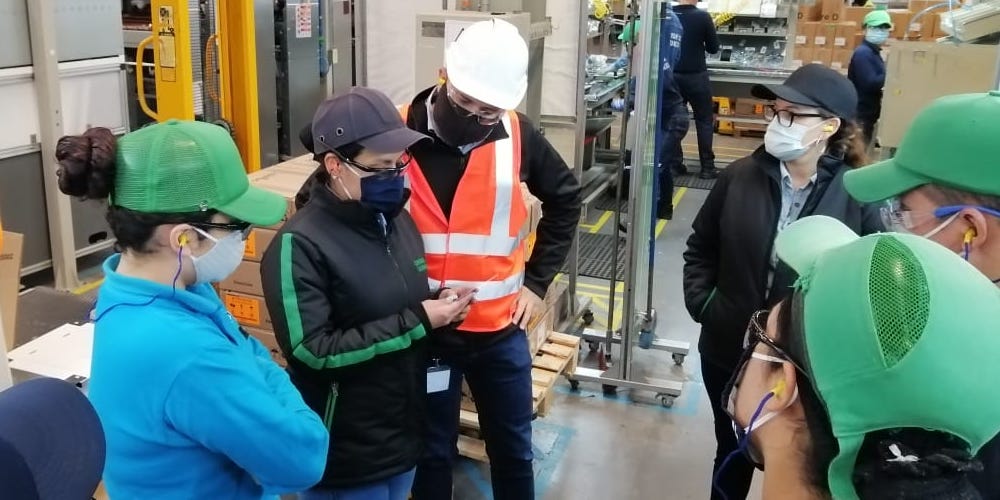
Kamishibai for better conversations at the gemba
FEATURE – How do kamishibai boards work and what sort of benefits can they bring to a lean transformation? The author discusses what he saw on a recent gemba walk.
Words: Juan David Ruiz Valencia, President, Lean Institute Colombia
We lean thinkers tend to make a rather indulgent use of Japanese words. At times, this can put people off, but I believe that there is no reason why we shouldn’t use Japanese terms, so long as we understand why we are using them and where they come from.
One of the most interesting ones, in my opinion, is kamishibai. In Japanese, this translates into “paper drama”, referring to a form of street theater that became popular in Japan during the Great Depression. In a kamishibai performance, travelling storytellers use paper scrolls to tell stories to their audience. Kamishibai has a strong educational component to it, which makes it very popular in kindergardens for example.
In the lean world, we talk about kamishibai boards (which, like many other tools and techniques, have been borrowed from the Toyota Production System). These are directly linked to organizational learning, having come to represent a fundamental tool for process confirmation and a powerful driver for improvement. Let’s see how they work.
When using a kamishibai board, a manager or supervisor picks one card from the board – either randomly or based on a schedule. Each card shows a specific task or element of the standardized work that is then checked upon (typically as part of a gemba walk) at a working cell or workstation. The card tells the supervisor what she is going to observe on a specific day, ensuring that standards are maintained and that quality controls are held on a regular basis.
In a Schneider Electric factory here in Colombia that I visited recently, day after day the manager and his team picked four cards from the board to go visit four random areas or sections of the line. (Interestingly, their inspiration to introduce kamishibai boards came from a seminar they attended, held by Dr Frederico Pinto, CEO of the cancer treatment center IOV in Brazil – a powerful example of yokoten.) There, the team of managers initiated a dialogue with the production team, starting from the questions shown on the cards they had picked from the kamishibai board. All questions are related to the standardized work in use at the cell. During my visit I saw how managers carry out this enriching exchange about how the work is done and, one more time, I was reminded of how different it was from traditional auditing – a trap it is all too easy to fall into when at the gemba. The team was asked about the different cycles of their daily management, the different meetings taking place and their purpose. Of course, the questions displayed on each card can focus on anything, with huge implications for safety, machine maintenance, quality and, of course, the flow of value towards the customer. It was exciting to see how the Schneider team leverages tools such as this to strengthen their management system, and even more to see how they have been able to take these constructive conversations to other areas of the business, including Engineering and (soon) in Warehousing. Experimentation with kamishibai is leading to great learning across the business, proving that this approach works well in all settings, from manufacturing to administrative tasks and office work.
