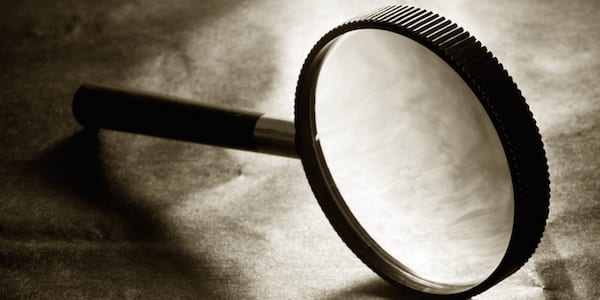
Six common problems you encounter during lean audits
FEATURE – Until “check” and “act” become a natural part of daily work, we will always need formal audits to keep people focused and to sustain results. Here’s a few tips to make them work.
Words: Malgorzata Jakubik and Robert Kagan, Lean Enterprise Institute Polska
As no true lean person should walk by waste and ignore a chance for improvement, we felt the need to put together our reflections on things big and small that, while working with our customers, we have found to be common “speed bumps” or even show stoppers in a lean implementation. Whether systemic or tool-related, these obstacles have one thing in common: they tell our “war stories,” which we want to share with those on the road to lean, hoping they will warn them against frequent hazards others have struggled with.
LEAN AUDITS: COMPLETING THE PDCA CYCLE OF YOUR LEAN IMPLEMENTATION
- DO THEM RIGHT, SO THAT YOU WON'T NEED THEM ANYMORE -
In a perfect PDCA-based, lean environment, there would be no need for a formal audit as people would simply “check and act” as part of their regular daily routine. But until you reach this future and ideal state, and therefore make lean a lasting deal in your organization, you will need to assess the status of your processes.
Be it 5S in your workstations, standardized work in a warehouse or a mitzusumashi system across a factory, you will need the same discipline and common sense to make an audit sustain good practices and identify what needs to be improved. How well you audit and what you do with the outcome of the audit will eventually (in the long term) determine the quality of your lean implementation and its sustainability.
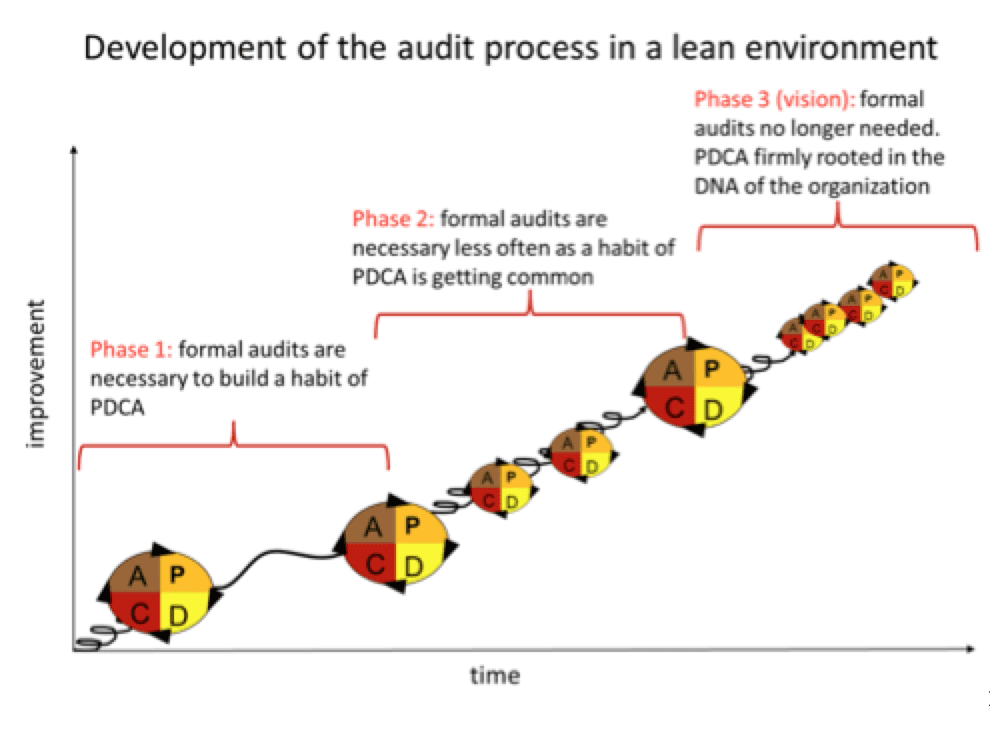
As with many things, when it comes to lean audits the devil is in the detail.
