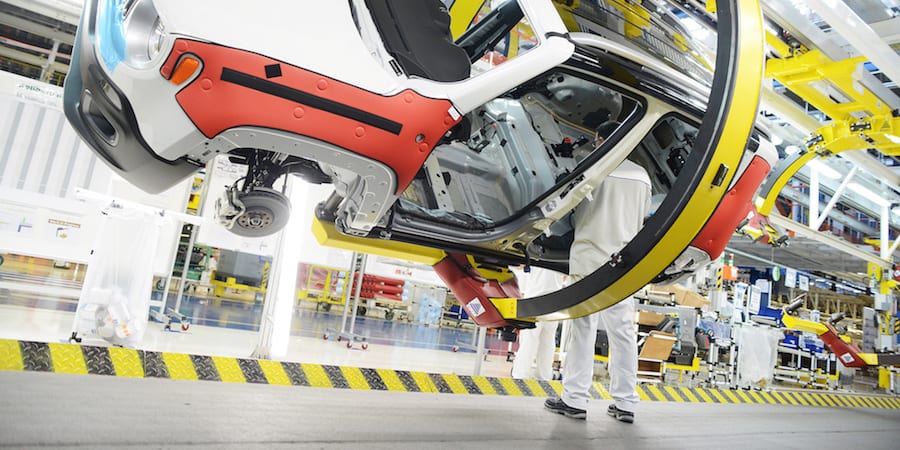
Automation and lean supply chain at FIAT Chrysler
INTERVIEW – At the recent European Lean Summit, we sat down with a senior executive from Fiat Chrysler Automobiles to learn more about the company’s World Class Manufacturing approach.
Interviewee: Luciano Massone, Head of EMEA World Class Manufacturing & Projects, Fiat Chrysler Automobiles
Roberto Priolo: When FIAT and Chrysler merged in 2009, how did management harmonize the two companies’ cultures?
Luciano Massone: It wasn’t a short process, it lasted around four years. One of the key success factors was working side by side and understanding each other. First, we created a team tasked with bringing consistency to processes, methods and tools. After that, we launched a change management program covering the cultural elements of our work. World Class Manufacturing (WCM) was, of course, one of the key programs contributing to the cultural integration of FIAT and Chrysler: speaking the same language and using the same techniques enabled us to work towards common goals and develop a common manufacturing culture. Through the WCM program we had the chance to work together on focused and profitable projects and to bring value to the company. People at all level were instrumental in delivering the necessary change. To support them in their learning, we launched the WCM Academy in Warren, Michigan, where a large number of people is exposed to WCM culture, tools and methods. Today, we can say that the integration is a success story.
RP: Fiat Chrysler Automobiles has 162 plants around the world. How do you tackle the cultural differences you encounter in different countries?
LM: That’s exactly where the managerial pillars of WCM help us: they set a series of behaviors enabling us to engage people, motivate them, reward them, and empower them to take responsibility of their own development. We believe that people development is more than just the training offered by the business – it’s also self-development and challenging yourself to grow as a person and a professional.
Our managerial principles and behaviors are common to all the cultures we work with, but teams in different countries adapt them to their own circumstances. For example, the Daily Improvement Meeting that takes place every morning has different characteristics depending on where it is set: in Italy, it happens at the beginning of the shift right on the factory floor; in the United States, it takes place during a break over a cup of coffee; in Turkey, it is something of a ritual featuring shouts and dancing, like in a rugby match, and involves intense debate and an exchange of technical opinions. This is the sort of customization we see around the world, with the improvement work being the common thread we use to bring people together to reach a shared goal.
RP: Can you tell us about the work that FCA is doing to bring its principles and way of working to its suppliers?
LM: In this journey towards excellence, we cannot allow for any weak links. Given the achievements of WCM, we decided to extend the reach its principles to our supply base, launching the World Class Suppliers program in 2010. When discussing new component sourcing with our suppliers, our aim is to create a common understanding of our respective production systems in order to maximize quality and logistics alignment.
We started by bringing the suppliers to our factories and showing them how we have transformed our shopfloors. Our hope was that this would give them an idea of what they need in order to create an improvement system of their own. Once they became aware of the fact that doing better is indeed possible, we started to make deals with them to bring similar change to their operations.
