
Arnaldo Camuffo discusses what makes lean a good practice
FEATURE – We tend to take the “goodness” of lean for granted, but – the author says – we should stop and think about what makes lean a good business practice. Why is it a way of thinking all businesses should adopt?
Words: Arnaldo Camuffo, President, Istituto Lean Management and Professor of Lean Management at Bocconi University in Milan, Italy
Over the course of the last decade, two famous economists, Nicholas Bloom (from Stanford University) and John Van Reenen (from MIT), have embarked on a large global study on management practices.
They borrowed a set of “good” management practices from McKinsey and surveyed 8,000 organizations from over 20 countries and a variety of industries to understand the extent to which such practices were applied and whether they really had an impact on the companies’ performance.
The results, as expected, are rather astonishing:
- organizations throughout the world are very badly managed;
- better management and superior performance are strongly correlated with measures such as productivity, return on capital employed, and firm survival;
- management makes a difference in shaping national performance accounting for a significant fraction of cross-country productivity gaps.
This research has merit, as it shows – with strong, large-scale evidence – that “management matters”, forcing us to reflect on what prevents good management practice from spreading. Indeed, it does a great job showing the performance effects of management practices, using them to explain and predict firm performance variation unexplained by the other production factors (capital and labor). However, it says nothing about what are the inherent, fundamental characteristics of “good” management practices.
Interestingly, among the management practices that Bloom and Van Reenen borrow from McKinsey we find “the introduction of lean manufacturing techniques”. The question they fail to ask, however, is: why are lean practices “good” management practices?
We lean thinkers know that it is not because these are the “best” operations management practices, providing “optimal” point solutions (for cost reduction and quality improvement) to operational problems, but for other, more profound reasons.
We know lean practices are “good” because they embody the principles of “respect for people” and “continuous improvement” and allow for structured, disciplined, and collective problem-solving based on: careful problem framing; explicit hypothesis formulation; multiple, repeated small experiments with counterfactuals; evidence and data gathering using valid and reliable metrics; discussion and corrective criticism; and frequent and quick learning loops.
A second thing that lean thinkers know (and others don’t) is that lean principles apply to all management areas (not just operations), from innovation management and new product development to marketing and sales, from strategy to entrepreneurship. These ideas and practices are echoed in the agile, design thinking and lean startup movements and translate into concepts and tools (from visual management to Kanban, to split tests) that, albeit in different forms, are increasingly popular in management practice across organizational levels, functions and industries.
In some large established firms, management practices inspired by these principles have even become comprehensive management systems, as in the cases of Danaher, Wipro, Alcoa, Wiremold, Lantech, Kimberley-Clark, Parker Hannifin, Textron, Illinois Tool Works and many others.
A third thing that lean thinkers know (and others don’t) is that management practices based on respect for people and continuous improvement are “good” because they require disciplined recurrent behavior (and are therefore somehow “disturbing” routines, allowing us to remain open to change) and a dual, do-as-you-learn and learn-as-you-do approach so that managers and their teams can simultaneously decide, solve problems and develop capabilities. This also explains why it takes time and effort to adopt them and why so many organizations remain badly managed.
In sum, what makes management practices “good” is the fact that they embody elements of the scientific method (epitomized by Edward Deming’s PDCA cycle), allowing managers to behave more like scientists and making organizations more like “communities of scientists”.
A final thing that lean thinkers know (and others don’t) is that lean practices are not only good for the bottom line, but also benefit employees, business partners, communities and the environment. In a recent article in the Economic Journal, Bloom and colleagues found that establishments in better-managed firms are not only more productive but also significantly less energy intensive, contributing to lower greenhouse gas emissions. Similarly, in a recent paper published by Management Science about Nike suppliers across 11 developing countries, Richard Locke (from Brown University) shows that the adoption of lean practices improves working conditions and leads to better compliance with labor standards. In another study of Pirelli tyre manufacturing plants worldwide, published in the Journal of Business Ethics, Federica De Stefano (from our own Bocconi University) shows that lean practices improve occupational safety, reducing injuries, especially when production department managers empower workers and lead by example.
In today’s hyper-uncertain world, plagued by all sorts of irrationalism, it makes perfect sense for managers to resort to management practices grounded on respect for people and continuous improvement. They are the only compass we have to navigate social, technological and market complexity, solve problems along the way, and learn continuously.