Sometimes audits just don’t bring the expected results and standards falter despite the huge and genuine effort made by the internal auditors. They keep diving onto unsuspecting employees like hawks, find all the non-compliances and explain to the people in the area what they have done wrong, and standards still don’t follow. They keep posting lists of corrective actions to be implemented, award special prizes to best-performing areas and punish those slacking, and standards still don’t follow.
Why? Because the devil is in the detail… In the quality of the audit checklist (What questions are we asking? Are there too few or too many questions in it?), in the frequency of lean audits, in the choice of auditors, and, above all, in how we are following up on the problems we find so that the auditing process is a learning and development opportunity, rather than a blaming game.
Let’s explore these all-important details as we go through six of the lean audit problems that we have seen our customers struggling with. Do they look familiar to you, by any chance?
Problem #1: We would like to audit regularly, but there are other things we have to do and audits take too much time. There’s not enough time.
This is one of the most commonly heard complaints about audits, frequent across all levels of an organization, from supervisors to directors, managers and team leaders. They all feel they have a lot to do, are under pressure to complete daily tasks and have results to deliver. Audits are the last thing on their mind. There is, after all, no immediate link to volume attainment, quality or delivery. They understand audits will help, but if there is a choice between fighting a burning fire now or auditing it, most people get to fire-fighting mode and postpone auditing for “later,” especially if that means saving a good hour or so on a busy day.
What to do then? First of all, limit the number of questions you ask. Checklists for a single audit event should not have more than 10-15 items. The truth is that the simpler the process, the bigger the chances it will be applied. A monster checklist of 40+ questions will scare a lot of people away and will take forever to use and feed back to the people of the area. Aim for a maximum of 30 minutes for the full event.
Secondly, have a schedule for your lean audits. Do not surprise people.
Two things are not negotiable:
- A planned audit of a lean process has to happen, no matter what. This way everybody knows it is important;
- Regularity is key (remember that your goal is not to find discrepancies but to improve processes, and make standards stick so that they will be followed as a habit). After all, auditing is not a boss’ whim, but a normal part of any lean turnaround!
Problem #2: Lean audits, like all audits, are about “painting the grass green” for the auditors.
We have stopped counting the times our customers would postpone a workshop or a visit because of some important audit long ago. They need resources to get prepared for the audit! It is an important and rare event. What they need is time to paint the grass green! Do your employees prepare specially for a 5S or a standardized work audit? If they do, you are most probably not auditing often enough and the intervals are so wide that there is no real pressure to constantly keep to the standard.
But how frequent is frequent enough?
It depends on the nature of the process and the area, but there is one general rule that we would like you to follow: the fresher the process you audit or the worse the starting condition, the more frequent the audits should be. With time, as the process stabilizes, people get comfortable performing it and results get better. This mean you can slow down on the frequency and use audits only to confirm the stability of the process and as triggers for improvement. In such a scenario, the grass is kept green through regular mowing and watering, not by means of artificial painting performed at the last moment in full panic mode!
Problem #3: Audit results are great, with over 90% compliance, but the actual situation on the shop floor is far from satisfactory.
If that is what you see, you have probably failed at phrasing the expected condition in your audit checklists or even in your standards. If your auditors ask, “Is there a documented standardized work in the station?” or “Are folders organized?,” people will look for a document or make sure the folders are in line and clearly marked, and check these audit items with “yes” – without worrying about the actual current status. “Is the operator using the standards and is this producing the desired results?” “Are people able to find what they need from the folders within 30 seconds?” These questions will tell you a lot more about the actual current condition and about the areas for improvement.
Another non-negotiable principle: audit the behaviors of process users and the results they are getting, not the mere existence of a process or tool.
Problem #4: The same discrepancies come back over and over again.
If this is true in your organization, you need to look into what is happening after the audit. Check your countermeasures. Are they clearly defined? Do they really address the root causes of the discrepancies? Are deadlines stretched or postponed? Are they specific enough? Or do you keep repeating actions like “talk to the operator,” “clean,” “motivate the team,” and so on, without thinking of what would actually make a difference.
Here is another piece of advice: add the question “Have all corrective actions from the last audit been addressed – either implemented or escalated?” to your checklist.That will ensure more discipline in the follow-up of your audit. And if you decide to be really tough, make this question #1 of your checklist and just fail the whole audit if the answer to this question is a “no.” The impact will be immediate!
