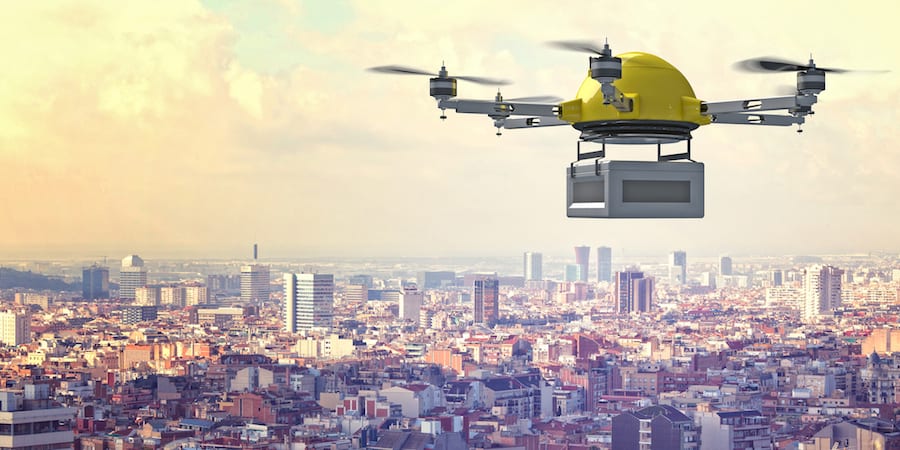
Work as we know it is disappearing; how can lean adapt?
WOMACK’S YOKOTEN – The rise of the robots may still belong in sci-fi books, but there is no doubt that work as we know it is fading away. What is the role of lean thinking in this world of drones and driverless taxis?
Words: Jim Womack, Founder and Senior Advisor, Lean Enterprise Institute
Work, defined as human actions creating value for customers, has been disappearing for a long time. The most striking example is farming, where the work of planting and harvesting was transferred to machinery and weeding was delegated to chemicals over the course of the 20th century, reducing farm employment from 41 to 2 percent of the workforce in the USA. But many other examples can be cited:
- In the late 1940s AT&T in the USA employed more than 350,000 telephone operators, mostly to connect long distance calls. Yet in 2016 government employment numbers show that only 9,750 Americans are employed as phone operators in the entire country even as total calls have grown dramatically and steadily.
- In the 1950s thousands of elevator operators also went away – when technology permitted occupants to do the work of selecting floors.
- In the 1960s the thousands of stevedores needed to manually load and unload ships largely disappeared, as containerization changed shipping.
The activities needed to create value for the customer were still performed, but in a different way and without the need for significant human labor. And much of the elimination of work described above was applauded. Who really wants to spend their life weeding, riding elevators, or carrying cargo off ships? In addition, growth in other, newer activities, aided by the availability of freed-up labor from older activities, meant the total amount of work and the number of jobs to do it increased. A win-win.
But something happened in 1961 that sent our thinking about work down a different path: the first industrial robot – the Unimate – was introduced in a General Motors plant in Ewing Township, New Jersey, to take over welding, directly replacing skilled work formerly performed by humans. In combination with computer-controlled machining centers introduced around the same time – which could be told to do a variety of skilled trades jobs by selecting different programs – this event touched off a wave of concern that robots (although bolted to floors at that time) were on the march and would soon un-employ millions of manual and skilled workers. The first automation panic.
And, very slowly, automation did supplant human work. I recently visited a newly re-tooled General Motors assembly plant in low-wage Brazil with very high levels of automation in stamping, welding, and paint. No humans touching the product there. Not one. However, in the same building hundreds of humans were doing assembly work on a brand-new old-fashioned assembly line, 55 years after the invention of the Unimate made it seem likely that assembly jobs would soon be gone.
So the robots have been marching, but not rapidly in every activity as was once envisioned.
It turned out that good things – and I believe that the automation of work on balance is a good thing – took time. And in the meantime there was another jobs scare – in developed economies, produced by outsourcing manual labor to low-wage countries – to take our minds off marching robots.
Which brings us to the present. The recent and rapid development of precision devices (“robots” is too restrictive a term) able to supplant human work now seems to be reaching a tipping point in which a wide range of tasks that only humans could do until now can be done cost-effectively very soon with no direct human help. Robots really can march now, and fly as well – drones are simply flying robots. Leaps in sensor technology (vision systems, Lidar, micro-location chips) permit tackling a much wider range of tasks. And AI-based programming that allows robots to interpret complex reality and learn from experience means they can even improve their work. What’s more, these advances can be applied to any new categories of work that emerge so that job losses may be a win for consumers but a big lose for workers. Time for the second automation panic. (Read Erik Brynjolffson and Andrew McAfee, The Second Machine Age: Work, Progress and Prosperity in a Time of Brilliant Technologies, 2016, for the details.)
