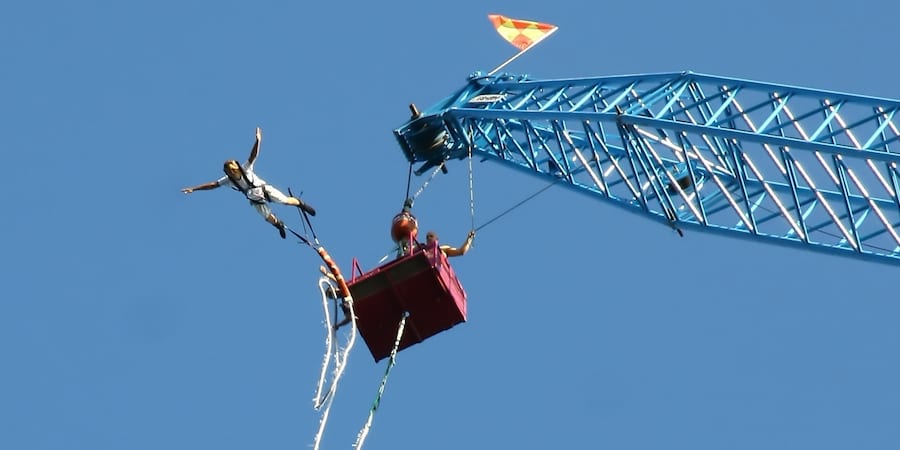
Why we should create a learning environment in our companies
COLUMN – Creating a learning environment that welcomes problems and experimentation and adapts to market changes should be our main objective. So why do we stick to obsolete ways to teach and develop people?
Words: Boaz Tamir, President, Israel Lean Enterprise
I remember the schools in which I studied as dreary places. With every year that went by, I fell more in love with learning but grew increasingly skeptical about the people responsible for teaching me. Sadly, many companies I observe closely resemble the schools I attended.
I have learned to not trust those teachers (and managers) who preach, call themselves "gurus", or start sentences with "Without a doubt". Only a very small number of teachers and educators showed me there is a different approach to education, and I have spent every moment since trying to discover their secret.
It was only years later, when I first encountered lean and its principles, that I found a way to guide and facilitate learning without dictating it from above (and without pontificating).
According to lean, the role of a teacher (sensei) or manager is, first and foremost, to create a learning environment that encourages experimentation, with an emphasis on adapting to the specific circumstances of the learner and the organization. Good managers, therefore, provide their workers with the tools they need to cope with problems autonomously, using their experience and judgment – from the first, simple set of questions defining the problem through to the understanding of the root causes of the problem and the brief experiments used to find potential solutions.
Lean thinking also opposes traditional management, which is based on a learning method that sees the worker (the learner) as just one element in the manufacture of a product. Who hasn't heard the ideal organization being described as "a well-oiled machine"? It's not our fault, really: we have all been taught to think like this – a result of the industrial revolution mindset and of decades of mass production – and our schools are still very much married to this idea. So are people development efforts in traditional organizations.
In fact, we have become so accustomed to this approach that we haven't noticed how, as the times changed, it became obsolete. So, why do we stick to archaic teaching and training models when technology is enabling everything else in our lives to fit the exact needs of the user? Shouldn't the same flexibility we strive to build in our software, services and products be included in the way we teach people, both in schools and in organizations?
Lean thinking suggests we replace hierarchy with flexibility and openness, as we try to find the right balance between individual development and organizational culture and language. It's about time we all embraced this view.
We might be in the age of artificial intelligence and robots, but it is still human beings who provide the strongest foundation for organizational innovation and flexibility. That's why learning is at the heart of every lean organization and an essential requirement in showing those firms that are not lean yet how to adapt to ever-changing market conditions.
To foster a culture of learning, however, we must facilitate dialogue in our business and make personal mentoring and a worker's freedom to act true staples of our organizational culture. As a lean facilitator, I have discovered how strong a temptation it is to provide ready-made expert-on-the-shelf solutions to people. If only it were that easy! A useful answer to a problem must be connected to the existing situation and based on the experience and current needs of the workers on the field. It must be tailored to the circumstances of the here and now. The only basic thinking that allows for such solutions to be consistently found is a lean system: in it, an exposed problem becomes an opportunity to learn rather than an unwelcome interruption of the routine work of the "well-oiled machine".
