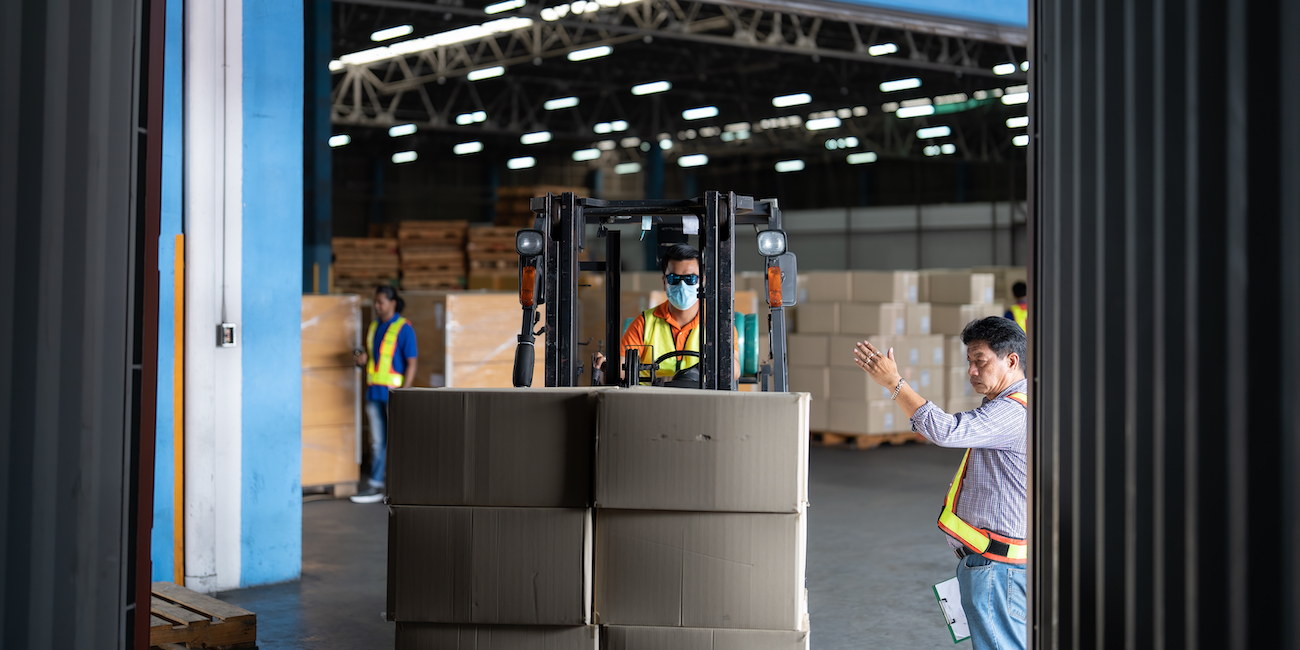
Why is it essential to plan in logistics?
FEATURE – There is more to logistics than an ancillary process that supports the rest of the company. But then, why do we never have a plan for it, like we do for manufacturing?
Words: Ágnes Antal, Lean Coach
In a production environment, it is obvious that manufacturing activities are planned. Typically, there is a monthly, weekly, daily, shift, and even hourly production plan. This minutely determines what will be produced, when and by which machine, and what the expected output is.
But what about logistics? Incoming shipments are generally pretty easy predict (unless there’s a traffic jam or a truck breaks down), but collection is almost always unpredictable. Usually, we do not know what needs to be picked, how much, or for whom. Planning in this kind of environment is difficult and, therefore, not very common.
But a plan is still essential! Why? Because having a plan is the only way to identify deviations from, well… the very plan. It sounds quite paradoxical, I know. Yet, in my experience, having a plan is the foundation of all work organization.
WHAT’S THE PROBLEM?
Let's look at an example. At one of our partner companies, we observed and studied the picking of small parts with similar parameters. The goal was to increase efficiency, specifically the order lines/hour metric.
The analysis of the current situation revealed that, although the number of lines to be picked varied daily, there was a noticeable pattern or trend concerning the days of the week and the month. This made it largely possible to know what to expect on Mondays or Wednesdays, for example, as well as at the beginning, middle, or end of the month.
