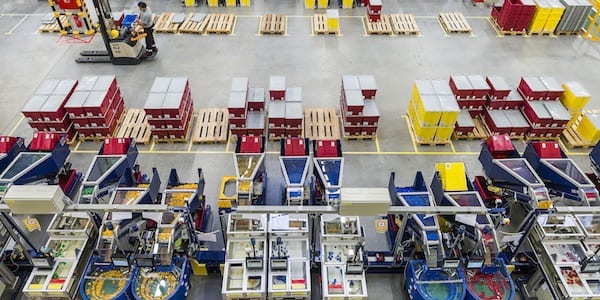
Lean thinking and modular layout: LEGO's model factory
INTERVIEW – Planet Lean meets LEGO’s Ilona Takács to learn how the toy manufacturer looked at its corporate values to built a new, super-lean factory in eastern Hungary.
Roberto Priolo: Can you tell our readers about the new LEGO factory in Nyiregyhaza?
Ilona Takács: This new plant represents a very important investment for the organization in Hungary. The factory was built in only one year and opened on March 25th. It’s the most advanced manufacturing plant of the LEGO Group to date. The Nyiregyhaza factory is 122,000 square meters, employs 1,500 people (250 new jobs resulted from the company’s investment of €200 million) and holds 662 molding machines.
RP: What convinced the organization of the need to create a new facility?
IT: We were producing out of a rented facility and using external warehouse capacity. We spent a lot of money to apply modifications to ensure compliance to quality and safety requirements. Additionally, there was simply no possibility for us to grow: now we have twice as many molding machines and our modular layout enables physical expansion of the factory depending on demand.
RP: LEGO has factories in Denmark, Czech Republic and Mexico, with a new planet being built in China to supply the Asian market. How did you apply the lessons learned at other sites around the world to the greenfield in eastern Hungary?
IT: We consulted with other plants, of course, and upon building the new factory we prepared a manual. It may sound funny, but that’s exactly what we did: we were trying to follow a standard approach to the construction of the site. If you go the Chinese plant you mentioned, you’ll find exactly the same layout.
There will of course be small modifications in different facilities around the world, depending on the country’s regulations for instance. However, the basic principles remain the same throughout the LEGO Group.
RP: Where you after right first time when you were building the facility?
IT: We had to accept the fact that there cannot be a perfect outcome at the first shot. We can always adjust and improve, but having our three main pillars - safety, modularity, and optimal flow - to guide us was critical. They were our vital few in building the new factory, if you will.
To make the building according to those specifications was one of the LEGO Group’s hoshin metrics for this year. Being the global owner of the hoshin tool within the organization (we have 15,000 people worldwide), I’m very proud of what we have achieved and of our success in Nyiregyhaza.
RP: Was the flexibility to adjust to fluctuations in demand, and therefore modularity, one of the company’s main concerns?
IT: It was. We are a very seasonal business, with 60% of our products being purchased at Christmas. There is nothing we can do to change that. In January we start selling the smaller boxes, and then closer to the end of the year we release the bigger boxes. But demand leveling is indeed quite difficult for us. That’s why building a factory whose production space can double depending on demand was very important.
Additionally, with the new facility we are able to produce the entire range of products, including the DUPLO line (which is critical for us, because those customers tend to be for life) and ‘classic’ LEGO products.
RP: How do LEGO’s corporate values translate into the layout of the factory?
IT: We really wanted our factory to help us to deliver on our four promises: Play Promise, People Promise, Partner Promise, and Planet Promise. That’s how we turned corporate values into a factory blueprint. Everything we changed, we wanted to be for our customers’ benefit. This way not only were we able to build a factory tailored to our production needs, but also to implement a number of green solutions which make it one of the greenest factories in the country. We also wanted to ensure our colleagues could work in a safe and comfortable environment.
