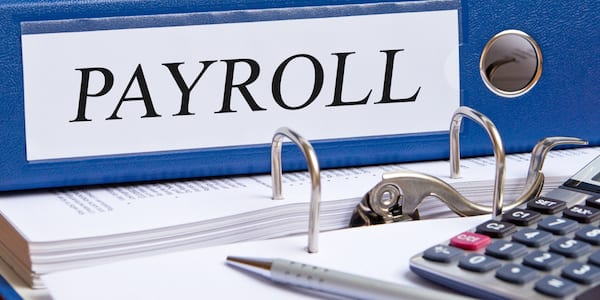
Workshop inspires a financial administrator to embrace lean
COLUMN – Finance is a critical function within a firm. Yet, lean thinking seems to struggle to make progress in this field. Following a workshop with Nick Katko, the author of this article sees an opportunity.
Words: Sylvia Mughal, Financial Administrator, Lean Management Instituut
I have recently become the new Financial Administrator of the Lean Management Instituut. As someone new to the world of lean, I have been marvelling at the value that these principles can bring to our customers. l am lucky enough to be surrounded by a team who fully understand the power of the methodology and I find the prospect of applying it to my own work thrilling.
But where do I start? How can I contribute to the process of increasing customer value? And how do I determine whether I have improved and reached good results?
Last year's motto at LMI was "Practice What You Preach" – well, it is easier said than done.
The most challenging part of my job - I manage the organization's finances - is dealing with incomplete and often last-minute information coming from different sources, which results in work accumulating and inevitably impacts on my accuracy and causes delays. It's a bit of a vicious cycle, too, because this seems to be a repetitive process: the work is inefficient, my focus shifts and unnecessary rework becomes necessary, generating ever more waste. The time I spend putting out fires could be invested in much more valuable activities.
Ideally, I would want the information to be delivered on time and accurately and the work to be processed immediately. In practice, I have taught wrong habits.
Here are a few examples: I am used to collecting the mail in a batch, entering data in the records following a batch logic, and processing payments once a week. Additionally, invoices for our services are processed once a month. This all leads to substantial rework based on the fact that information must be re-checked before an invoice is sent out.
In the meantime, however, I have discovered lean. With it, I have found that it makes much more sense for me to standardize my processes and use one-piece flow as much as I can. Doing that would give me more time to improve my processes and to address the causes of problems (rather than finding a way around them in order to be able to keep up with the work). Previously in my career I had never paid any attention to the concept of "root cause," something I am now very much aware of.
My personal observation is that there are not many experts in lean finance. So imagine my joy when, recently, I have had the chance and privilege to attend a seminar on Lean Finance held by Nick Katko, a very knowledgeable and inspiring teacher.
Before attending the seminar, I had started to read his book The Lean CFO, which has given me new insights and helped me through Nick's lecture. The book describes how financial people must take the lead in developing the company as a lean management system, gives insight into how to create flow in an Accounting Department and - most importantly - explains how to apply these principles to your organization.
The seminar helped me to understand how to recognize waste and see problems in accounting. It also gave me the tools to directly calculate batch sizes or set up a daily flow chart myself.
Essentially, I walked out of this workshop with the necessary knowledge to re-evaluate the current processes and many ideas on how to improve them.
Creating flow in accounting is now my focus. At the moment I am working on a Daily Flow Board for my work as well as for the support team. This way, I get visibility over the workload, I can move towards standardizing it, keeping the flow going and unearthing issues. This will ultimately be the contribution.
I also have the tools to complete the right internal P&L reporting, based on the Box Score. This also requires a major change in thinking, at least in mine, because it entails a calculation at value stream level. Structuring LMI's finances in a way that leads to properly allocating direct and indirect costs will make it possible for everybody in the organization (including non-financial people) to be able to read and digest information.
A statement Nick Katko made during the seminar really stuck with me: "Accounting people need to lead the people in the process." That's where I hope to get.
