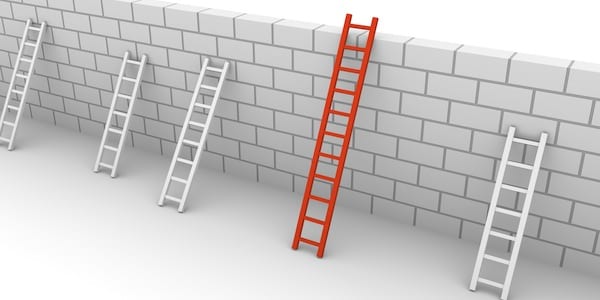
Why national traits do not matter when it comes to lean
OPINION - How often have you heard the sentence, “Lean can’t work here – this isn’t Japan”? Probably more than you can remember. Here’s why national traits are simply another excuse for a failed attempt to change.
Words: Malgorzata Jakubik, Lean Enterprise Institute Polska
There is a set of recurring questions that I get asked almost every time I start talking to a business: how long will it take us to see results? Will lean work in our high mix-low volume environment? And, unmistakably, the queen of them all: Will lean work in Poland?
There seems to be an idea that Polish people are too individualistic, too unruly, and too “non-Japanese” for lean to work.
Well, my no-doubt-about-it answer has always been that being Polish does not stop you from reaping the benefits of lean management principles.
When challenged for proofs, I usually draw on my personal experience and share the example of when I was working with vehicle assembly plants, one in Germany and two in Poland (let’s call them A and B). The German plant was an established lean facility, and so was the Polish plant A. Polish plant B was an old-style organization, with plenty of waste in its processes.
A Pole would always work better with another Pole, wouldn’t you say? And definitely better than with a German, right? Wrong!
People from Polish plant A worked both with the German plant and with plant B. Because the operations in the German site were familiar and the systems supportive and logical, Poles from plant A would fit in within minutes and find themselves fully immersed in daily activities, which they easily understood.
It was quite a different story with plant B. To quote one of the workers from plant A: “It was like we had landed on Mars, with aliens behaving strangely and illogically. It was like learning a completely new language and set of social behaviors.” Who would have thought Mars was actually located on Polish soil!
OK, so we know lean can cross borders, and even become a linking factor. However, there is a reason why in some Polish companies lean really works and brings results while in others national traits are used as a great excuse if things fail. What is this reason, you ask?
A lean transformation is not about copying somebody else’s solution, but knowing what you want to achieve and then designing your own method to get there.
However, with the complex nature of the matter (we all know that a small mistake in how you manage people can take forever to fix), you have to be very careful here.
Here’s the recipe I usually give my customers:
- Understand what behaviors you need - things like support for a common goal, accountability, teamwork, following standards, to name a few.
- Agree on them and communicate them, so there is no confusion.
- Decide what in your national culture will trigger the desired behavior in your people (from the top down, of course).
- Be consequent in how you implement your people change management plan. Adjust your approach as you learn and P-D-C-A it as if it was just another lean tool you implement.
You might wonder what that trigger is for us Poles.
In many nations, people will cooperate because they want to be part of a social structure and are after some sense of belonging, even when this sacrifices individual benefits. Will people in Poland get involved for that reason? Usually no. We like to be part of a group as much as anybody, but if our individual interests are to suffer or our beliefs questioned, there goes the team spirit! What always works with us is healthy competition – being better, faster, or first at something seems to do the trick here. We may laugh about it publicly, but the seed of rivalry grows in every one of us.
So, every time it crosses your mind that lean will not work in your country because of the character of your people, remember this: your ability to change doesn’t depend on the country issuing your passport, but on your ability as a leader to find the trigger that will get your people enthused and to pull it.