Problem #5: Audit results depend on the auditor. Some are more lenient than others.
The problem can either be caused by a lack of good standards, which equals lack of an objective point of reference, or by the subjective phrasing of the audit questions.
How to fight these?
- Never start an audit before the standards for the process or area to audit have been established. The better the standard, the easier it will be for the audited to understand the expectation and for the auditor to stay objective.
- Your auditors will have different opinions, experiences and backgrounds – in the audit checklists, the less you refer to opinion and the more to the observable current condition, the more objectivity the process will have. Don’t ask “Is the area clean?” or “Is the material stored in the right quantity?” Instead, go for “Is the area free from unused tools?” or “Is the material stored in the quantity defined by the min/max levels?”
Problem #6: During lean audits high-level managers look into details of processes that are normally not their responsibility, like checking oil levels during a TPM audit. It is unclear who the auditors are and who should check what.
You must understand that there is a difference in the purpose of audits performed by different levels of management and that the structure of audits should be tailored to reflect that purpose.
Remember:
- Lower levels of the organization check the actual condition and control the process. Middle levels audit to understand where their subordinates do not control the process or do not see problems (and therefore need support and development). Top-level management audits to show the importance of audited tools and processes and coach the rest of the organization in key lean principles.
- Lower levels should audit more often than top levels.
