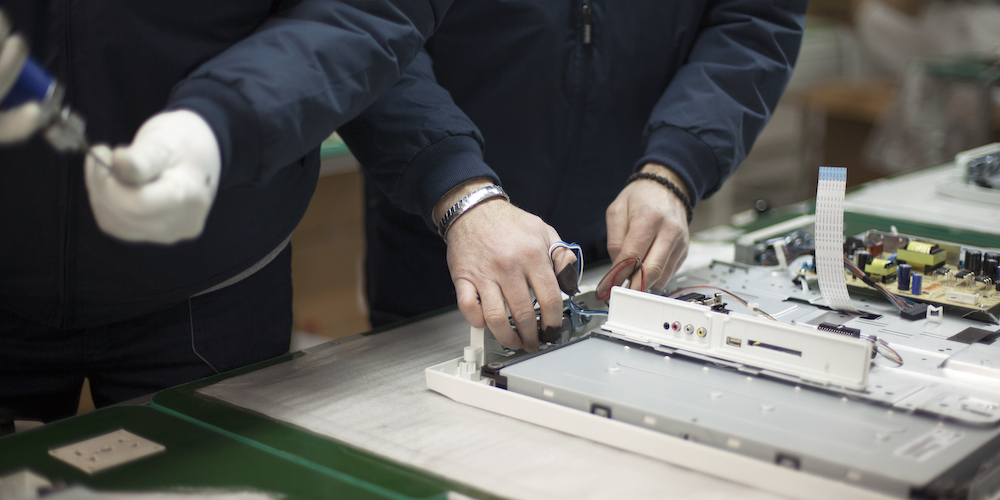
What is kaizen?
ROUNDUP – This month, we look at the most effective lean improvement approach – kaizen – by looking back at some of our best articles on the subject.
Words: Roberto Priolo, Managing Editor, Planet Lean
Lean thinking teaches us about the continuous, iterative nature of improvement: there is always a better way of doing things and it is our duty as lean practitioners to strive for an ever-better process by digging more and more waste out of it.
The improvement tool par excellence is kaizen. The Lean Lexicon defines it as “continuous improvement of an entire value stream or an individual process to create more value with less waste”. So popular has this concept become that it is not uncommon to meet people who have never heard of lean but are still aware of what kaizen is. The word – much like “Google” – is even used as a verb (as in, “We kaizened the process”).
For a few examples of kaizens, read this recent article by our colleagues from the Lean Management Instituut in the Netherlands.
KAIZEN DEFINITION
Semantics aside, what is kaizen all about?
According to Mike Rother and John Shook, there are two levels of kaizen:
- System or flow kaizen focusing on the overall value stream. This is kaizen for management.
- Process kaizen focusing on individual processes. This is kaizen for work teams and team leaders.
To learn what problems we are going to “attack” with our kaizen efforts, it’s typically very useful to start with an analysis of the value stream: there is no better tool for mapping the process and identifying pain points within it.
One of my favorite things about covering the lean world is hearing about the creativity of lean practitioners from across our community, which shows us over and over again how kaizen doesn’t have to be complicated or costly. In fact, some of the most effective improvements are those who cost no money – like our friends at Halfway Ngami in Botswana have proved. In this article, Sharon Visser tells us: “In our workshop you’ll see several clever “hacks” that cost us nearly nothing, but had a huge impact on the work. These kaizen ideas, most of which came from our people, included a soap-and-wash station built with simple parts bought at a hardware store, old gutters used to drain oil filters, and a device made with plumbing supplies that has considerably shortened the time required to grease wheel bearings.”
Another great example of creativity applied to improvement is karakuri kaizen, which consists in developing equipment that needs no power to function and is commonly used at Toyota as a method to encourage people to find better solutions to problems on the line. This fantastic article by Catherine Chabiron tells you all you need to know about karakuri.
ANOTHER ONE FOR LEADERSHIP
As most lean tools, kaizen can be applied in any environment. Theodo, a software company our readers will be familiar with, has made it its go-to method for successful scale-up. In this piece, CTO Fabrice Bernhard says: “Kaizen is now the approach we use on all scaling projects, to maintain velocity and quality past the MVP phase. We observed that the teams who engage in good kaizen have had impressive results, finding new smart ideas to tackle bugs, improve performance and boost security.”
Fabrice and CEO Benoît Charles-Lavauzelle were inspired to bring kaizen to Theodo after seeing it in action in a factory in Japan. Their first experience with it entailed using it to reduce the page-loading time.