THE AUTHOR
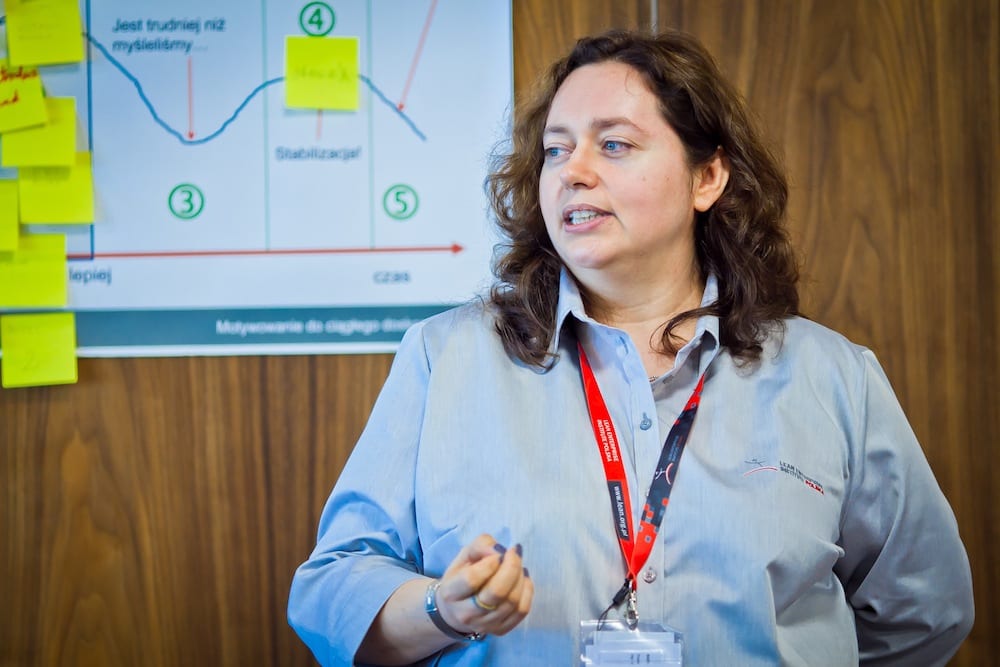
Read more
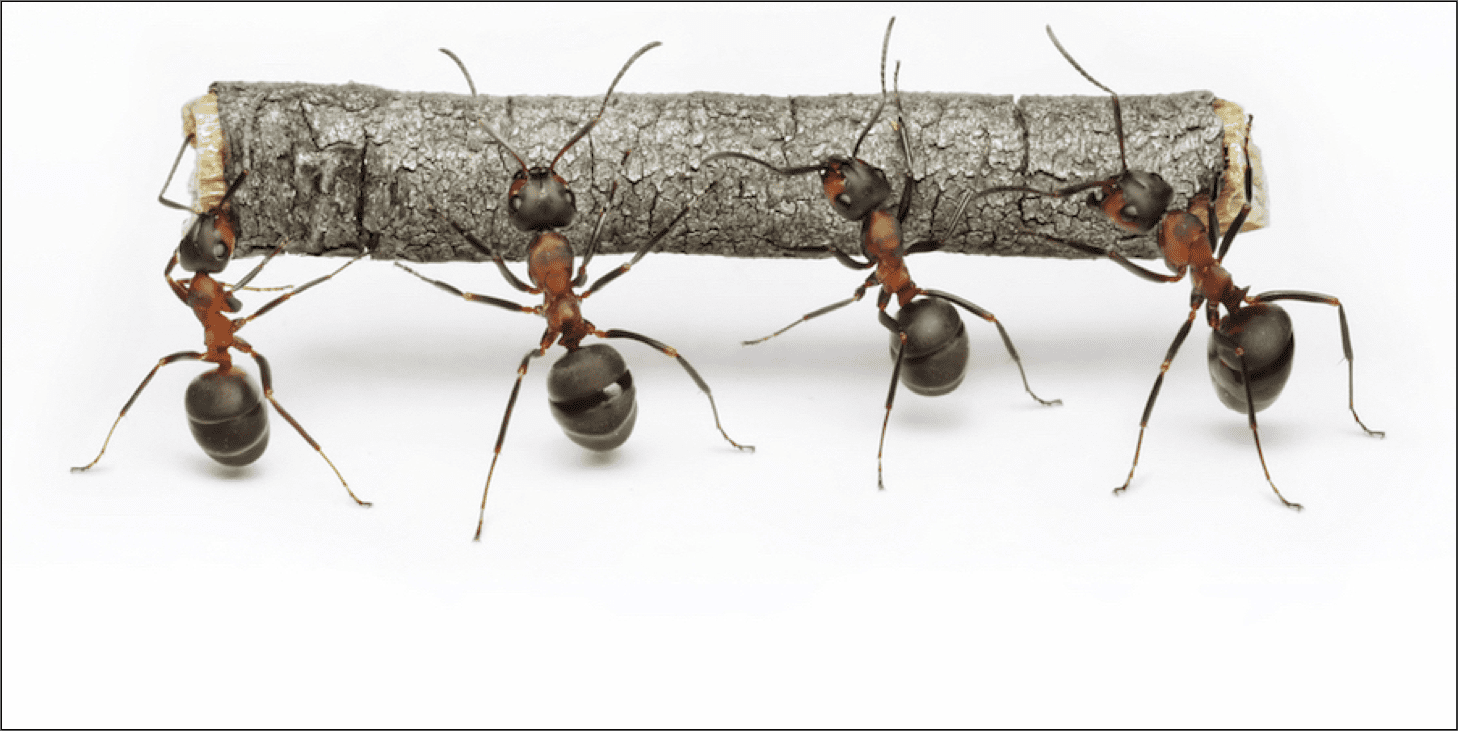
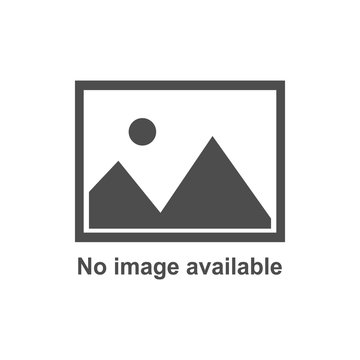
OPINION – Development managers and start-up entrepreneurs are under the illusion that innovation is just the work of especially talented individuals, but in today's world resource sharing and teamwork are preferable.
