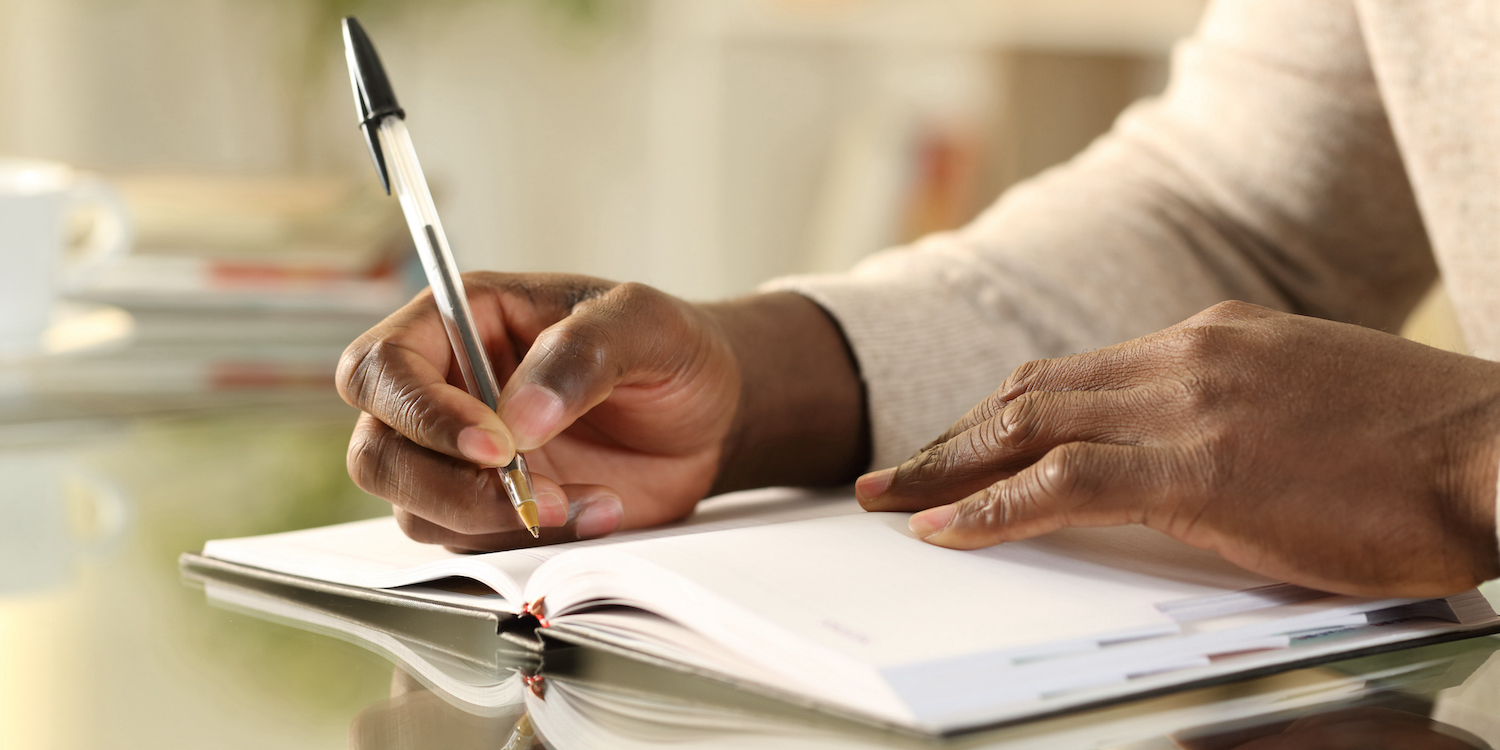
Lean on the agenda
FEATURE – This Brazilian manufacturer was able to achieve significant improvements in its processes in just one week thanks to kaizen.
Words: Claudio Marcelo Macedo and João Marcos Linares
In just five days, as part of their second Kaizen Week, Tilibra, a manufacturer of notebooks and personal organizers, achieved improvements of over 50% in several business indicators, including the number of defects, the fulfilment of the production plan and OEE.
