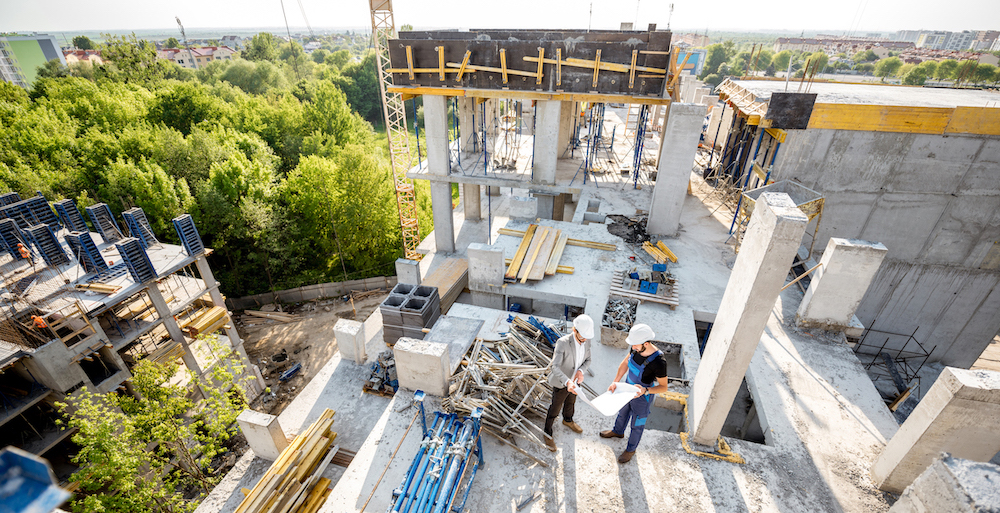
A different approach to construction
INTERVIEW – Lean is not widespread in Colombia’s construction industry yet. The interviewee discusses the benefits this philosophy can bring to construction sites.
Interviewee: Mauricio Llanos
Roberto Priolo: Mauricio, you recently joined Lean Institute Colombia. What’s your background?
Mauricio Llanos: Lean and operational excellence have been the pillars of my professional career over the past 25 years. I started in manufacturing, but also worked in logistics and construction. Construction is, in fact, the sector in which I have worked for most of my career – 15 years spent with the same company, where I participated in a successful lean turnaround.
RP: What made that lean turnaround so successful?
ML: We had fertile ground to build on (pun intended), because we had the full support of top management. That was incredibly helpful. This was a process of transformation and the fact that we had top leaders on our side meant that we were able to quickly and effectively overcome obstacles and problems.
From a methodological standpoint, the secret of our success was that we were able to define the problem very clearly. And it was a strategic problem, which affected not only our bottom line, but also the customer.
RP: What are the most common difficulties construction companies encounter in their day-to-day work?
ML: There are all kinds, of course, but I would highlight two main ones. The first difficulty I see is caused by leadership. The most hierarchical institutions in our world are typically considered to be the Army and the Church. Let me tell you, there is a third one: the construction industry. I realized this early on in my career. The prevalent, extremely hierarchical leadership culture that exists in construction (I have been guilty of it, too, in my early days) is what prevents change from taking root.
The other huge difficulty is that, generally, a construction site is not perceived as a production system, meaning that the work is not as well-planned as it is in a factory. The reason productivity is much higher in manufacturing than it is in construction is not the presence of machines – like many people assume – but the solid scheduling and planning work that takes place. A factory plans the work 21 times per week (seven days a week, with three shifts per day) and, because of that production plan, every worker knows exactly what they are expected to do over the course of their shift. Conversely, there is very little planning going on in construction. Even when a company uses Last Planner System, that planning only takes place once a week.
Don’t get me wrong, Last Planner is a great tool. It’s not lean, but it helps you a lot by generating quick, low-hanging-fruit results that will enthuse people and encourage them to keep exploring what a lean culture can do for the business.
RP: What are your biggest learnings about lean in construction?
ML: First of all, as I mentioned before, having the support of leadership really makes all the difference. However, it’s important to realize you don’t always get that from the very beginning or from one day to the next. You need to work at it. You need to be brave enough to speak up, to try and explain why lean just makes sense from a cost/benefit perspective.
Secondly, it’s important not to fall into the trap of seeing lean as nothing more than a set of tools for process improvement. Of course, there are tools, but Lean Thinking is so much more than that. It’s a good idea to understand the purpose of your lean transformation and build a framework around it, as that will act as a compass guiding you in your journey. Without it, you’ll just get lost in a sea of 5S implementations and Job Instruction sheets. In the construction company I was with, there were three areas of focus in our framework: planning and scheduling; productivity and optimization; and culture and skills (which then became our main focus).