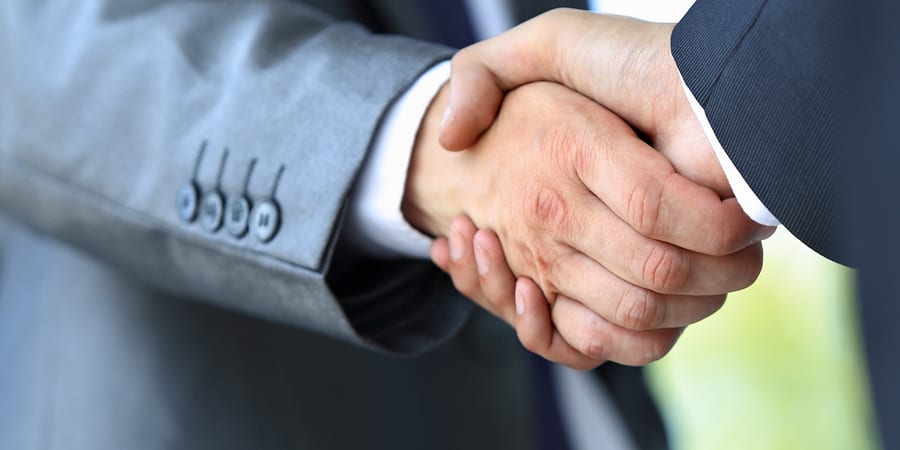
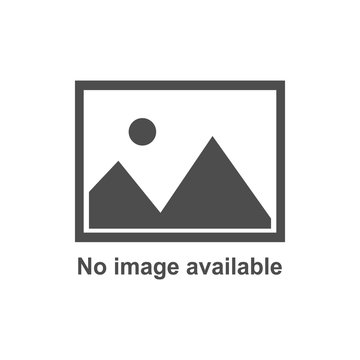
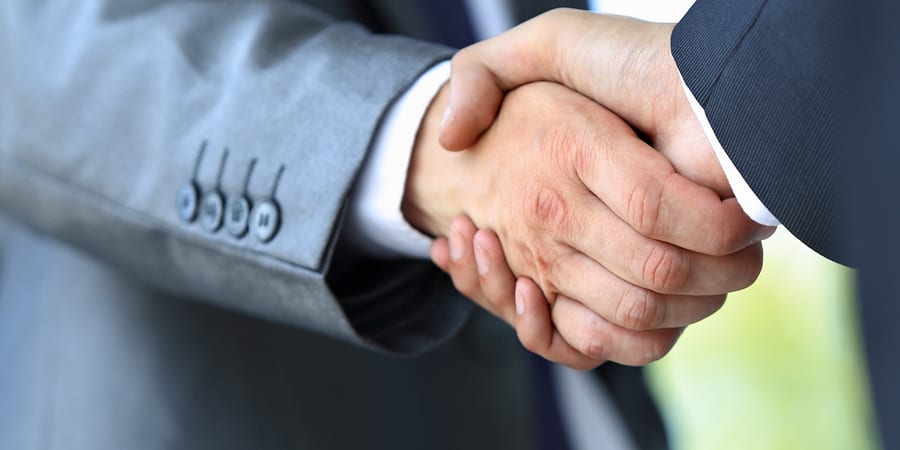
OPINION – The digital revolution has forever changed the nature of employment: today's workers have more choice and employers competing for them than ever before. It's about time our approach to HR reflected that.