Here are some of the results they achieved:
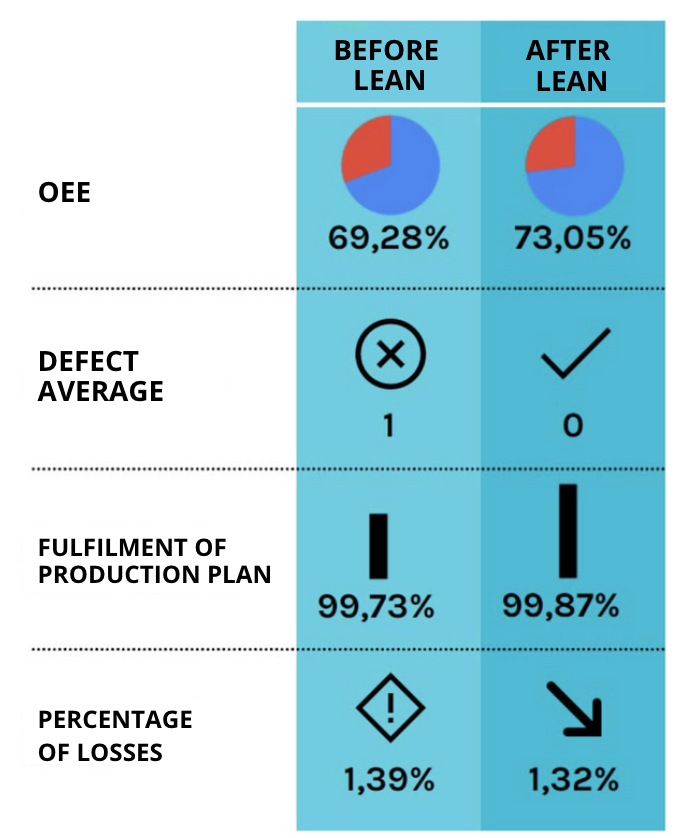
All of these results had a direct impact on the flow of production, reducing the number of equipment stoppages and operator’s idle time, on safety and on the quality of the products. This was possible because of the engagement of the participants in the development of a Value Stream Map, which was used to identify the main obstacles in the process and the opportunities for improvement they generated. Such improvements were aligned with the action plan that was executed during the Kaizen Week. Over the course of the five days, 71 suggestions were made – tackling improvements in equipment, process, quality, 5S and planning – and 52 were immediately implemented.
Tilibra operates in a market niche that is extremely seasonal: the demand for notebooks and personal organizers is not very high between March and November, but it grows esponentially at the end and at the beginning of the year, during the transition between school years. The company wants to be ready for such seasonality, so that it can meet the spike in the demand that comes every year. They, therefore, looked for alternatives – both cultural and technical – that would help them move away from push production model and better serve their customers. Lean Thinking soon appeared as the best management model.
For its first stint into Lean Thinking, Tilibra familiazed itself with the concept of “lean office” – that is, the application of lean in administrative environments. The President of the company was, from the very beginning, very enthusiastic about the prospect of using lean in Tilibra’s administrative departments. However, they decided to start with a pilot in the manufacturing area, with the idea of learning more about the principles to then apply them in the office.
They wanted to reach maturity in their manufacturing operations first. So, they organized two Kaizen Weeks: the first one was a pilot kaizen, the positive outcomes of which were enough to galvanize the organization and encourage it to dive into the second stage with confidence. That second Kaizen Week was testament to the maturity that the organization has been able to reach after just a few months working with lean: it was smoother than the first one and it led to the impressive results we mentioned above.
So, here are a few tips and lessons learned that Tilibra would like to share with the Lean Community, on how to make a Kaizen Week a success.
Tip #1: A Kaizen Week calls for discipline
To run a Kaizen Week requires the complete dedication and engagement of all participants. It is vital that everyone focuses on the objectives defined in the A3, actively taking part in the discussions about countermeasures and in their implementation. Of course, this means people need to be open to the change that will follow the improvements. A good gauge of engagement during the Kaizen Week is the ability of the team to stick to the agenda: are we carrying out actions in line with what we planned for? Are we respecting the timeline we set? Answer these questions to ensure you are making the most of your Kaizen Week.