Those companies – like Zappos, Google, Pixar (Disney), Menlo and Toyota – whose leaders-mentors have been bold enough to create an alternative management culture and a unique approach to people development, have been able to achieve extraordinary results. What I don't understand is why so few are picking this up as a powerful example to follow. Why are leaders so scared to try? Can't they see the leap towards becoming a learning organization is the only way to go?
THE AUTHOR
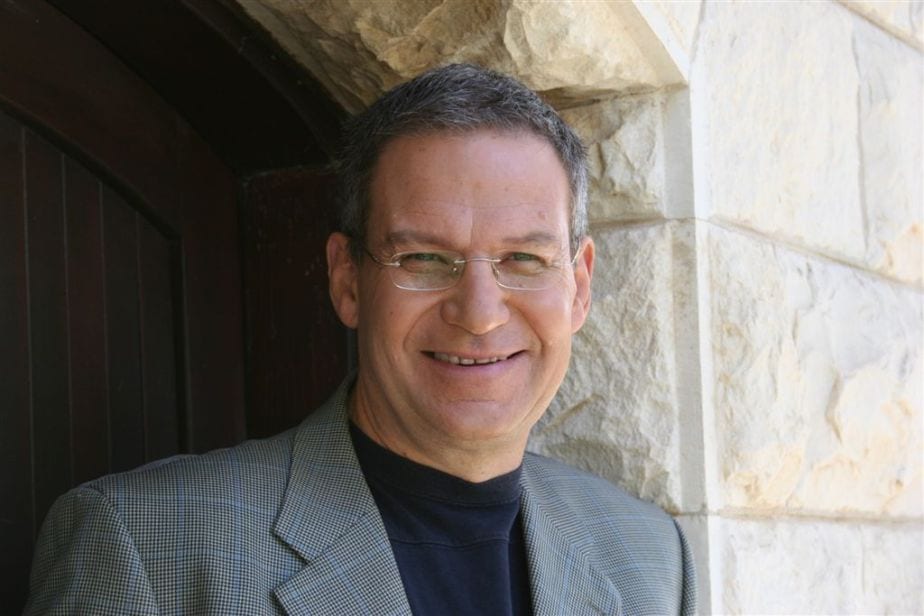
Read more
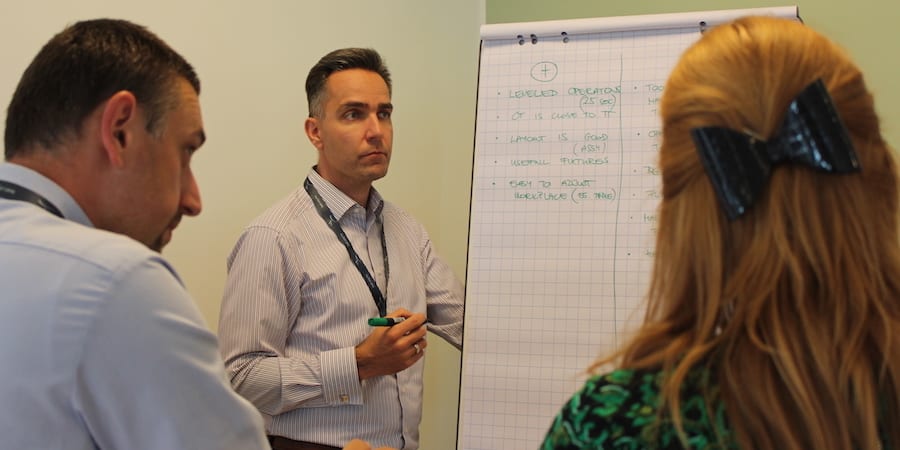
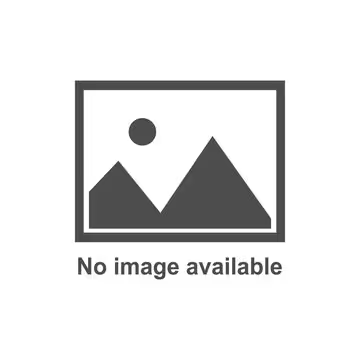
GETTING TO KNOW US – For our second interview with LGN directors, we travel to Hungary to meet the President of our affiliate institute there. He tells us his country’s need for good workers and how lean can make the difference.
