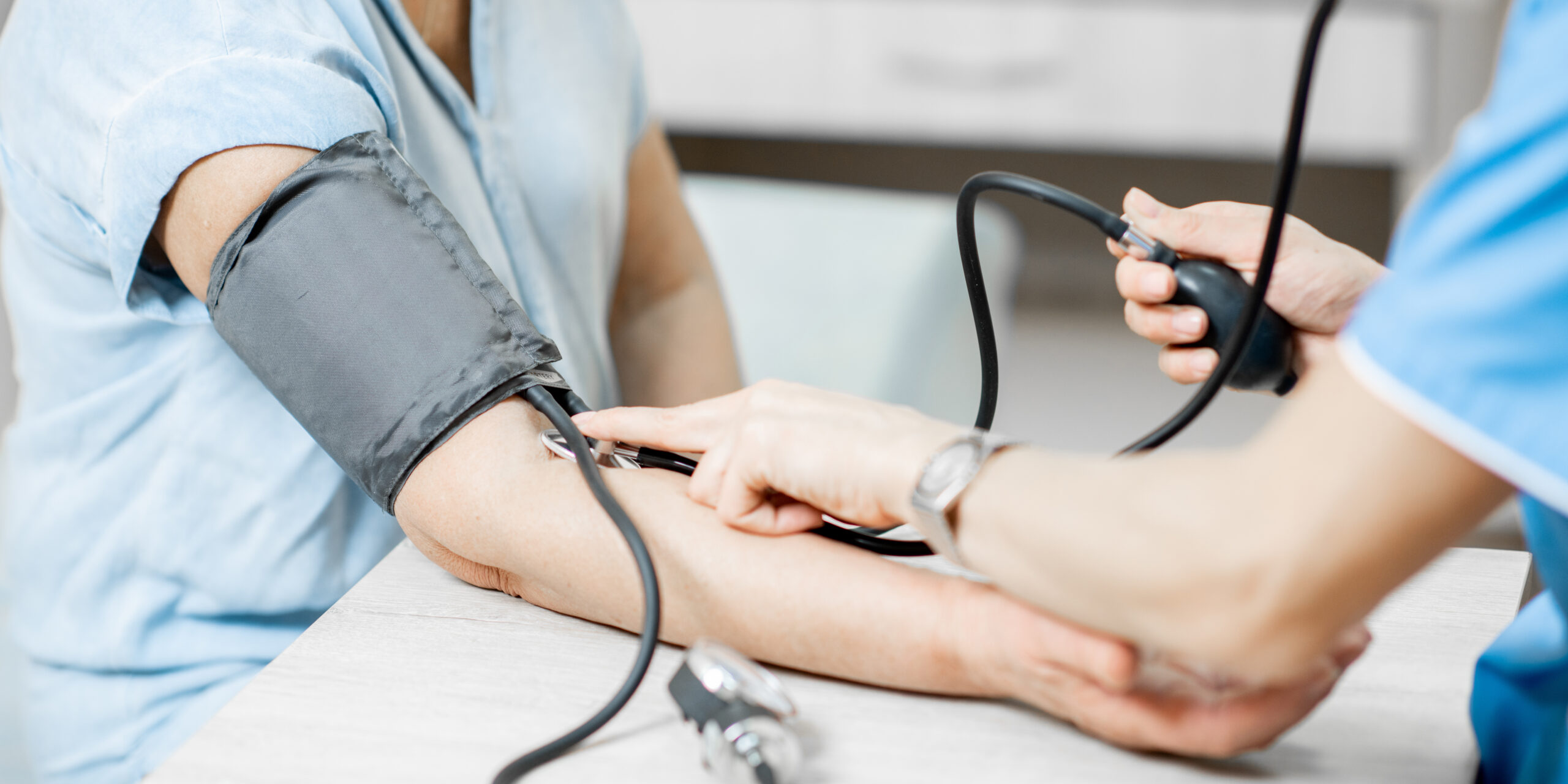
Changing our approach to emergency care
FEATURE – The ER of this Catalan hospital is finding great value in the application of Lean Thinking, which has already led to a dramatic change in its processes and to better care for patients.
Words: Francesc Chavalés and Imma Tort
Since introducing lean in 2017, the Emergency Room of the Hospital Comarcal de l’Alt Penedès (HCAP), part of the Consorci Sanitari Alt Penedès-Garraf, has experienced an overhaul in its way of working.
