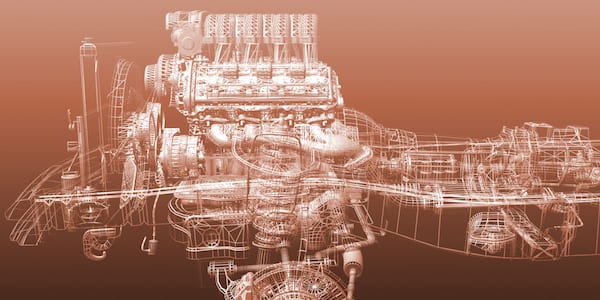
How to transform product development with lean management principles
INTERVIEW - We caught up with LEI’s Senior Advisor, Jim Morgan after his plenary talk at the Lean Summit in São Paulo last month and got him to answer a few questions about product development and lean management.
Interviewee: Jim Morgan, Senior Advisor, Lean Enterprise Institute
Roberto Priolo: In your talk here in São Paulo you said that product development was creating the future. Can you tell me what you mean by that?
Jim Morgan: Every time you develop a new product you have the opportunity to change the trajectory of your organization – to create a new future for it in a very real sense. There are numerous examples of companies that, through product development, changed not only their organization and their industries but also the world.
At an enterprise level, product development is one of the few activities that impacts your top line, your bottom line, and the overall performance of your organization – for better or worse. New products can add significantly to your top line and help you to grow your business. In addition to delivering products, the new product development process determines 60% to 70% of ongoing operating costs and quality potential. It also requires a level of organizational collaboration that can become a competitive advantage in its own right.
Lean product and process development represents a powerful and sustainable system for developing both innovative, value-added products and successful new value streams. It should be a central part of every company’s annual policy deployment process. It is a game changer in the truest sense of the term.
RP: That brings up another point from your talk. You said that product development is not an “engineering thing, it is an enterprise thing.” What does that mean?
JM: Great product development is the ultimate team sport – it requires collaborative effort from all areas of the company (manufacturing, engineering, marketing, Finance, HR, etc.) in order to create a high-powered development system.
Too many organizations still think of product development as something the engineering department does to them, instead of treating it like the incredible opportunity that it is. One of the key characteristics that differentiates lean product and process development from more traditional methods (and some more recent methods that might be labeled as lean) is the focus on creating new value streams – that is to say, all the activities required to deliver the product to the customer. This activity requires the full participation of the entire organization. The key is understanding how best to integrate these efforts and that’s where LPPD is so effective.
RP: What’s required to transform an organization’s product development system?
JM: To begin with, a bit of patience and perspective. We can’t diagnose, let alone prescribe, until we have examined. It is important to truly understand the current state.
A surprisingly high number of organizations don’t really understand their current product development capability. Consequently, they have a tendency to try to plug in whatever trendy program they read about. However, that is not what lean is about – in whatever environment it is applied. First of all, we need to ask ourselves what the problem we are trying to solve actually is.
One way to begin to understand, of course, is value stream mapping. Laying out the process normally leads to a number of surprises and ah-ha moments for the engineers. For the first time, they realize they are part of a larger system (developers often tend to think of their work as very compartmentalized) that is full of interdependencies between functions. Get these folks talking. Look at the data, study the failure modes, even conduct a process capability study. These activities often lead to revelations.
The other realization that engineers normally get to is how much rework is present in a workplace. Of course, they know of their own frustration but when you show them everybody else’s, they really understand. Discussions on process capability (hardly a top-of-the-list item to reflect on for developers, at least traditionally) follow, from which a dialogue on several other problems normally stems.
After these initial stages, the implementation plays out like in any other setting: you find early adopters and you try to get some quick wins to show the effectiveness of the approach.
The support of senior leadership is fundamental throughout the process: without it, applying the changes that will have an impact on the performance of the entire organization - thanks to the close and often overlooked relationship of product development with other business functions - will be extremely difficult, and the only result will be the creation of pockets of excellence.