OBSERVATIONS
The picking lists were distributed to employees on a “first come, first served” basis, which occasionally led to disputes. The work organization involved relatively large buffers around the completion of tasks and an average performance was determined (even though it was known which employees typically picked faster and which picked lower, who was precise, and so on). This could result in employees pacing their work and filling the time available to them.
EXPERIMENTS AND SOLUTION
After numerous measurements and observations, we managed to create a plan that, based on the number of lines and the pickers’ speeds (considering several other factors), accurately estimated the working time required for the different picking lists. This allowed shift leaders to know exactly when each list would be completed (e.g., ready for dispatch) and when an employee could start the next task.
Surprisingly, the experiments revealed that things were not as they seemed ("I told you so!"). Of course, there will always be deviations. No two lists have the same work content, no two days are the same, no two people are the same. We are not machines operating at the push of a button. However, whether the deviation is half an hour or only five minutes matters greatly – a half-hour deviation clearly indicating that something is wrong.
Why is this useful? Because knowing this means that the team can react immediately. They can quickly investigate what happened. Did the employee encounter a difficulty? Did they have to solve a problem? Or was this list simply different, for example, with a larger quantity per line? With short reaction times, plans can be adjusted, and assistance provided. The delay is not discovered hours later – or, worse, at the end of the shift – and immediate intervention is possible.
