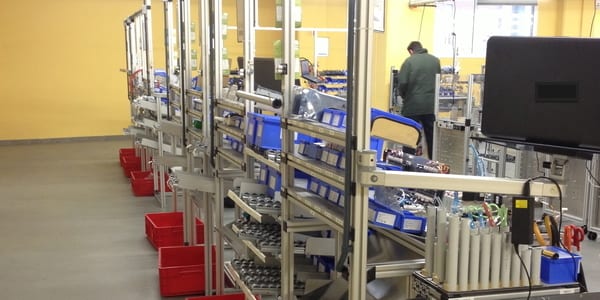
Rethinking an entire production system
FEATURE - It took a Spanish clinical diagnostics instruments manufacturer the introduction of a new product to realize how an old-fashioned system and management style were preventing the company from thriving.
Words: Eduard Antón, Director of Operations, Instruments, BioSystems
I started at BioSystems as an engineer many years ago. Even though I worked in R&D, I have always had a keen interest in manufacturing, which at the company had a number of problems. Machine malfunctions, unfinished products, and piles of stock were the rule.
But the business was doing well at that point in time: we were known for how innovative our products were and did not have many competitors. Our old-fashioned assembly line, therefore, did not seem like much of a problem. The great amount of work in progress - unfinished products sat on shelves on a regular basis - was not perceived as an issue back then.
In 2000, I took an MBA (Lluis Cuatrecasas, founder of Instituto Lean Management was one of my teachers there) during which I studied different manufacturing models, including lean manufacturing. I saw an opportunity to do things differently, but I was only an engineer with no power over the manufacturing department.
This started to change in 2002, when I was asked to start a manufacturing engineering department. We designed and planned for a number of standards and looked at a few processes, but our efforts did not go much further than that. My new department was working to provide technical support to manufacturing and to help us engineers not to be interrupted every second and asked to solve a problem.
The following year, the manufacturing engineering department absorbed the technical office. At the point we began to implement some of the new standard procedures, but still in a very traditional manufacturing environment.
Management eventually saw the potential of lean. In 2004, I joined the manufacturing department and I finally had control over the line, which is when I started to fully apply those standards to our production activities. In many ways, that is how BioSystems’ lean journey began.
At first, the new methodology was not welcomed (or understood). We did a few things nonetheless, but it wasn’t until 2007, when I was also put in charge of purchasing, that I “put all the pieces together” and could start doing things in a fundamentally different way.
Flow and supply were our main problems. With so much stock lying around and so many problems with suppliers, our lead-times had gotten very long. We took action to improve the purchasing process and therefore avoid material failures. I started to gradually eliminate shelving space as an incentive to improve and modernize the line.
That was around the time we started to work with the Instituto Lean Management (we were their first client). We saw lean as a great system, but we were very far from being able to implement it properly, because our focus was still on solving our most pressing issue: supply.
In other words, we did not have a proper burning platform.
And then 2009 came.
That’s the year we started to develop a new analyzer, bigger than any machine we had ever manufactured before. Until then, our most expensive machine cost around €5,000. The new piece of equipment was €12,000, and much bigger in size.
I used the machine example to explain the difference between the traditional way and the lean way to the company’s top management: I told them that if we wanted to assemble, for example, 40 new machines per month, we would have needed at least 120 in process. I asked them to multiply 120 by €12,000 so that they would get an idea of the incredible amount of money we were just sitting on. It was pure madness for a company our size, and stock was threatening our financial health.
At that point, many people were still giving me a hard time, telling me than lean could not work in a non-automotive environment and in a company as small as BioSystems (which employs a total of 200 people, of which 100 in manufacturing and R&D).
But I thought it could. The Instituto was instrumental in helping us – they were keen to bring lean to a small enterprise, and were up for the challenge. Eventually we got permission from top management to start an experiment.
We introduced a few initial changes and organized workshops for all employees. This time around, we didn’t even have to get a few quick “low-hanging-fruit” results to get the traction we needed: it became clear to everybody that it would not have been possible to finance the production of the new analyzer with the traditional system. Lean became a matter of survival, really.
Because we are a small company where everybody knows everybody and where politics is not prevalent, getting support from people was fairly easy, once clarity over the seriousness of the issue was made.
WHAT THE TRANSFORMATION MEANT
The moment we finished with the first workshop, our productivity had already increased by 50%.
