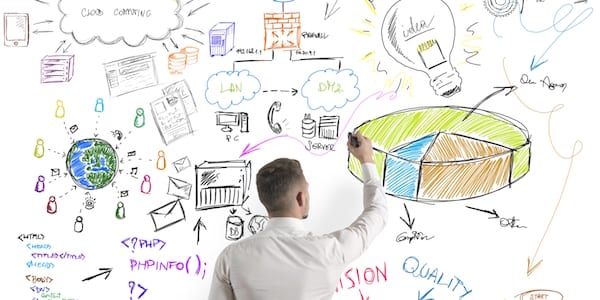
A CIO's journey towards lean thinking
COLUMN - For her latest column, Sari Torkkola describes the initial steps that must be taken to move towards becoming a lean CIO and warn us against some of the pitfalls along the way.
Words: Sari Torkkola, CIO, Patria
“Oh, you have an Oobeya room!” People seem overwhelmed when they first visit our site and see how we have visualized our operations. Unfortunately, when watching the current visuals they can’t see the steps we have taken in the past four years to get to where we are today.
Because people often seem intimidated, and as a consequence reluctant to even start improvement experiments, I have thought it would be good to write a bit about the things that I wish I had known when I started off.
If I could give my old self some advice on how to set things in motion in a chaotic, non-lean environment, I would probably share the following four tips.
1. CHANGE YOUR OWN THINKING
The success of the transformation will depend on your own thinking and discipline. You need to become familiar with the difference between traditional management and lean management. Some call this difference a “switch in values”: flow efficiency over resource efficiency, learning over execution, facts over opinions, system level reasons over blaming individuals, and customer value over organization-chart hierarchy.
Find yourself someone experienced in lean thinking who can teach you and discuss with you. This is relevant because lean consists of principles that are against your current beliefs about what makes management and leadership effective. To really grasp the difference in thinking that comes with adopting lean, I recommend you check out Dr. Deming’s System of Profound Knowledge: understanding variation, appreciation for a system, creating knowledge with the PDSA cycle and psychology. You’ll need all of these.
You should start thinking of your actions as a series of small experiments that all end with a reflective moment before continuing to the next one. Take baby steps and expand gradually: try everything by yourself first, then with your trusted managers, then with one team, then with a department, then take the customers along, and after them vendors or subcontractors. This way, you keep learning but the risks are mitigated and you have the ability to solve any obstacles that may come your way. Your lean journey is not linear; its shape is more similar to a spiral.
Beware! You are about to lead a group into a zone of great discomfort, and extra care is called for.
2. CHOOSE THE PROBLEM YOU NEED TO SOLVE
My urgent problem was the overburden of staff and the increasingly unsatisfied customers. What are your pressing issues?
Once you have identified the problem, spend time to understand its current state. Visualize it, go and see what’s really happening and create your first metrics. There are several useful tools to apply at this stage, like gemba walks, A3 problem solving, kanban boards, value stream mapping and statistical process control charts (nowadays, I don’t think you need to start using lean tools in a specific order).
Experiment and stop after each trial to consider what you have learned and how your perspective of the problem, your personnel and your organization has evolved. Resist the urge to solve the problem quickly at this stage. More importantly, be ready for a shock: inevitably, the situation is worse than you thought at the beginning.
From a learning point of view, I find my lean journey to be like a circular railway: you jump on the train at one of the stations and eventually go full circle and end up where you started, getting deeper and deeper in your understanding at every trip.
3. ACCEPT CHAOS, DRIVE FOR STABILITY
If you don’t already have your processes in statistical control or you don’t understand what this means, I bet you’re building on a chaotic foundation. The bad news is that you cannot fully improve chaos. The good news, however, is that if you manage to at least bring some stability to it, your customers will be surprised and pleased. Stable IT service processes are, unfortunately, very rare.