Due to this newly developed visibility, the work became more predictable, and the organization of the work became more accurate. The “leftover” half or full hours no longer disappeared. As a side effect, the hostilities ceased, because the shift leader now assigns the picking lists to everyone in advance.
CONCLUSION
It’s important to understand that logistics serves production, customers, and indeed the whole company, but that it is more than an ancillary process. Seeing it like this and just expecting it to deliver can severely complicate your attempts at planning logistics.
But fear not, as it’s always possible to do it. There are always patterns and trends to highlight and recognize. If we identify them and create a plan around them, we will enable high-level utilization of our capacity and minimize our reaction time for interventions. So, why is a plan essential in a logistics environment as well? Because that means we can “safely” deviate from it and get back to the right track in no time.
This article is also available in Hungarian here.
THE AUTHOR
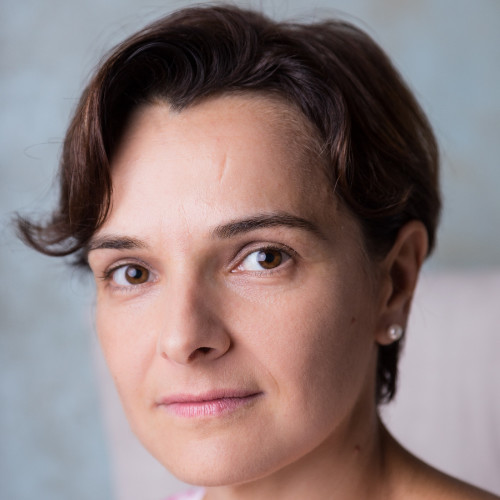
Read more
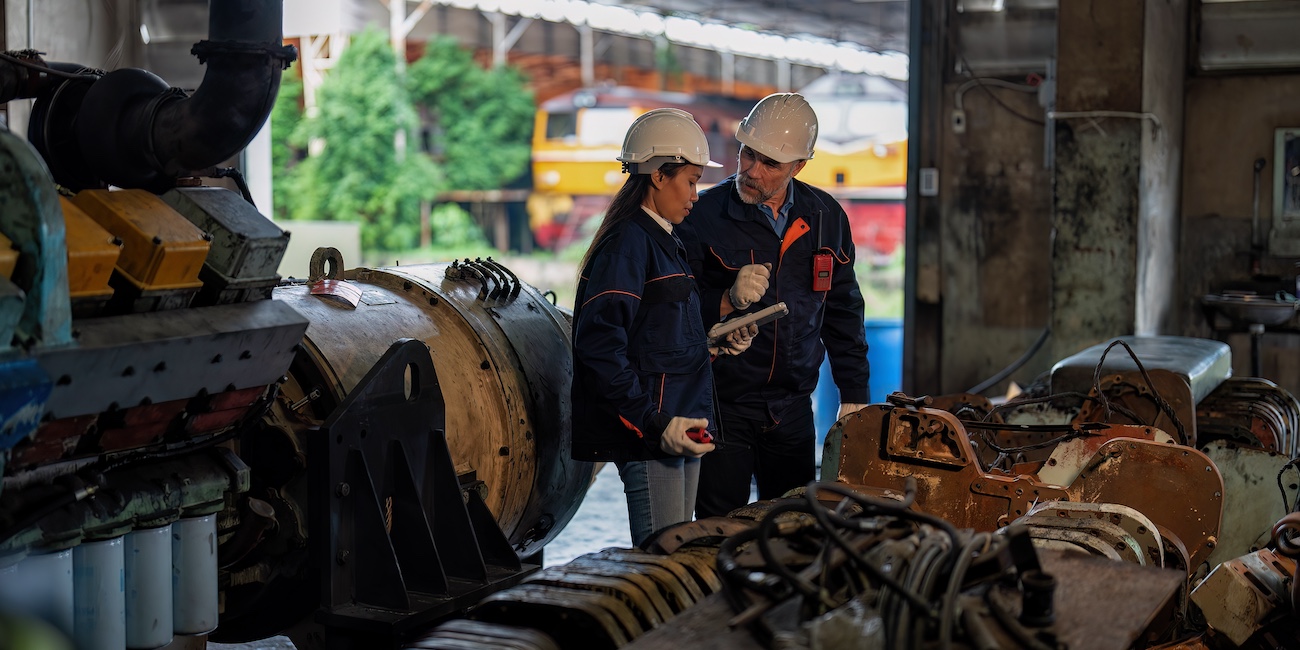
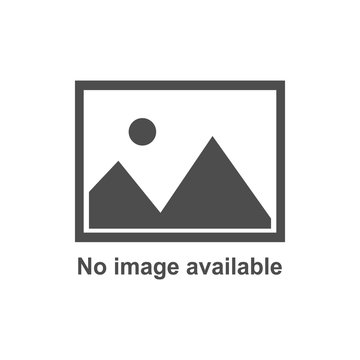
FEATURE – To accelerate learning and change, don’t copy blindly—observe, adapt, and apply with purpose. That’s how yokoten drives real transformation, argues the author.
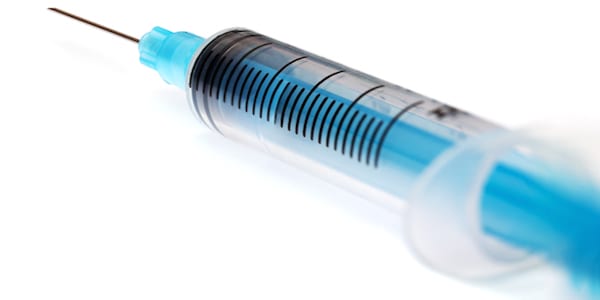
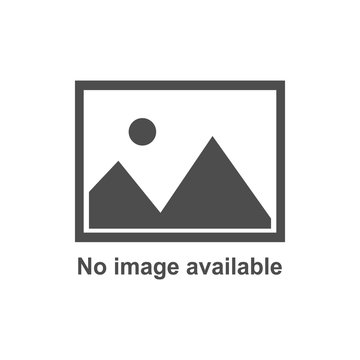
FEATURE – Menlo Innovations has proved there is a different, more "joyful" way of running a software development company – could those same lessons be applied to the healthcare industry?