In this great article, Benoît explains how kaizen really starts with leadership’s involvement and ability to understand what problems need solving in order to give the organization a competitive advantage. He writes: “We learned that real kaizen first requires leadership to understand what typical problems – those “hard-to-do” things – will make a competitive difference and then communicate this to the teams, in order to involve their talent and passion in finding creative ways of doing things better. Kaizen can’t be programmatic.”
In this sense, understanding of customer problems and kaizen go hand in hand. And it makes sense: as lean thinkers, our first concern should always be making our process better for our customers.
Tokheim, an Italian firm servicing gas stations, is also on a lean journey. Their management team seems to agree with Theodo’s that kaizen traces a clear path to innovation. Here, they write: “Lean gives us a system to continuously develop everyone, and we try to promote the people that come up with the most unexpected and efficient ways to solve concrete problems. In this sense, we now see lean, with all its technical tools, as essentially a talent management system. Talent spotting occurs during problem solving and kaizen.” […] “We now see innovation as solving problems for our customers and ourselves by identifying key wastes and asking people to think creatively about how to eliminate them.” And how do we eliminate problems again? Through kaizen!
For a word of caution on the “gemba cardinal sins” that hinder your ability to kaizen, check out this article by Michael Ballé. It’s invaluable advice.
THE KAIZEN PROCESS
Over time, kaizen has been “packaged” and described in different ways. There are kaizen events, kaizen blitz, and kaizen weeks… and probably a few more I am forgetting to mention. These definitions tend to focus on the length of the improvement activity (some would deem this unnecessary, given that the nature of improvement is continuous in lean thinking). In my mind, the duration of a kaizen “event” is entirely situational and it’s much more useful to talk about kaizen as a culture. It’s critical we focus on the thinking and behaviors necessary to create an environment in which people are comfortable raising problems, encouraged to analyze them in depth, and free to suggest countermeasures. This is the true enabler of kaizen.
THE AUTHOR
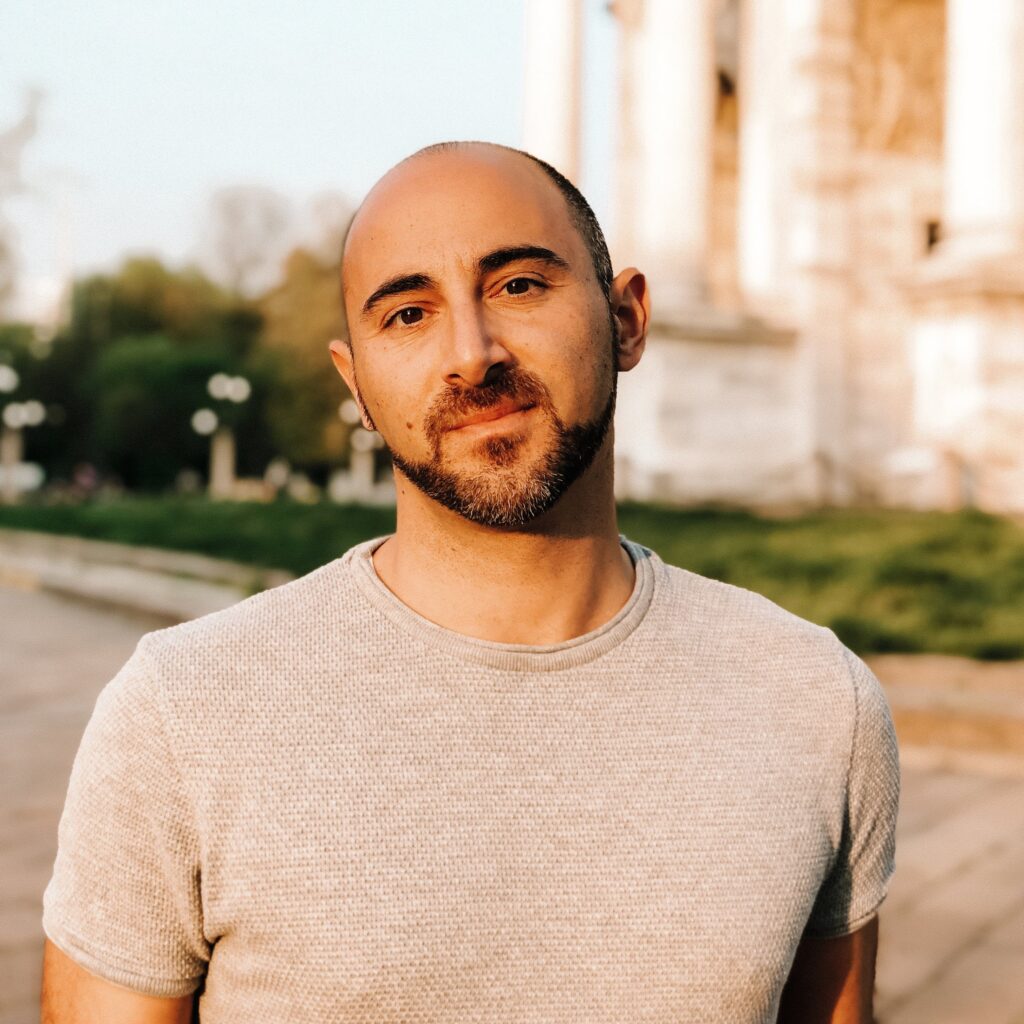
Read more
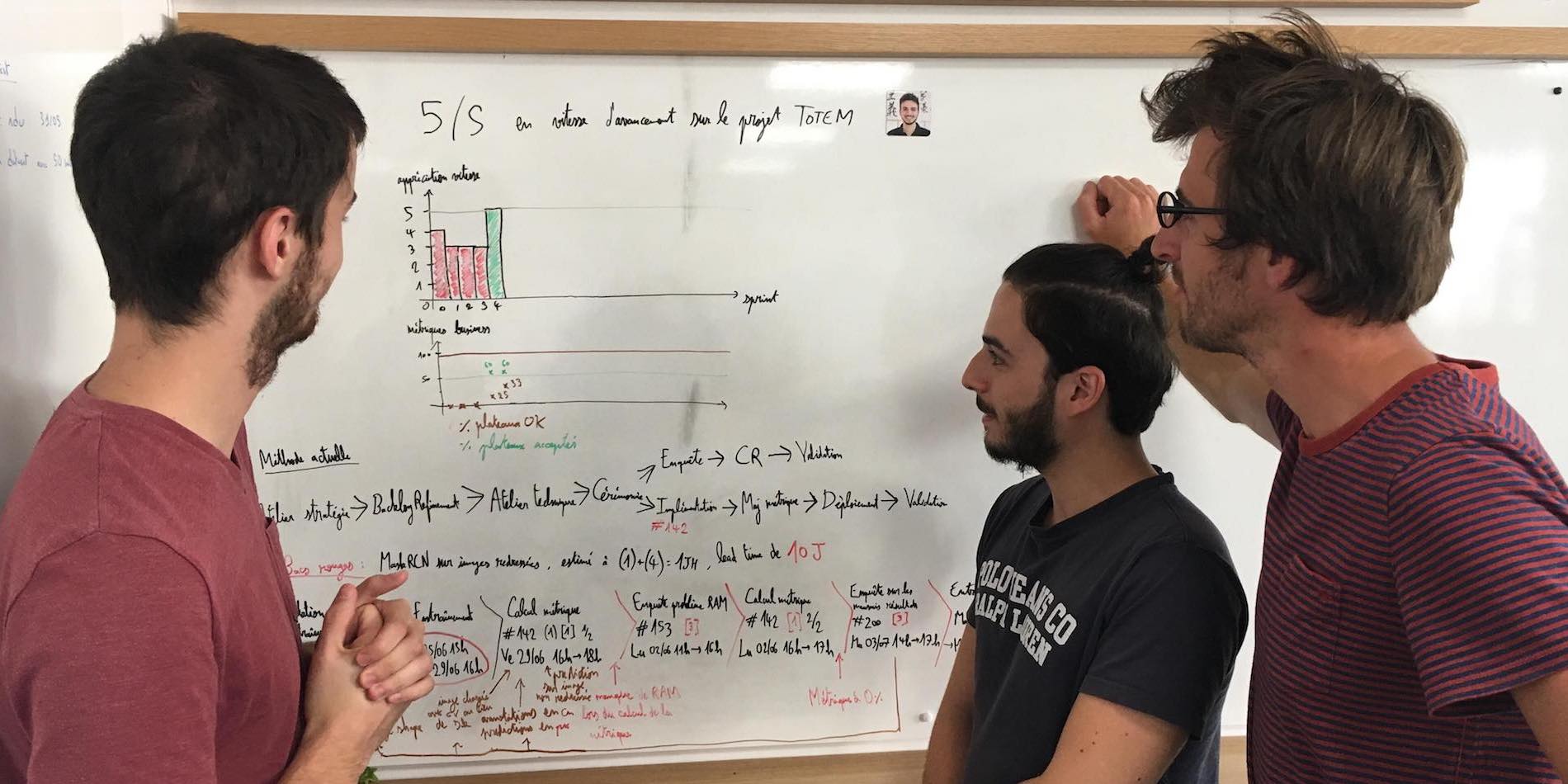
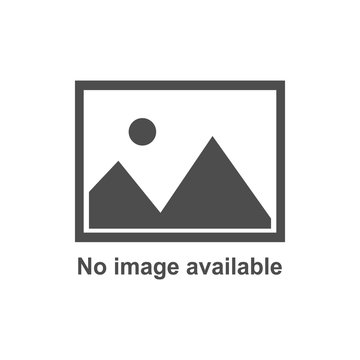
BUILDING BRIDGES - This month, we hear how addressing work-in-progress led a startup specialized in AI to productivity gains on their machine learning projects.
