How Tuinderij Vers is learning to see
FEATURE – Faced with increased production volumes, this Dutch company realized the need to improve its processes by developing people skills.
Words: Rob Witmer with Patrick Saleh
In organizations that experience rapid growth, increased volumes are rarely accompanied by process improvements and an investment in people's skills. This is exactly what happened to us.
Tuinderij Vers is a Dutch vegetable processing company specialized in cutting, mixing, and packaging vegetables and fruits into ready-made and ready-to-eat products. We supply supermarkets and food services with a range of ready-to-cook vegetables, vegetable mixes, salad mixes, raw vegetables, ready-made salads, and meal boxes.
Since 2015, we have worked in partnership with Vezet, which has significantly influenced our growth. In the past decade, the volumes we need to process every day have grown substantially, and so has our workforce (we have experienced a fivefold increase in the number of employees, in fact – today, we employ 650 people). Our production runs for 16 hours a day, with the remaining time dedicated to cleaning. Historically, our focus has been on reaching our production goals for the day, but we recently realized that we were not paying enough attention to how we did the work. This led us to challenge ourselves to find a better way to work. That’s when we figured out that for the company to grow, our people needed to grow with it.
IMPLEMENTING LEAN
In September last year, our leadership team, including myself, participated in a Black Belt course with Lean Management Instituut. The next step was to involve front-line staff through an Orange Belt course. Initially, there was skepticism from some team members and internalizing lean principles and practices proved difficult. Spending time away from the daily work to “do lean” seemed counterproductive to them. Over time, however, the team realized that lean is not separate from our work; it is the way we need to do our work.
Getting Patrick’s support was critical in ensuring buy-in from our people. As a former Vezet employee and someone who’s visited Tuinderij Vers many times in the past, he knows the language we speak at the factory. Collaborating with him and LMI on the lean training was a winning decision.
The Orange Belt course for operators, held in October 2023, was our way of investing in our people. It encouraged participants to think about the real problems and root causes of the issues they face. They went to gemba together, visiting each other’s areas to understand their colleagues' work and how it influenced their own. This interaction opened their eyes to new perspectives and solutions.
ADDRESSING CHALLENGES AND FINDING SOLUTIONS
Lean was a new concept for the Orange Belt group, and their initial skepticism was evident. During the training sessions, we guided them through Purpose, Process, and People, helping them to see the problems. We taught them A3 Thinking, which involves defining the real problem, grasping the current state, and analyzing the process. They performed deep investigations of problems, a new experience for them. We reviewed their A3s daily and assessed their progress, fostering a supportive environment where people increasingly asked questions and supported each other.
Although Tuinderij Vers was meeting its production goals and had, therefore, no “burning platform” per se, there were underlying issues with the work. The course was the key to unlocking people’s ability to see and address such problems.
From a waste perspective, for example, we discovered that we were cutting vegetables too fast. In other words, we were engaging in push production, rather than pull production. Reducing the cutting speed and aligning it with downstream processes reduced waste by 9% on the bok choy line and by 5% on the paprika line.
We also ran a project on SMED (single-minute exchange of die), which resulted in our changeover time for foil on the packaging machines to go down from 15 to 8 minutes.
Another project addressed the cost of washing clothes - an idea that came from the housekeeping department. People need a new uniform every day, and some used up to two sets daily. By reducing this to 1.25 uniforms per person per day through 5S (sort, set in order, shine, standardize, sustain), we achieved significant savings.
Maintenance was also improved by prioritizing the work of technicians based on the problems faced each day, thus increasing the time they spend working on equipment and decreasing machine downtime.
We also introduced start-off meetings every morning to review the previous shifts and plan the day ahead. This change promoted a culture of looking forward instead of blaming, improving communication and understanding across the factory. When one area is understaffed, for example, operators can be quickly moved to avoid problems, and maintenance can be dispatched immediately when a machine is down.
