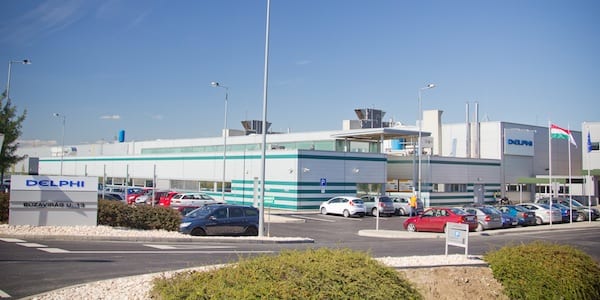
Interview: Delphi Connection Systems
INTERVIEW - The General Manager of a Delphi plant in Hungary talks about the lean transformation the site went through and the challenges automotive suppliers face in this day and age.
Words: Balazs Sebestyen, General Manager, Delphi Connection Systems Hungary
Roberto Priolo: How would you describe the situation of the car industry in Europe at the moment and how is Delphi trying to respond to that?
Balázs Sebestyén: The European automotive market has gone through several difficult years. But right now the sector is recovering in the continent. From Delphi’s standpoint, we’ll always need the adaptability and flexibility to react to anything, and that’s when lean becomes really important.
RP: Tell me about the plant you run.
BS: The Tatabánya plant is located about 60 kilometers west of Budapest. The plant has been operating in the Industrial Park of Tatabánya since 2001, now employing over 1,700 people. We produce Safety Restraint System, or SRS connectors used in airbag applications, electrical connector housings for various electrical/electronic applications, such as ABS systems and high power connectors for charging electric vehicles.
Last year, we completed the extension of our production capacity at the plant doubling our facility. This helped to strengthen Delphi’s position as a global automotive supplier of electrical/electronic architecture systems.
RP: Delphi has a long history of using lean thinking. What’s the level of lean maturity of the organization in Hungary specifically?
BS: Delphi, in general, is quite advanced in the use of lean manufacturing globally. In Hungary specifically, the company is focusing on the pragmatic implementation of tools used on the facility floor and on transferring standards, know-how and information across the four facilities in the country.
RP: Are standards and requirements driven from the top?
BS: Delphi works with an Enterprise Operating System, or EOS. The EOS helps to establish clear, easy-to-understand rules for all departments, functions and facilities – lean is completely embedded into the EOS.
Each facility has the freedom to interpret standard operating procedures to better respond to local specifications, issues or requirements. As an organization, we are clearly moving towards increased integration and better standardization. Lean tools are standardized throughout Delphi Connection Systems globally.
RP: You said that your plant was already quite advanced in lean thanks to the strong support of the top leadership. What’s leadership support like today?
BS: Delphi has a very strong culture of excellence that influences our everyday life. Regional, global and executive leadership are all committed to making Delphi a real benchmark supplier, and lean has a very important role in achieving this. As a plant manager, I get full support in continuously improving my plant through lean.
RP: How do you translate company goals into concrete actions?
BS: At the Tatabánya facility, we use a lot of lean tools and hoshin kanri is one of them. Every morning employees gather on the shop floor to listen to presentations given to management on the improvement workshops they lead, also reviewing QVC metrics (quality, volume and cost). Even the plant controller attends, as financial forecasts stem from first-hand experience of the events the plant is encountering.
Our toolset is like a Swiss Army knife: we have a tool for all management expectations. When management expects to reduce the number of days of inventory, for example, we have the tools to do it.
RP: Can you tell me about people development at your plant?
BS: The development of our people is very important to us. As the plant manager, I’ve learned that it is absolutely necessary to spend time on the shop floor coaching people and taking part in their meetings. By spending time on the floor, I get to know who does what, and I better understand their behaviors. Leaving the office to be to the gemba is one of my top priorities.
RP: What is the main difficulty that you encountered in implementing lean at the factory?
BS: It is my experience that change often brings resistance. In this instance, perseverance led to becoming lean. Through perseverance, I was able to demonstrate quick wins that I could share with the rest of the organization to get buy-in. I managed to push the ball past the top of the hill, so to speak, as we are now enjoying the momentum we have been able to develop in our lean activities. We now have a critical mass of people including shop floor technicians and shift leaders leading QRQC, TPM, SMED, 5S, hoshin, kaizen, pull leveling workshops, flash meetings, employee suggestions, first defect stop, red bin reviews, or using one of the many other lean tools implemented in our plant.
RP: Can you give me a couple of examples of actual improvements you’ve been able to achieve in Tatabánya?
