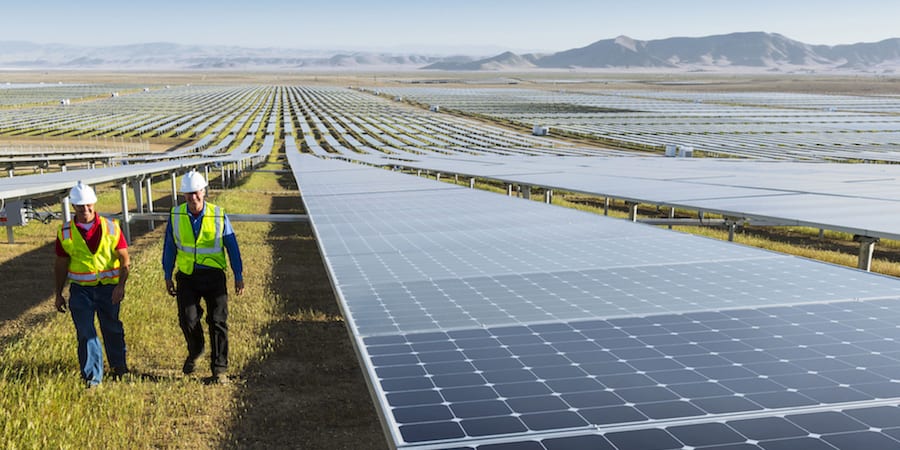
Lean makes our economy more responsible – the SunPower story
FEATURE – The experience of solar company SunPower shows how, by marrying the concept of circular economy, lean principles can help us to transform our habits and save our planet.
Words: Marty Neese, Chief Operating Officer, SunPower
For nearly 200 years, our industrial system has functioned in the same way: we extract raw materials and transform them into products, which we then use and discard. This linear model – take, make, and dispose – is also known as “cradle to grave.”
But what if things didn’t have to end there? What if instead of “cradle to grave” we transformed our economy and made it “cradle to cradle”?
Stopping the devastating effects our lifestyle and industrial system have on the planet and moving towards the cradle-to-cradle paradigm – also known as the “circular economy” – might just be our only hope. To get there entails, first of all, looking at the end of the process to understand what happens to our products when a) they are no longer at their highest state of value, b) become obsolete or c) we are simply not interested in them anymore.
There are already examples of this, like automotive – and it is no coincidence this is the industry in which lean first appeared. The car industry has been setting an example for a while: think of the reused or refurbished cars market, or the remanufacturing of engines and components. As positive and promising as the recycling of durable goods is, however, a bigger question remains: what about other types of products, like phones, for example? I am happy to see the electronics industry increasingly thinking about the next use cycles right at the design stage (design for disassembly, design for remanufacturing, and so on), but these efforts should spread to every product in every sector.
THE STORY OF SUNPOWER
SunPower is a vertically integrated solar company that designs and manufactures solar cells and panels for residential roofs, commercial buildings and wholesale power plants. We are 66% owned by French multinational integrated oil and gas company Total and operate factories in the Philippines, Malaysia, France, California, Mexico and South Africa.