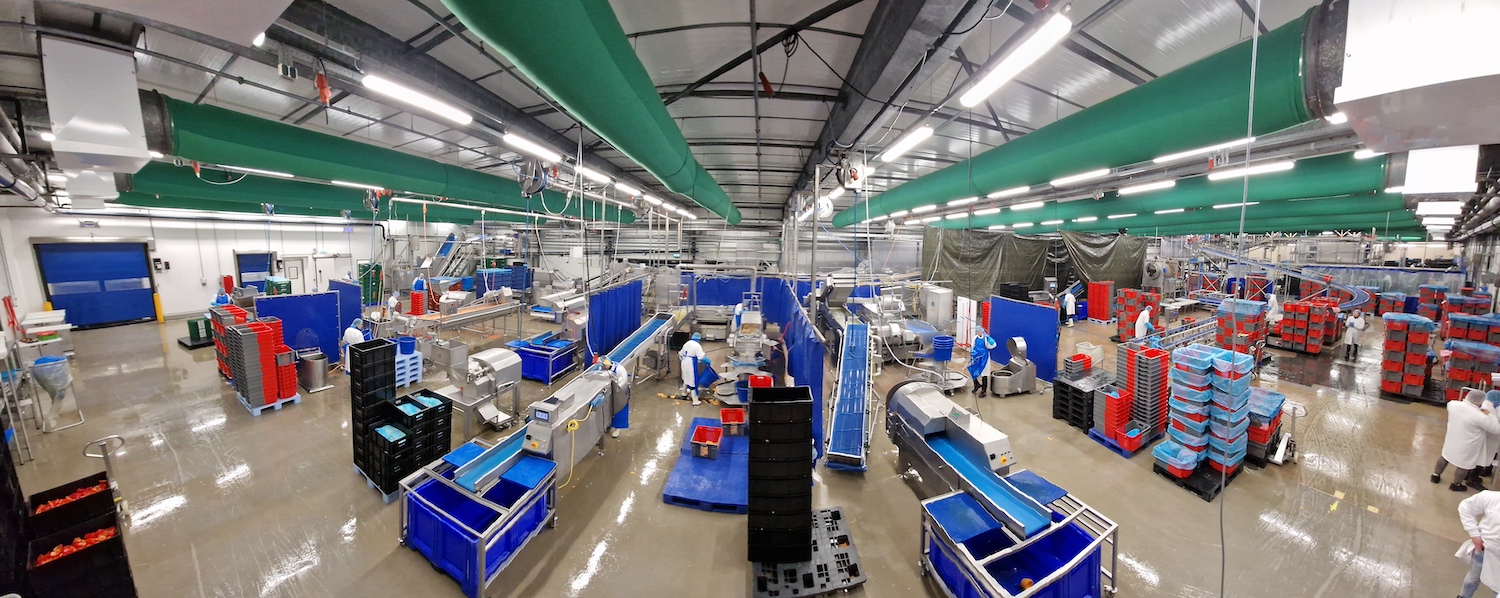
A3 THINKING AND COLLABORATION
A3 Thinking allowed people to understand the gaps and truly learn to see. As they warmed up to the approach, they started talking to each other and understanding the work. This not only gave more meaning to their tasks but also highlighted how their work contributed to the company’s mission. The more they used A3, the more enthusiastic they became, with even the most skeptical members leading the team's improvement efforts.
Leadership realized the importance of explaining the work, roles, and expectations clearly. We emphasized why we are doing lean and why we want everyone to grow together with the company. By learning to see the process end-to-end, people moved past silo thinking and began understanding the meaning of pull production. In fact, the success of these projects lay in people working together and solving each other’s problems. We are moving past silos and developing value stream thinking across the organization.
We have recently conducted an internal assessment and confirmed that people are now very happy with the lean training and changes. They are more satisfied with their work now, which is something we value immensely, and that’s because they are more autonomous in their problem-solving efforts. A3 Thinking taught them to look at the root causes of problems rather than relying on quick fixes. We are now starting a Green Belt cycle to instill more coaching capabilities within the company and establish a proper coaching structure. Over time, this will make us independent in our continuous improvement efforts.
LEARNINGS AND FUTURE PLANS
Our key learning is that making time for developing people is a fundamental investment. Although it may slow you down initially, but it will ultimately pay dividends by fueling our growth.
We have also learned that people have the answers to our problems; they just need to be taught how to find them. That’s why the Toyota philosophy of "making things by making people" (monozukuri through hitozukuri) resonates with us so much!
THE AUTHORS
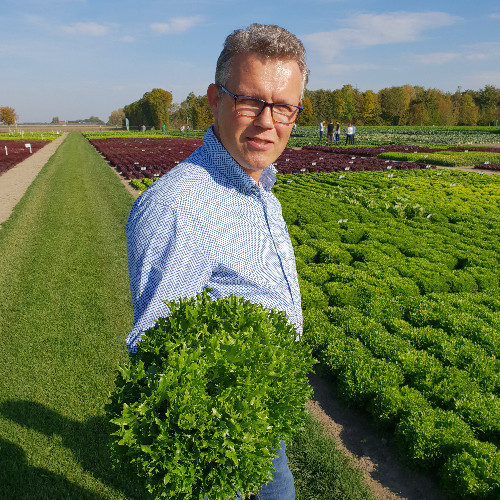

Read more
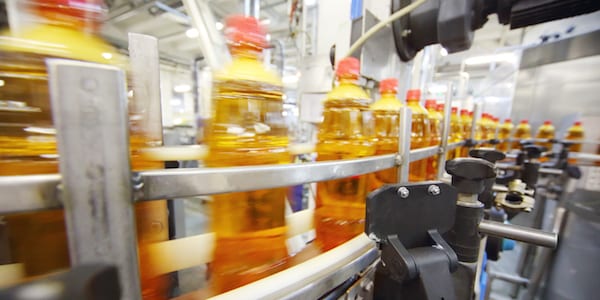
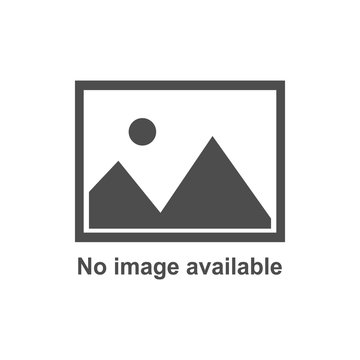
FEATURE – Effectively applying just-in-time and achieving flow is impossible without leveling production first. Yet, most companies seem to think this is impossible because demand is so variable… but is it really?