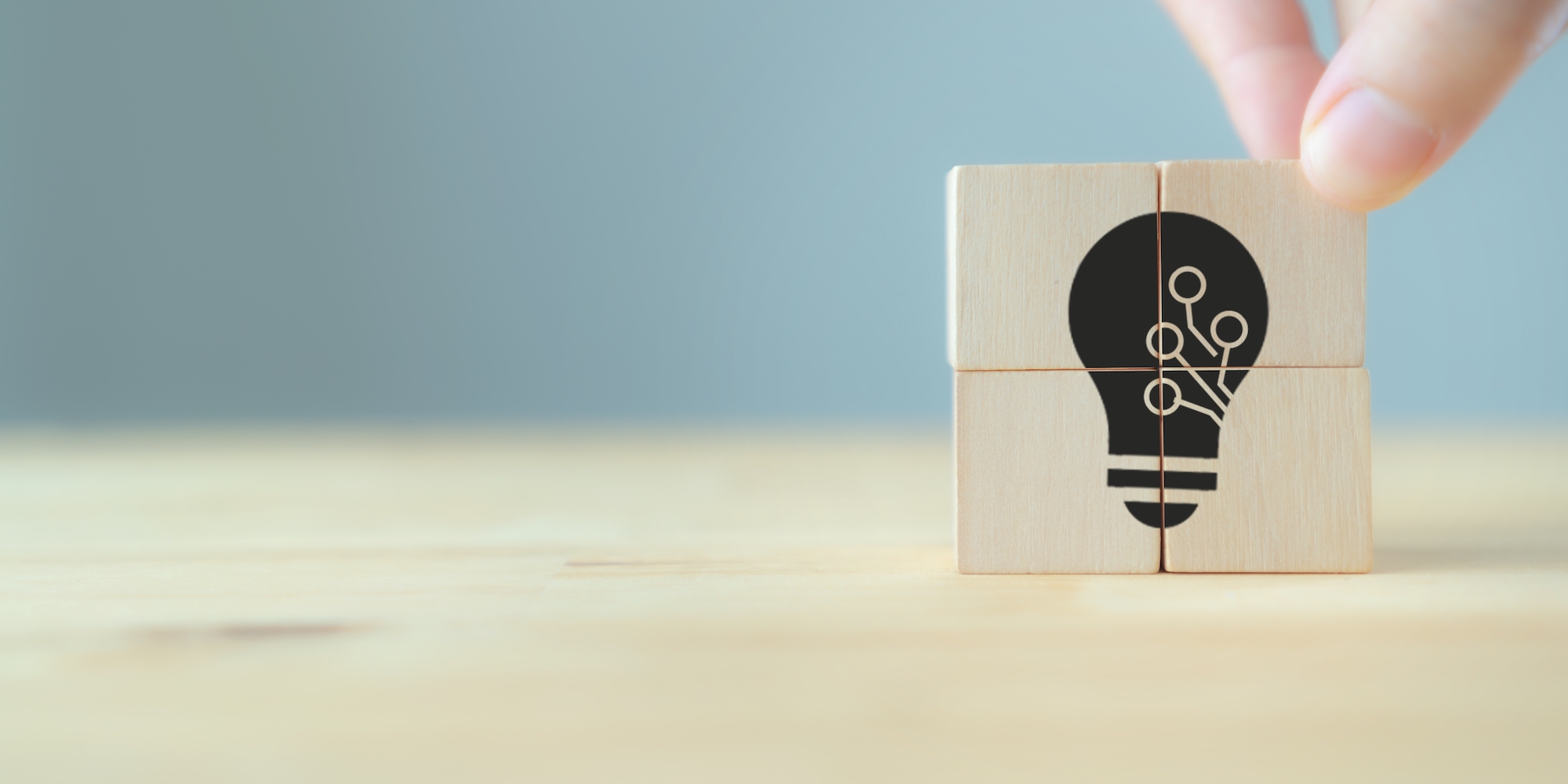
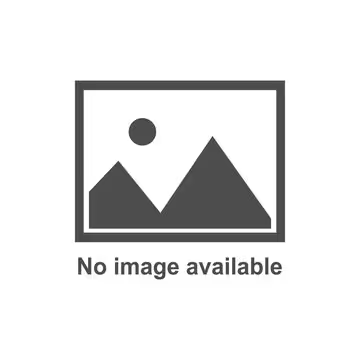
FEATURE – The authors explain why putting value at the heart of customer discussions is key to developing a successful, resilient tech firm.