It took me a while to really understand what chaos and stability mean in practice. When statistical process control charts were introduced, they totally changed my way of seeing the operations and transformed the focus of the team. I organized the daily study of incidents above the statistically calculated control limits and stopped wasting time in explaining noise; which were, in other words, results inherent to our current way of working. Seeing a process as a statistical distribution of events rather than a detailed list of actual tasks organized in a series is not obvious, but it does make managing easier.
The symptom of overburden was a consequence of variation, which was now evident. When we learned to see it and attack it, we achieved speed in the services and better performance.
At first, it’s important to study your operations as a black box: analyze demand going in and compare it to the output (completed tasks delivered to customers). This is faster and more efficient than trying to describe exactly what the inner workings of the box are. It is also a very useful perspective when you start to analyze the performance of your subcontractors. This way you don’t use your time finding out details rather than understanding the overall performance.
4. REORGANIZE AND COACH
It is your responsibility to organize the work. The current way is probably not aligned with lean principles or with the end-to-end-processes through teams. Be ready to reorganize when you have enough insight on both. Start daily reflective meetings, make people stop after each cycle and figure out what actually happened i.e. what we learned.
Teach lean principles in all appropriate occasions and learn to coach (see kata coaching). If something does not work, don’t worry too much - it was only the result of that one experiment. Learn and move on.
It’s the system that creates the problems, not the people in it. Fortunately, as a CIO you have the power to modify the system: policies, organization, competencies, IT systems, tools, methods and metrics.
On the other hand, IT is only one part of the whole system. Accept it. Show results and others will follow.
WHAT YOU DID NOT SEE IN MY LIST
I see IT as a service function and that’s why I don’t recommend using popular manufacturing lean tools like 5S or starting with waste hunting. Tools have been developed to solve problems. If you understand the principles, you can alter the tools accordingly and even create your own. Remember your goal. If you apply 5S and for example make your staff clean their desks, is that an actual improvement of customer satisfaction or of the speed in providing your services?
Try to always understand the relationship between cause and effect for all your actions. That is at the heart of lean thinking.
THE AUTHOR
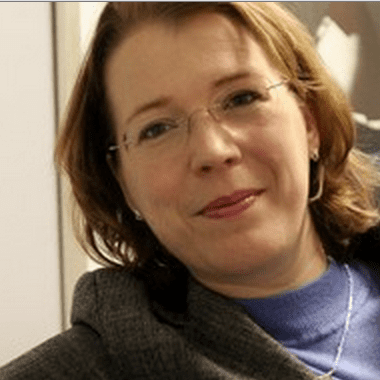
Read more
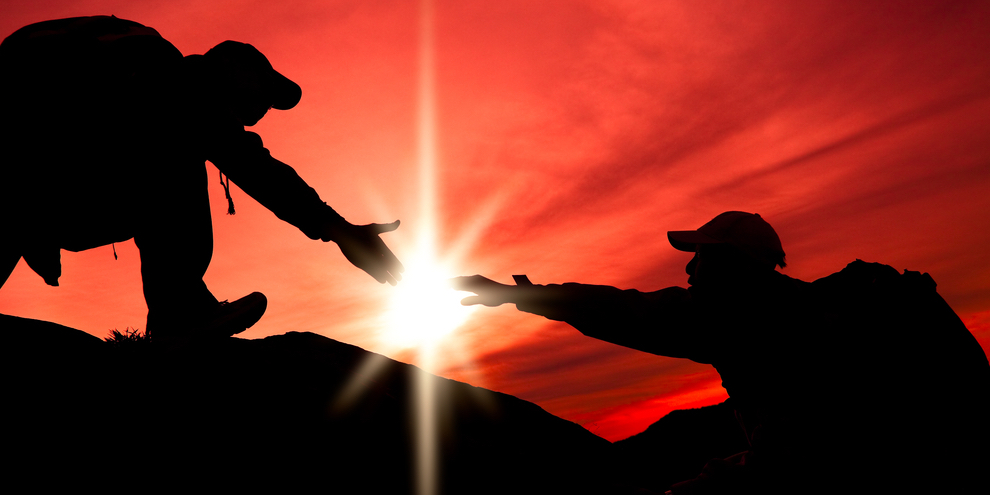
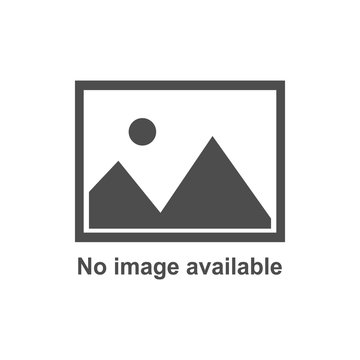
FEATURE – What does it mean to be a lean leader? Our editor tries to answer this question by searching the Planet Lean archives for the best nuggets of wisdom from our authors.