It’s easy to see why a scenario for the decline in human work and jobs seems plausible to many. To cite a few examples in the USA:
- Retail scanners for check out and for receiving goods threaten the 5 million retail clerks, as consumers are conditioned to scan their own purchases and to buy on the web instead.
- The continuing improvement of ATMs and the growth of web-based banking spells trouble for the 500,000 bank tellers still on the job.
- The introduction of automatic binning, picking and packing in distribution centers represents a menace to another 900,000 workers.
- The introduction of autonomous vehicles threatens 4 million commercial drivers, not to mention the million new drivers for Uber and Lift not captured in government statistics.
With all this potential for job elimination, it’s not surprising that dystopian visions are widespread: Perhaps sometime soon there simply won’t be enough work for humans to do?
Given these trends and perceptions, the Lean Community now needs to think hard about the future of “work” defined as value-creating activities performed by humans. This is because the improvement of work has always been at the center of lean thinking. Could both work and lean thinking disappear? I have three thoughts.
First of all, to repeat, good things still take time. There is lots of talk now about millions of autonomous vehicles on the world’s roads very soon. For example, Tesla has just announced that it will immediately start including all of the hardware – vision systems and radars – in its vehicles to make autonomy possible as soon as the software is perfected and passes regulatory approvals. Perhaps a driverless Tesla limo will be coming to pick you up soon, leaving its unemployed driver behind?
But the history of automation is that the prospect always runs far ahead of the reality, like Unimate robots in 1961. The thought that the 4 million plus Americans who make their living by driving vehicles will be unemployed in short order sounds massively disruptive. But it can’t happen quickly. The more than 260 million vehicles using the roads today are completely dependent on their drivers and up-fitting them for autonomy will take far more than some new software. It will require scraping most current vehicles because the needed hardware is not economically practical to retrofit. Equally important, autonomy will require agreements on the social and regulatory context.
Technologies in a narrow sense may soon be ready to eliminate work but creating an acceptable context for their use will take time. So think decades, not years, before most Ubers have no drivers, roboristas (or is it robaristas?) replace humans at Starbucks, and all touch labor in manufacturing, distribution, and retail disappears. Let’s put the automation panic on hold and agree that the improvement of old-fashioned, front-line work by humans will be important and useful for the Lean Community for many years.
On to my second thought. Even as automation grinds rather than leaps ahead, human work – increasingly the design of the equipment and the software that do the work – will still exist in abundance. It will simply have migrated one level higher. Rather than doing work, humans will progressively work on creating and managing value creation systems that do the work. And the work of maintaining (through trouble shooting and problem solving) and improving (through kaizen) these automated value creation systems as conditions change – the task of most of the 7,000 IT folks in a Brazilian bank I recently visited – will still need to be done mostly by humans. (True visionaries, of course, dream of current robots manufacturing the next generation of robots and current software writing the next generation of software. But now we are talking tens of decades rather than just decades. Or maybe we are just talking nonsense.)
Thirdly, following on from my second point, we need to think harder and more systematically as a community about the improvement of software development (it’s a process) and of hardware development (it’s also a process) and of these two processes in combination (because molecules and hardware aren’t going away and need to work in harmony with their electrons and software.) And we need to think more about the improvement of maintenance, to keep new systems running and to upgrade them steadily (e.g., continuous delivery in software – a new, 2.0 version of kaizen?) As we move ahead, this type of work will become a larger and larger fraction of total human work. And its design and improvement will become a larger and larger fraction of lean practice.
Note that this is the exciting task of the lean future – improving the development of value-creating processes and the software controlling them in accord with lean principles. It’s what will keep us relevant in the automatic, autonomous economy.
We are already on the case, of course, with scrum and agile tied more tightly to user experience in the software world. But it’s a real change in mindset to acknowledge that the future task for “workers” will be creating the systems that perform the value-creating tasks rather than actually doing the work. And the future task for lean thinkers will be to improve the way we design these productive systems. We need not only to be on this case but to be playing with much more intensity than we are today if our own work as improvers is not going to end or become irrelevant.
