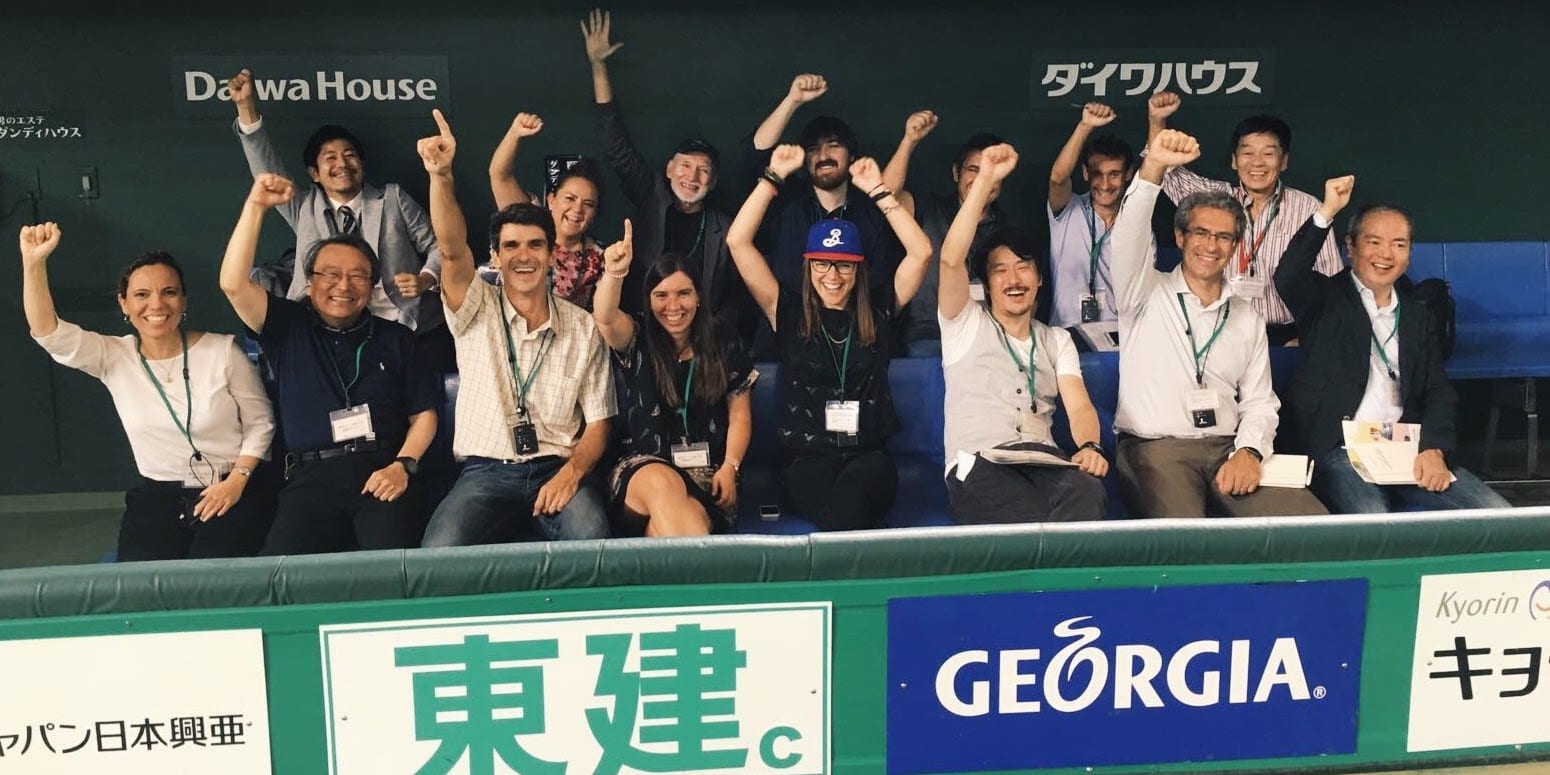
Learning a different way of thinking in Japan
FEATURE – Study tours in Japan are an increasingly popular learning tool for lean practitioners. The author reflects on the first ever tour she ran and on what it left people with.
