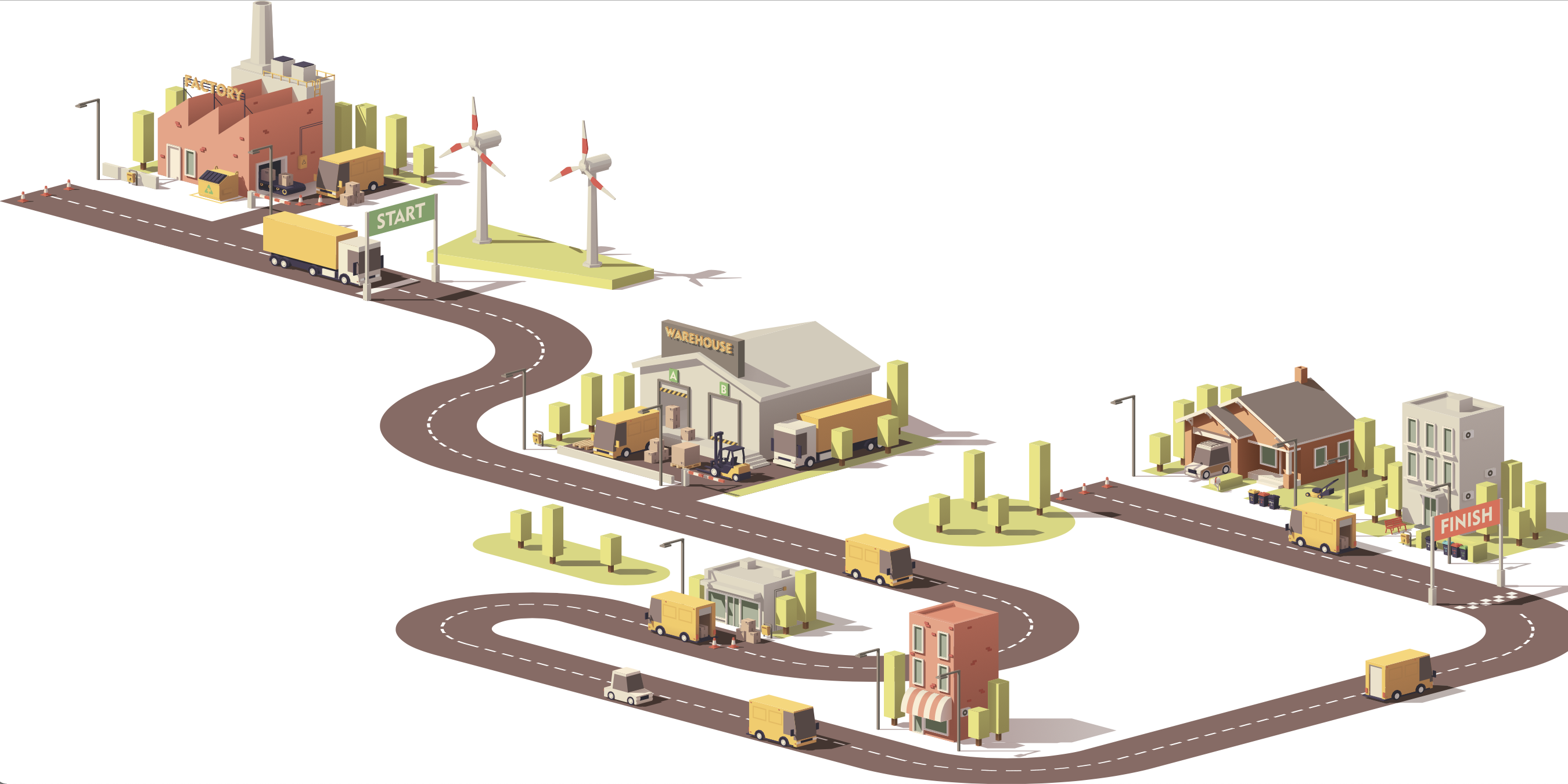
Bringing Dantotsu quality improvement to parts makers
FEATURE – Improving supplier quality and reduce defects was an important part of Toyota Industries Corporation’s (TICO) Dantotsu activities since the very beginning. In this article, the author visits two parts suppliers.
Words: Toshiko Narusawa
Originally published in Kojo Kanri (Factory Management)
KAMIZEN
Kamizen specializes in metal stamping and laser sheet metal processing for a wide variety of applications. Demand can fluctuate wildly; the company’s specialty entails small quantities and short delivery times.
At the end of 2014, Kamizen received the Toyota Industries President's Award, and the following year it completed a new laser machining factory. Stepping into the site, you immediately see Mr. Nomura's Quality Management Board and designated area for Defective Product Storage. These tools clearly visualize the current quality situation including weak points at three levels: company, department, and each department.