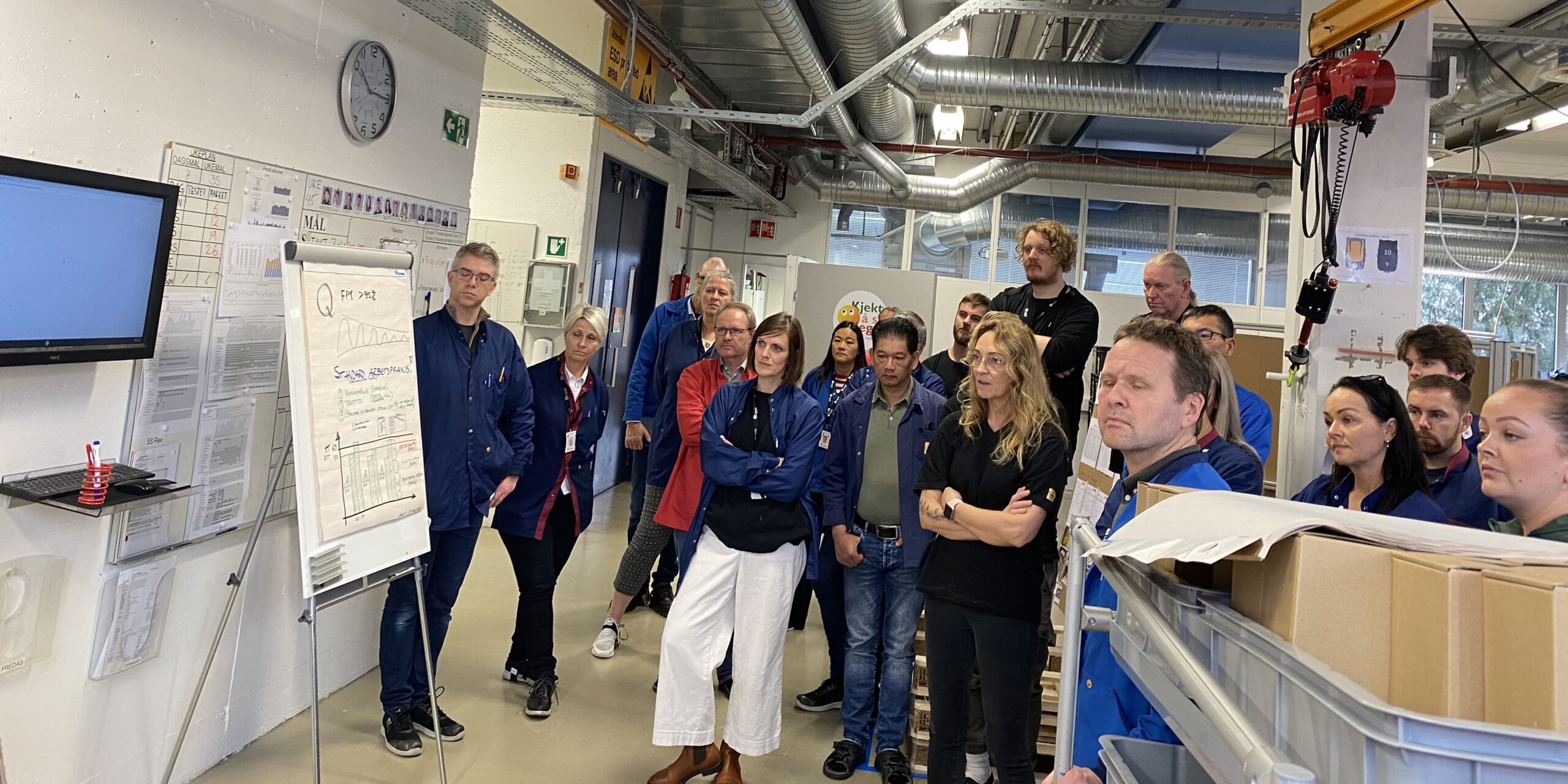
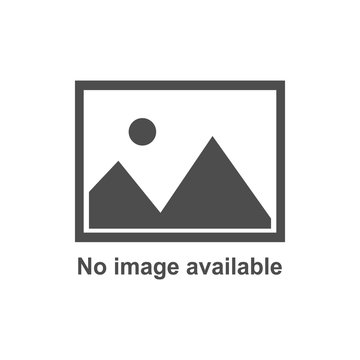
FEATURE – How Lærdal Medical was able to enthusiastically restart its lean journey with help of a good old-fashioned Kaizen Week.