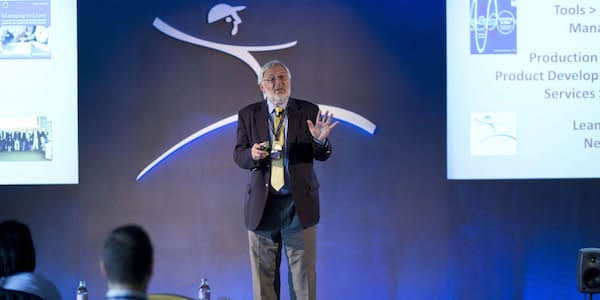
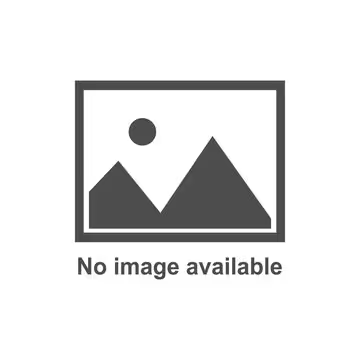
INTERVIEW – Dan Jones will be a keynote speaker at this year’s Lean IT Summit in Paris. In this interview, he gives us a sneak peek of what he is going to talk about.
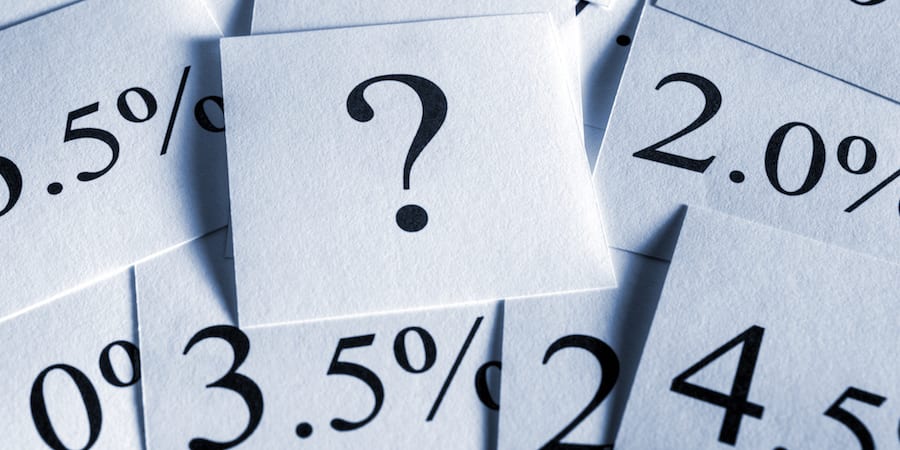
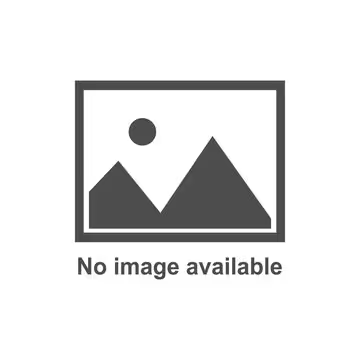
FEATURE – In the latest article in his series on how to effectively level production, Ian Glenday discusses why the perceived high variability of our demand is actually the result of a misconception… think about it in percentage terms!