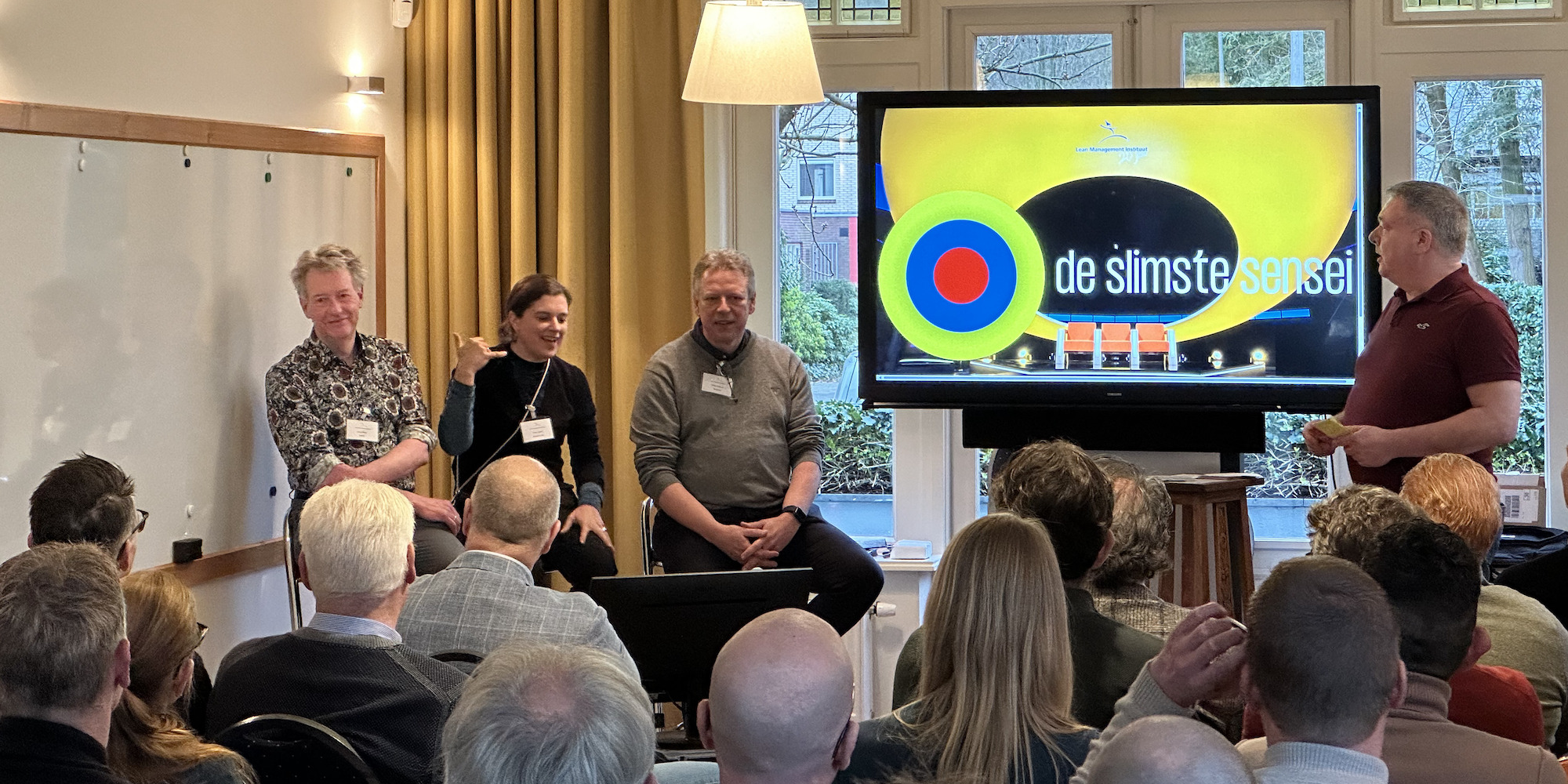
20 years of Lean in the Netherlands
FEATURE – In February, our affiliate in the Netherlands turned 20. The President of Lean Management Instituut reflects on this achievement and looks back at these two decades.