- “Check” and “act” are the standard task of management and supervision of all levels. The task should not be given to a specialized “audit force.”
- There is a number of audit structures and processes you can pick from (so make sure they suit your needs): layered audits will engage all levels of the organization, cross audits (areas cross-audited by peers) will open the eyes of the area owners to new perspectives, while random audits (with regular audit schedules but areas to be audited randomly selected) will help keeping the organization on its toes and support stable readiness. Know your needs and make your choice!
Don’t forget that the ultimate goal is to audit your way out of formal auditing and into a habit of continuous PDCA. But if in your company you have found any of the six problems described above, there is only one thing you can do: look at them as you would at any non-compliance to the standard and get into countermeasures as quickly as possible.
“Plan” and “do” will help you to ensure your lean implementation gets results, but it is only by completing the picture with the discipline brought in by “check” and “act” that you will change your organization and make it a long-term lean success.
THE AUTHORS
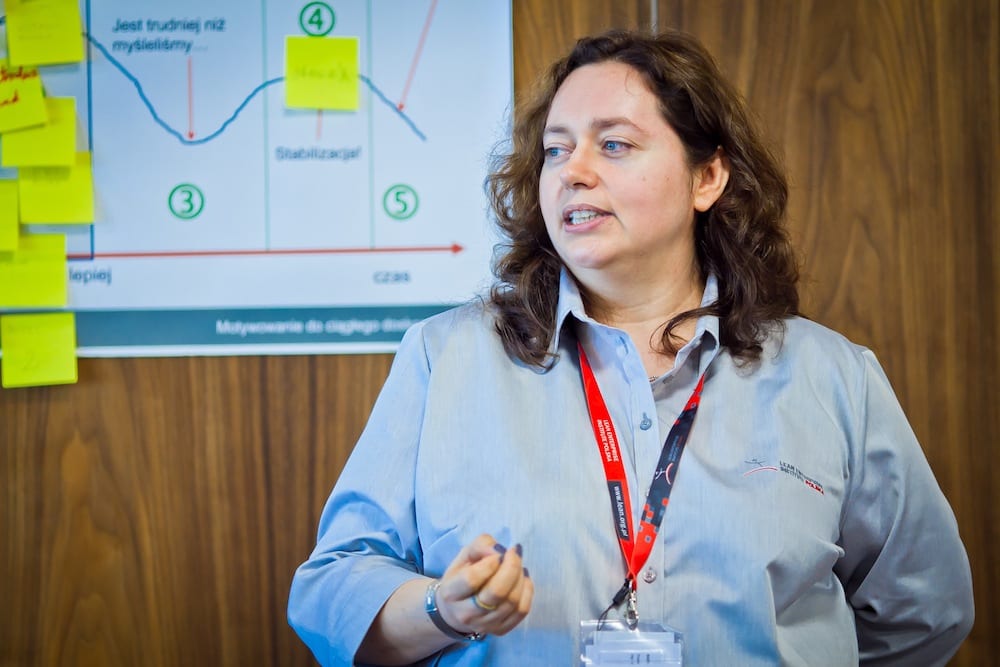
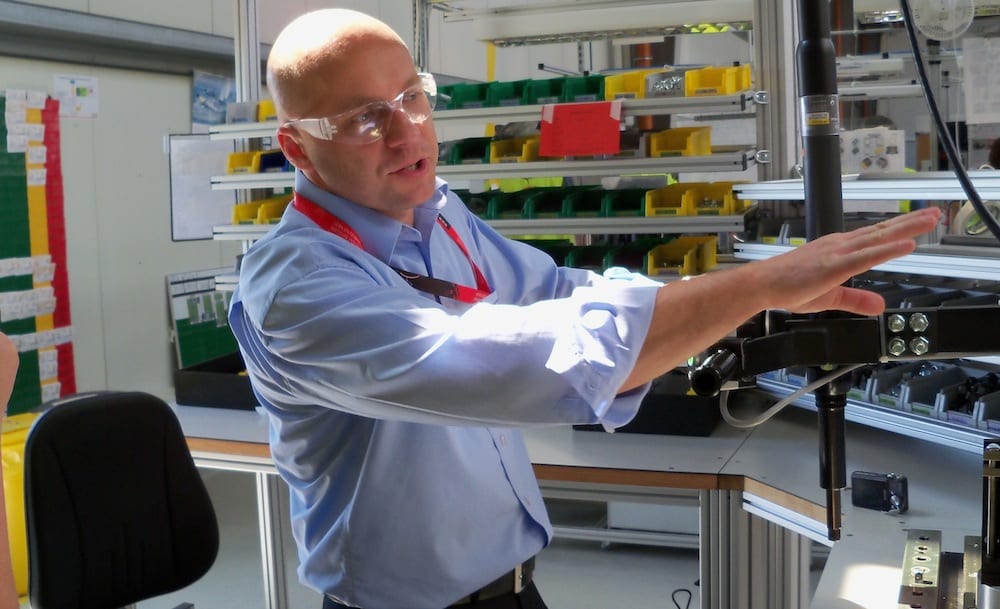
Read more

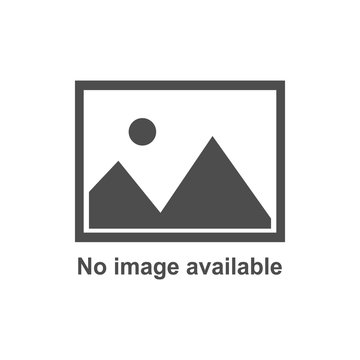
FEATURE – In the second article of our series written by the front-line staff of Siena University Hospital, we learn how the lean principles of pull and flow have transformed the blood donating process.
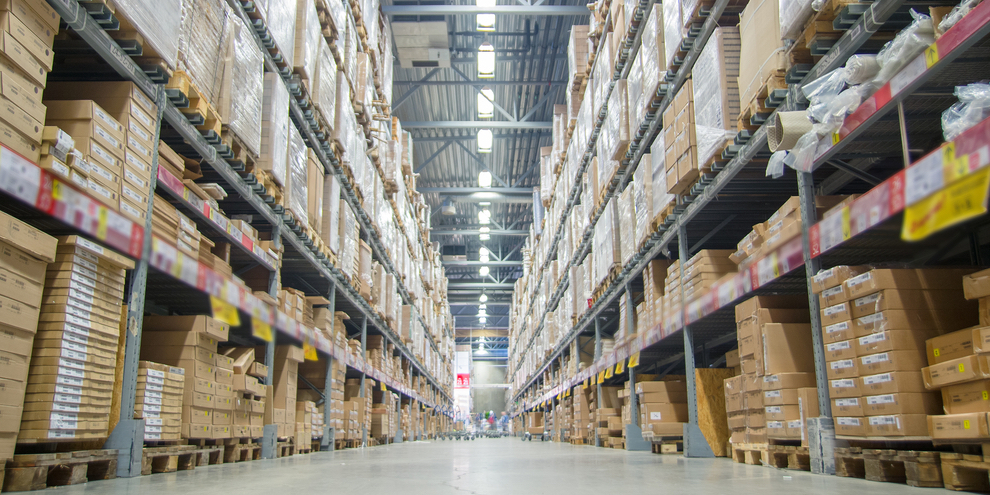
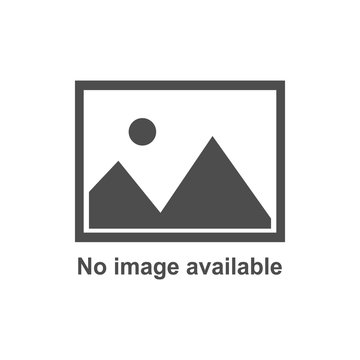
FEATURE – The author discusses the most common mistakes leaders make during gemba walks and the things they need to keep in mind to make the most of this important management practice.