BS: The most impressive one is inventory. Before we started to apply lean principles, our inventory was 70-80 days. At that time, we were using an ERP system for production planning and procurement. We ran big batches with the idea of minimizing changeover times and maximizing the use of production lines. We then started to conduct workshops, installed a kanban system and improved flexibility in working with our suppliers. Today, our inventory is 13 days. Now, the whole plant operates through a pull-flow system - we moved to smaller batches and we now produce every SKU every two days, as opposed to the previous two to three weeks. This means flexibility to meet our customers’ needs and a smoother and efficient operation on the shop floor.
RP: How do you think supply chains will evolve in the future?
BS: There is a shift towards regional supply chains. Ten years ago the trend was to globalize, now it’s the opposite. It has become a more important expectation for suppliers in the automotive industry to have regional capabilities and enough flexibility, providing globally accessible products manufactured through standardized processes. Delphi is able to offer exactly that.
THE INTERVIEWEE
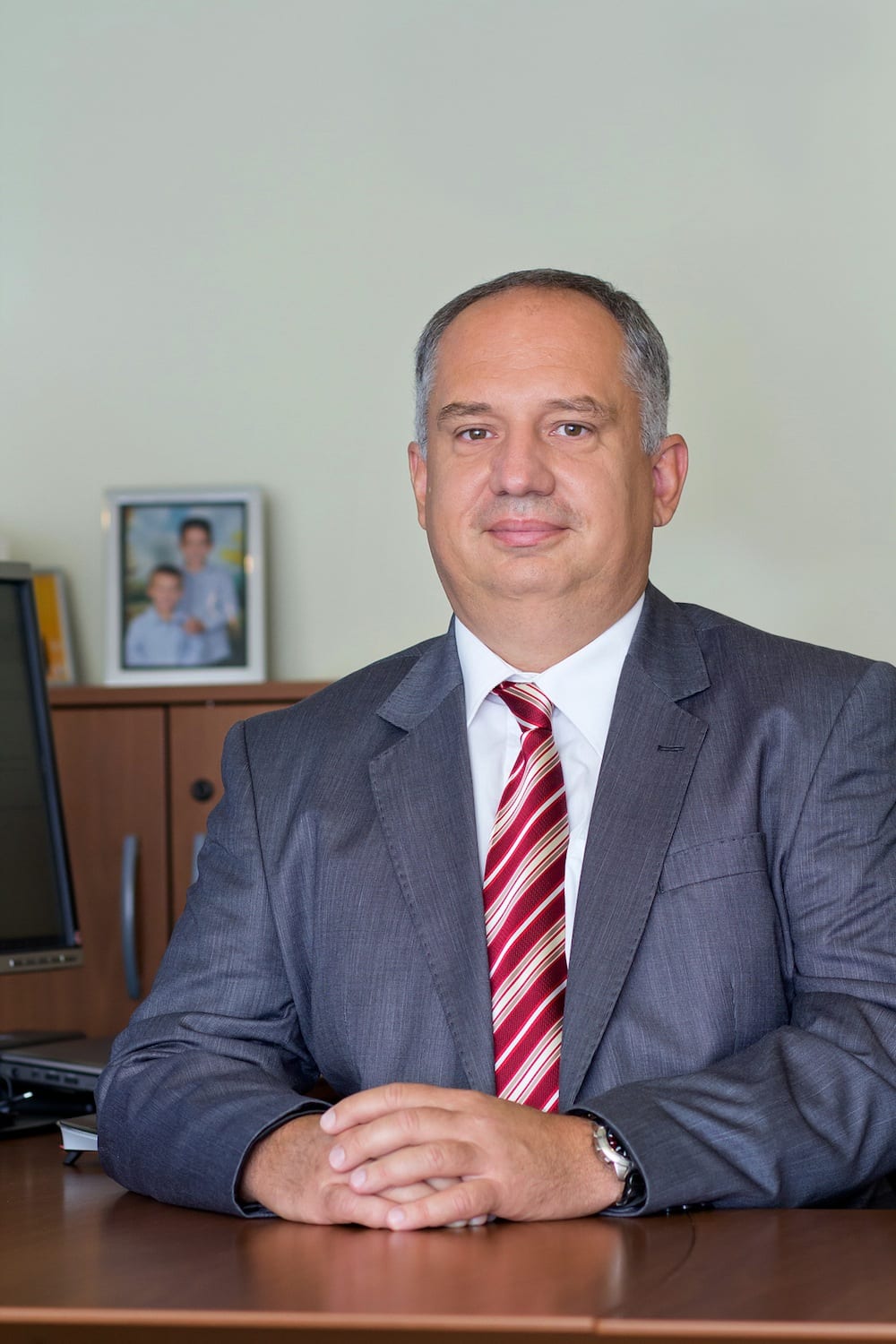
Read more
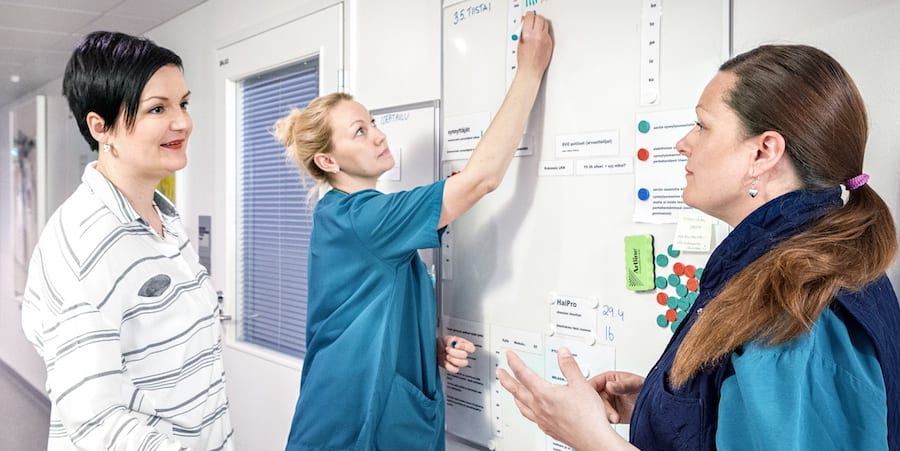
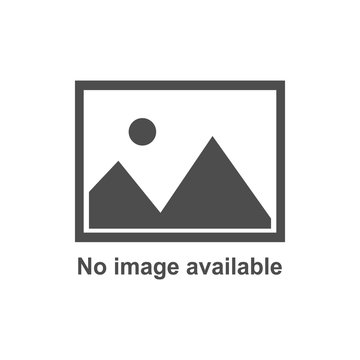
CASE STUDY – The whole of Helsinki’s hospital district is leaning out, with incredible results. It isn’t every day that we come across – let alone have the opportunity to observe – a lean transformation in such a large healthcare organization.
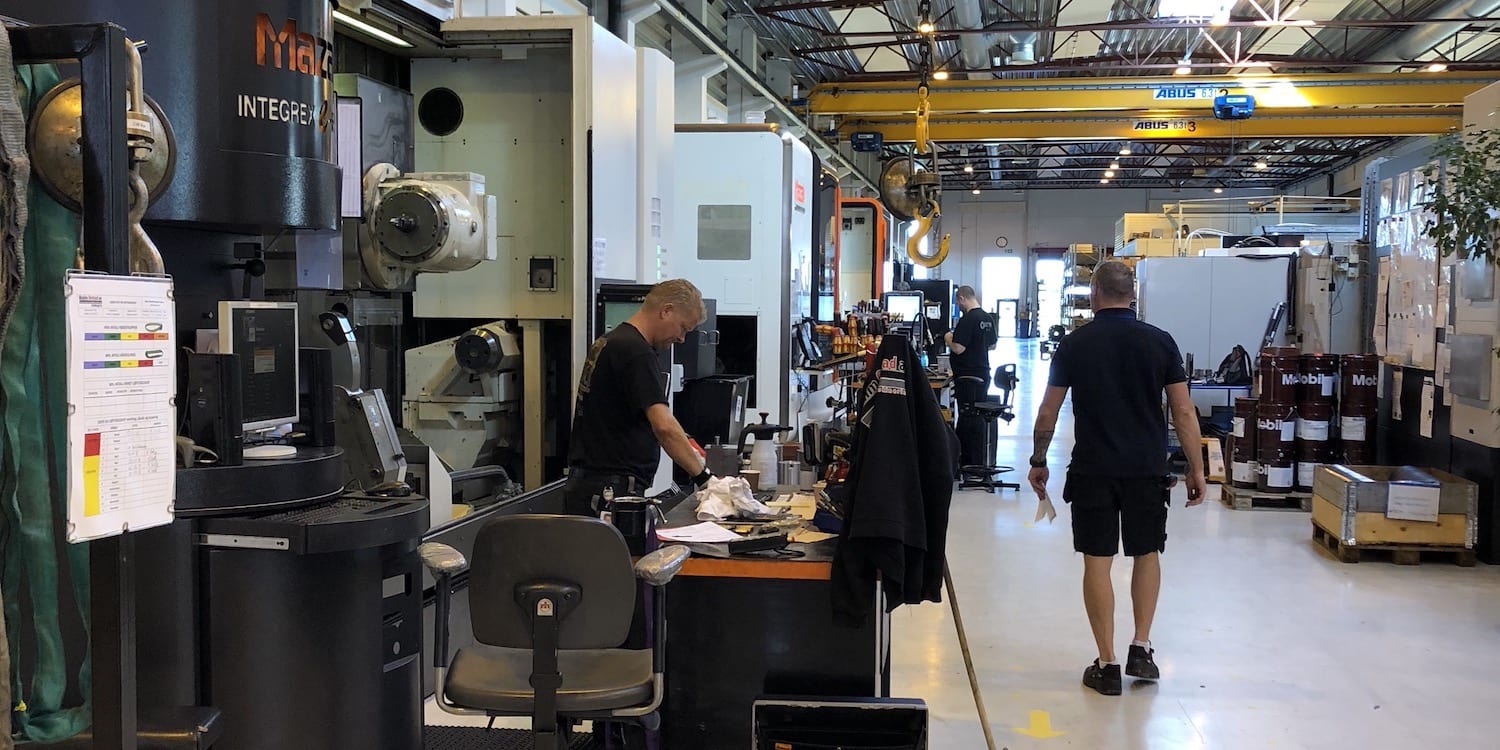