We even have an internal consulting office that supports them in their sites. Of course, our work has nothing to do with traditional consulting: we want to make sure our suppliers become autonomous in their ability to improve, and that they do so as quickly as possible. As soon as they have the internal capabilities necessary to sustain change, all we do is carry out audits to measure their growth and performance, offering education and development opportunities whenever they become necessary. This is our way of building an improvement infrastructure – aligned with our strategic WCM goals – across the entire supply chain.
RP: Waste comes in many forms – what about FCA’s commitment to minimize its impact on the environment?
LM: This is a challenge that relates to our entire process, and one that we are facing head-on. FCA’s sustainability practices help support global efforts to stimulate the transition toward a circular economy that is focused on maximizing the value and use of materials and products while minimizing waste. Keeping resources in use for as long as possible is a business practice that reduces material costs and promotes efficiency, while also helping to reduce the impact on the environment through the entire lifecycle of a product. That way, we favor a well-thought-out and balanced approach that addresses the full spectrum of opportunities. From logistics to energy consumption, from water recycling to the type of paint we use, our commitment to minimize our environmental impact is directly connected to people engagement. We need our people to be aware of and take part in our efforts to become more and more eco-friendly. That wouldn’t be possible without the improvement culture we have been able to create.
RP: You use state-of-the-art technology to support the work of your people in the plants. But how do you strike the right balance between embracing modern technologies and giving manual work the dignity it deserves?
LM: Because people are directly involved in the improvement work, most of the suggestions we get – including those related to the use of technology – come straight from the shopfloor. Through training and education, WCM creates the conditions to take and implement the ideas that people come up with. In fact, many of the digital devices (like smartwatches) that we have implemented in our sites were our people’s suggestions, rather than solutions imposed by management. Whenever our people give us sound ideas that use technology to improve the quality or safety of the work, it is our responsibility as managers to include such ideas in our digitalization effort. You won’t find any operators in our factories who are not willing to use a smartwatch, for instance, because they have been part of making that solution a reality. To us, continuous improvement is a matter of responding to the improvement suggestions our people make.
RP: Speaking of solutions, how important is it for you that they spread across your entire network of factories? How critical is cross-fertilization to FCA’s improvement work?
LM: It is absolutely critical. Remarkable results and savings stem from our ability to come up with solutions that are applicable across our operations, not just in one factory. It costs time and effort to develop them, but reusing them multiplies their value: imagine the impact of an improvement to a robot that can then be applied to, say, 1,200 other robots in 161 other factories!
We have a number of ways to ensure solutions “travel” across FCA: approved ideas become best practices (standards referring to a certain process, work station or piece of equipment) that everyone can then access online. People are encouraged to take on best practices and implement them in their own workplace: we have KPIs not only for the number of ideas a plant generates, but also on the number it implements (which includes those coming from elsewhere). In order to protect the intellectual property of our Best Practices, we have a process of systematic evaluation and patenting of the best solution in terms of effectiveness, novelty and inventiveness. Cross Projects are another very effective means to spread best practices across our plants. They address specific areas of improvement by supporting synergies between our plants, promoting continuous benchmarking, and generating new ideas through periodic workshops among our WCM specialists. An example was the Low Cost Automation Cross Project, which has succeeded in designing and implementing cheap and flexible solutions through the use of simple technology such as compressed air, electric power, gravity or springs. These applications have brought significant results, both in terms of savings and ergonomic improvements.
To be honest, however, the most effective form of cross-fertilization comes from all the people within FCA who have had their mindset changed by World Class Manufacturing and who have embraced and absorbed lean principles. Today, they are the best promoters of WCM, both inside and outside our company.