RP: Are there any example of companies that are doing LPPD well?
JM: Yes, there are a growing number of companies who are making excellent progress. Goodyear, Pfizer, Herero Builders, Menlo Innovations and, of course, Ford Motor Company have all done some really good things. Industries including software, pharmaceuticals, construction, and automotive (among others) are making fundamental changes to the way they create new products with LPPD practices and principles.
But there is a lot more work to do – that is why we have started a major initiative at LEI to help companies with product and process development.
RP:Can you tell us more about this initiative?
JM: I am working with the Lean Enterprise Institute in the lean product and process development area. We are doing a number of things: first of all, we have established learning partnerships with a select group of high performing organizations to both improve their development capability and advance our knowledge of LPPD. Secondly, we are developing new material that we will use for training, books, articles and other means of sharing knowledge. Finally, we have just launched a website - www.leanpd.org - which aims to bring together lean developers from a number of different industries and disciplines (agile, scrum, design thinking, makers, Lean UX, LPPD, etc.), most of which have common roots in lean and have simply been adapted to their respective environments. To me, this is an opportunity to learn from one another and broaden our scope of knowledge. To create a seamless solution set. The best products are seamlessly integrated systems – our strategy should be as well.
RP: Some organizations argue that lean is for manufacturing, and that it will not work in other industries. How do you react to that?
JM: To be honest, I normally don’t react. Sometimes it is just best to let people figure things out for themselves… But I do believe that lean is ultimately a people centric system that is driven by people’s nearly unlimited capacity for creativity and innovation. That’s why Lean has been so incredibly successful in such a wide variety of environments: From health care, to retail, to manufacturing – and especially in product development.
Even the primary methods of TPS (the roots of Lean) are referred to as countermeasures, with the underlying expectation that something better will be developed. This is perfect for product and process development, in any industry. The most fundamental principles of LPPD are:
- First, deeply understand what the product must be.
- Second, create flow and eliminate waste for speed to market. It’s hard to beat speed – especially if you have the right product.
- Third, understand that the fundamental element is learning.
- Finally, realize that a great development system is all about people.
People provide the creativity to power the system. They enable the sustainability of your results. There are many specific tools and methods to LPPD – the key is adapting the principles to your own environment. Of course this is no color by numbers exercise. It requires hard work, and that you - as Jim Womack says - switch your brain to the “on position”.
RP: Any final comments?
JM: Yes. I learned first hand the power of transforming your development system to deliver product excellence, both in my research and while I was at Ford. It definitely changed Ford’s trajectory, keeping the company from having to accept a government bailout. It created a much better future, which included the creation of the best selling vehicle on the planet – the Focus.
A growing number of companies have begun to do significant work in this space. They are leveraging lean to achieve all new levels of performance in new product and process development. This is going to raise the bar in their respective industries the same way lean manufacturing did. We are busier than ever helping companies with LPPD and I think we are just seeing the beginning of this change.
