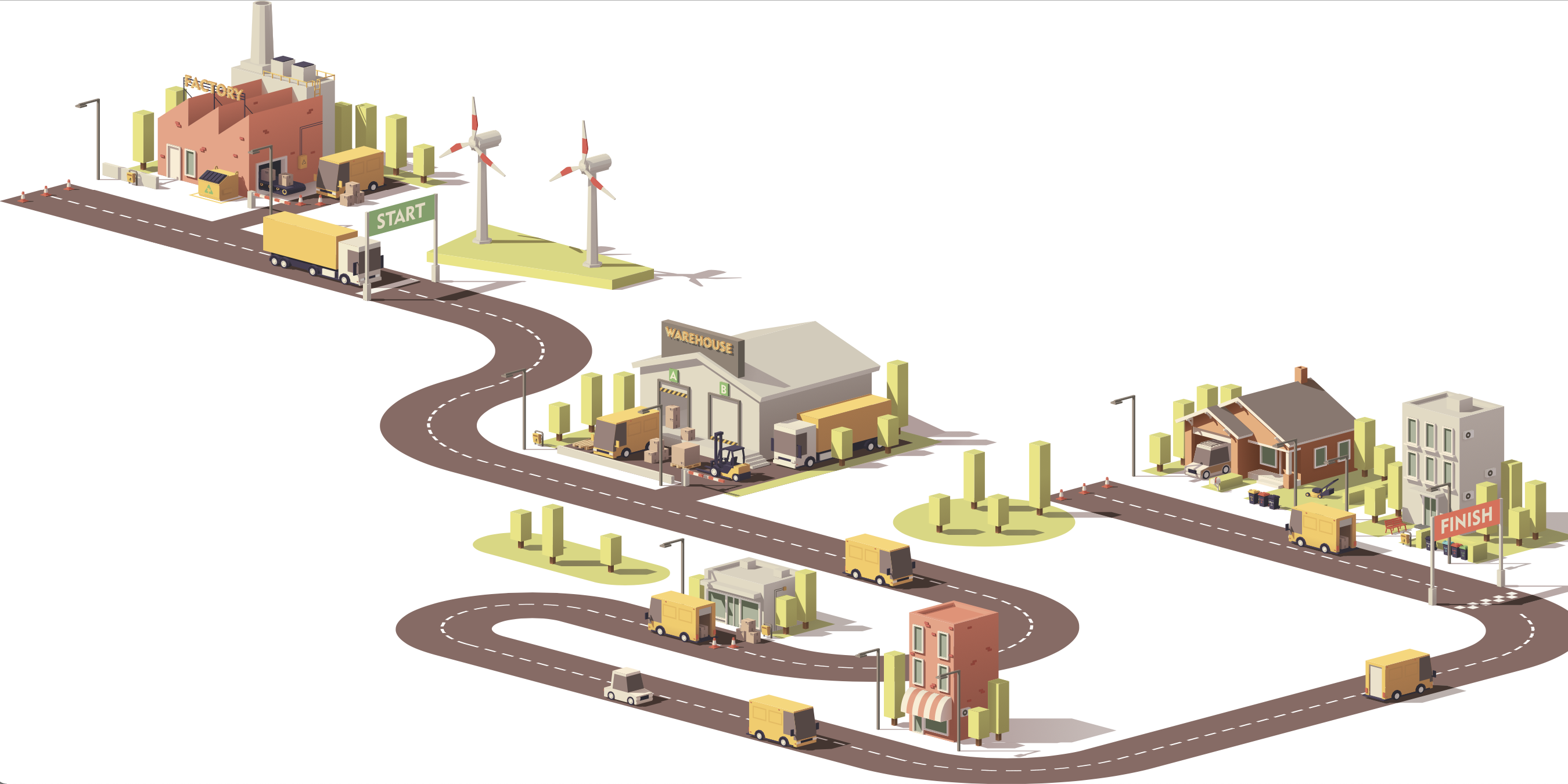
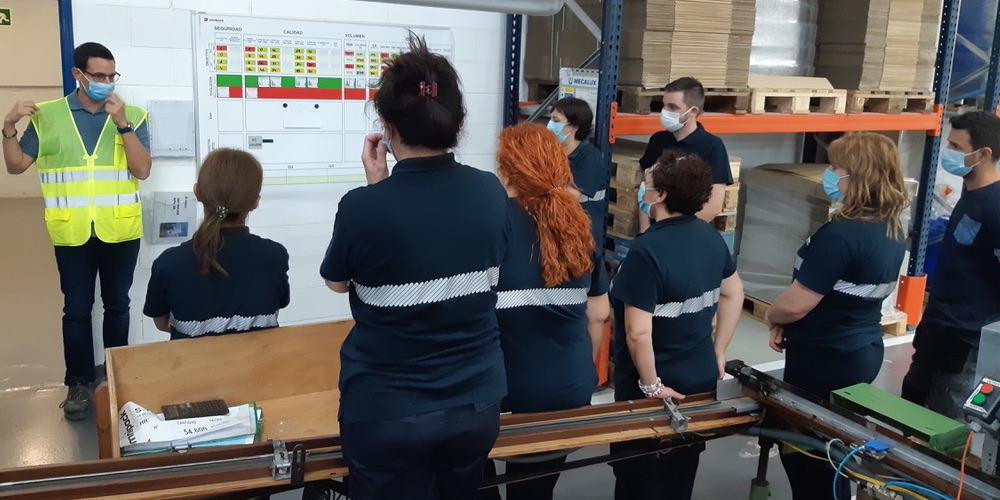
FEATURE – Improving supplier quality and reduce defects was an important part of Toyota Industries Corporation’s (TICO) Dantotsu activities since the very beginning. In this article, the author visits two parts suppliers.

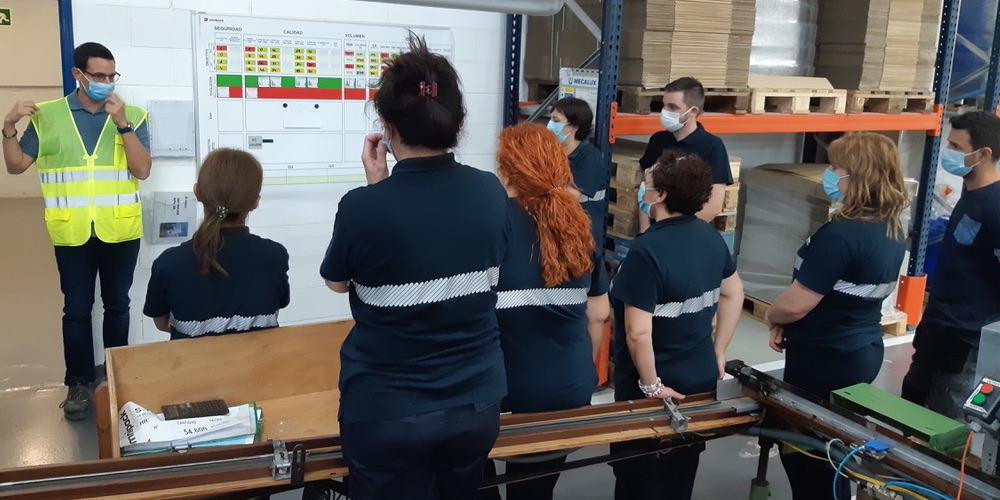
FEATURE – Reflecting on Nomura-san’s recently published book on radical quality improvement, the author encourages us to embrace the spirit of “Dantotsu” to meet the challenges we face as a society.
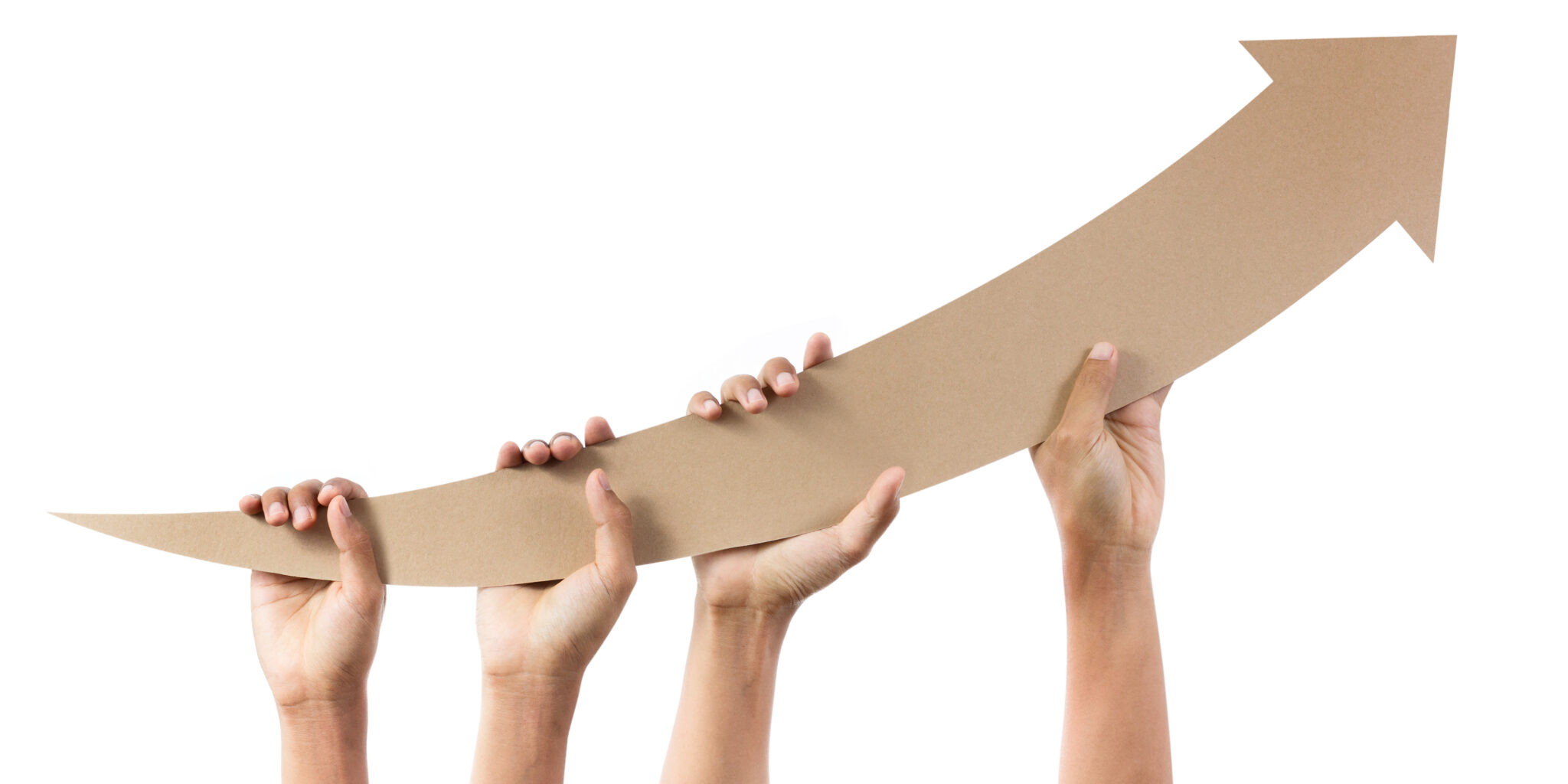
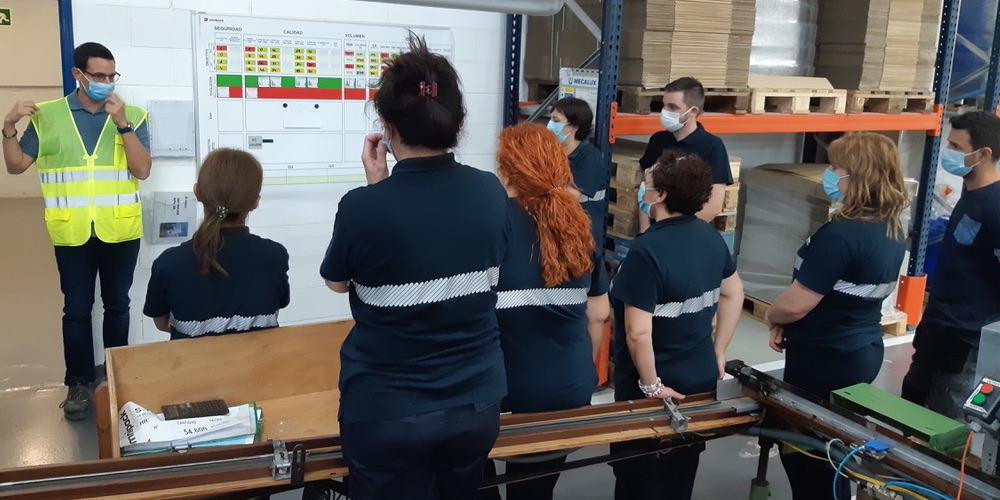
FEATURE – Today we repurpose a great article published in 2016 on Japanese industry magazine Kojo Kanri that focuses on radical quality improvement at Toyota Industries Corporation.
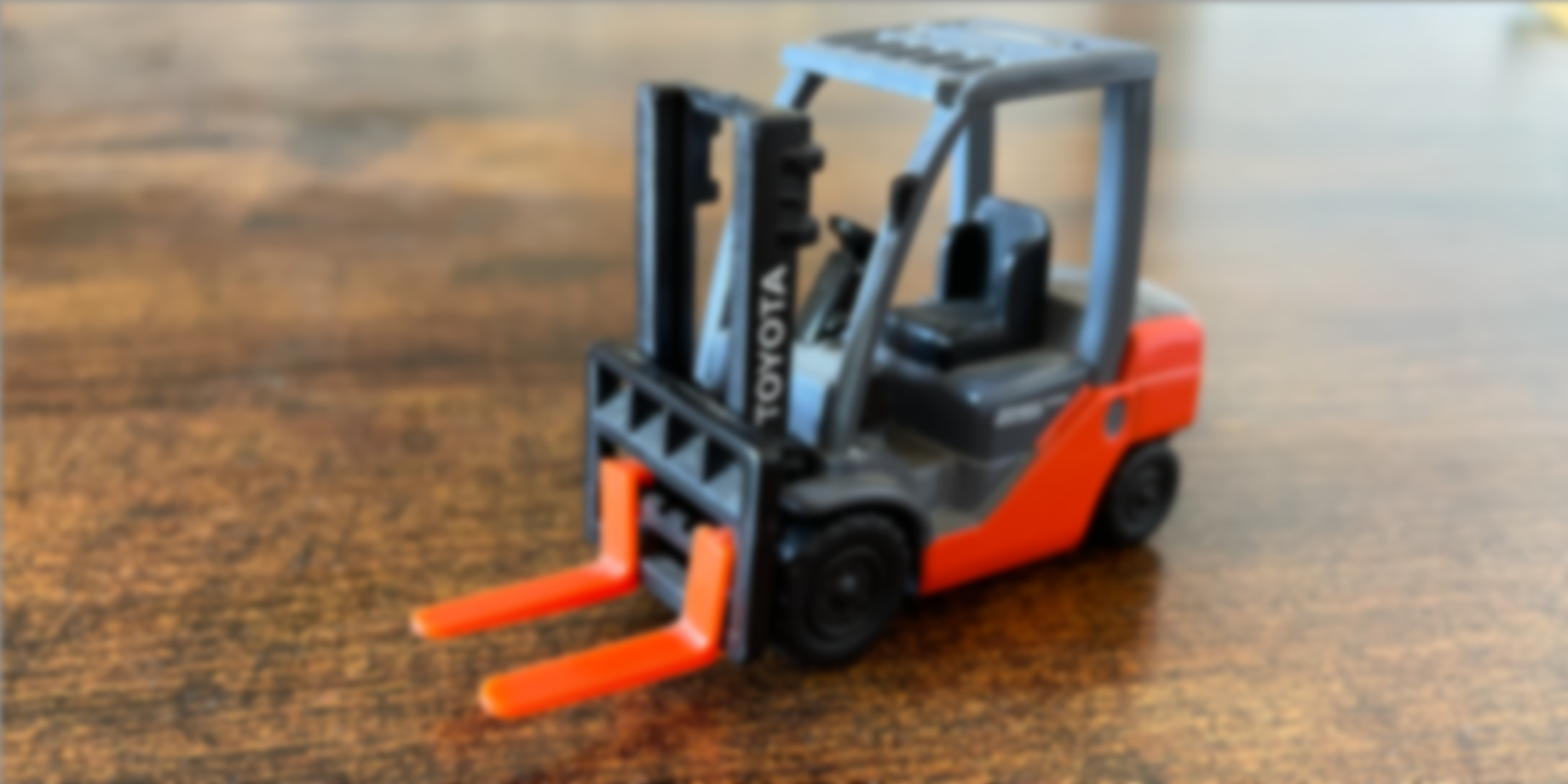
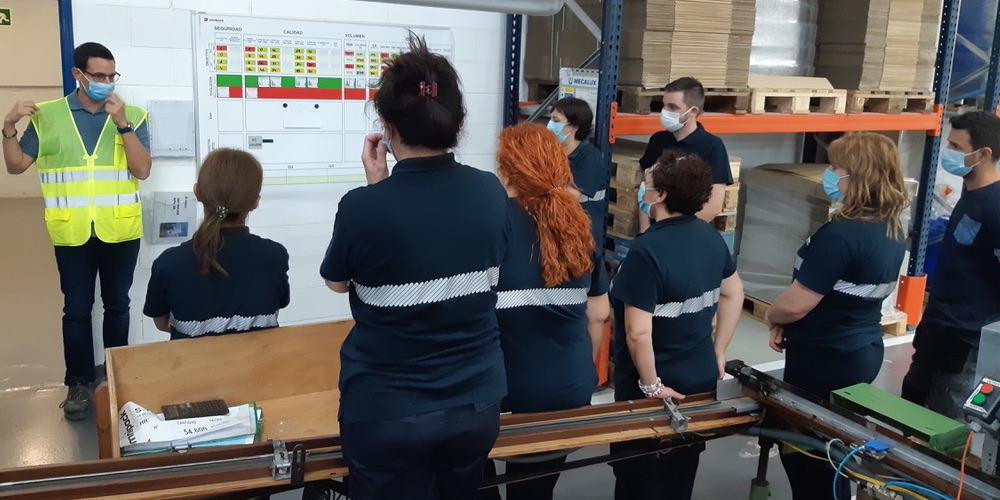
INTERVIEW – The former executive of the Toyota Material Handling plant in Italy reflects on how Sadao Nomura’s “Dantotsu” method helped them to drastically improve quality.
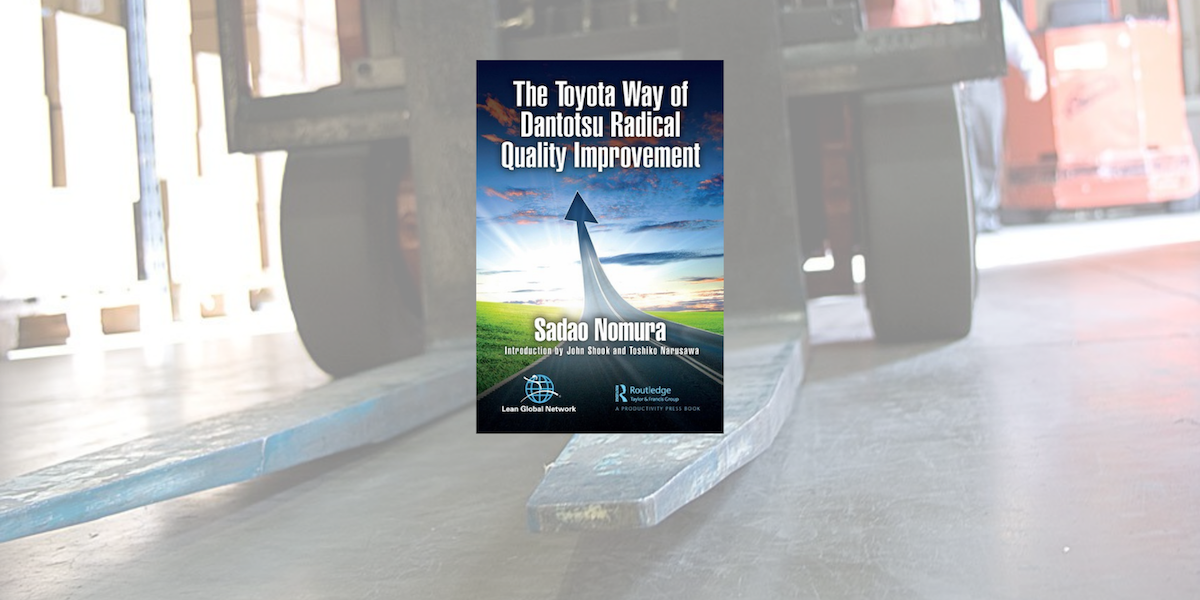
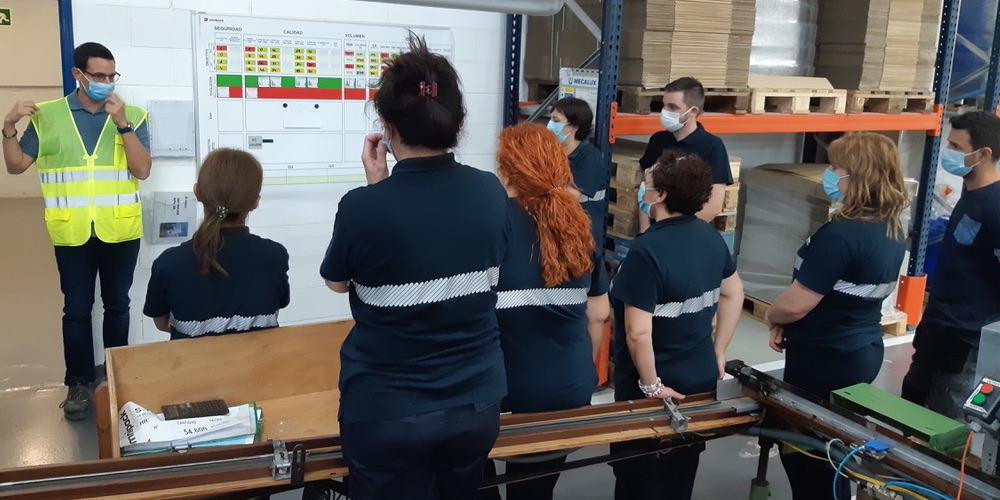
FEATURE – The authors discuss radical quality improvement at Toyota and introduce a new book by Sadao Nomura that the Lean Global Network has just co-published.
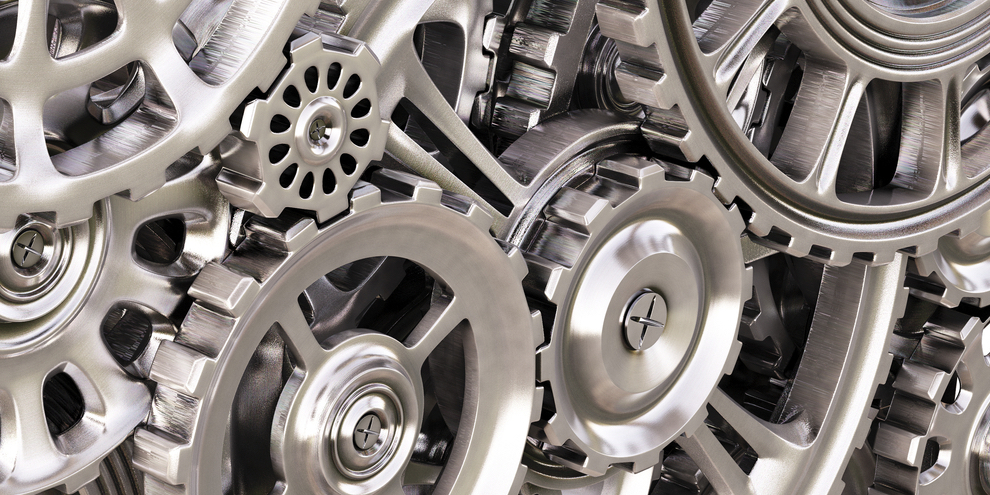
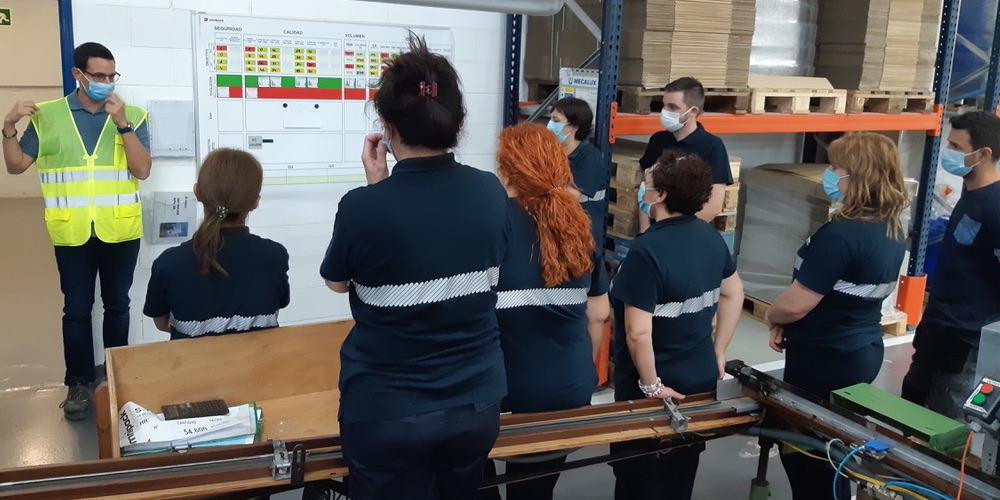
FEATURE – Kanban is the best-known method to establish pull production, but it is not the only one. Here’s a few other ways you can create a pull system.
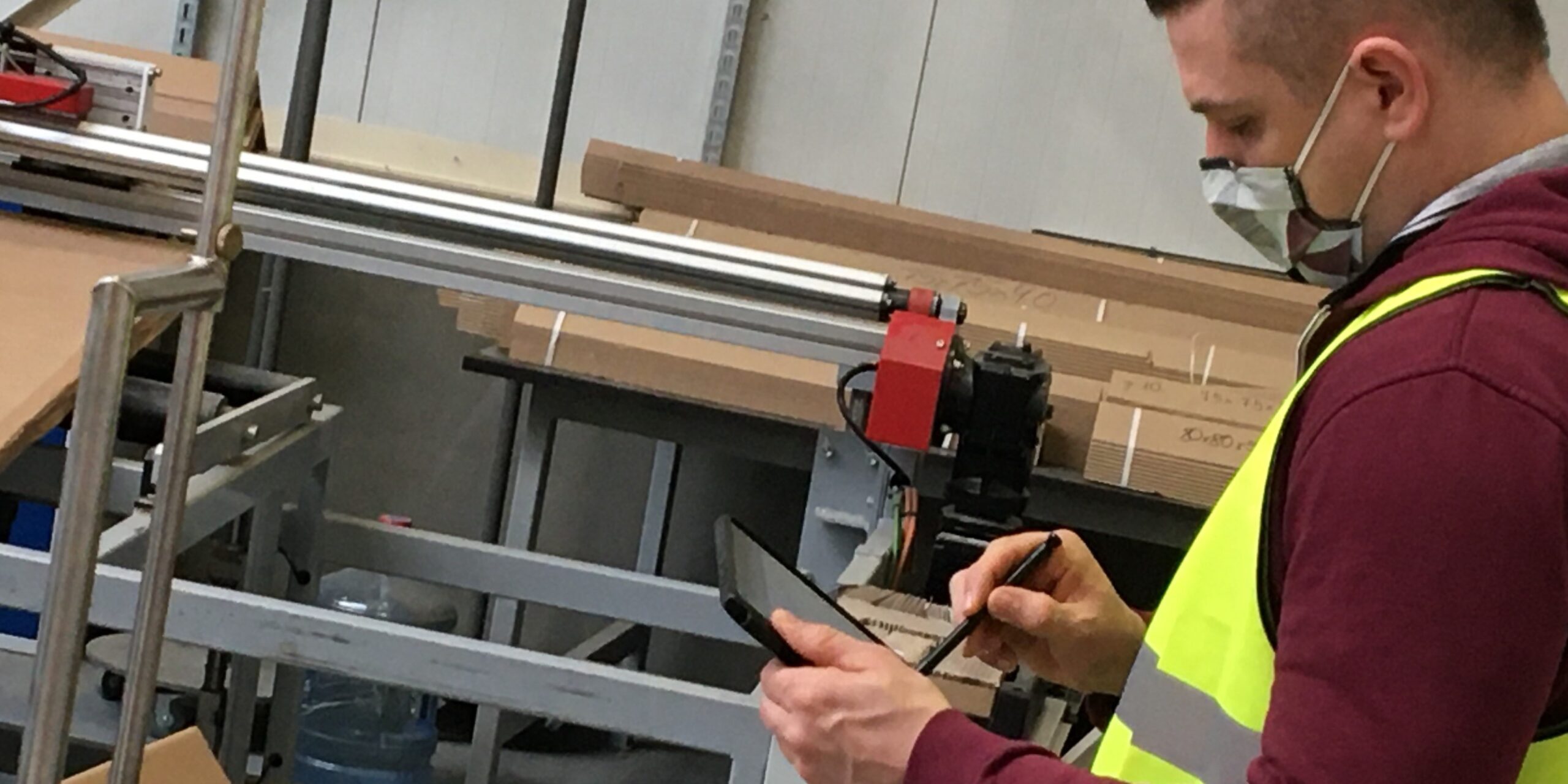
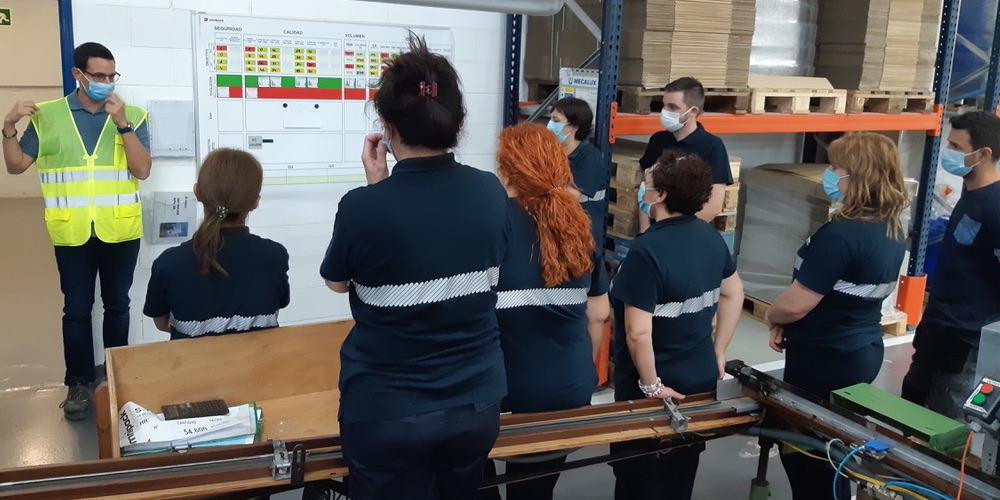
FEATURE – During a recent Jishuken workshop, Poland-based Schumacher Packaging experimented with a newly-developed App to quickly create standardized work instructions at the gemba.