Today we are able to manufacture nearly twice as many machines as before, in the same facility and with the same number of people. Having introduced one-piece flow and reduced WIP, we are now more efficient and our lead-times are much shorter. We have also become more competitive (after reducing our prices) and more successful in tenders.
These days we are more reactive to customers’ urgent queries (which is particularly useful when, as it often happens, we sell machines in bulk to hospitals). Our production system is more flexible than ever before, to match demand and help us to navigate market changes.
On the shop floor, we have established autonomous production cells. This is giving a great contribution towards respecting lead-times and increasing our ability to respond to day-to-day problems. Additionally, the cell configuration is giving everybody visibility over KPIs and performance, and is helping us to identify leaders within the business.
Before lean, it was a disaster. Everybody worked a lot of extra hours, often on Saturdays and Sundays. Since 2009, when our lean efforts began, there has not been a single hour of overtime, not even when we won big contracts.
Another problem was that we had a monthly schedule, which means that we didn’t know whether we were reaching a target or not until the last day of the month.
The manufacturing manager used to spend his time giving orders, moving stuff around the site, organizing the shelves. Now that we have balanced demand and production, all he does is problem solving. His focus used to be on organizing the process in-house and fighting fires, as opposed to taking instruments to market. Once flow was established, his responsibility moved to maintaining it alive.
PEOPLE AND LEAN
When we introduced lean, the first thought people had was that we were going to fire half of the workforce, even though reducing head count was the last thing on our minds. In fact, we had to hire a few extra people to allow for the production of the new analyzer.
With the traditional way, it would have been simply impossible to ramp up production. But that is not to say that it was just the way of producing the machines that changed. The cultural engagement of people proved critical, too.
In order to get there, we have been investing a lot of our time in providing training (the engineering department being the latest one to start learning about lean). And we haven’t even encountered much resistance on the way.
Everybody knows that if we are to survive, we have to learn how to compete with Asia. Everybody knows that we cannot afford to have a thousand people in production, and that we therefore need to do more with what we have. And today everybody is involved in the development of our new products and feels proud of the work they do.
We have a new training procedure, based on the ILUO matrix and train-the-trainer. We have also developed a hiring process with HR so that teaching the system to newcomers happens more smoothly.
A Knowledge Center was introduced. We have lots of expert workers, but with the new analyzer came many newly hired people. A lot of problems with quality and processes followed, which proved the importance of training and multiskilling to avoid mistakes.
Top management is on the same page: now that they understand the process better (they are doctors and chemists, not technical guys), they realize that it’s not about having a machine do all the work. We don’t compete with China on cost, but on quality… and quality comes from training on and perfecting the manual work, screw by screw, and component by component. We need to be as precise as possible in assembling, if we are to keep our name. Jidoka helped us here, as does better communication among departments: for example, by working more closely with R&D, when we design a part we know all the problems we might encounter in production down the line.
IMPROVEMENTS OVER 18 MONTHS
- Stock of completed machines: from 0-25 units to 1-4 units (84% improvement)
- Assembly lead-time: from 480 to 330 minutes (32% improvement)
- Rework: from 8% to nearly 0%
- Pre-processing activities: from 9% to 0%
- Spaghetti flow: from 48.8 meters to 31.2 meters (36% improvement)
- Machine waiting time: from 9,700 to 255.5 minutes (97.20% improvement)
- Production area: from 14.3 to 1.5 square meters (89.50% improvement)
WHAT’S NEXT
One of our struggles at the moment is managing the relationship between kanban and MRP, which is still a tool very much based on push. What we want is for people to start using it without being prompted, in the spirit of pull.
Another issue is the integration of kanban with our suppliers, which is still in its early stages. We want to involve the entire supply chain in order to be able to further reduce our stock and become even more flexible.
The creation of cells, among other things, required further development of our people. At the same time, our product portfolio is bigger than ever before and the number of processes we need to manage has increased, and it’s not as easy as it once was to move people around the factory. Again, people development will be key in this respect.
To facilitate the empowerment of people at BioSystems we will need the support of “numbers”. By showing figures – call it “marketing” if you like - we can show progress in a way that everyone can understand.
Read more

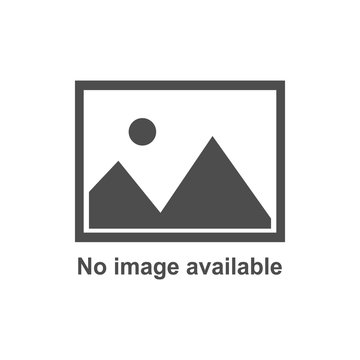
FEATURE – A school board in Holland is discovering the potential of lean thinking and improving its processes to tackle the overburdening of teachers.