At the brainstorming session ahead of building the new facility, all kinds of ideas came up. It was the time when we had to look at our corporate principles and really concentrate on making them part of our project going forward. It was a massive undertaking, but a great accomplishment in the end.
RP: What are the advantages of a greenfield project?
IT: The number one benefit is that you have a blank piece of paper and you can do whatever you want on it. But there is also an opportunity to involve people from the very beginning, to work on solutions together right from the design phase.
RP: How did you see people react to the new factory? How did their daily working life change?
IT: The new facility is three times bigger than the previous one, and I have seen how getting used to such a different working environment can take a toll on people. But they are now starting to figure out the advantages of a modular, safer site. It’s a trade-off, really.
Another thing I’ve discovered is that there is no such thing as too much information: sometimes you need to make a business decision and if people understand why it was made, they can better digest it.
RP: Would you say LEGO is a company people are proud to work for?
IT: Very much so, but everything we have become stems from the fantastic results our people have been able to achieve in terms of safety, quality, etc. Those are some of the factors that convinced the company to invest so much in Hungary.
RP: How do you keep track of progress and improvements at LEGO?
IT: By having a plan and following up on it. Very simple visual management is the way to go: are we on time or are we behind? Even though we had been using lean tools in operations since 2008, at the beginning of the transition to the new factory we had not set up visual boards. But we soon recognized this is the only way to track progress and action immediately. People are often worried such a system will highlight their shortcomings, but it’s important that they understand that being behind is okay, so long as you are taking the needed corrective action as soon as possible.