I was surprised to hear that the target for the number of defects reaching Toyota Industries Corporation had been set to zero for the previous two years. It wasn’t reached, but it encouraged people to dive into each potential cause and come up with possible countermeasures. That’s why the target was set to zero for the following year as well.
Despite there being around 1,700 SKUs , workers had a “master sample” at hand, helping them to perform a predetermined quality check. Master samples are good products – meeting all technical specifications – fabricated in the early stages of production, painted in bright blue so they can be easily distinguished. In these types of products, the press dies or molds will gradually deform due to wear. Failure to notice when the life of a die is exceeded will result in a large number of defects rolling off the line. As obvious as this sounds, not many sheet metal makers do well with this. To tackle this and keep quality high, Kamizen relied heavily on standardized work – which I noticed all around the factory. (For example, it was clear that the Dantotsu standard for 2S was implemented throughout the site: “Anyone can get or return what they need within one second in the process and within one minute in the shop”.)
Another key activity Kamizen was focusing on is Simultaneous Engineering (SE) for creating operations manuals. The company manufactures products based on the drawings that come from Toyota Industries, but when a design is particularly challenging, the process will initially often generate waste and the quality won’t be consistent. Design changes can fix such problems, but they come at a cost. Kamizen shared its processing know-how with Toyota Industries by means of an SE manual, which established a common understanding with Toyota engineers. This meant that they began to incorporate more manufacturing requirements into drawings from the beginning. Between 2013 and 2014, this led to a significant drop in the number of design changes after drawing.
Sharing learning and insights brought great benefits to both companies. When I visited, it seemed that the sailing has been smooth until then, but it was very painful during the Lehman shock. With less work, they spent about half a year studying the process one day a week. During that time, Mr. Nomura provided intensive guidance, mainly to young members of the company along with plant managers, which aligned perfectly with the company's policy to develop the next generation and led to quality improvement later. A big factor in the success of the initiative was that they were willing and eager to give it a try. This attitude helped the team to finally realize that while they had been confident that they were successfully engaging in successful kaizen all along, their points of view had been misaligned. Newfound deeper and aligned understanding led to true and steady kaizen.
ANDO IRON WORKS
Machining specialist Ando Iron Works has been supplying Toyota Industries since its inception. Thanks to its flexibility, the company is able to provide a variety of products in small batches – which was key to its growth. Ando Iron Works has a factory full of state-of-the-art equipment in Toyota City, as well as its main factory in Kariya.
When the management team receives one of Nomura’s handwritten memos, they first read it carefully and try to understand the content. Naturally, if we don't understand deeply, we can't properly lead the organization. We compile a list of all improvement items and categorize them between completed versus uncompleted so we can focus on the incomplete items to make steady progress.
“Looking back on our Dantotsu quality improvement activities, it all started with the bane of any machining shop: chip management. In other words, I had to work from the basics of the basics, " said a female manager, with a smile, pointing to the chip management shelf. It is said to be the basic of the basics for machine shops, but there are many companies that are simply not able to manage this. The tool rack, which took three to four years to complete, was also in good operation. There was no metal scrap. It can be said that it is one of the best “clean” machining plants in Japan.
With five different changeovers per machine per day, there was an urgent need to improve setup time. Now Kanban cards are picked up at the dedicated production scheduling board – in order of shipping – and the corresponding instruction sheet is taken from the shelf, which ensures that the right tools are sourced to process the work and complete the changeover swiftly and smoothly.
Investigation into defects proved that there were many instances of workers not following standardized work. When asked why that was, many of them replied that it took a long time for them to find the standardized work sheet and that they’d rather rely on their memory. (This is the reason Nomura-san was very strict about, among other things, “one-shot retrieval” – never searching around, never going more than once to retrieve a needed item.) Following the standardized work means that people can concentrate on the process and their operations without strain and that the work just flows. This is of course easier said than done, and it’s clear how much effort and patience it took to reach this point.
The team developed a chuck jig that can be attached and detached with a single bolt to shorten the handling time and attached a pulling mechanism to catch the processed product. This increases the time that people can be separated from the processing machine. Machining operations require a high degree of knowledge and specialized skill so tend to rely on individual capabilities. Every company struggles with how to share know-how. Aware of this, Ando Iron Works exerts great effort to reveal individual technical know-how by visualizing it on a board. In addition, as with the Kamizen example above, this experience was utilized to incorporate manufacturing requirements at the design stage.