THE INTERVIEWEE
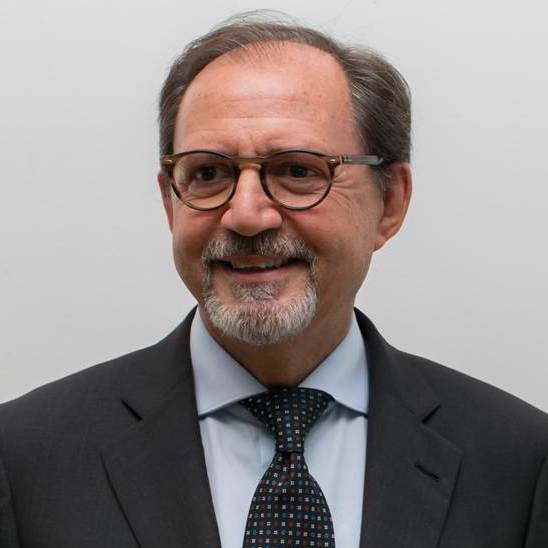
Read more
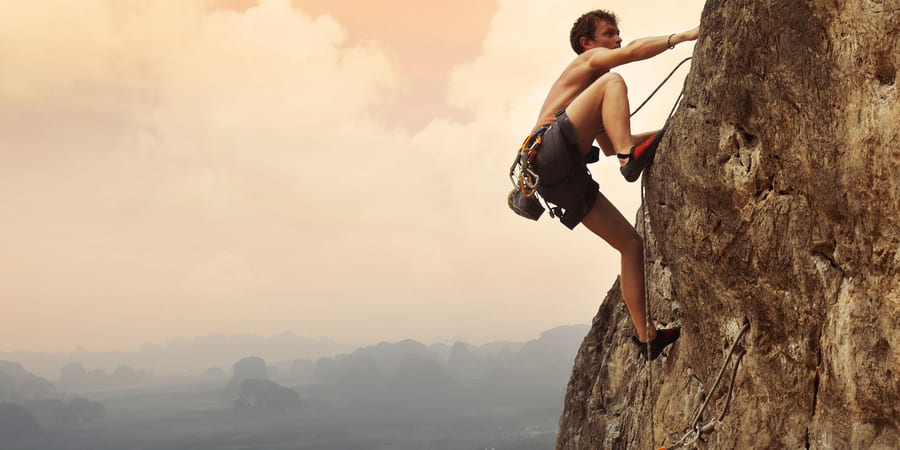
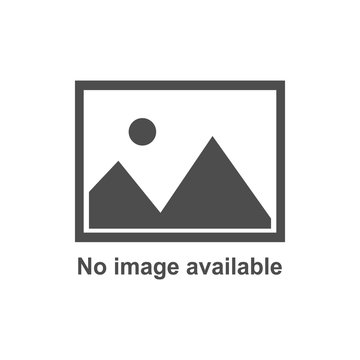
FEATURE – A lean journey often has more downs than ups, but it is a responsibility of management to persist and keep asking the right questions that will steer the firm in the right direction.
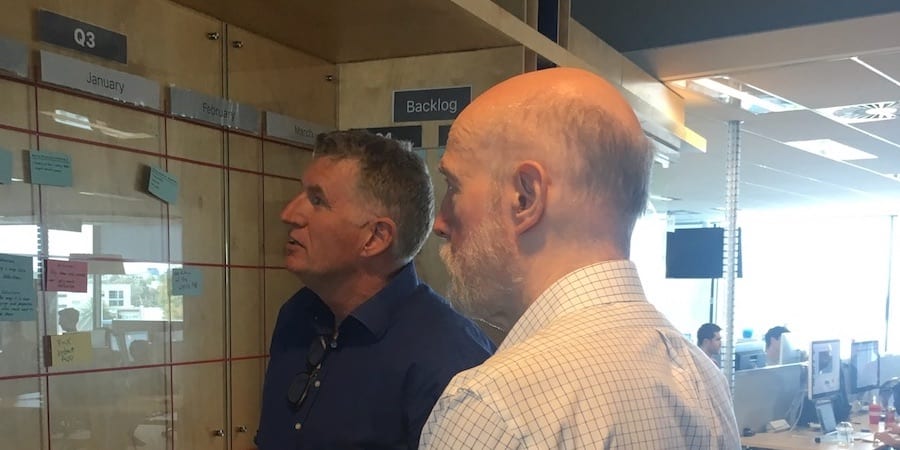
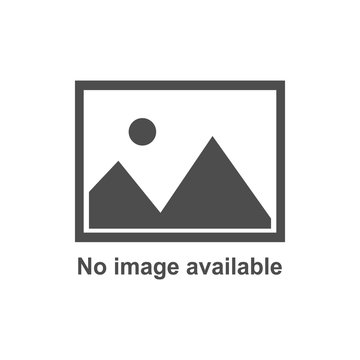
PROFILE – The leader we profile today has a holistic view of the digital world. He brought Agile to Australia, and after embracing lean thinking he has helped to make REA Group one of the country's best digital brands.