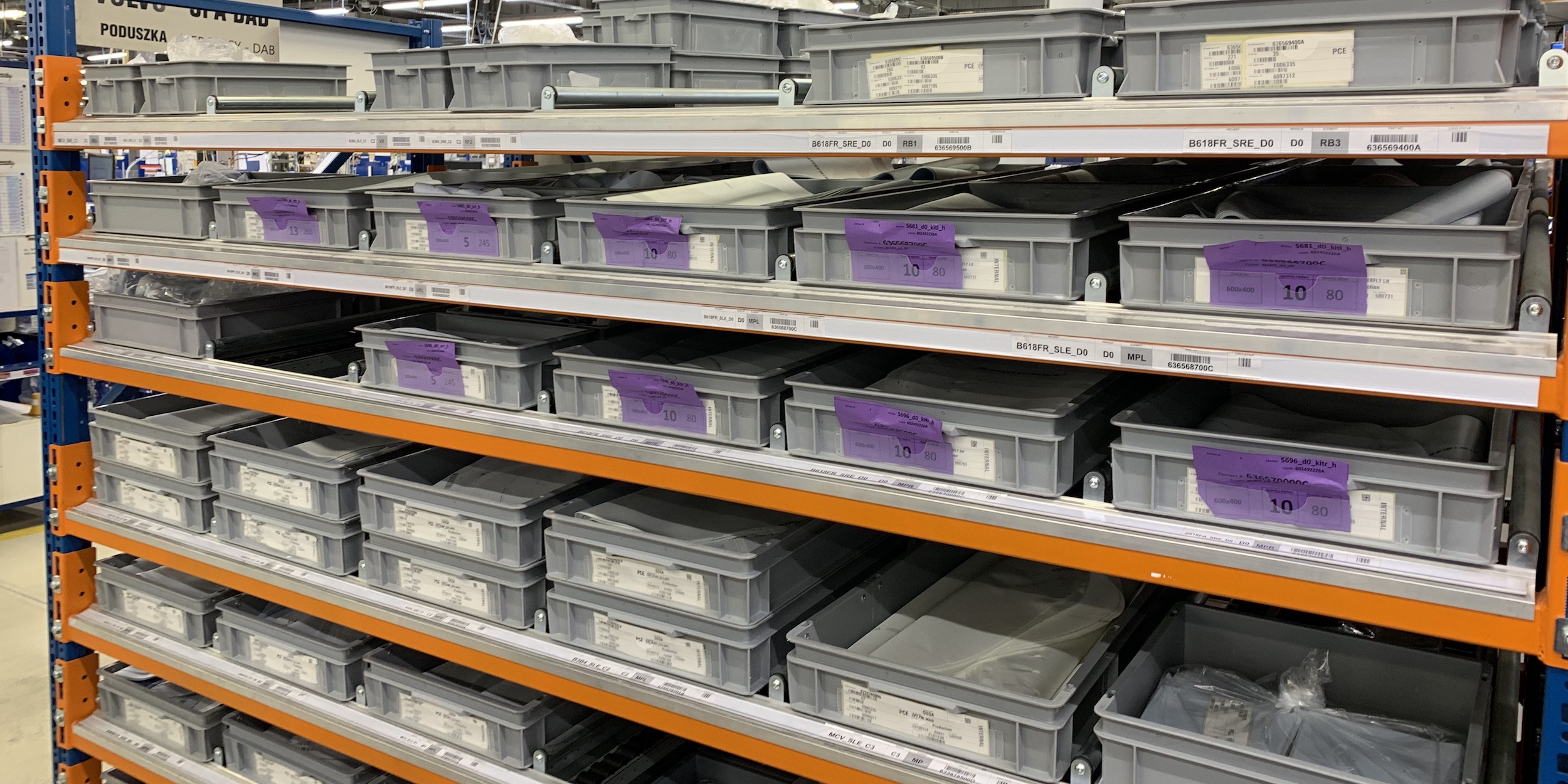
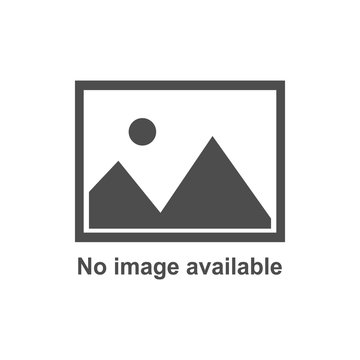
THE NAKED GEMBA – Our new series goes back to basics to unlock the secrets of the gemba and tell us about some of the main tools and techniques we can use in a lean transformation. First up, supermarkets.