From the perspective of Toyota Industries Corporation, working with suppliers and providing designs that are “easier to make” makes perfect sense. In the past, suppliers would be grateful when problems were highlighted before volume production started but did not have the time to tackle them all prior to start of production. Now, in contrast, a virtuous cycle has been created. Nomura’s method was incorporated into Ando Iron Works’ modus operandi. Not only does this ensure the company makes products of a superior quality, but it also helps workers – in the face of what is at times very hard work – find a great sense of accomplishment in their jobs.
Nomura-san's new book is out now! Read about the remarkable quality revolution he led at Toyota Material Handling sites and learn about the Dantotsu method in great detail.
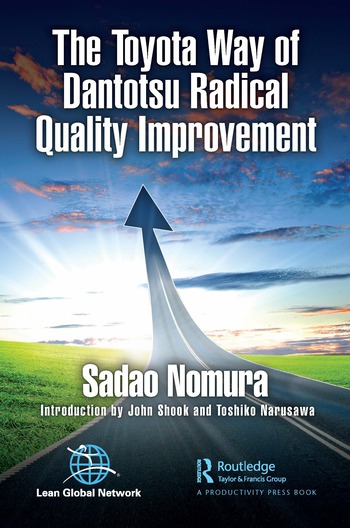
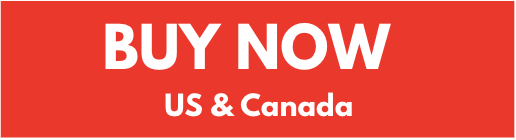
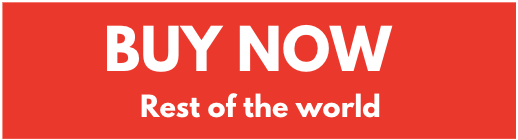
THE AUTHOR
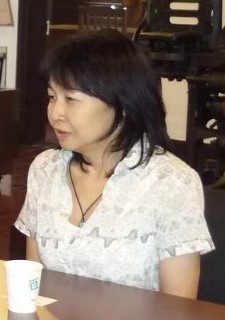
Read more
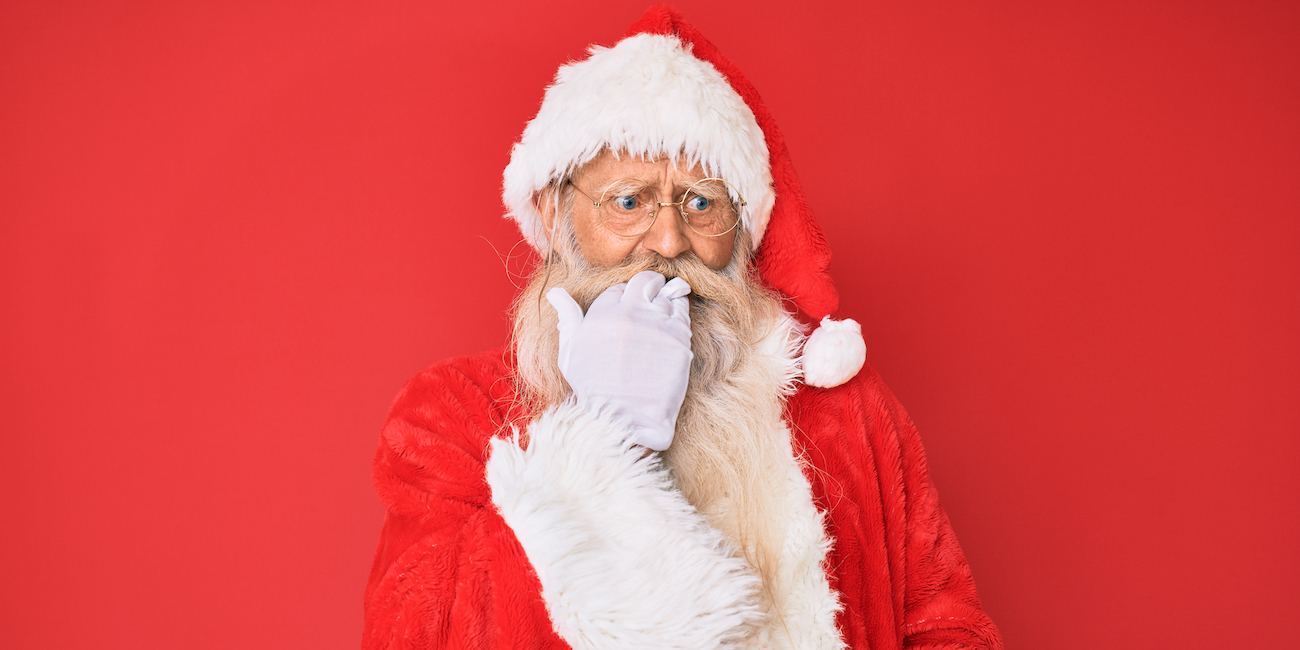
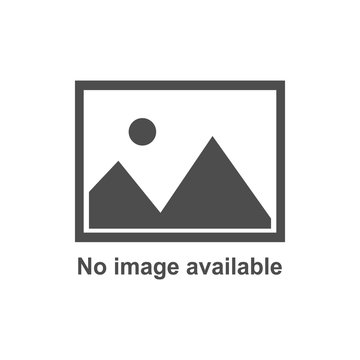
FICTION – The pandemic is throwing curveballs to us all, including a certain bearded gentleman who lives in the North Pole – until a magic “time-bending” solution is presented to him, that is.
