Lean Thinking is about creating the most value for the customer at the minimum cost, which is achieved by minimizing resources, time, energy and effort.
A lean approach to work is about:
- understanding what’s really going on at the place where value is created – commonly known as the gemba.
- improving the processes by which products and services are created and delivered.
- developing and empowering people through problem solving and coaching.
- developing leaders and an effective management system.
Lean thinking and practice help organizations become both innovative and competitive, which in turn allows them to become sustainable.
Lean principles may have their roots in Toyota's factories in Japan, but today lean thinking has come to represent an alternative, superior approach to doing work - no matter what the work is, the sector or the size of the organization. In a lean organization, problems are opportunities for meaningful learning rather than mistakes to be swept under the rug or quickly resolved. Managers act as coaches, helping others get comfortable identifying problems and practicing daily continuous improvement.
Leadership means creating a management system to support a new kind of engagement with the real work at hand, the way the work is being done now, not the way you and your teams hope to be doing work sometime in the future. Planet Lean (and the Lean Global Network) aims to inspire people and organizations around the world to embrace lean principles and practices.
Here's a few sample stories from our archives, which will show you the far and wide lean has gone... and how many opportunities lie ahead:
- Every Person Matters - a great story of leadership and transformation in a car dealership, all the way from Botswana
- How to Transform Your Hospital Using Lean - a fantastic example of how lean is making inroads in the healthcare sectors
- No Loafing Around - the extraordinary lean-fuelled growth of a chain of bakeries in Barcelona
- All Rise, Lean Is in Court - not even traditionally stiff government organizations are immune to the power of lean thinking
What lean is not
- Headcount reduction (“lean = mean”).
- A set of tools: 5S, Kaizen events, value stream maps, andon, visual management, metrics, dashboards, A3, etc.
- A program (efficiency, process improvement, performance management, MBO, cost reduction, 6Sigma, etc.) “done” to the people doing the work (and therefore creating value) by management, outsiders or internal expert staff.
- Something that only applies to manufacturing or operations.
- Training for certifications and belts.
- Regimentation through standard work
Lean principles
As part of their research, Dan Jones and Jim Womack identified five principles that are still guiding organizations in every sector that are trying to turn to lean thinking. These principles are:
- Define value, as perceived by the customer
- Map all the steps in the value stream, eliminating those that don't contribute to the creation of value.
- Ensure your products or services flow towards the customer in a smooth way, with no interruptions, by the value-creating steps occur in a tight sequence.
- Let the customer pull value from the next process upstream, allowing them to set the pace for your work.
- Strive for perfection, by trying to achieve a situation in which value is created with no waste.
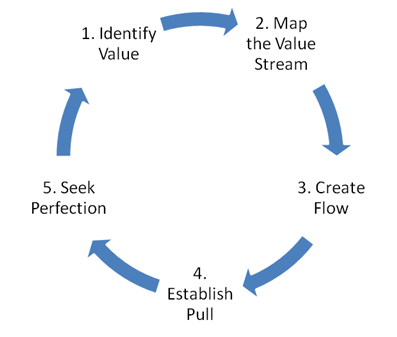
Here are a few articles that will help you to better understand some of these principles: an article from our Polish institute explaining why value creation is the foundation to a healthy organization; a video in which a manager in a Brazilian clinic explains the move from siloes to value streams; a case study on a vehicle preparation center in Johannesburg that has introduced flow; and a story from Turkey on a gas valve manufacturer that has turned itself around using flow and pull.
Lean manufacturing
As mentioned, lean thinking originated in manufacturing, the first sector to embrace it. Around 30 years ago, the founding fathers of our movement - Dan Jones and Jim Womack - were carrying out research for the Massachusetts Institute of Technology, which revealed that Japanese carmakers were outperforming their Western counterparts. Their research was communicated to the world in The Machine that Changed the World, the book that started it all. Dan and Jim's realization prompted them to look into what was allowing Japanese manufacturers, and in particular Toyota, to achieve such high levels of performance.
The tools and practices Toyota had developed quickly started to make their way to pioneering factories around the world. Manufacturing interiorized lean principles and applied them in earnest ("lean" is a word most manufacturing companies have heard of). Over the years, lean thinking has made its way to other industries - from healthcare to government, services to construction. Today, it is clear it can be applied to any human endeavor.
To read more about lean manufacturing, click here.
The Lean Global Network’s definition of Lean Thinking & Practice
Lean thinking and practice is about embracing the challenge of creating more value for each customer and prosperity for society by:
- Showing respect by developing people to continuously improve the work through problem solving.
- Focusing on, and continuously, improving the work.
- Minimizing/eliminating waste — time, human effort, injuries, inventory, capital, space, defects, rework, etc.
- Asking what type of management behavior and management system is needed to improve and transform the organization.
To Improve (or Transform), an Organization Must Address
- Purpose: What value for customers?
- Process: How to continuously improve?
- People: How to respect, engage and develop employees?
Aligning purpose, process and people is the central task of management.
What is a Lean Transformation?
- Enterprise transformation is the process of an organization shifting its business model to a desired future state.
- A lean transformation requires learning a new way of thinking and acting, characterized not by implementing a series of steps or solutions, but addressing key questions of purpose, process and people.
Here’s a video on the LGN’s Lean Transformation Model, narrated by John Shook.