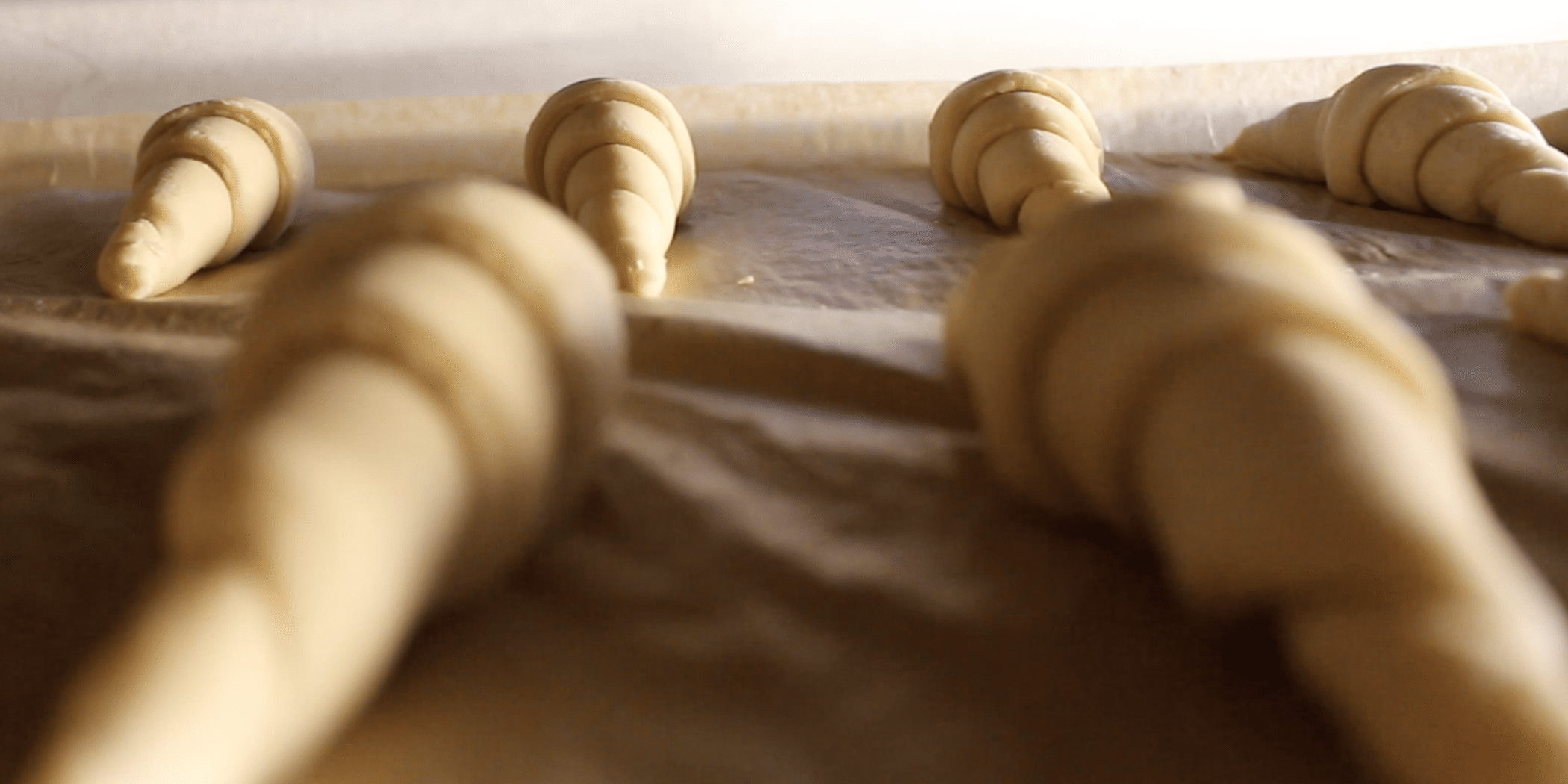
Visit the stock-free workshop of our lean bakery
THE LEAN BAKERY – In the second video in the series, we visit the stock-free workshop of one of 365's lean bakeries and learn about quality bread, customer focus and making lives easier for bakers.
Interviewee: Jesus Marquez, process engineer, 365.café
In the previous video, Emi explained how our chain of 100+ bakeries is managed using lean. Today, I would like to tell you more about what goes on in the back of our shops/bakeries.
I will show you one of our "365 Obrador" shops, a new concept of bakery that brings together show cooking, lean thinking and customer focus. In these bakeries, we make bread on site rather than having it delivered from our central workshop like we used to. The most striking thing for a newcomer might be the very small size of the workshop and the complete lack of inventory - we have learned long ago that more space always translates into more waste. We focus on keeping our supply system as efficient as possible to keep only what's strictly necessary.
