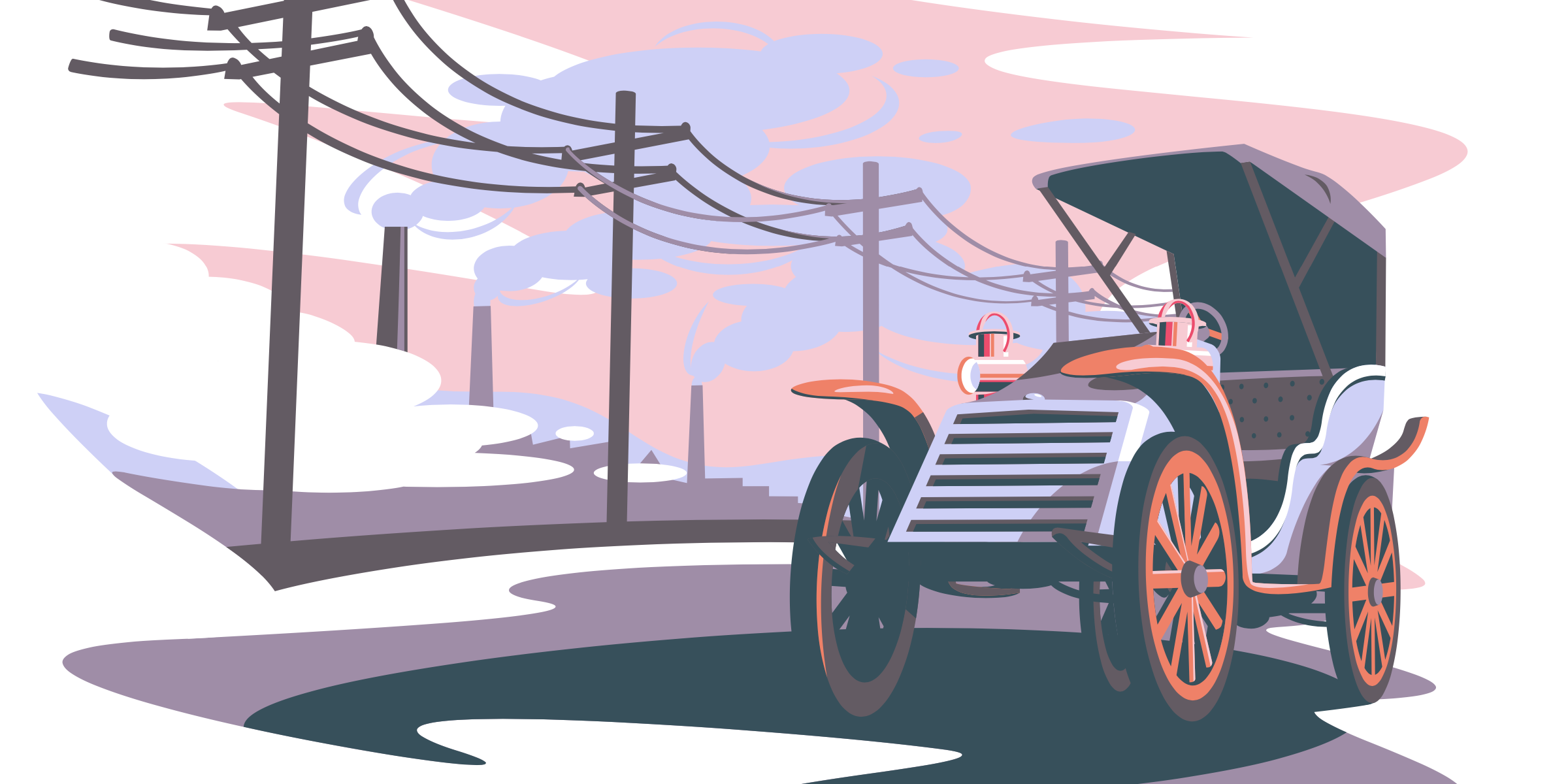
Lean through four generations
FEATURE – Every lean generation has faced challenges, and it’s critical we understand the context around us if we are to continue to grow our Community, says Jim Womack.