Words: Monica Rossi, Assistant Professor, Industrial Engineering Department, Politecnico di Milano
Last September, I organized my first ever “Learning Week” in Japan. Because of my work in Lean Product and Process Development, the five-day tour (offered as an official program of the MIP – Politecnico di Milano Business School) put a lot of emphasis on engineering. Indeed, this was probably the first Japan study tour to focus on lean product development, but we also dove deeply into Japanese culture (complete with a Zen meditation experience) and we had a lot of fun doing it (karaoke every night, singing in the streets of Tokyo).
It’s been incredibly interesting for me to observe the people I accompanied on the Learning Week as their way of thinking was transformed over the course of the week. Mine was too! It is very common to seek a magic Japanese recipe that will easily transform processes, engage people and make a company prosperous. But, it is not that easy. In my experience, people believe that in Japan they will see similar “lean” practices to the ones they can observe in Western organizations: a coach (or consulting) helping an organization understand and implement lean, a number of tools being used, and so on. What we found is that, in many Japanese organizations, these “best practices” are simply embedded in how organizations work. They are not always easy to see and they are certainly not given the same labels we use. You won’t hear many people talk about a “value stream map”, for instance. And the name “obeya” often causes a few giggles.
Because lean transformation is not such an obvious thing to observe, I decided to structure the learning activity around the personal challenges that the participants faced at work. When we visit another company (or Toyota, or Japan) our problem doesn’t change: it is still to improve the way we do things – for instance, how long it takes us to design a product, or develop a person’s capabilities, or to eliminate rework. This makes a copy-and-paste approach a useless undertaking. Why should we simply try and replicate what Toyota does, when we are not Toyota?
I wanted people on the tour to really understand what they saw in Japan and to grasp the principles behind other lean transformations – something they would only bring back if and when it makes sense. At the same time, I needed to structure the learning in a way that would help them to understand that simply copying what Toyota does wouldn’t take them very far. So, after each visit, we discussed what we had seen and wondered together if the approaches observed were specific to Toyota or Japanese culture or if they could be applied elsewhere.

As the week progressed, I witnessed a change in the minds of the participants. Half way through the tour, I noticed they started to pick up on things they didn’t even notice two days before. They started to take pictures on the streets, in restaurants, and stopped to marvel at how two people were folding a table or at the omnipresent plastic food used in Japanese restaurants to display the menu (a fantastic example of visual management and certainly something we would never see in the West… and possibly the most photographed thing during the tour). It was clear to me they were learning to learn, so to speak – by the end of the week, Toyota was one of the things they had seen, not the only focus of the study tour.
If to many the Learning Week had begun as a visit to a number of high-performing companies, after a few days it became clear there was so much more to it: it was a deep dive into lean in engineering in Japan, which included visits to automakers (Toyota, Nissan, Mitsubishi and Sumitomo) as well as less traditional environments (like Yahoo or Tokyo Dome, but also the Tsujiki Fish Market).
At the beginning of the tour, participant’s expectations were not as ambitious as I hoped: they just wanted to see and copy what Toyota does. Sharing study tour design practices with the Lean Global Network, which was organizing a mission at about the same time, we asked participants to state whether their expectation were more: 1) Best Practices, 2) A-ha Moments, or 3) Life-changing experience. At the end of the week, I asked them to assess their experience along the same three dimensions and they universally shifted from a prior expectation of mainly “Best Practice” to actual “life-changing experience.” This made me very happy.