THE AUTHOR
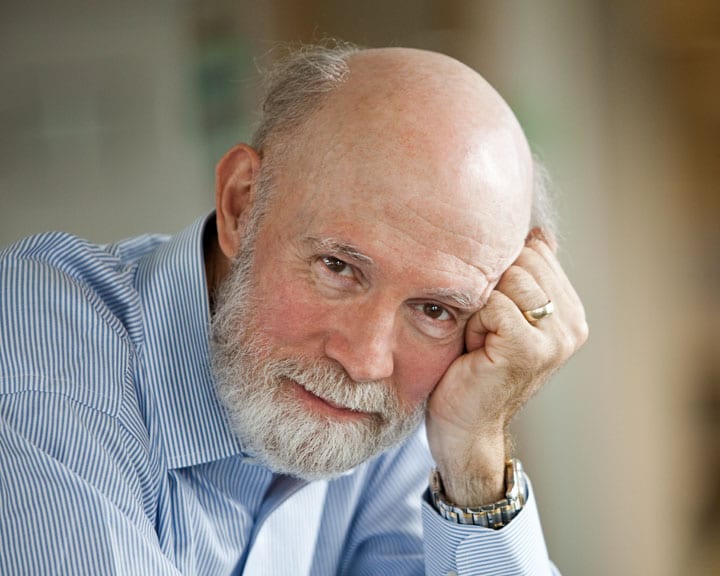
Read more
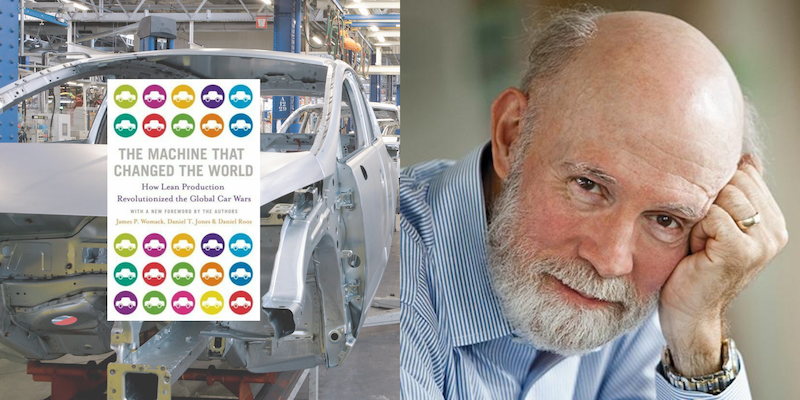
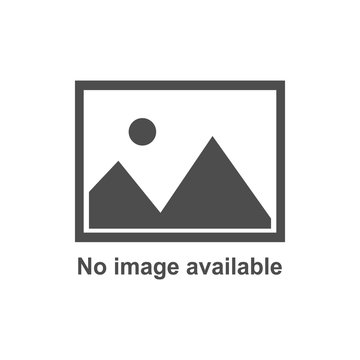
INTERVIEW – Thirty years ago, a book introduced lean thinking to the world, started a global movement and transformed business forever. Our editor caught up with one of the authors.
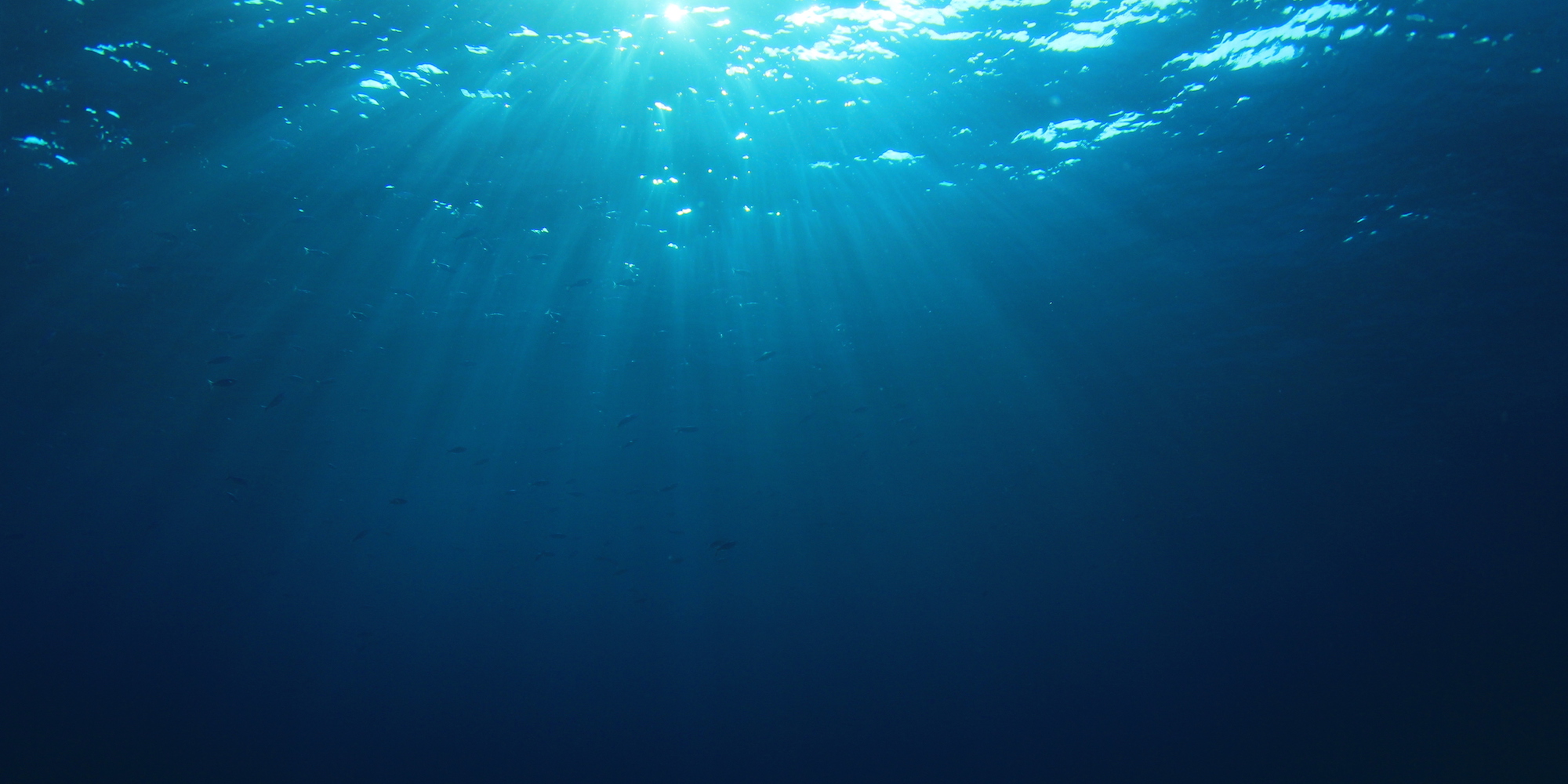
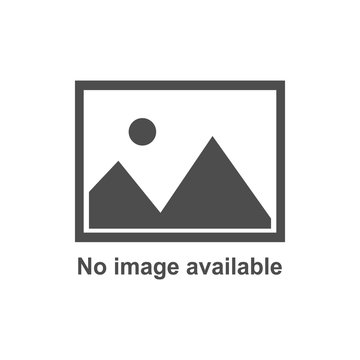