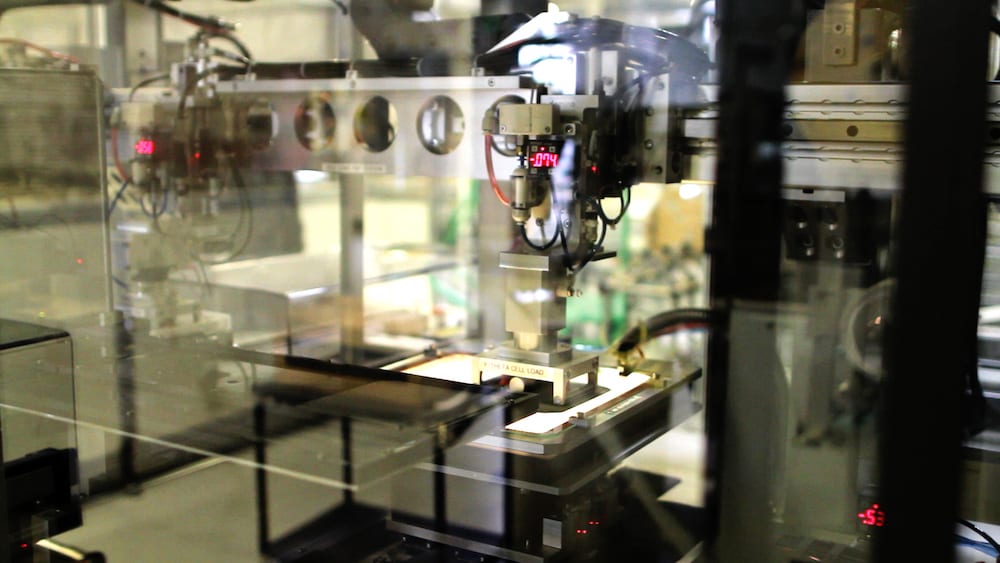
When I joined in 2008, SunPower was very semiconductor-oriented. When we started to lay the foundations for lean in 2009-2010, our focus was predominantly on statistical process control. To function as a unit, every cell needs to perform the same, so we aimed to reduce variation as much as possible and we became very good at that. We were going extremely deep into process control, and we saw lean as an opportunity to orient ourselves more towards flow.
What does the circular economy have to do with SunPower?
Well, we soon decided to add another dimension to our transformation and to embrace the “cradle to cradle” concept in our factories. Products can be Cradle to Cradle certified, and all of our DC PV panels have obtained this certification. For SunPower, the circular economy has been a breath of fresh air. More than anything else, it gave us a framework to open our aperture a little wider: we stepped back and asked ourselves if what we were doing to improve was sufficient. Was it inspirational enough? Was it the best we could do? Was it challenging our innovators enough? Was it encouraging our employees to dream big? It wasn’t.
Adopting the circular economy framework and the ideas it promotes (such as, being at the highest ecological standard of production or having targets like zero waste to landfill) boosted the engagement of our people and encouraged them to ask more questions. Previously, we often never considered what happens when our product leaves the factory, or where our raw materials come from – let alone, what happens after the customer is done with a product.
A PERFECT MATCH
When I was first exposed to cradle-to-cradle thinking, I finally saw an opportunity for mankind to design our way out of what we designed our way into. If we ran an industrial system based on the linear model for 150 years, there is no reason we can’t have a circular framework as our guiding principle for the next 150. If we are to ever get there, however, we need to start thinking in terms of restorative systems.
The beauty of this approach is that once you start thinking that way, you can’t unlearn it. It’s like lean… when you learn to see, you can’t un-see (which is a bit of a double-edged sword at times). At SunPower, we see the circular economy as an inspirational, expansive and highly teachable concept that resonates well with people of all ages and at every level of the organization.