Tip #2: It all starts with leadership
A precondition of engagement is leadership spearheading the initiative. Without the active participation of leaders and their effort to bring everyone on board, involvement of front-line staff will be limited. Leaders are responsible not only for the planning of the week, but also for sharing the results achieved during the Week. Everyone in the organization needs to be made aware that a Kaizen Week is taking place!
Tip #3: The secret is objectivity
Simplicity is the essence of Lean Thinking and, by extension, of a Kaizen Week. Many times, our improvement efforts get stuck in needlessly complex actions and bogged down by bureaucratic issues. Theis hinders the improvement work and, more often than not, prevents us from achieving the results we are hoping for. What makes a Kaizen Week a success is its objectivity. When you are presenting improvements or changes we want to make, always try to be as direct as you can, making it clear to everyone what needs to be done and when. And don’t forget that using more images and less words is the way to make things easier to understand and implement.
Tip #4: The Kaizen Week reflects your lean culture
You can’t see a Kaizen Week simply as a few days of improvement. It is so much more than that! Working for a whole week with a focus on kaizen has to be a unique experience that promotes a complete immersion in lean culture. This way, it’s possible to ensure that more improvements take place and more projects are initiated in different areas of a business in the future – such is the promise of yokoten. Don’t forget: the foundation of lean lies in thinking before acting and in going to see. A Kaizen Week should happen with minimum investment and maximum participation. Practice “trystorming”, work hard and get your hands dirty.
Tip #5: Have fun!
At the end of the day, people need to have fun during a Kaizen Week. They need to be able to forget about their personal problems, leaving behind smartphones and emails, and truly connect with the work and with their colleagues. If the Kaizen Week feels like a burden to them, like something they have to do, something is going wrong. Create a positive environment so that people can be happy throughout the week, celebrate every result that is achieved, and get to a point where they can’t wait for the next kaizen week to happen.
KEEP ON LEARNING
Tilibra has organized two Kaizen Weeks to date. Even though the first one had already been a great success, the second one really showed great progress. They learned the importance of teamwork: together, they looked at 71 problems and came up with countermeasures to try and solve them, something that no one could do on their own. In the end, 73% of the counter-actions devised were implemented, 94% of which required a relatively small effort (an Impact Effort Matrix was used to identify them). They also learned the importance of planning, sharing and engage people in the week-.ong activities.
They divided the week into three stages: on Day 1, they provided some basic training to people and asked them to start looking for potential improvements; on Day 2 to Day 4, the improvements were carried out at the gemba; finally, on Day 5, the achievement of the week were celebrated. All departments (production, maintenance, operational efficiency, warehouse and planning & production control) were involved, and the whole initiative was completed at a very low expense.
To live with the problems and then learn to see them through the Value Stream Map gave the Tilibra team a clear idea of the processes and facilitated the identification of more problems, thus guaranteeing a better alignment along the value chain. Finally, they managed to carry out these actions without bureaucracy, embracing the true kaizen spirit. To run a Kaizen Week means more than just doing improvement; it means to take a deep dive into a new culture that has continuous improvement at its core.