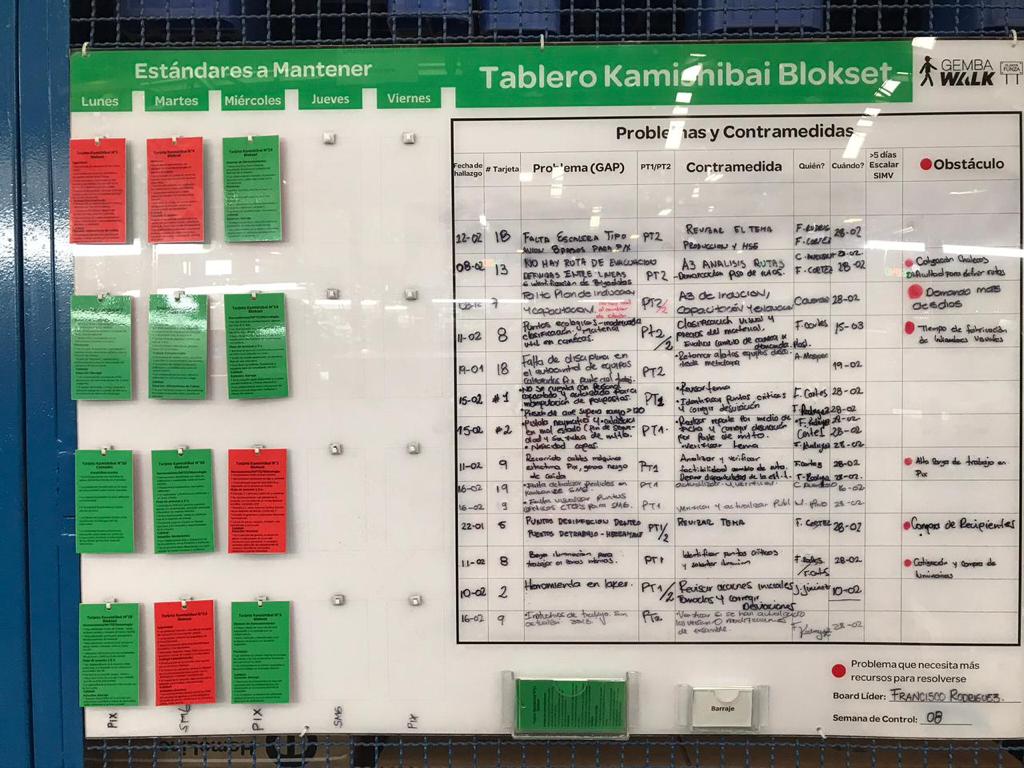
I would argue that people development is the main objective of a kamishibai board. Whenever a manager realizes that a standard is not being followed or that a problem has occurred, an opportunity arises for people to learn something new about their work and develop their skills. This way, a simple card turns into a door into a deeper conversation about the work and the standards in place on the production floor. In this sense, kamishibai – coupled with daily management and standardized work – becomes a key enabler of improvement.
These random visits are also meant to recalibrate standards. The objective is not for the leader to go to a workstation and deliver a lecture, but to generate a productive conversation between the manager and the front-line workers. In lean companies, where leadership understands the importance of deepening the workers’ understanding of the work and ensuring their adherence to standards, it is not uncommon for managers to have conversations with operators for 20 minutes each time. These short visits are often enough to elevate the standard, but I challenge to find a traditional organization where it is okay to keep an operator away from their work to have a discussion.
In the event of a standard not being followed, after the visit the manager goes back to the Kamishibai board and marks the card red. This doesn’t mean that someone is to blame, but that a deeper analysis is necessary to understand the gap, think about potential countermeasures, assign the resolution of the problem to someone and give them a deadline, and track any obstacles that might arise as a solution is sought out.
It is clear to me that companies that put such strong emphasis on standardization intrinsically respect their people. Telling workers what’s expected of them and giving them the tools to perform their jobs as well as they can is the highest form of respect.
