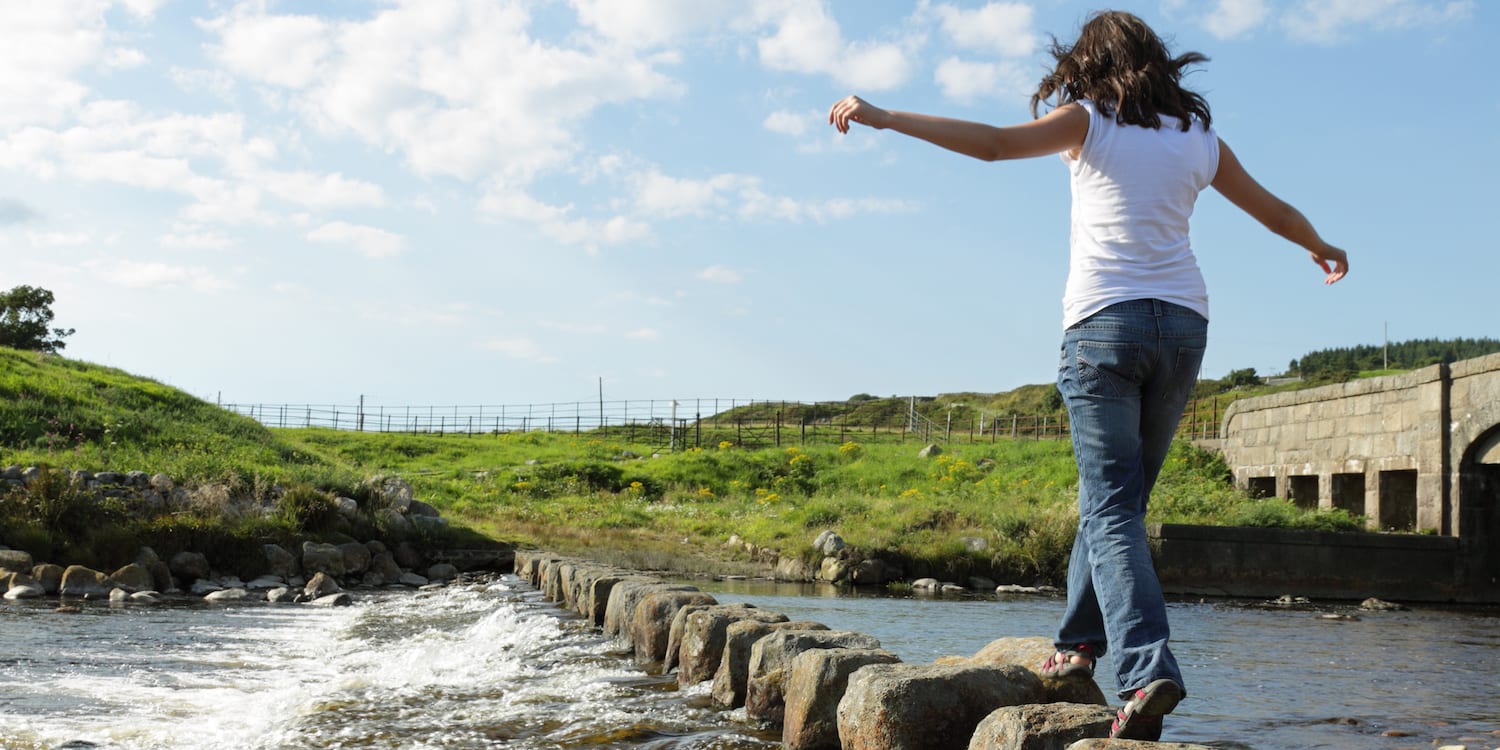
A value stream for people development
FEATURE – The continuous flow of developing people’s capabilities throughout their studies and careers is lacking, to say the least. It’s time we saw this as one big value chain.
Words: Csaba Bereczki, lean coach and co-founder, Lean Enterprise Institute Hungary
If we think of today’s educational systems – and this is as true in Hungary as it is in other countries – it’s often very hard to find one that meets the expectations of the different players it is supposed to serve.
Let’s take students, for example. How can they be satisfied with their education when, after years of sacrifices, they are consistently left ill-equipped to face the challenges they’ll encounter in the job market? Why would they want to spend their time and money to learn notions of little practical use and that don’t create any value for them? Here in Hungary, more and more students are favoring work experiences at companies, like internship programs. Can we blame them?