THE AUTHORS
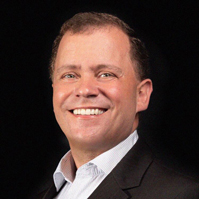
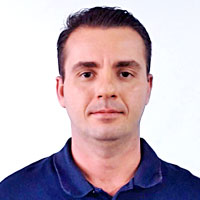
Read more
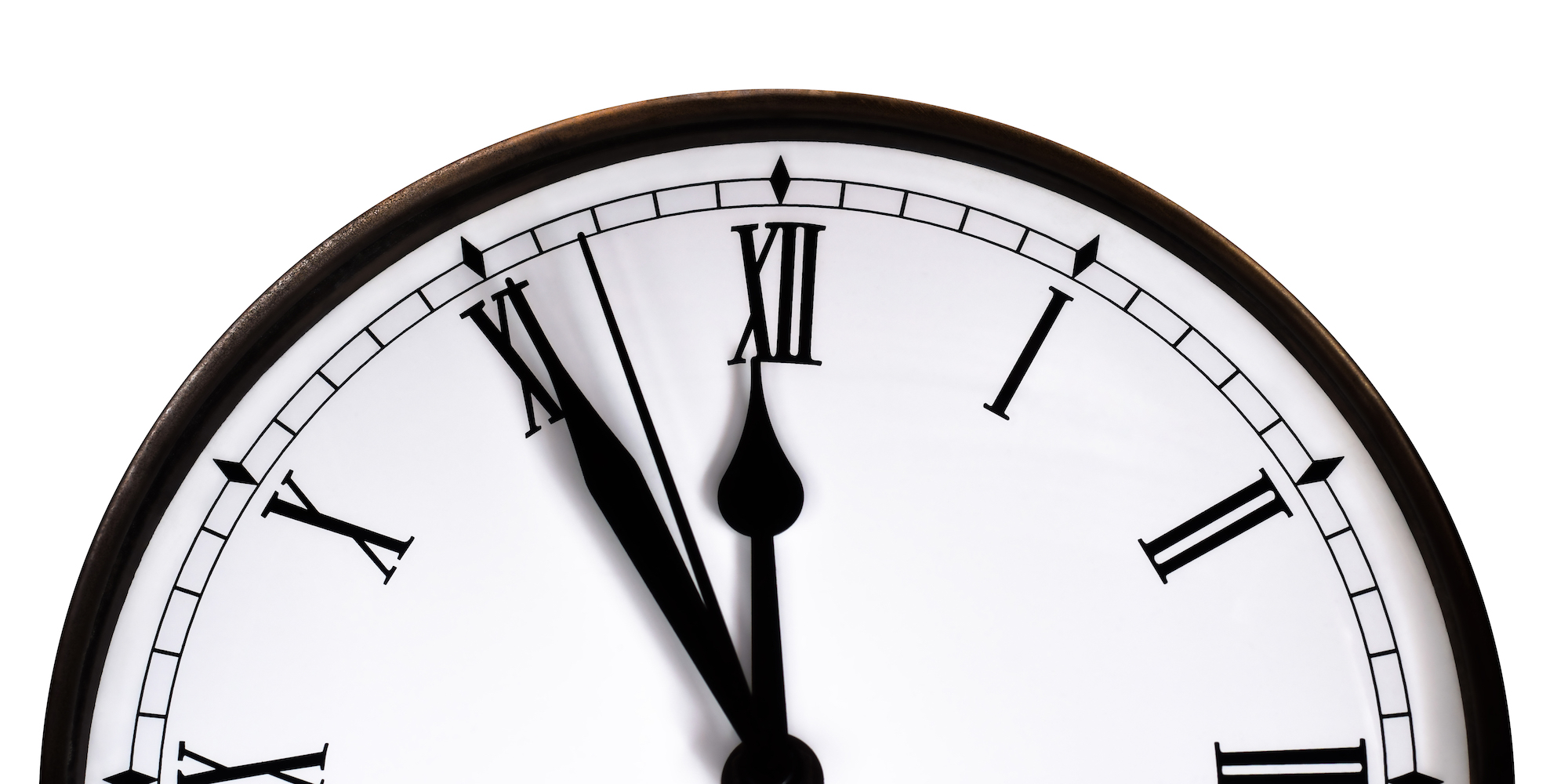
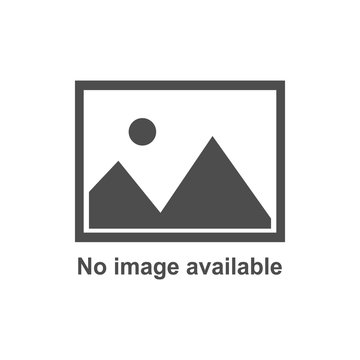
FEATURE – Freeing up beds is an age-old problem for hospitals. The medical area of this Catalan hospital group has found in lean a creative way to solve it.