This interview is also available in Hungarian here.
THE INTERVIEWEE
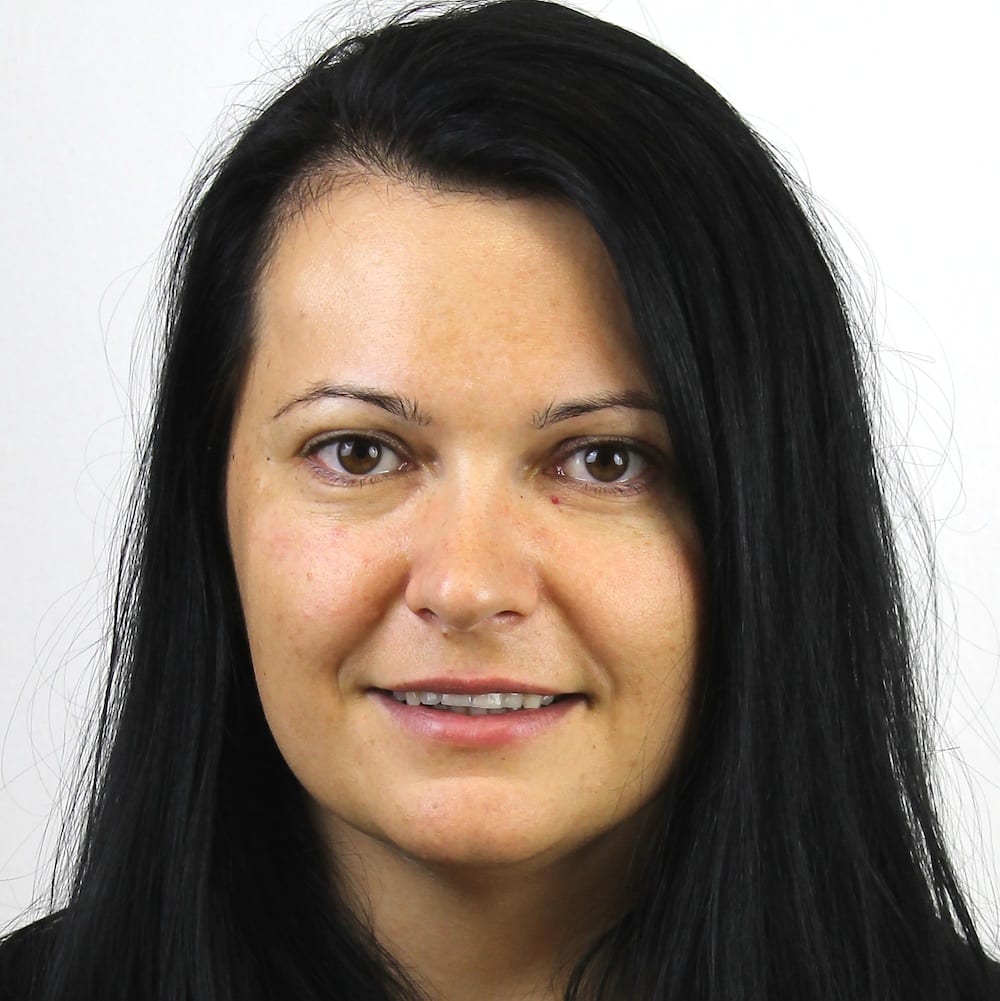
Read more
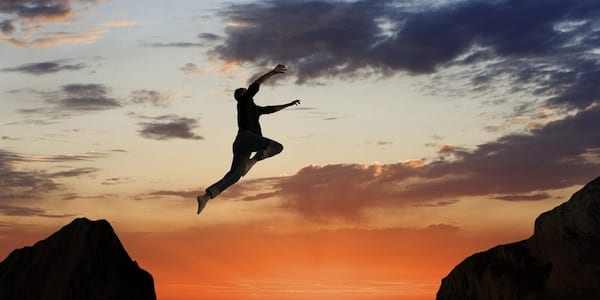
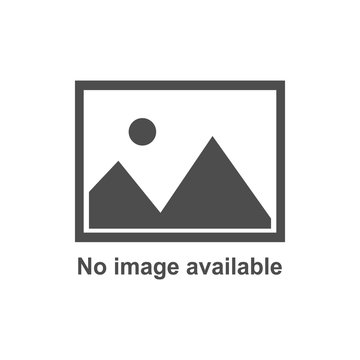
INTERVIEW - What does "leading through incompetence" mean? Peter Willats discusses the role of leadership in a lean management system and the evolution of lean thinking.
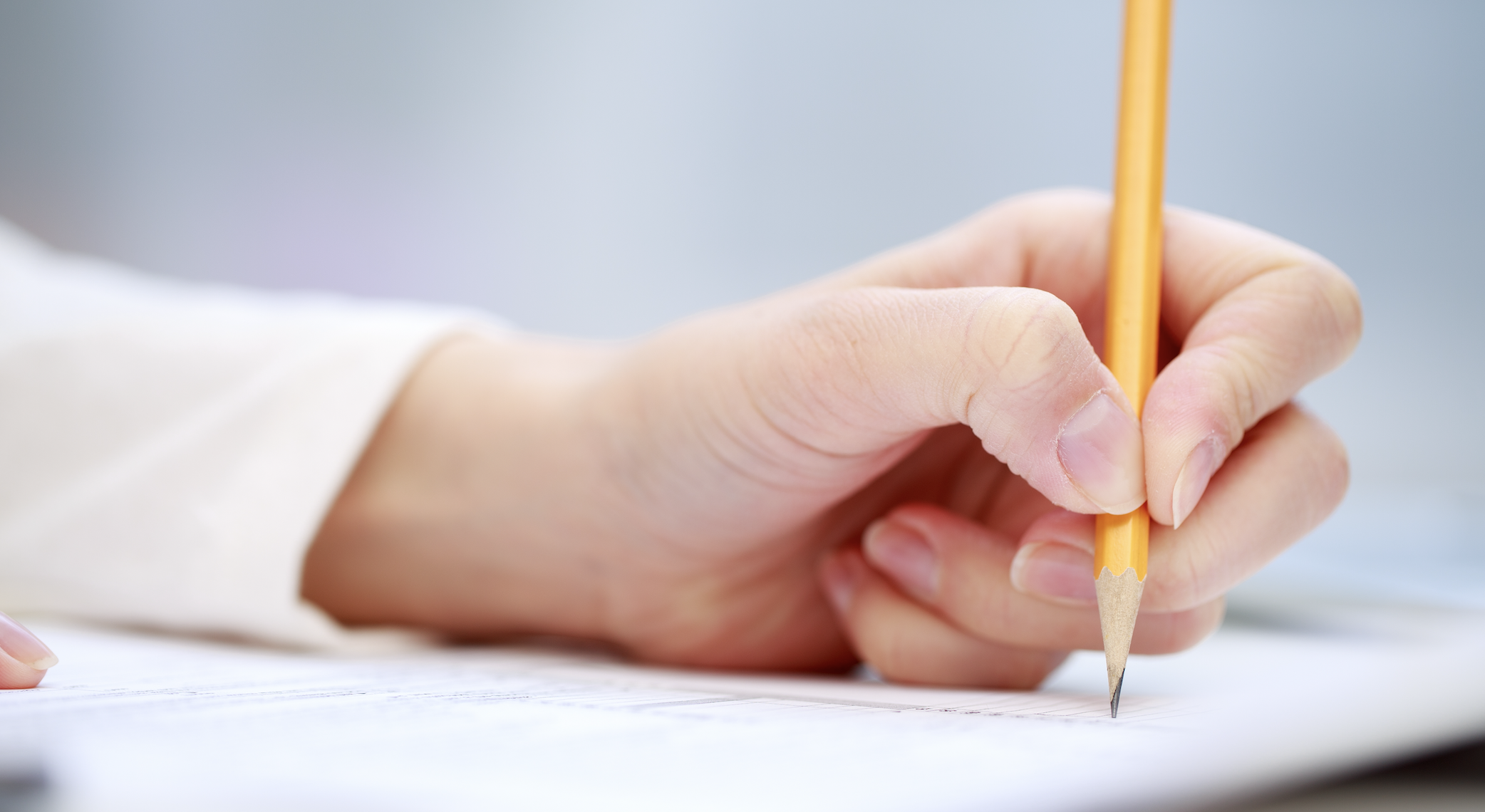
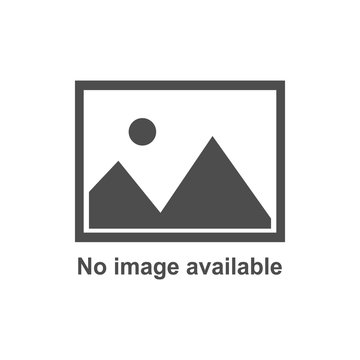
FEATURE – Using her distinctive narrative style, the author breaks down the A3 process to help you understand how it works and how you can tap into its potential.
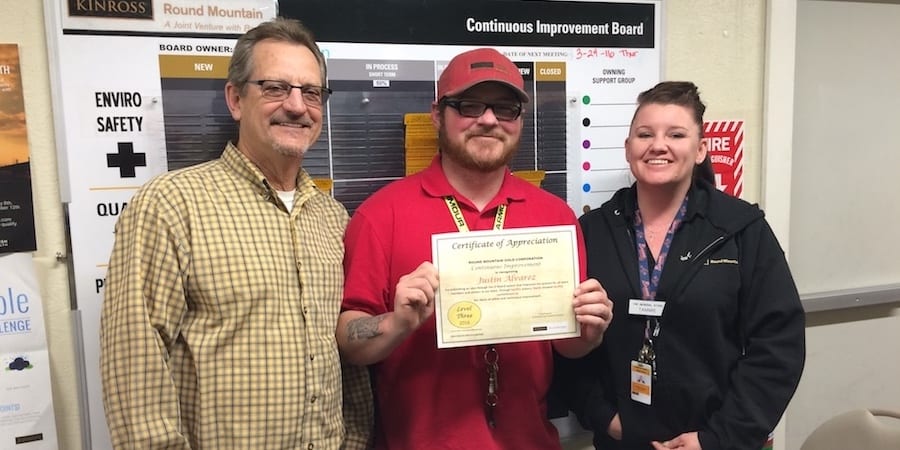
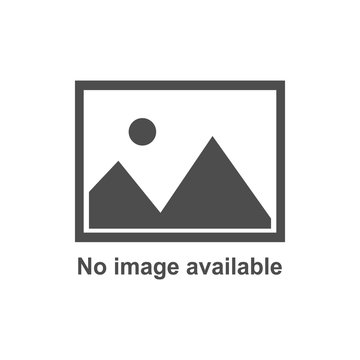
FEATURE – The Continuous Improvements Boards at the Round Mountain mining site have been critical to shifting the company's culture... the secret, it turns out, is always providing feedback on people's suggestions.