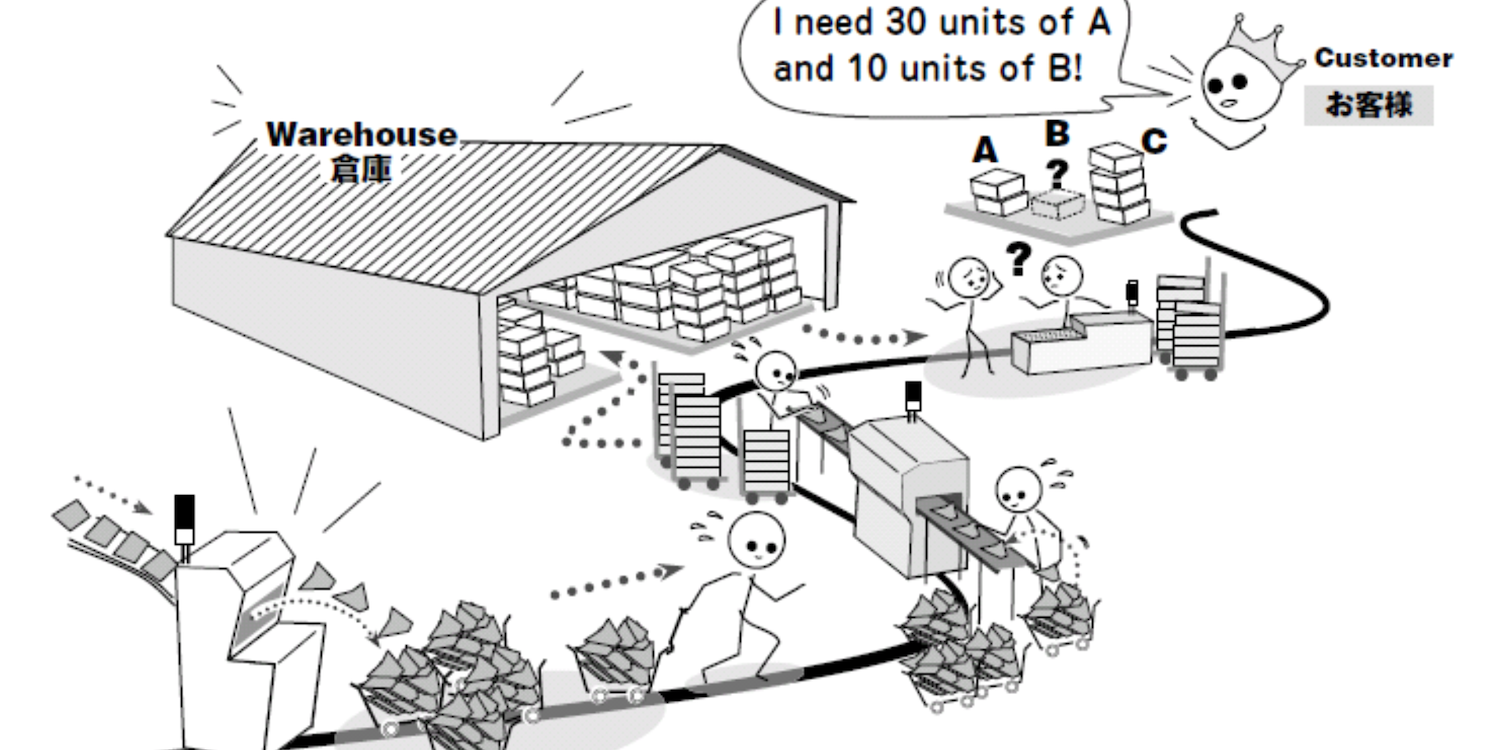
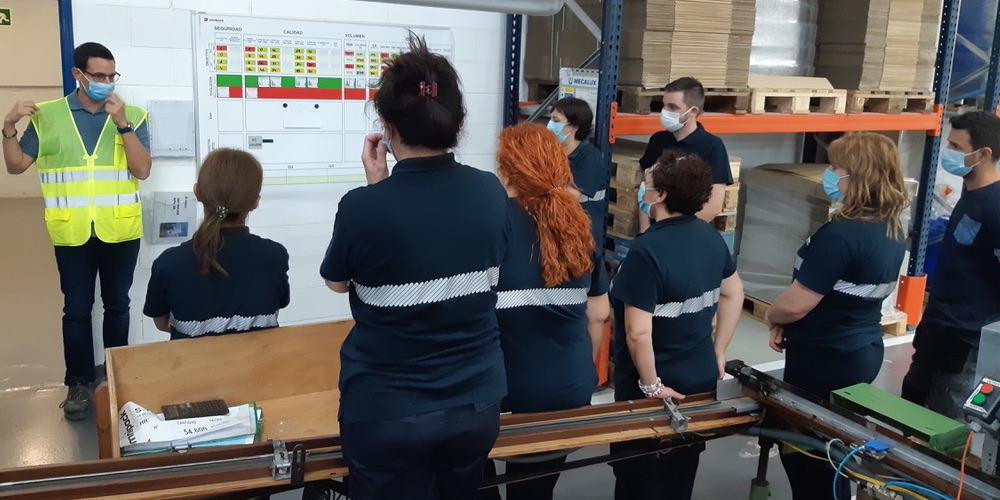
FEATURE – The release of Christoph Roser’s new book All About Pull inspires John Shook to discuss the origins and true meaning of “pull” and why it is incorrect to blame JIT for the shortcomings of global supply chains.
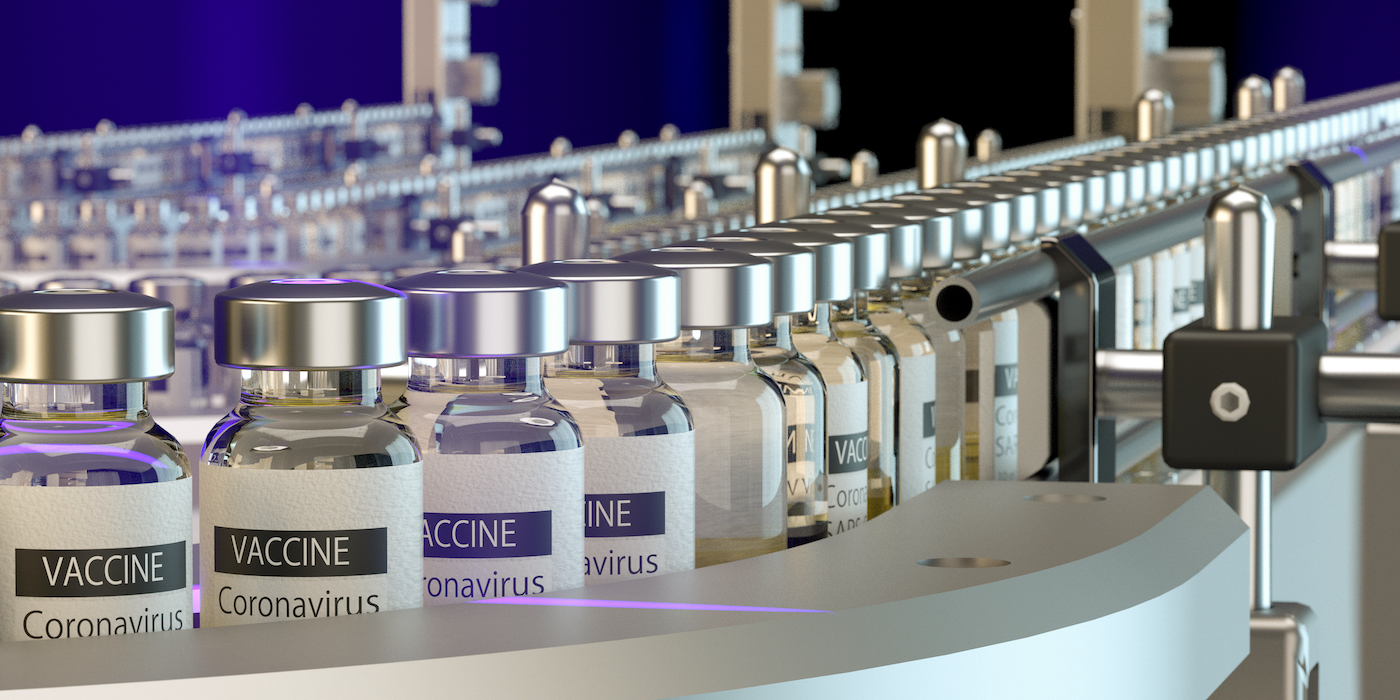
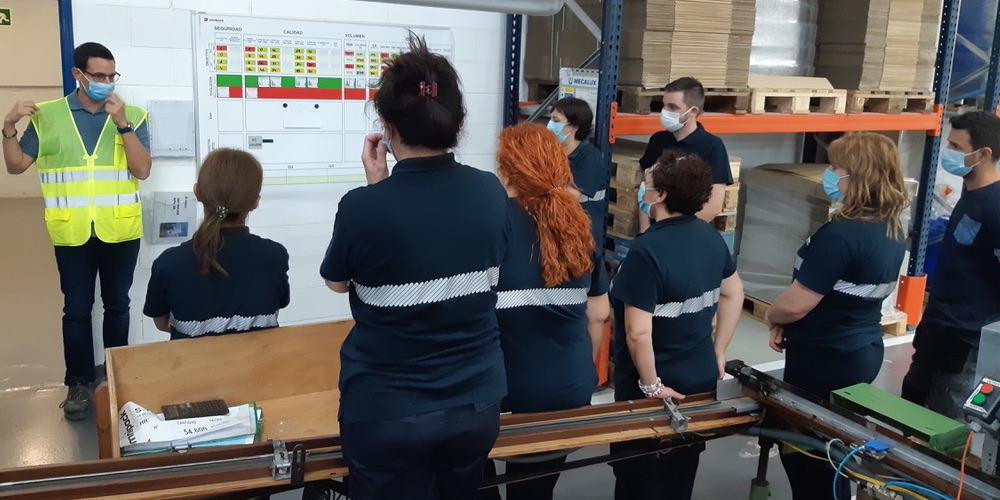
FEATURE – What does it take to meet the historic challenge of rapidly increasing the annual global vaccine capacity from 5 billion to 19 billion doses? And how could Lean Thinking help?
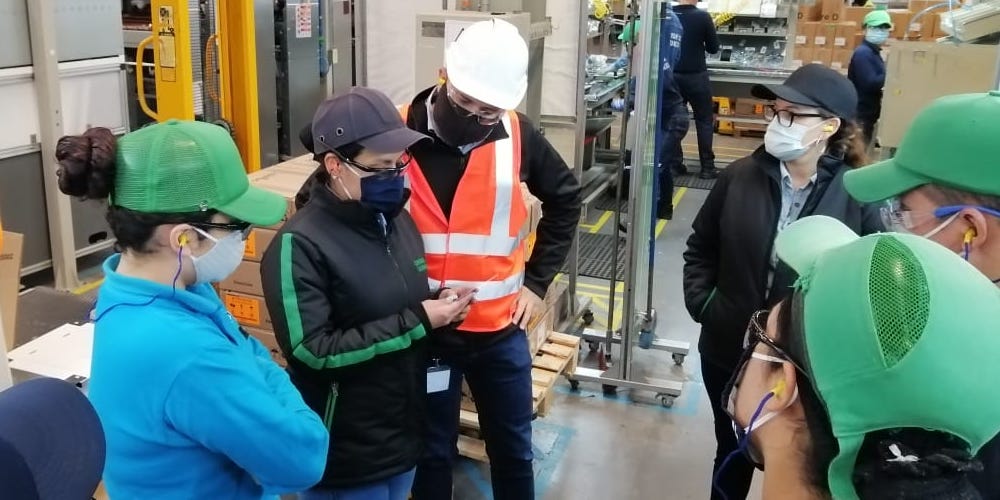
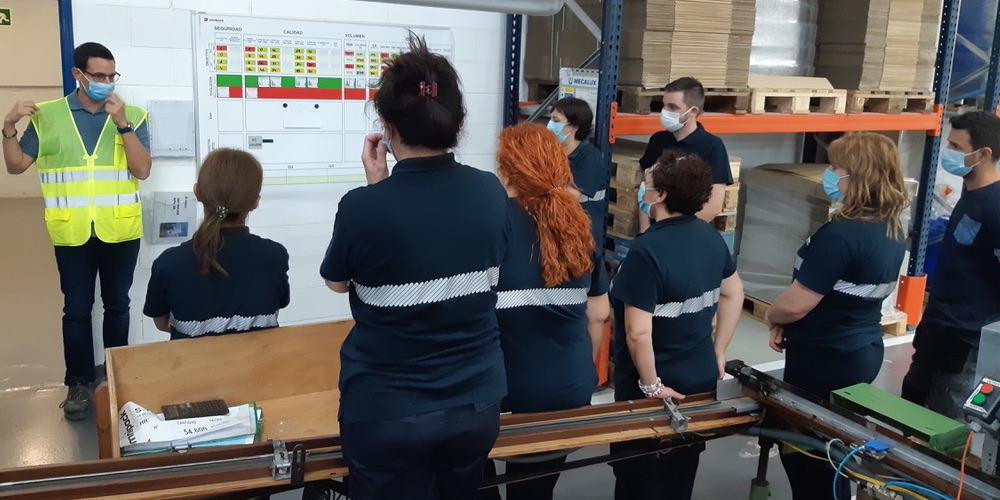
FEATURE – How do kamishibai boards work and what sort of benefits can they bring to a lean transformation? The author discusses what he saw on a recent gemba walk.
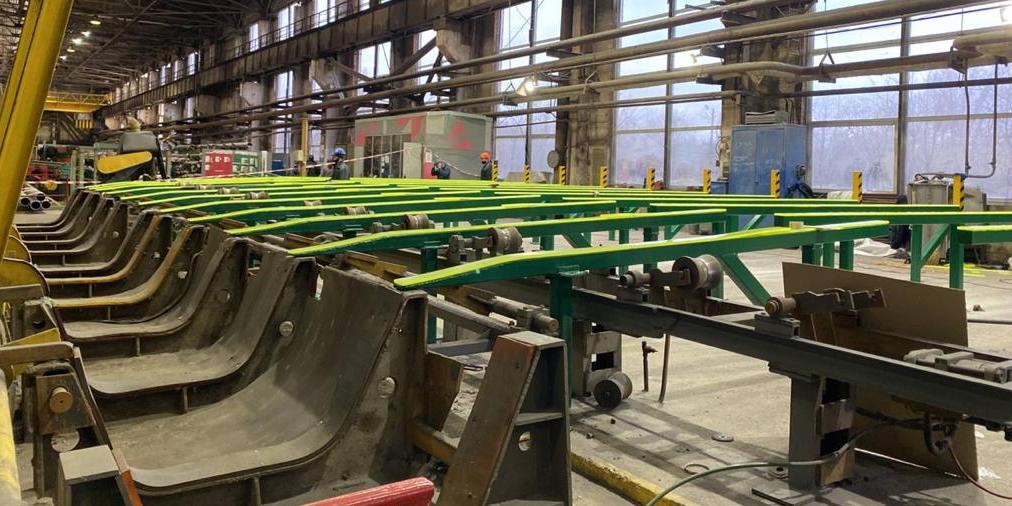
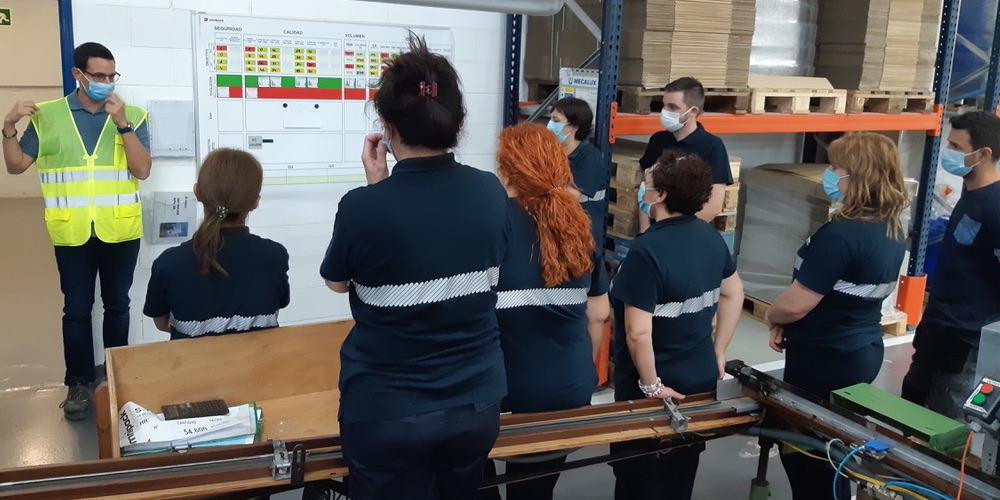
FEATURE – With the help of Lean Thinking, this Ukrainian producer of stainless steel pipes is retaining its competitive position against larger players in the market.
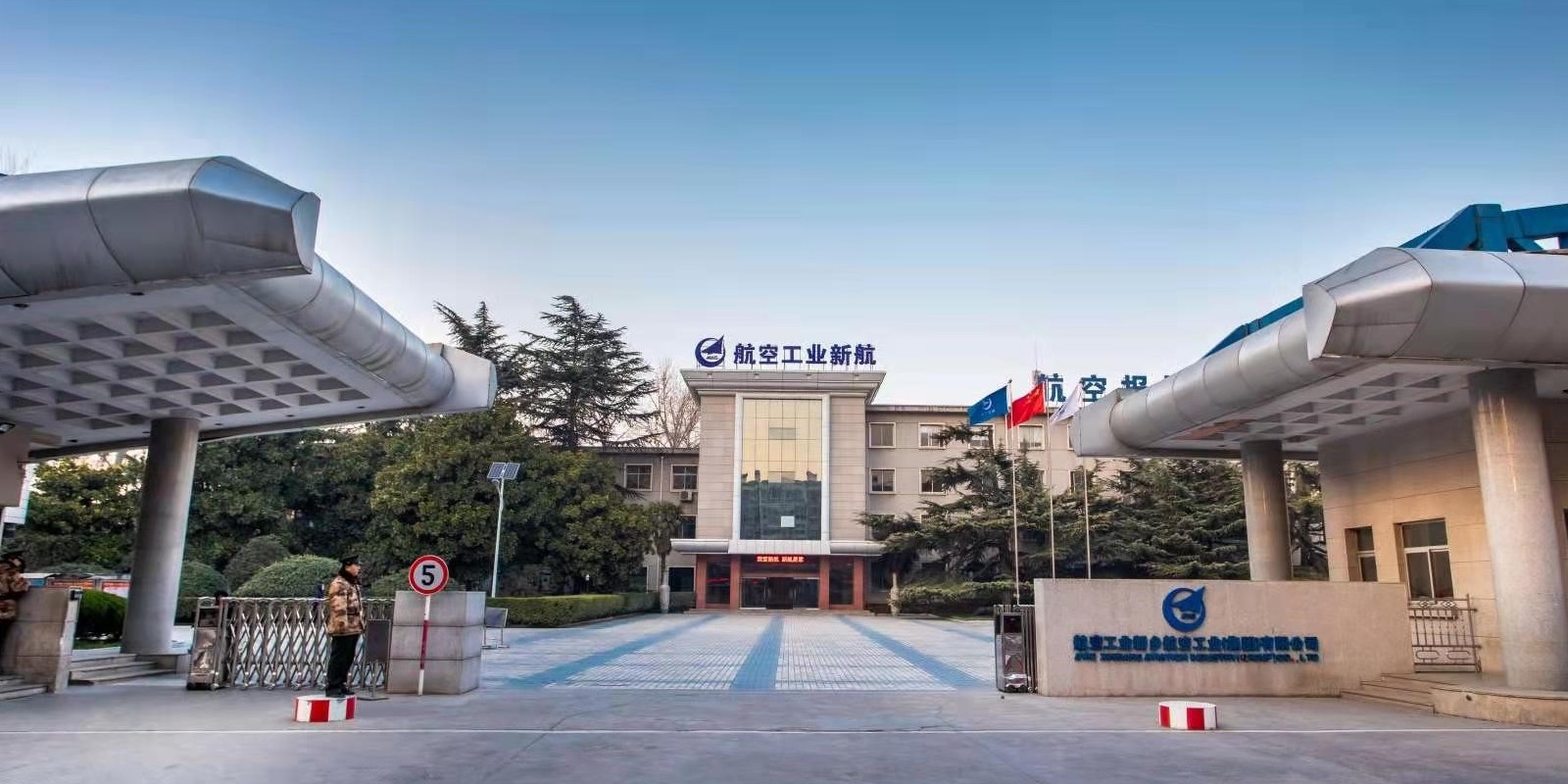
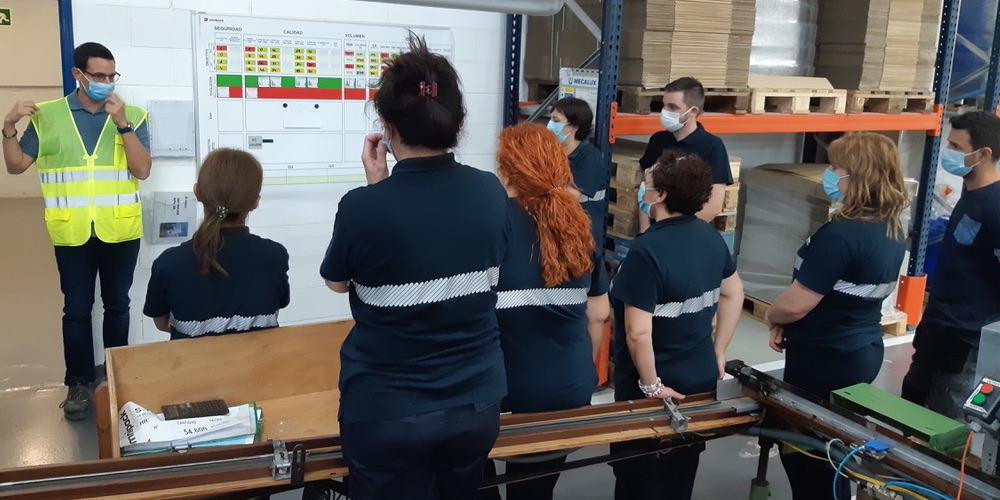
FEATURE – The approach described here, first adopted by this Chinese company, directly connects the daily work in manufacturing with an organization’s financial results.
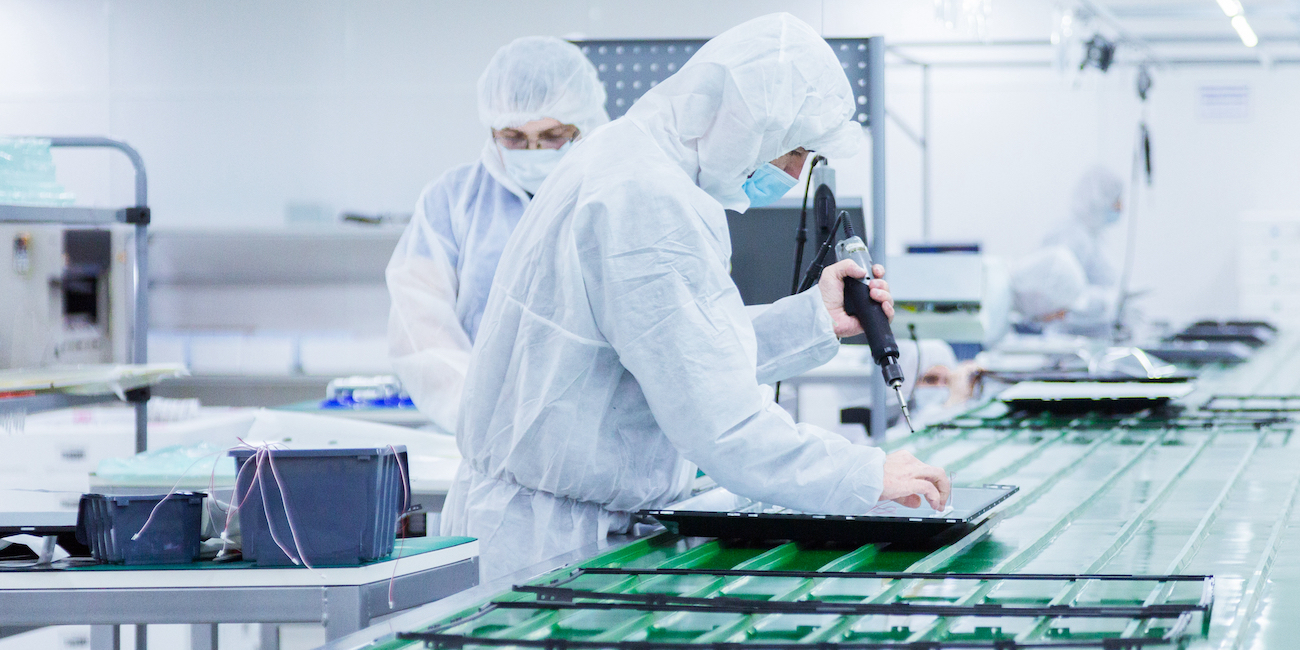
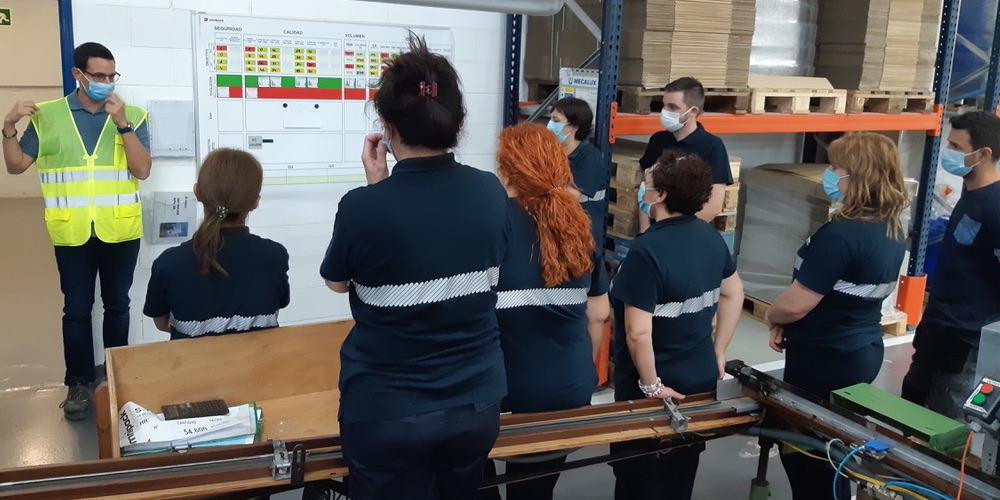
FEATURE – Aligning supply flows with demand is crucial to success, but it can be complicated. Lean Thinking can help us identify the strategy and sequence of activities that we need to make it a reality.
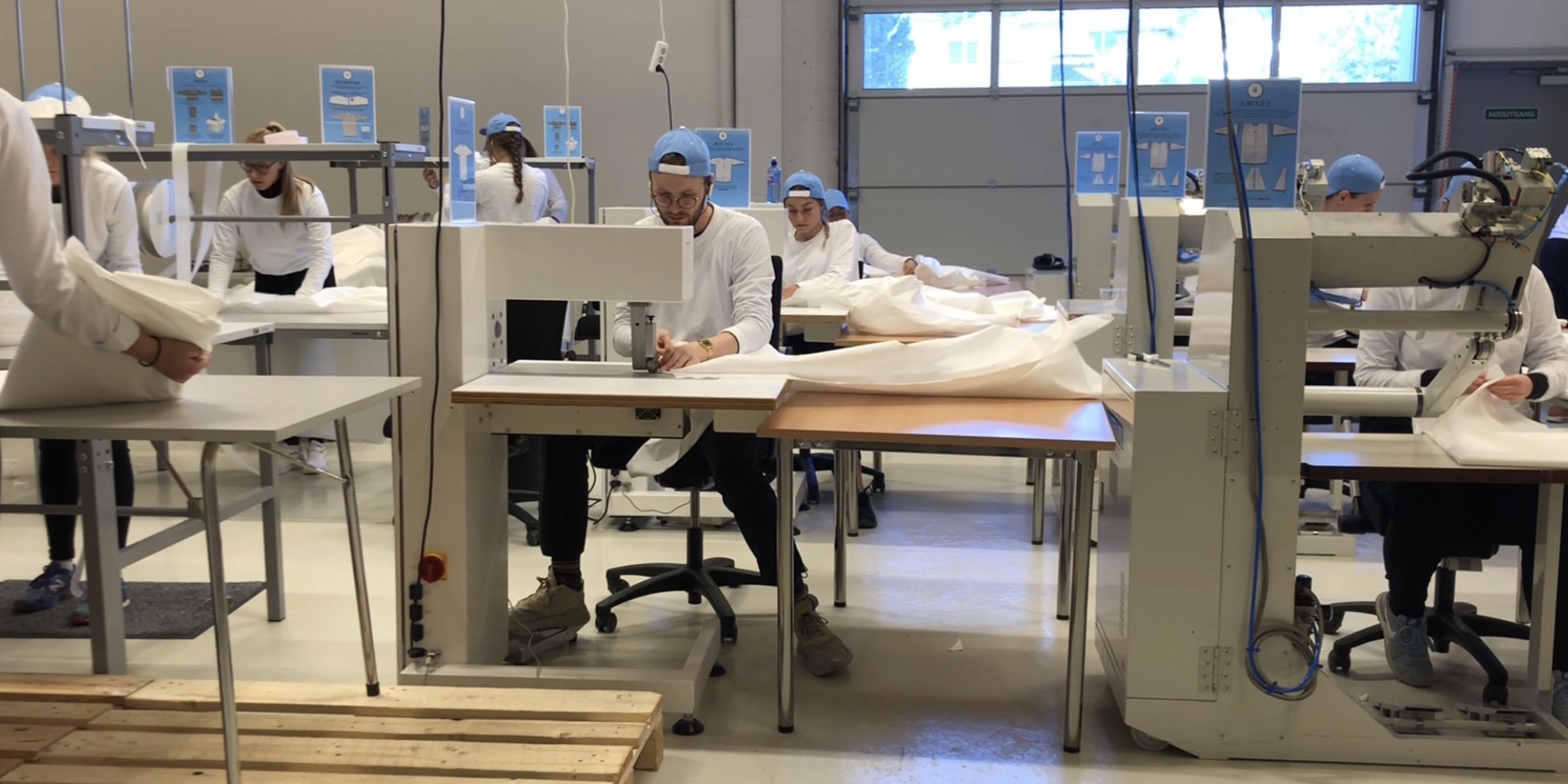
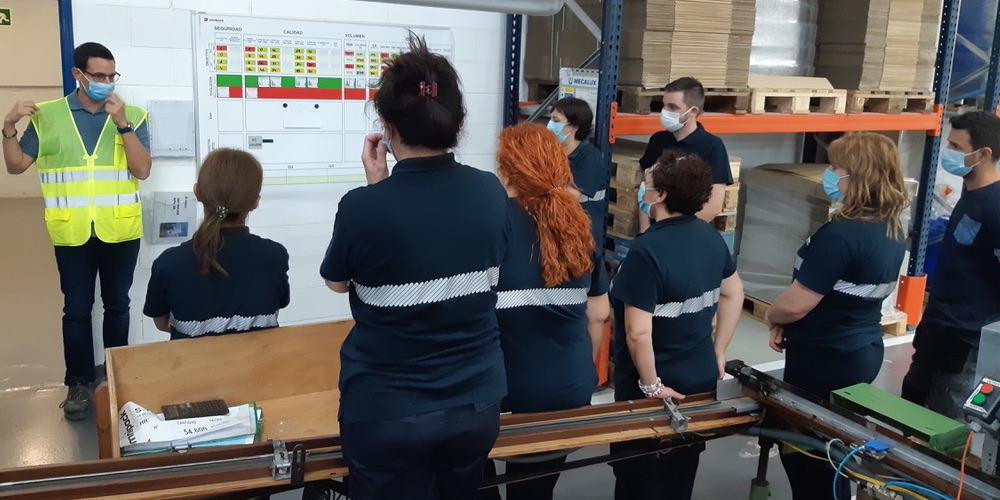

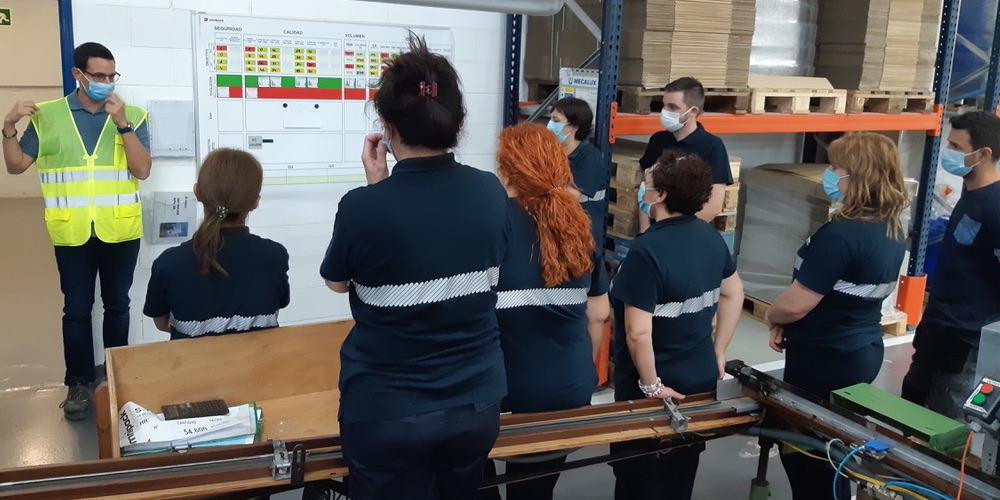
FEATURE – Sometimes you just need to get creative: as part of its flexible manufacturing model, Esquel introduced a new role on its shop floor – the “mangineer”.