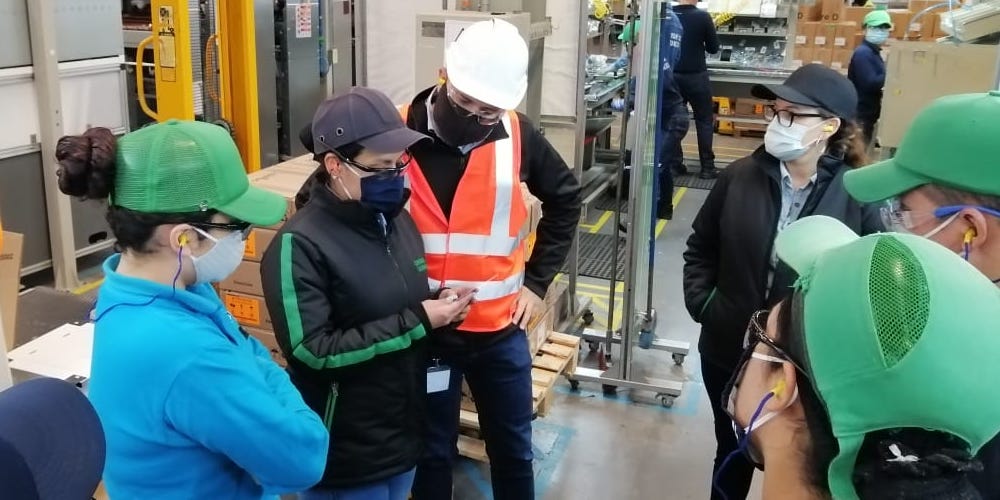
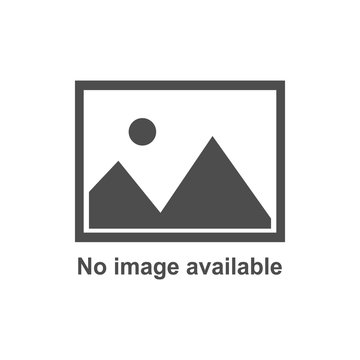
FEATURE – How do kamishibai boards work and what sort of benefits can they bring to a lean transformation? The author discusses what he saw on a recent gemba walk.
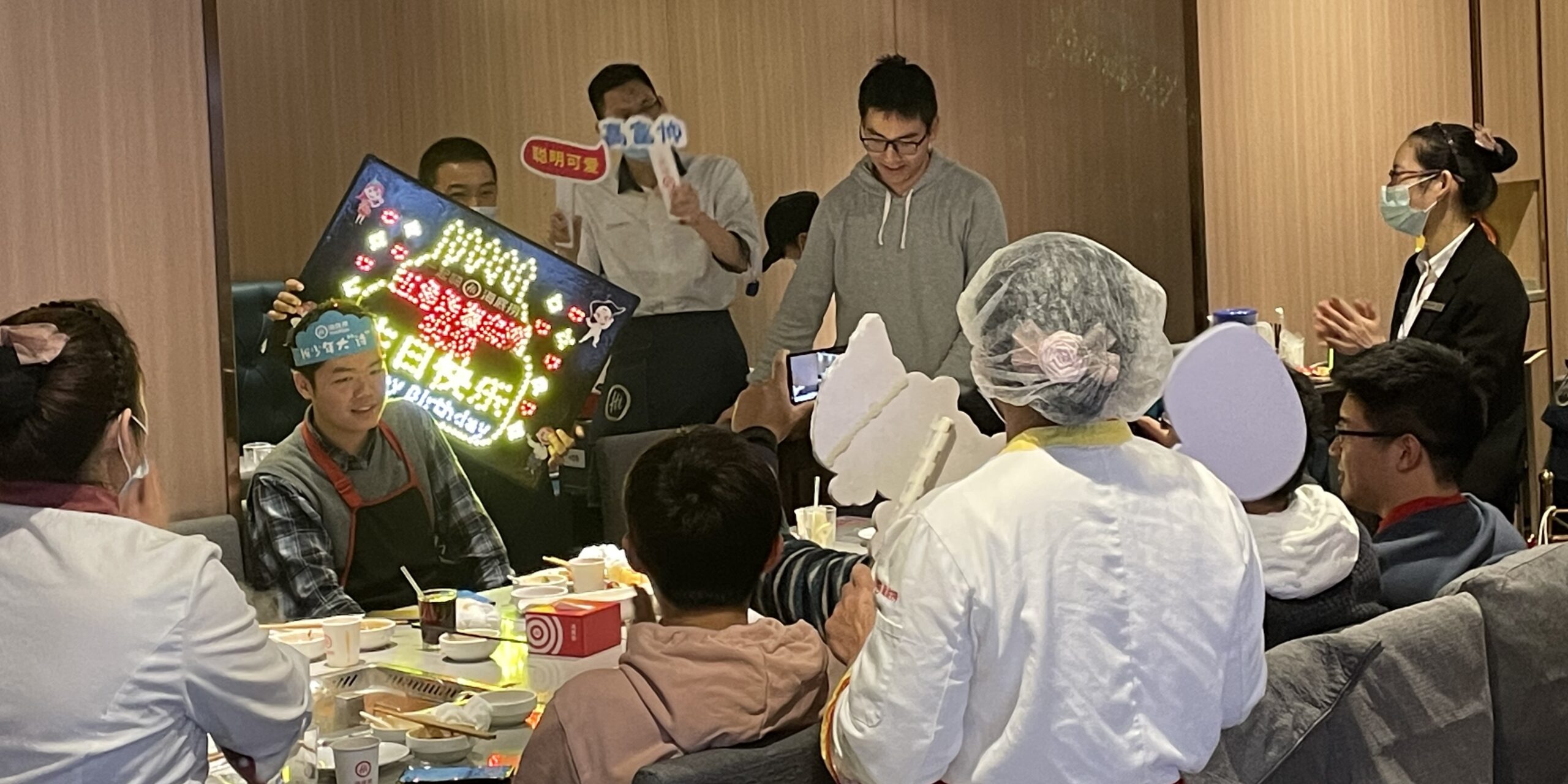
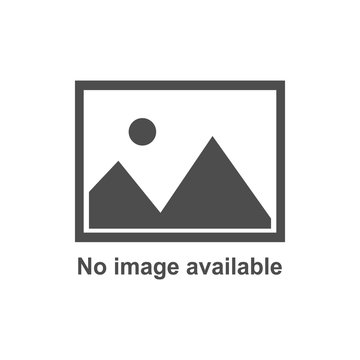
CASE STUDY – How does a small food shop in Sichuan turn into a $30 billion