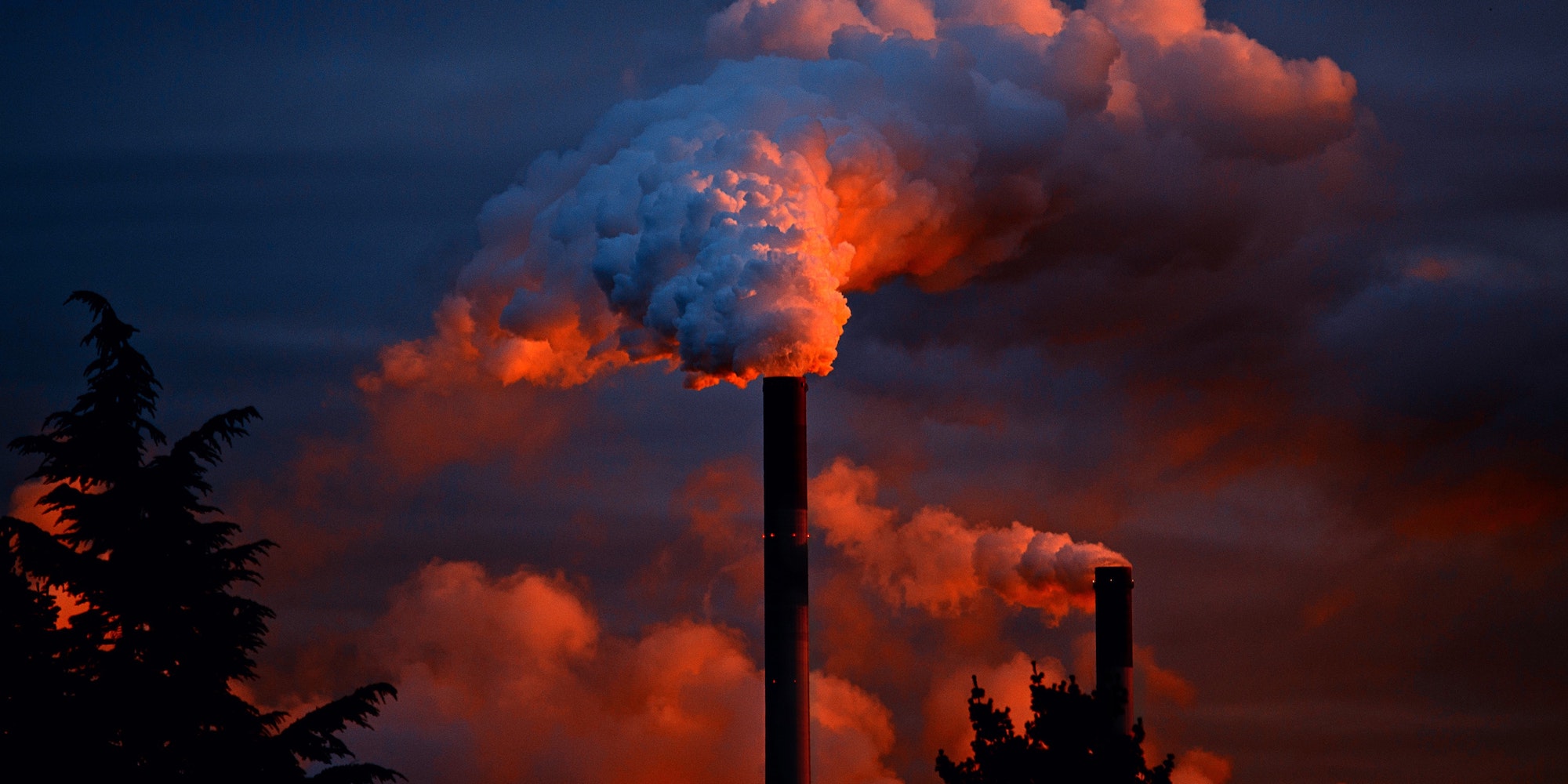
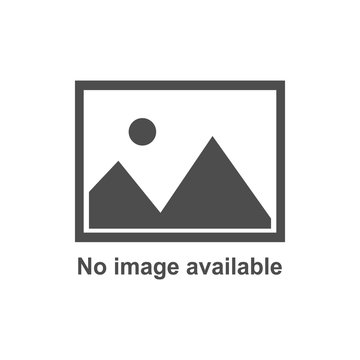
FEATURE - Imagine targeting a quarter of the world’s greenhouse gas emissions by setting our lean minds to it? The authors discuss building better, circular supply chains and designing sustainable products.
