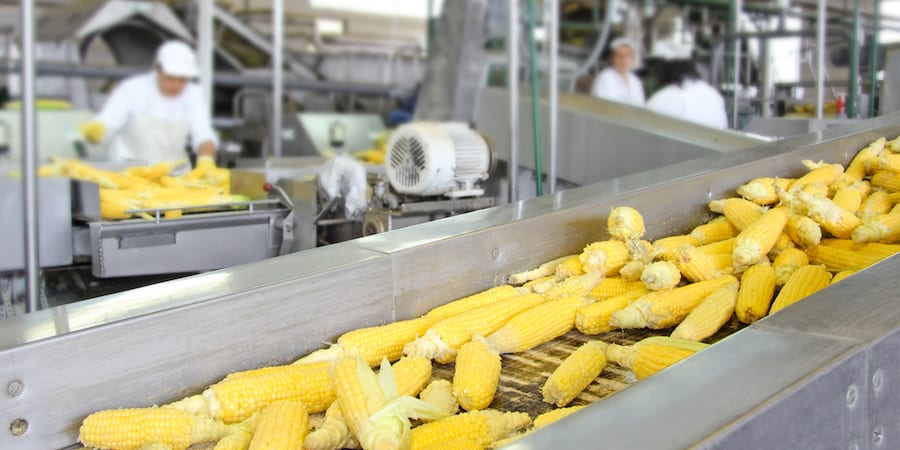
Dedicated green and red equipment for different products
FEATURE – If we have high-volume (green) and low-volume (red) items in our production schedule, doesn’t it make sense to also have dedicated green and red equipment whenever possible?
Words: Ian Glenday, lean coach and author
A previous article introduced the analysis tool called the Glenday Sieve, which separates products into different coloured categories. The two most important colours are green and red as, at the end of the analysis, all products are classed as either green or red. Greens are a small number of the biggest-volume items that run to a fixed (usually weekly) schedule over 6 to 8 cycles and therefore repetitive. Reds are a lot, often quite a lot, of small-volume items that are scheduled for production when required, and are therefore flexible.
In my work supporting organizations, I have learned it’s important to try to have dedicated green and red equipment in the factory, as much as possible. When there are two types of equipment, we began to realize there was another aspect of levelled production we needed to consider that we had previously overseen. One site manager in a firm I worked with summed it up neatly when he said, “We need green and red people”.
He explained that the green and red equipment needed people with different skills, aptitude and even personality. Green equipment required the individuals running it to be naturally neat and tidy, to focus on keeping to the right standards and settings, to like routines and to keep making little improvements to the work. In contrast, red equipment running many different products with a new plan every week that was often changed needed the best fire fighters in the house – people who could react quickly, relished a challenge and got on with whatever was thrown at them. This applied not just to operators but also to engineers and maintenance teams. It all made perfect sense: put the right people in the right place and performance will improve on both green and red equipment.
Of course, what needed to improve in each case was different. Green priority was getting better and better hourly output rates, with little to no quality issues and waste, which in turn meant inventories could be substantially reduced. Red priority was all about flexibility and responsiveness to demand changes, but still with little to no wastage and quality problems. The two types of equipment had also different targets in the KPIs for things like efficiency and lost time to changeovers. This idea made levelled production even more effective in improving performance.
It is not always possible to have dedicated green and red equipment, even though it is not as hard as some think. During my five-day workshops on the rapid implementation of levelled production, one of the first things I like to do is going for a gemba walk and looking for a large shed or sometimes a taped-off area of a warehouse. If I am lucky, what I find is old equipment that still works but has been replaced by newer, faster machines. This equipment may not be good enough for the greens anymore, but it is still perfect for the reds (generally, it is slower, easier to changeover and to maintain). A new task for the workshop participants appears then: to get the equipment up and running again to make the reds.
At this point we have two types of equipment running, which has a double benefit. Firstly, dedicated green and red machines are suitable for each product group. Secondly, removing the reds means that the green equipment runs more smoothly, with fewer changeovers, and that it will be easier to agree on standards and settings for the green items. Word of caution: now there is likely to be spare capacity on the faster lines, which will lead people – usually those working in the accounting department – to suggest moving the reds back to the green equipment. Their reasoning is that the product costing seems better than in the scenario in which they are produced on slower lines. But it isn’t so, because moving back the reds will actually cause lower efficiencies for the greens: by having more products on the lines, more changeovers with different set-ups are likely to damage the overall performance of the equipment and increase the number of breakdowns. Whenever possible, I recommend to stick to dedicated green and red equipment – even when there is spare capacity on higher speed lines.