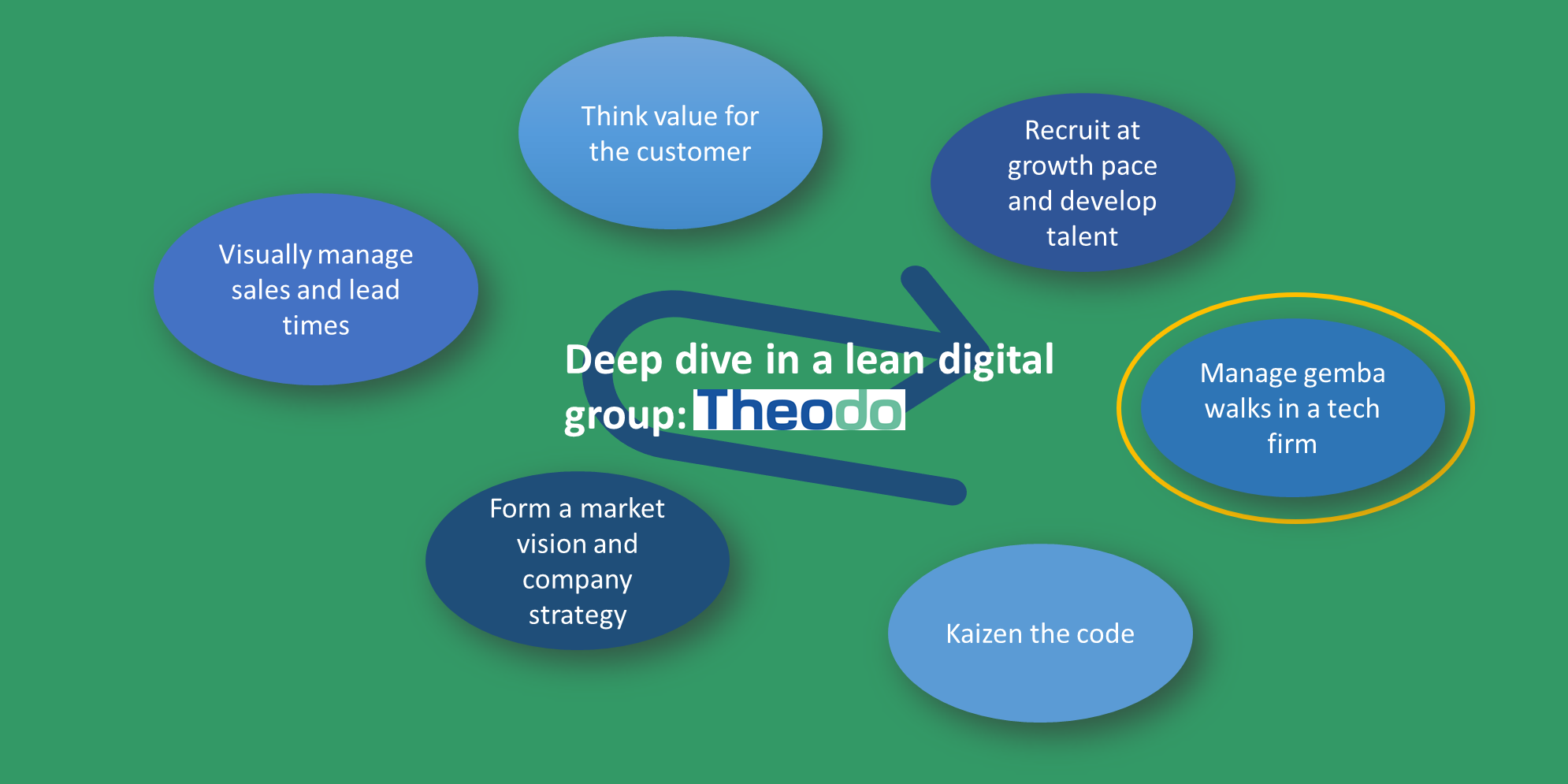
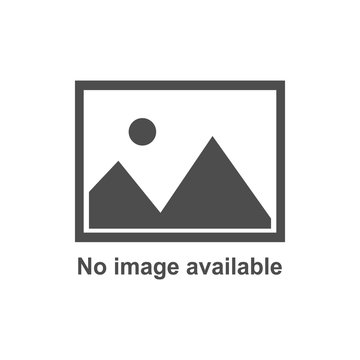
FEATURE – This month, the author learns how gemba walks happen in a digital environment, where the work and information are typically hidden in computers.