Marco Bassoli, Director of Research & Product Development at Beretta is a great example. He said that the deep dive into lean organizations and Japanese culture inspired a deep understanding of kaizen in him. After returning, Marco wrote a 78-page report of his learning, full of descriptions and insights such as these:
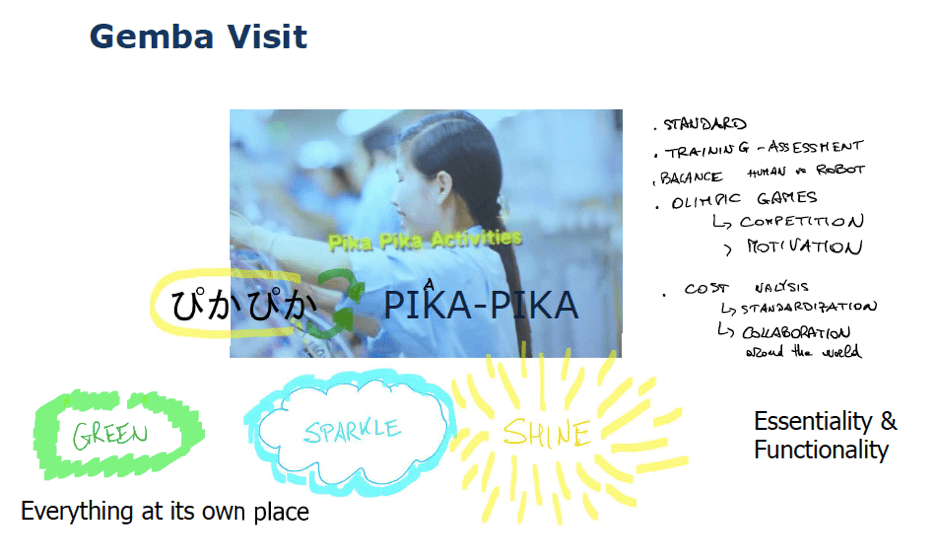
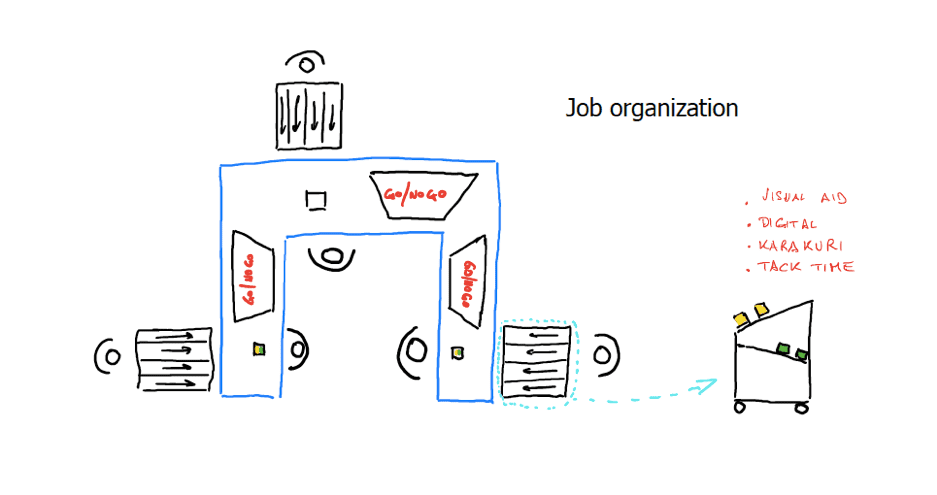
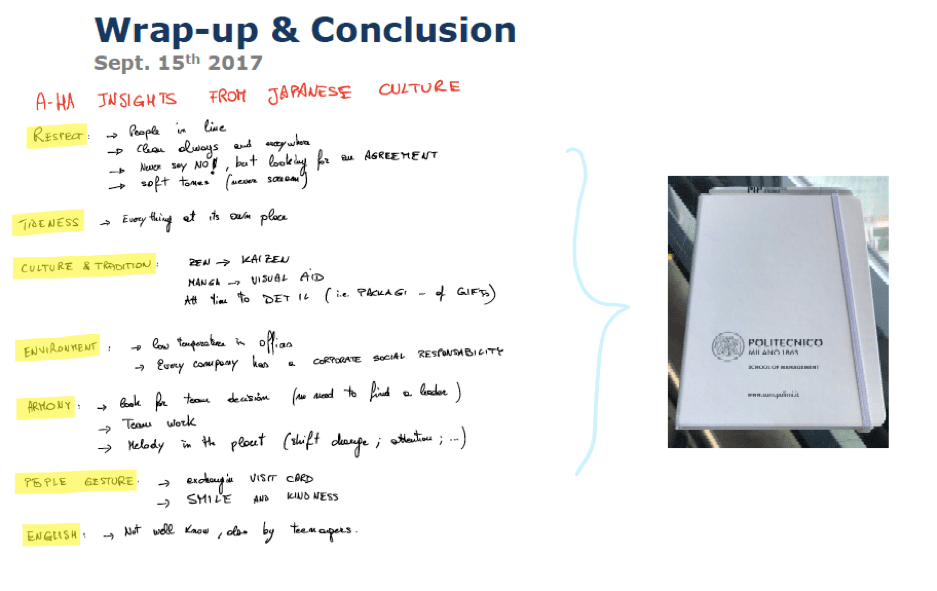
As I prepare to host a second Learning Week in Japan in a few weeks’ time, it is compelling to reflect on what I learned last year, as those lessons are shaping how I organize future study tours. Of course, visiting Toyota taught us a lot about concurrent engineering (the fact that the company engages with different functions and customers when developing new products is very evident), but there was much more than that.