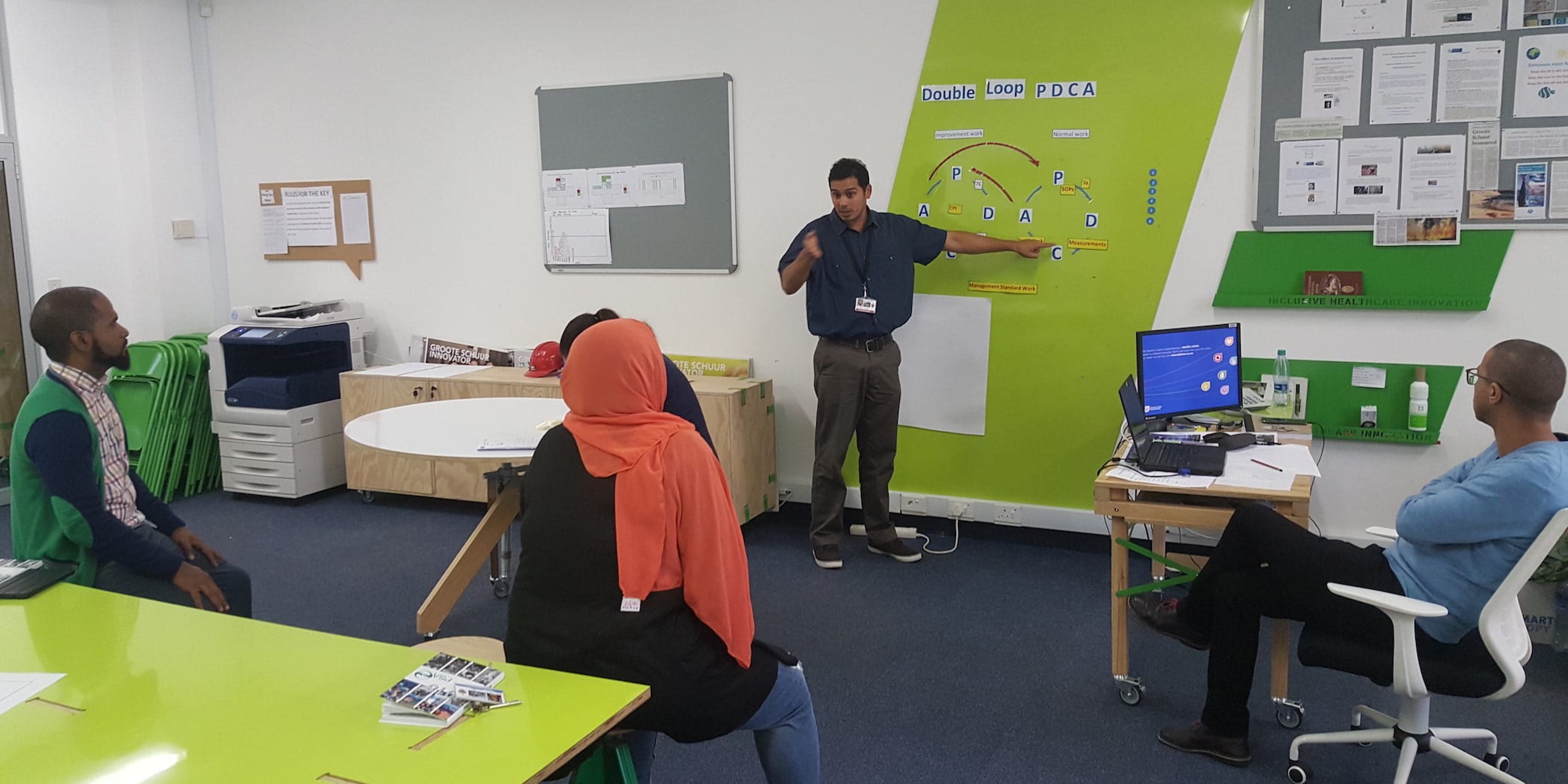
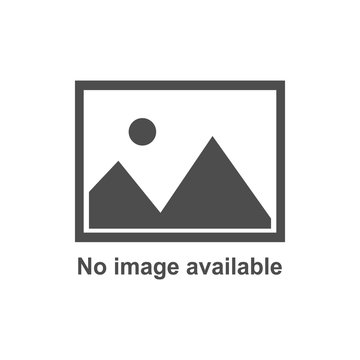
FEATURE – How “Double-Loop PDCA” was discovered due to a problem with implementing a lean daily management system in a South African hospital.