On their part, companies hiring graduates learn quickly that they will have to spend a lot of time and money to get them up to speed. Because universities tend to teach theory, the real practical learning for the graduates only starts on day one of the job. This is very true for lean as well.
Universities are striving to change and teach certain skills that students will truly find useful, but they are still trying to figure out how. For example, teaching students how to work in teams or how to report on a real problem to a room full of top managers is invaluable, but education systems can’t provide those skills at the moment.
Every time we hear someone accuse Generation Y kids of being uninterested and unwilling to work hard, we should perhaps wonder if we are doing anything wrong in our attempts to engage them.
We had an opportunity to give our contribution to solving this issue when we were asked to run an experiment with Robert Bosch Energy and Body Systems, based in Miskolc, Hungary and Miskolc University, which started in 2014. Strong in our conviction that the lean approach to learning could fill the gap that neither companies nor universities can fill, we thought we could act as a bridge between organizations and academic institutions. That’s how the Bosch Lean Academy was born – an attempt to equip university students with the practical skills they will need once they enter the job market. They would spend eight days per semester at the Academy at Bosch’s gemba to learn the lean fundamentals.
The first thing we did was dividing the students in group – randomly, to prevent them from sticking with their friends – and asking Bosch to assign a mentor to them (that was a learning point for the company, which realized they’d have to invest more in the development of their mentors’ capabilities, like listening, problem solving, understanding the work, etc). We tied individual work with group work, so that one couldn’t be completed without the other, to teach students about working in teams.
Bosch then gave them a real business problem to solve: they had to achieve a 10% increase in productivity on the line and ensure milk runs ran on time and with the right quantity. The time on the field was spent observing, measuring and identifying countermeasures, a big challenge for the students at first: they weren’t used to having to think that quickly, and having to show the thought process behind the offered solution. Indeed, real-life experience created great learnings for everyone involved: imagine the look of disbelief on the area managers’ face whenever a university students unearthed a problem with the process!
In traditional education, assessing whether or not a student is actually learning typically happens at the end of the teaching process, when you can’t influence outcomes anymore. We designed the Bosch Lean Academy to have an assessment of progress at every step, not just at the end. Nonetheless, a big milestone for students was to present the results of their work to senior managers at the end of the semester – this is what really lit a fire in their minds. A far cry from a university exam.
For the second year, we raised the bar and introduced a new experiment: students would have to get quick wins in the first semester and complete the physical implementation of a countermeasure in the second one. Bosch gave them a line supply problem: how can they provide material to all lines just-in-time through milk runs in a 20-minute sequence for a new assembly line? The students could use the capabilities developed in the first semester to improve practically in the second semester, and they met their objective. In so doing, they contributed to the lean transformation of the company. Everybody was happy with the results.
The key learning for the company from the second year was the importance of mentoring people on the spot to help them reach their goals. It is clear that the challenge for organizations is to develop the right learning environment and ensure that leaders act as teachers (this must become embedded into the daily work of management). With the right approach, no student is left behind!
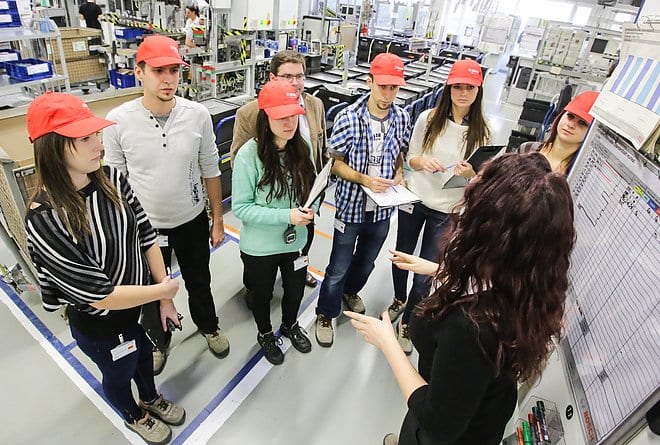
A BETTER RELATIONSHIP
We have established how both universities and companies have a lot of ground to cover before they finally start delivering the right knowledge to the people they teach or employ. To get there, they need to realize they are actually working on the same problem: the development of a person’s capabilities. Universities need to understand there is more to learning than writing a thesis, just like companies must accept that to be a leader is more than just being given a promotion. The moment universities and businesses start sharing the burden of this challenge, we will be able to move the first steps towards a better education.