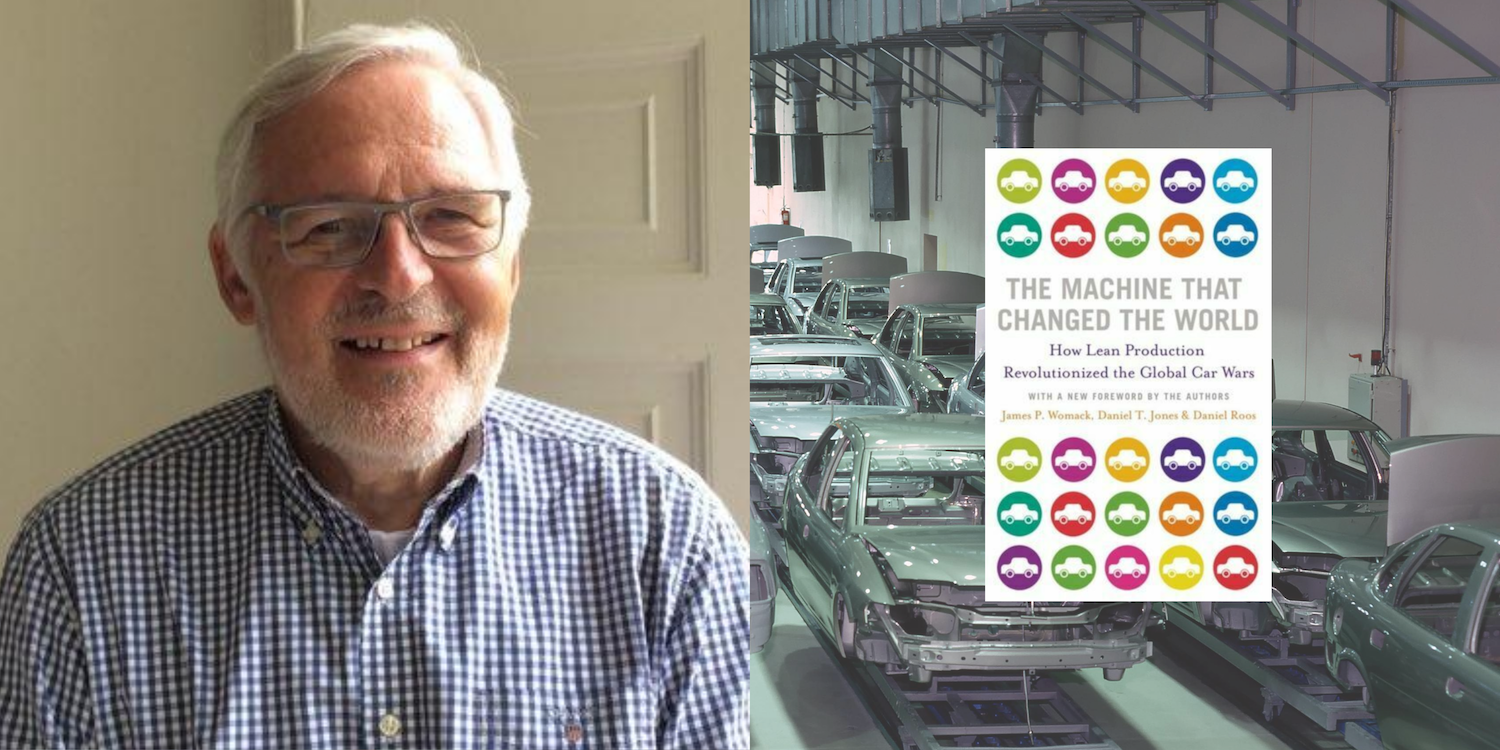
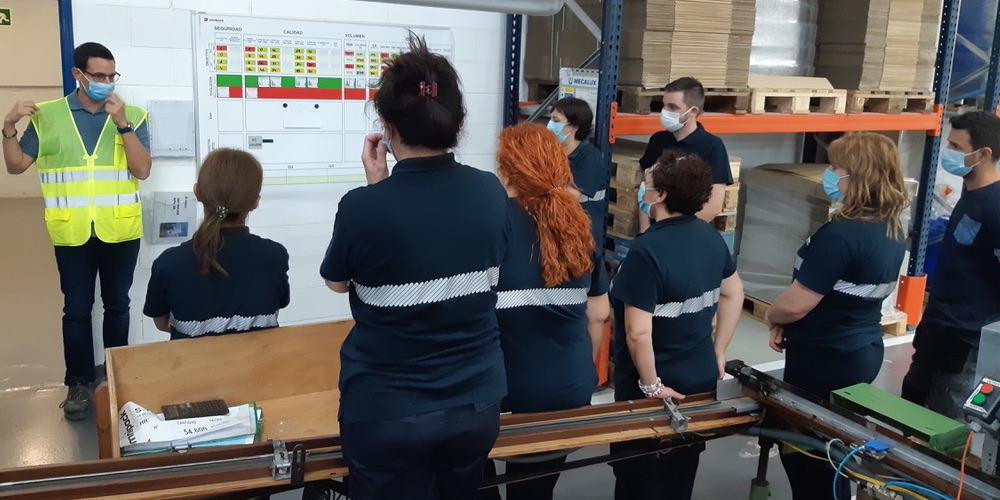
INTERVIEW – In the fall of 1990, a book was published that would kickstart a revolution in business. This week we are catching up with the authors to understand where we are and where we are headed. First up, Daniel Jones.
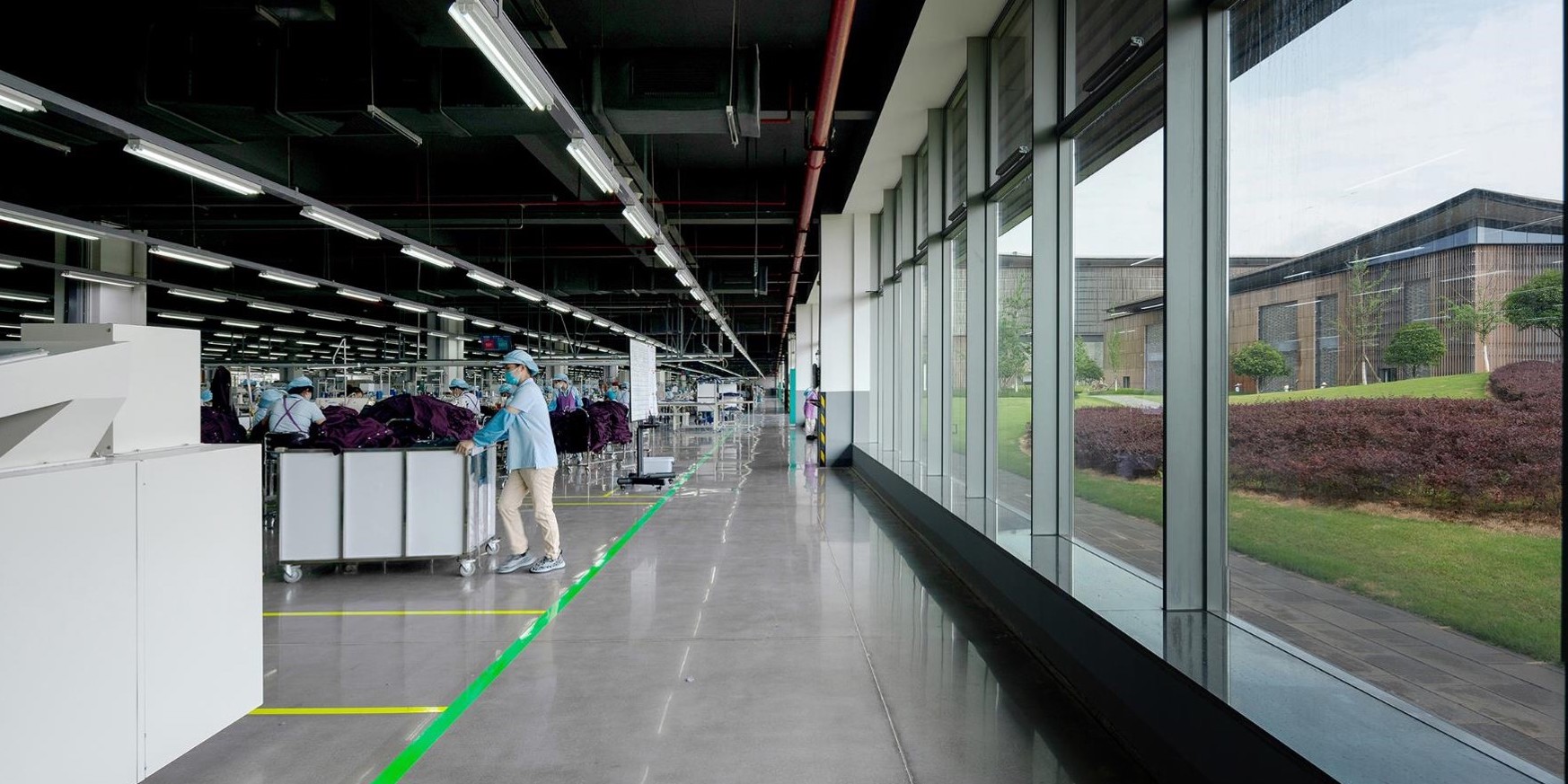
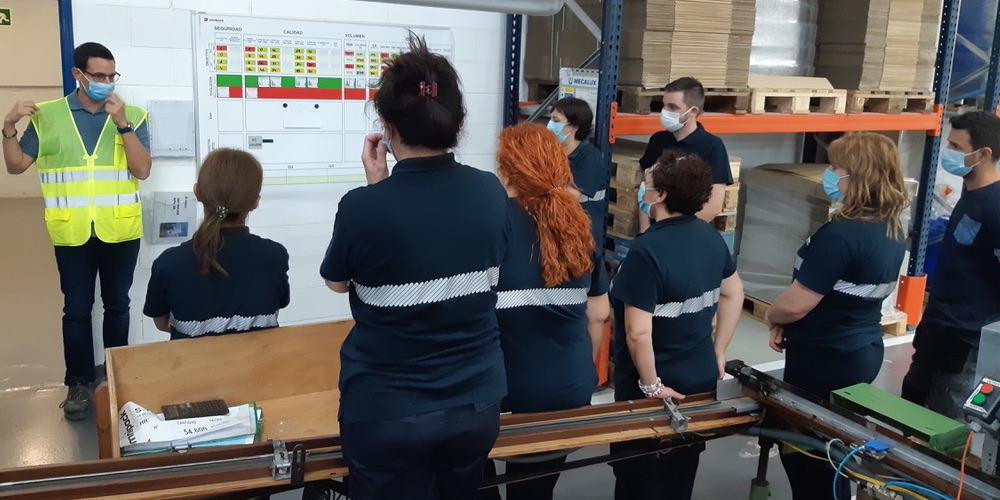
CASE STUDY – An Esquel factory in GuiLin, China injected lean principles and practices into its processes to become more efficient and environmentally-friendly.
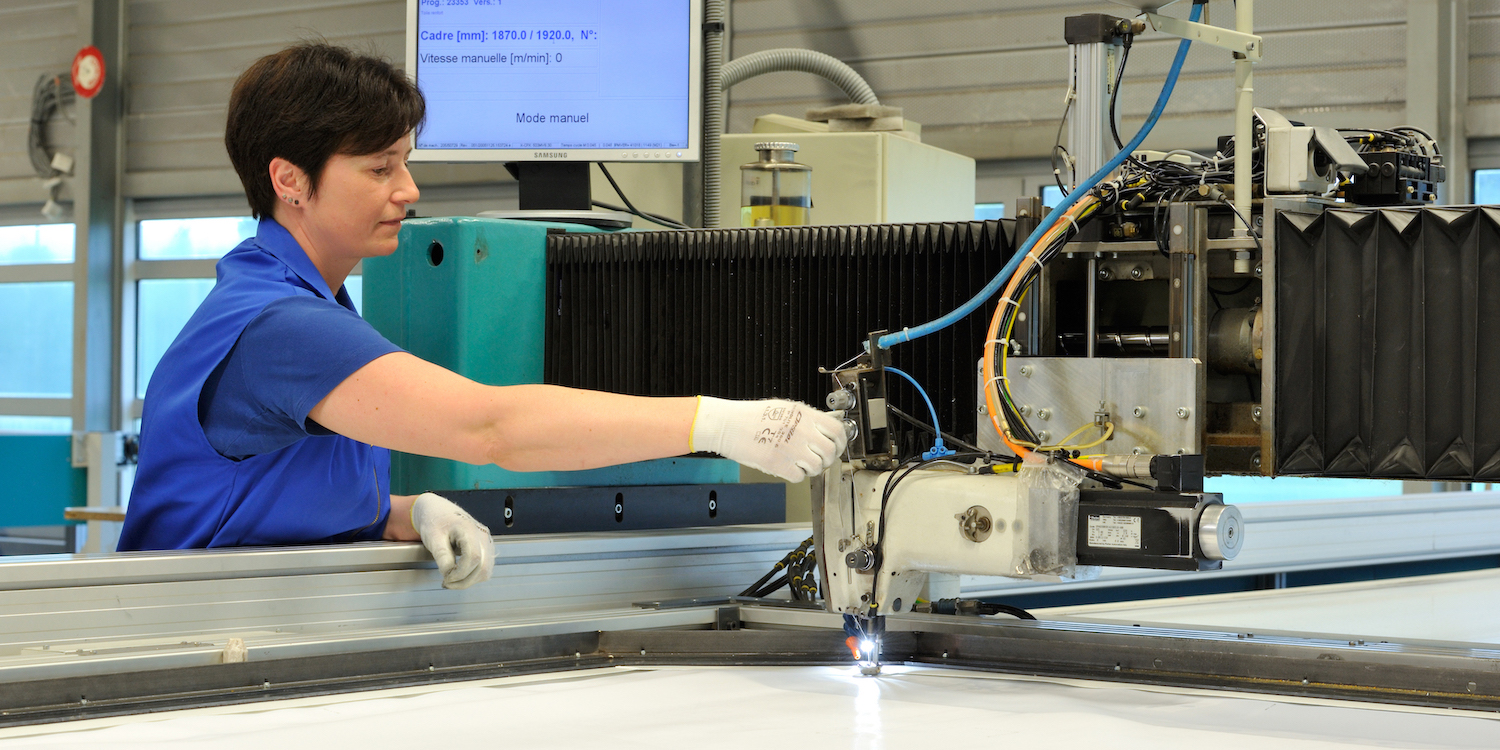
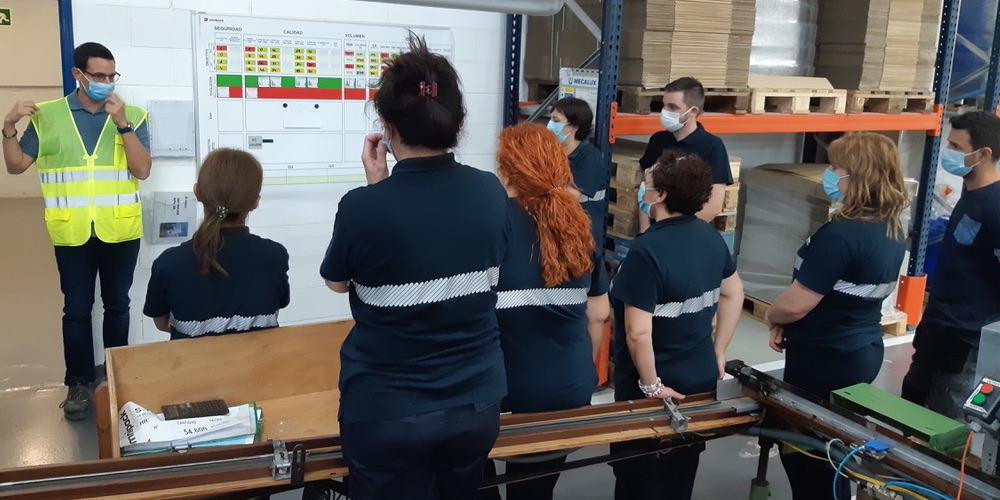
NOTES FROM THE GEMBA – It can take time to challenge our misconceptions and set off on a lean journey. Once we get it, however, it’s hard to stop the improvements, as this French company found out.
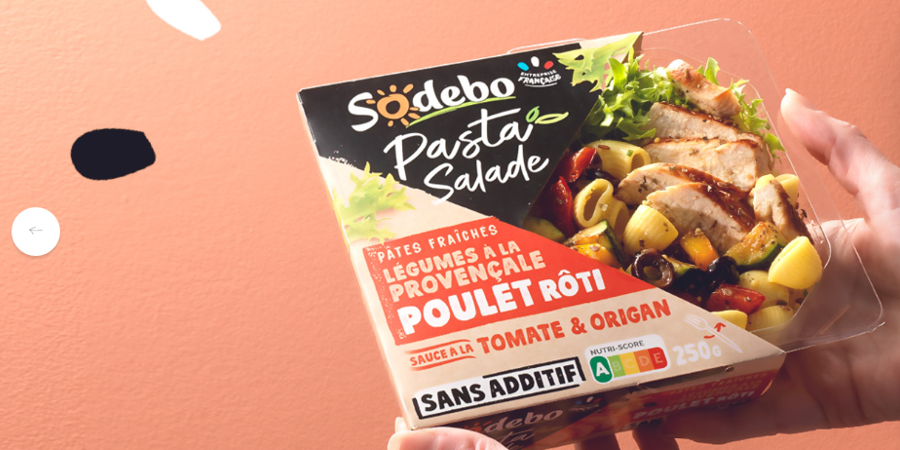
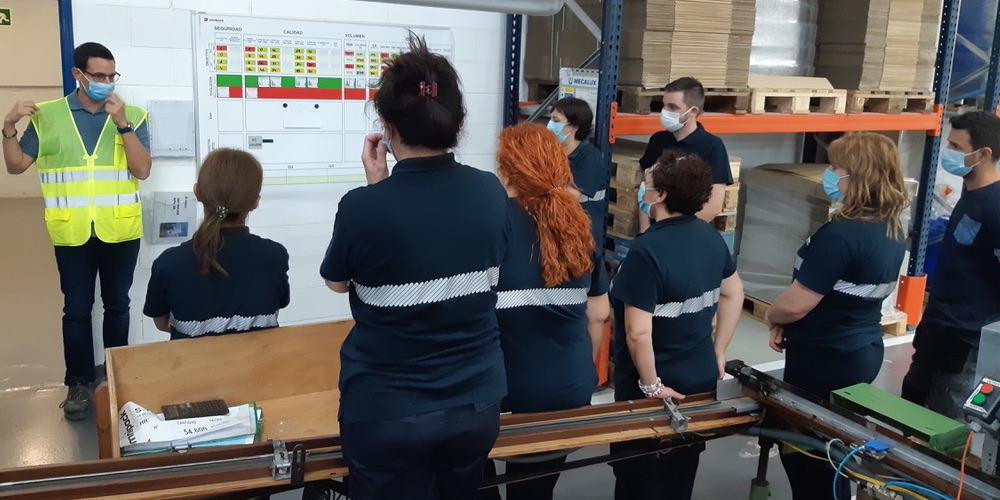
NOTES FROM THE VIRTUAL GEMBA – Despite a 40% drop in sales and the looming prospect of having to furlough part of its staff, this French company is finding in lean manufacturing an ally to fight the current crisis.
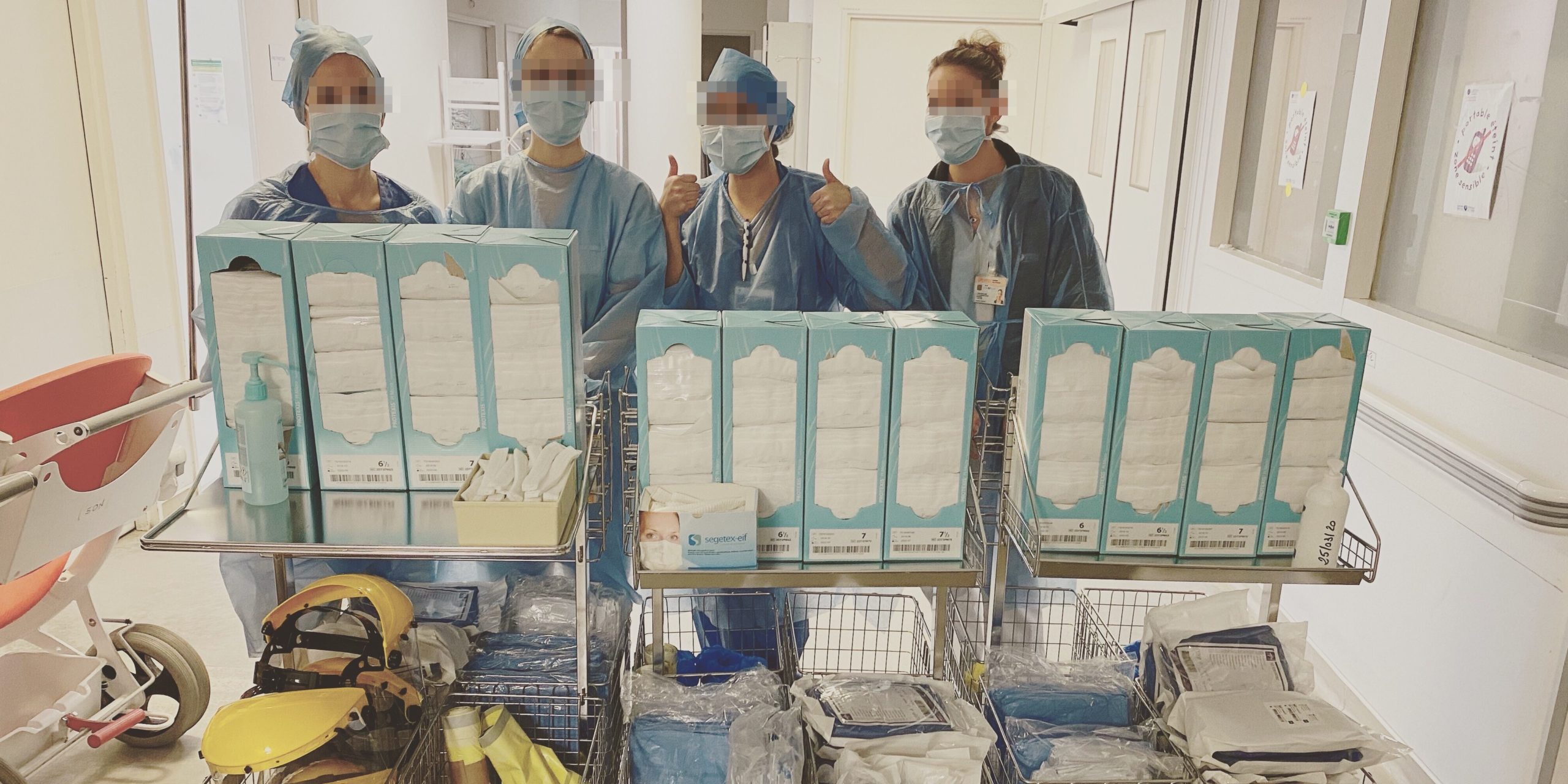
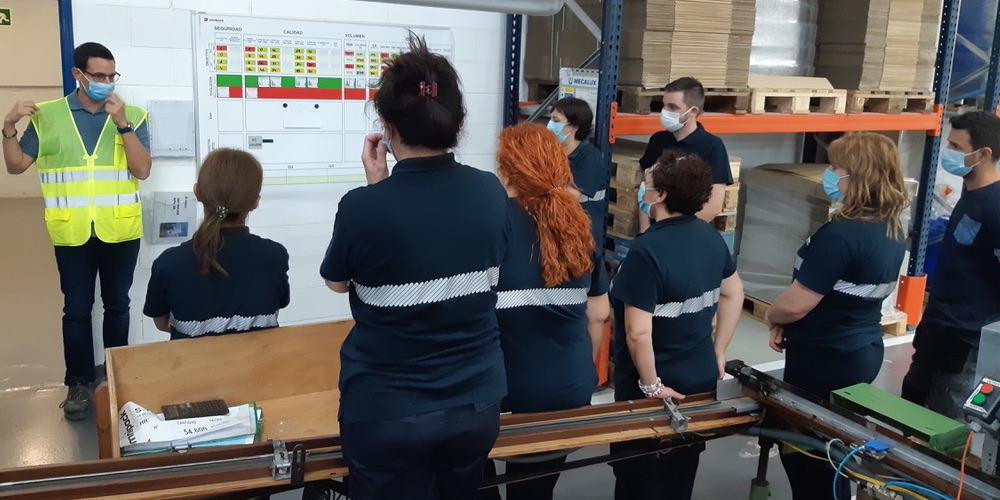
NOTES FROM THE (VIRTUAL) GEMBA – This small manufacturer is relying on Lean Thinking to keep the business running during the Covid-19 crisis, overcome the disruption in its supply chain, and even innovate.
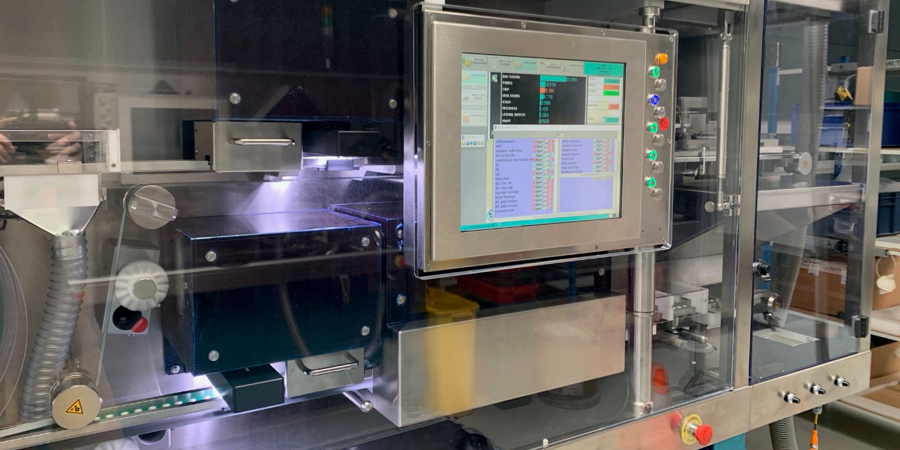
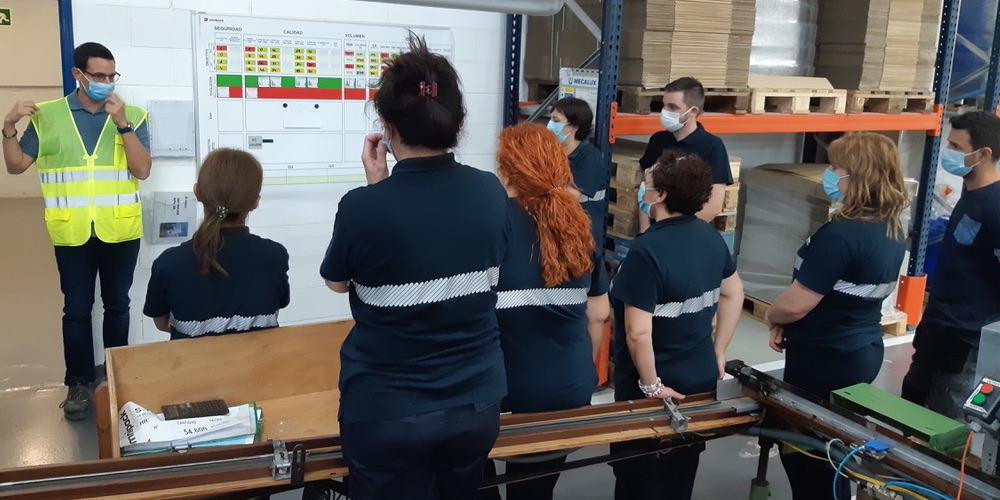
NOTES FROM THE (VIRTUAL) GEMBA – In this new series - one new article every week during the Covid-19 crisis) - the author asks companies how they are reacting to this health emergency. First up, Proditec.
