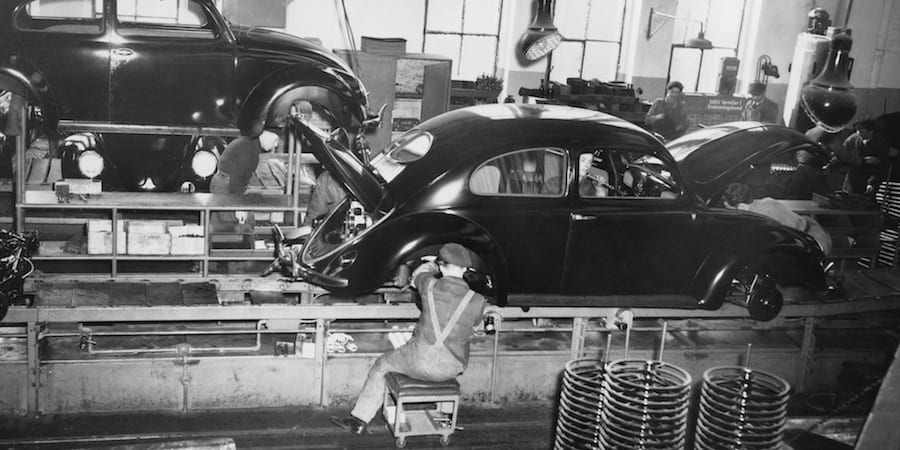
Jim Womack takes on the legacy of Taylor and Ford
WOMACK'S YOKOTEN – The author reflects on how the legacy of Taylor and Ford still poses challenges to the lean movement, and why critics should move past a simplistic view of lean as mere standardization.
Words: Jim Womack, Founder and Senior Advisor, Lean Enterprise Institute
Every family has a few members who are eccentric and problematic – like the proverbial crazy uncle locked in the attic. While this makes for fun conversations at family events – provided these folks don't attend! – crazy relatives can become a real problem if their antics reflect on the whole family. In the lean movement my two candidates for crazy relatives are Frederick Taylor and Henry Ford, who continue to cause us trouble 101 and 69 years after passing from this life.
Frederick Taylor, most famous for The Principles of Scientific Management published in 1911, did one good thing – he focused on how people did their work. This was in contrast with big company practice in his time of managers paying piece rates to encourage workers to work as hard and fast as possible but without knowledge of or interest in how they actually did the work. Taylor wanted to change this by observing each job in an organization – typically in large manufacturing companies like Bethlehem Steel – to find out who performed the job the most effectively, what Taylor called "the one best way". He then wanted to standardize this practice and direct everyone else to follow it while setting a higher production target to qualify for a bonus. He believed that everyone could make the bonus by following his standard work and everyone would be better off.
What was wrong with Taylor's approach? Just about everything. Taylor was convinced that most workers hated to work and were therefore "soldiering", pretending they were working as hard as they could. It was management's job to make them work harder and this required a sharp distinction between those doing the work and the managers thinking about how to get them to do the work. Thus the need for the manager to actually understand the work by observing the work. This meant in practice that the person doing the work the "best" way would effectively have his knowledge appropriated for use by everyone else without any reward. And everyone else would be mindlessly and grumpily following the instructions of the manager-expert based on the best way of the best worker. A great formula for mass misery.
But Taylor didn't stop there. He envisioned the work needed to create a completed product as a set of isolated, discrete steps, not as a continuous flow. So there was no need to align and tightly connect all of the work with everyone working at the same rate (known to us today as takt time.) He concluded that process village layouts were fine if progress was monitored with accurate "travelers" and production schedules for each step (later automated as MRP) and that the really important task for managers was to make full use of the assets in each village, both technical and human. This led to chronic overproduction to keep every machine and worker busy. To make the best of a bad thing, Taylor also invented standard-cost, absorption accounting, which judged managers on how fully they utilized labor and machines and then treated in-process inventories, no matter how unnecessary, as assets. And, as Dr. Deming pointed out, the focus on production without reference to the quality of the production was corrosive both to quality and to improvement.
As for improvement beyond current best practice, this was to be done by experts making observations without consultation with workers or line managers and, in Taylor's case, by external consultants. Indeed, Taylor invented the modern consulting industry as the first management consultant, in addition to being the first process consultant.