This is possible if we begin to see developing people as a value chain – from one stage to another, elementary to high school, high school to university, university to first job, junior company position to leadership position, and so on. There should be a dialogue on this, to understand what capabilities are needed at what stage and who is delivering them. At the moment, this process doesn’t flow. We are batching, and we are not integrating theory and practice. The two worlds need to work together to create good outcomes for students first and employees later, and to bring out the best in them.
We talk a lot about traditional management in lean, but in the education world there should be at least as much talk about “traditional teaching”. This is just as damaging to our economies, because it is the gateway to traditional management. Most of the teachers still think in a command-and-control way, giving instructions and assessing execution. If we change the way they teach, however, we can change how people will lead in the future: academic leaders should embrace lean thinking to become better teachers, and their institutions should work with businesses to make the learning experience they offer more hands-on.
I believe that when a student or an employee underperforms or struggles, it is the system of teaching that is to blame (both in a school and in a company). Our attempt to combine the best of the university world with the practical learning one can only get on a job was met with enthusiasm by the students of the Bosch Lean Academy.
Students told us that their experience there was the highest-value part of their university careers: they liked how we (Bosch and LEI Hungary team) supported them through the learning journey and how comfortable they felt in an unfamiliar situation. This confirmed to us that learning is not just about the subject, but also about the process. We followed up again with a few of the students recently and found that many of them are still working in lean engineering positions. Working on improvements on the line is what they want to do.
Feedback from Bosch was equally positive. We asked the leaders who worked with the students what they thought of the program, and they told us that the kids were ready to start working on their second day. That’s amazing value for an organization, as the onboarding phase is often a time-consuming and labor-intensive exercise.
Lean thinking clearly has an important role to play in the transition towards an education system that combines the strengths of universities and businesses. This alternative and revolutionary way of thinking turns everyone into a teacher, fosters an environment based on trust in which learning becomes second nature, and favors a systemic and long-term view of value delivery. Albert Einstein once said: “Intellectual growth should commence at birth and cease only at death.” I couldn’t agree more, and I encourage more people in the lean community to join this battle.
This article is also available in Hungarian here.
THE AUTHOR
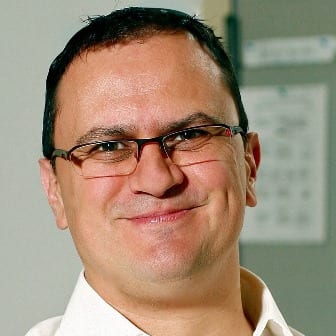
Read more
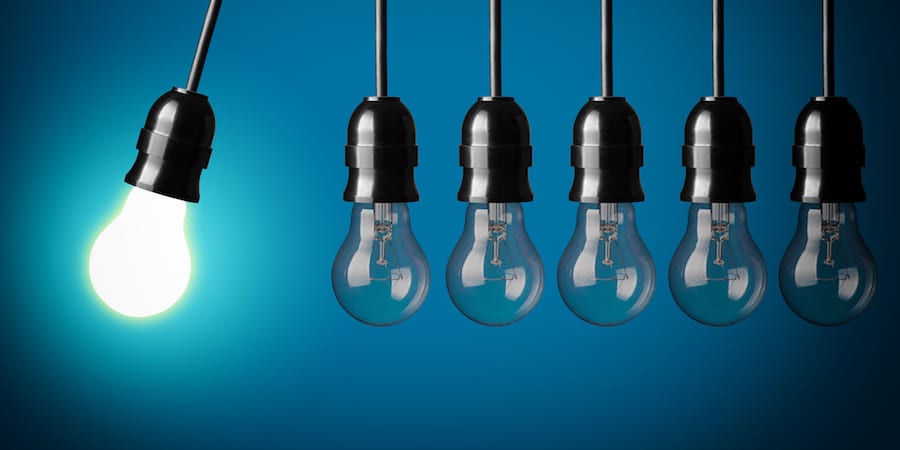
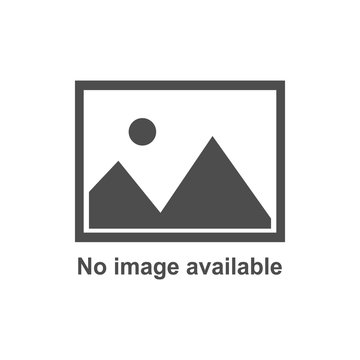
1 QUESTION, 5 ANSWERS – Without the active participation of people in improvement activities, lean is nothing but theory. Sadly, engaging folks is easier said than done. We asked five lean practitioners to share their approach to people engagement.