THE INTERVIEWEE
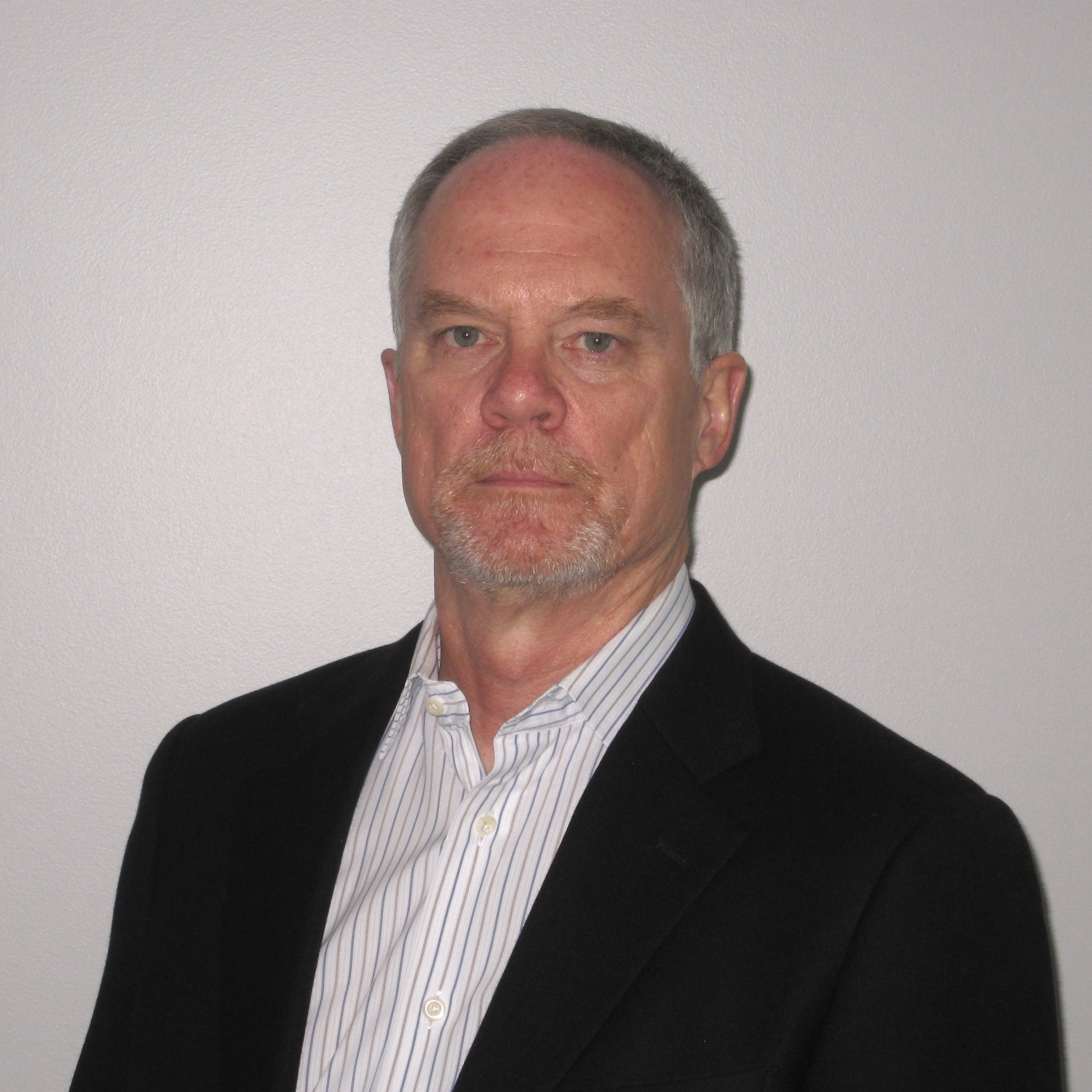
Read more
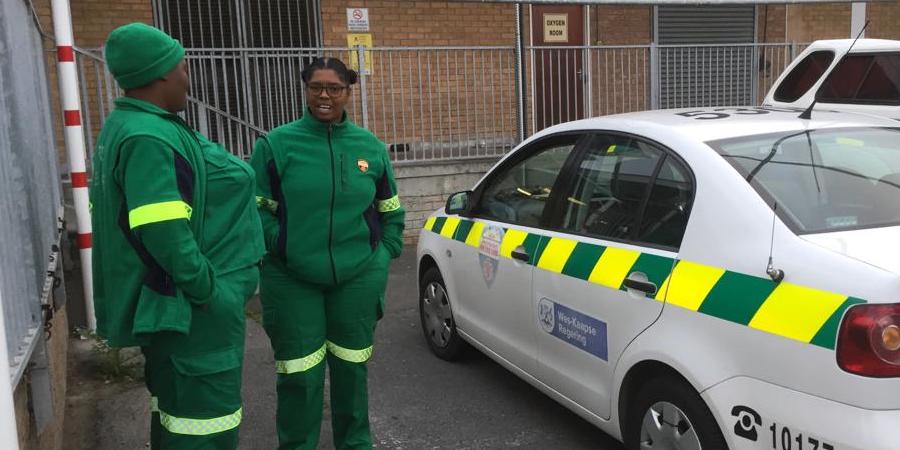
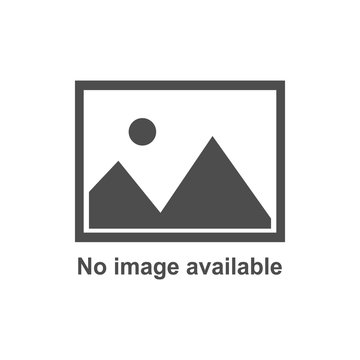
FEATURE – Only when we go where the action is, do we begin to truly understand the work. Rose Heathcote joins the Emergency Medical Services in Cape Town for a day.