Watch the video below to learn how we are ensuring we offer the highest-quality products to our customers, and how we are improving the lives of our bakers in the process.
You can read all about the 365 story in The Lean Bakery
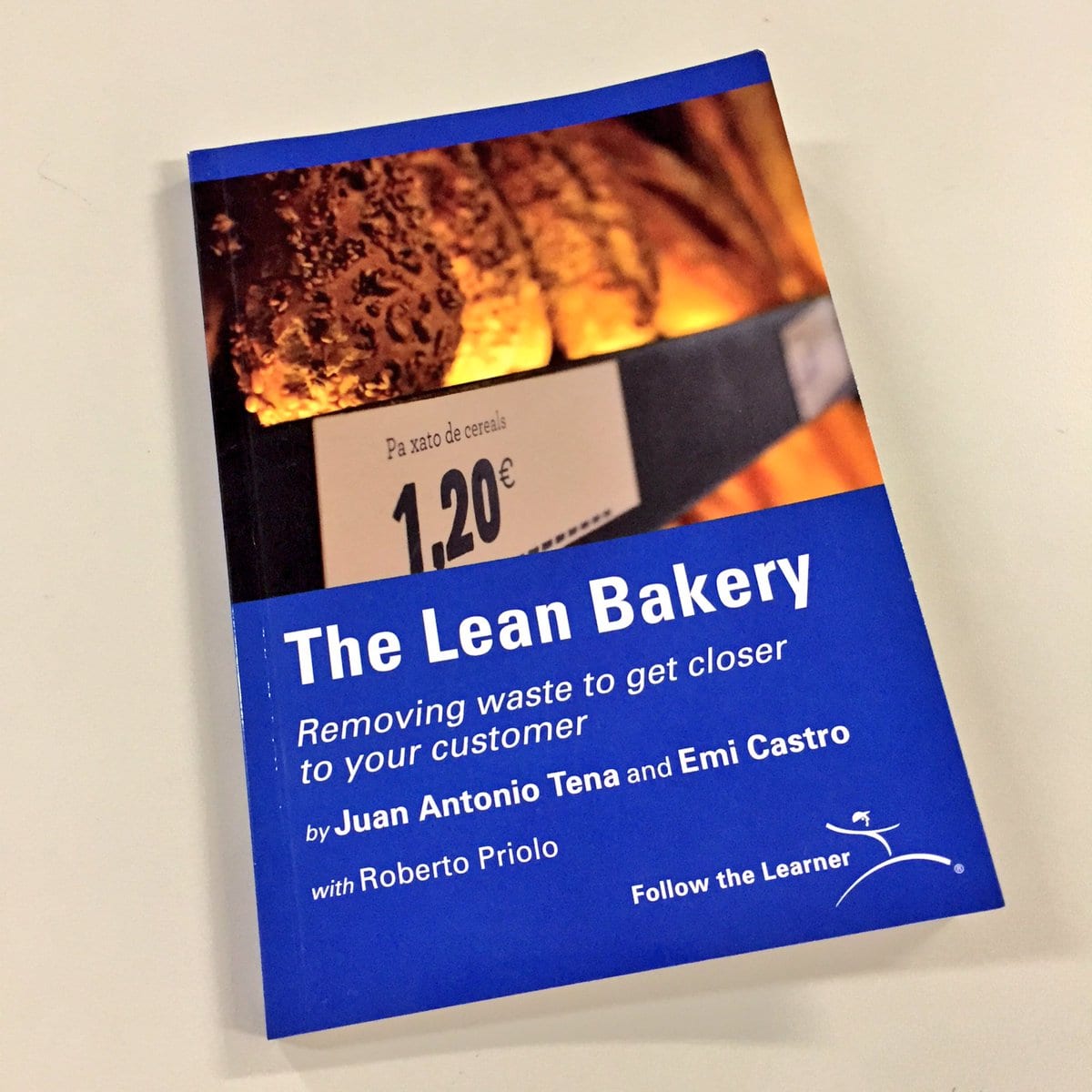
Buy your copy here