Oh, and finally, Taylor was a notorious cheat who doctored his results regarding productivity gains. (See Matthew Stewart's The Management Myth and Jill Lepore's "Not So Fast" in the New Yorker, October 12, 2009, for the lurid details.) Good grief. A really bad relative.
Henry Ford had no use for Taylor. He observed that the hard work of Taylor's classic worker, Schmidt the pig iron handler, would be unnecessary if the pigs were put down in the right place to begin with. If there was no in-process inventory between production steps and if everything from the previous step was delivered directly to the next step there would be no pigs or anything else to lift. Moving from process villages to cells and continuous flow for each product family was the solution, leaving out many wasteful steps altogether. And in the early days, until the Highland Park complex was completed in 1914, Ford's line managers and workers consulted intensively about the best way to do each task in Ford's new flow production system by working backwards from the work itself, not by observing many workers to see who did the work the best way. But as his company grew in size, managers began to simply tell workers what to do and how to improve their work based on the analysis of industrial engineers. Workers were to keep their heads down and keep working – Taylor had come in through the back door.
Ford was one of those folks who lived beyond his time in other ways as well, thinking that he knew what customers needed, specifically a completely standardized product with no options offered for years on end with no change. And he loved political systems that could supply the stability needed to make his system run smoothly. He was awarded medals for boosting industrial productivity by both Hitler and Stalin. And he was notoriously anti-Semitic and anti-labor and anti- a lot of other groups as well. In short his reputation would have been better served, the world would have been a better place, and lean thinkers would have had an easier time if he had been run over by a Model T in 1914 rather than living another 33 years to be become progressively more eccentric and destructive.
Today, we suffer from Taylor and Ford when critics rely on pattern recognition to brand us as "Taylorists" or "Fordists", always focusing on the issue of work design and management. They see one dimension of one small piece of lean's tool kit – standardizing individual jobs – as the whole. But they never ask about how standardization can work when work content varies (it can) and they never ask about the total process of value creation and how work and the management of work can be connected from end to end (they can) for the benefit of everyone, through shared inquiry about the work.
This critique seems to be heard more frequently as lean thinking is applied to professional work, where "professional" for many has meant the opportunity to do their work in their own way with no one else knowing what they are doing. I recently encountered a lovely example in a government organization that regulates drugs and medical devices critical to human health. The hundreds of doctors and PhD's involved in making determinations about efficacy and toxicity worked in one-desk rooms behind closed doors. The senior management actually had very little knowledge of what they did, how the many steps were connected, why it took so long, and why many items authorized for use after years of analysis produced unanticipated side effects. I was called in for a second opinion after efforts to improve professional work by traditional management consultants had led to the development of standard operating procedures without actually understanding the work, KPIs for performance of each step, complaints of "speed ups", and no improvement in results. I explained that managers and value-creators needed to begin by actually understanding the work and its impediments through intense dialogue.
Professional work – that of the engineer, the doctor, the app designer, the manager too – is particularly important for lean thinkers to tackle because over time office and professional work have become a larger and larger fraction of the total work done in society. And in the future, as automation proceeds, touch labor in manufacturing and other manual work will probably go the way of farm work to become a very small part of economic activity. So if we can't improve professional work we reach a limit, perhaps the reason the world's most highly developed economies are showing only slight gains in productivity in recent decades despite many new technologies.
How can we deal with this problem? First, let's make sure that we are not secretly Taylorists or Fordists ourselves. In my visits to companies I sometimes hear members of our community slipping into "I will tell them how to do the work and I will also think about how to do the work better" mode. Block that urge. It's disrespectful to people and it leads to bad results.
Then let's be clearer with everyone we meet about the nature of lean. We need to explain that it always involves intense collaboration between everyone – line managers, front-line value creators (from assembly workers to surgeons), contributors from support functions – to deeply understand the work and then to rethink and align complex streams of work involving many people with different skills. The objective must be to produce a better result for the customer, better work experience for employees, and better performance for the organization, all by removing waste. We must help organizations achieve all three objectives or we haven't done our most important work as lean thinkers.
The lean movement over 100 years has moved a long ways beyond our crazy American relatives, Taylor and Ford, by going to Japan and back and by adapting lean principles to practically every type of value-creating activity across the world. So let's invite our critics to come along with us, beyond simple pattern recognition and kneejerk responses to the very notion of standardized work, to a higher level of understanding about the nature of human work and how to it make better.
