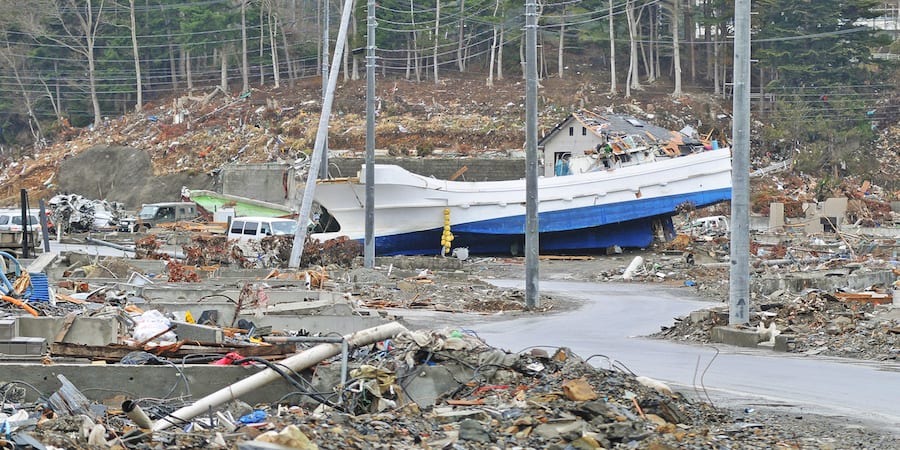
What informs disaster recovery efforts at Toyota
FEATURE – Much has been said and written about Toyota’s ability to recover from disasters. What many don’t realize, however, is that the company’s recovery strategy is informed by its underlying values – not just its tools.
Words: Takahiro Fujimoto, Professor of Economics and Executive Director of the Manufacturing Management Research Center at the University of Tokyo
After Japan was hit by a 9.0-magnitude earthquake and tsunami on March 11, 2011, Toyota’s global supply chain was affected significantly, as the production of components in the north-east of the country ground to a halt.
Even though Toyota’s main assembly factories resumed operations fairly quickly – by either recovering on the spot or switching to temporary substitutive production – the earthquake revealed additional problems with its anti-disaster preparations.
Since then, the company has developed a plan that, it claims, would allow it to respond to a disaster within two weeks. There was a lot of discussion across the media, government and business world about the company’s new “quake-proof” supply chain and anti-disaster measures, which include standardizing parts, making every region autonomous in its supply of components by duplicating production lines, and engaging with suppliers to ask them to either hold inventory of specialized parts.
These, however, are conventional measures that can work in certain conditions, but do not represent the main approach that Toyota adopts to respond to disasters.
If a measure, such as adding inventories, improves a company’s supply chain’s robustness but sacrifices its competitiveness, it should not be used: global competition is an every-day concern, while the next major disaster is still a rare occurrence. The core people managing anti-disaster activities know that building capabilities to strengthen supply chain competitiveness and robustness is much more important than simply adding inventories or duplicating lines for the sake of “being ready”. We should never forget that today’s major disasters still take place in an extremely competitive world.
Being based on the powerful idea of flow, lean thinking is very useful to understand the robustness-competitiveness duplicity: we want value to flow without interruption from our companies to our customers (a robust supply chain), but for this to happen we also need our suppliers to remain healthy and willing to stick to us (which eventually determines the competitiveness of our supply chain).
Toyota sees these two aspects as part of the same problem, to the point that they typically make the person in charge of kaizen at a company the leader of the disaster management efforts. One reason for this is that fact that these people are already out there helping suppliers with continuous improvement, and are therefore very knowledgeable about the supplier and its internal dynamics, management team, equipment, and so on. But they are also experts at problem solving and know how to pass those capabilities on to others.
There is literature out there saying that the structure behind incremental improvement cannot handle problems as massive and disruptive as an earthquake or a tsunami. Toyota, however, strongly opposes this idea, saying that recovering from a disaster is the same as kaizen. In their mind, kaizen is nothing but every-day disaster management. Indeed, if you break down big disaster management efforts into individual tasks, those are not different from the kaizen activities we normally tackle.