THE INTERVIEWEE
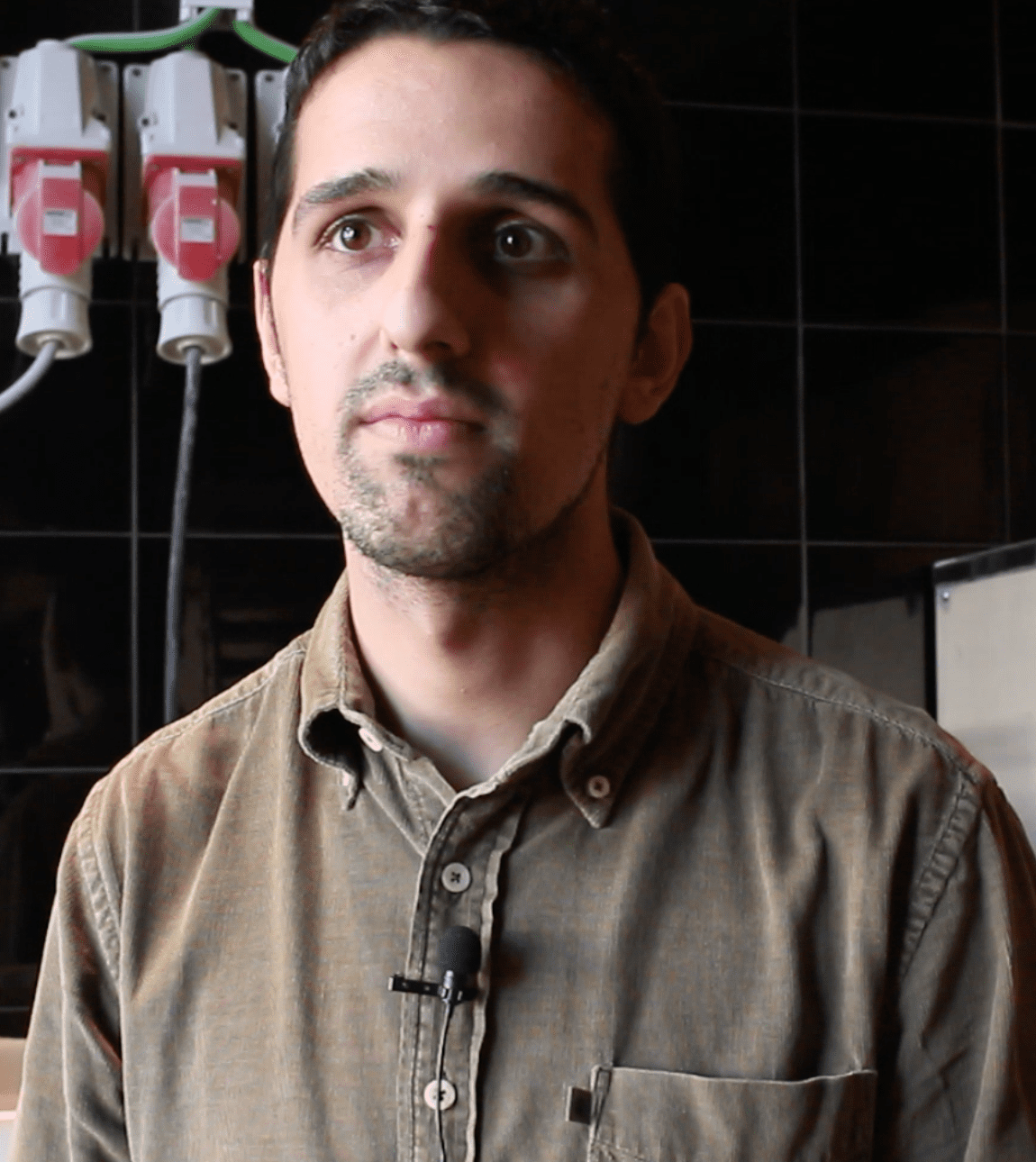
Read more

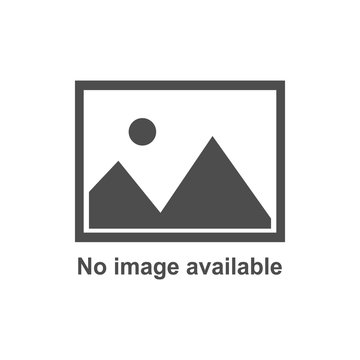
INTERVIEW – A recently-published book discusses how Lean is the only way for a company to scale while retaining an Agile culture. We talk to one of the authors.