THE AUTHOR
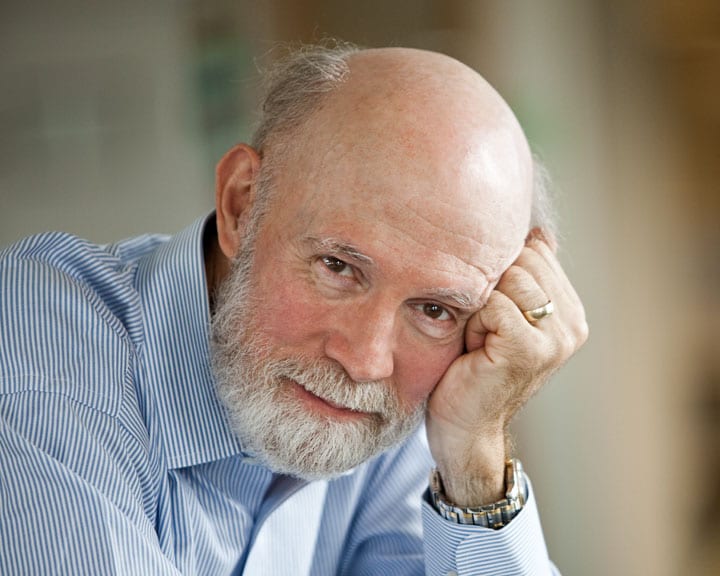
Read more
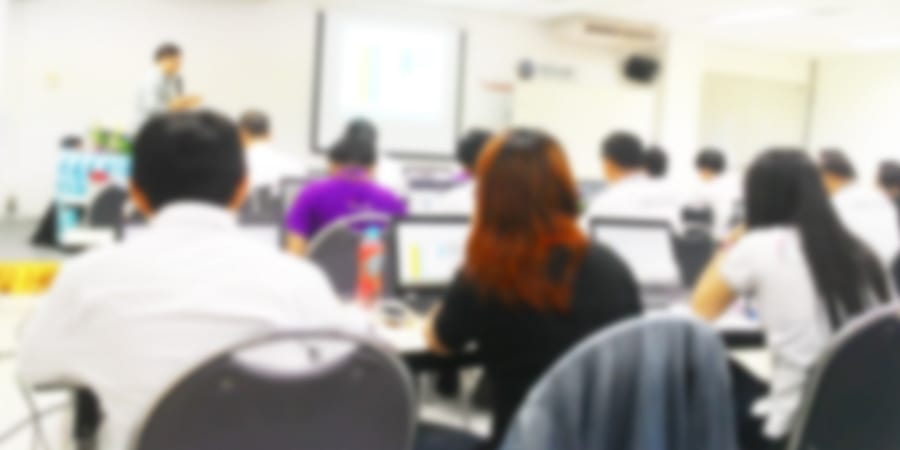
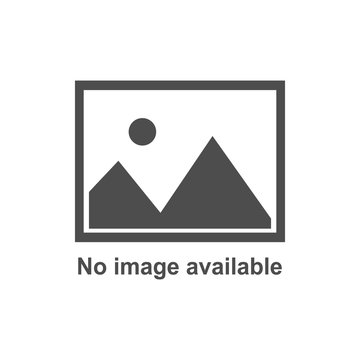
WOMACK’S YOKOTEN – Somehow surprisingly, management schools teach very little about management, and when they do all learning is classroom-based. Instead, they should go to the gemba.
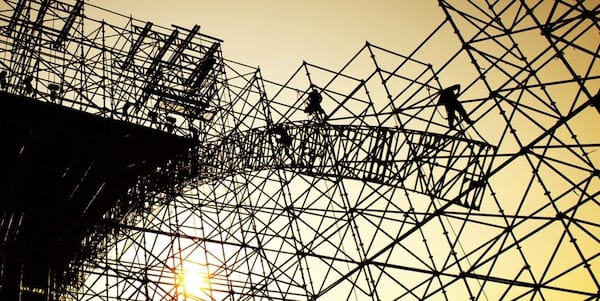
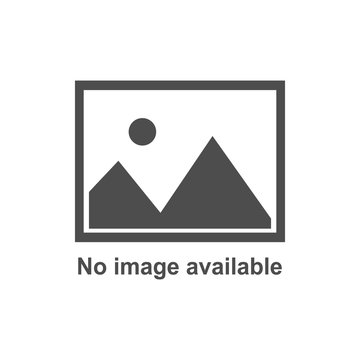
RESEARCH - For most CEOs, working with a sensei is common practice. Yet, many questions remain on this role. This paper aims to bring clarity to the "sensei mystery".