CASE STUDY – Designing good products is challenging in itself, but doing so in harsh, impenetrable environments like the seafloor presents even bigger problems. The answer? Lean product development.
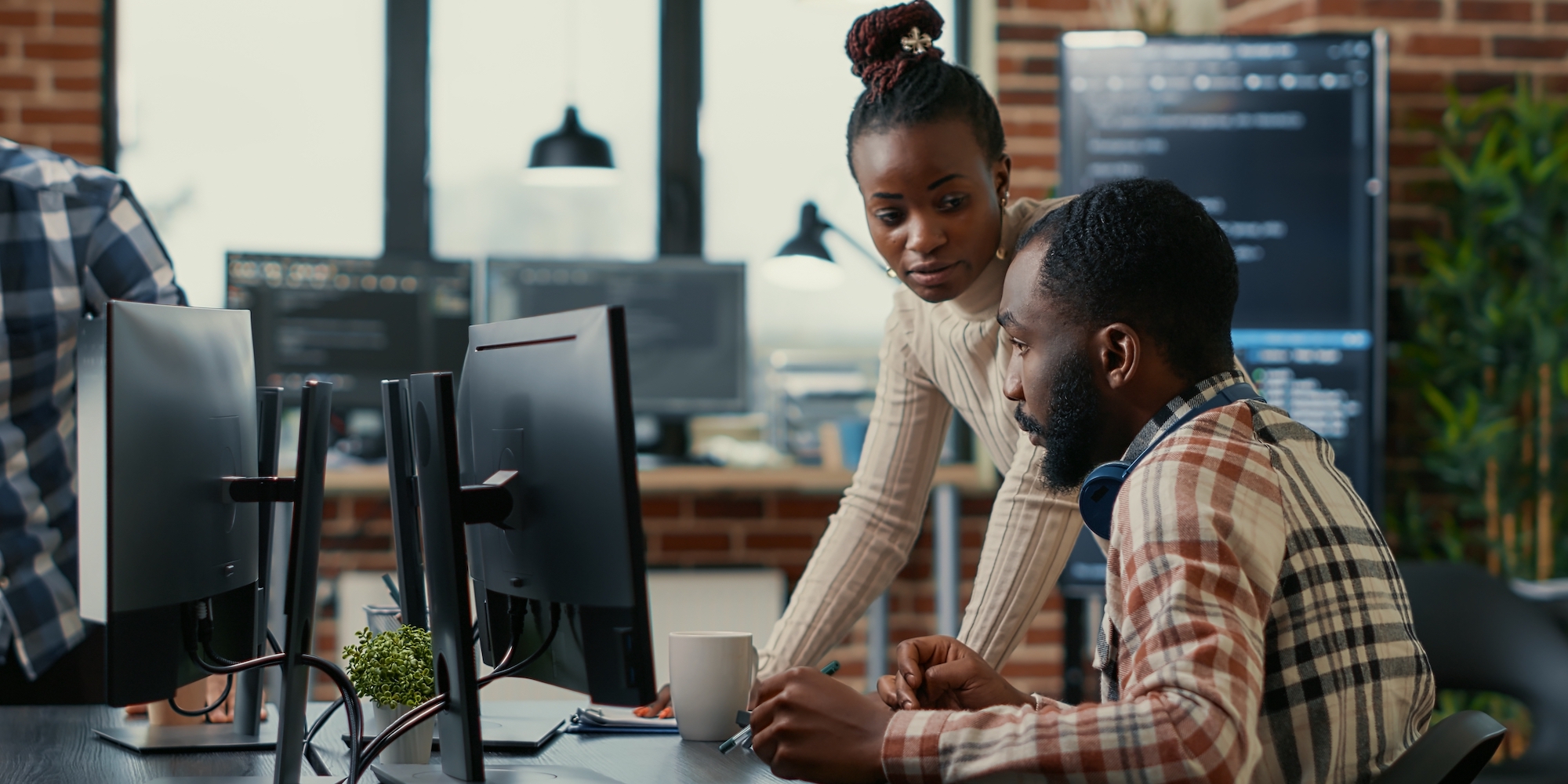
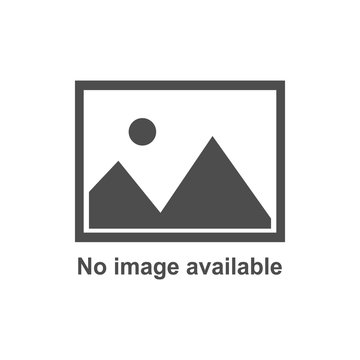
FEATURE – BRQ Digital Solutions shows that effective customer-focused improvement must happen from the inside out, with