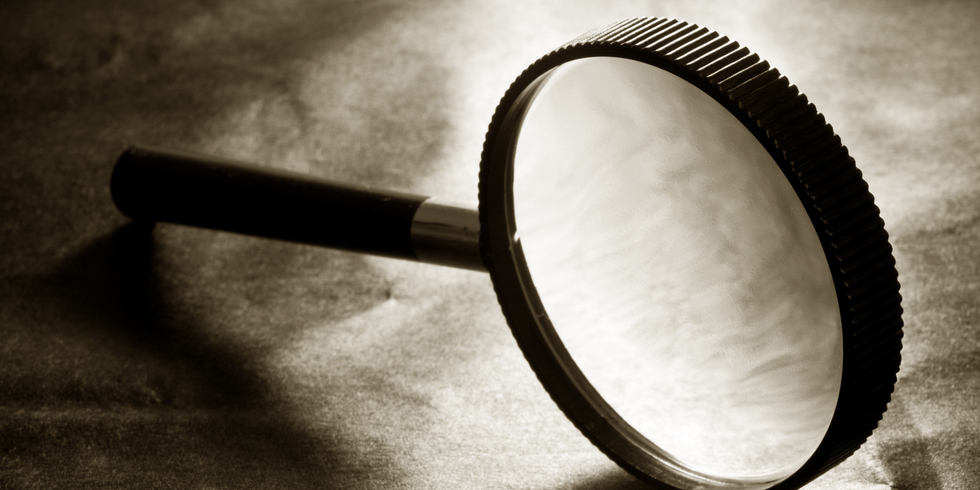
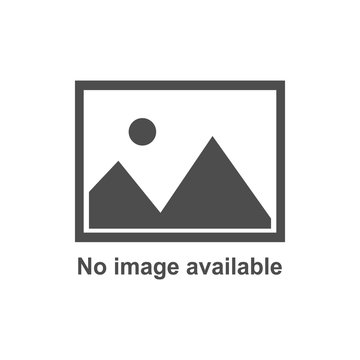
FEATURE – As we progress on our lean journey, results seem to become harder to achieve: it’s because we need to become more granular in our analysis and improvement of the work.
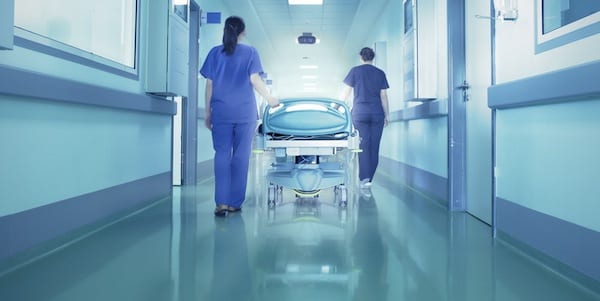
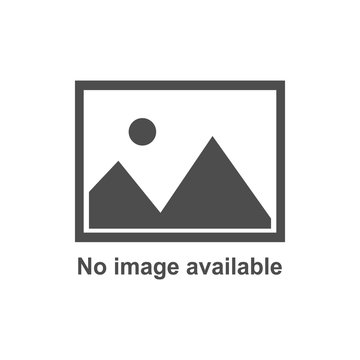
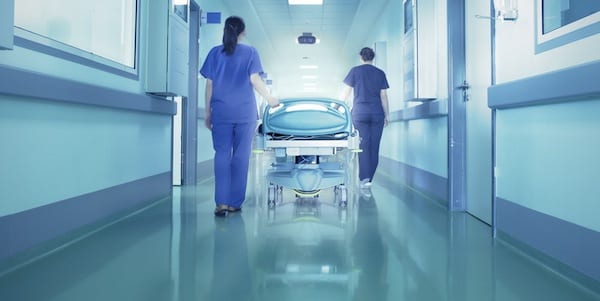
CASE STUDY - This article reports on the efforts that Erasmus Medical Center in the Netherlands has made to apply Theory of Constraints to patients' length of stay.