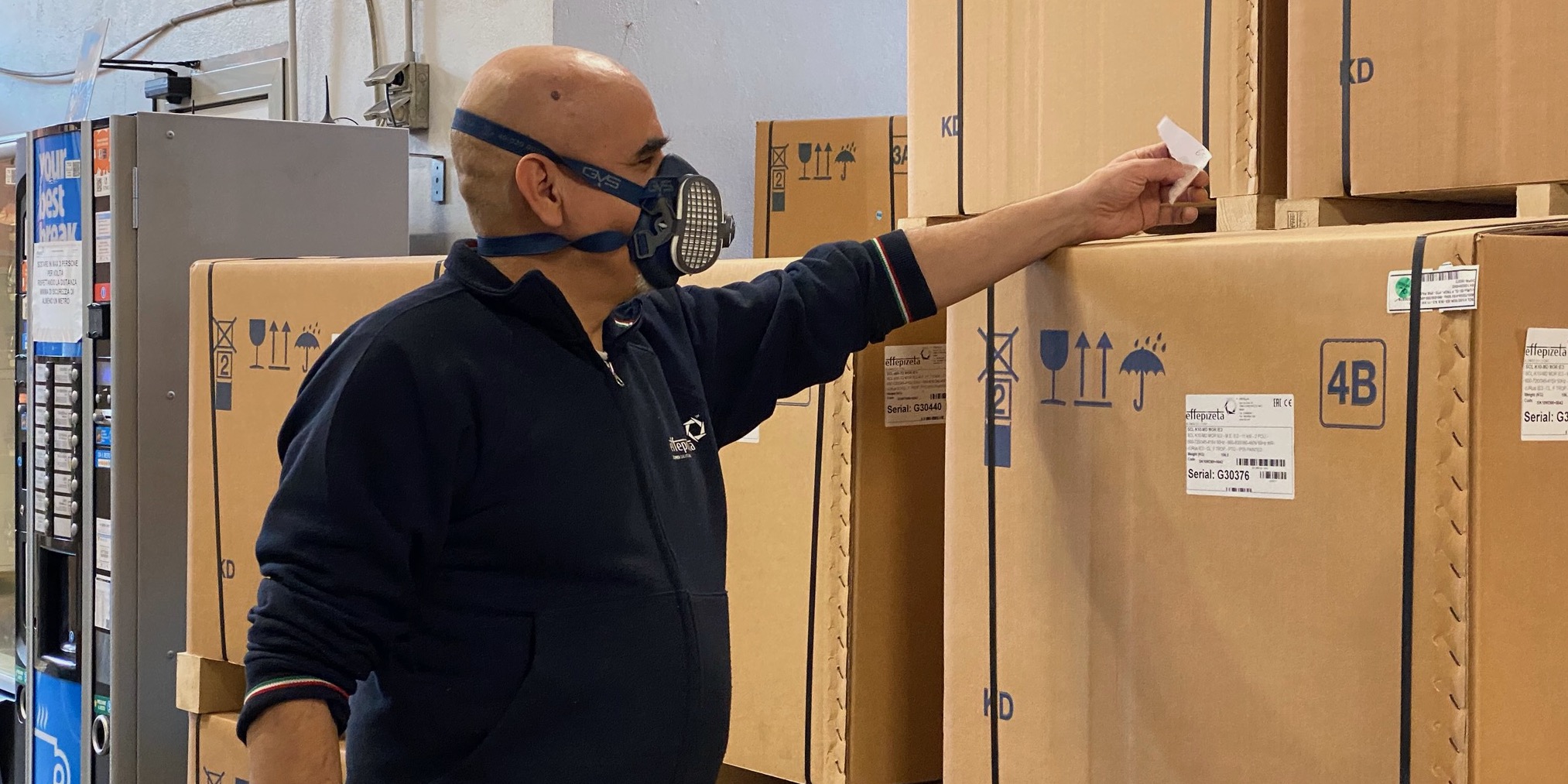
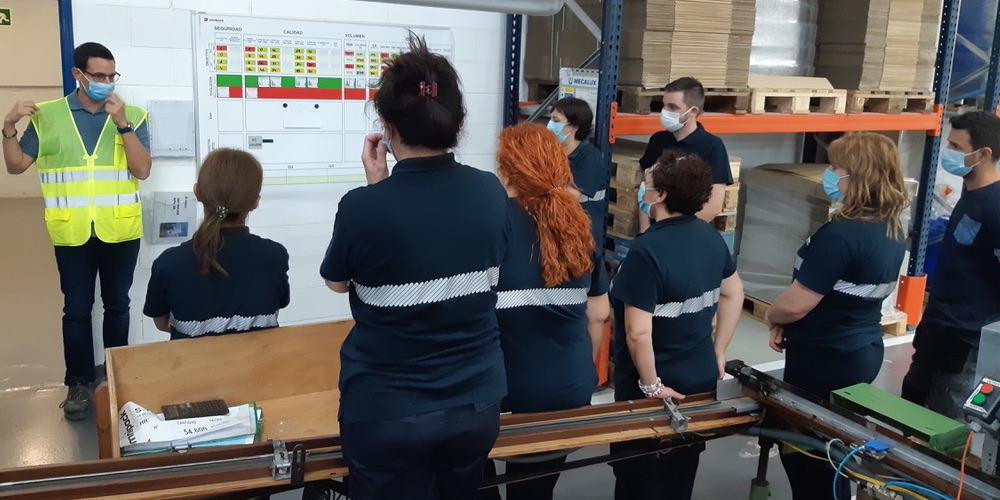
CASE STUDY – This Italian manufacturer has found in lean a way to ensure business continuity and provide support to a distraught workforce in the midst of the coronavirus outbreak.
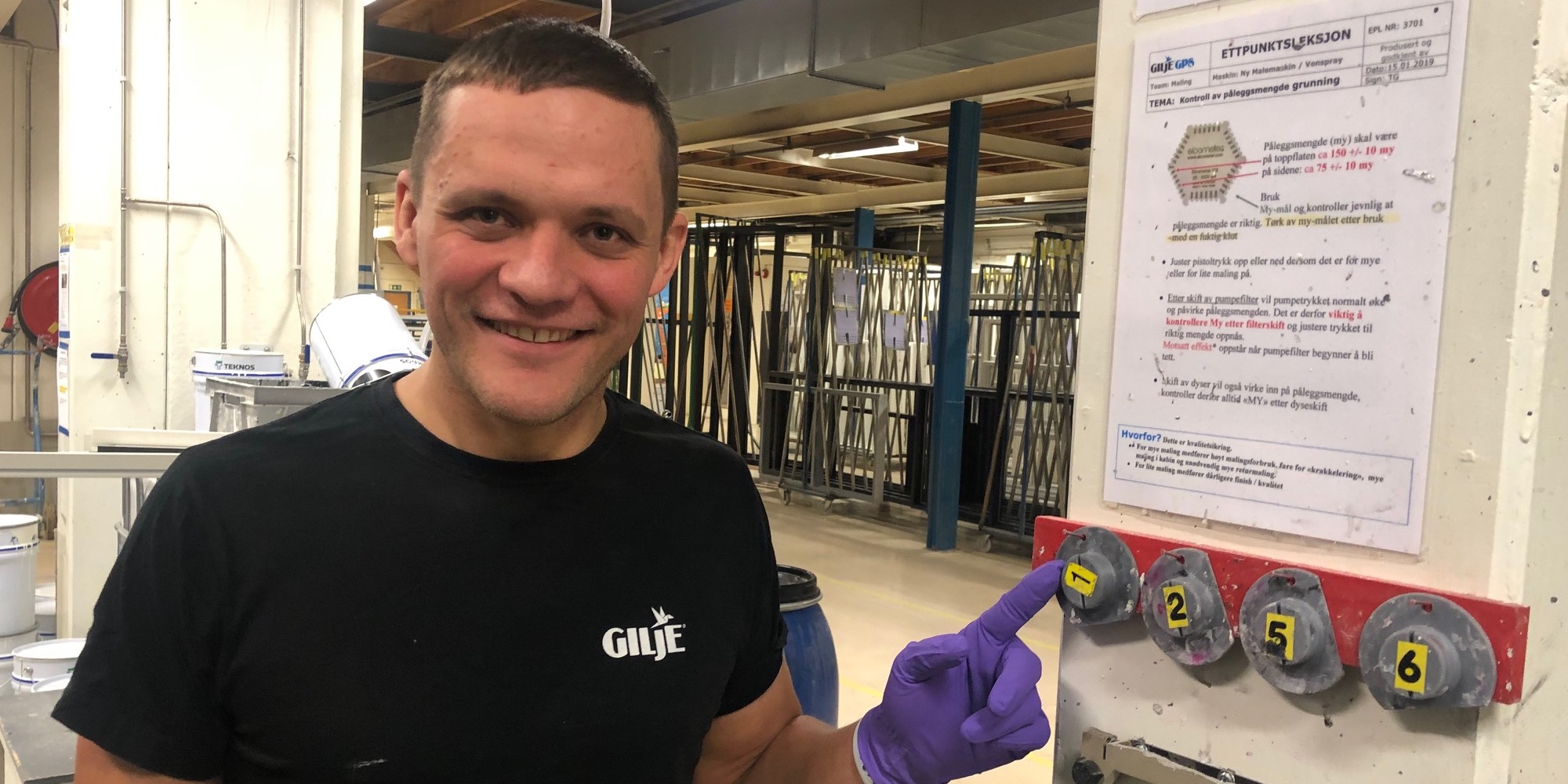
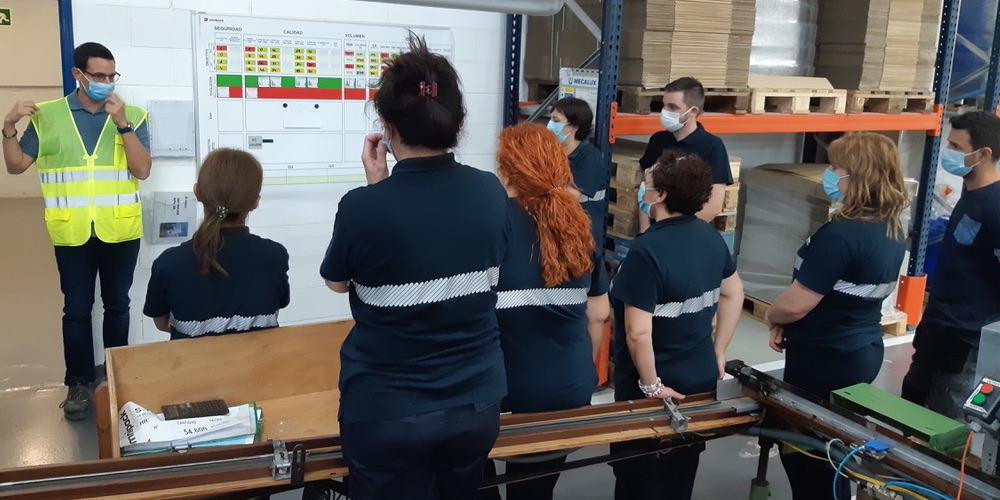
CASE STUDY – The story of this Norwegian window and door manufacturer shows how a deep and ongoing commitment to a lean transformation can help a company thrive against all odds.
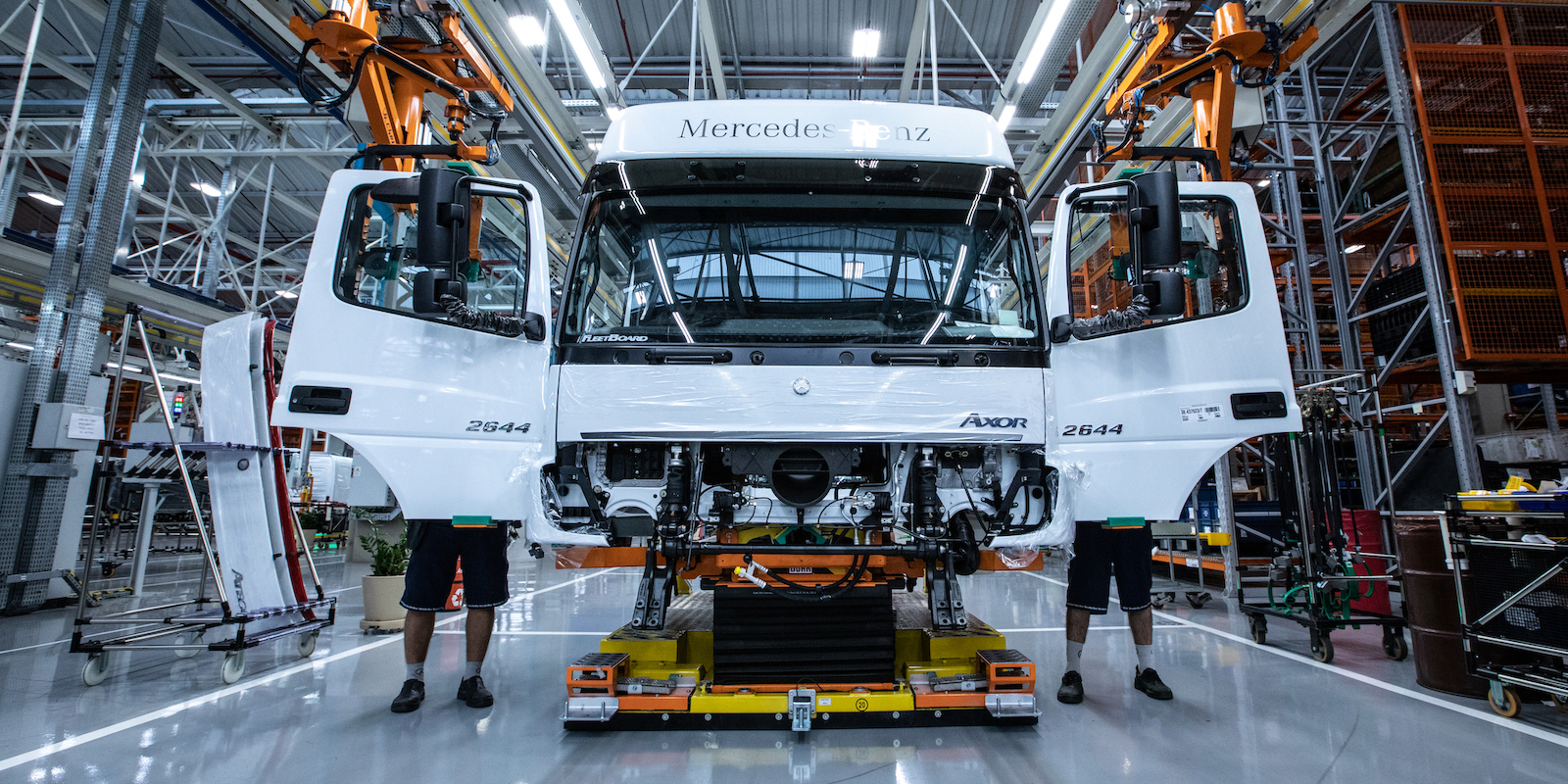
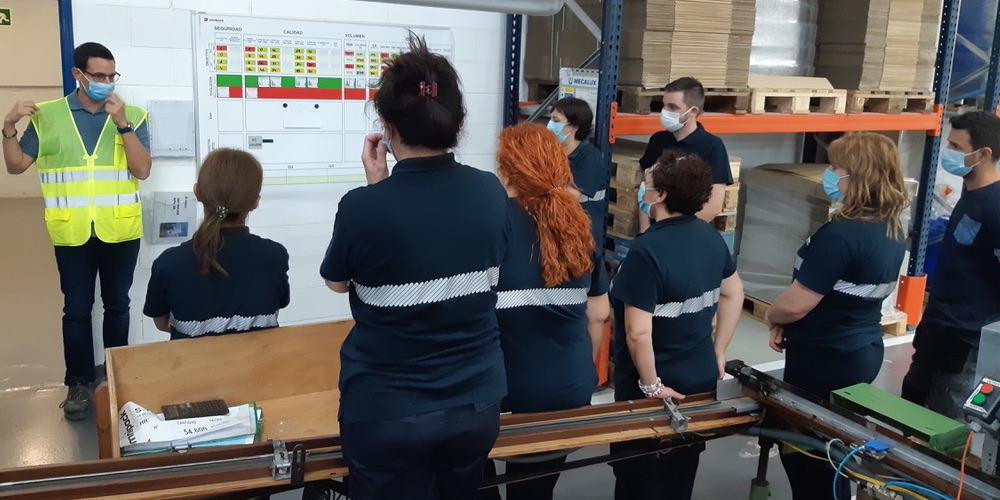
CASE STUDY – This article briefly outlines the different stages of the lean transformation at Mercedes Benz Brazil, as the company looked for the best approach to engage everyone in continuous improvement.
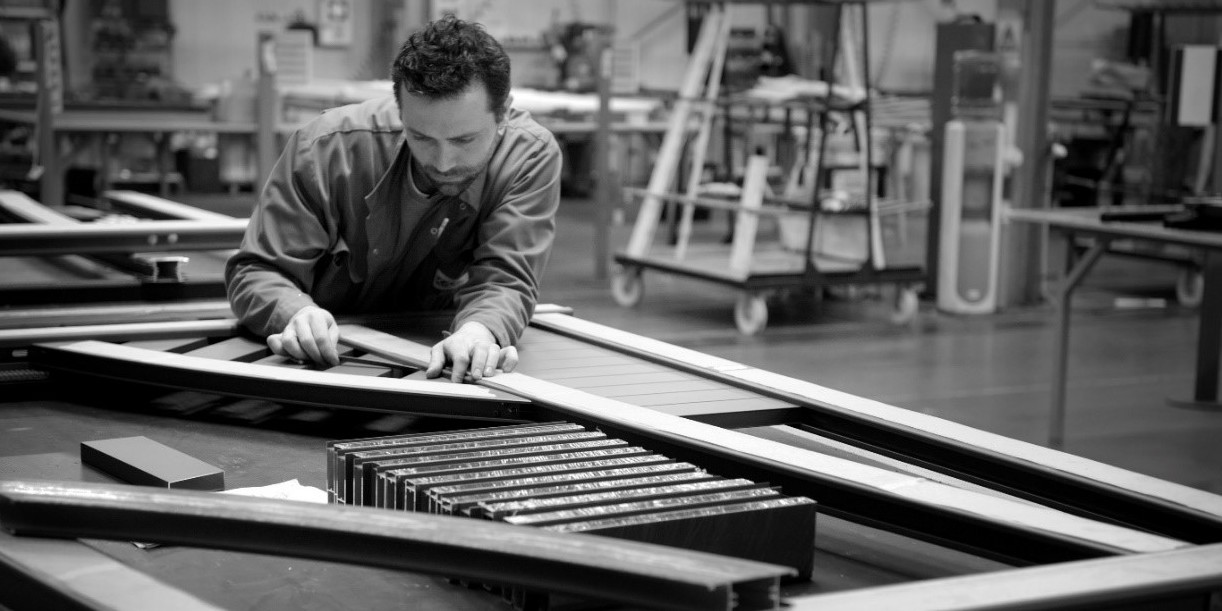
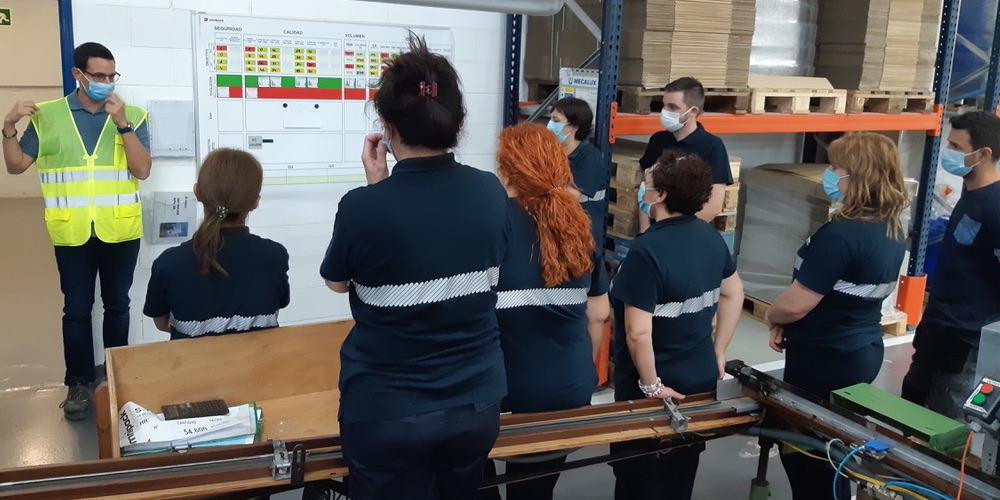
NOTES FROM THE GEMBA – By introducing flow in its processes and transforming its approach to managing the business, this French manufacturer of fences and gates is building a competitive advantage.
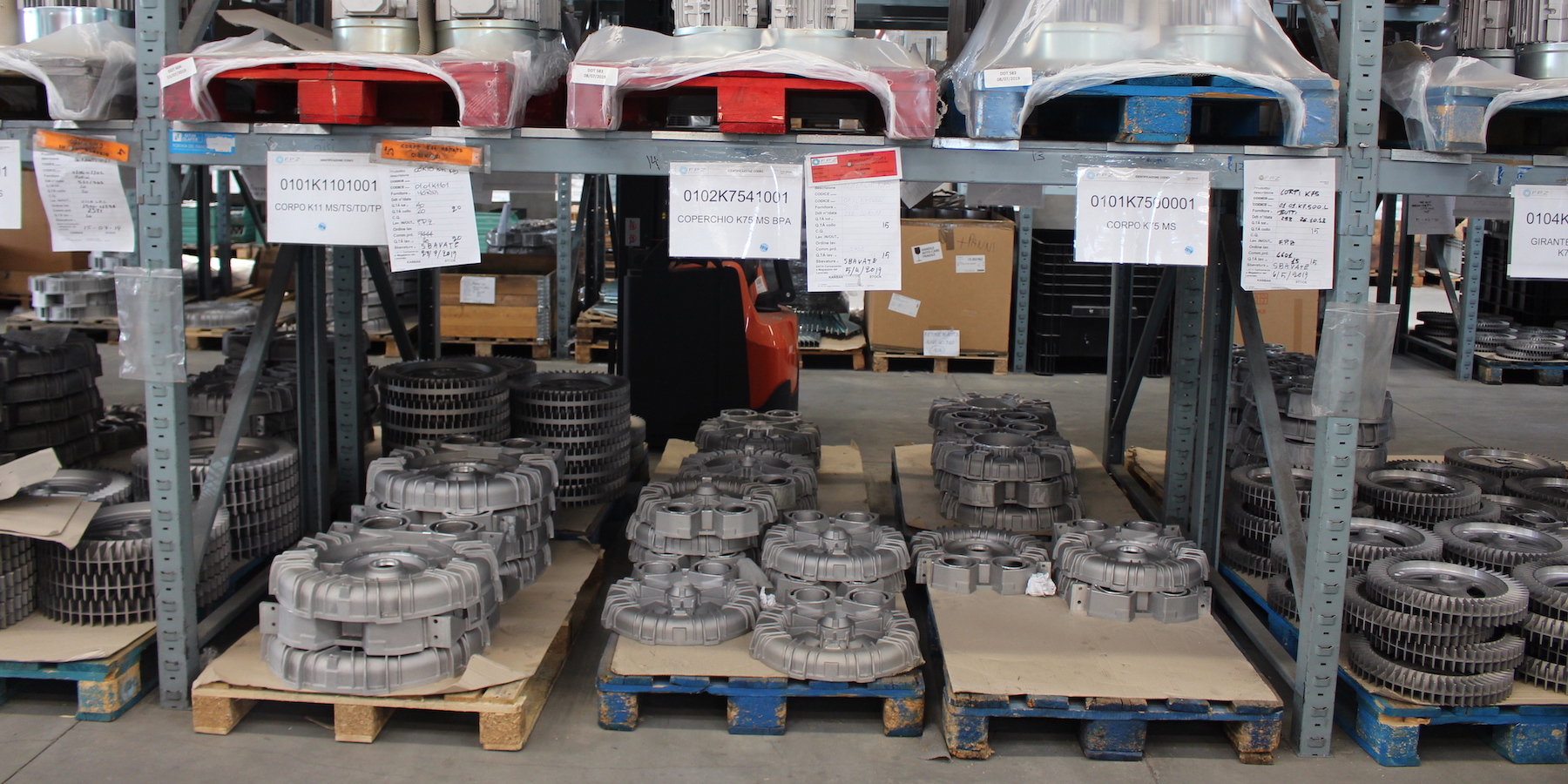
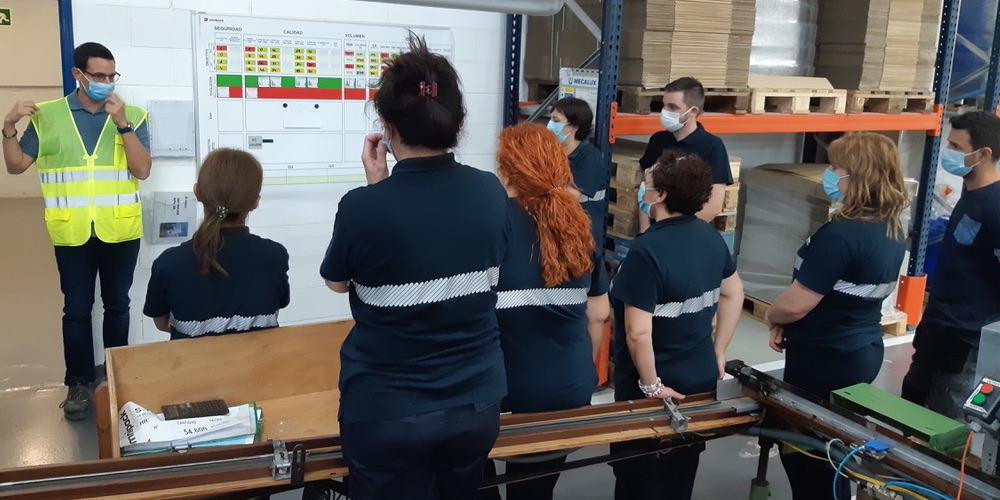
CASE STUDY – Seven years ago, this Italian manufacturer ran an experiment to reduce inventory in its warehouse. Today, lean thinking permeates every aspect of life at FPZ.
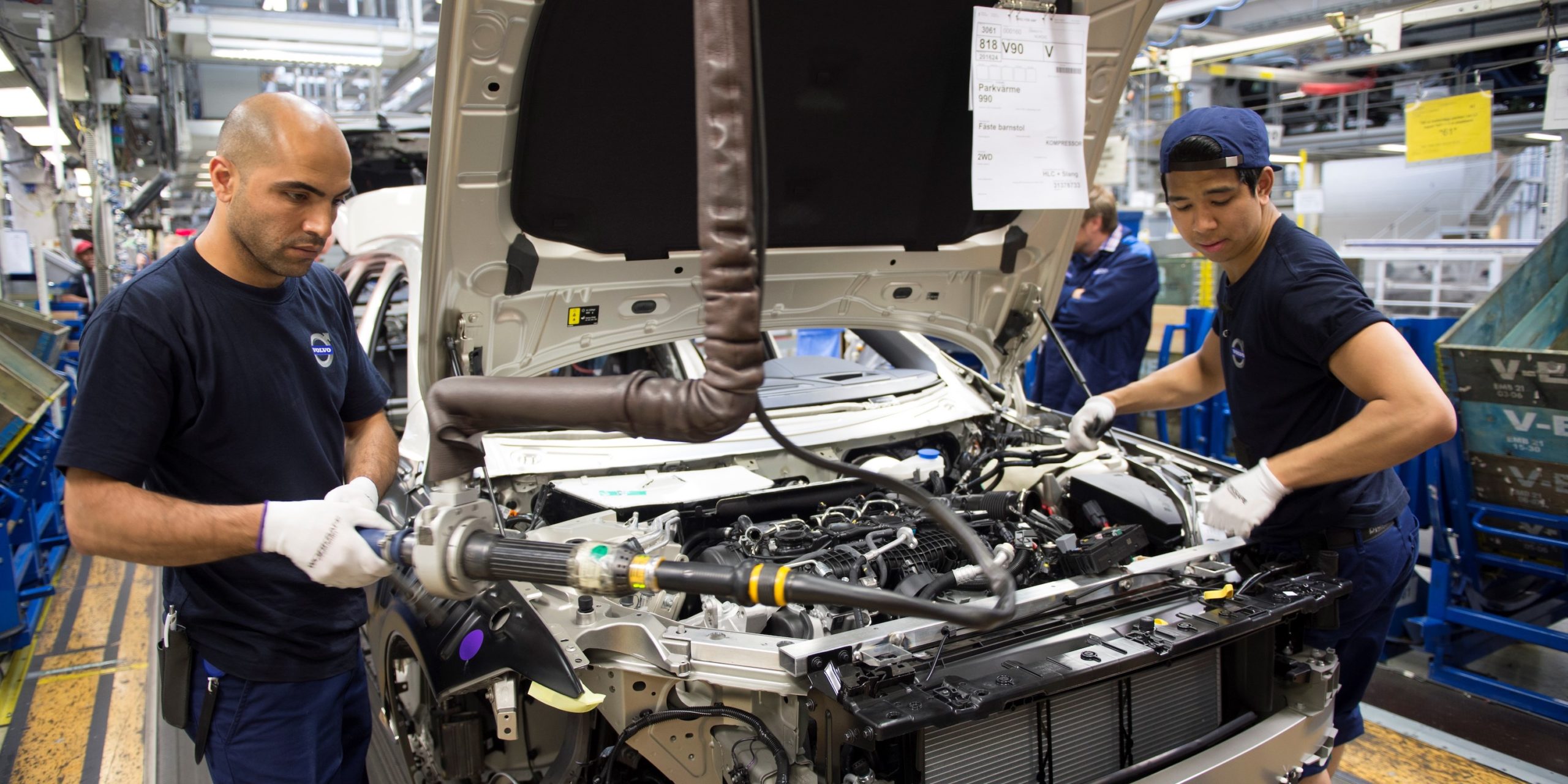
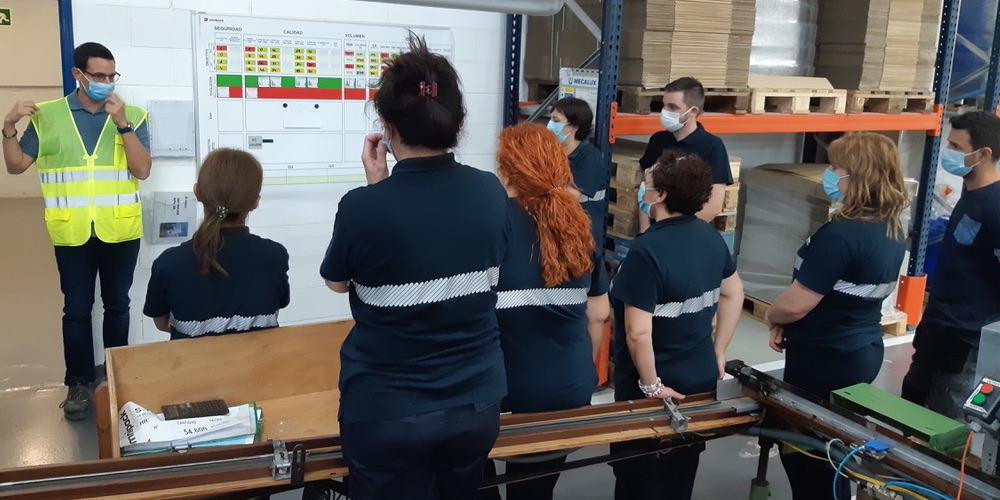
CASE STUDY – What is the approach to people development used at Volvo Cars? The authors explain how the organization has created a production system fully owned by operators and managers.