Another important aspect of Toyota’s approach to disaster recovery efforts – once again linked to the competitiveness of its supply chain – is that it prioritizes interventions on the spot: that means going out to the suppliers as soon as possible to start the work of bringing things back up. In those cases, when an alternative supplier can initiative production faster than the every-day supplier can resume it, Toyota will switch to that – but only temporarily. The reason for this is that they know that what they need in the long run to achieve competitiveness is trust. If suppliers see you switch to a competitor as soon as things go south, they won’t be able to trust you. Toyota remains loyal even in bad times.
And when they reach a supplier hit by a disaster, Toyota displays its incredible ingenuity and speed of action. As soon as a disaster occurs, the company dispatches an advance team to assess the situation: they are very good at calculating how many people they will need, what tools they will need, what the recovery will entail, etc.
Another important thing is that Toyota’s employees possess a keen sense of priority. For example, in the case of a disaster, they will typically focus on: the quick recovery of the damaged factory first; switching to substitutive production at another factory of the same supplier next; and switching supplier as a last resort. The most important thing is the life of employees and families, followed by the help that can be provided in surrounding communities and, only then, production recovery. Furthermore, the recovery of Toyota’s production lines should come last when there are other customers’ lines in the damaged factory, because the company knows that a hasty “me first” or “production first” attitude will end up destroying the trust employees, suppliers and communities have developed over time.
Interestingly, Toyota doesn’t have a permanent dedicated unit for disaster recovery, but a center for Recovery Assistance – part of the Production Control division – that will summon the people who can support the recovery efforts and send them out to the struggling companies. It comes as no surprise that when emergencies occur, a plant manager cannot prevent one of his employees from