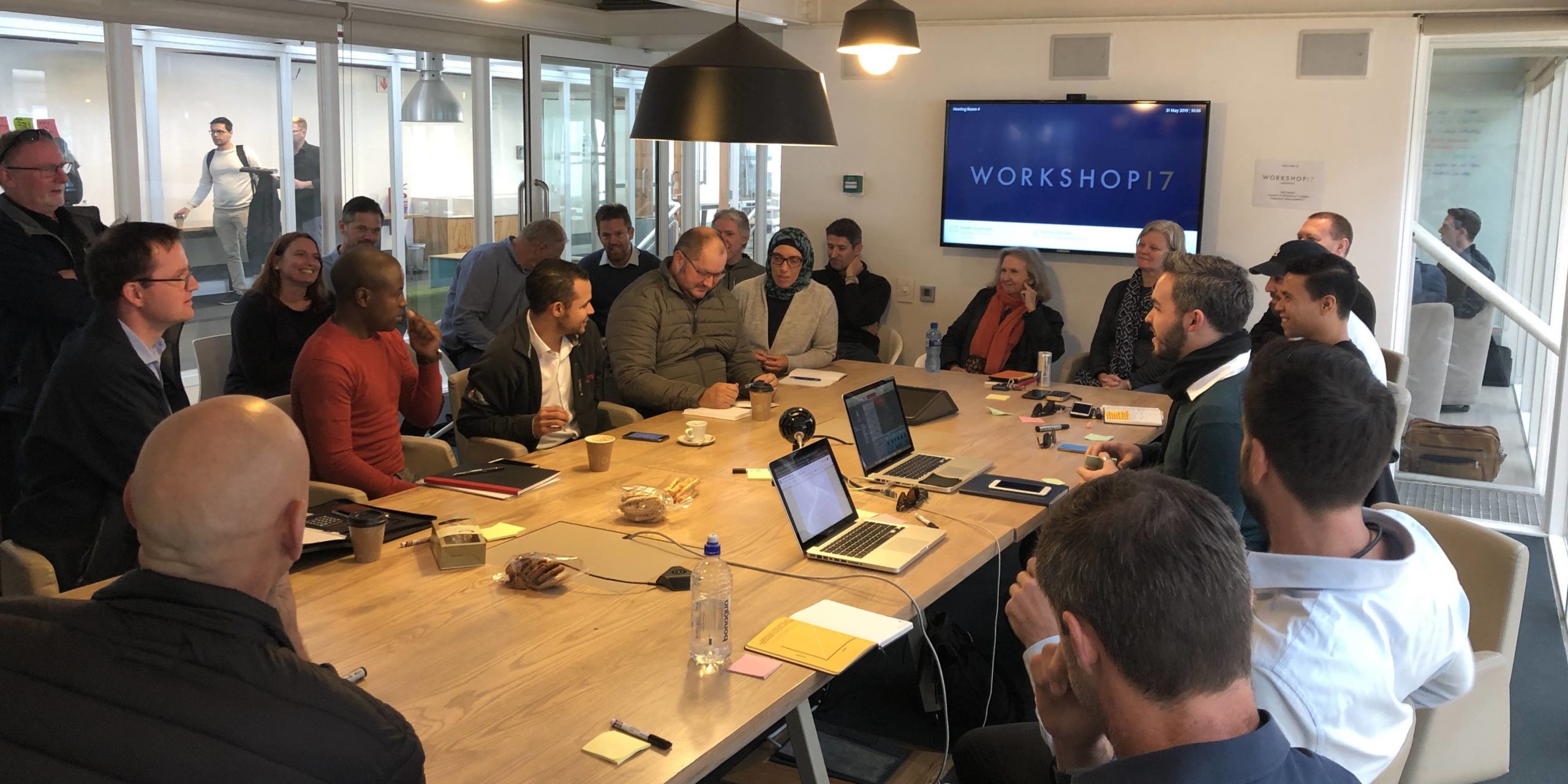
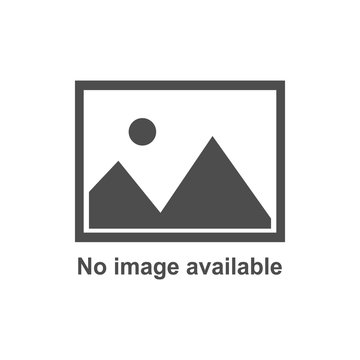
FEATURE – What started as the idea of two friends to meet up and discuss their lean journeys turned into a regular get-together of lean practitioners in the Cape Town area. Another example of the importance of sharing.