Words: René Aernoudts, President, Lean Management Instituut
In the summer of 2004, I was running Lean Management Instituut from my house. I had founded it just four months earlier and we were already getting ready to hold our first Lean Service Summit. I remember my fax machine churning out registrations in the middle of night, coming from people as far away as Australia. Around 220 people participated in that summit, which I organized with Dan Jones, and that was really the first time I realized there was really something to Lean Thinking.
It wasn’t the first time people in the Netherlands showed an interest in it – we had run sold out workshops and “lean days” before – but it was really in 2004 that things started to take off. I had been a lean consultant since 1997, developing relationships with Dan Jones and other key figures in the global Lean Movement. My work was purely missionary back then: we had to raise awareness about Lean Thinking, which is why we ran free events and translated books like Learning to See into Dutch. Consultants showed up at our events in droves, which also helped with the spread of Lean around the country.
In 2005-2006, I developed the first 5-day lean training, which later developed into the Lean Practitioner Program, together with Oriol Cuatrecasas in Barcelona and Roberto Ronzani in Italy. We sold out before the program was even finalized – further proof of the great interest that Lean was generating. From that moment on, things started to happen really quickly. Large consultancies were buying into Lean, taking it to the boards of large organizations, while we started to work in more and more sectors.
I had begun to work with healthcare and government organizations already in 2003, as Lean made its debut in non-manufacturing environments. Over the years, we worked with several hospitals and government agencies and municipalities – including the Municipality of Amsterdam.
That was incredibly important work, not only because it proved the viability of lean in non-manufacturing environments, but also because it inspired people around the world. In 2004, for example, a team from Flinders Medical Center in Australia came to our summit. The organization would then become a pioneer and model for lean healthcare in Australia.
It wasn’t until the early 2010s that Lean reached banks, insurance companies, energy companies, construction, and even universities (with institutions like Nyenrode Business University introducing lean modules into their curricula).
In 2008, we landed some major work with the Ministry of Infrastructure. Over the course of the following decade, we trained hundreds of their people and supported around 90 projects, coaching project leaders and getting some great results (we helped them to build highways with a 25% reduction in lead-time). Those things had a lasting impact on the country and saved millions of public money.
PRIDE IN THE WORK
These 20 years have just flown by! It seems like yesterday that I hired my first three people at Lean Management Instituut. Since then, we have grown and touched countless lives.
It is that “we” that I am most proud of. I am very grateful to the people who have worked with me over the years, helping me to build LMI. Together, we were able to create a safe space for everyone (something very different from the traditional cut-throat consultancy environment), where you can be yourself and where qualities are recognized and developed. As lean thinkers, we need to practice what we preach, after all. Some of our people have been with us for a very long time, some for as long as 17 years! It’s been a joy to see them develop themselves and learn new skills, starting with one background and gradually evolving into completely different professionals. It’s the kind of personal development we strive to teach organizations!
Even those who are no longer working for LMI and have taken their skills elsewhere are contributing to the spread of Lean around the country and the world, which lies at the heart of our mission at the Lean Global Network. Being part of this group of people, who constantly support each other and learn together, is something else I am very proud of. I have now been on the Executive Committee of the LGN for almost 15 years. During this time, it’s been wonderful to see the network take initiatives like Planet Lean or the Lean Global Connection. Our collective efforts have created great impact and changed many lives for the better.
LOOKING AHEAD
For much that we have achieved, I still get people occasionally asking me whether Lean is still relevant, and my answer is always the same: “It is, because there are still problems to solve.” That tells me there is still a lot to do to spread Lean Thinking and Practice around the world.
Our world is changing quickly, and I believe it’s critical we become more vocal in explaining the contribution that Lean Thinking can give to making the world a better place, whether it is by leveraging technology to improve the work or by helping to tackle existential threats like climate change. We need to do more on that front and continue to solve problems.
More than anything, I want to make sure that, as an institute, we motivate enough young people to work in the lean world. My son Lars is writing his thesis about Lean Thinking, and it is very heartening to see the new generation understanding and embracing these principles and practices.