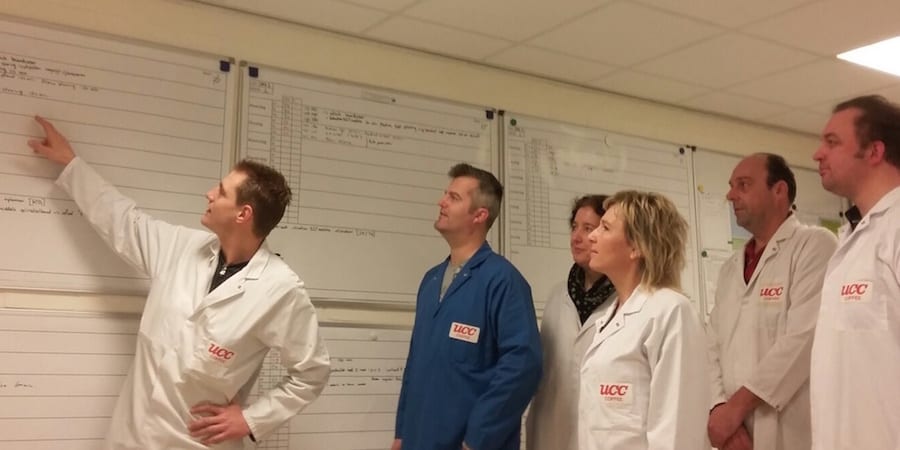
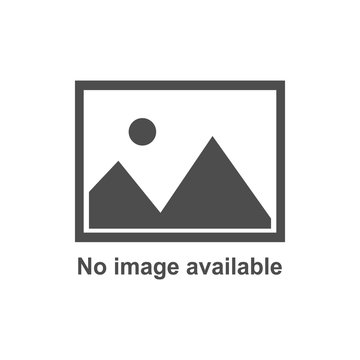
FEATURE – Repetitive flexible supply is a very effective method to level production scheduling, but as a FMCG company in the Netherlands found out, sometimes a number of conditions must be met before the approach becomes viable.
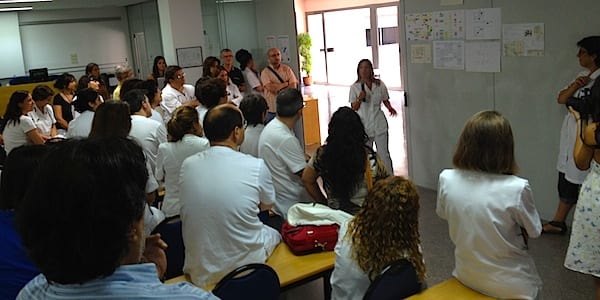
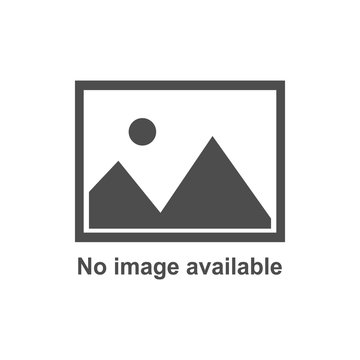
CASE STUDY - In the past two years, the Consorci Sanitari del Garraf near Barcelona experienced a lean turnaround. The author gives us an overview of the key building blocks of this transformation.
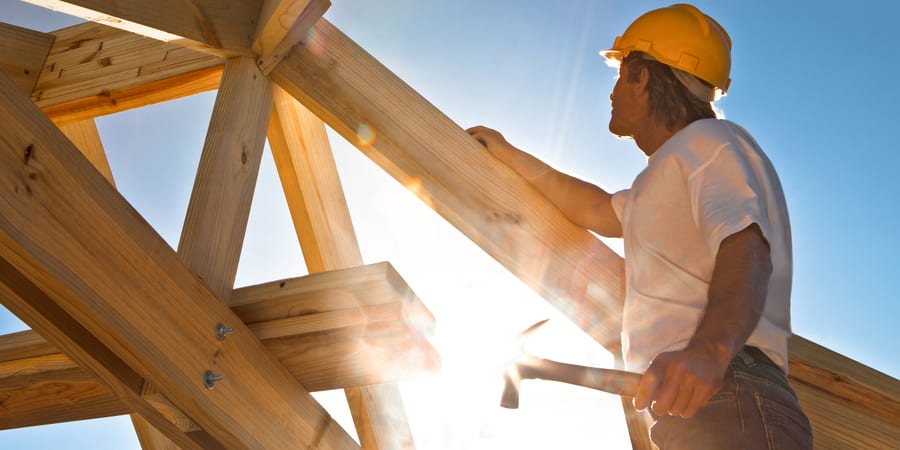
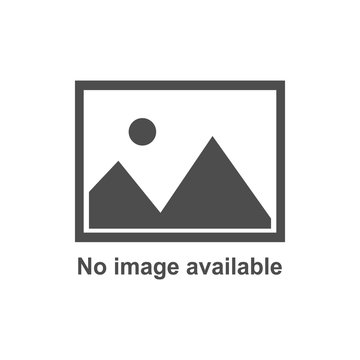
WOMACK'S YOKOTEN – Small firms represent the backbone of the economy, and there is no doubt lean can help them improve and grow – by making the jobs they offer great. Without it, countries won't be great either.