We have so many lean tools at our disposal – to diagnose problems, to tackle them, and to sustain our results – but I think that the real breakthrough comes from learning how to integrate them. Extensive standardization coupled with the use of kamishibai boards empowers people at the gemba, ensures the continuous development of leadership skills and represents an effective way to ensure the sustainability of lean results.
THE AUTHOR
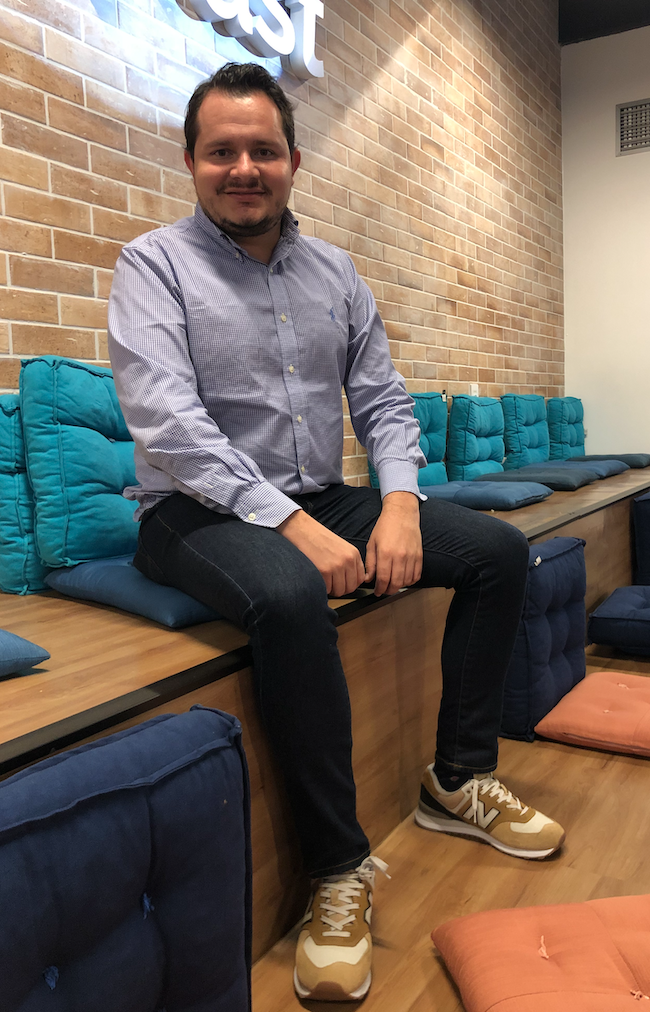
Read more
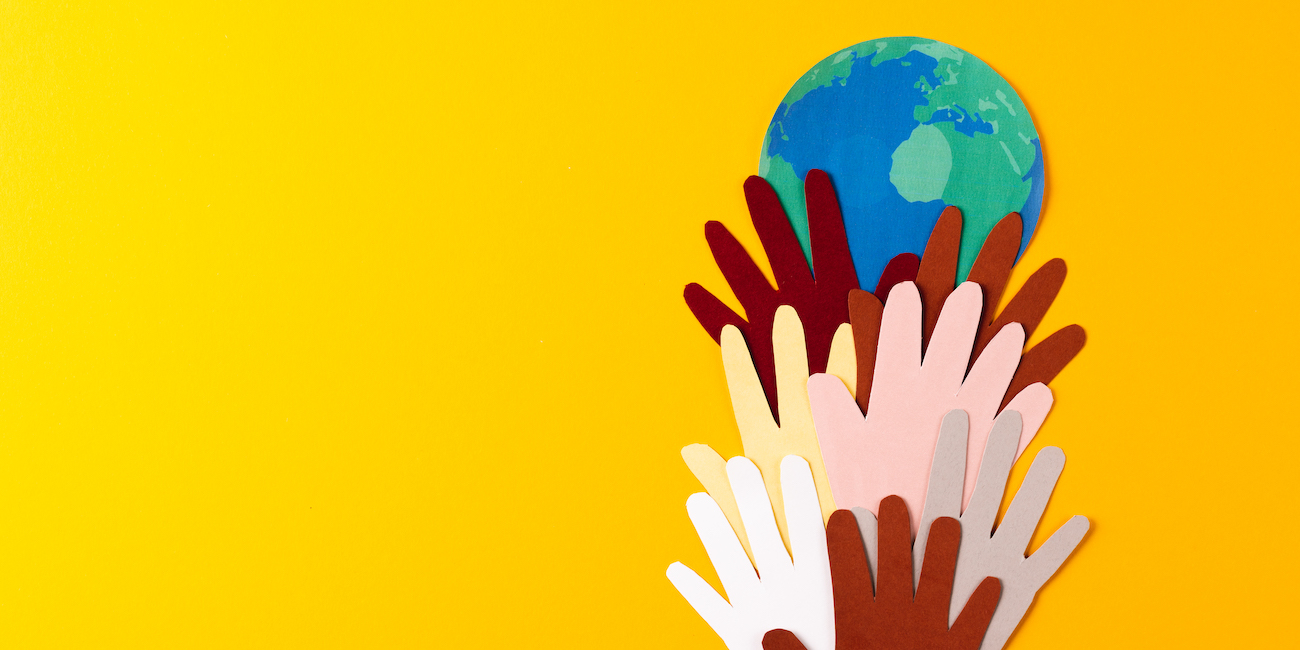