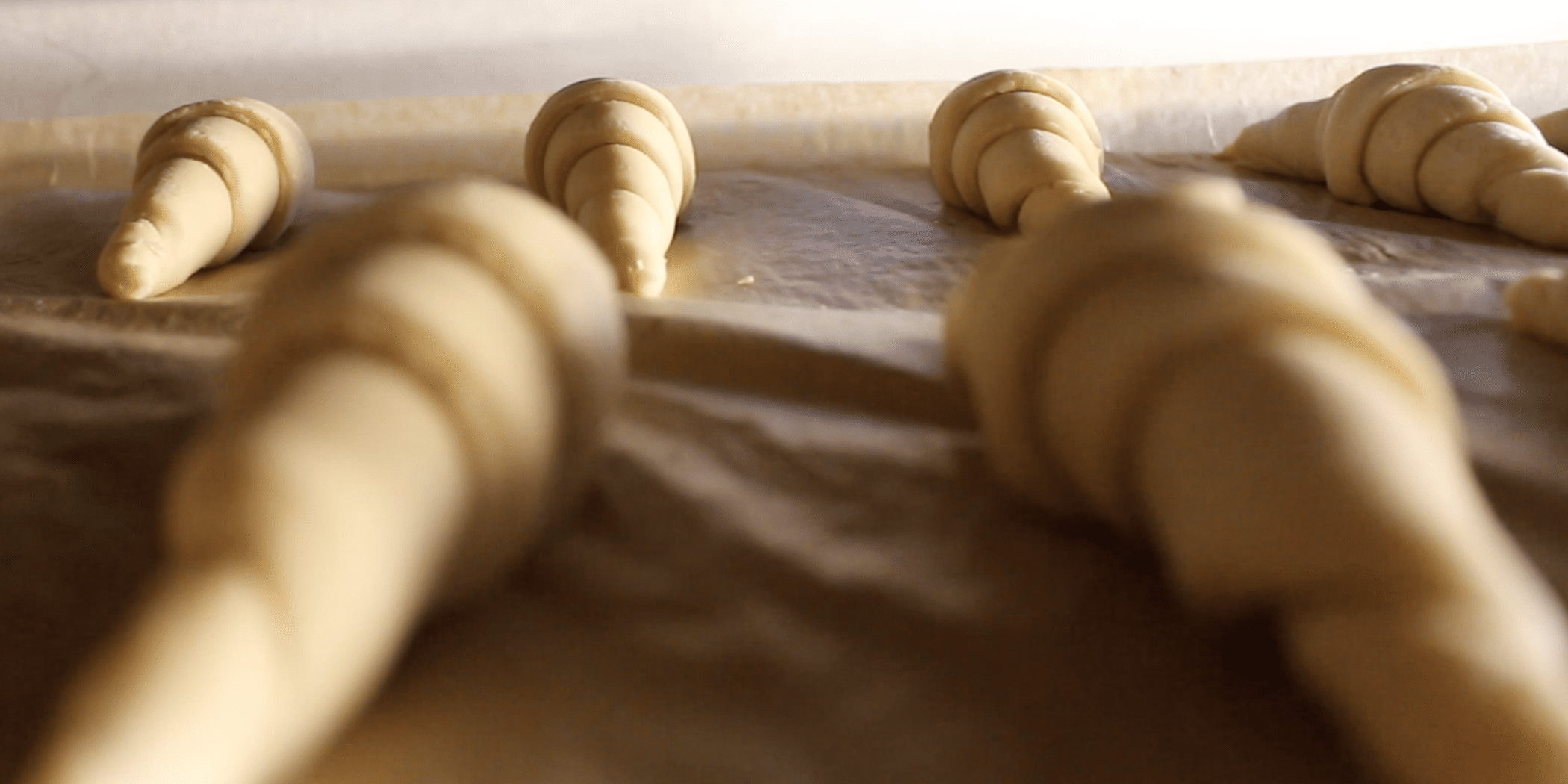
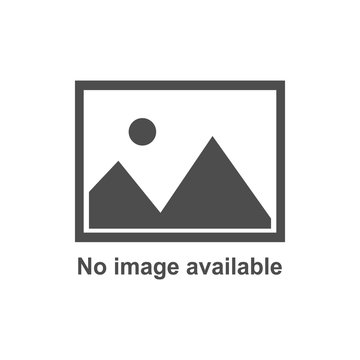
THE LEAN BAKERY – In the second video in the series, we visit the stock-free workshop of one of 365's lean bakeries and learn about quality bread, customer focus and making lives easier for bakers.