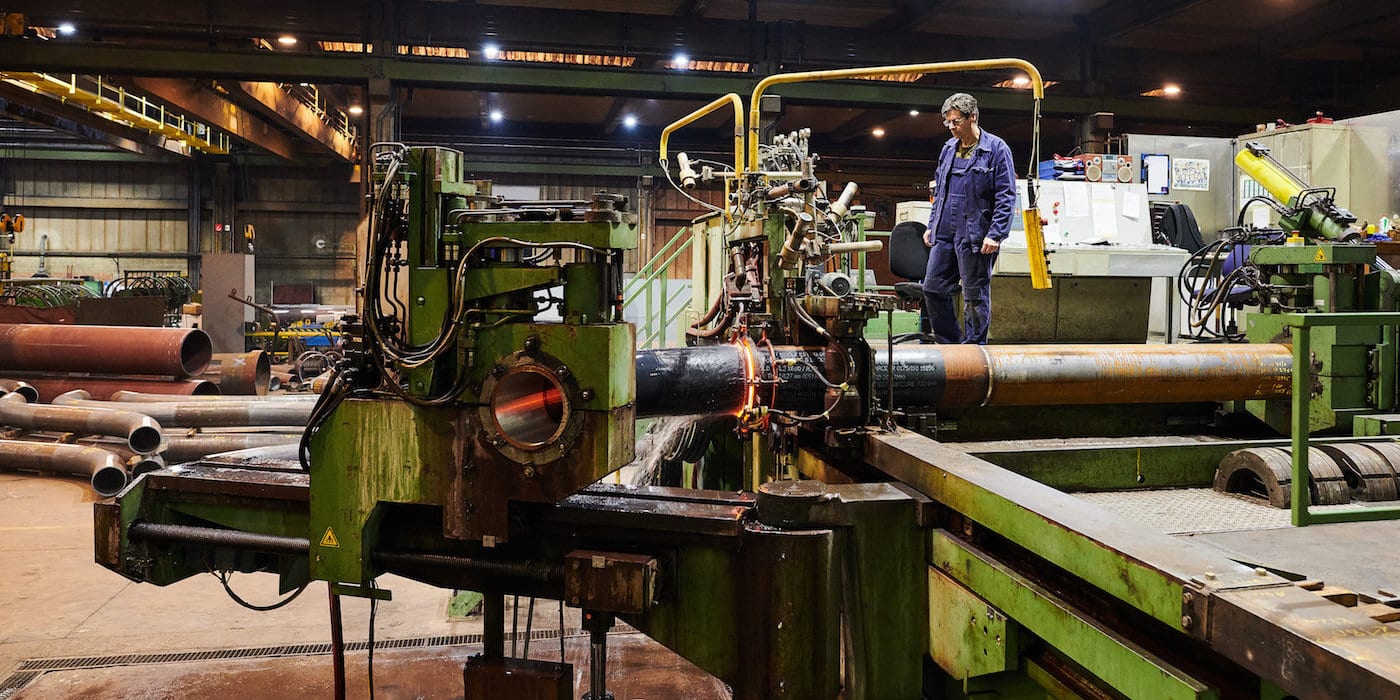
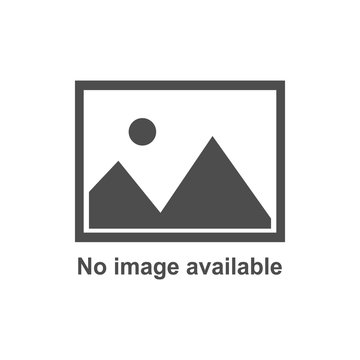
FEATURE – This Dutch company decided to start its lean journey by involving its suppliers in the improvement work. We hear from both customer and supplier.