For me personally, the most striking lesson was the unique way in which Toyota develops and leads people. Even since the tour, I have started to ask myself more questions than ever before: do we have all the information necessary to make a decision? Have we consulted all stakeholders? Are we enabling people to succeed? These are the types of concepts that apply across the board, in every culture or organizations. To make it work, however, you need to make an abstraction of what you see, understand why it is the way it is, and then assess whether it can apply to your work. This is surely the most valuable skill imparted by the MIP Learning Week.
"When Monica asked me to help her to organize the Learning Week on lean product development, I was immediately intrigued. I wondered whether or not “lean product development” was known as a concept in Japan (like “lean production” is). Many in my country think that abandoning our traditional way of thinking and learning something from others are signs of weakness. Indeed, “importing” cultural traits from others is an uncomfortable exercise, which can only stem from a strong will. This study tour offered me a different perspective of my own culture: it was fascinating to see foreigners understand some of the most distinctive traits of our character as a nation and making a connection between them and the business challenges they face back home. The Zen lesson was a turning point in that sense! I encourage you to attend this year’s Learning Week to develop a unique understanding of Toyota and Japanese thinking."
Hiroyuki Anzai, Director at De-Tales
THE AUTHOR
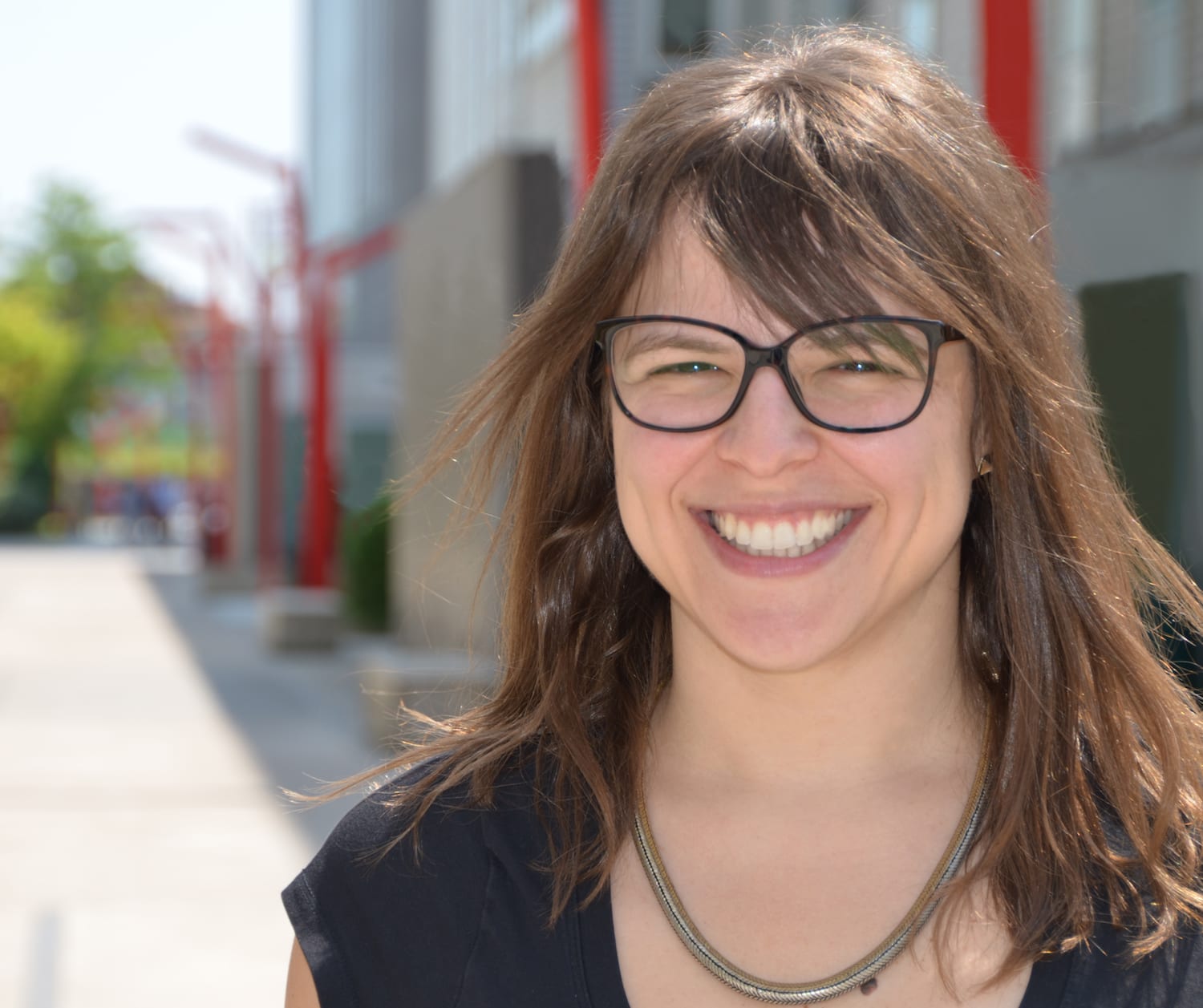
Read more
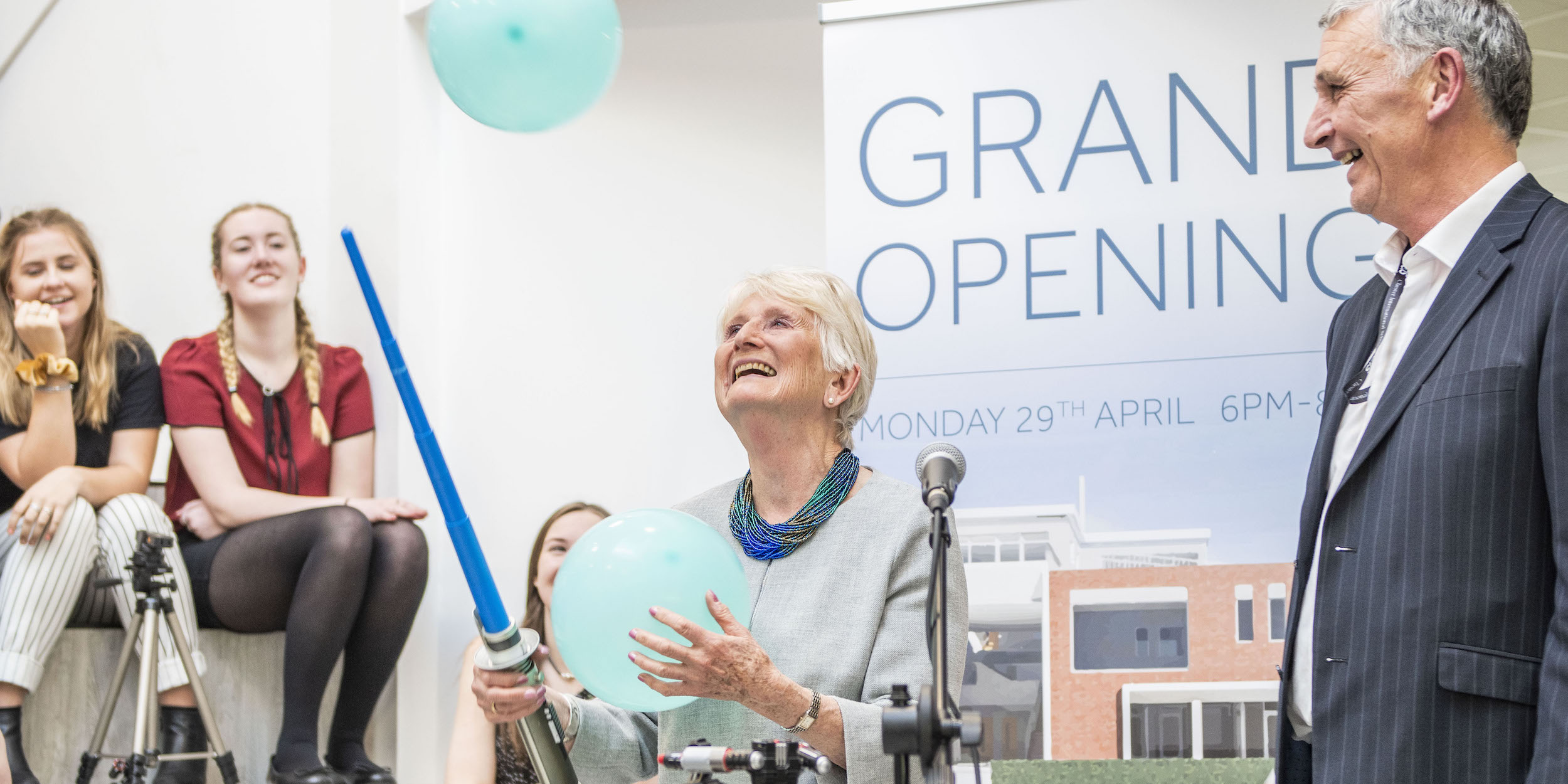
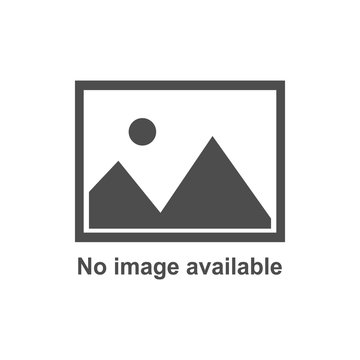
FEATURE – How does lean apply to learning? The author reflects on the lean transformation his schools are undergoing and on its practical implications on students, staff and leaders.
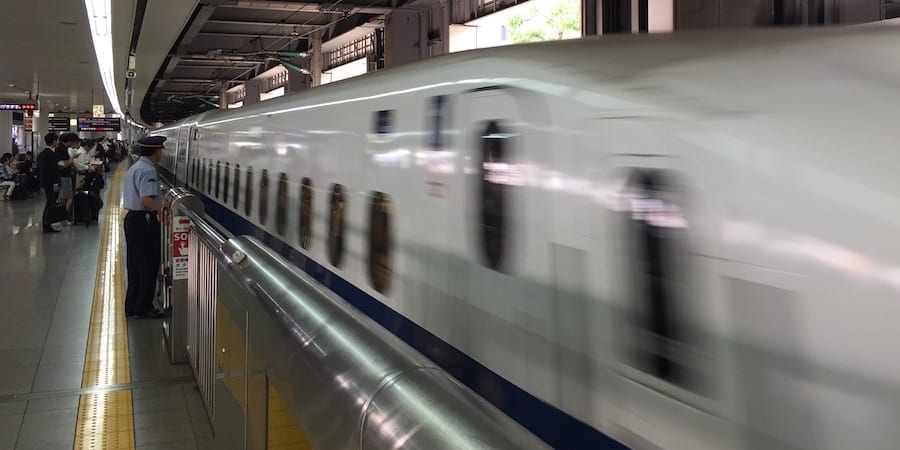
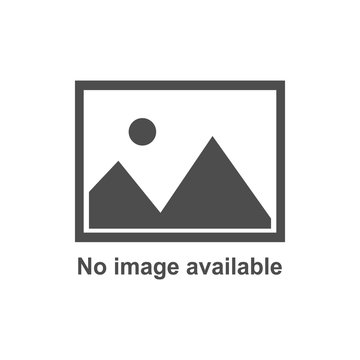
FEATURE – How many times do we hear people say lean is not for them because “it’s a Japanese thing”? After spending 18 months in Japan, the author explains why the country’s culture is not necessarily "lean by nature".