Philip Uythoven, Borgesius – CLIENT
"I have become “business friends” with LMI. We help each other out all the time! Over the course of my career, I have worked with lean in three different companies and always got great results from it. The relationship with LMI has been a constant throughout that time. If I am in need, I know I can just pick up the phone and that René and his team will be there for me. It’s great to be part of this community."
Carin Hendriksen-Otten, Ubbink – CLIENT
"One of the first questions René ever asked me stuck me throughout the years – “What is the problem you are trying to solve?” I answered that top management didn’t fully understand what we were trying to do, and he asked me the same question again. What problem were we trying to solve as a business? As simple as it sounds, this question is very profound. I have taken it with me ever since, no matter what company I was with or what project I was embarking on. You often start by jumping straight into solving problems, but that question puts it all in perspective."
Dian Uphof, Ministerie BZK – FORMER EMPLOYEE AND CLIENT
"I used to work at the Ministry of Infrastructure, and through that I came to work at LMI. Here, I learned that my focus shouldn’t be to “implement lean” for the sake of implementing it, but to solve the problems of the organization. In other words, I learned the importance of truly understanding the problem at hand. René also taught me that if you want to explain Lean to people, you have to begin at the lowest level possible. I always remembered that. Today, when someone new joins the company, the first thing they do is an introduction to Lean. We make it as simple as possible, with the goal of helping people see waste around them. It is gratifying when they come to you and tell you they are noticing problems around them."
Tom Assink – FORMER EMPLOYEE
"LMI is the best employer I have ever had. There, I always felt like people had trust in me and gave me the freedom to explore who I am. It is a very safe environment."
Gertjan van Potten, Koninklijke Vezet BV - CLIENT
"The collaboration between Vezet and LMI is like a shared journey, where the knowledge and expertise of LMI comes together with our company’s desire and curiosity to create maximum customer satisfaction."