team development aligned with the pillars of lean digital transformation.
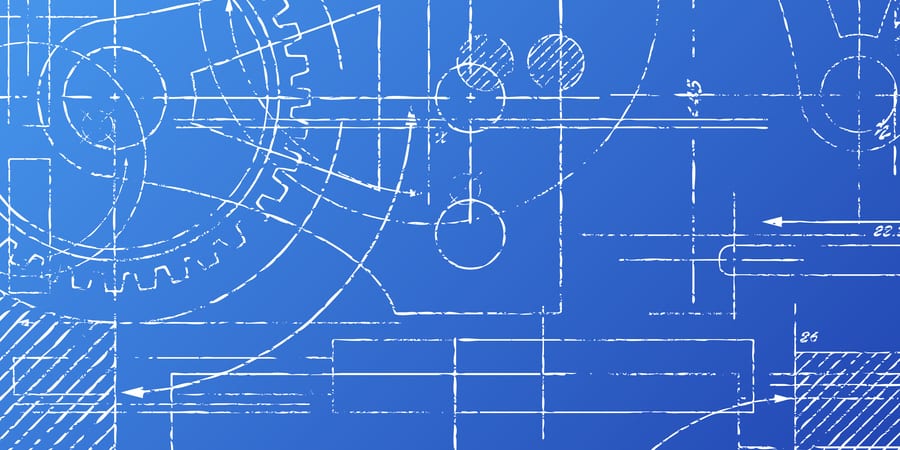
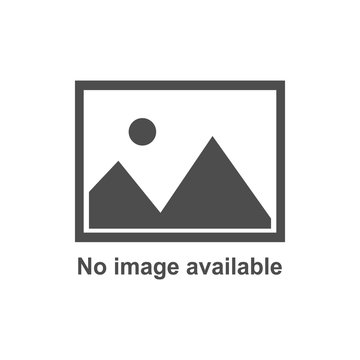
OPINION – Working on new product development without first assessing potential risks will almost certainly lead you to failure. Can you imagine the Wright brothers flying without having done preliminary studies on the feasibility of their idea?