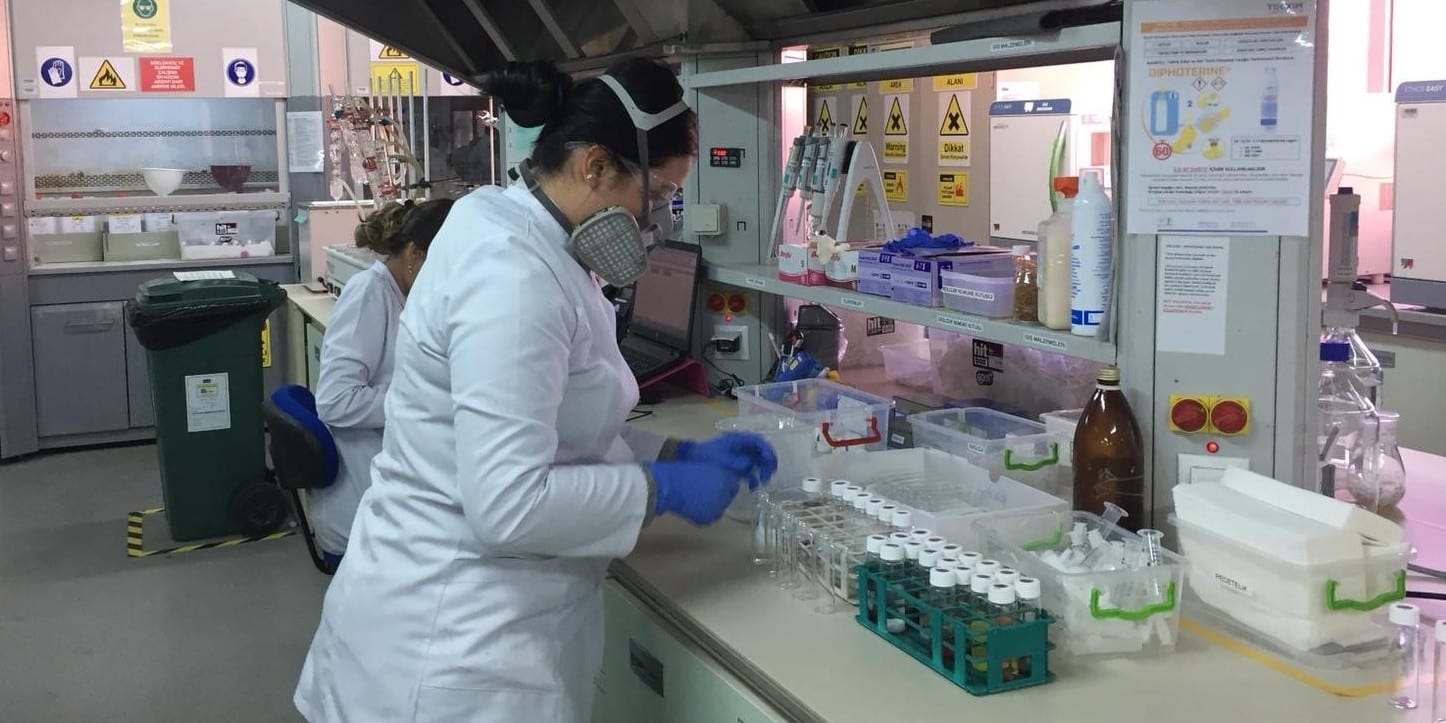
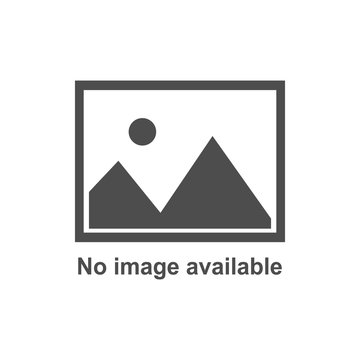
FEATURE – A laboratory testing services firm in Istanbul has turned to lean management to reduce complexity, shorten lead-times, and make its growth sustainable.