joining a recovery team – no matter how important she or he might be. It is understood that if the company doesn’t send out its best people to help suppliers out, sooner or later every plant in the “Toyota system” will be affected.
In conclusion, there is more to Toyota’s disaster preparation work than just duplicating lines and standardizing components. Once again, it is the company’s underlying principles and values that inform and guide its moves – not the tools anyone can see right there on the surface.
THE AUTHOR
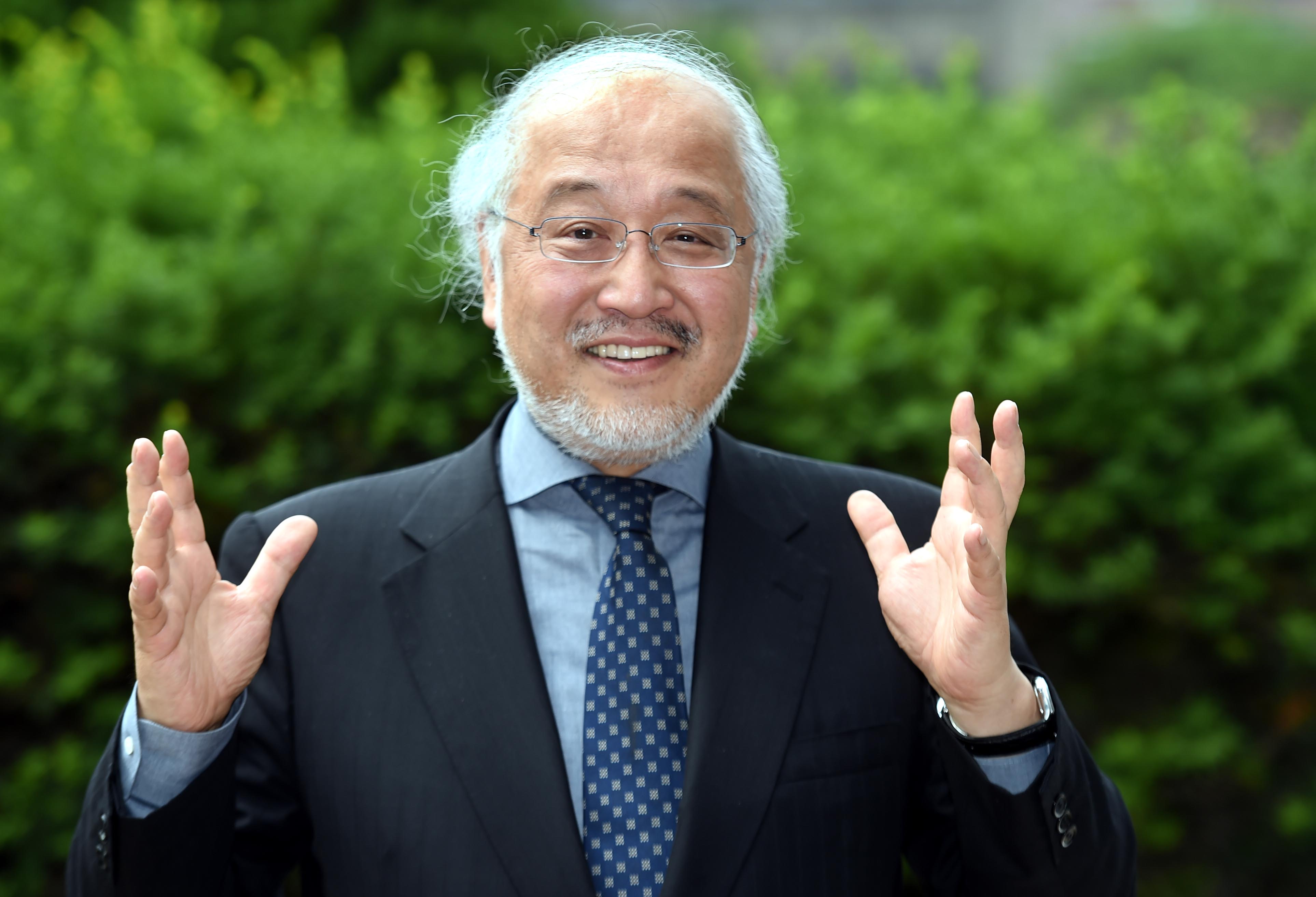
Read more
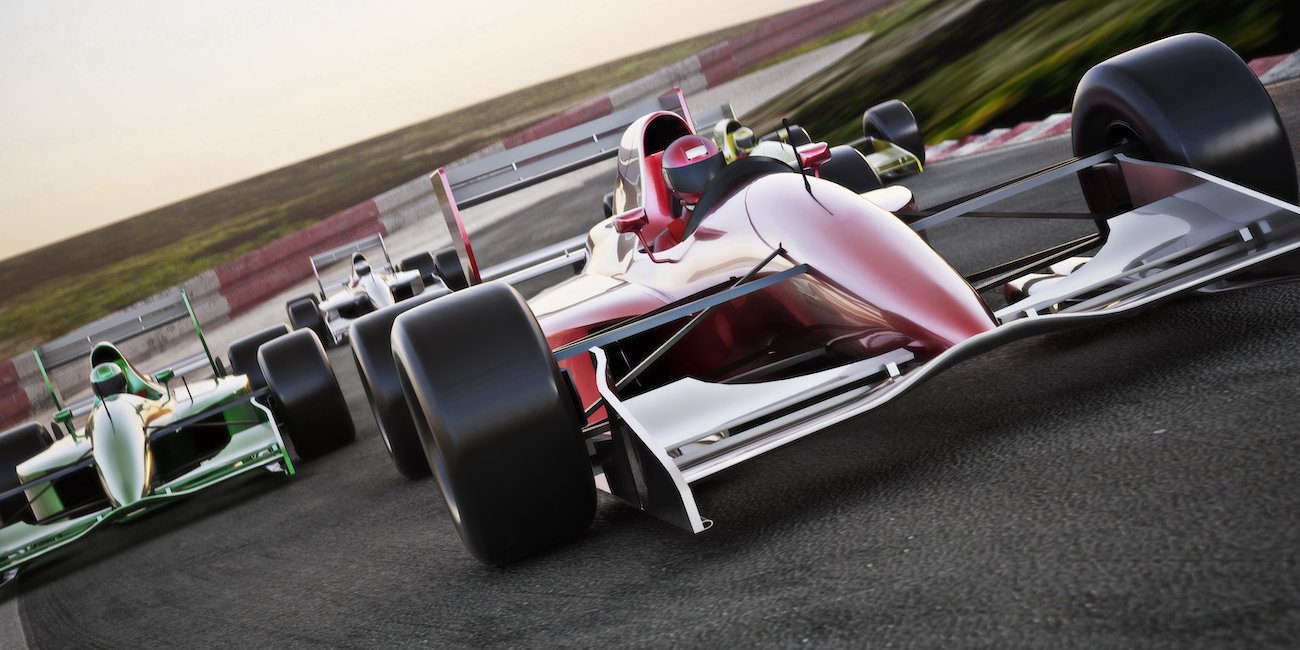
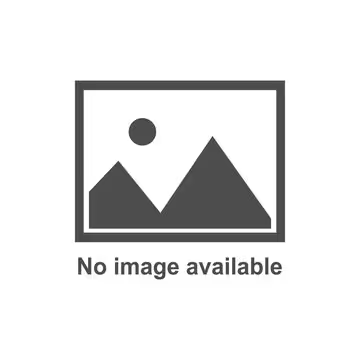
FEATURE – A situation that would be unthinkable in a sports context is an every-day occurrence in many of our organizations. Should we change our way of thinking about our machinery?
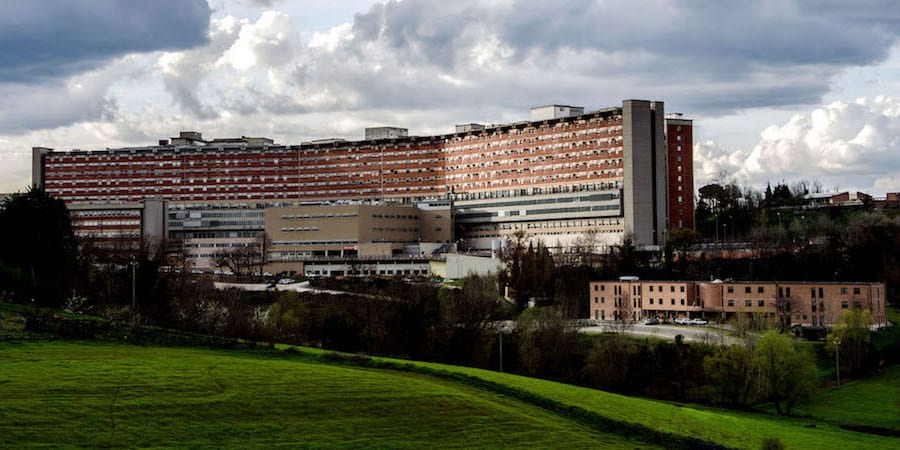
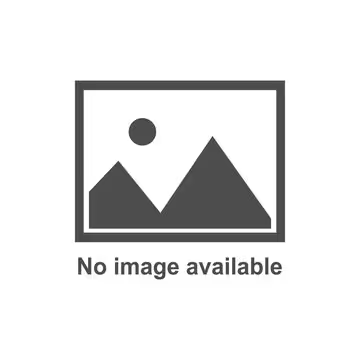
CASE STUDY – There is more to Siena than the Palio: the Tuscan city boasts of one of the most advanced examples of lean healthcare in Italy. We asked the team at the University Hospital how they are doing it.