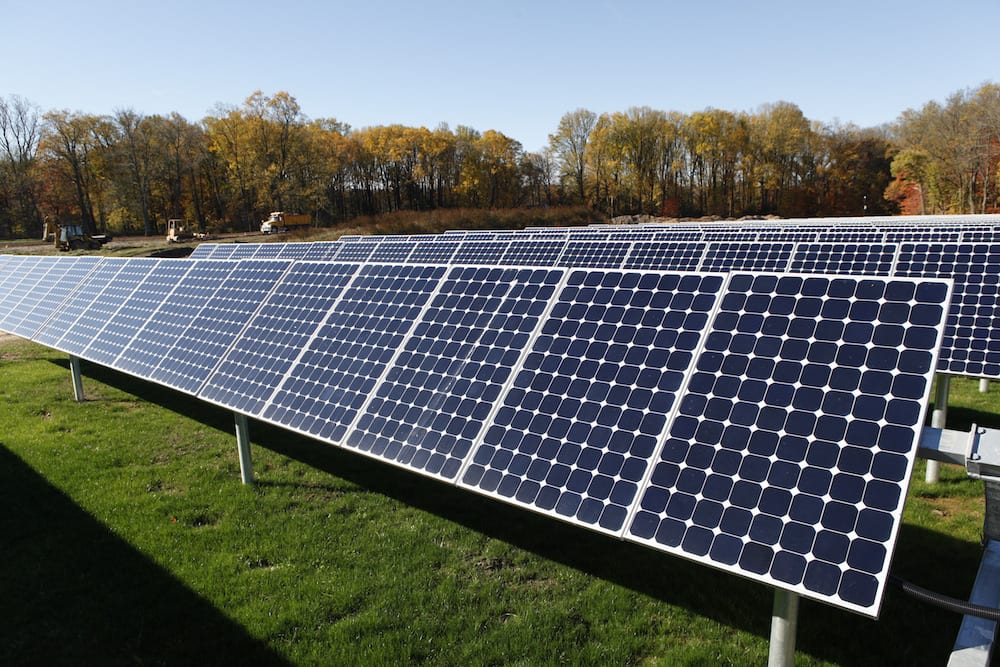
People have a certain awareness of how critical it is that we change our ways: they leave work and see air pollution, environmental changes and waste, and they easily get their minds around the benefits of the circular economy. They see how globalization is turbocharging resource depletion, multiplying the negative effects of environmental damage, and exacerbating the effects of the linear model we have been following for too long.
There is a lot of talk about “lean and green” and there is no doubt that lean has a critical role to play in transforming our economy. In fact, in SunPower’s experience, cradle-to-cradle thinking and lean thinking go hand in hand: we have taken full advantage of lean – the transformational drivetrain that we use to move the company from point A to point B – and we have used the concept of circular economy to push ourselves to aspire to something higher. Can we make products that are entirely beneficial by design? Can we create a restorative power plant? It’s like a seed you plant into your R&D team, and it does grow. In simple terms, one could say that the circular economy framework is our “where to”, whereas lean is our “how to” through engagement of people at all levels. Without lean, we certainly wouldn’t have gotten the level of interest and engagement in cradle-to-cradle thinking that we see: thanks to the methodology, we can show our people a pathway to doing inspiring things. And wouldn’t they want to stick around to see how that goes?!
Lean is helping us to rally our troops, but this is a two-way street: lean thinking and cradle-to-cradle thinking have a lot in common. The former might be the highest form of respect for our planet and the future generations inhabiting it, and the latter is of course the evangelical voice advocating for respect-based improvements.
Over the past two centuries, we have designed a hugely valuable system that has revolutionized the world and given us prosperity, but there have been consequences. The limitations of our planet are starting to show and unless we adopt a new, leaner and more responsible approach to designing and producing what we need, our future won’t be too bright.