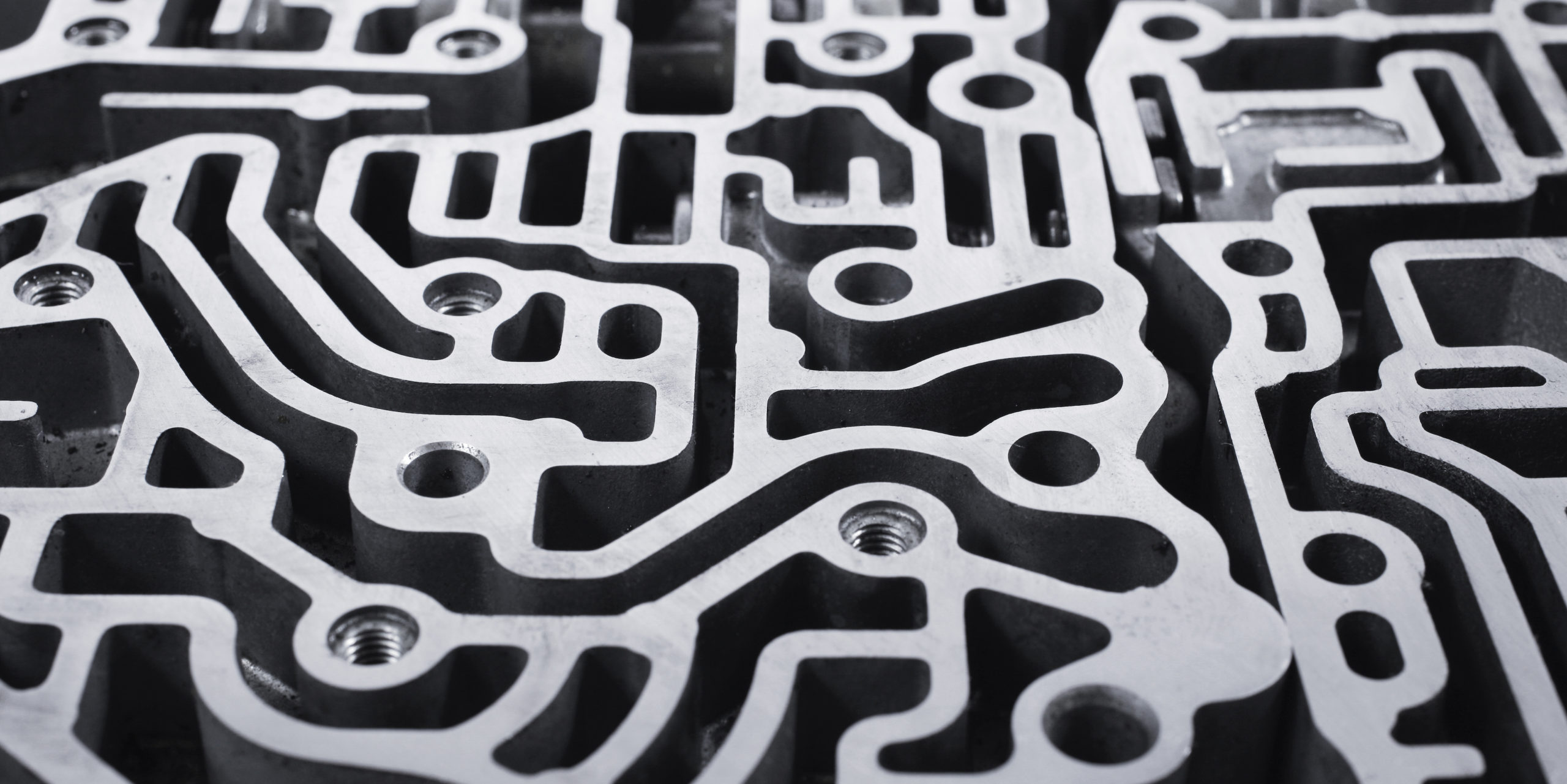
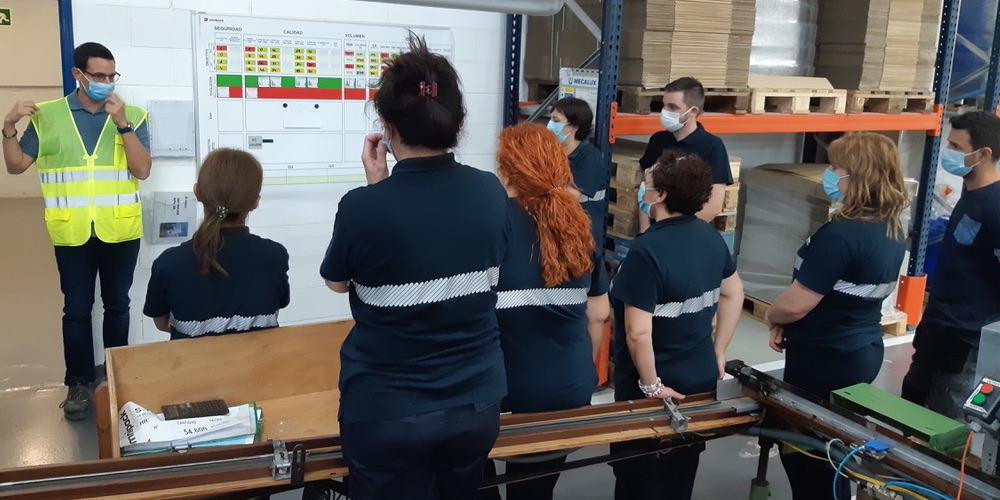
FEATURE – In a market where products become obsolete very fast, this Toyota supplier has learned the importance of staying true to its heritage and developing know-how and people’s capabilities.
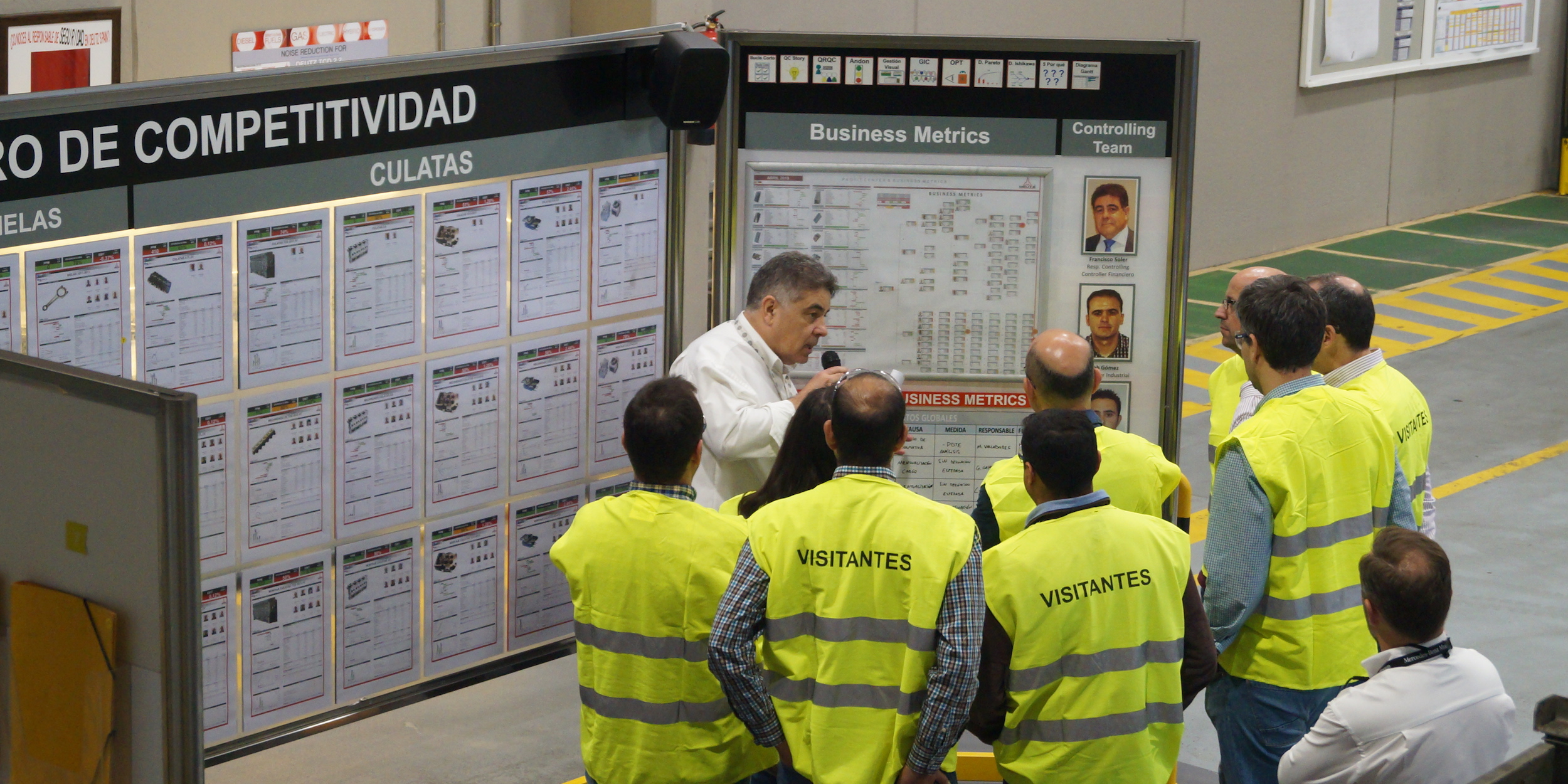
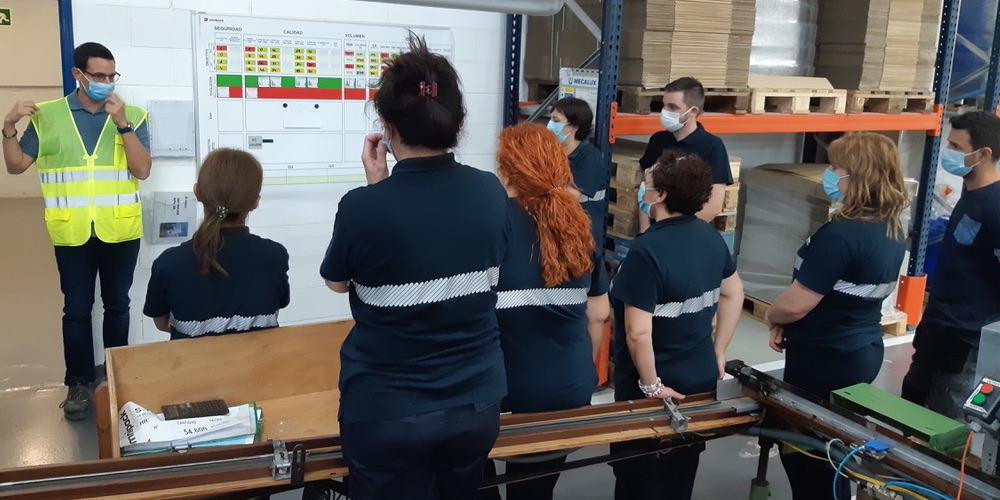
CASE STUDY – What to do when you operate in a competitive market and are located in a remote corner of Europe, thousands of miles from your customer? One word: lean.
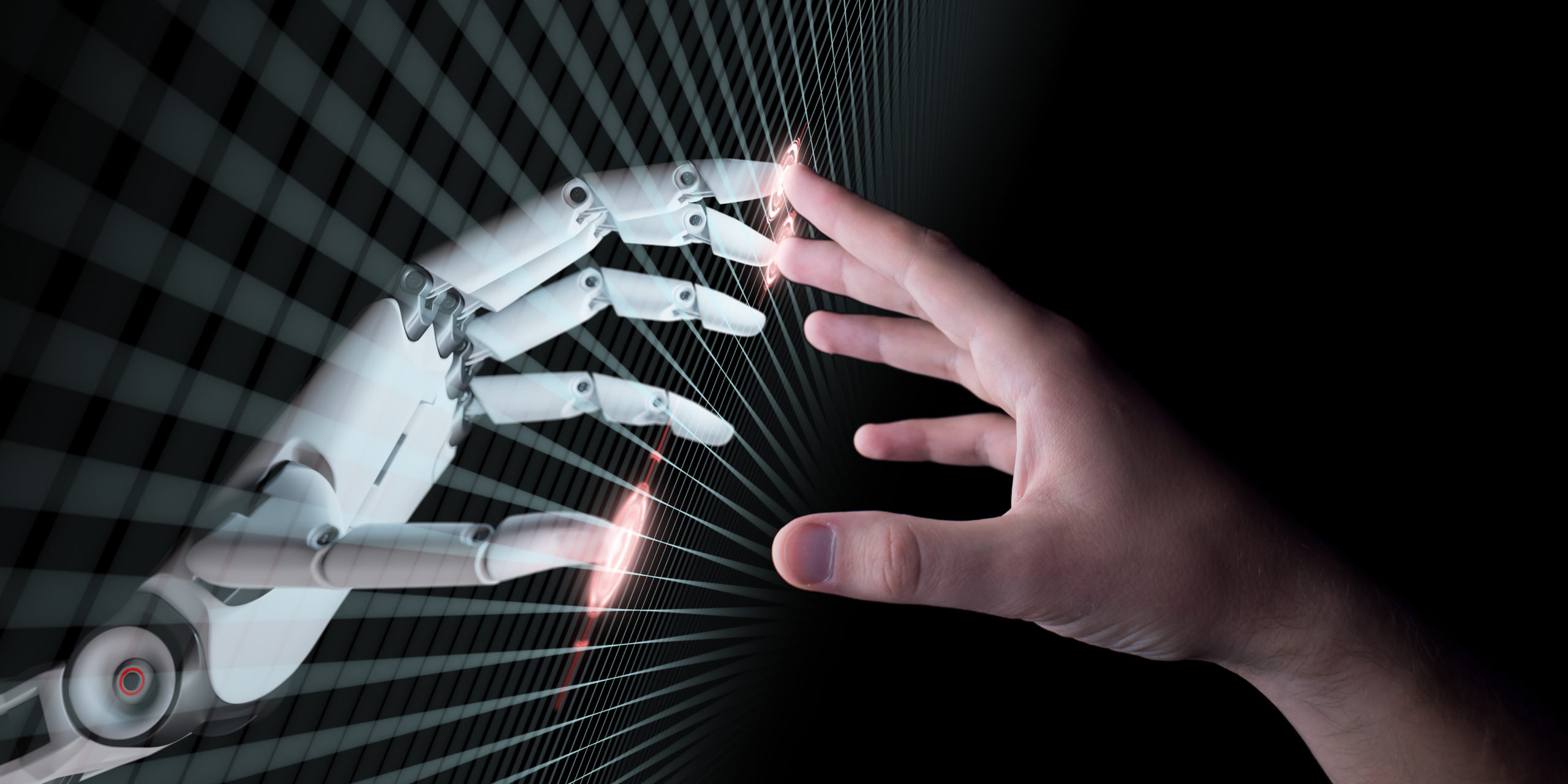
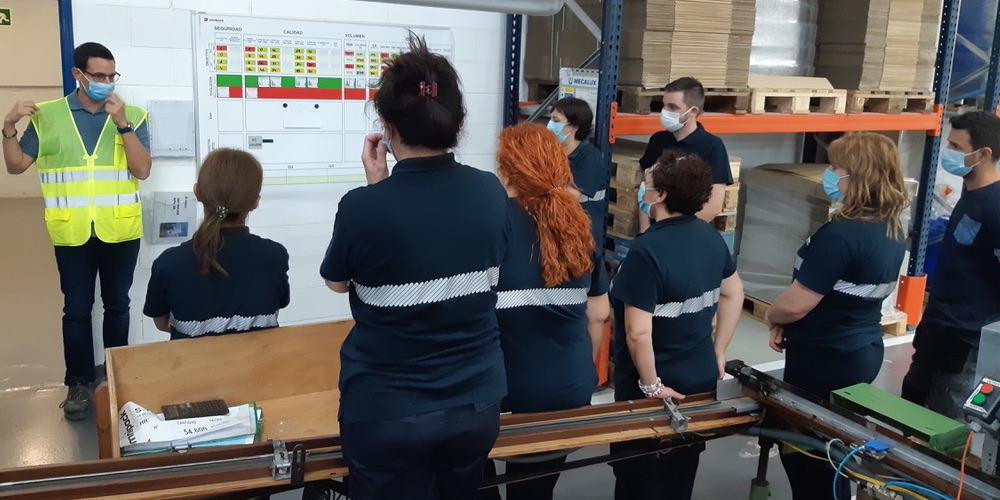
INTERVIEW – Atlantis Foundries was able to achieve zero defects for three months in a row thanks to machine learning. Here’s why the human component can’t be discounted.
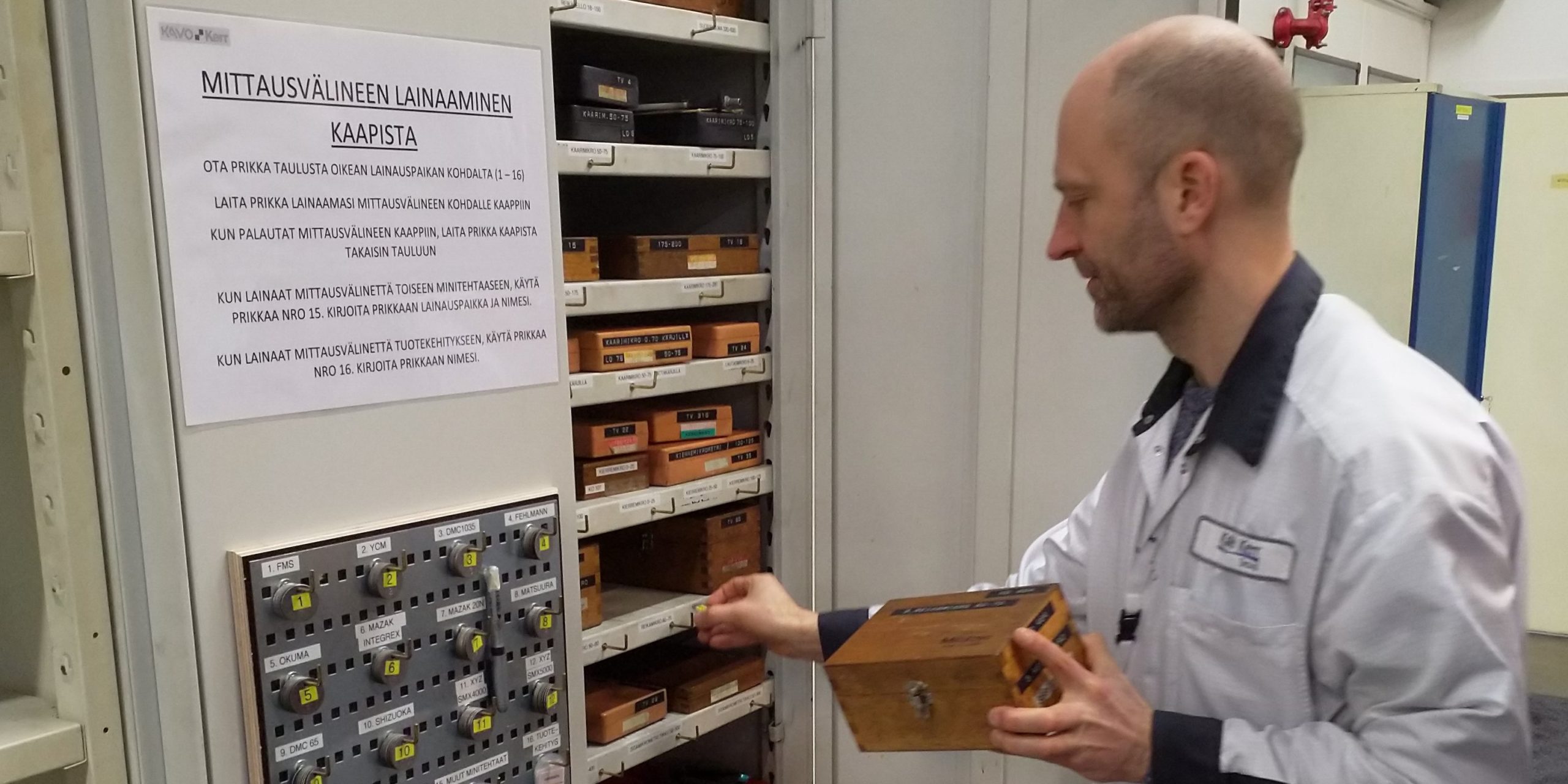
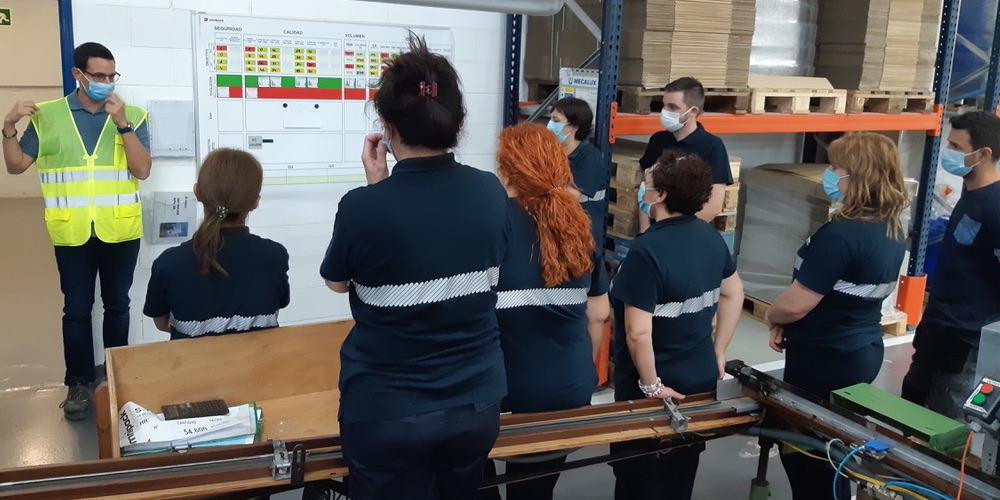
FEATURE – When people become enthusiastic about improvement work, there's no limit to what can be achieved. Join the author on a visit to a Finland-based manufacturer, whose lean efforts range from production to customer service.
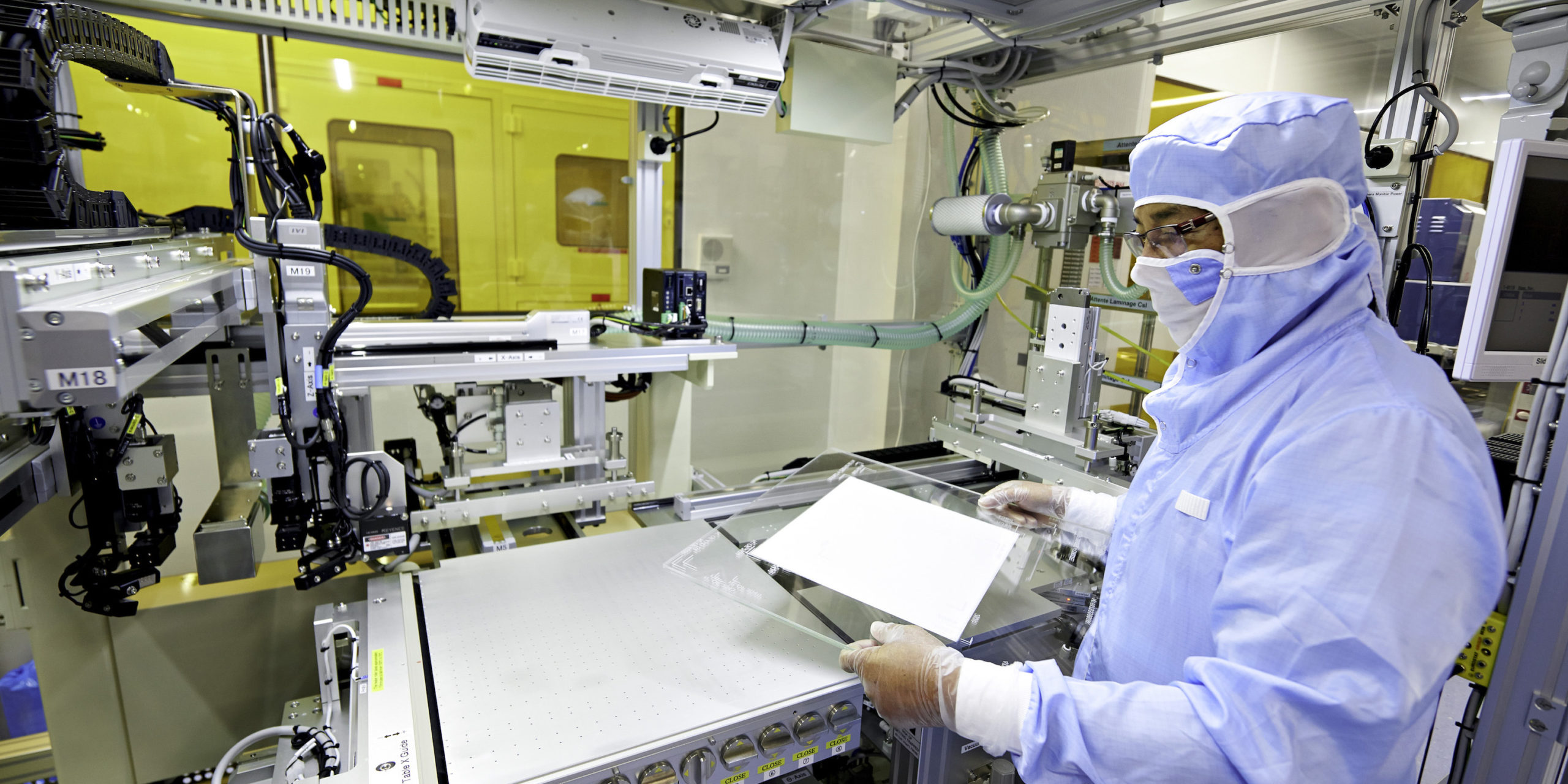
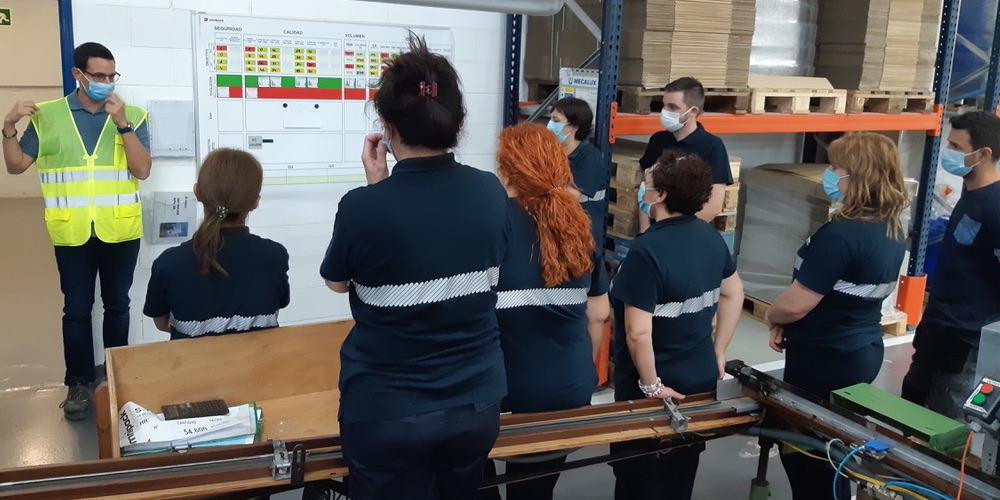
NOTES FROM THE GEMBA – A culture in which problems are tackled as soon as they appear and the production and product development teams work closely together is helping this French healthcare technology company to thrive.
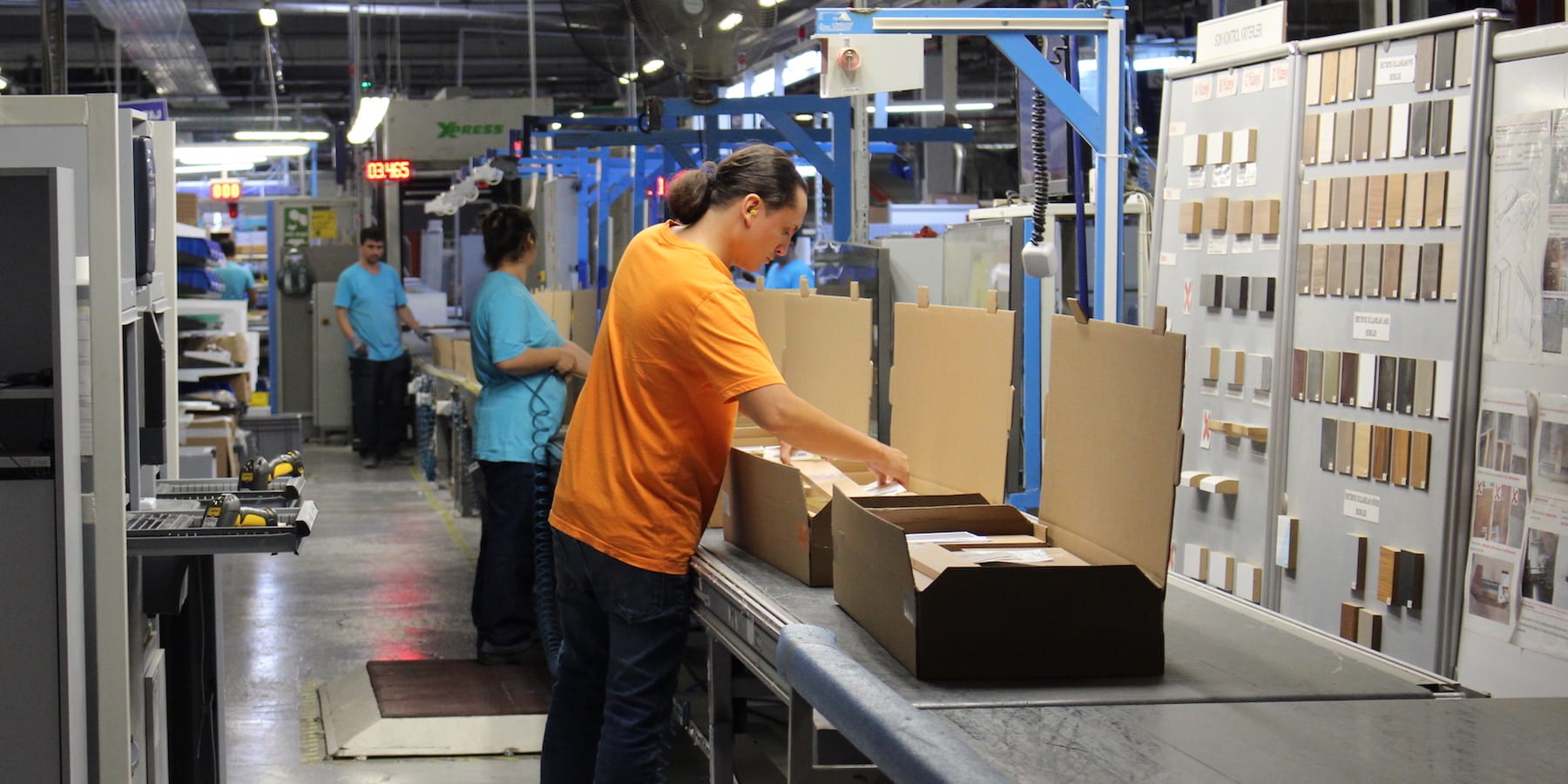
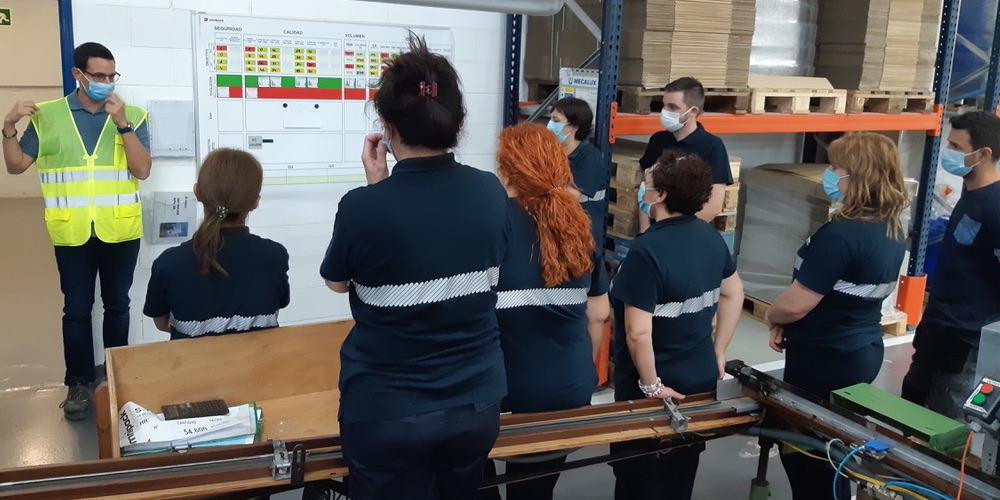
CASE STUDY – This Turkish producer of sanitaryware has boosted its quality so dramatically it’s now a player in the German market. It did so by bringing drastic change to its production system.