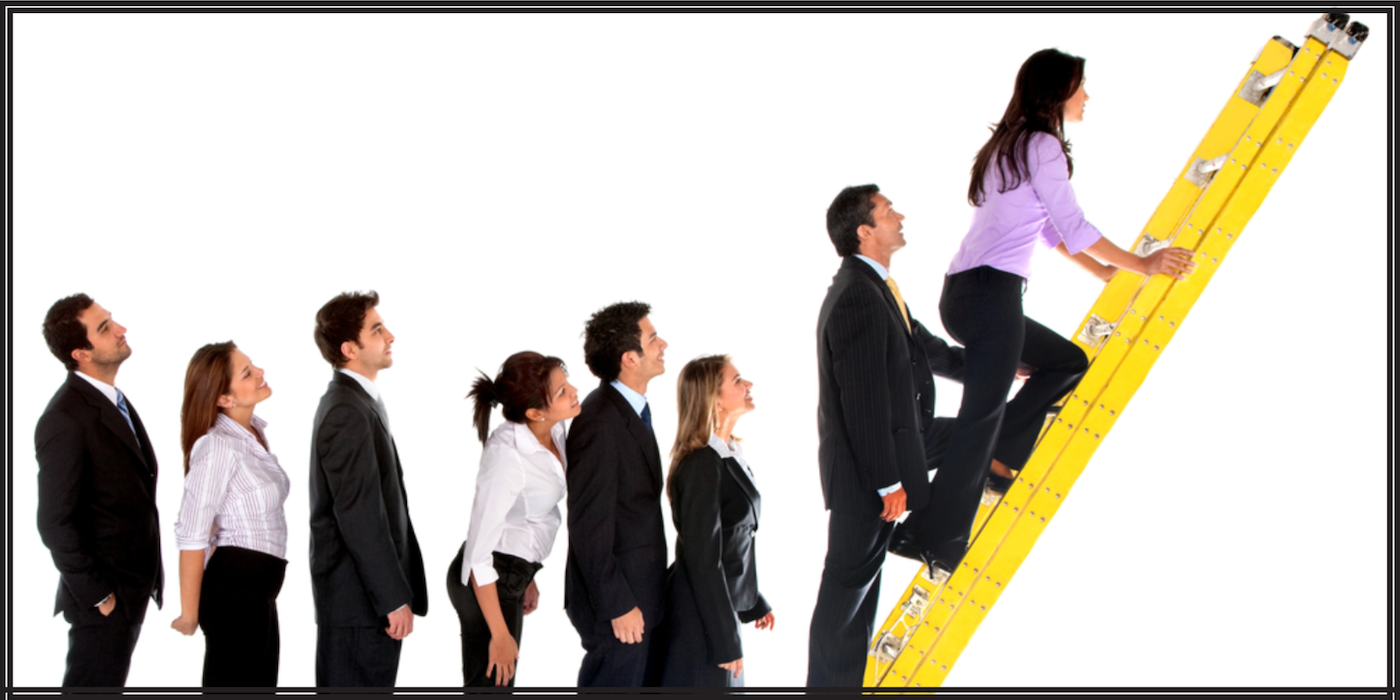
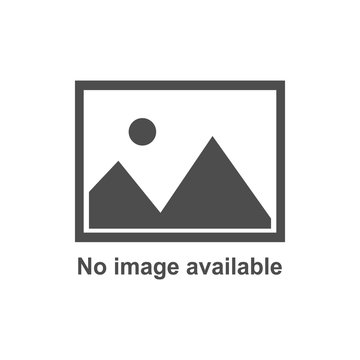
FEATURE – If you think one is born a leader, think again. Leadership can be learned and, in this article, the author provides a four-step guide to developing it.