THE AUTHOR
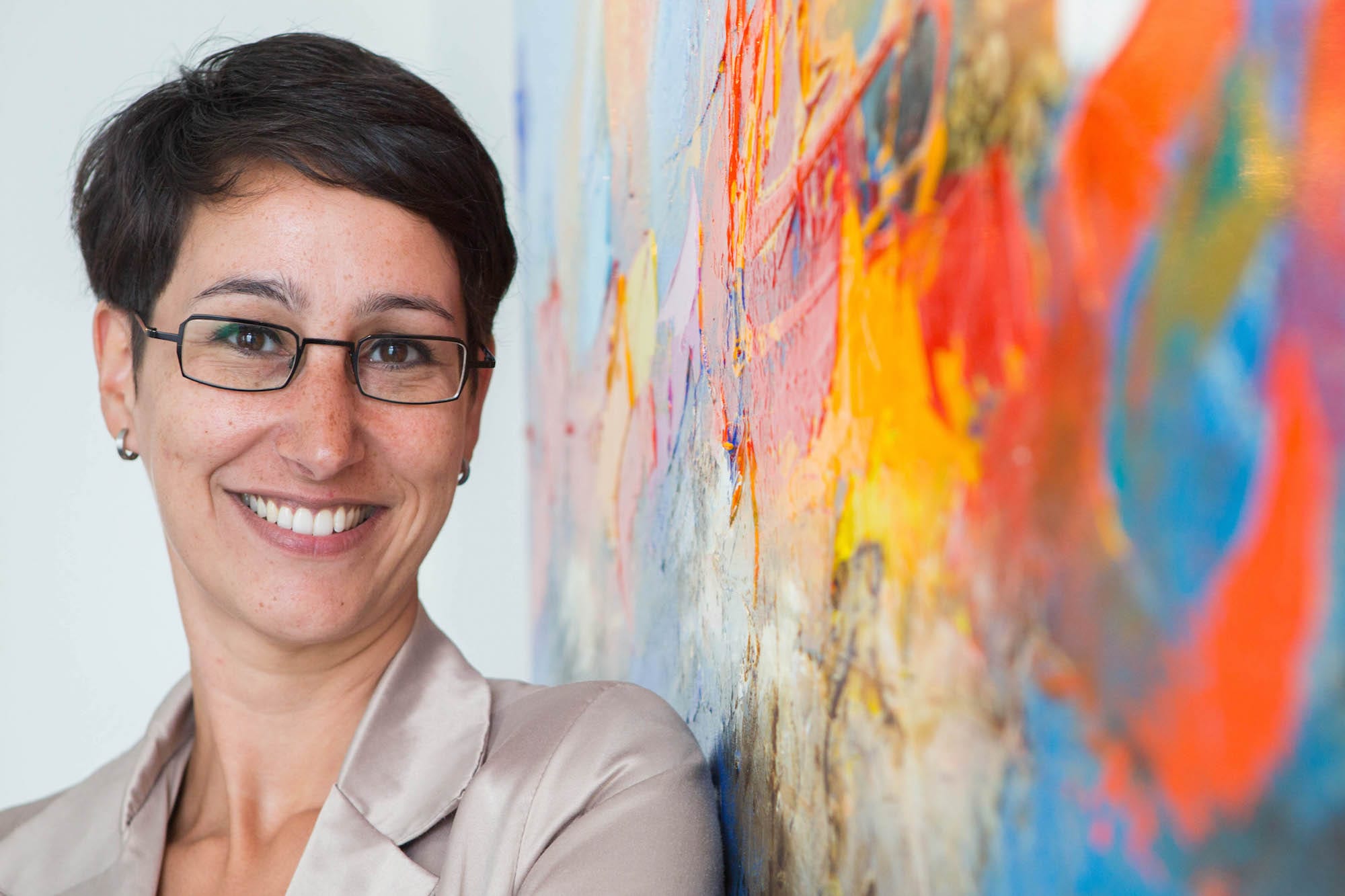
Read more
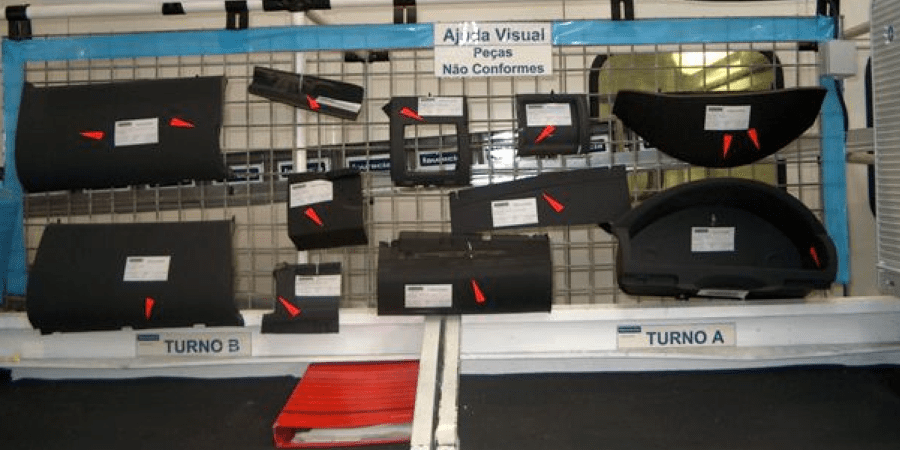
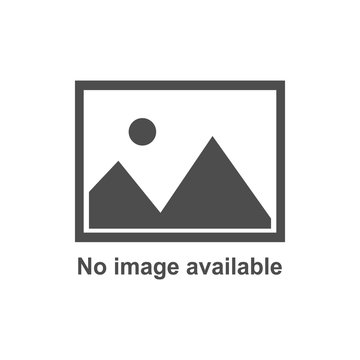
THE TOOLS CORNER – This month, the author discusses how we can ensure quality problems are identified early, tackled swiftly and prevented from reoccurring.