Quirina van den Berg van Saparoea, DZB Leiden – CLIENT
"In 2017, I started my Lean Black Belt training at LMI. At first, I felt dizzy for all the information, but they managed to explain the theory well and also helped me to apply it practically. As a result, I am able to work with it in my daily work. Gradually, I was able to count on continued support from LMI, which gave me increased confidence. Because of this solid foundation, I have been given the opportunity to hold a challenging position at DZB Leiden where we apply Lean with a primary focus on people and on fulfilling our mission. I am happy with the support, the focus on practically applying Lean and the confidence LMI has given me. I'm sure we'll be doing great things in the future."
THE AUTHOR
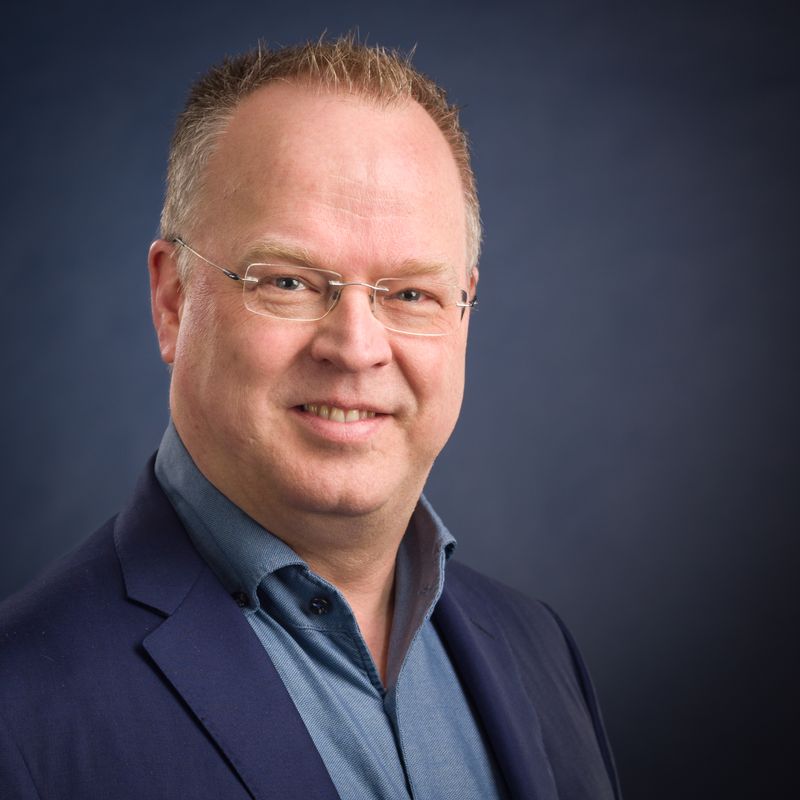
Read more
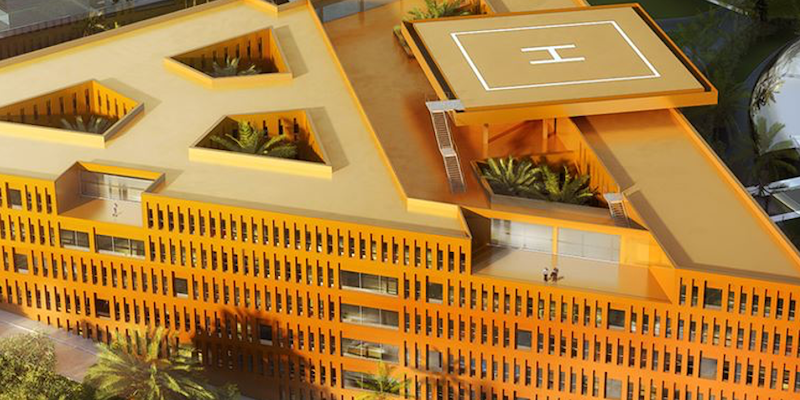
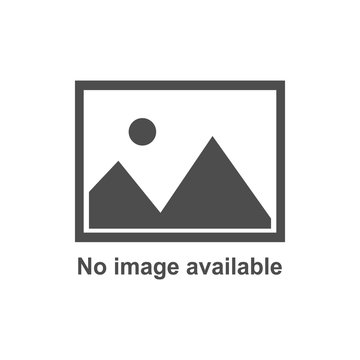
NOTES FROM THE (VIRTUAL) GEMBA – In the last of her series of virtual gemba walks, the author learns how a hospital in the Caribbean island of Martinique relied on Lean Thinking in its fight against the Coronavirus.