Thirdly, having a clear understand of the problem you are trying to solve is fundamental. If you don’t have that clarity, you are going to get lost. Assigning a clear goal and figure for your problem-solving exercise is a good practice, too, and the SMART framework is a great reference for that.
Another learning, which I mentioned earlier, is around Last Planner. You should start using it as a system to plan the construction work in the short, medium and long term. In the construction industry, there is a direct correlation between the fulfilment of the plan and the achievement of deliverables. This is known to everyone. What isn’t understood by everyone is that before you fulfil the plan, you need to fulfil the PAC (Percentage of Activities Completed – a simple indicator telling you how you did against how you expected to do) every day. If you achieve your daily goals, you will achieve your plan-wide goals and fulfil your promise to the customer. This means helping people on the site to understand how their work today will impact overall results.
Finally, you should never forget quality. Sticking to the plan and delivering on time is of course important, but it’s equally important to have controls in place throughout the process that ensure the quality of the product match our and our customer’s expectations.
These five things were critical to me when it came to initiate bounded experiments in the company I worked for, which then led to a wider transformation across several construction sites.
RP: In Colombia, Lean Thinking is still not prevalent in construction. Why is that? And what would the benefits be of spreading it in this industry?
ML: The construction industry tends to be quite conservative. Thinking about managing a site and leading people in a different way is not easy. It’s a cultural shift you need to work really hard at, but the great benefits of doing that hard work are impossible to ignore.