THE AUTHOR
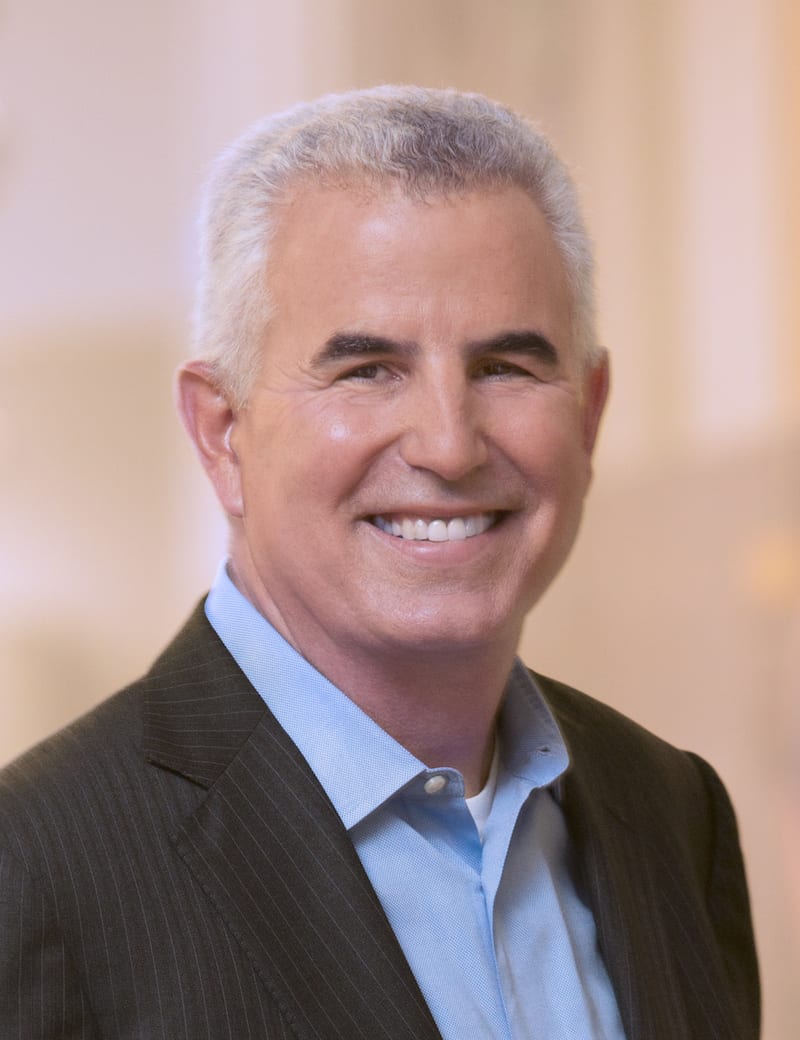
Read more
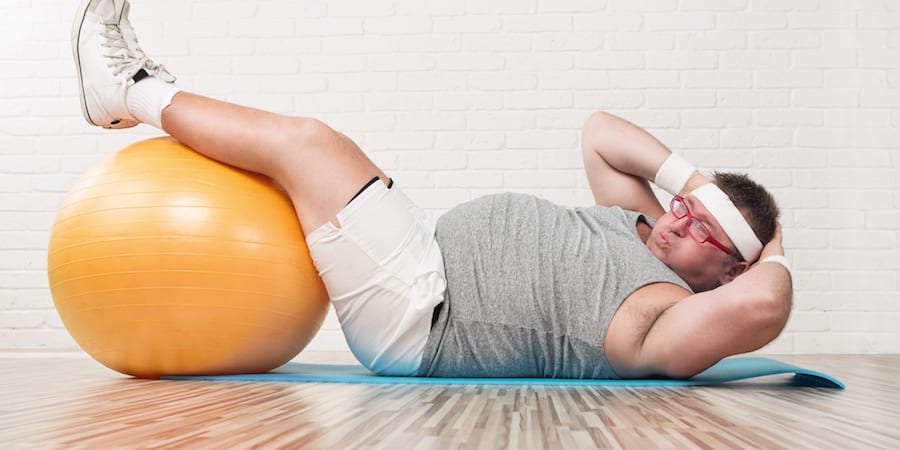
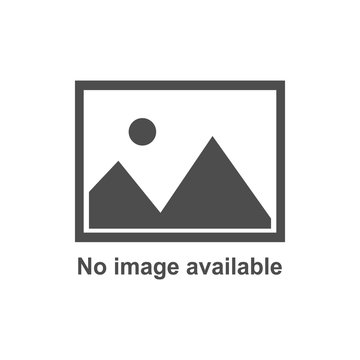
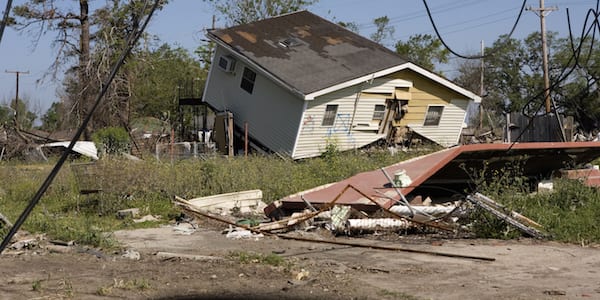
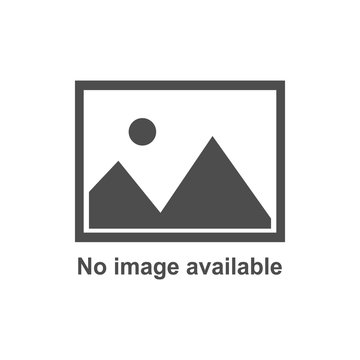
CASE STUDY – Following one of the deadliest hurricanes in US history, an NGO started to use lean management principles to speed up the reconstruction of homes in the Louisiana city… and the results were impressive.