GREEN AND BEIGE PEOPLE
Here’s an example of how the Managing Director of the company I mentioned took visual management to a whole new level, which shows the importance of putting the right people in the right place.
The company, a manufacturer of hydraulic pipes and couplings, produced 2,000 SKUs with a 48-hour lead-time to customers, something they were finding increasingly costly and hard to achieve with consistency. The Glenday Sieve analysis showed that over 50% of sales were coming from a mere 92 products, 5% of the company’s portfolio. The other products were ordered infrequently in small quantities, even as single items.
Armed with this information, the MD decided he needed two types of factory, a high-volume repetitive facility and a flexible jobbing shop. It was not cost effective to build two factories or even possible to physically separate the equipment inside the existing factory building, so it quickly became clear the company would have to find another way. They worked out what equipment would be needed for the high-volume green items in a fixed cycle, and the staff required. They then painted that equipment green, and gave all employees working with those machines green overalls. The remaining equipment was painted beige, with beige overalls for the employees (not sure why they went for beige instead of red).
Although the equipment and staff were totally intermingled on the shop floor, each “business” operated in a totally different way. The “green factory” had fixed hours of work, JIT deliveries of materials and improvement activities focused on achieving faster cycle times and increased productivity. The “beige factory” had variable hours according to the level of work needed each week based on the variable demand of the small sellers, purchasing materials only when required and running improvement activities focused on flexibility and responsiveness. Product costing was based on the different actual costs incurred in the green and beige factory: very similar products had quite different costs depending on whether they were a green or beige SKU. This didn’t necessarily translate into different selling prices for customers, but it certainly helped the business to get a much more accurate understanding of the real margins – and therefore to make informed decisions.