When we turned to lean in the company I previously worked for, we improved our fulfilment rate of the construction plan by 43% over eight years. It wasn’t from day to the next, but it was a substantial result – coupled with a 15% improvement in customer deliveries. There is a lot of money to be saved there! For us, it was around $850k per year.
RP: What can we do to help lean spread in this industry?
ML: You’d think that the first thing we should do is talking to the CEOs and top leaders of construction companies to help them understand why lean works, why it makes sense. In other words, make a business case for it. But that won’t always work, because not all CEOs will be responsive. Instead, we need to talk to middle managers – like productivity managers and quality managers – and propose experiments to them, indicating in unequivocal terms how much improvement they can expect from them in different scenarios (from the most pessimistic to the most optimistic). This will put the ball in their court and kill the argument that “my CEO won’t pay attention to me”. We all have a responsibility to help lean thrive!
THE INTERVIEWEE
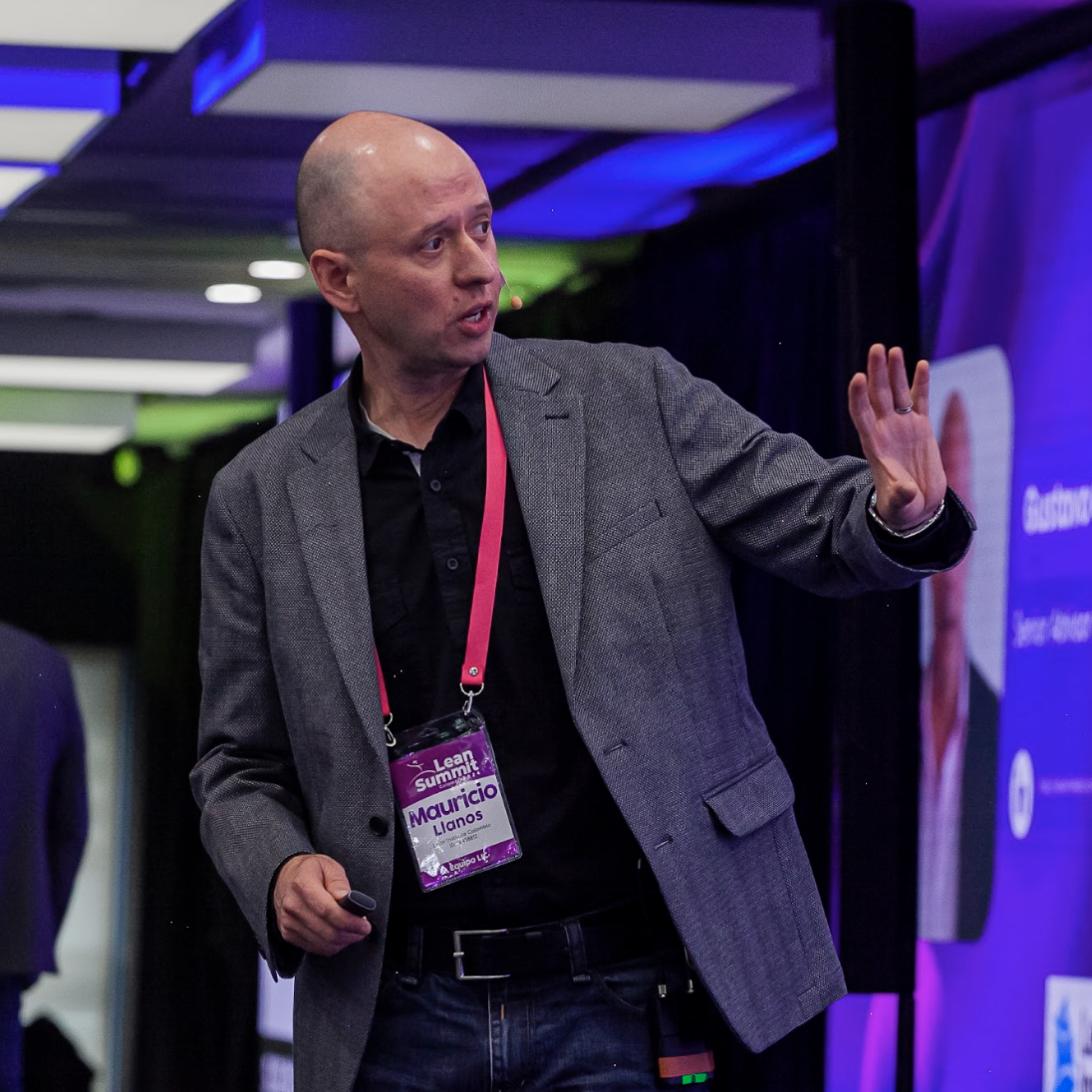
Read more
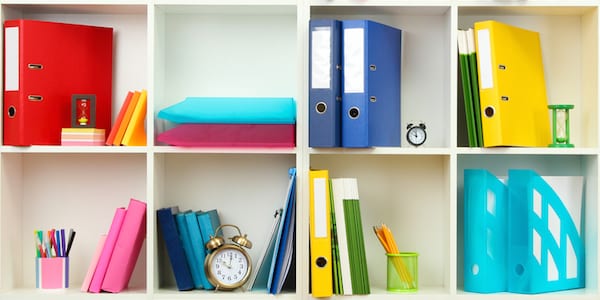
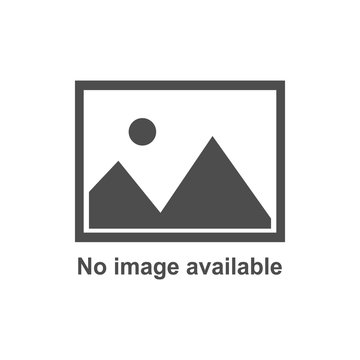
OPINION - If you have ever 5S-ed your daughter’s room or tried to bring one-piece flow to your grocery routine, this article on what lean management looks like in our personal lives is for you.

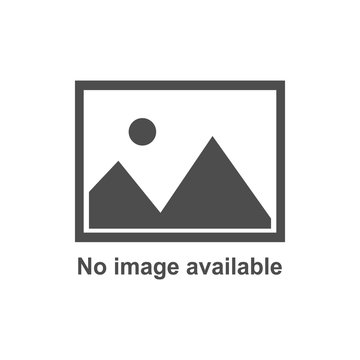
FEATURE – In business, the word “turnaround” refers to radical changes in the direction a company is moving toward. Here’s why Lean Thinking can increase the chances of success of such endeavors.
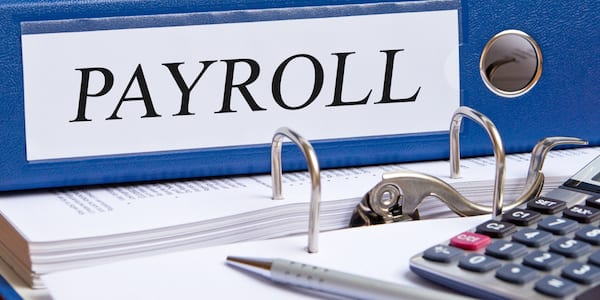
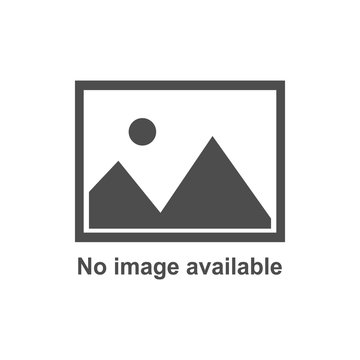
COLUMN – Finance is a critical function within a firm. Yet, lean thinking seems to struggle to make progress in this field. Following a workshop with Nick Katko, the author of this article sees an opportunity.