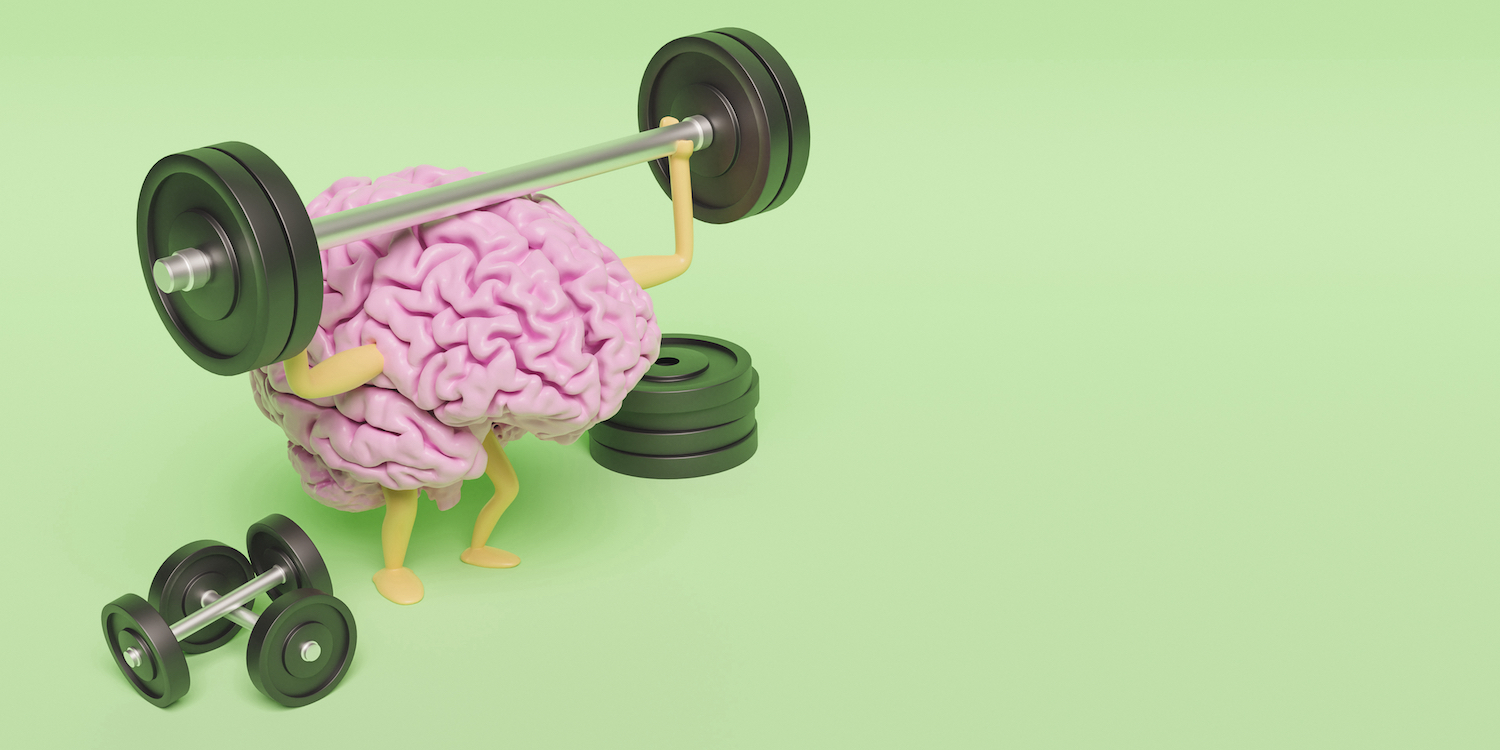
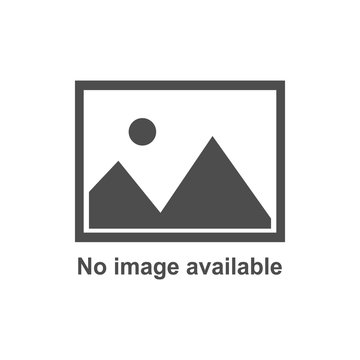
FEATURE – In this interesting piece, the author explains how lean provided everyone, everywhere with a framework to work their intuition muscle and develop insights.

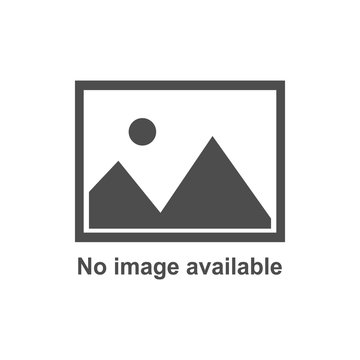
FEATURE – A school board in Holland is discovering the potential of lean thinking and improving its processes to tackle the overburdening of teachers.