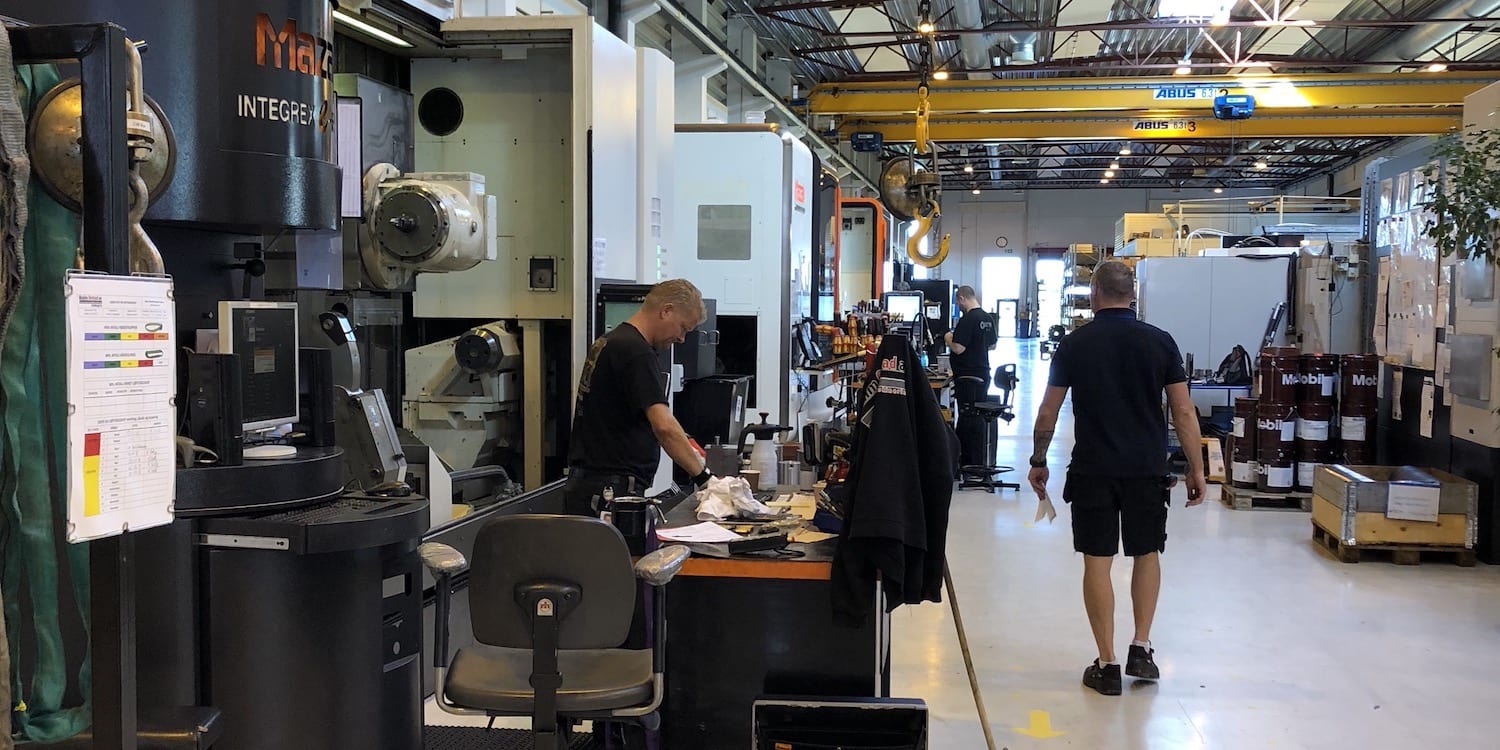
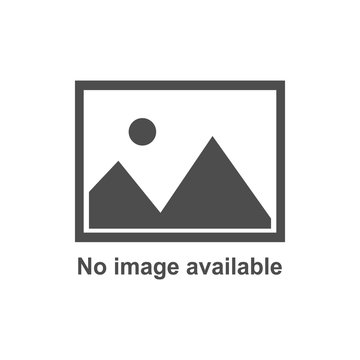
FEATURE – This Norwegian company has come back from the brink of bankruptcy by rallying its people around a common set of values, by leaning out its processes and by involving its leadership team.