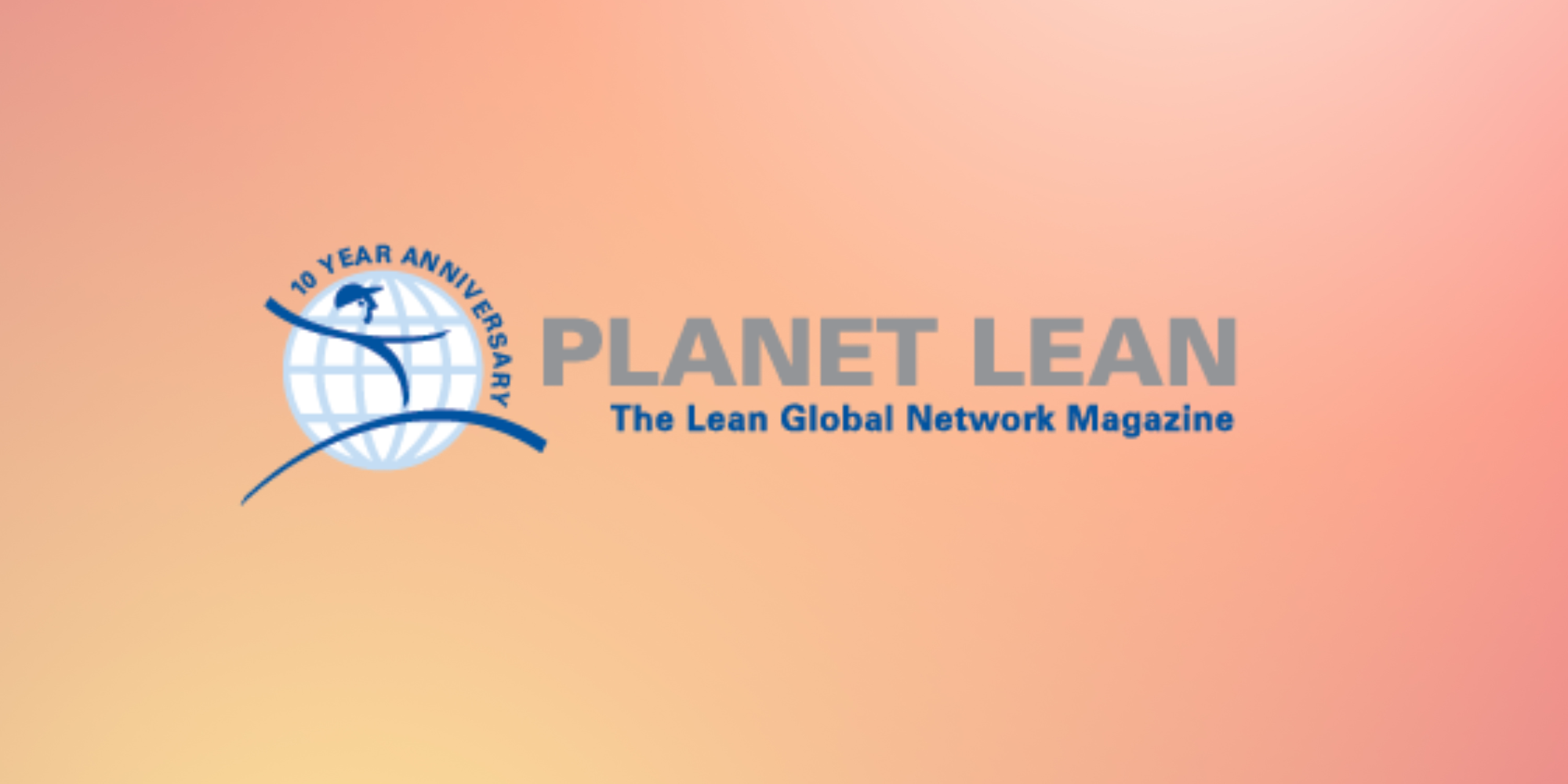
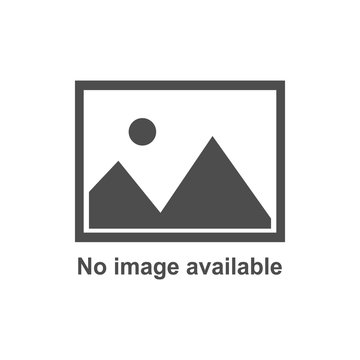
FEATURE – Ten years ago, Planet Lean was launched as a new platform for the Lean Community to share its experiences and knowledge. Our editor reflects on the magazine's mission, history and contribution of the spread of Lean Thinking.