Words: Jim Womack, Senior Advisor, Lean Enterprise Institute
All ideas face generational challenges because knowledge increases with experience and the external world changes. Habituation effects and boredom with ideas are real. So, it’s necessary to revitalize the message in every generation on the foundation of enduring basic ideas. Lean Thinking is no different and we struggle today with the next generational change, indeed the fifth in the long history of lean through nearly a century.
The founding generation was a long one through the work of a father (Sakichi Toyoda, who contributed the idea of jidoka for his textile looms in the 1920s) and his son Kiichiro Toyoda (who in the 1930s contributed the idea of just-in-time to manage the flow of materials and information from the start of production to the end). These eventually became the two pillars of the Toyota TPS house. However, due to the chaos in the world – the Great Depression and World War II – the founding generation found it hard to progress beyond theory to actually build the house before handing off the challenge of implementation to the next generation at the time of Toyota’s financial crisis in 1950. (Kiichiro stepped down then as CEO to take the blame for the need to terminate a third of the work force in order to survive the sudden depression in Japan.)
After Toyota’s crisis, the ideas were taken up by the second generation for elaboration and deployment inside Toyota – Taiichi Ohno (TPS in production), Kenya Nakamura (the product and process development system), Shotaro Kamiya (the distribution and customer support system), and Eji Toyoda (the self-effacing genius who worked behind the scenes to create the lean management system.) They created a complete business system by the early 1970s, when Toyota’s ideas were suddenly of interest to the world due to Toyota’s superior performance during the energy and economic shocks of that era. Toyota began a rapid global expansion to eventually become the largest motor vehicle company.
The next generation, beginning in the late 1960s, invented what might be called the Toyota “missionary society” in the form of the Operations Management Consulting Division, eventually led by Fujio Cho, to rapidly spread Toyota’s ideas through its supply chain and its growing operations across the world. (This work continues inside Toyota to this day in the Operations Management Development Division and externally through Toyota TSSC in North America and by organizational units with other names in other regions.)
And then there is the long fourth generation of independent missionaries, starting with the NPS (New Production System) and Shingijitsu consultants in the 1980s as they spun out from OMCD’s lean crusade within the Toyota Group companies. These efforts carried on through the 2010s, expanding their scope to include the educational initiatives of the Lean Enterprise Institute (from 1997) and the 30 other affiliated organizations in the Lean Global Network.
In the fourth generation, lean ideas were applied to practically every activity (production, product and process development, supplier management, customer support, general management) in practically every industry, in practically every country, with extraordinary zeal and with many dramatic examples of lean leaps to a higher level of performance in specific activities. But no new “Toyotas” were created, with an entire lean business system, and the results of isolated leaps were difficult to sustain. (I just visited a company in Europe that was busy cellularizing a production process for a complex industrial component that it had used identical lean methods to cellularize 30 years earlier, at the end of the 1980s, before entirely losing the knowledge and reverting to traditional mass production.)
This long chain of generations now extends through more than 90 years, and it is daunting to think that we are really just getting started. In addition, the world has changed in important ways that create new challenges as the fourth generation approaches the end of the line. But let’s not waver: our ideas still work! They are the best way known to create more value with fewer resources by creating stability and removing waste while creating satisfying work in communities of lean practice. Thus, there is real urgency in thinking about the important work of the fifth generation now emerging as we look beyond the pandemic.
The first element in A3 thinking about a problem is to grasp the current situation, so let me fill in the first box in the upper left corner of an A3 (titled “Moving Lean Forward”) by describing the situation as I see it at the beginning of the next era of Lean Thinking.