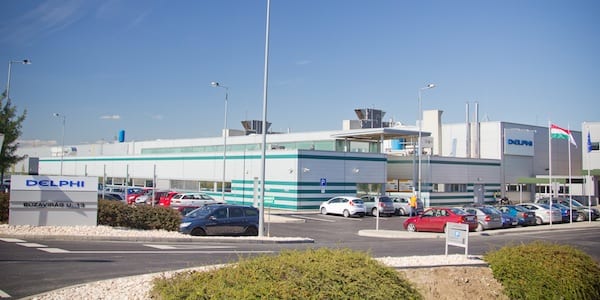
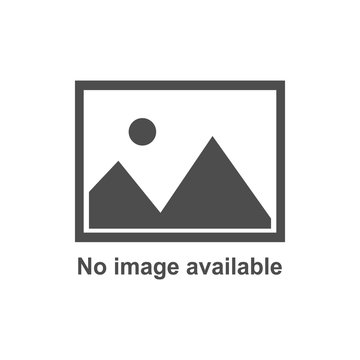
INTERVIEW - The General Manager of a Delphi plant in Hungary talks about the lean transformation the site went through and the challenges automotive suppliers face in this day and age.
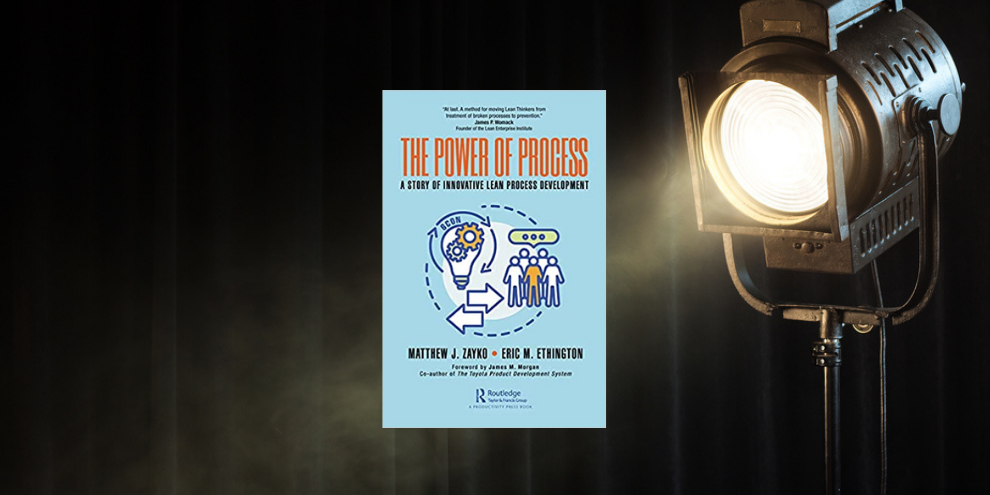
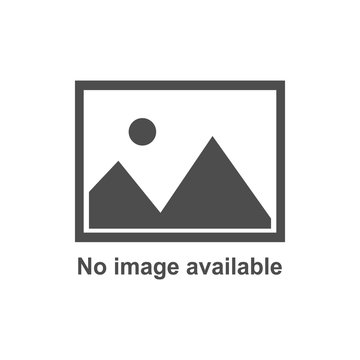
INTERVIEW – The authors of the new book The Power of Process debunk some of the most common myths about lean process development.