Our ER, which receives around 200 patients a day, had to find a way to better utilize the limited space available. As a first step in our lean journey, we did a Value Stream Mapping exercise, which helped us to understand the process in depth and the need to reorganize our areas.
We had patients wait in the two largest areas in our ER without taking their condition into account, while another two areas were used to house patients who needed hospitalization and those who were completing their treatment and could be discharged soon. The system didn’t work, as it meant we had to sacrifice precious space that could have been used for patient examinations – a particularly big problem at peak times. So, we decided we would organize our working areas by condition.
Our approach to Triage, we also found, needed an update. It was based on specialties: we didn’t triage patients based on the time they would have to wait given their condition, but based on whether they would need to see a specialist. It wasn’t the best model of what a Triage should be, and friction and discussions among team members were a common occurrence. We corrected the focus of the Triage – bringing it back to waiting times – which allowed us to speed up care considerably.
Another important realization for us was that we were not working in teams. Doctors and nurses had no relationship while performing the value-adding work, and communication was scarce. So, we created EDITs (Emergency Department Integrated Team), with one doctor and one nurse, to work more closely together. Another action was to define more clearly their responsibilities. For instance, the transfer of patients is no longer a prerogative of doctors, but of nurses. We also avoid batching processes and try to work in a single-piece flow instead. More importantly, we are currently able to assign a doctor and a nurse to a patient as soon as they walk into the ER. This really changed everything, because it means that our patients no longer have to sit there wondering who’s going to care for them and that our doctors and nurses know exactly what they are supposed to work on. Today, there is a better distribution of the work and a clear improvement in the service we provide to our patients. In fact, all our KPIs have improved.
Even though the adoption of Lean Thinking has been a shock for many in the ER (it’s hard to move away from old ways of working), the change the methodology has brought about is incredible.
THE AUTHORS
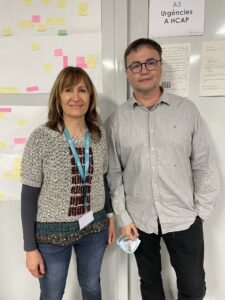
Read more
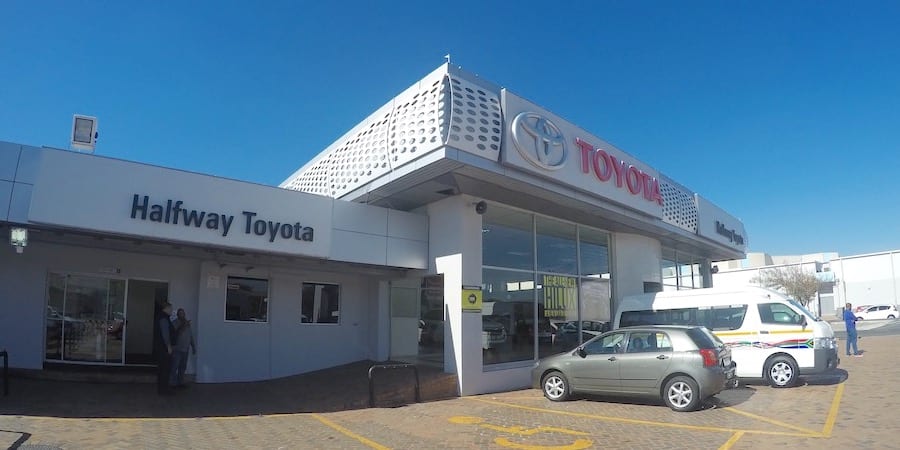
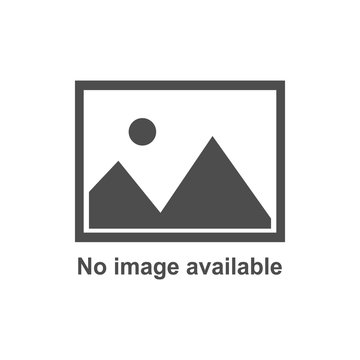
FEATURE – For the first article in our series on the Halfway transformation, we asked the Sales team to tell us about how they apply lean to selling cars in a challenging social context.