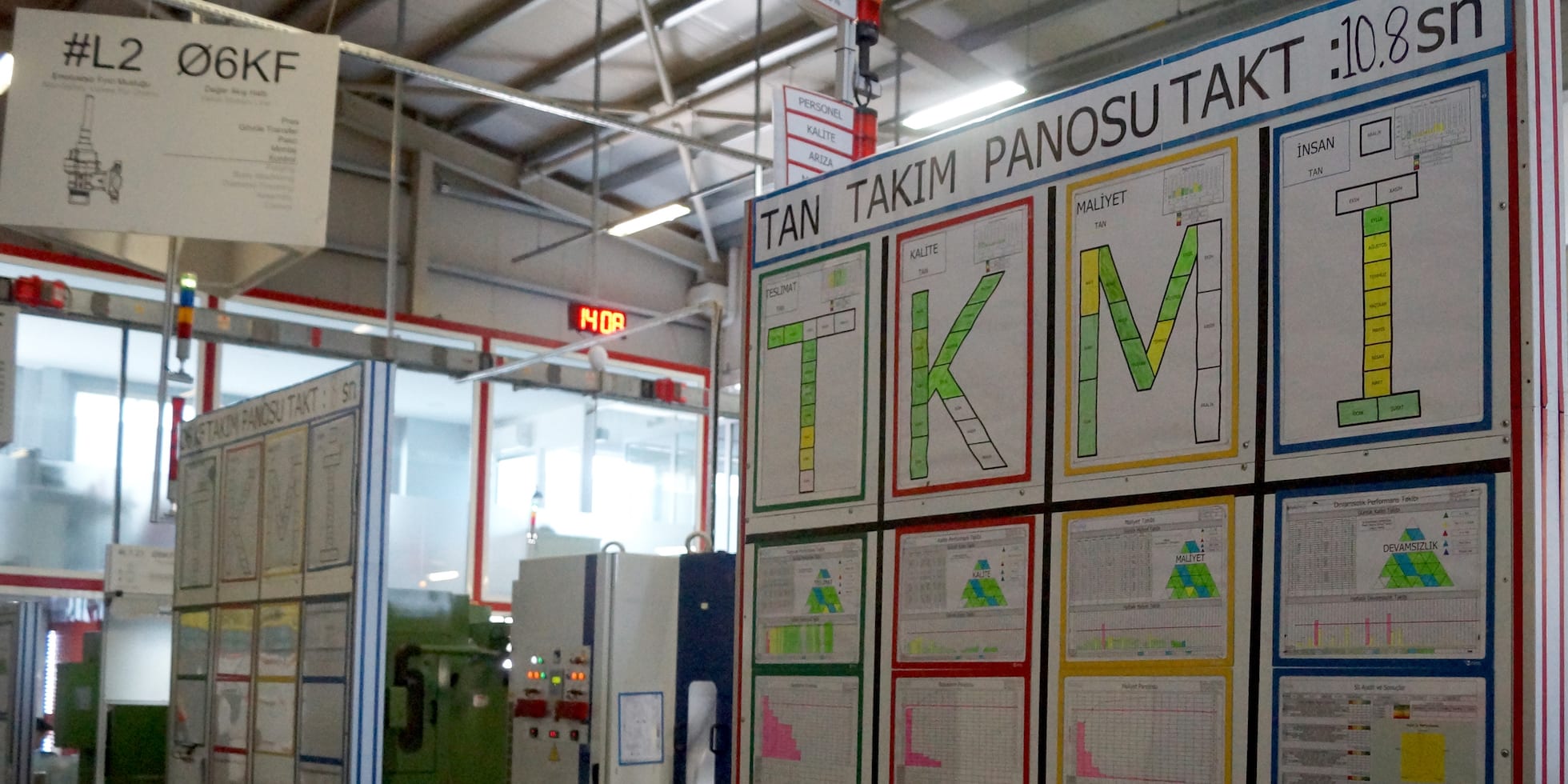
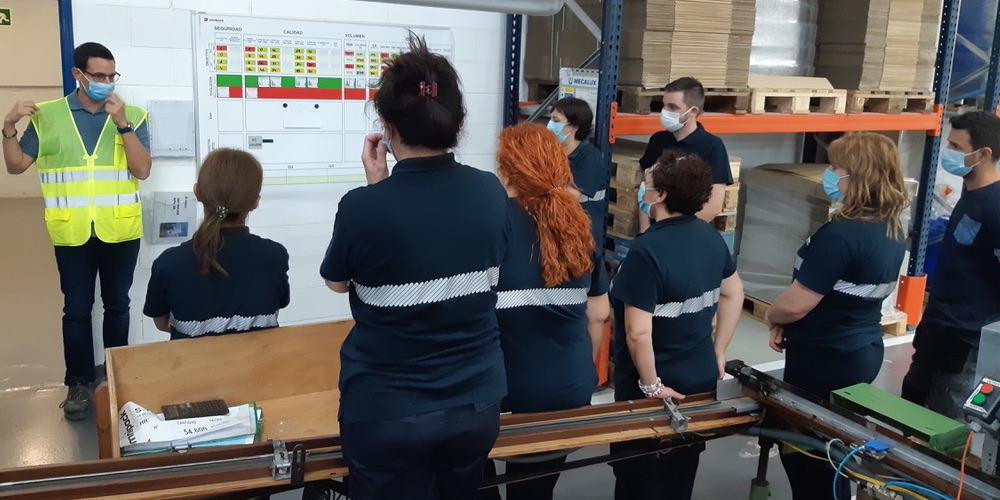
CASE STUDY – A Turkish producer of gas valves for kitchen appliances has discovered the power of the lean principles of pull and flow, reaching results beyond its imagination.
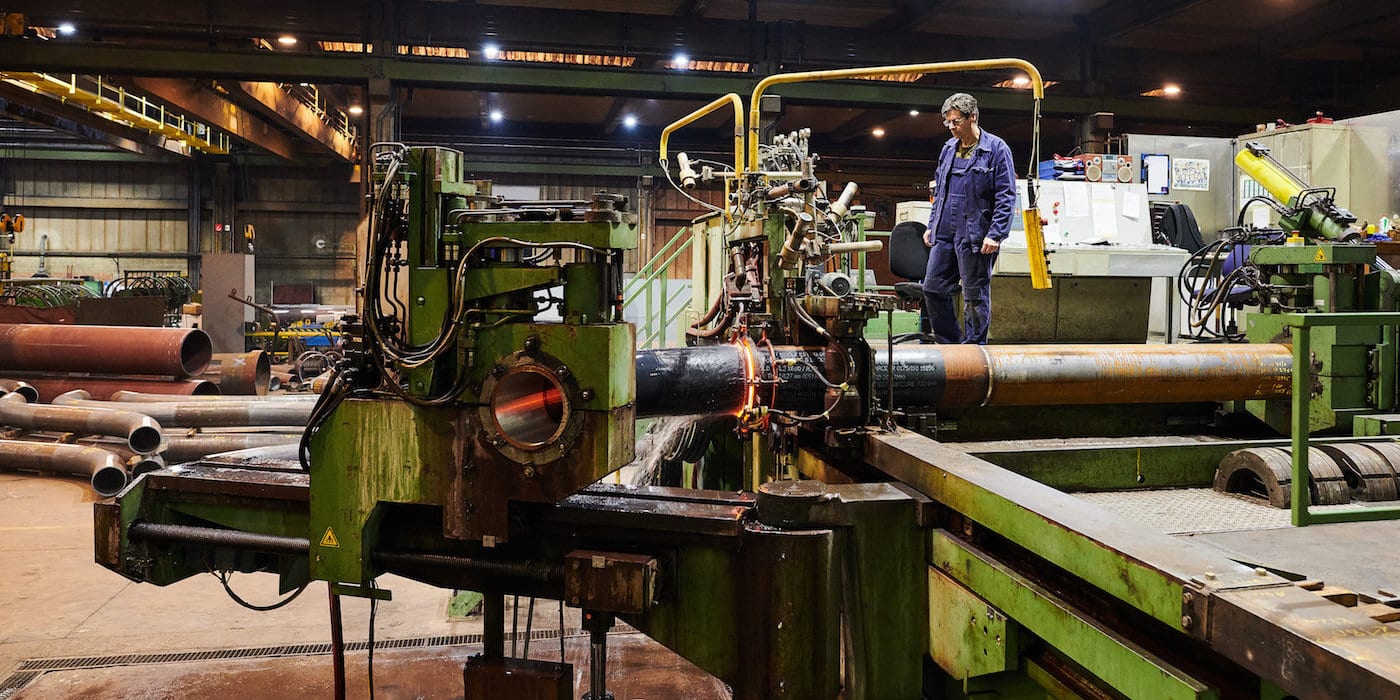
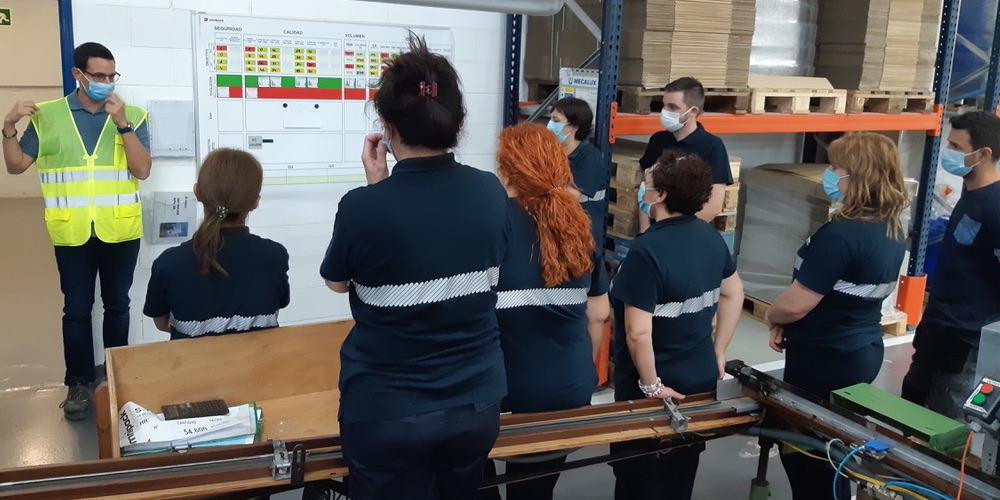
FEATURE – This Dutch company decided to start its lean journey by involving its suppliers in the improvement work. We hear from both customer and supplier.
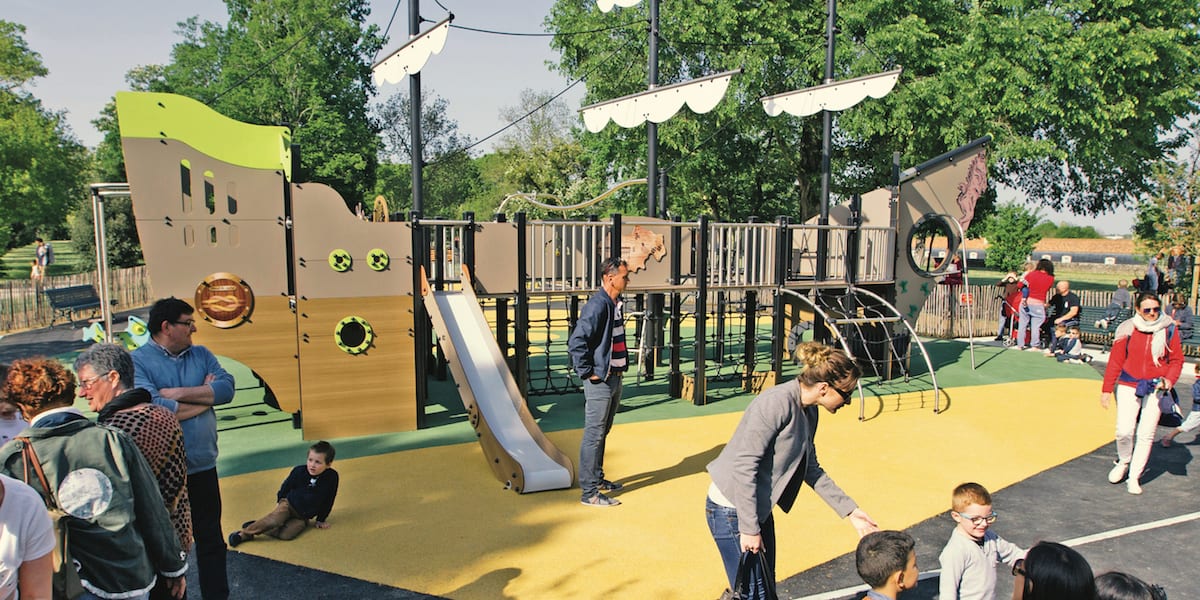
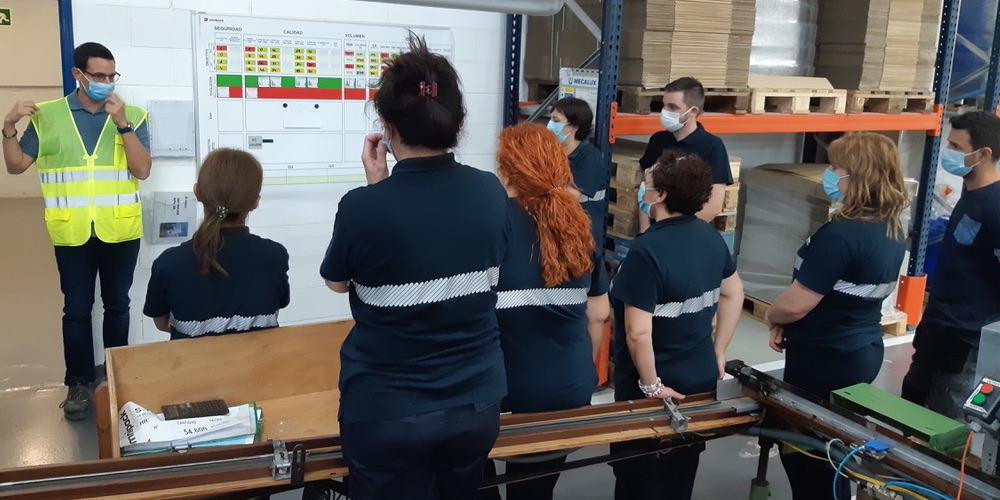
FEATURE – Enabling its people to think autonomously about problems and fostering collaboration among departments is allowing a French company that makes and installs playgrounds to thrive.
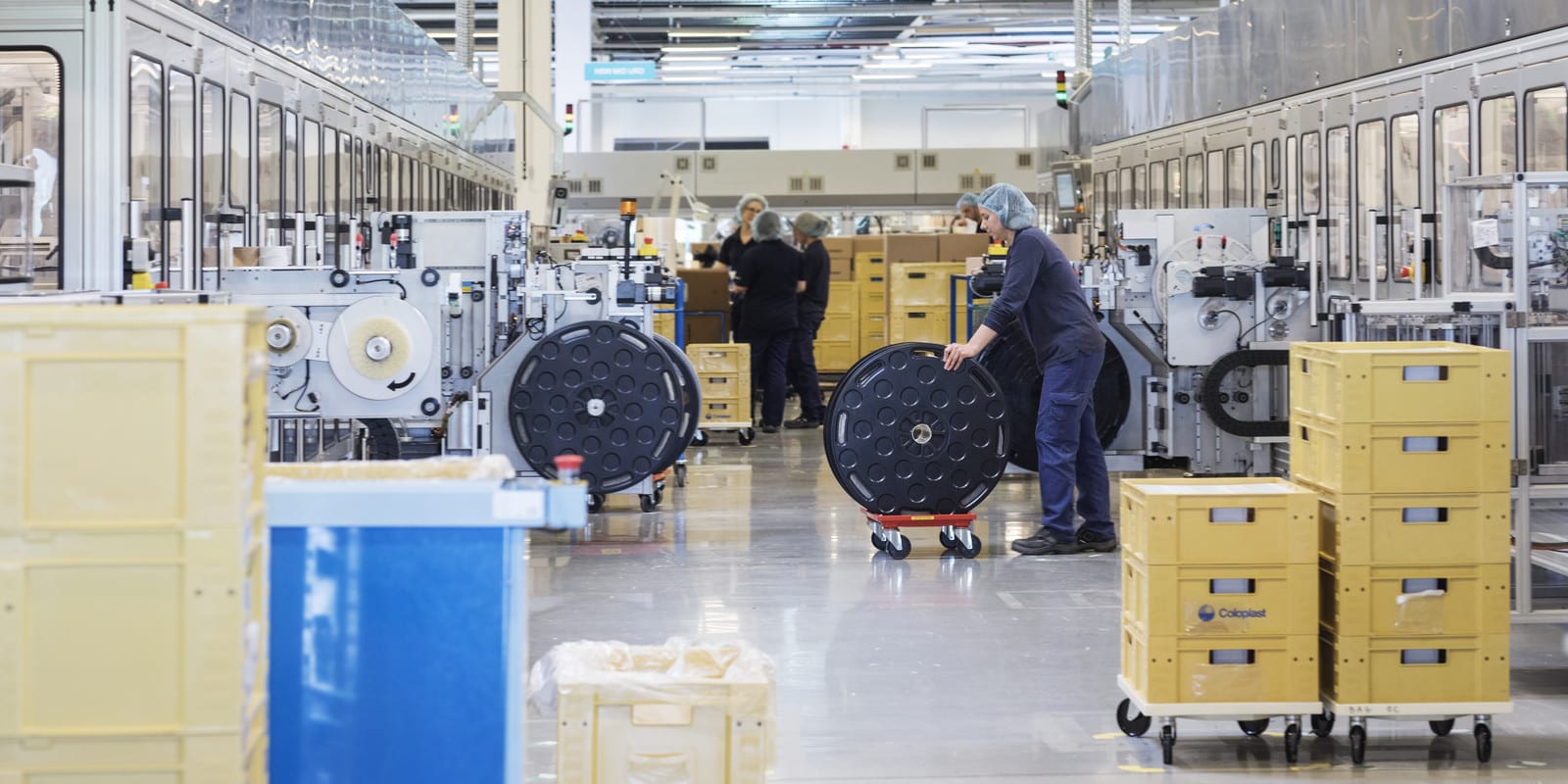
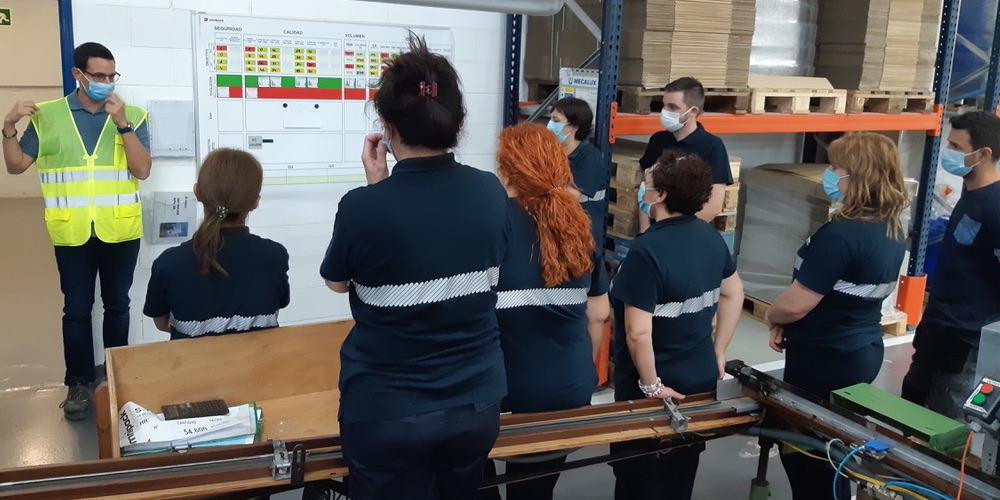
CASE STUDY – The author looks back at the impressive lean transformation of the Hungarian plant of Coloplast, a Danish company offering medical devices and services.
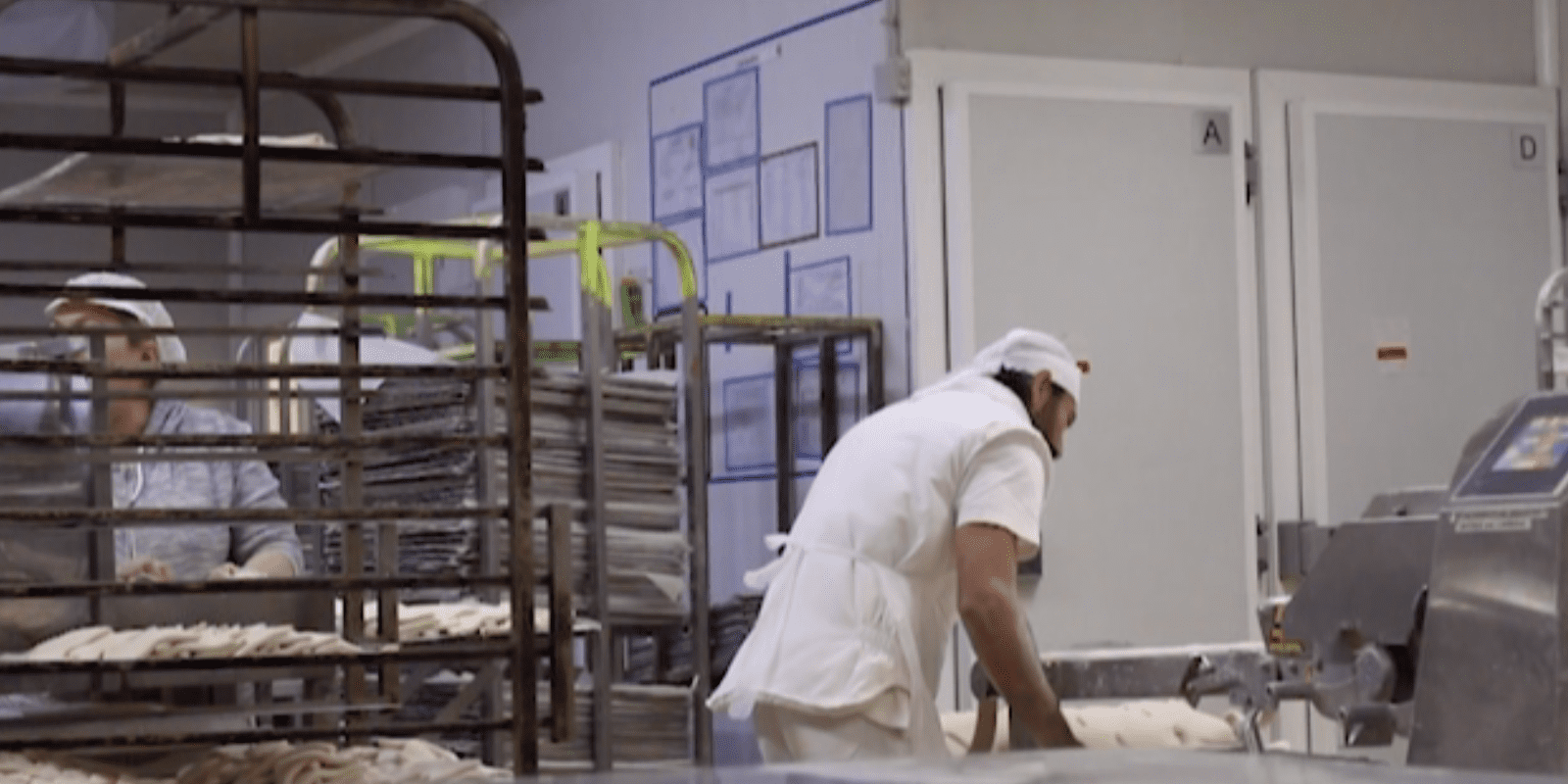
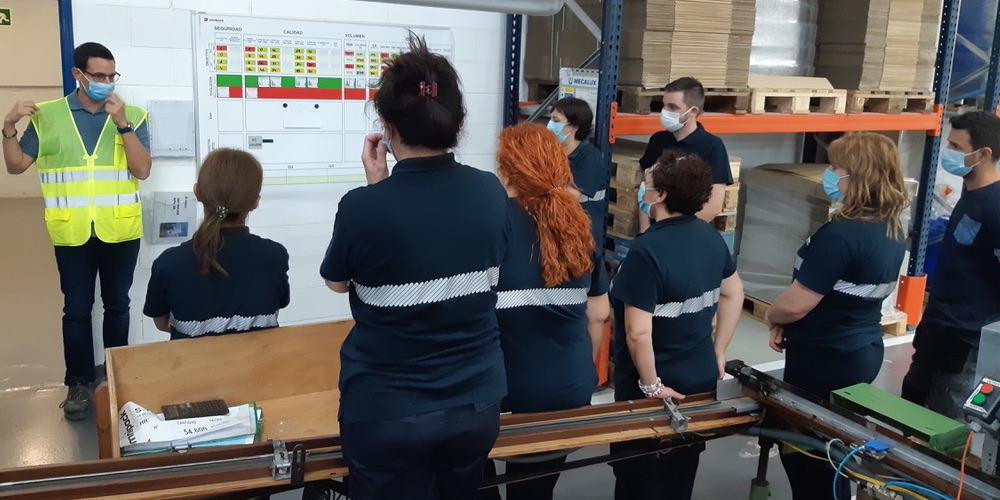
THE LEAN BAKERY – In the fourth episode in our video series, the CEO of 365 explains how lean showed him that his business could grow (exponentially) without using any extra resources.
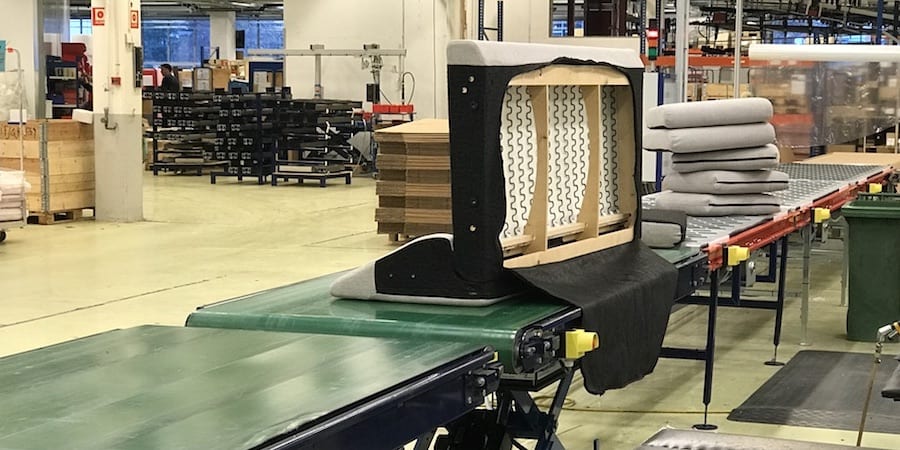
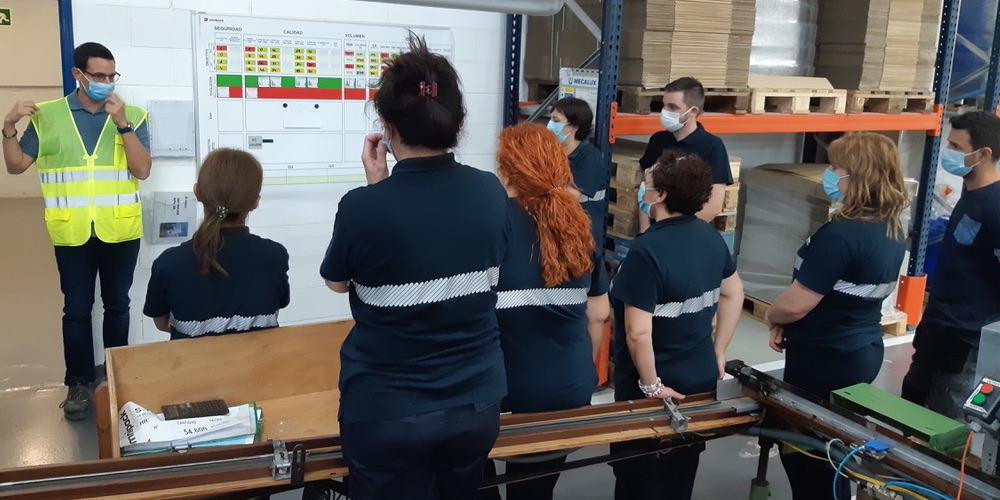
FEATURE – Sometimes all you need to change minds is a successful experiment. This is how a Norwegian furniture manufacturer managed to transform the way it thinks about its sofa production.
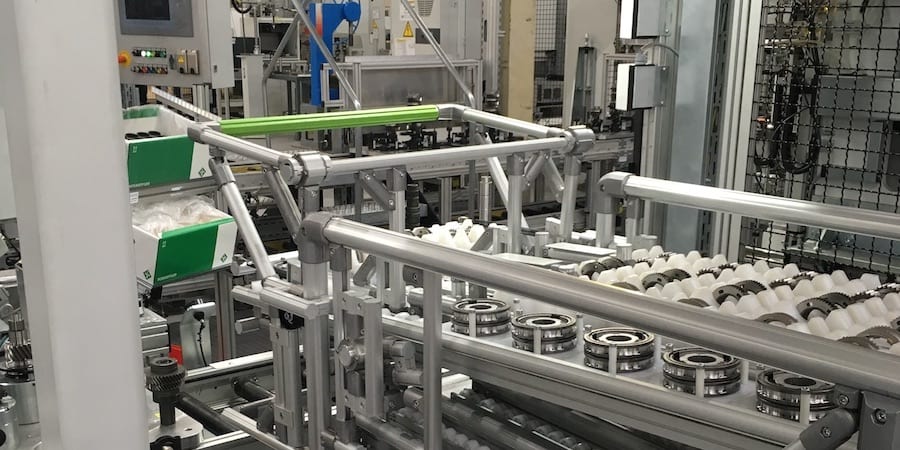
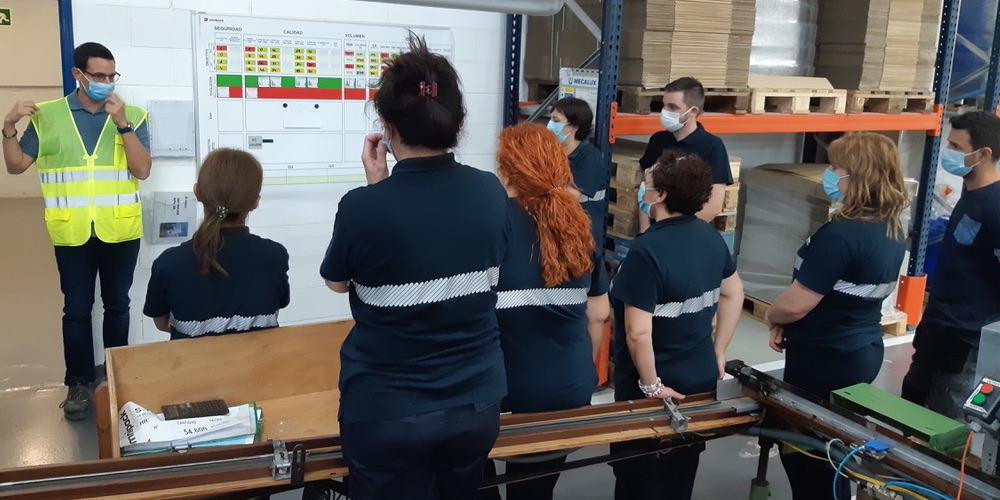
NOTES FROM THE GEMBA – If you need proof that kaizen leads to real innovation, look no further than AIO. This French Tech company that reinvented itself as a karakuri kaizen coach.