Effectively, the organization had created two businesses with many separate policies, procedures and measures. The definitions of added value, flow and waste were also completely different. Although on paper the “beige” factory looked like a more expensive way to make products than the “green” factory, the reality is that it achieved the flexibility required to meet customer service without causing short-term plan changes and the disruptive fire fighting that had impacted the green products in the past. It enabled green products to be made in a totally fixed and repetitive cycle, achieving higher levels of efficiency and throughput and lower levels of inventory across the supply chain that were never thought possible. At the same time, the company was able to develop flexibility and responsiveness for the beige products. Separating the two “businesses” resulted in better customer service and overall increased profit margins while maintaining the product range.
Moving to levelled production is difficult for many, because it calls for a different way of thinking: a visitor to the site once congratulated the MD on what he had achieved and asked him how long it would be before all the workers in green were sufficiently trained and flexible to be given beige overalls. The MD’s response was that would never happen and the visitor should try and answer for himself why that was. Privately, he shook his head, as he knew the visitor had not understood the whole point of the change that was implemented, and that he probably never would.
This article is also available in Polish here
You can find out more about levelled production in Lean/RfS: putting the pieces together
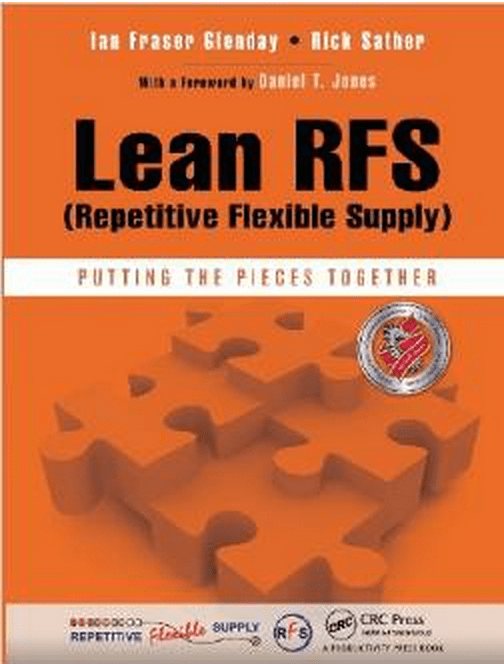
THE AUTHOR

Read more
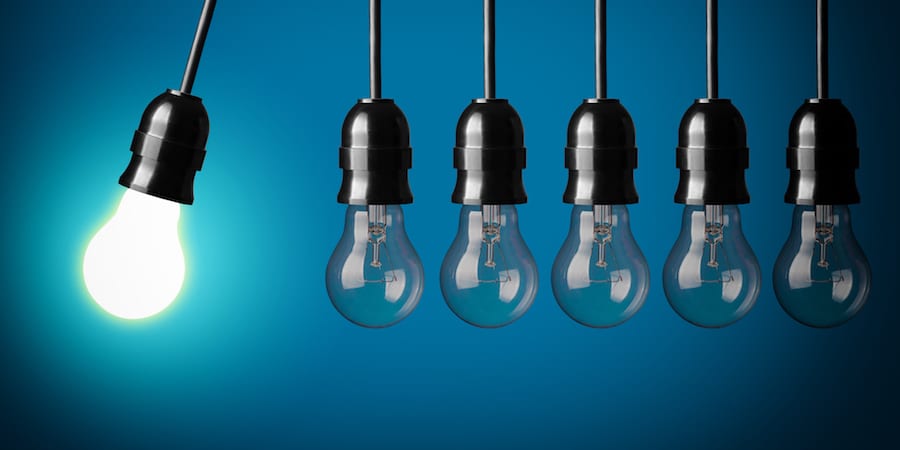
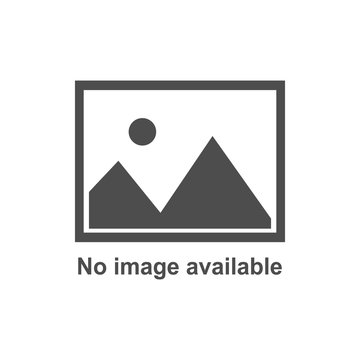
1 QUESTION, 5 ANSWERS – Because each of us has a different learning path, “a-ha moments” come to us in a variety of shapes. We asked five practitioners when their lean epiphanies happened.
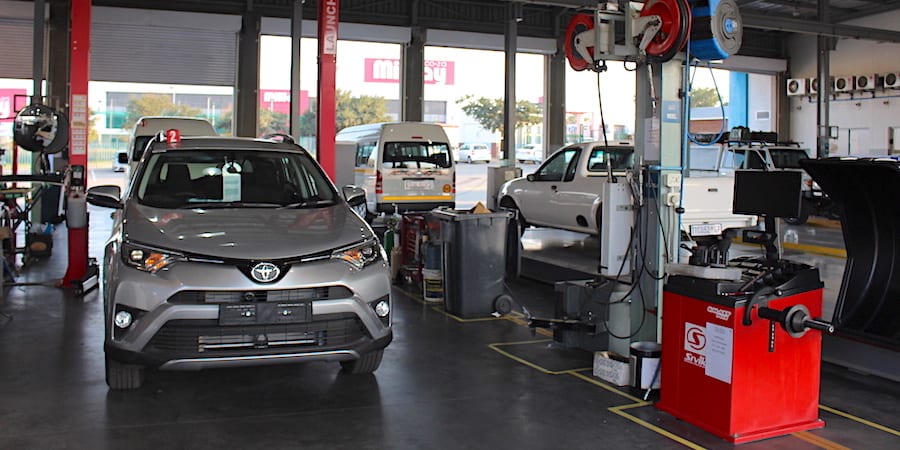
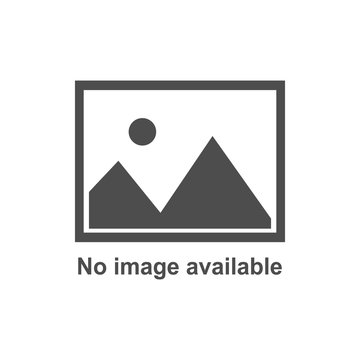
CASE STUDY – One-piece flow and a focus on lean leadership and kaizen have allowed the Halfway Production Centre in Johannesburg to turn itself around in just 14 months.
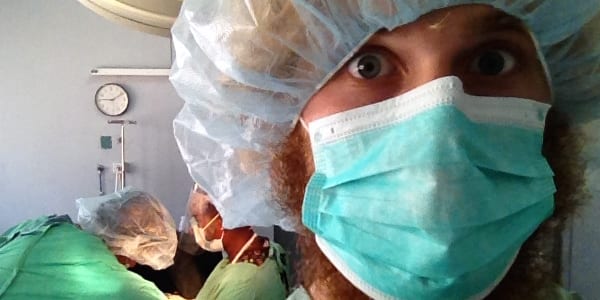
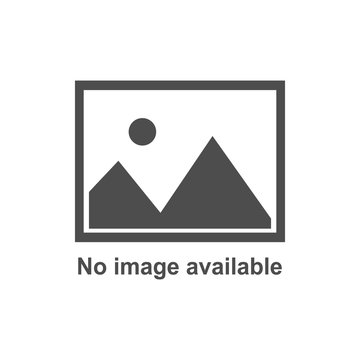
ARTICLE – While supporting the adoption of lean in a Mozambican hospital, a young engineer learned a number of valuable lessons on leadership and what it really takes to help developing countries to grow.