Read more
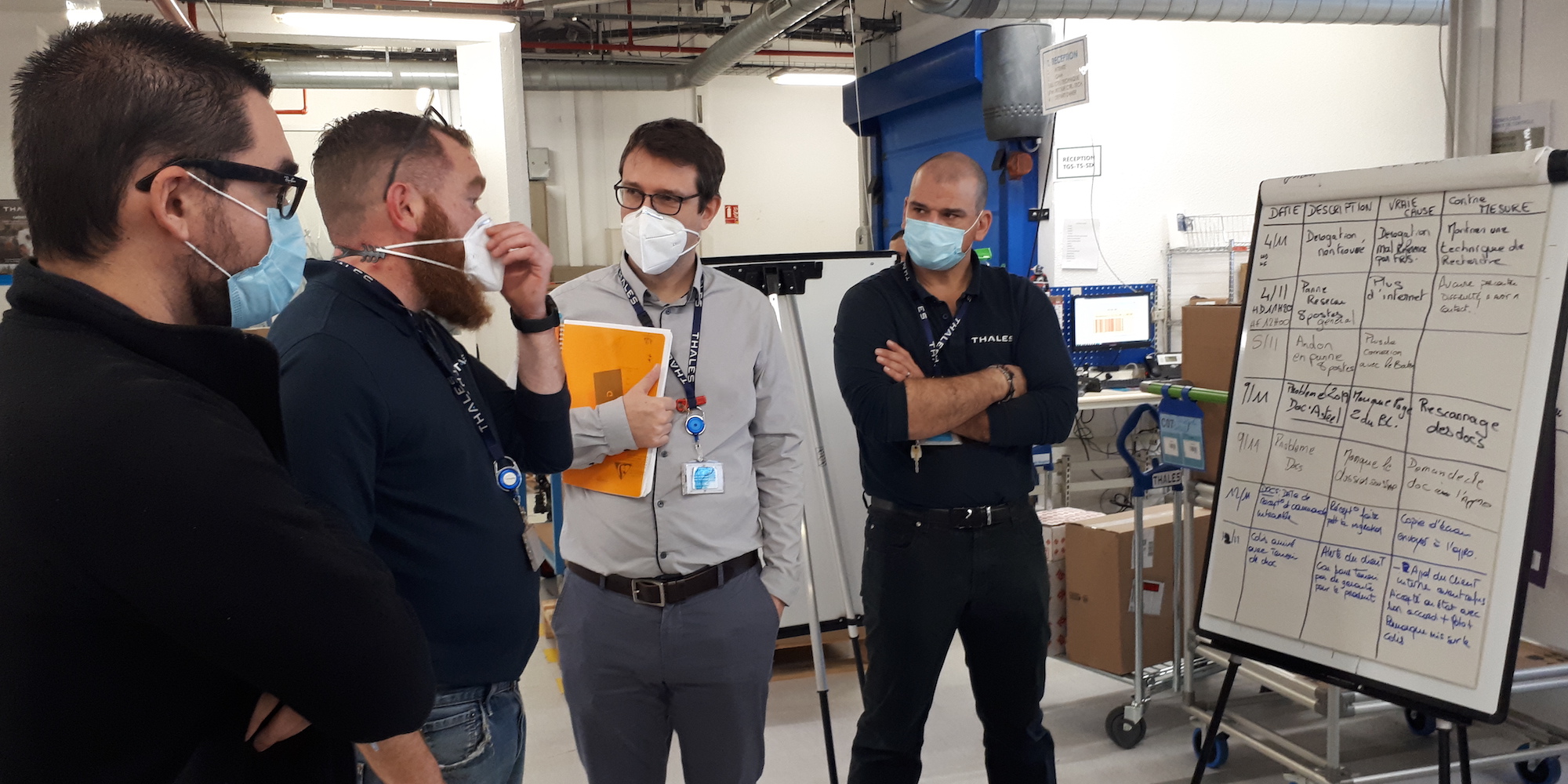
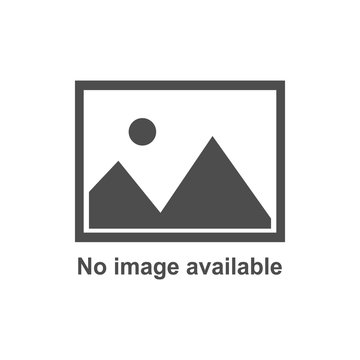
NOTES FROM THE GEMBA – Thanks to the effective application of Just-in-time and Jidoka, Thales LAS has managed to turn around its logistics department. Catherine Chabiron reports.