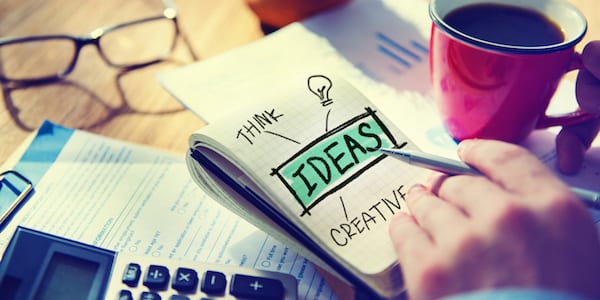
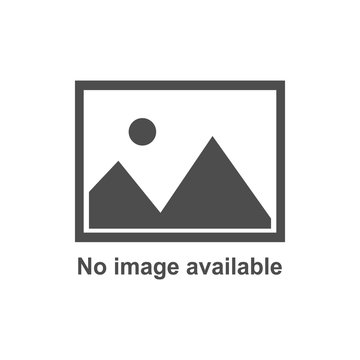
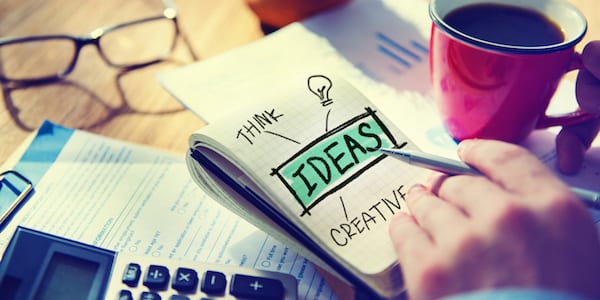
VIDEO – Meetings are critical to create a culture based on teamwork and to establish a learning organization, but their traditional format tends to encourage individual agendas. Not Lean Coffee…
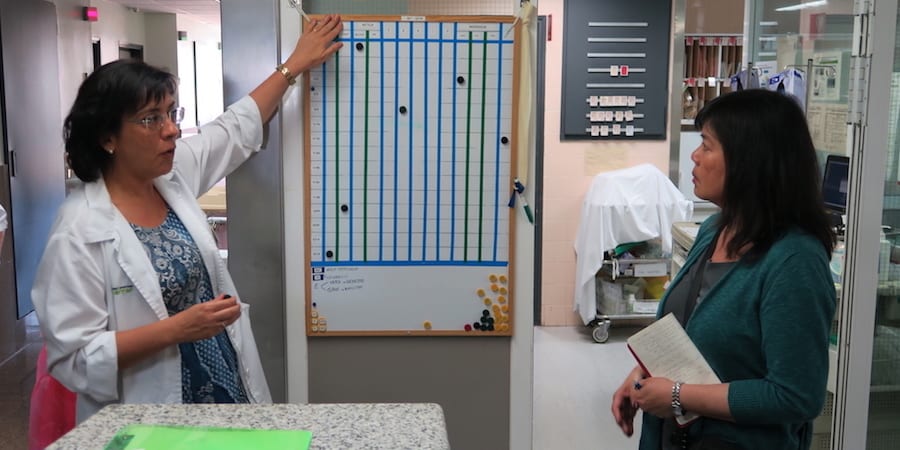
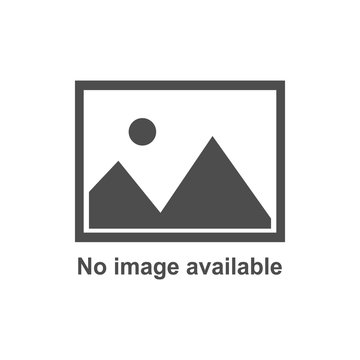
PROFILE – Lean is spreading like wildfire across the Catalonian healthcare sector, following a do-it-yourself model unique to this part of the world. Our editor met one of the practitioners who are making it happen.
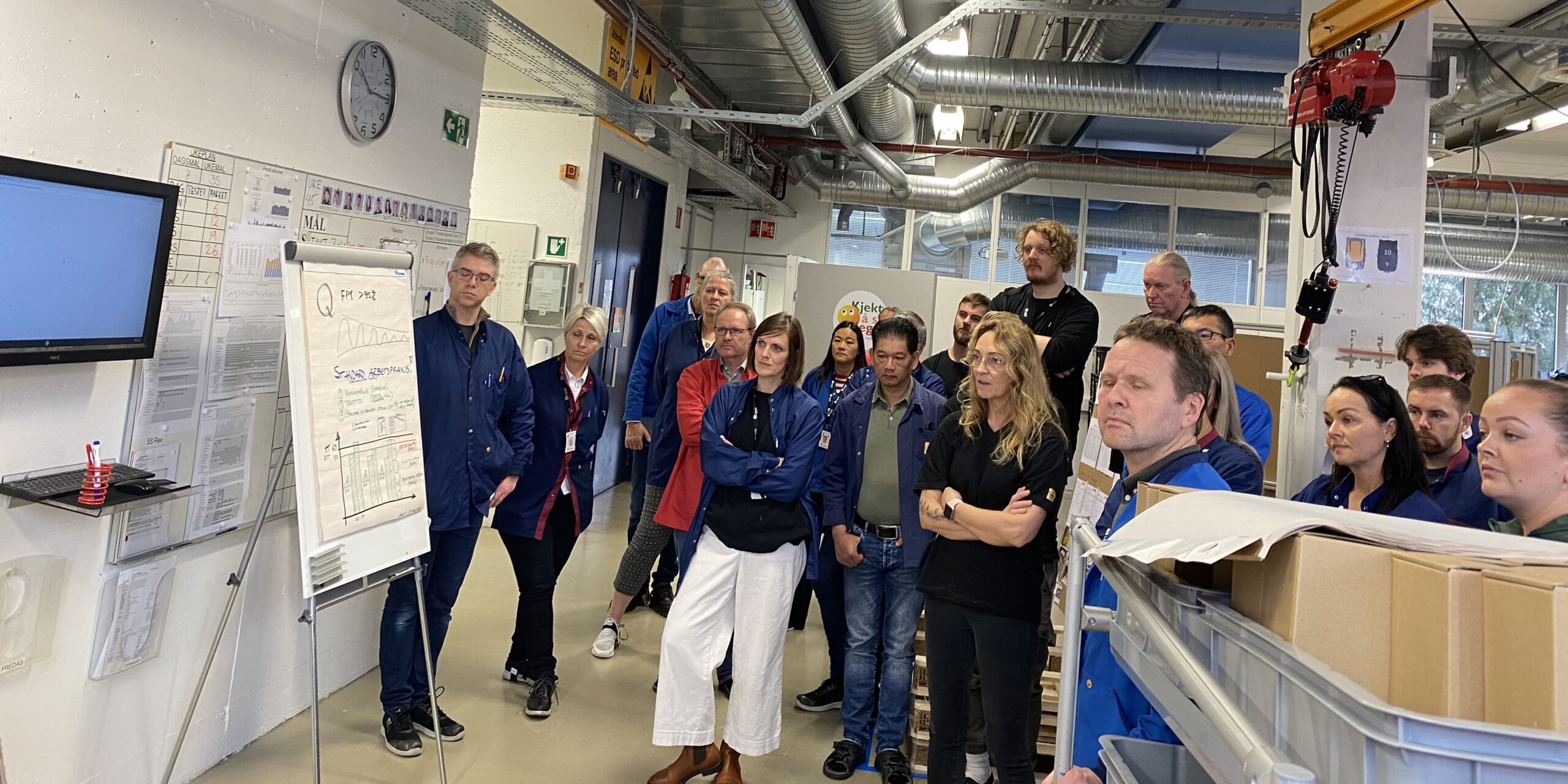
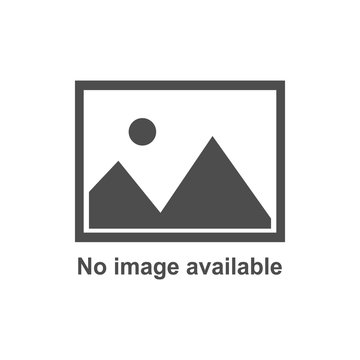
FEATURE – How Lærdal Medical was able to enthusiastically restart its lean journey with help of a good old-fashioned Kaizen Week.
Read more
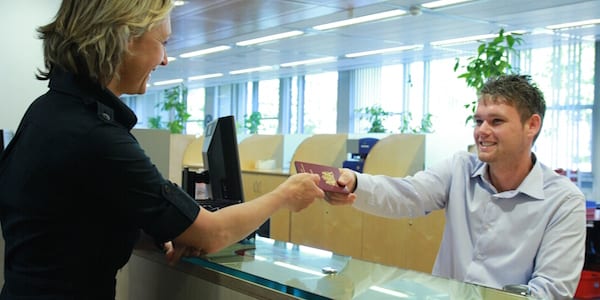
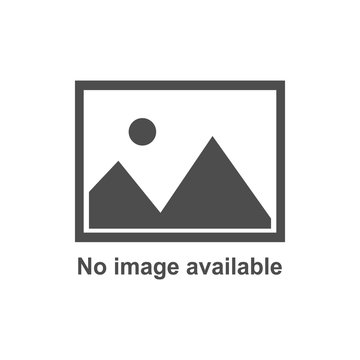
INTERVIEW - The historical city of Amersfoort in the Netherlands has introduced lean thinking and practice in local government to provide better and faster services to its citizens.