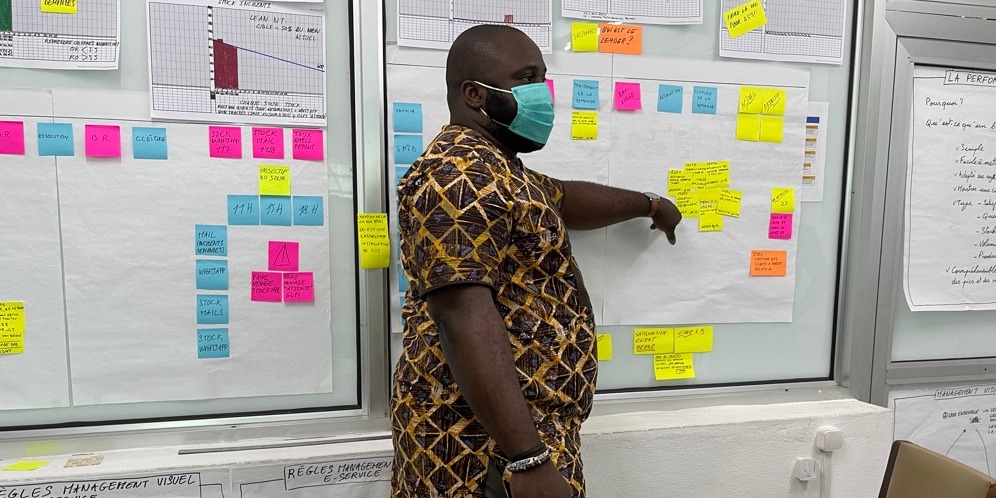
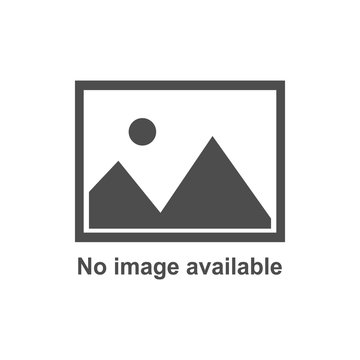
INTERVIEW – In today’s Q&A, we learn how Lean Thinking is supporting the digital transformation of the public administration of the African country of Benin.