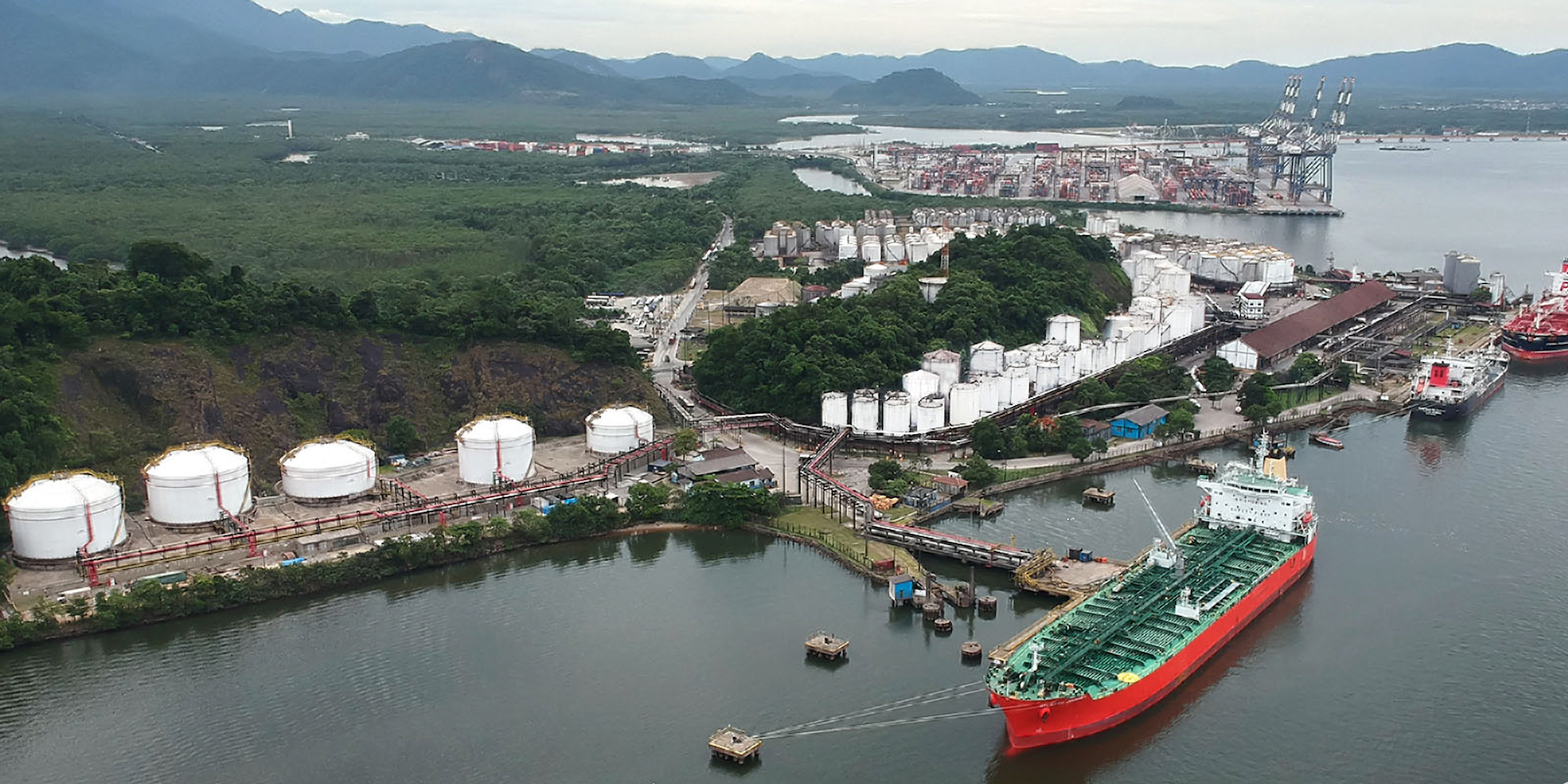
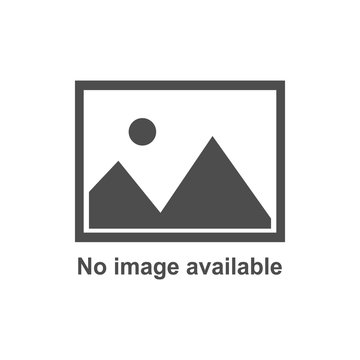
CASE STUDY – Logistics can be the key to achieving success and creating a competitive advantage in a company. This case study tells the story of a port terminal in Brazil that has used lean to achieve significant gains in managing its road flow.