Perhaps the most important background condition is that while our community was working to promote Lean Thinking, modern management – fully developed in the 1920s at General Motors before Toyota really got started and elaborated through the era of Jack Welch at General Electric – was proving remarkably robust. It’s a hardy perennial, replacing traditional management systems going back to the Pharaohs, that is easy to plant and able to survive many attempts at eradication – Theory Y, Total Quality Management, Six Sigma, Business Process Reengineering, team-based management – as well as wars, depressions, and pandemics! And it is taught today, usually implicitly, in business schools and corporate employee development programs across the world. Staging a frontal assault, as many lean practitioners in earlier generations attempted, has proved extremely difficult. We have found a number of leaders of modern management organizations who have been able to change their fundamental thinking and management styles to introduce lean management, but it has been hard to sustain their success as leadership is passed to the next CEO or when the business is sold.
Part of the financial success of modern management in recent decades was its willingness to ignore current employees and out-source or off-shore a growing fraction of value creation to low-wage areas in order to deal with growing cost competition. (These practices were abetted by financial systems confusing narrowly defined cost cutting with lower total cost.) Thus, the need was reduced to think seriously about new management methods that could create more value in existing organizations and develop capability in every employee. (Remember that Toyota has always taken the position that it will defend the career paths of its permanent employees over a 30-year working life. So, the company has had no choice but to continually create new capabilities in its existing work force through Lean Thinking. This always works to create the stability within organizations that makes this approach possible and effective.)
In addition, the steady arrival of new process and information technologies has held out the hope of productivity and quality advances that do not require employers to manage employees in a different way. Industry 4.0 is still largely a slogan without demonstrated benefits, but its prospect causes managers to waiver in attempting to change fundamental work processes and management methods.
Finally, the world’s perception of value-creating work has changed. As Lean Thinking entered the world in the 1920s, the prototypical human activity was the production line with tightly linked work sequences of highly repetitive tasks in massive facilities. Today, after years of advances in information