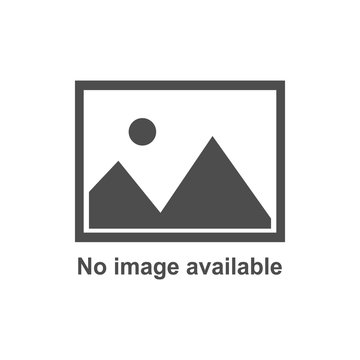
INTERVIEW - In this interview, Lynne Smith discusses the potential and difficulties of applying Lean Thinking to NGOs and looks back at the lean transformation at the Gates Foundation.
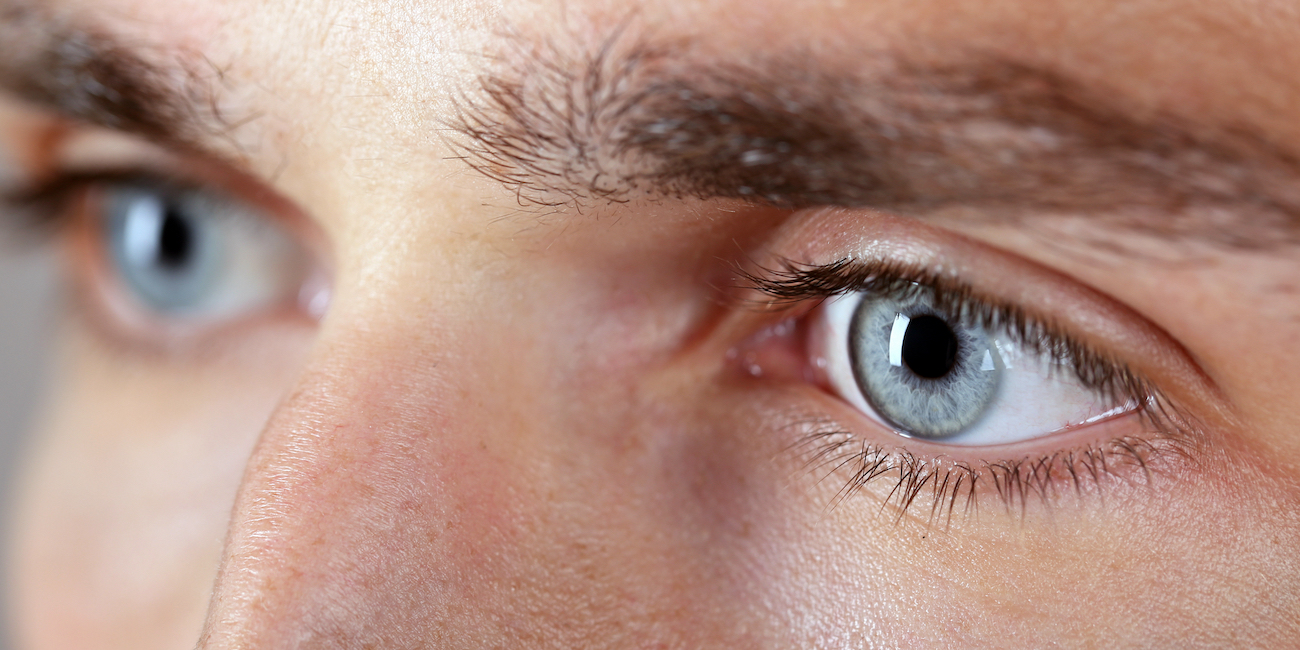
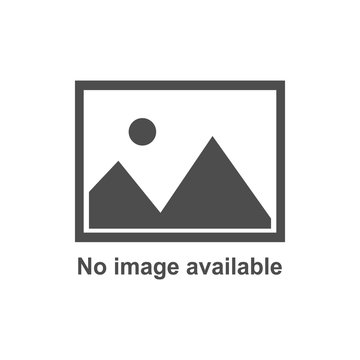
FEATURE – Whether improvement efforts are paying off and people are internalizing a lean way of thinking is a constant worry for many leaders. Here’s a trick to gauge how well – or how poorly – things are going in your transformation.