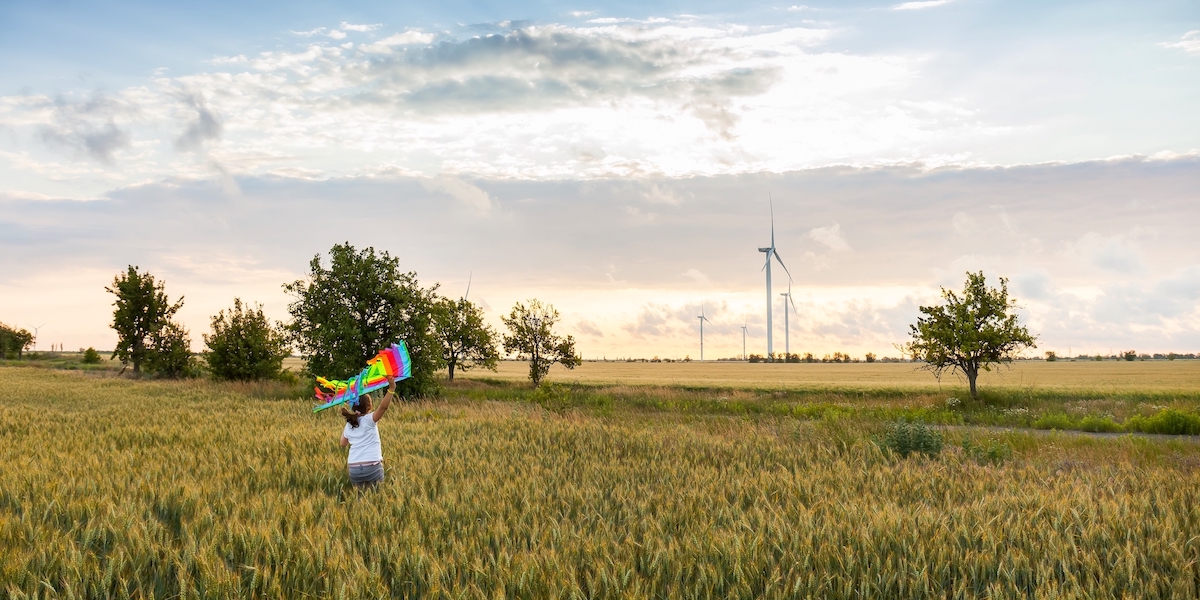
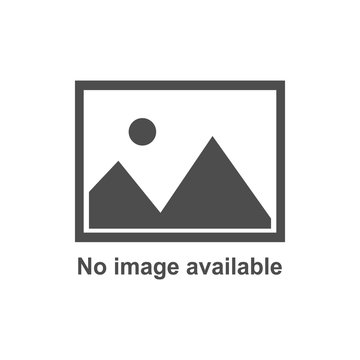
FEATURE – When it comes to the fight against climate change, we can’t expect to achieve much until we fundamentally challenge the way we think about resource consumption. Lean is our tool to do that.