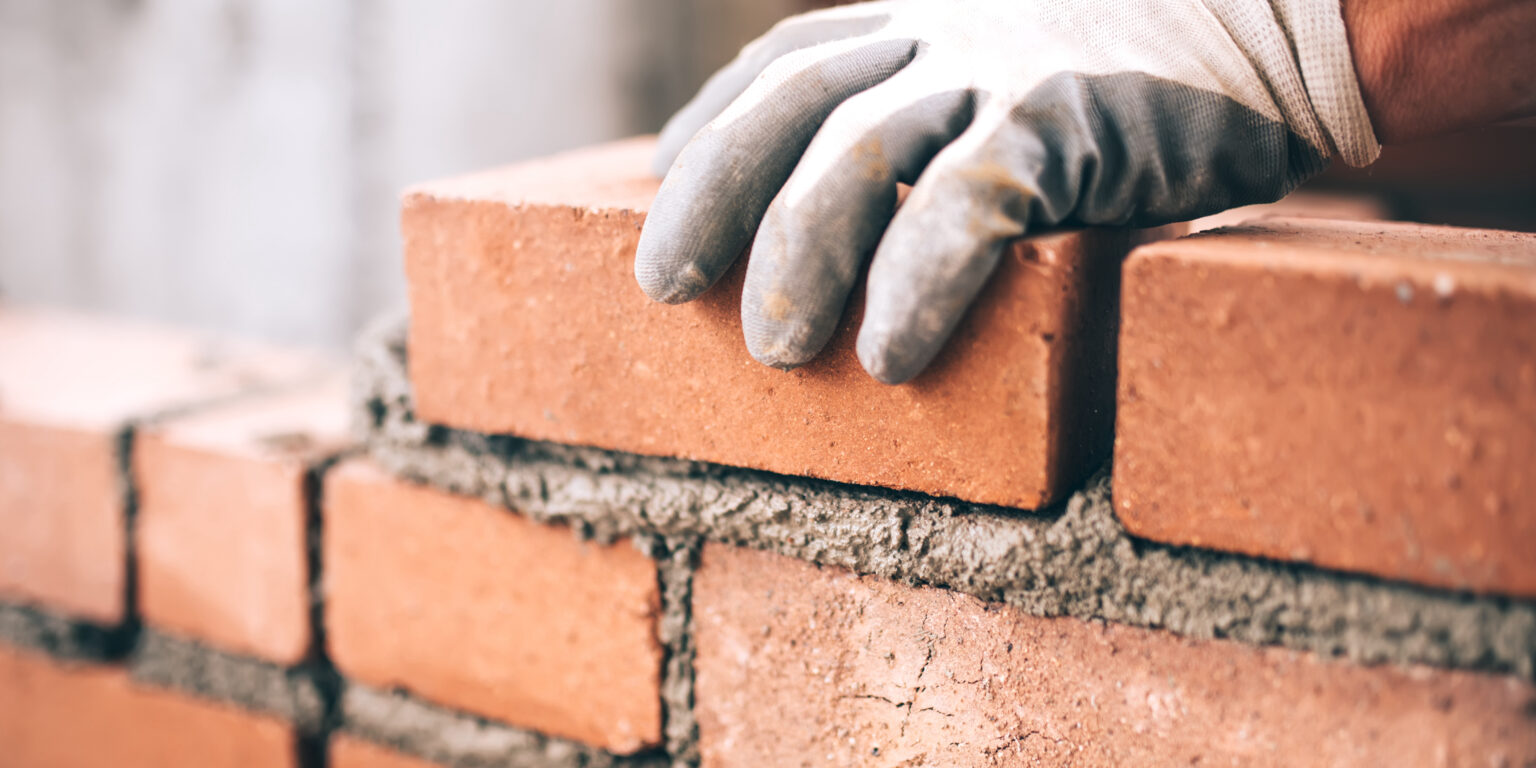
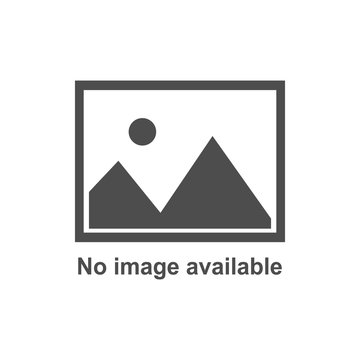
FEATURE – When we emphasize systems and roles but fail to encourage and support kaizen, we cannot expect to tap into the full potential of Lean Thinking as a cognitive revolution.