THE AUTHOR
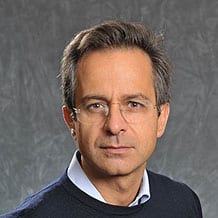
Read more
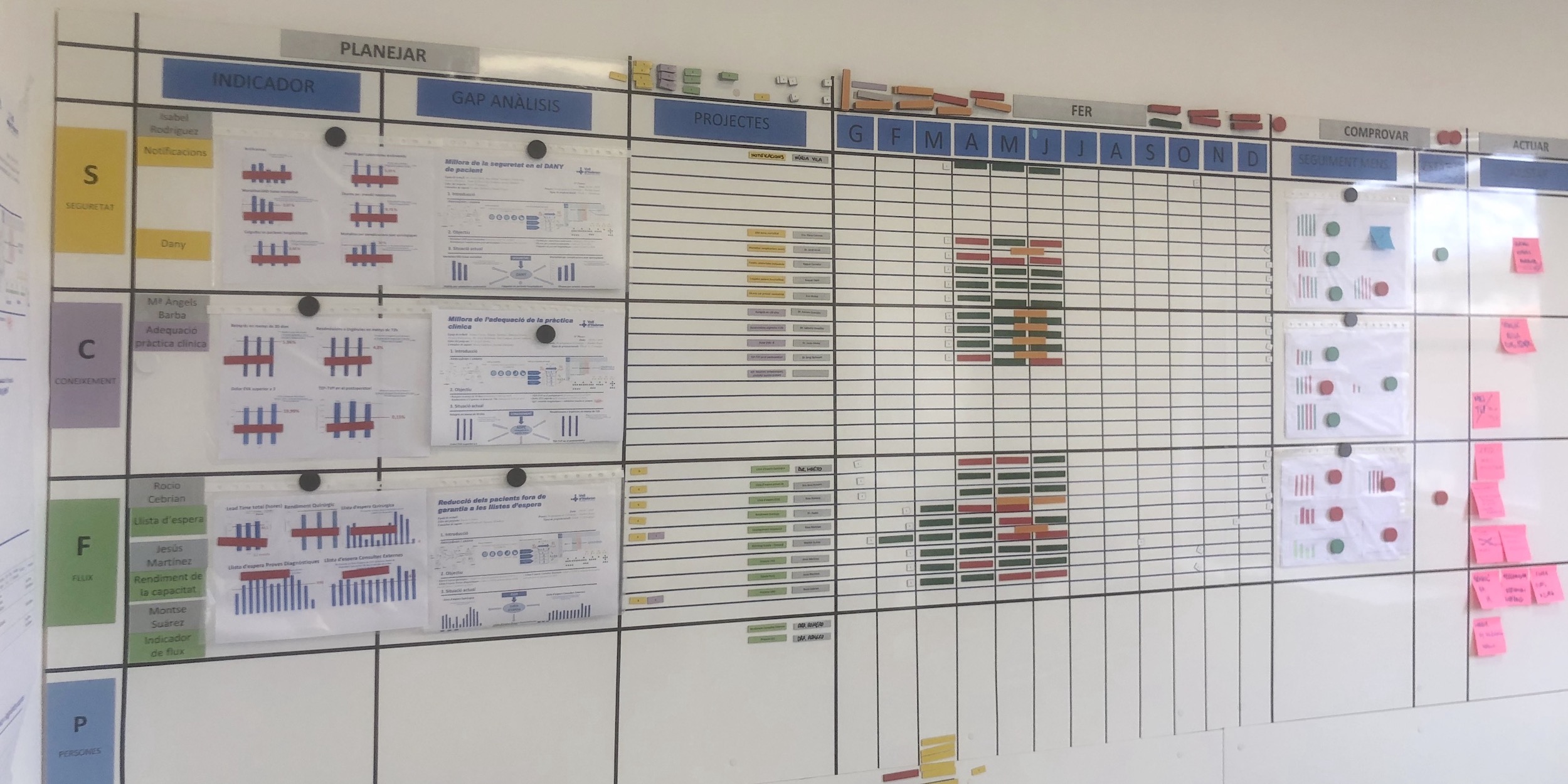
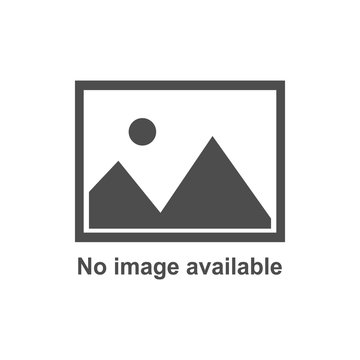
CASE STUDY – Catalonia’s largest hospital is undergoing a successful transformation – supported by pioneering hoshin experiments – that has already turned it into a poster child for lean healthcare in the region.