chain with around 900 restaurants in several countries? By always going the extra mile for customers!
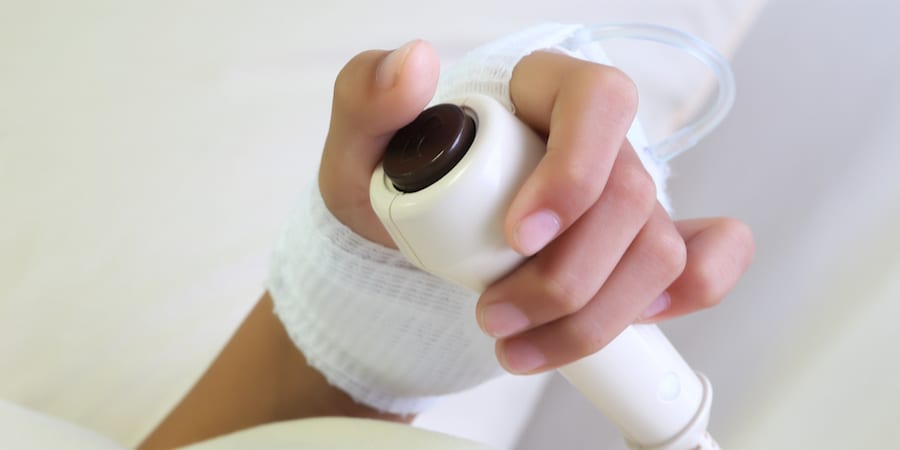
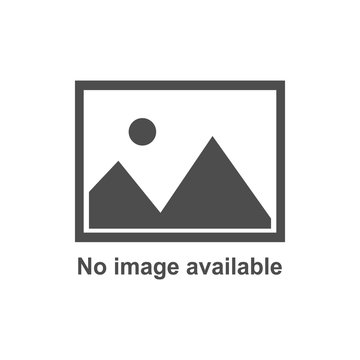
FEATURE – Every year, Siena University Hospital runs a Lean Day to celebrate and award its best lean projects. In this new series, front-line people write about five of these initiatives: first up, Internal Medicine.