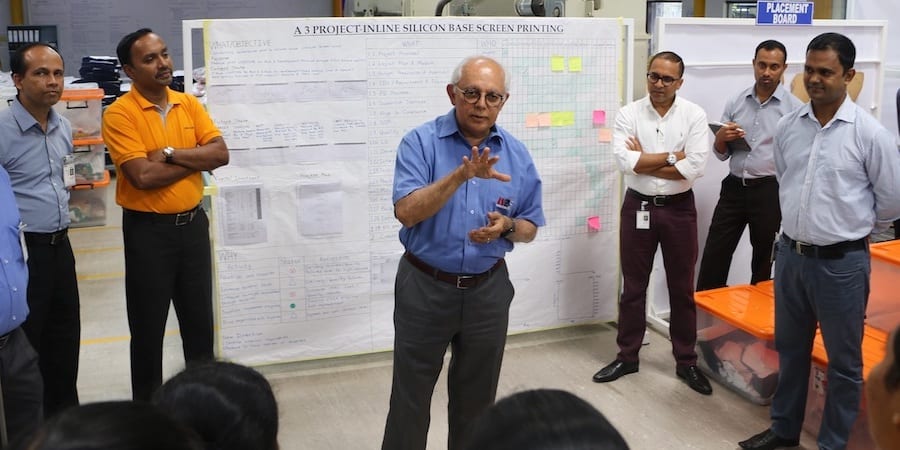
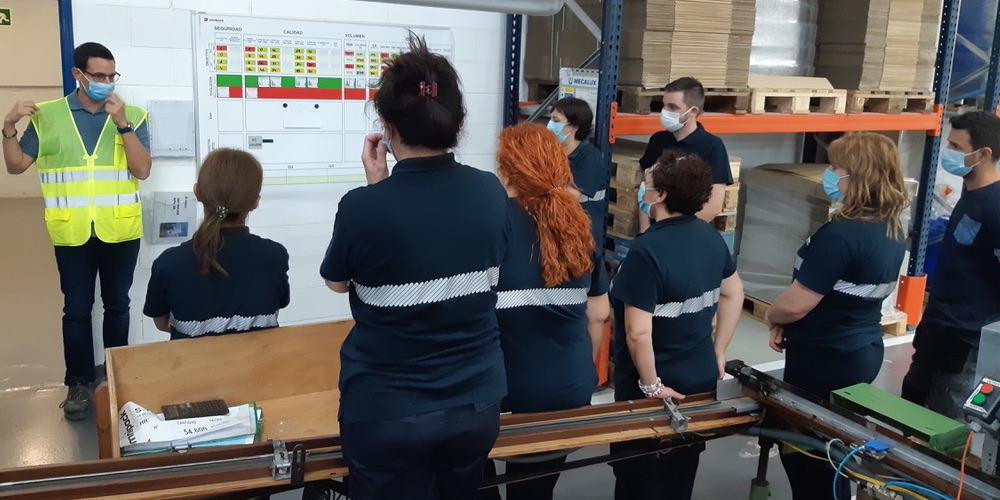
INTERVIEW – Prior to his talk at this year’s Lean Transformation Summit, the CEO of a large apparel manufacturer tells us about the company’s lean journey, and its impact on Sri Lankan society.
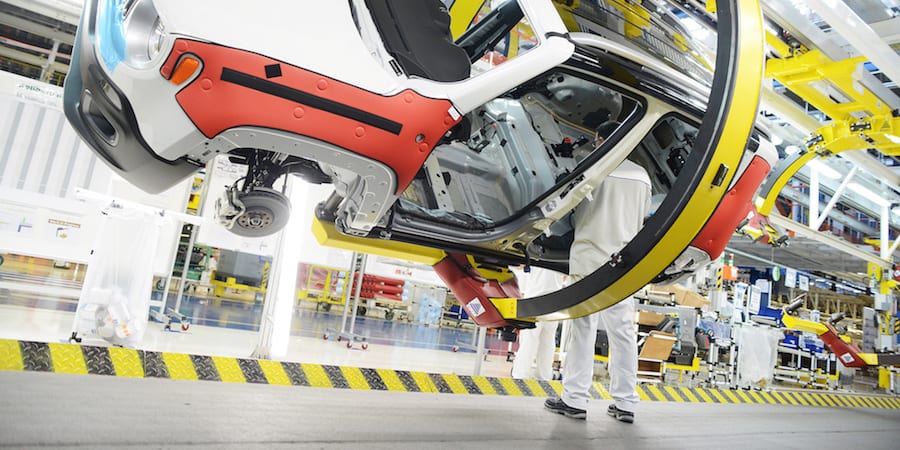
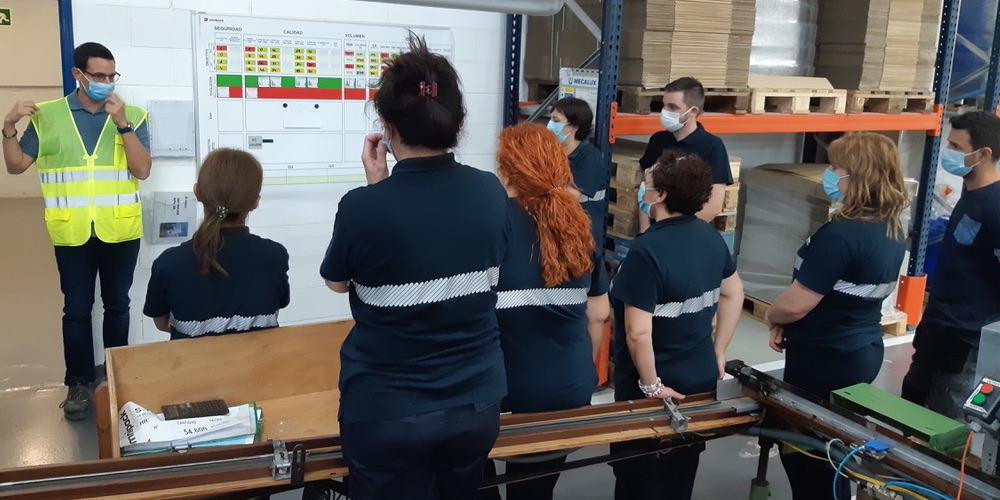
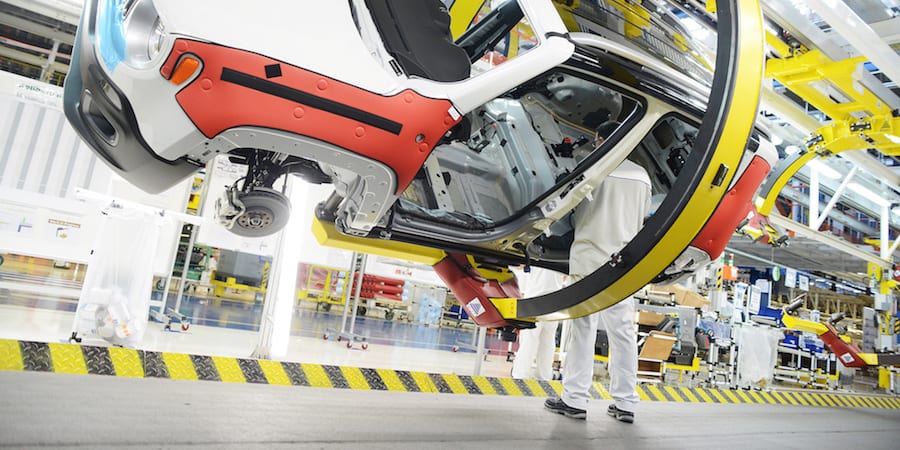
INTERVIEW – At the recent European Lean Summit, we sat down with a senior executive from Fiat Chrysler Automobiles to learn more about the company’s World Class Manufacturing approach.
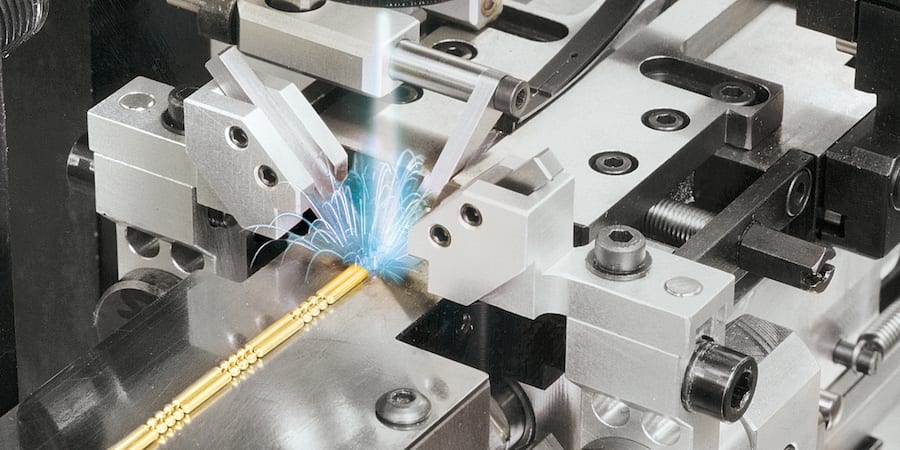
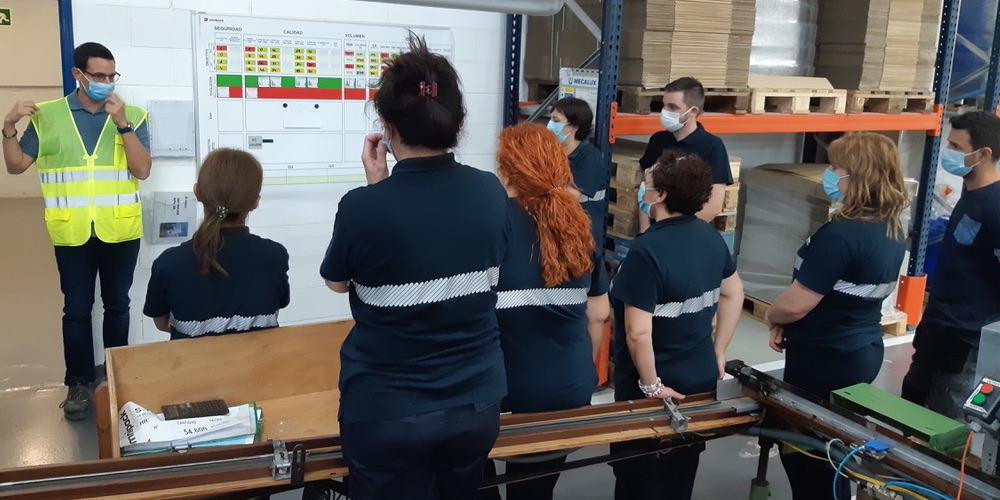
INTERVIEW – Italy-based precision machinery manufacturer Sisma has changed skin many times over the years. We sat down with its general manager to learn how the firm has been able to continuously innovate over the years.
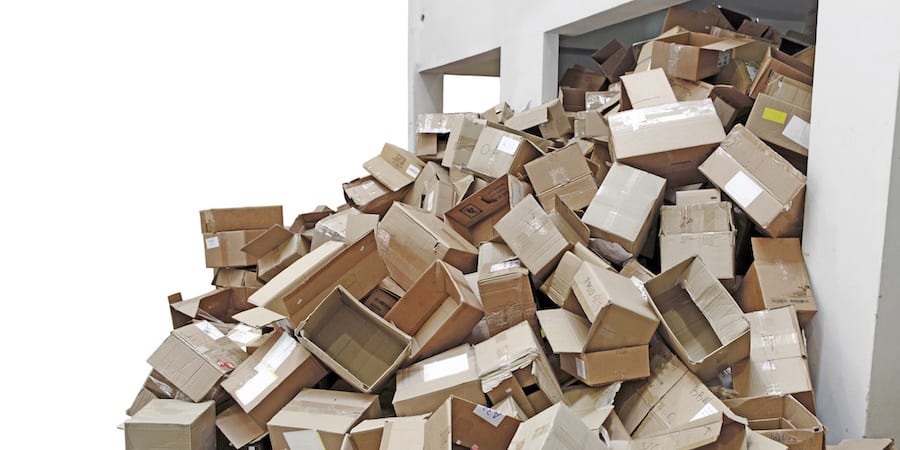
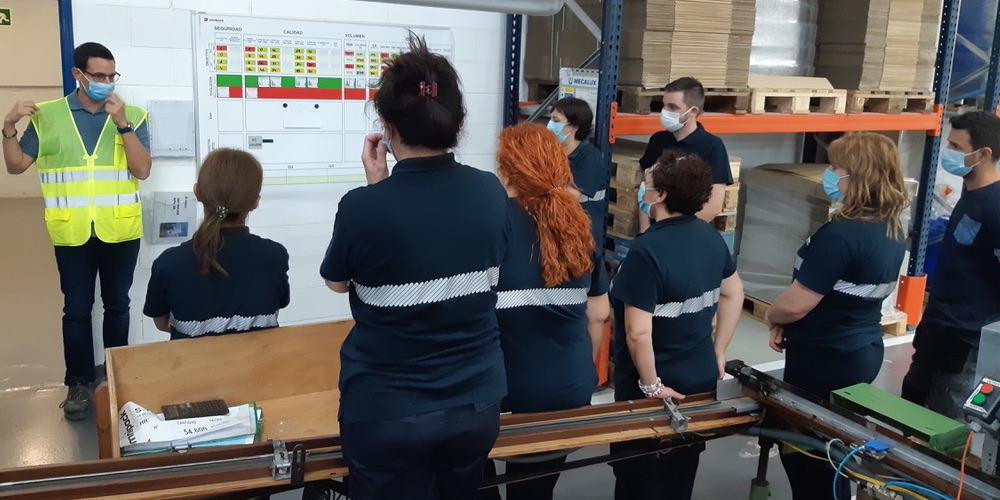
FEATURE – There is a form of waste – complexity in raw and packaging materials – that adds costs to manufacturing without creating value, but it is often overlooked. The author explains what it is and how to banish it.
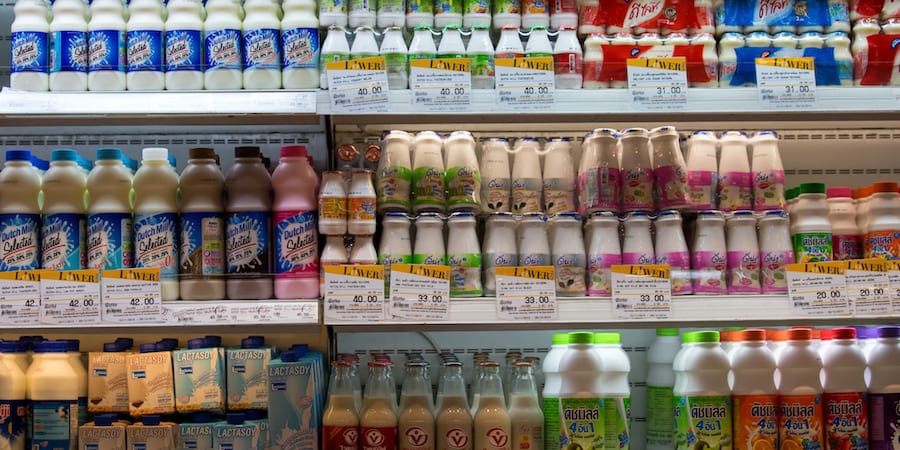
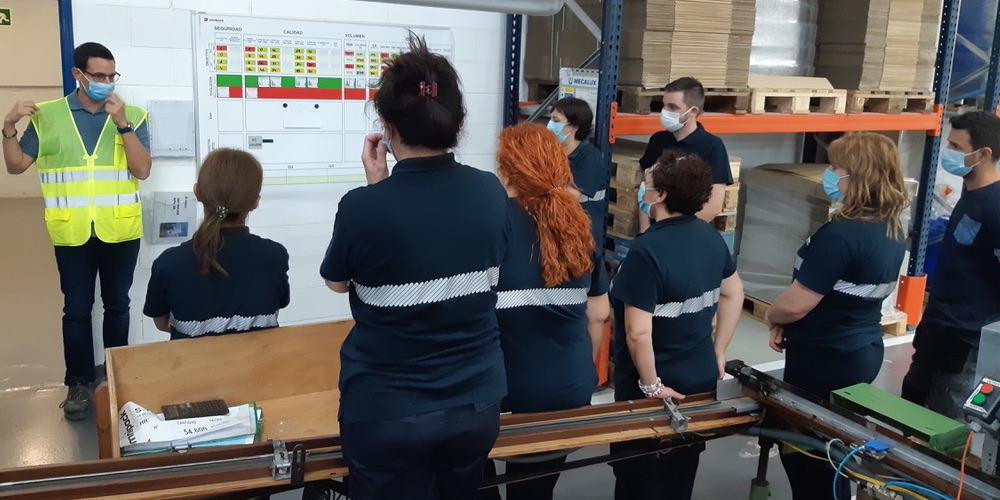
FEATURE – We often think that making every product customers might want – no matter how little they sell or how much complexity they add to our schedule – is inherently lean. As Toyota understands quite well, however, it is quite the opposite.
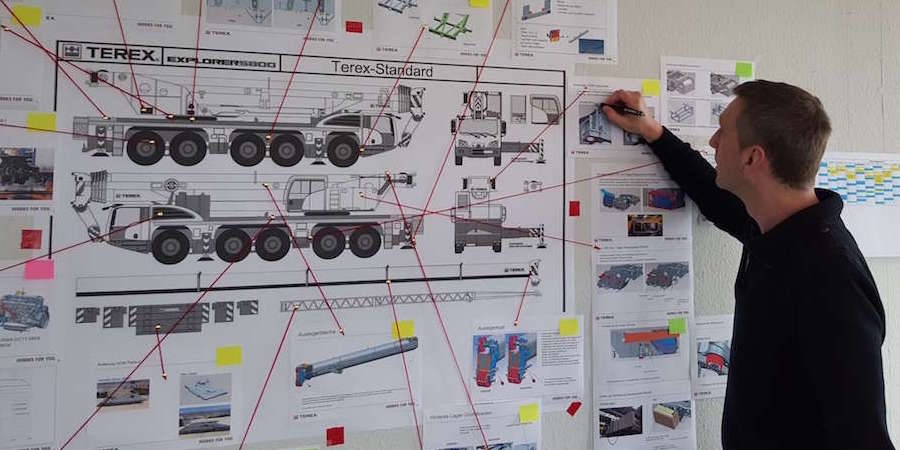
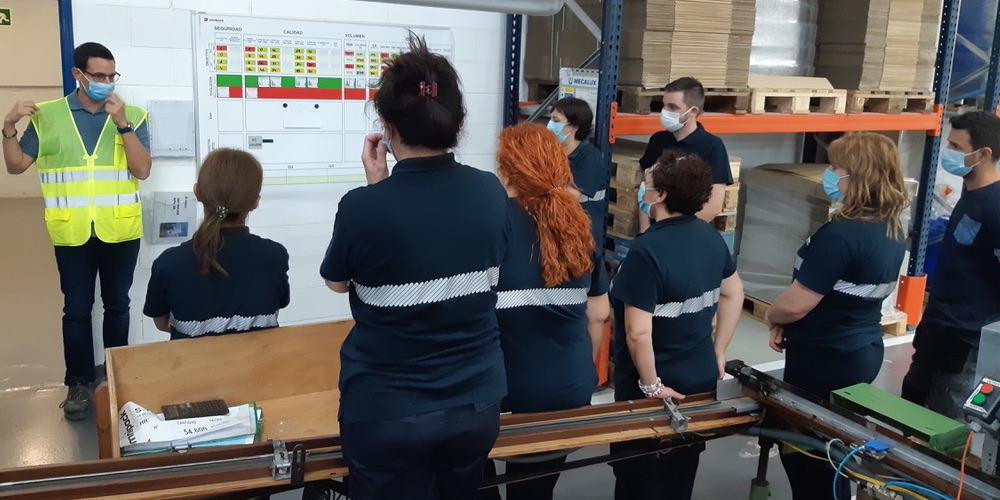
NOTES FROM THE GEMBA – In the past 15 months Terex Cranes has successfully initiated a lean transformation. Follow Catherine Chabiron on her gemba walk to see what this large company is doing to put learning at the heart of its activities.
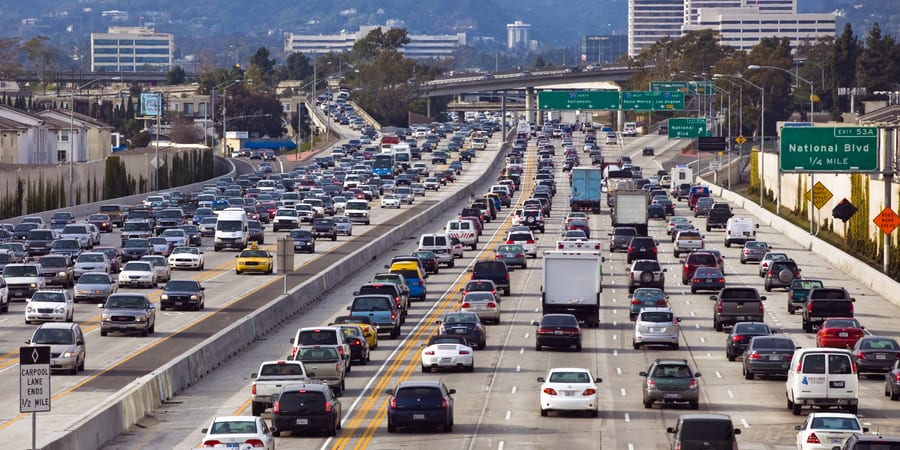
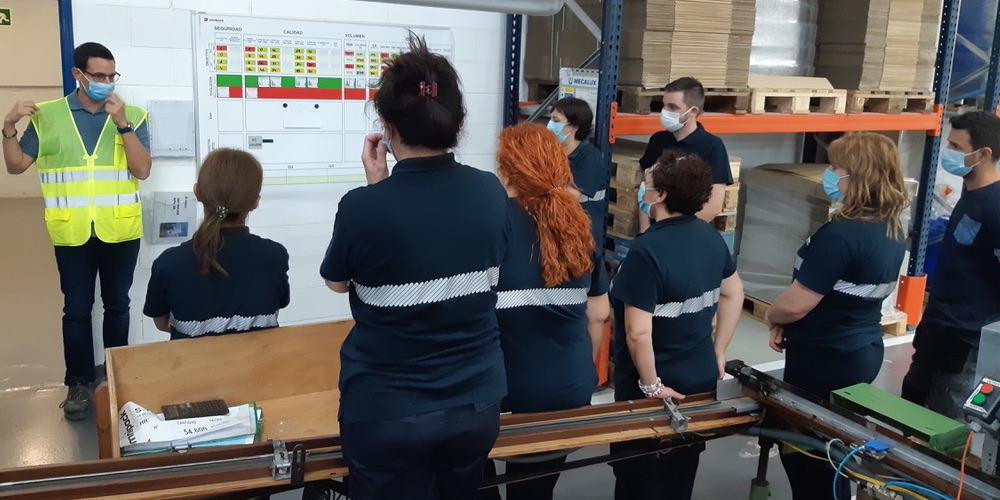
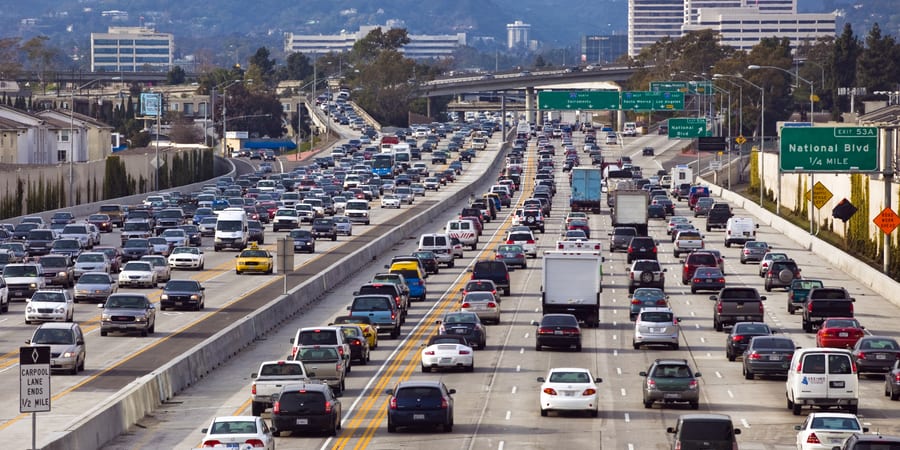
WOMACK’S YOKOTEN – In this month’s column, Jim shares an insightful analysis of the trends and dynamics of today’s automotive industry and looks at the opportunity that lean has to facilitate its next transformation.
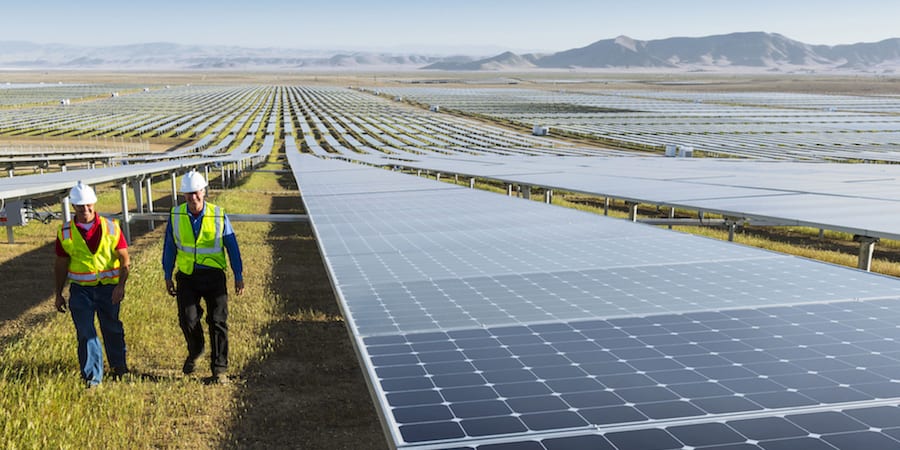
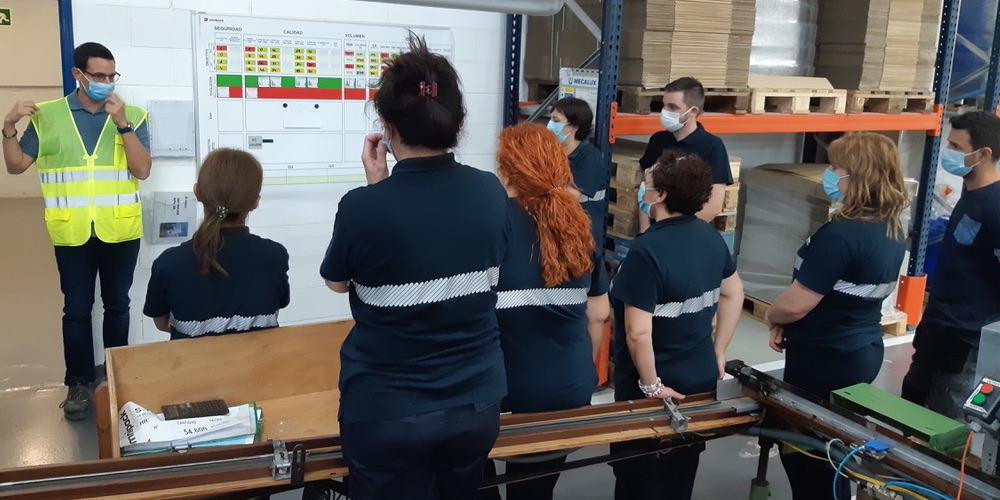
FEATURE – The experience of solar company SunPower shows how, by marrying the concept of circular economy, lean principles can help us to transform our habits and save our planet.
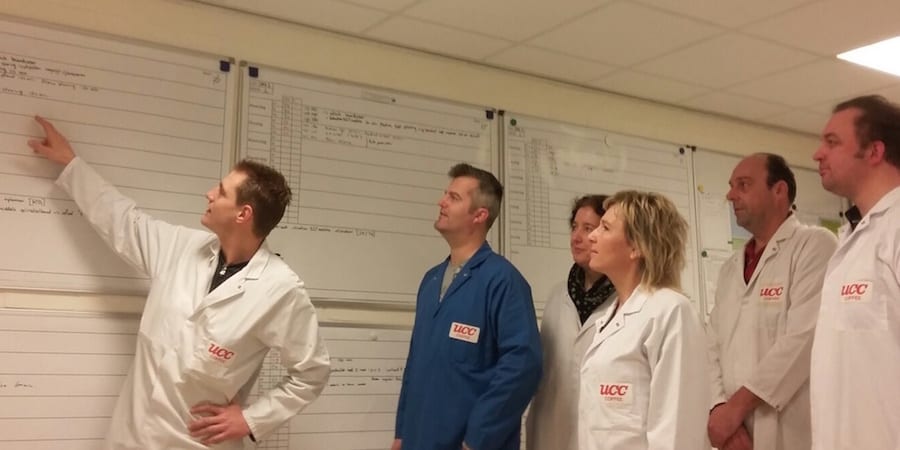
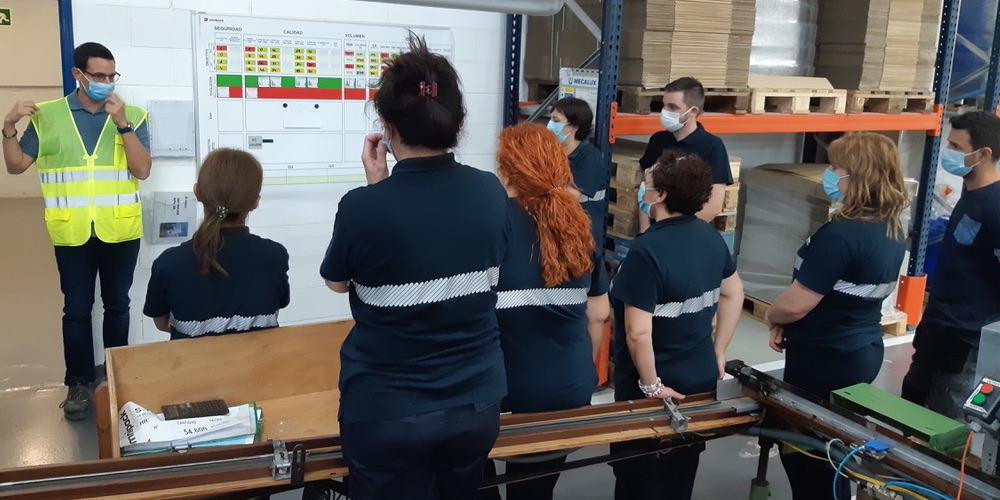
FEATURE – Repetitive flexible supply is a very effective method to level production scheduling, but as a FMCG company in the Netherlands found out, sometimes a number of conditions must be met before the approach becomes viable.