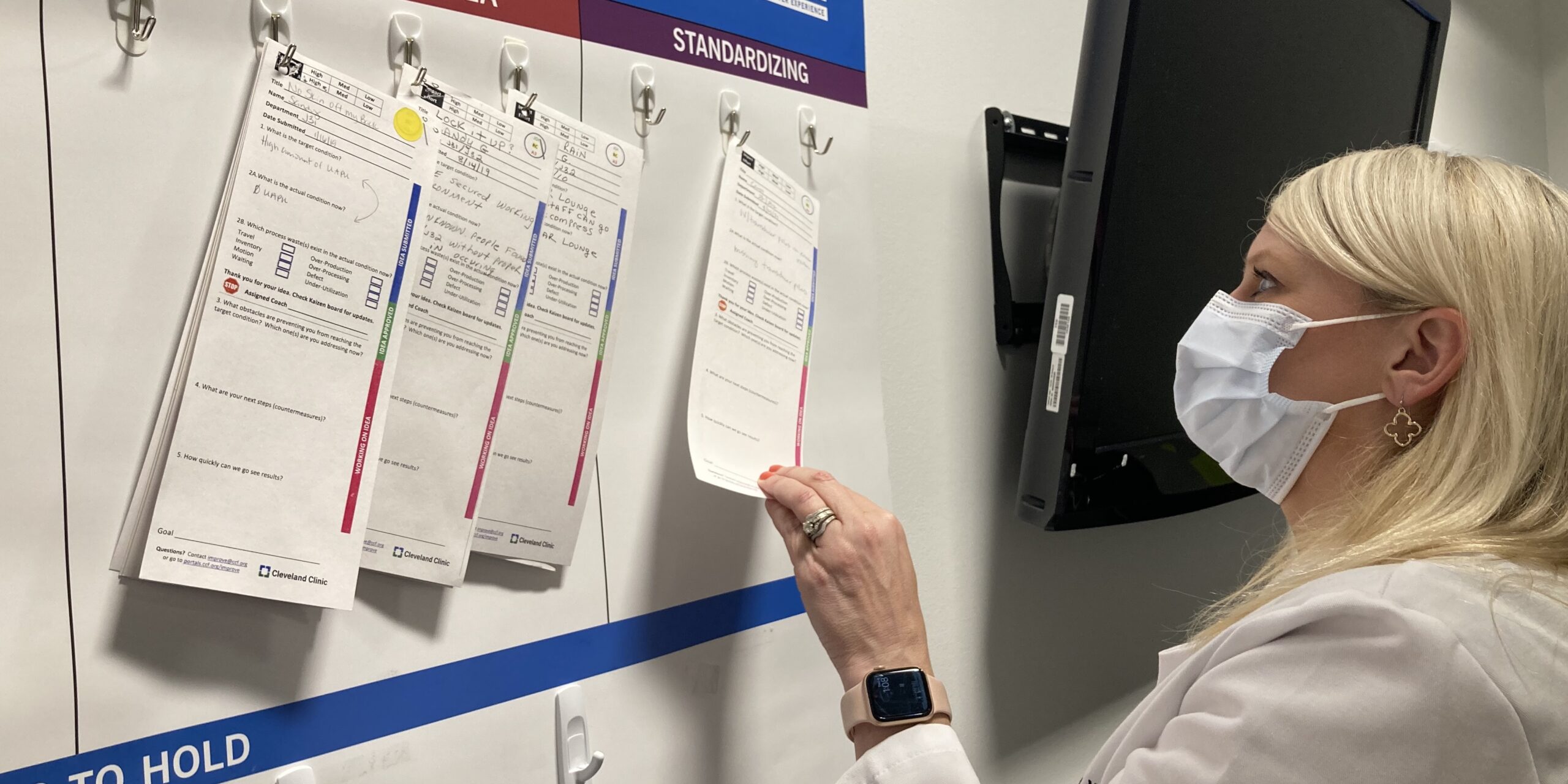
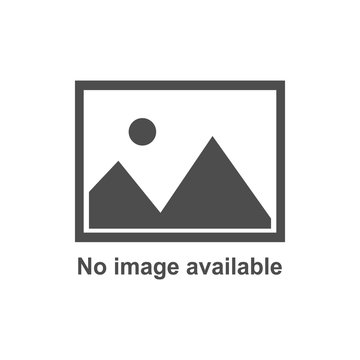
INTERVIEW – Cleveland Clinic has been on a lean journey for a few years now. In this interview, their Chief Improvement Officer and Chief Nursing Officer talk continuous improvement, metrics, and sustaining results.