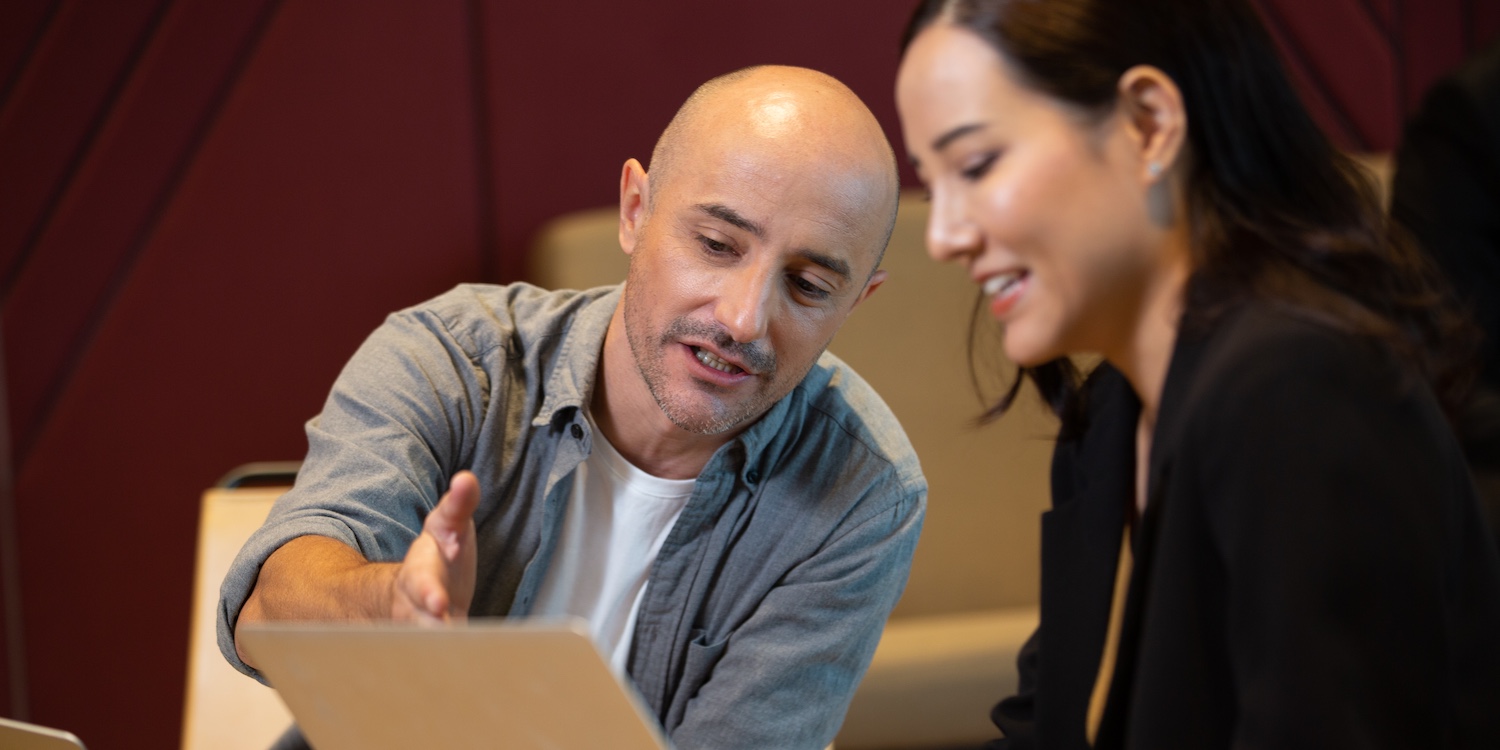
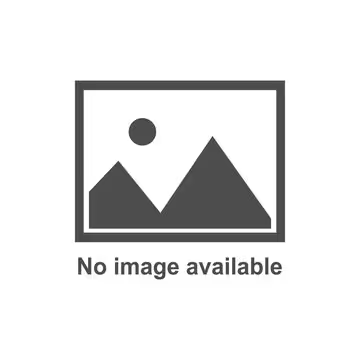
CASE STUDY – A Scaling Kaizen initiative at Veolia Water Information Systems engaged 45 teams in Lean IT practices, improving delivery, incident reduction, and fostering talent.

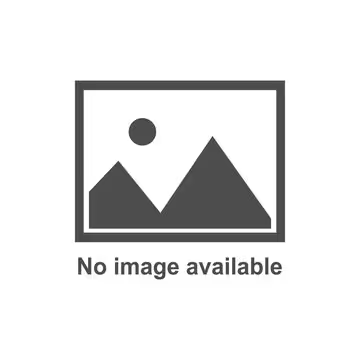
FEATURE – What role does packaging play when it comes to marketing a product? The author discusses “lean packaging” and shares the example of an Italian toilet paper maker.