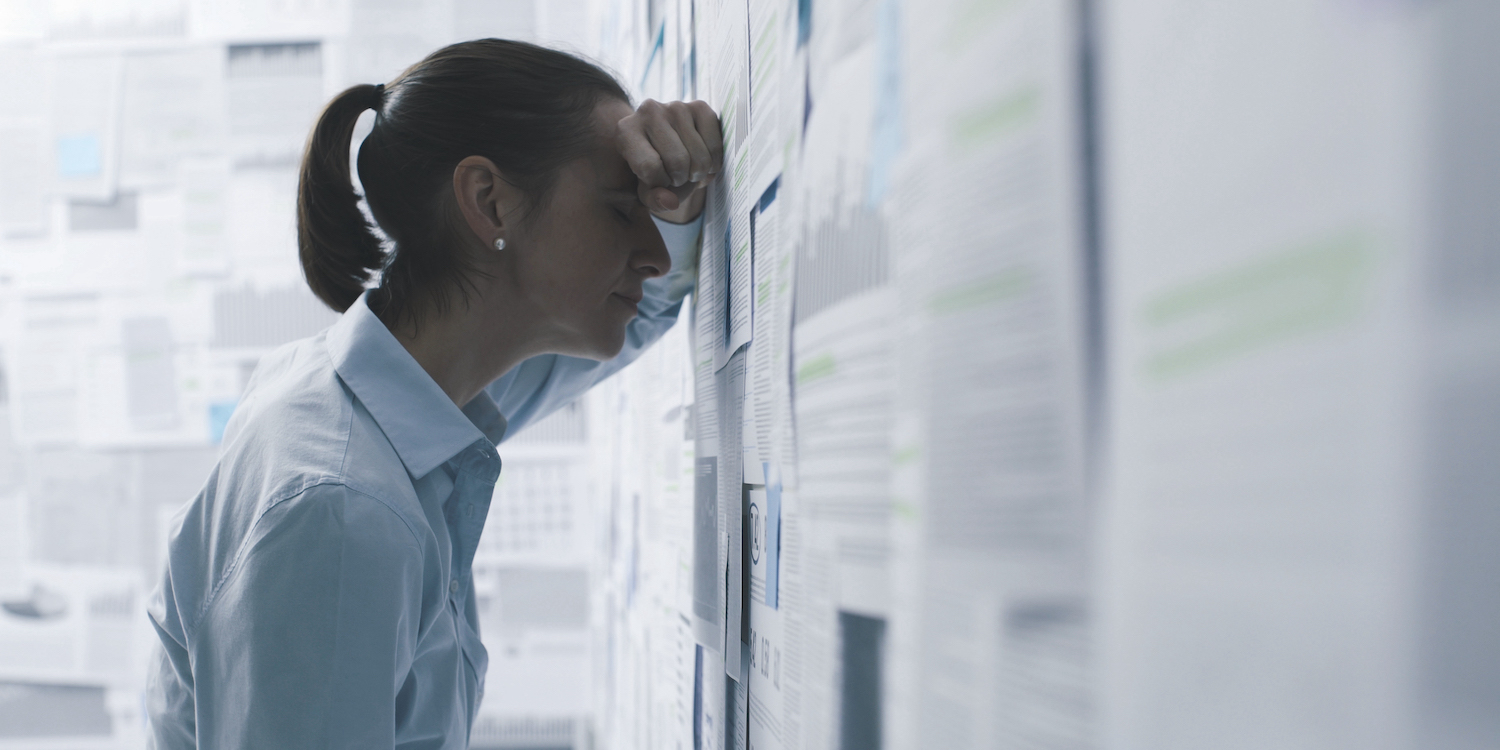
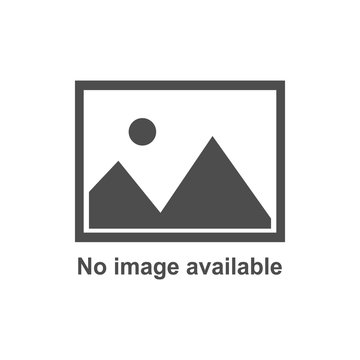
FEATURE – In this article, you’ll understand how potential errors can become an endless source of personal and managerial growth.