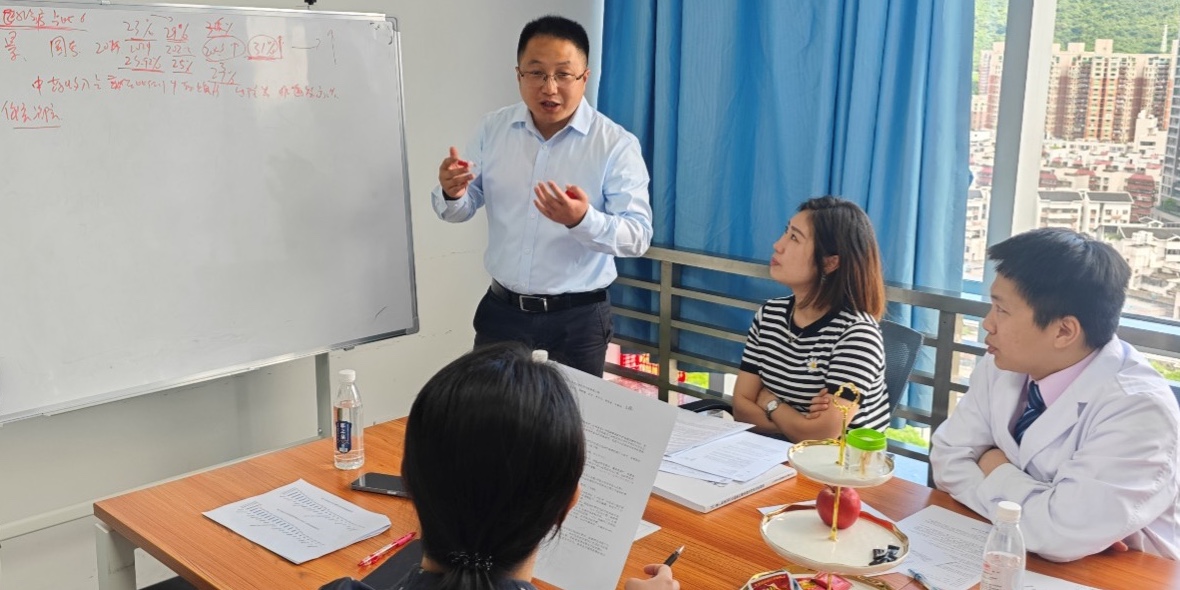
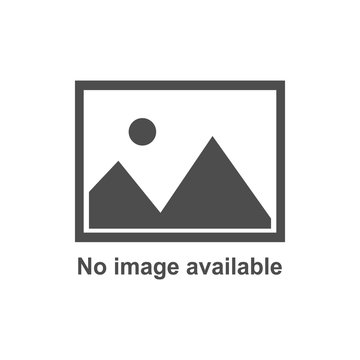
CASE STUDY – Thanks to a commitment to Lean Thinking and a solid coaching system, this hospital in China has been able to initiate a remarkable transformation.
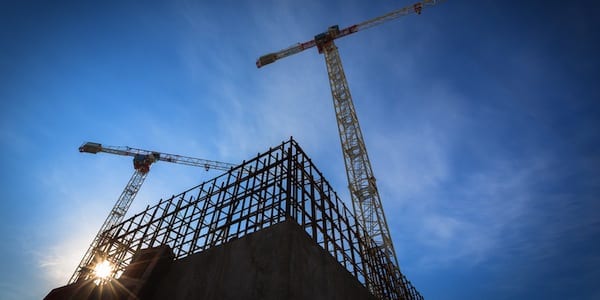
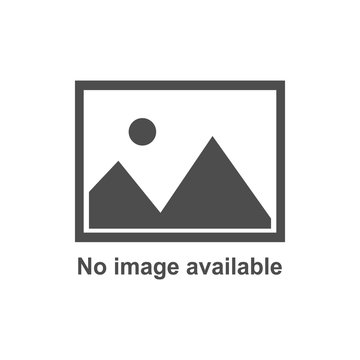
FEATURE - The author addresses the ongoing debate on rewards and recognition, explaining how an optimal relationship between team members, team leaders and group leaders will influence motivation.