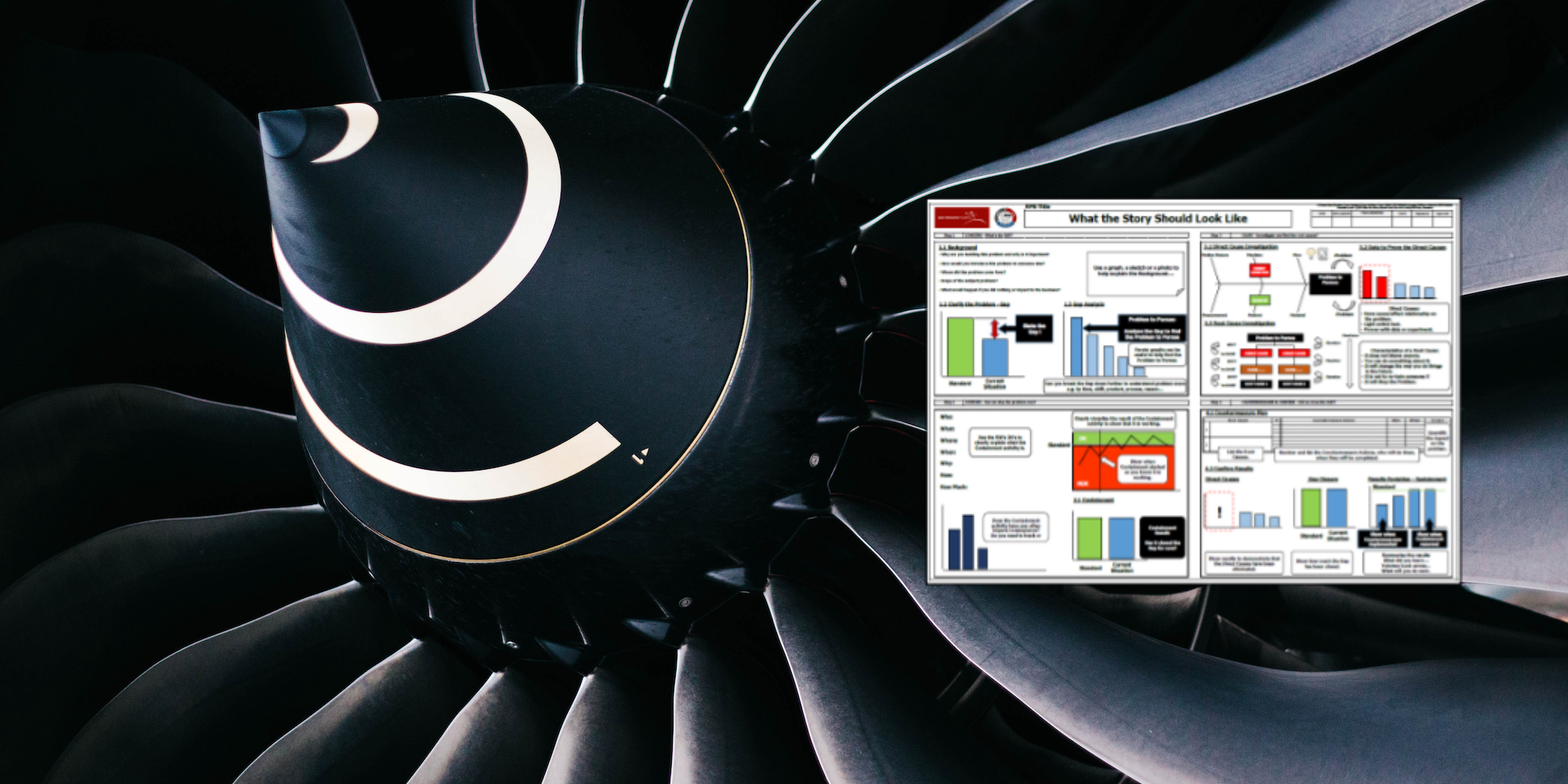
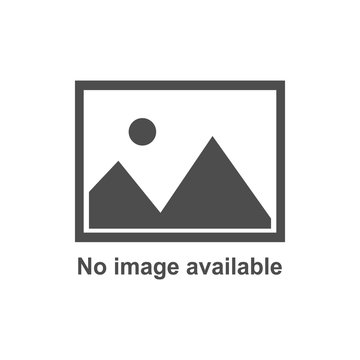
INTERVIEW – From hospitals to start-ups, lean principles have been applied far beyond their origins at Toyota. This article discusses how lean can be applied to learning – specifically, how we can apply lean learning to learning lean.