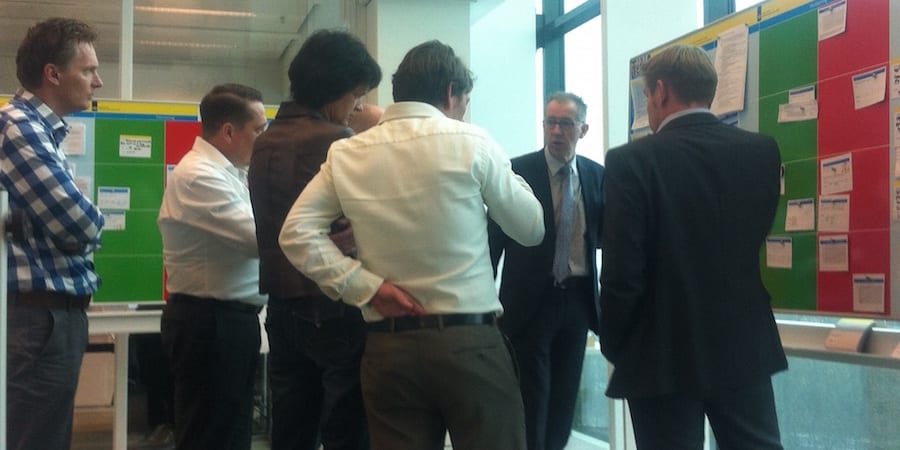
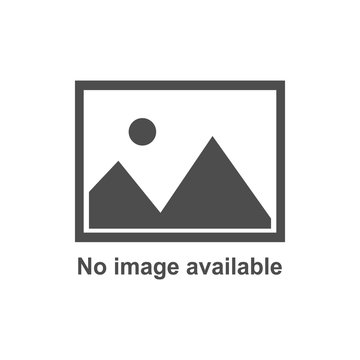
FEATURE – The theory of hoshin kanri is clear, but how can you adapt it to a government organization structured in departments where making A3s is not a daily practice? A Dutch ministry shares its experience.
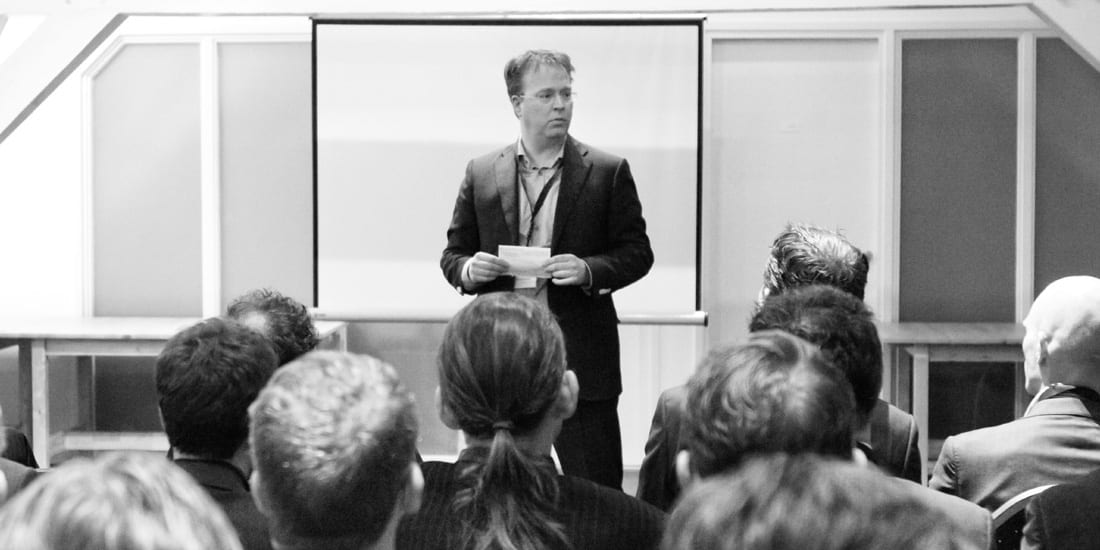
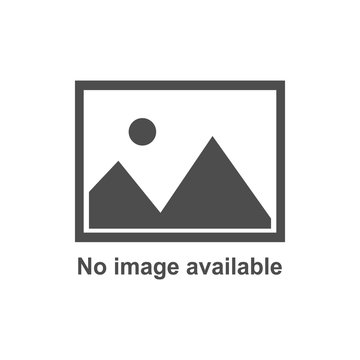
GETTING TO KNOW US – We continue our series of interviews with key Lean Global Network people with a chat with the President of Holland-based Lean Management Instituut.