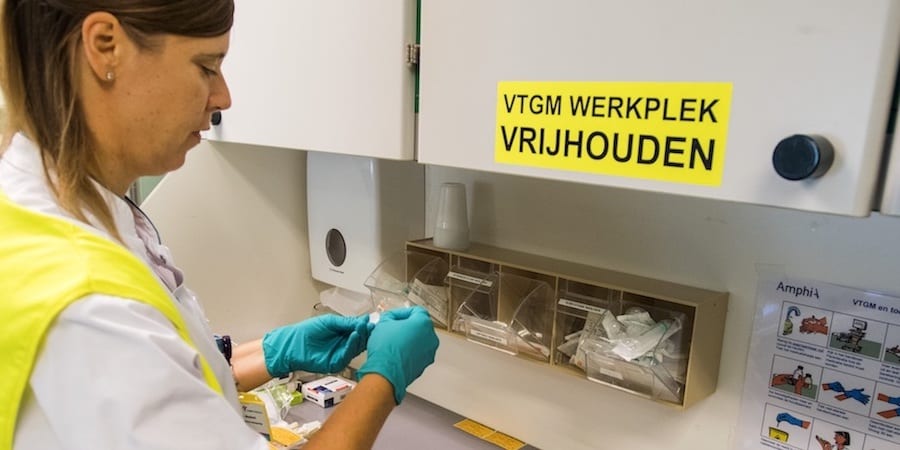
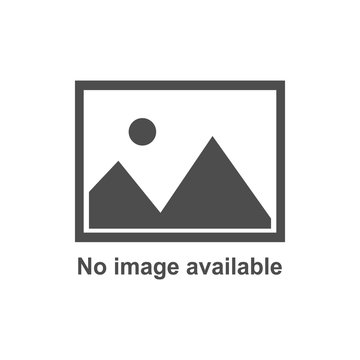
INTERVIEW – Bringing nurses together and giving them a space to discuss problems on a regular basis has allowed this hospital in Holland to successfully embrace lean thinking and reap its benefits.
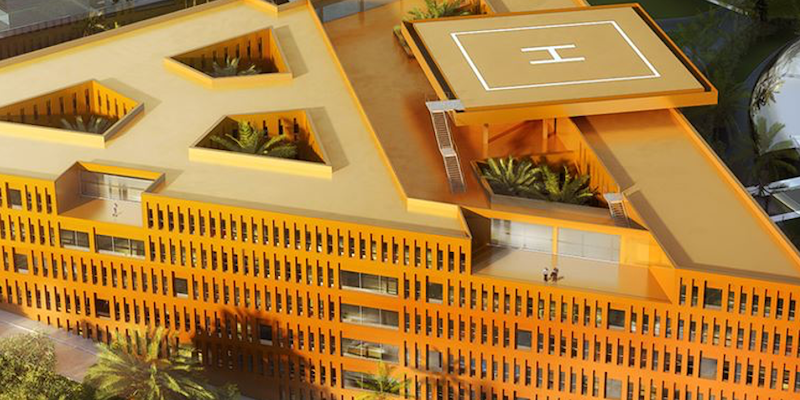
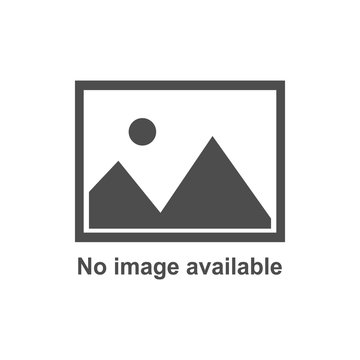
NOTES FROM THE (VIRTUAL) GEMBA – In the last of her series of virtual gemba walks, the author learns how a hospital in the Caribbean island of Martinique relied on Lean Thinking in its fight against the Coronavirus.