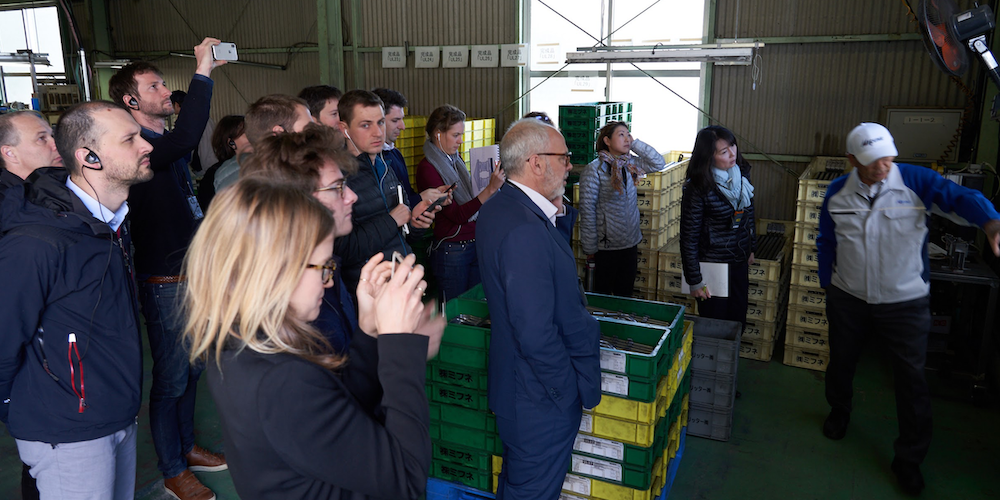
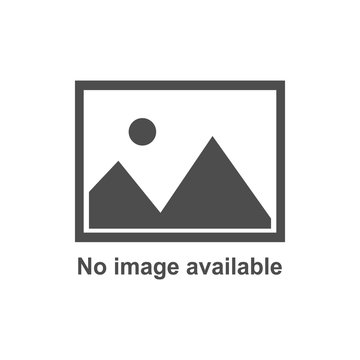
FEATURE – Digital organizations are starting to recognize that Toyota’s unique approach can show them the way forward, just like it does “traditional” organizations. Here, we hear from a few startup CEOs following their trip to Japan.
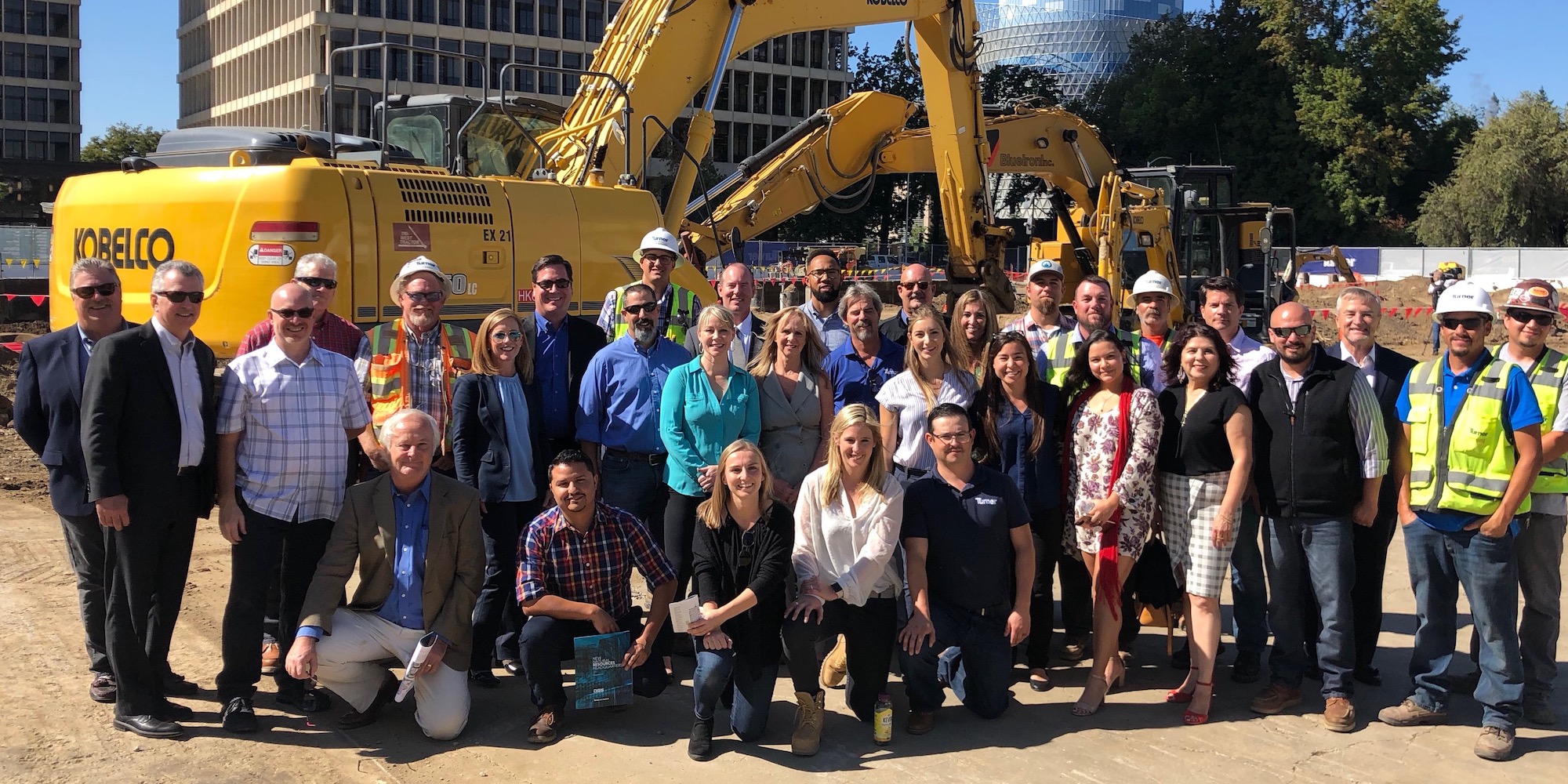
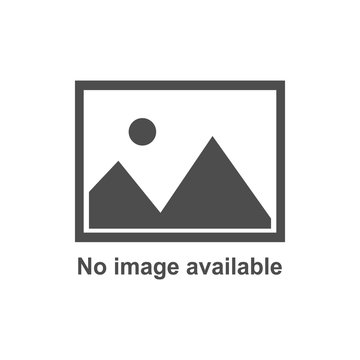