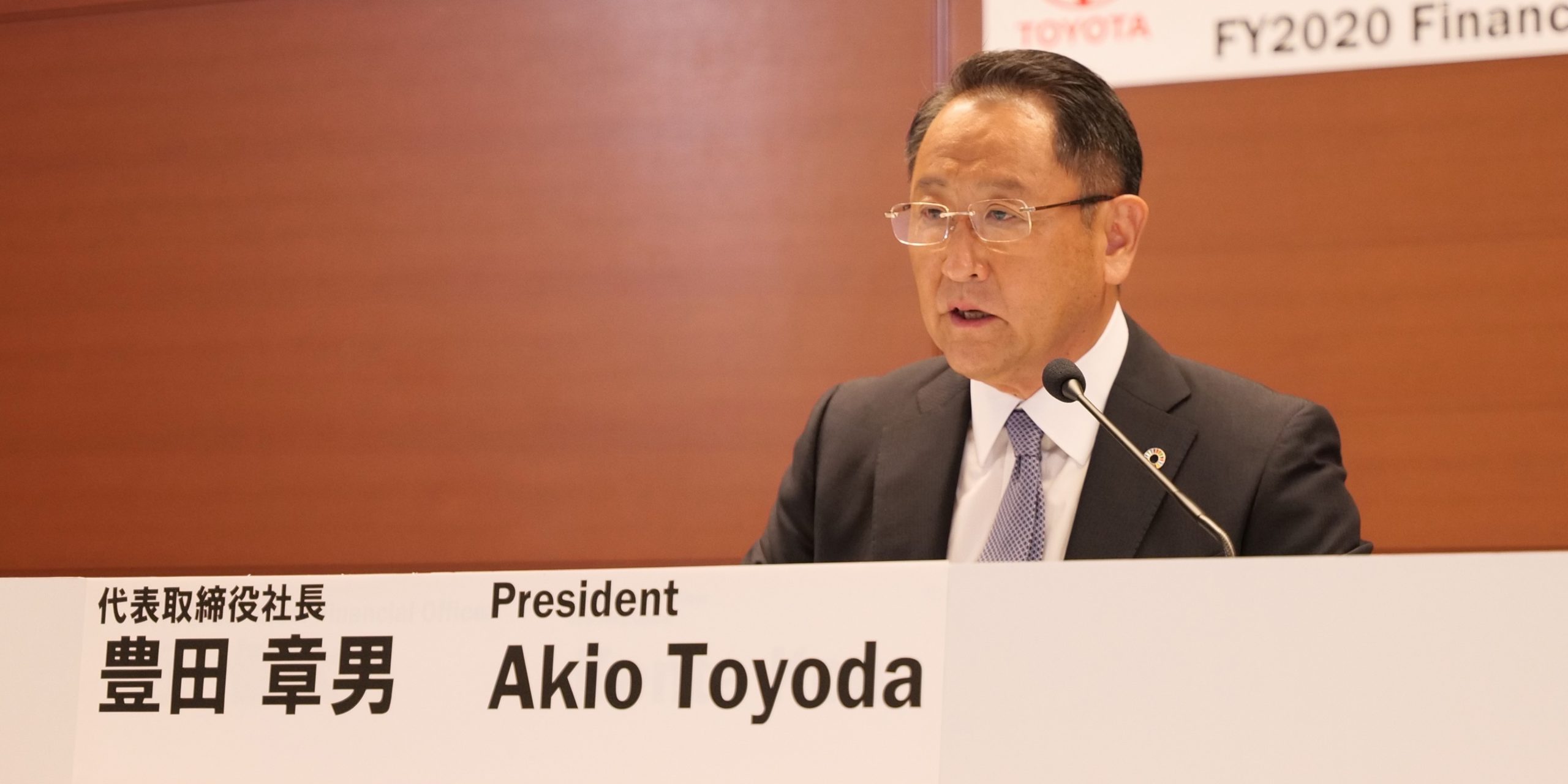
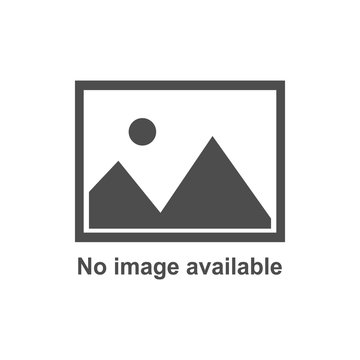
FEATURE – Akio Toyoda’s May 12th press conference to present Toyota’s financial results offers great insights into how the company is reacting to the pandemic, say Jeff Liker and John Shook.