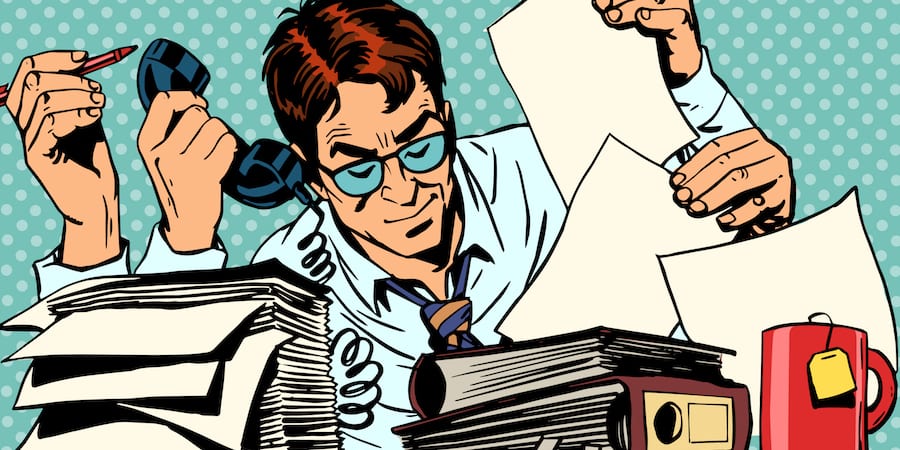
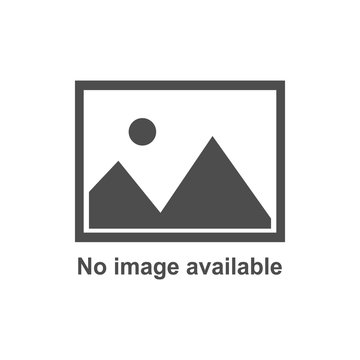
INTERVIEW – In this interview, the former CFO of uber-lean company Wiremold explains why our finance people hold the key to our transformation and gives us the lowdown on lean accounting.