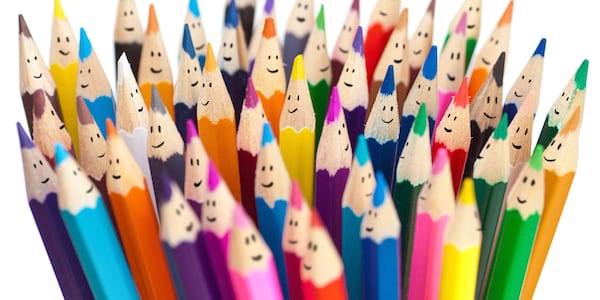
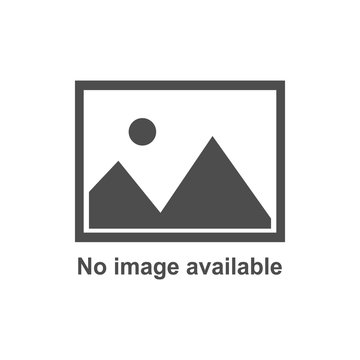
COLUMN - As the lean community grows, experimenting with tools for self-organization like Open Space in order to build stronger lean networks.
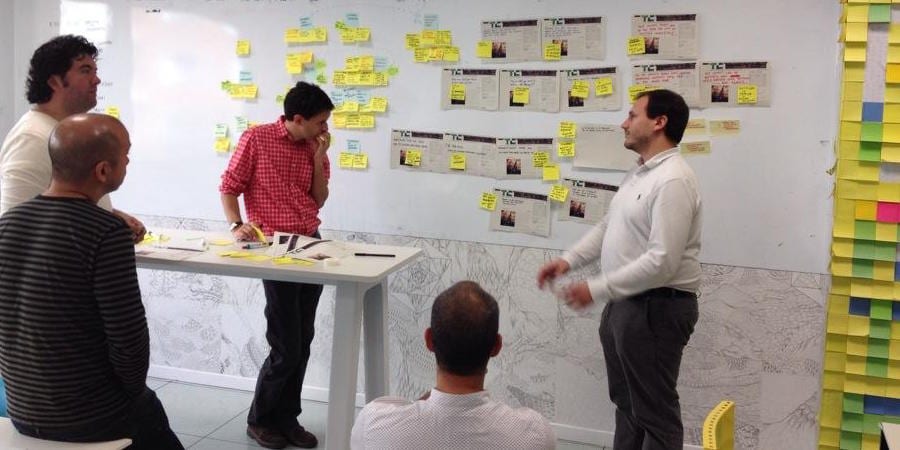
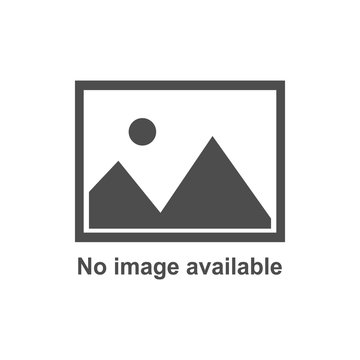
INTERVIEW – Planet Lean speaks with telecommunications company Telefónica about the organization's attempt to apply lean startup principles in its R&D department.