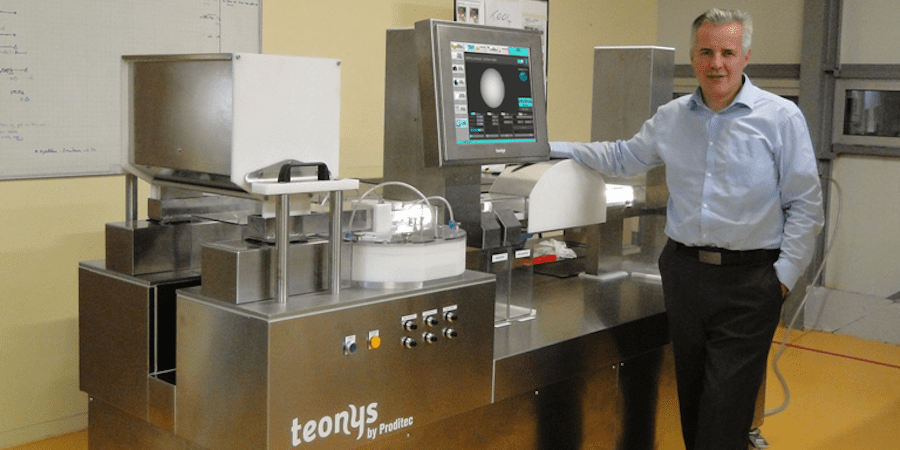
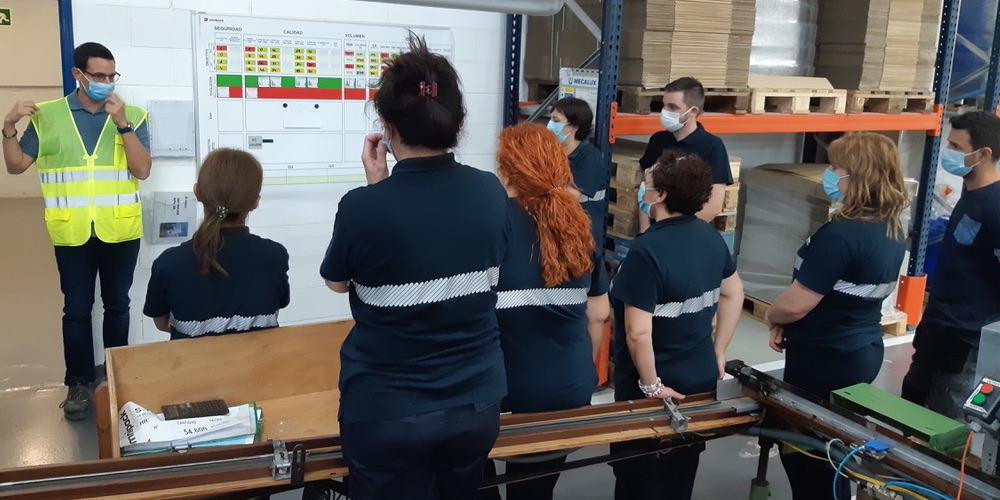
PROFILE – Before anything else, a good lean leader must be open to changing and continuously running experiments – something Christophe Riboulet, CEO of a small French manufacturer, knows quite a bit about.
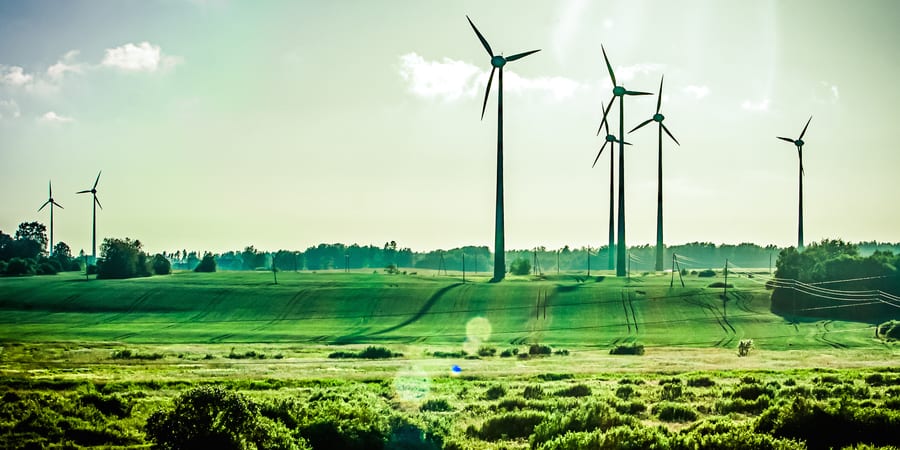
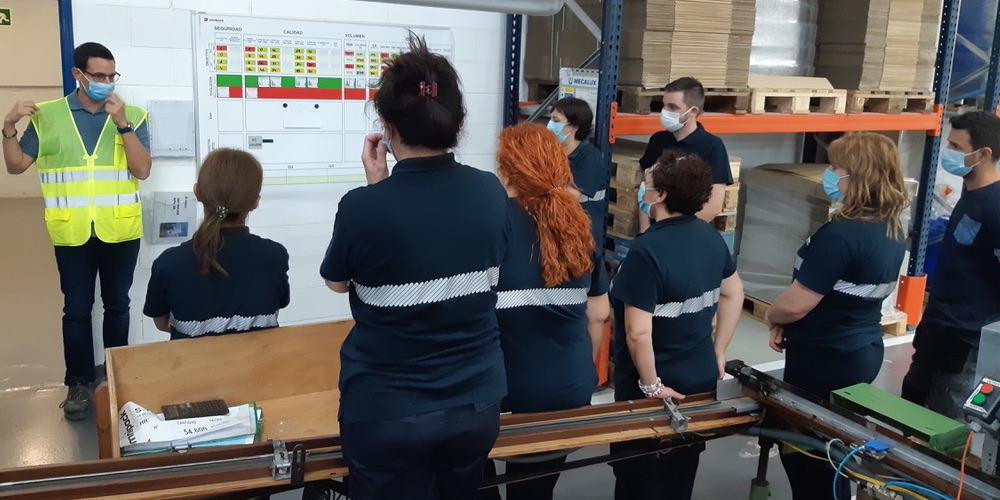
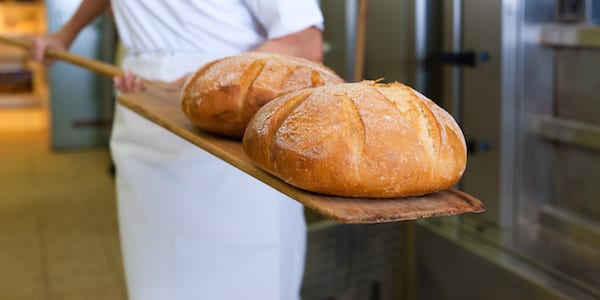
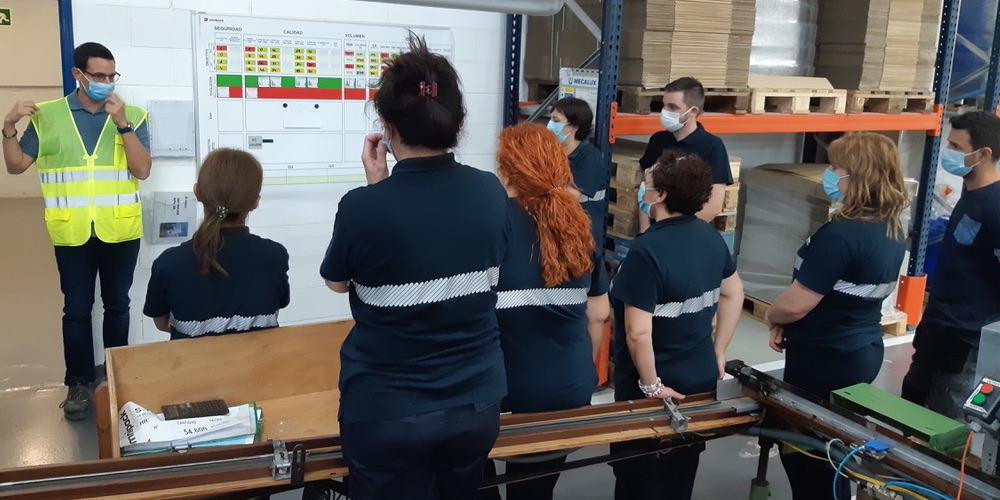
CASE STUDY – A very lean system that runs like clockwork and constant attention to customer service enable Barcelona-based 365.café to achieve the impossible: supplying 55 bakeries out of a 650-sqm factory.
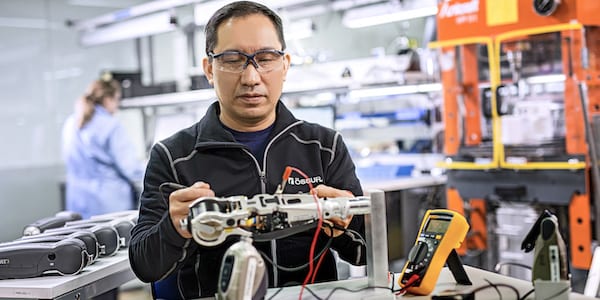
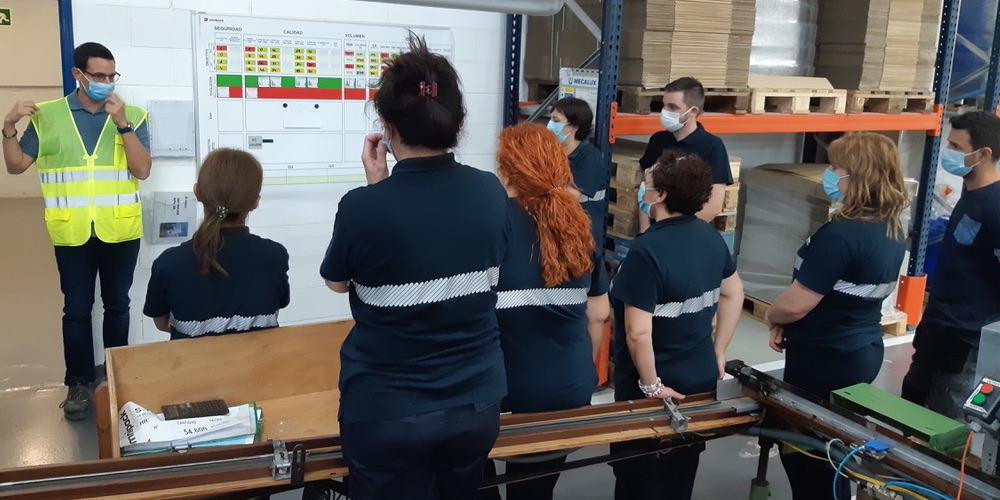
CASE STUDY - Össur is recognized as a leader in the fields of prosthetic, osteoarthritis and injury solutions, but how did lean management and a trial-and-error approach to improvement help it to stay competitive?
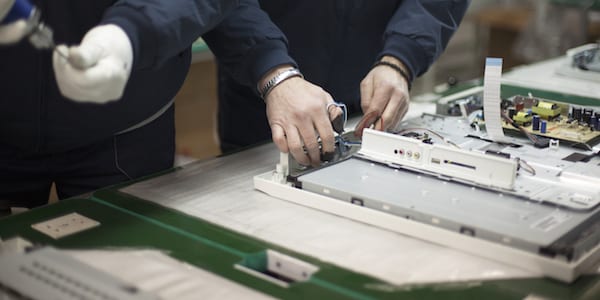
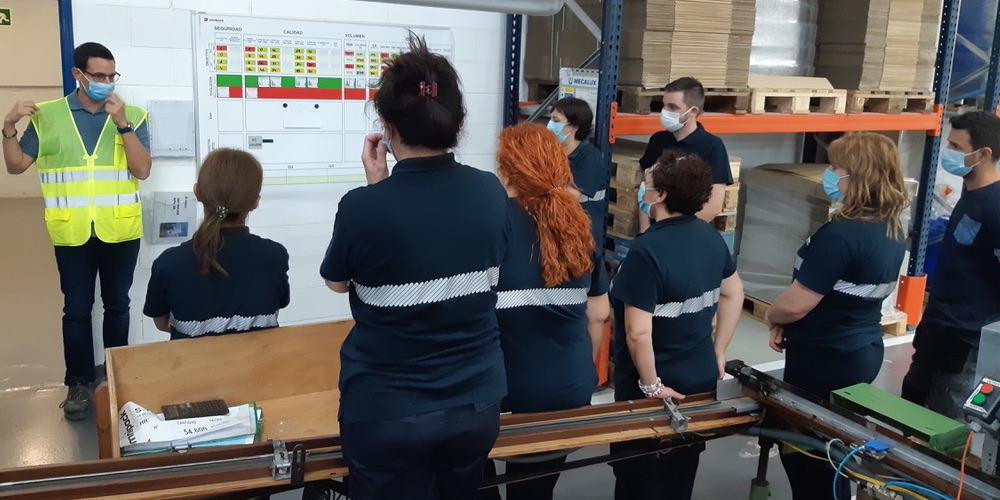
ARTICLE - We always talk about going to the gemba, but we often don't understand what that entails and what changes it can bring to our companies. In this article, we hear about the experience of Thales.
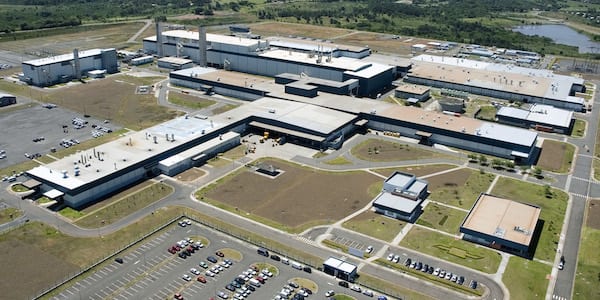
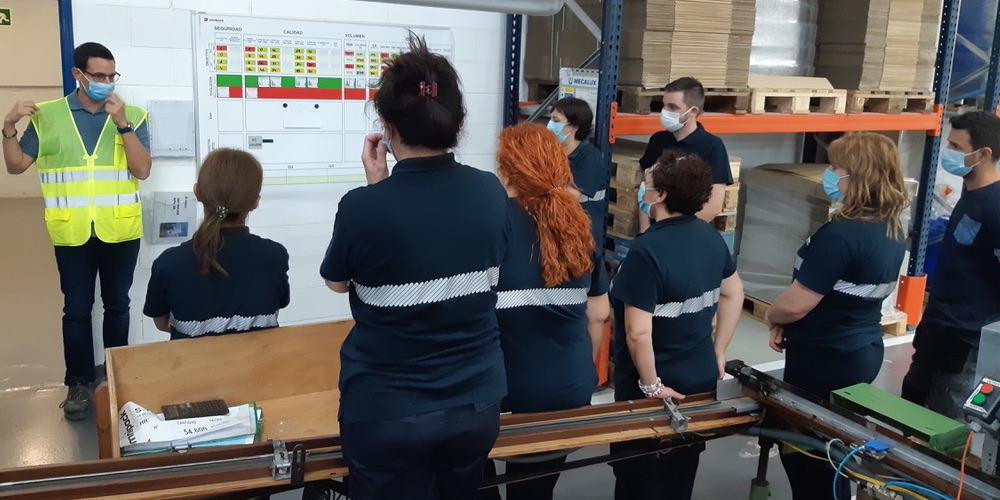
INTERVIEW – We speak with Sérgio Caracciolo of General Motors do Brasil about the carmaker’s approach to lean, its struggles, and its lessons learned.
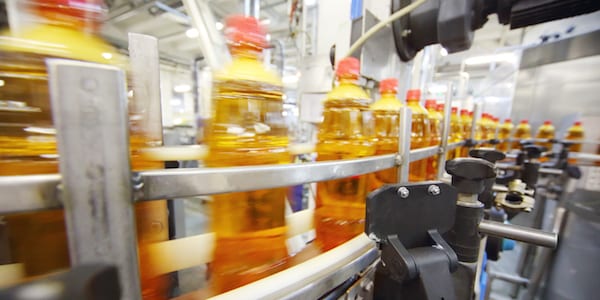
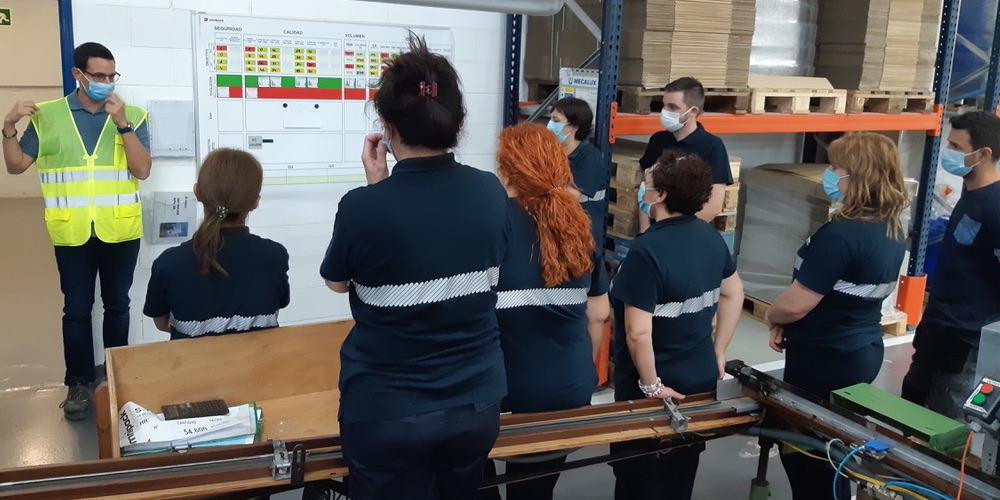
FEATURE – Effectively applying just-in-time and achieving flow is impossible without leveling production first. Yet, most companies seem to think this is impossible because demand is so variable… but is it really?
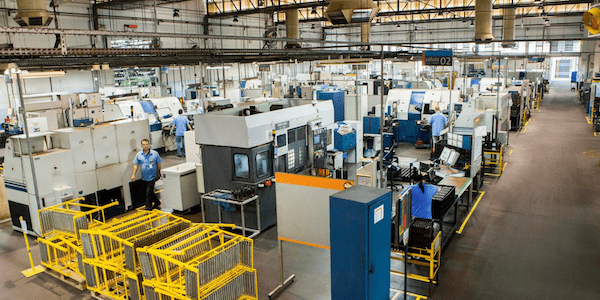
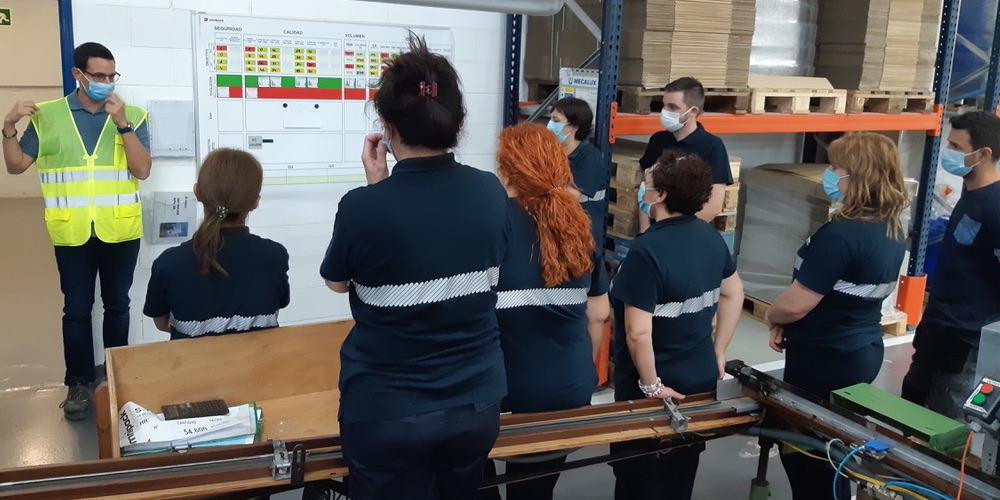
INTERVIEW - Lean manufacturing principles, successful training programs and the involvement of management in daily continuous improvement are transforming Brazilian automotive supplier ZEN.
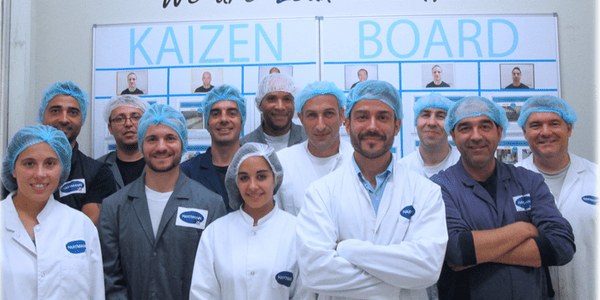
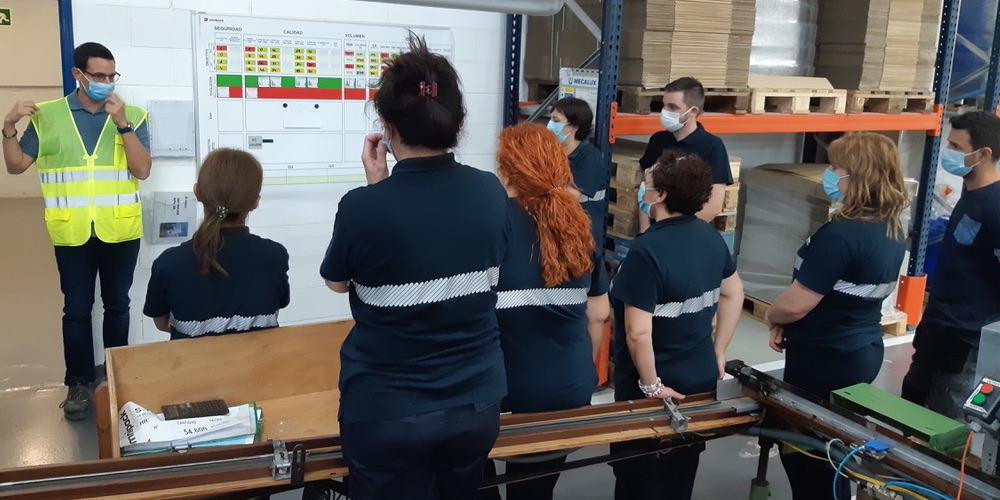
CASE STUDY - Through the involvement of front line staff, Hartmann’s production plant near Barcelona is paving the way for an expansion into different markets and inspiring the adoption of lean across the multinational.
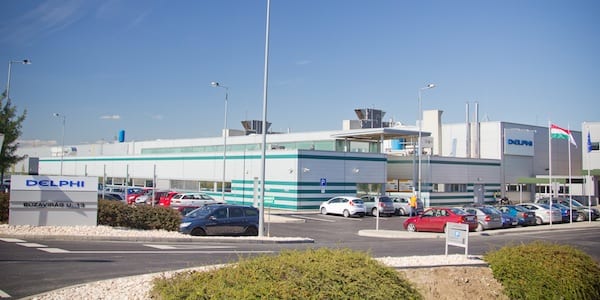
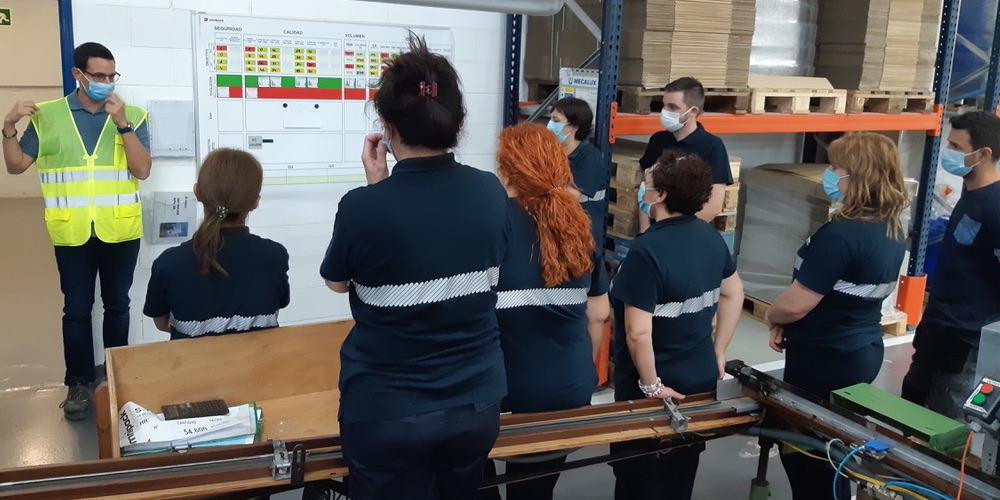
INTERVIEW - The General Manager of a Delphi plant in Hungary talks about the lean transformation the site went through and the challenges automotive suppliers face in this day and age.
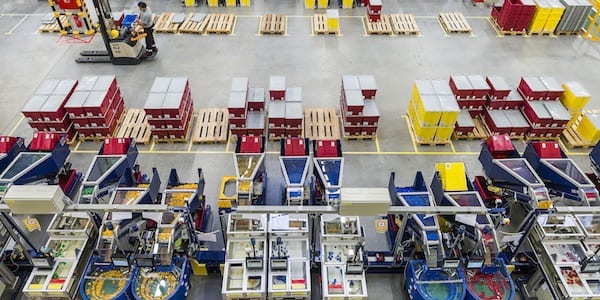
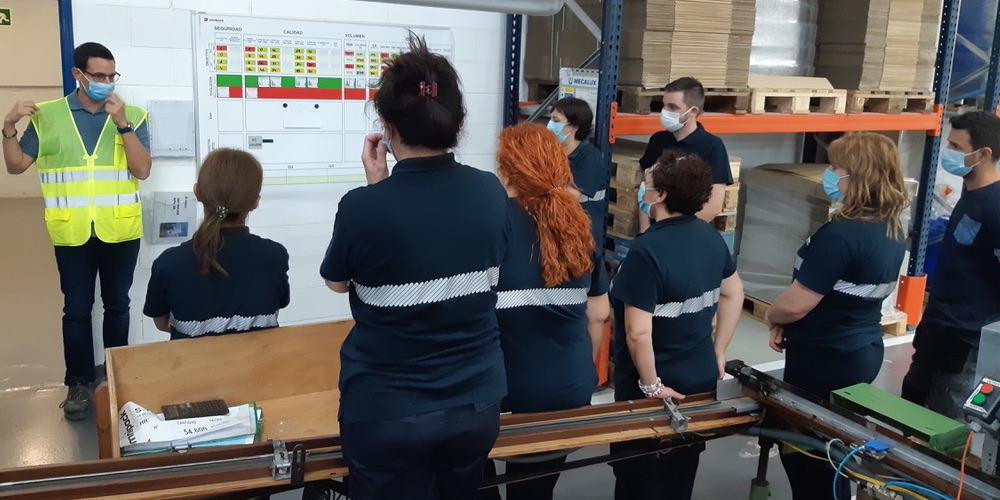
INTERVIEW – Planet Lean meets LEGO’s Ilona Takács to learn how the toy manufacturer looked at its corporate values to built a new, super-lean factory in eastern Hungary.
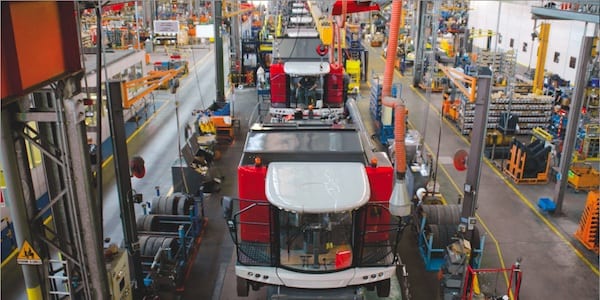
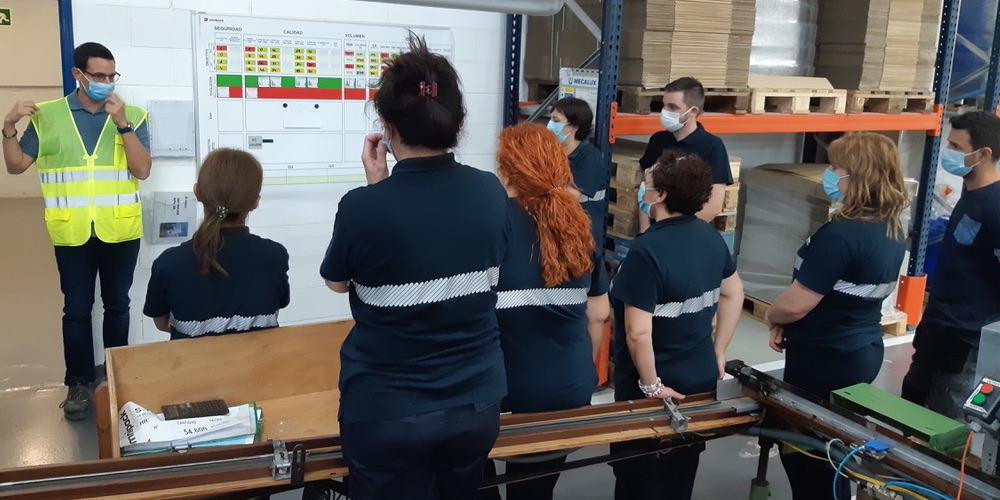
CASE STUDY - An approach based on Lean Daily Management System and experiments in a model area led an Italian manufacturer of combine-harvesters to become one of the leanest organizations in the Veneto region.
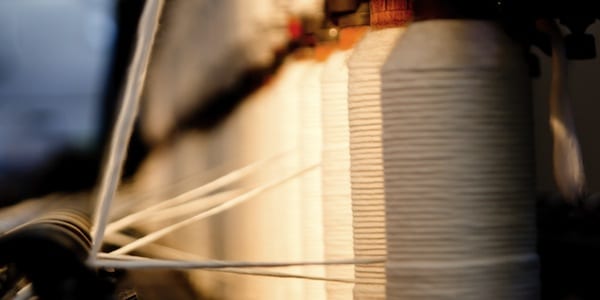
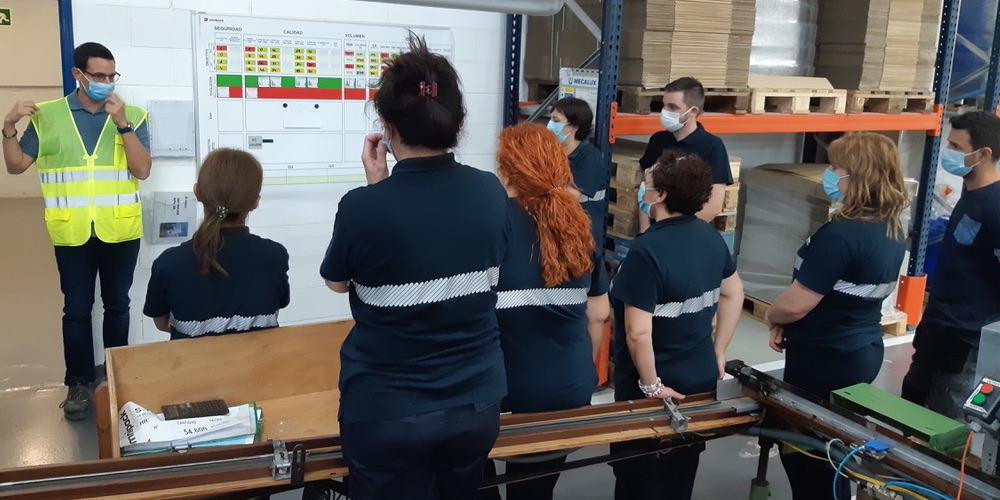
CASE STUDY - Faced with high costs, low demand and growing competition from China, Turkish textile manufacturer Yesim managed to develop a competitive advantage by transforming its ways with lean thinking and increasing its focus on the customer
Manufacturing is where the lean movement originated from. For their MIT research in the late 1980s (which resulted in the 1990 seminal book The Machine the Changed the World), Jim Womack and Dan Jones identified a set of principles and techniques that made Japanese carmakers far more productive than their Western competitors.
The superiority of the Toyota Production System is now a recognized fact (Toyota has been profitable every year but one, for half a century), which means that today most manufacturing organizations around the world practice lean manufacturing thinking to some extent. The prevalence of this alternative way of thinking and managing in the manufacturing sector often generates confusion in other industries, in which people’s first reaction to improvement attempts is the now proverbial “We don’t make cars. Lean is a manufacturing thing.”
When applied to manufacturing, lean tools like heijunka, SMED or Kanban cards allow for the optimization of production processes and the systematic elimination of waste (in its three incarnations of muda, muri and mura – respectively, non-value-adding work, overburden and unevenness). These happen by implementing the fundamental lean principles of pull and flow. However, it has now been proved that the principles characterizing lean manufacturing are universally applicable. They work in any sector and they apply to any kind of work – even though at times they require some adjustment.