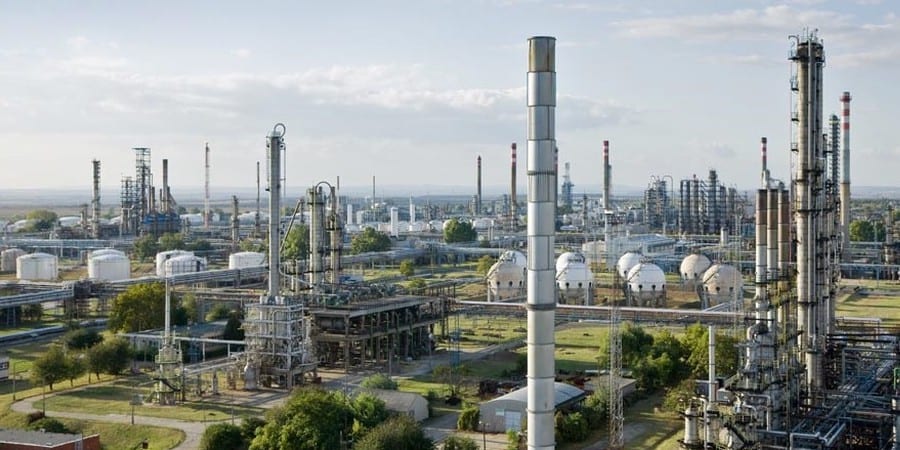
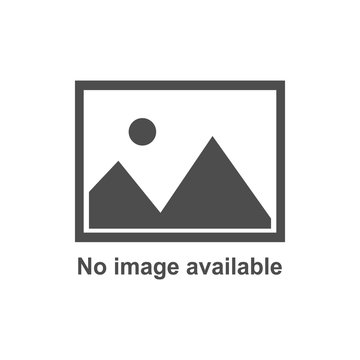
FEATURE – In this frank account, a senior executive discusses the challenges facing an oil and gas company as it tries to manage the complexity of its upstream and downstream supply chains.
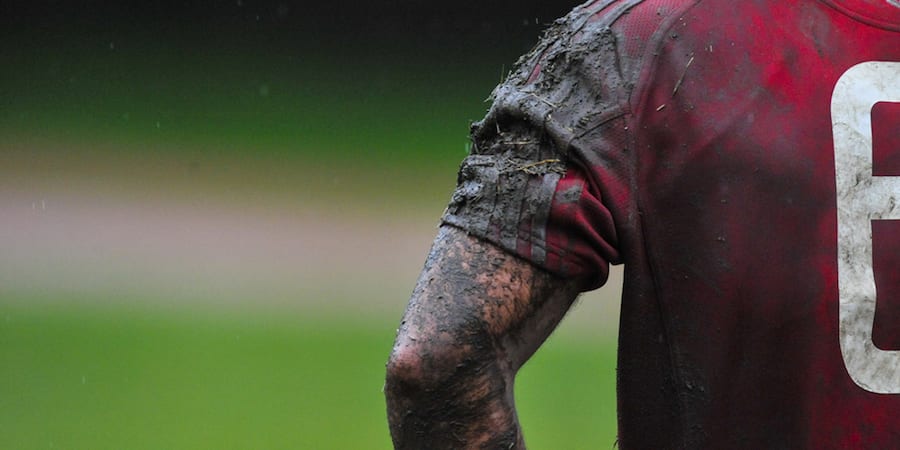
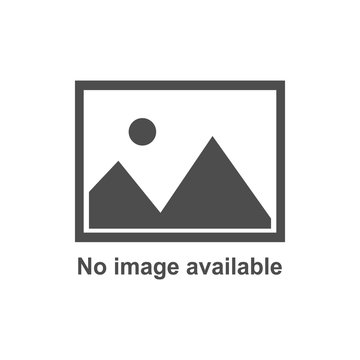
FEATURE – When lean seems to fail, leaders should persist and work even harder to bring people on the journey - by observing the situation, providing clear success criteria, and learning together on the job. That's what leading with lean is about.