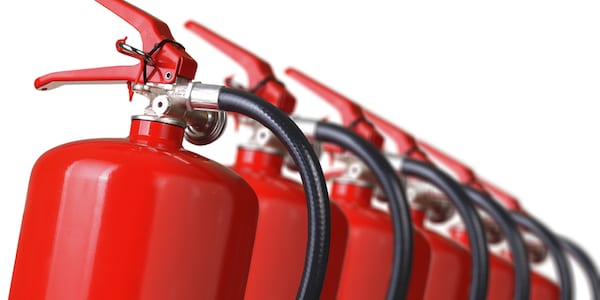
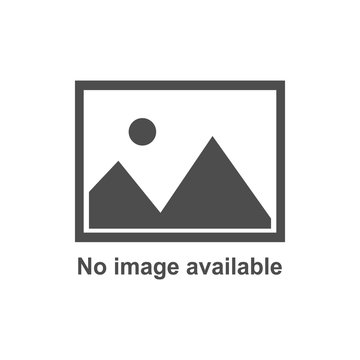
INTERVIEW - Eric Ethington shares what he has learned about lean thinking implementations during his 30-year career holding positions at General Motors, Delphi and Textron.
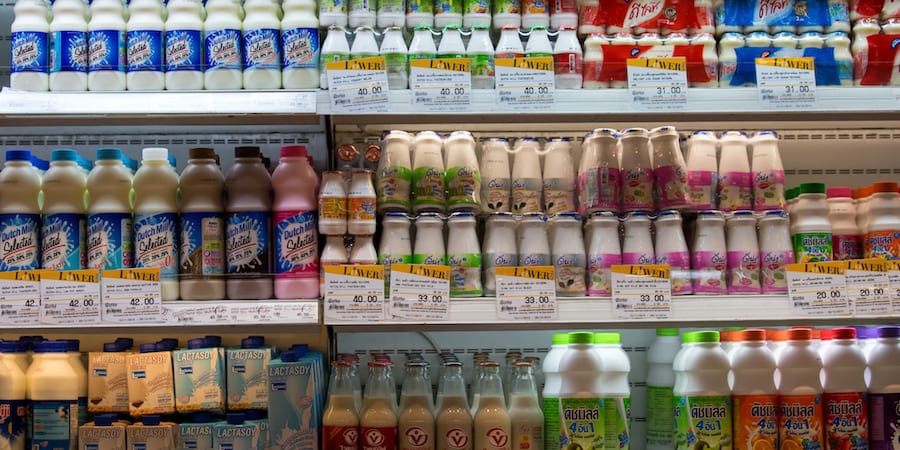
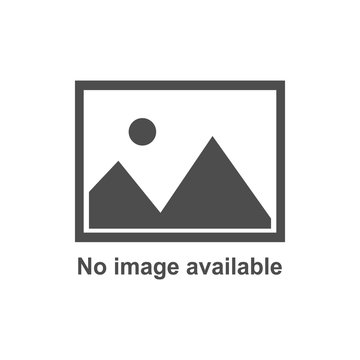
FEATURE – We often think that making every product customers might want – no matter how little they sell or how much complexity they add to our schedule – is inherently lean. As Toyota understands quite well, however, it is quite the opposite.
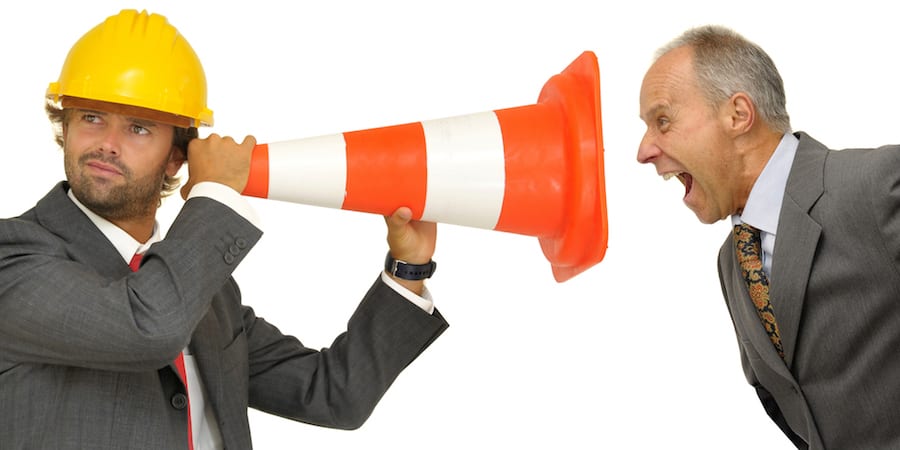
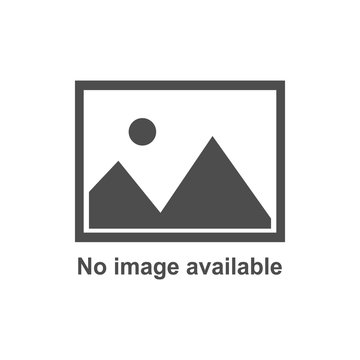
FEATURE – Lean has now been around for quite some time, and its impact on business world is hard to dispute. But what does it tell us about traditional management practices?