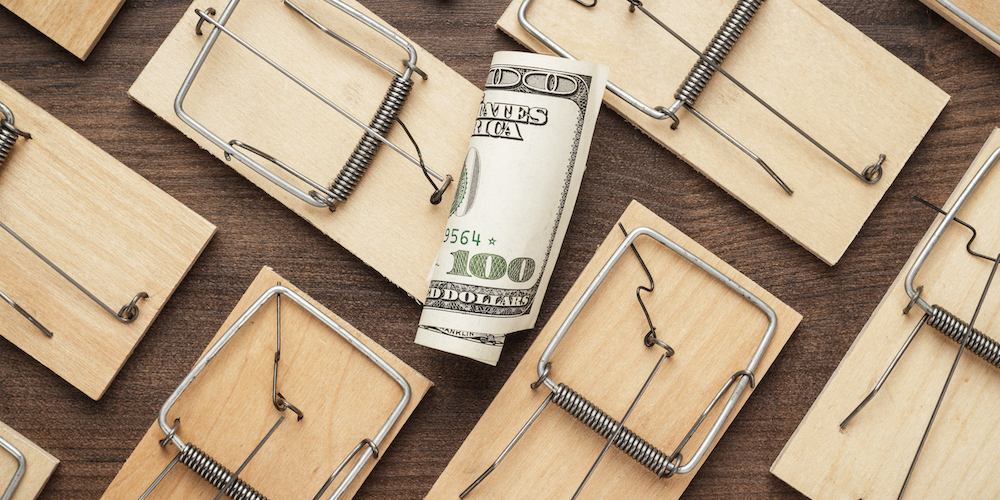
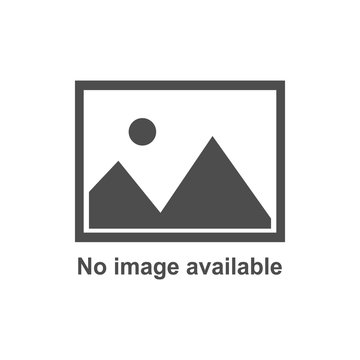
FEATURE – We see the shortcomings of strategies based solely on financial metrics every single day. The author discusses how Lean Thinking offers an alternative that leads to better and more sustainable results.
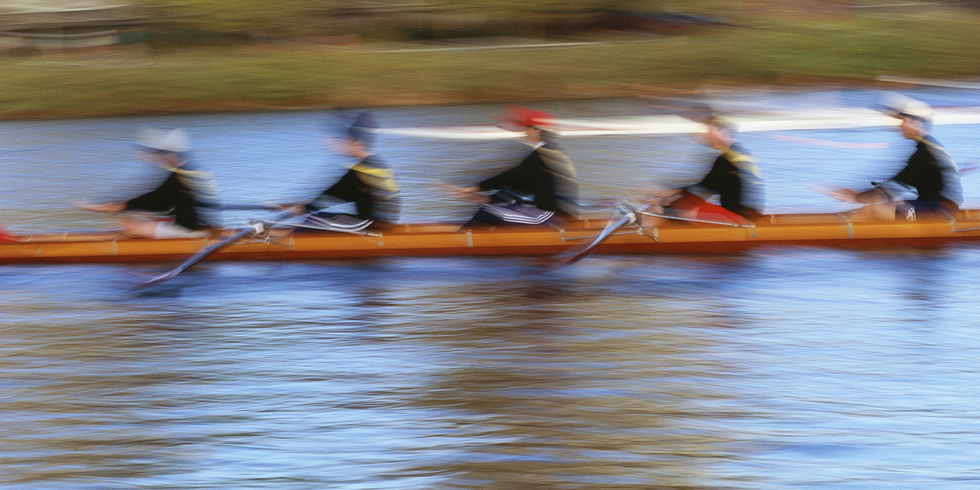
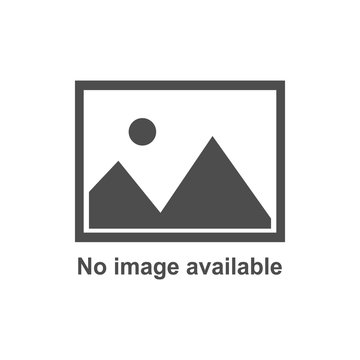
FEATURE – Hoshin is a powerful management practice that aligns the work at different levels to a company’s strategic goals. The author offers a one-page visual summary.