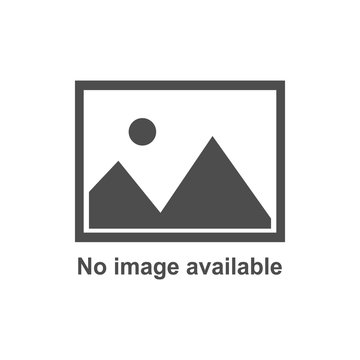
FEATURE – This Norwegian company has come back from the brink of bankruptcy by rallying its people around a common set of values, by leaning out its processes and by involving its leadership team.
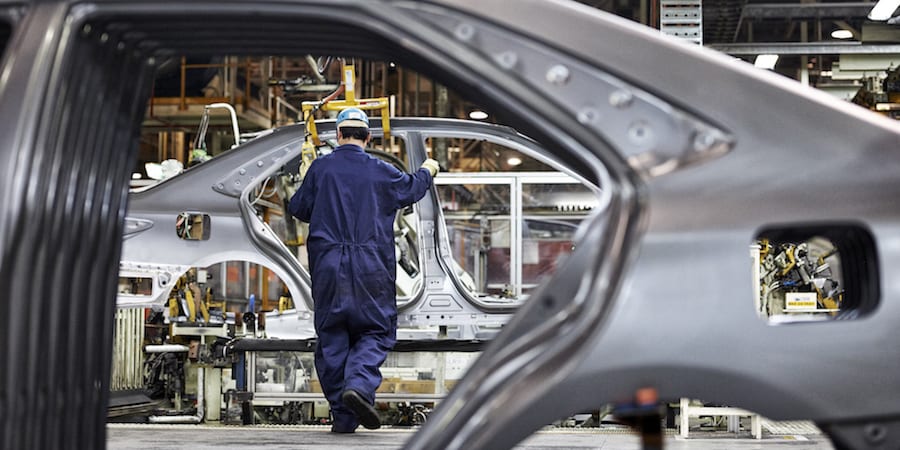
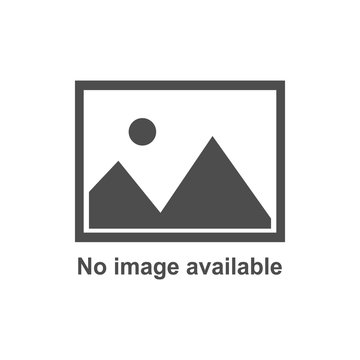
WOMACK'S YOKOTEN – On October 3, Toyota will cease its manufacturing operations in Australia, but the way it is managing the transition - in the leanest way possible - holds great lessons for us all.
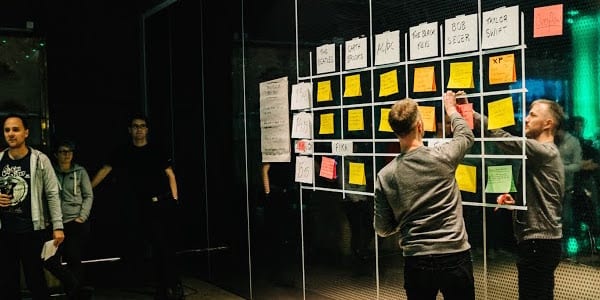
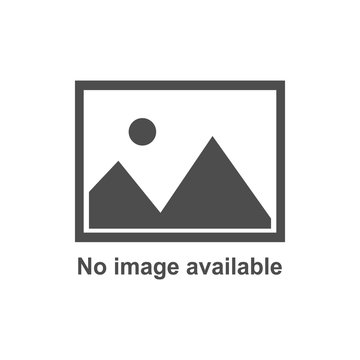
CASE STUDY - How Spotify developed an alternative management system based on servant leadership, interaction-based learning and adaptability – changing the music industry along the way.