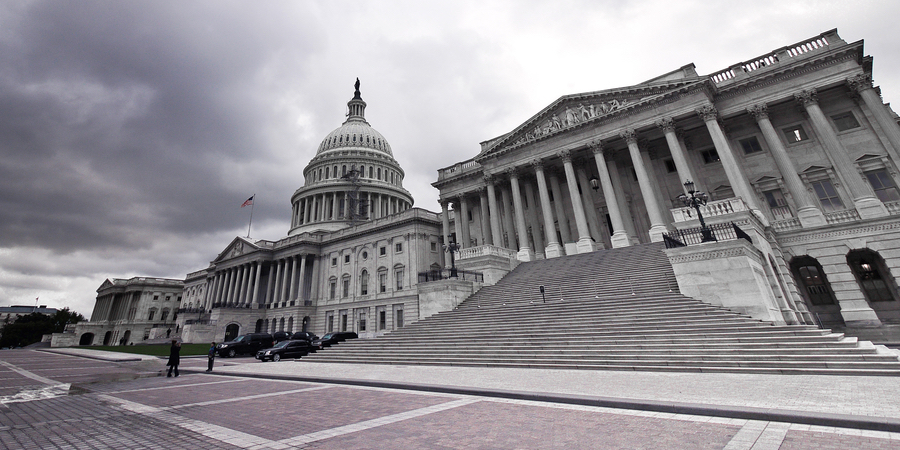
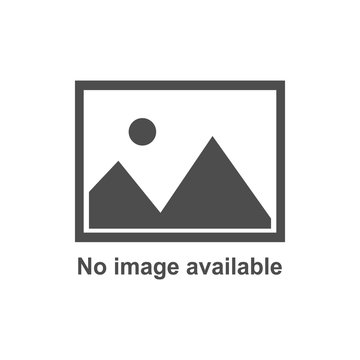
INTERVIEW – In another interview in our series that looks at global events from a lean perspective, we discuss politics, the challenges to democracy and the phenomenon of populism.