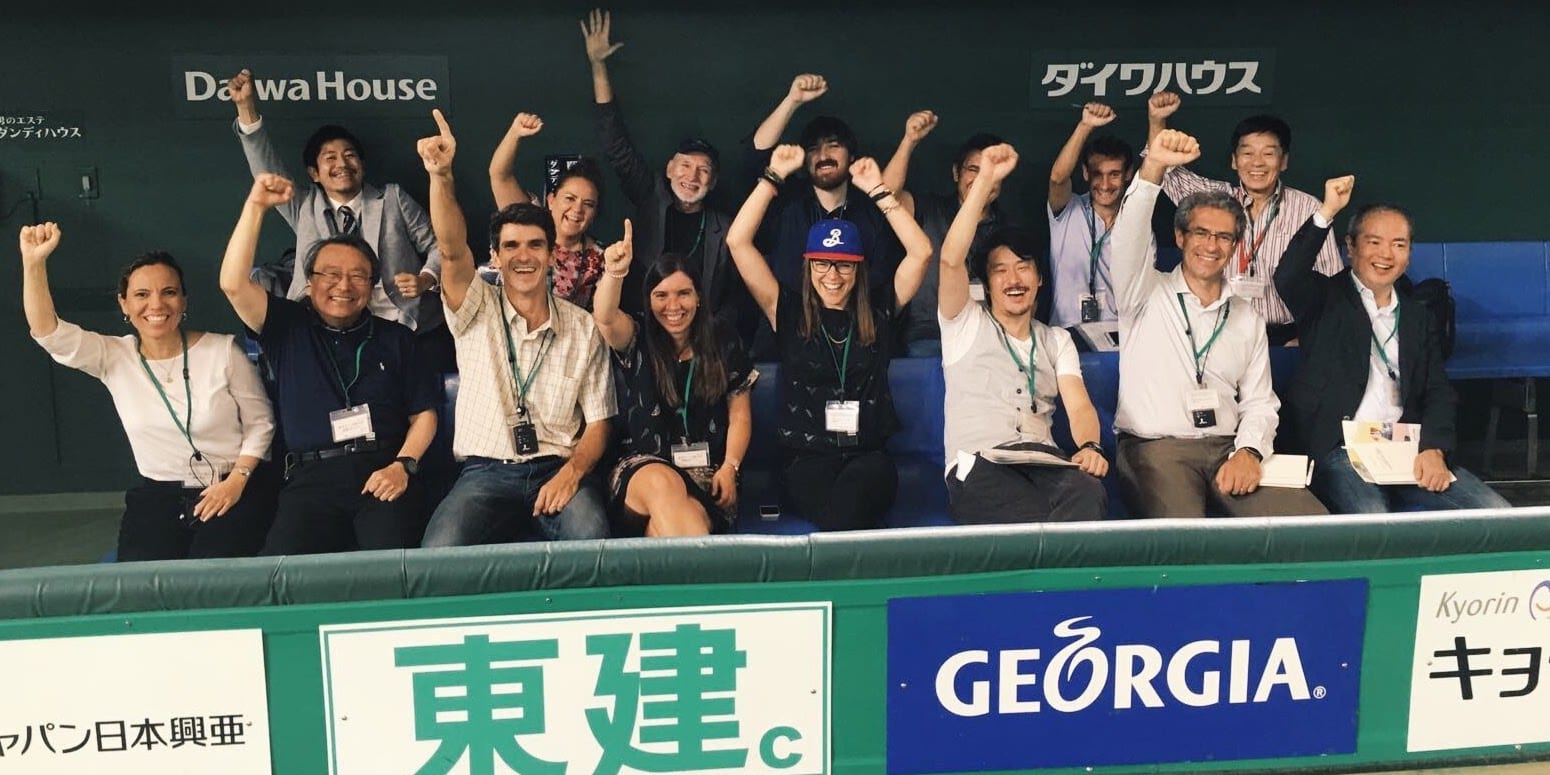
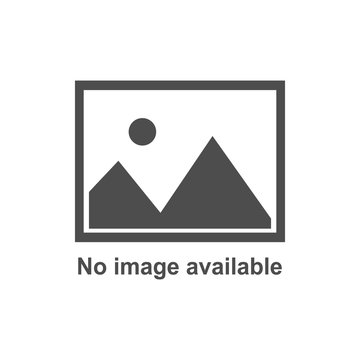
FEATURE – Study tours in Japan are an increasingly popular learning tool for lean practitioners. The author reflects on the first ever tour she ran and on what it left people with.