INTERVIEW – During his recent visit to California, our editor sat down with a Senior VP from Turner Construction to discuss leadership transformation and the importance of diversity in the workplace.
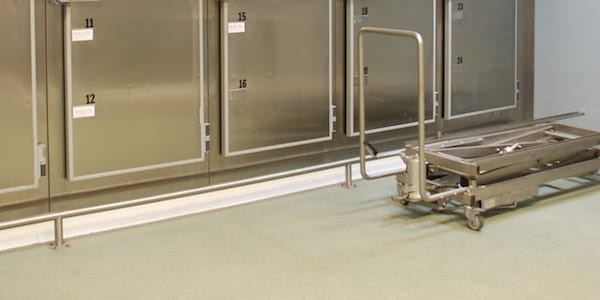
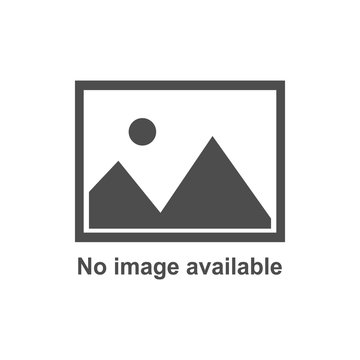
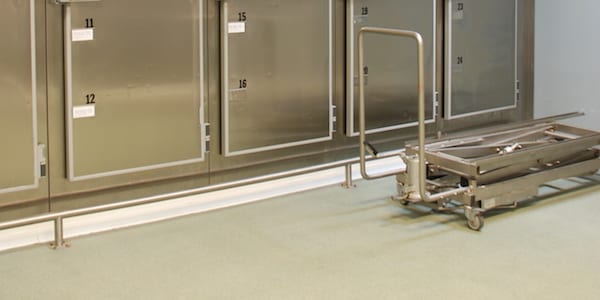
ARTICLE – The Institut de Medicina Legal de Catalunya has learned that employee engagement and lean thinking can shake up even the stiffest of the public sector's working environments.