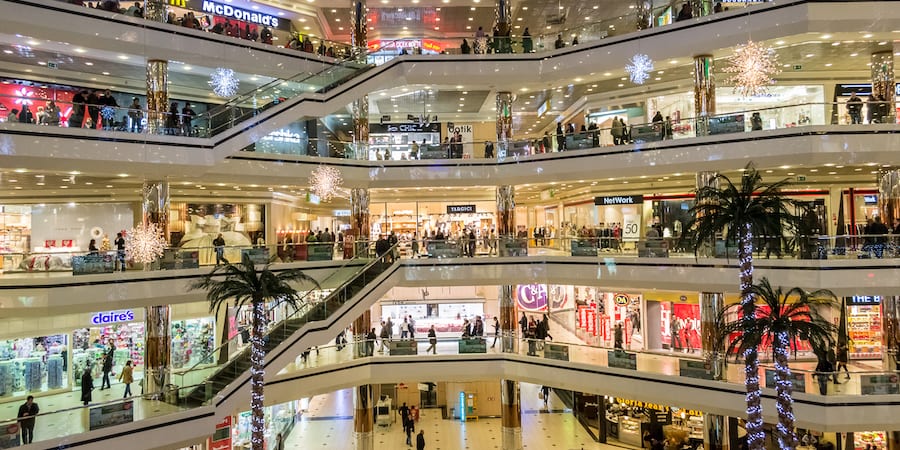
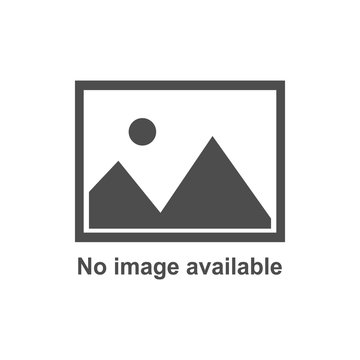
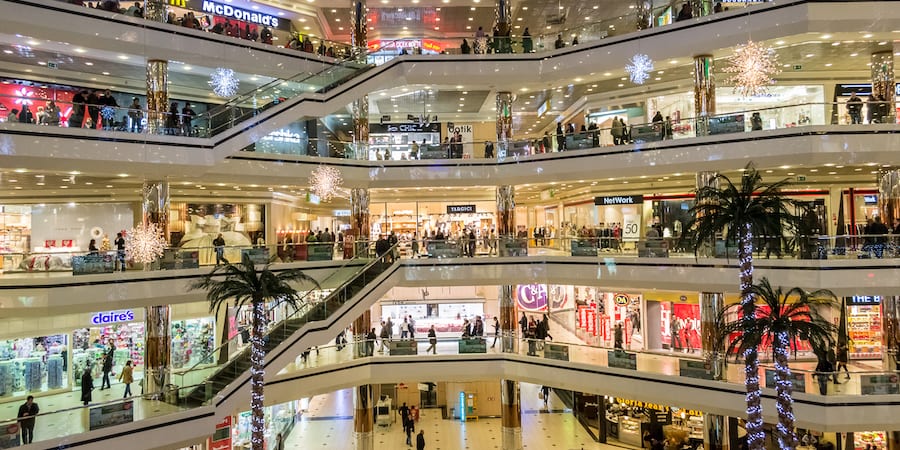
WOMACK’S YOKOTEN – Toyota’s commitment to employees reminds us that it is impossible to tap into the full potential of lean without providing people with stable, gratifying employment.
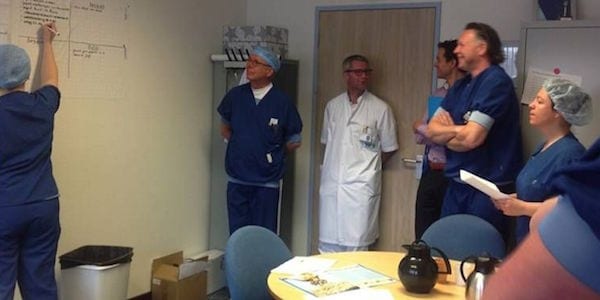
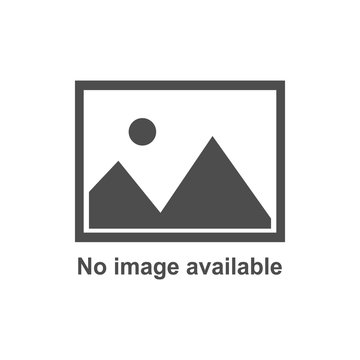
INTERVIEW – PL sits down with a consultant and a manager from the St Elisabeth hospital in the Netherlands to talk about the organization’s “loving care” approach to treating patients.