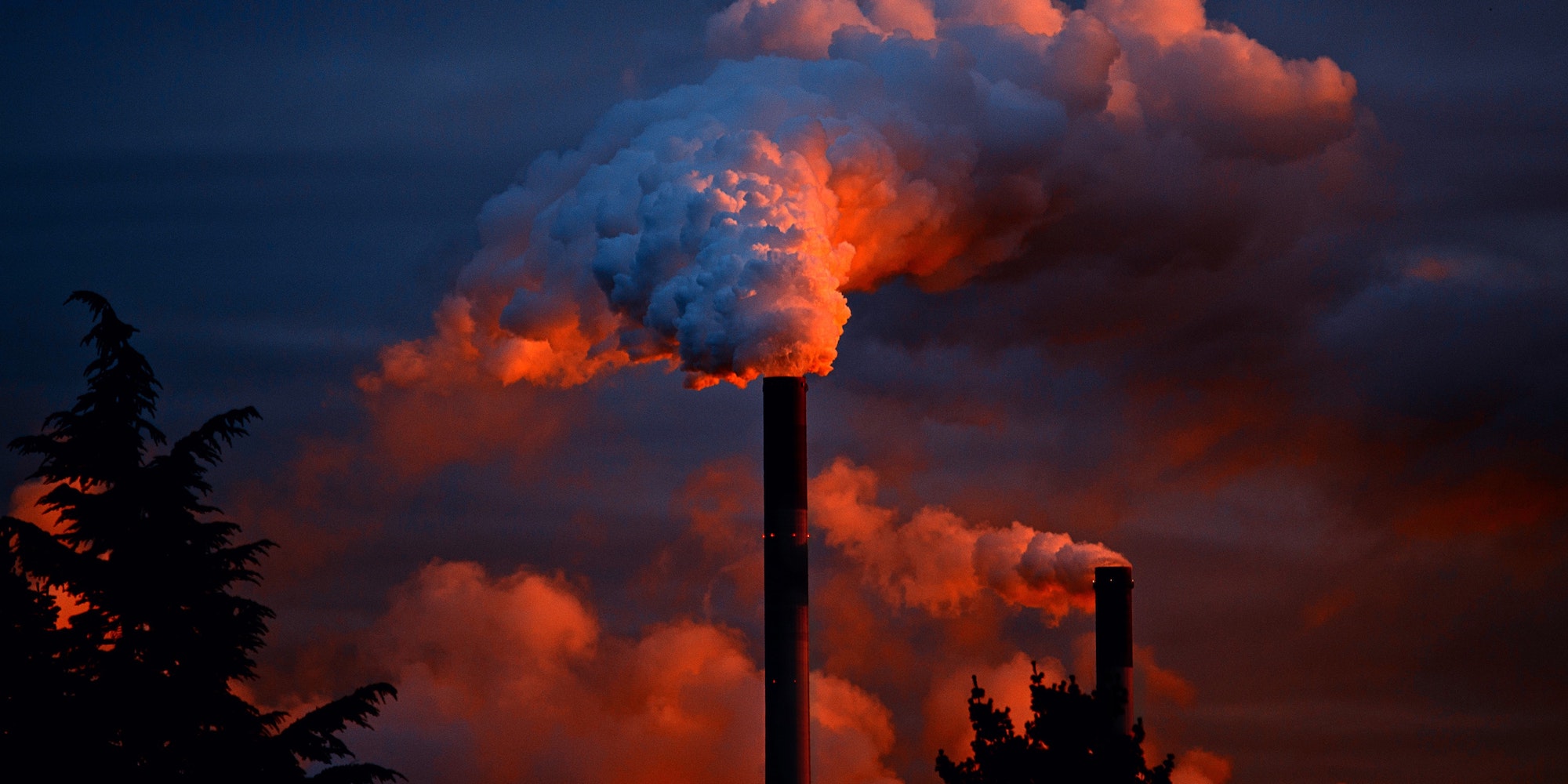
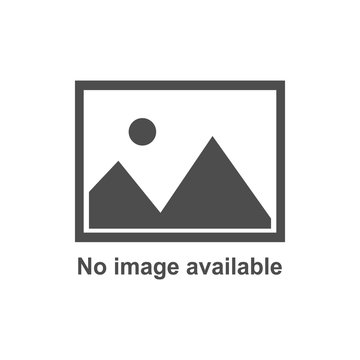
FEATURE - Imagine targeting a quarter of the world’s greenhouse gas emissions by setting our lean minds to it? The authors discuss building better, circular supply chains and designing sustainable products.