technologies and a shift from an industrial to a service economy, the prototypical activity has become the seemingly self-directed work team developing a module of software in virtual environments, often to supplant traditional touch labor in other activities. While the original ideas for scrum and agile were derived directly from Lean Thinking, this fact is often lost in the post-industrial economy where managers of knowledge work often don’t know what they don’t know.
On the bright side, these expedients are now largely exhausted. The global pool of cheap labor is no longer growing while political resistance to labor arbitrage across borders is. Indeed, a good bit of the political turbulence in developed economies in recent years traces to wage stagnation or even decline among front-line value creators who are seeking to create a better division of the spoils and greater respect for their work. Employers will be forced to take these trends into account.
In addition, work as reorganized in the information age is proving to be far from satisfying for most workers, who feel the loss of community and sense of mutual obligation that are central to Lean Thinking. Thus, the great resignation and the general malaise regarding the world’s work.
As I look ahead, I believe that there will be real opportunities in the next generation to advance the cause of Lean Thinking to address these challenges. Lean is a hardy perennial as well! But these opportunities will need to be actively seized if the fifth generation of lean thinkers is not to be the last. This is the collective work of the Lean Community moving forward to fill in and act on the rest of the A3.
THE AUTHOR
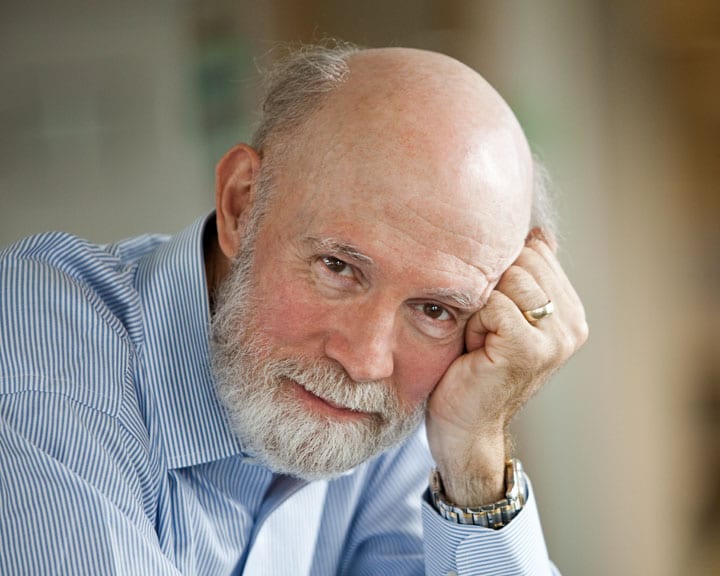
Read more
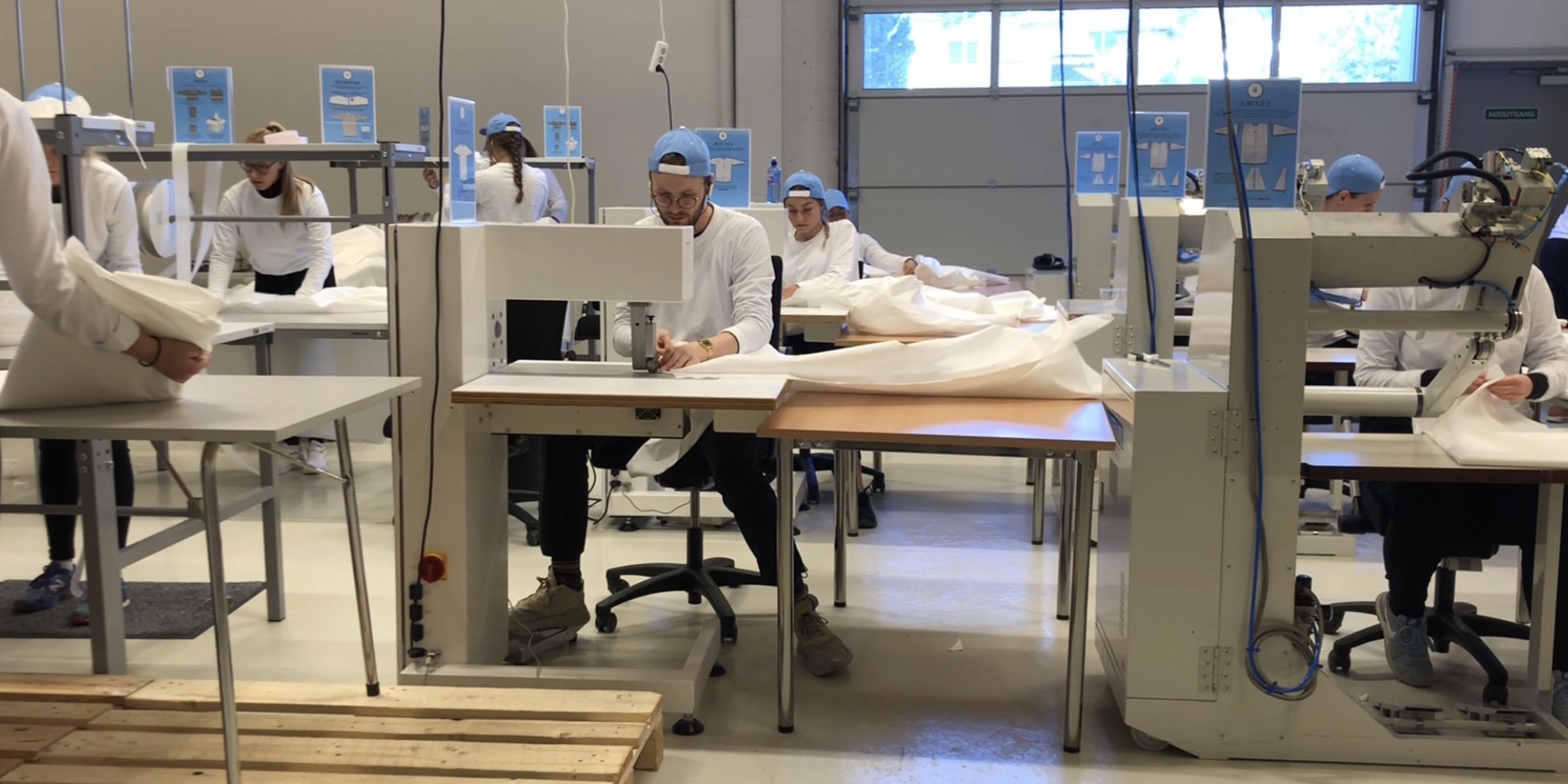
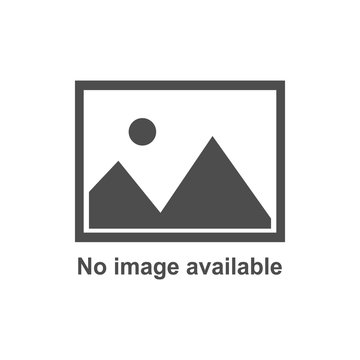
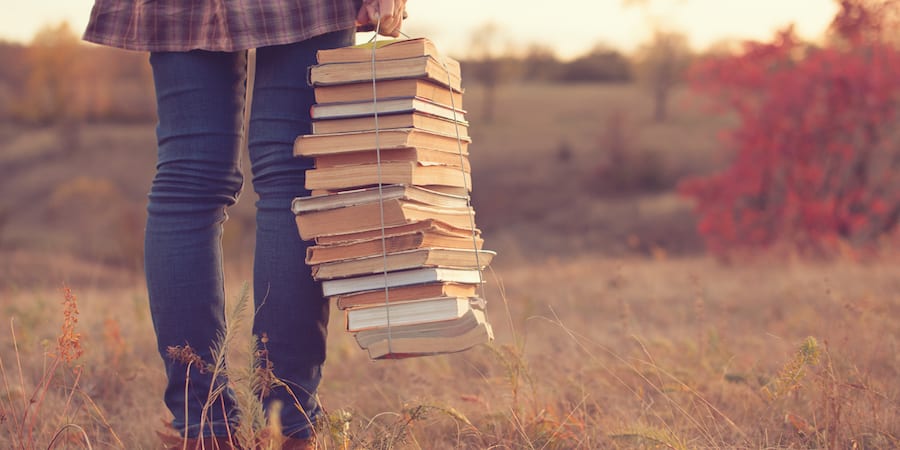
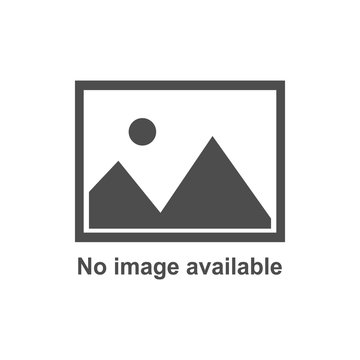
FEATURE - Effectively dealing with a problem means learning to solve it in a variety of scenarios, not perfecting a point solution. For too long in lean we have only focused on gaining reusable knowledge... but what about reusable learning?
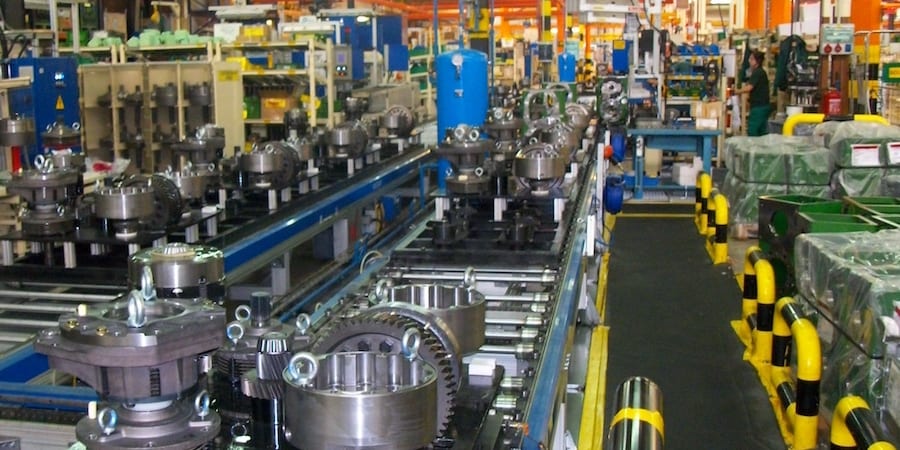
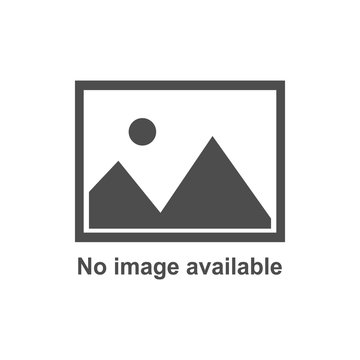
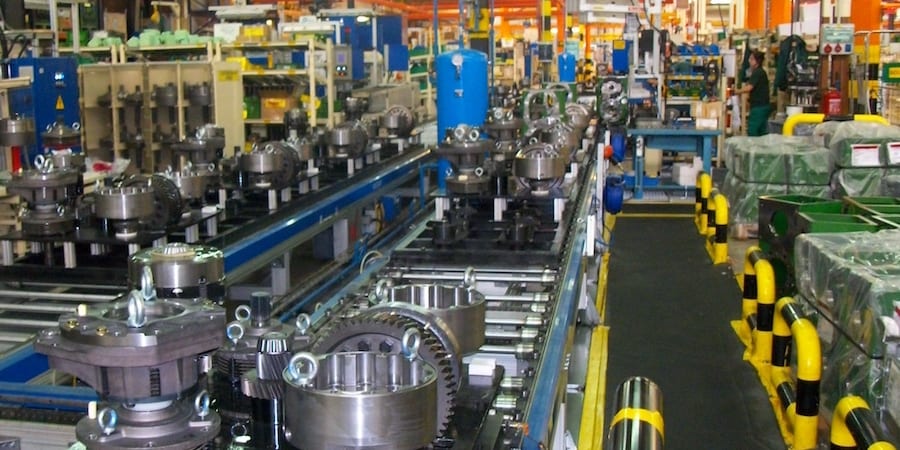
INTERVIEW – For the past year, agricultural equipment manufacturer John Deere Ibérica has worked to spread lean thinking to the supply chain. We met with them in Madrid to understand how they’re going about it.
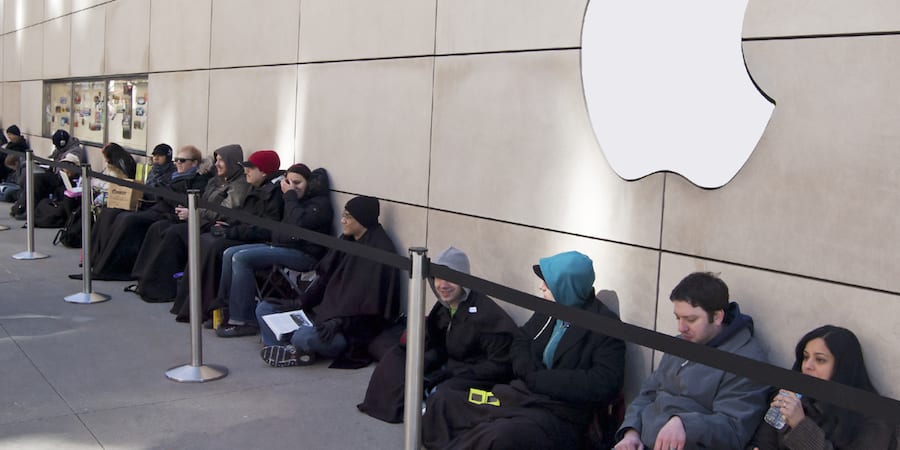
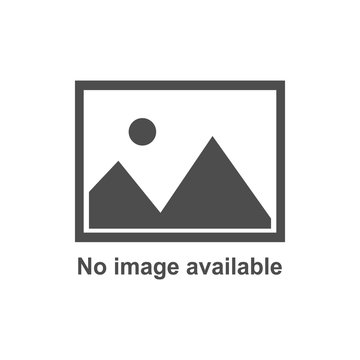
OPINION – When it comes to lean product development, it doesn’t matter whether you are making wine or motorcycles. Success comes from our ability to tell a story that engages our customers and a product they would line up for.