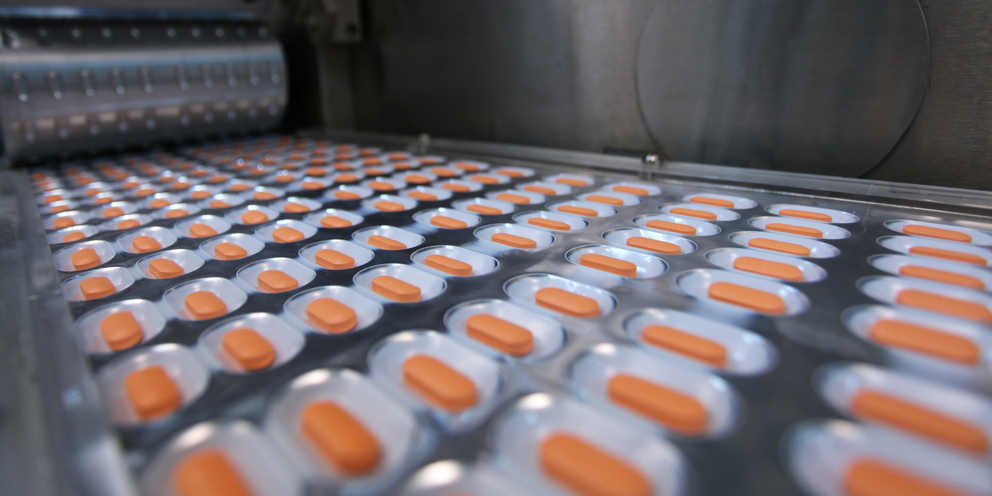
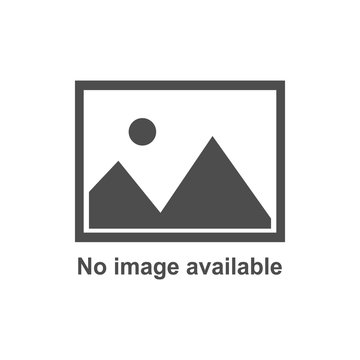
CASE STUDY – The implementation of lean in the internal logistics of a pharmaceutical company in Brazil proved key to increasing productivity and quality in the organization.
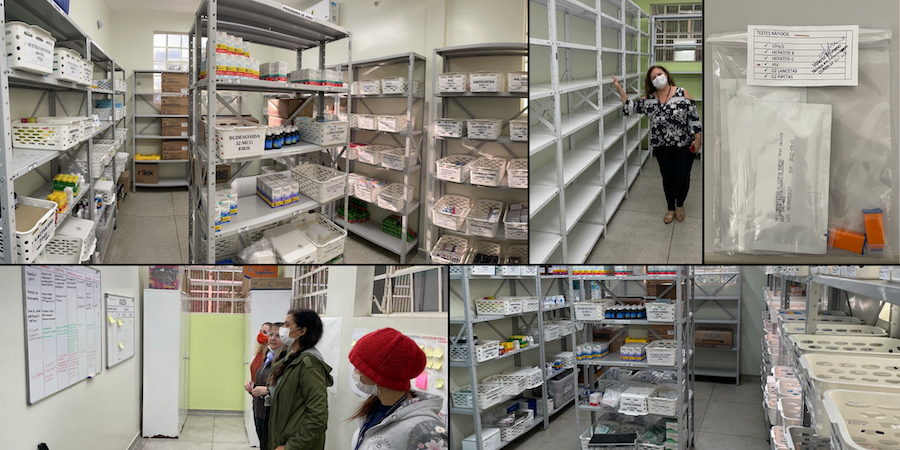
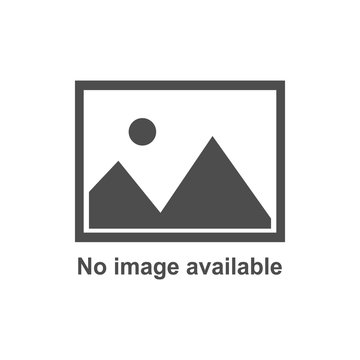
FEATURE – In this article, we hear about how the lean successes of one hospital inspired an entire healthcare authority to introduce changes to their processes.