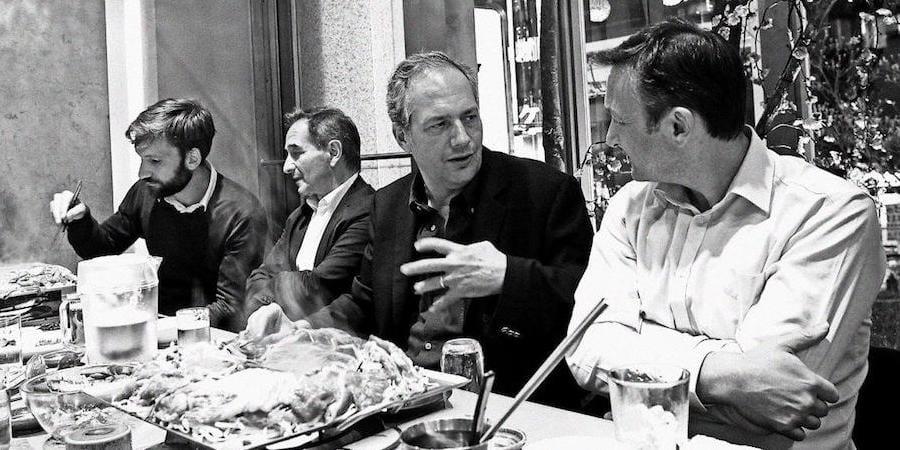
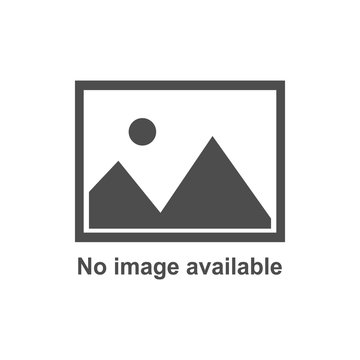
FEATURE – Following a visit to a Toyota supplier in Japan, the authors reflect on the nature of kaizen and explain why we might be looking for it in the wrong place.
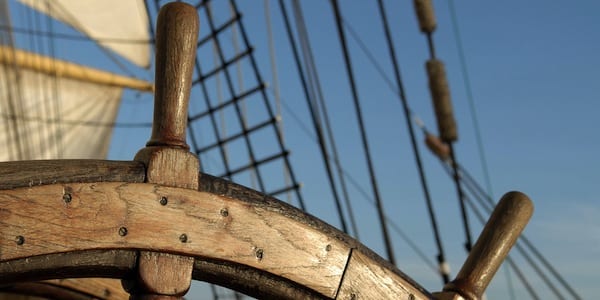
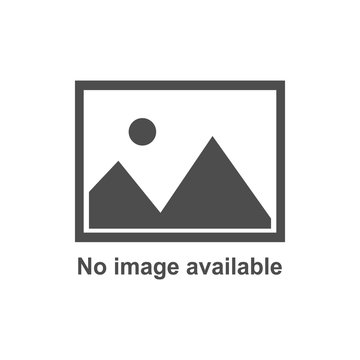
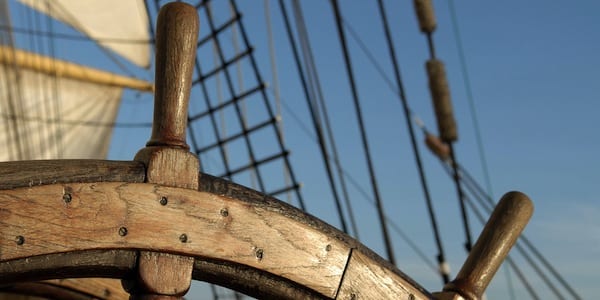
FEATURE - We are often told that employee resistance to change is natural, but it’s really just the result of a wrong approach to lean thinking. Learn to effectively engage people and change will follow.