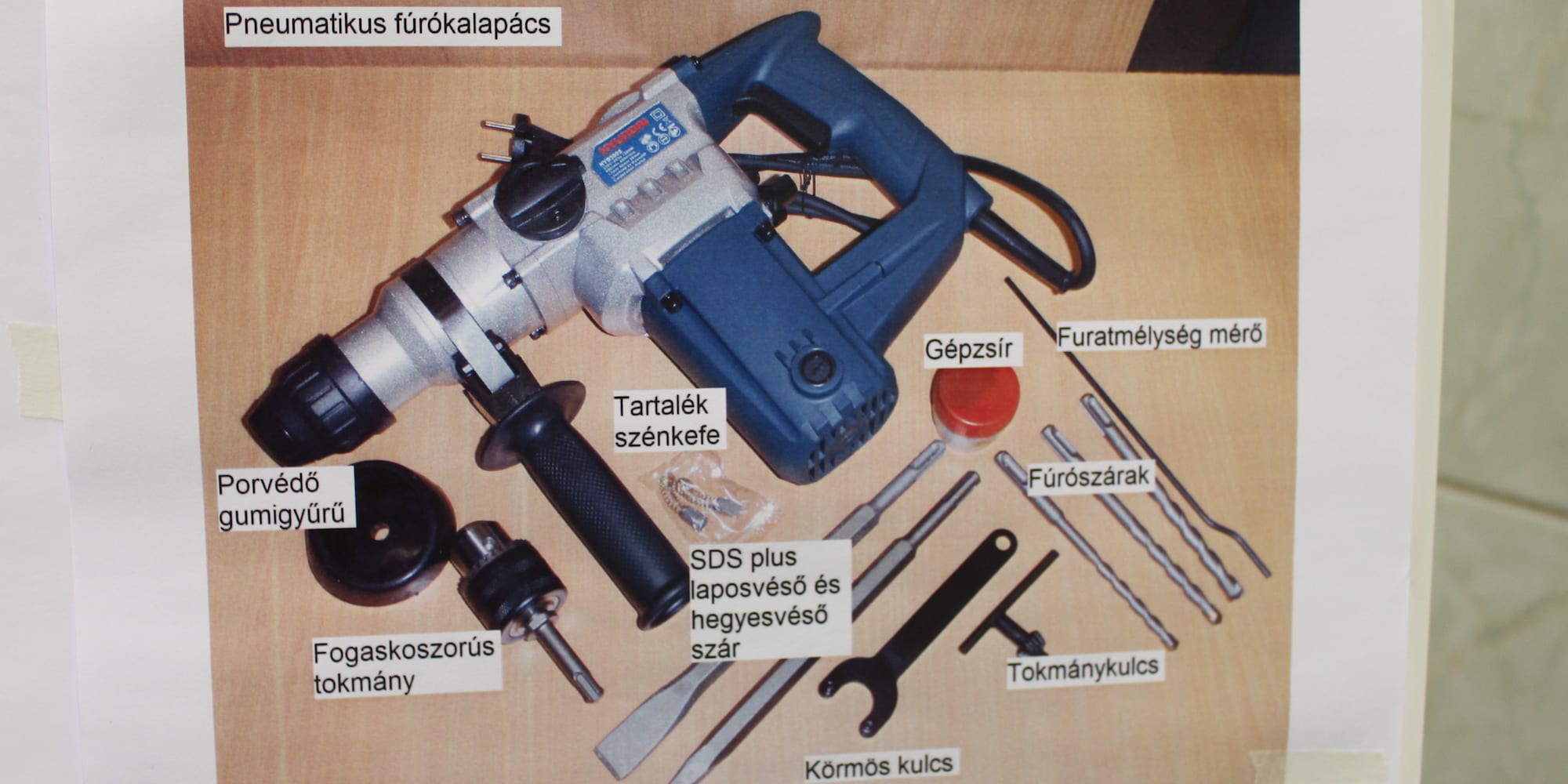
How we slashed waiting times for our customers
VIDEO INTERVIEW – A store manager explains how a simple kaizen reduced waiting times for customers who want to return products. We use today’s video to launch our Lean Improv contest.
Words: Zsolt Móczik, Deputy Store Manager, Praktiker Hungary
As a company, we want to make it easy for our customers to return products, should they wish to do so. So, when our transformation started, shortening the time it took them to return items quickly became a lean project at one of our stores in Budapest.
By observing the process, we realized that our Information Desk staff (those who in contact with customers returning products) wasn’t equipped to effectively and swiftly answer the query. They didn’t have the information they needed in order to make an informed decision on whether a product could be returned (if it’s been used, for instance, we don’t take it back), and as a resulted they used to rely on the salesperson from the area the product originally came from.
Not only did this mean a long wait for our customers, but also that our salespeople spent a staggering 51 days a year walking back and forth from their areas to the Information Desk, just to complete a process that other staff could have done… given the right information.
Take a look at this video to learn how we fixed the problem.
THE AUTHOR
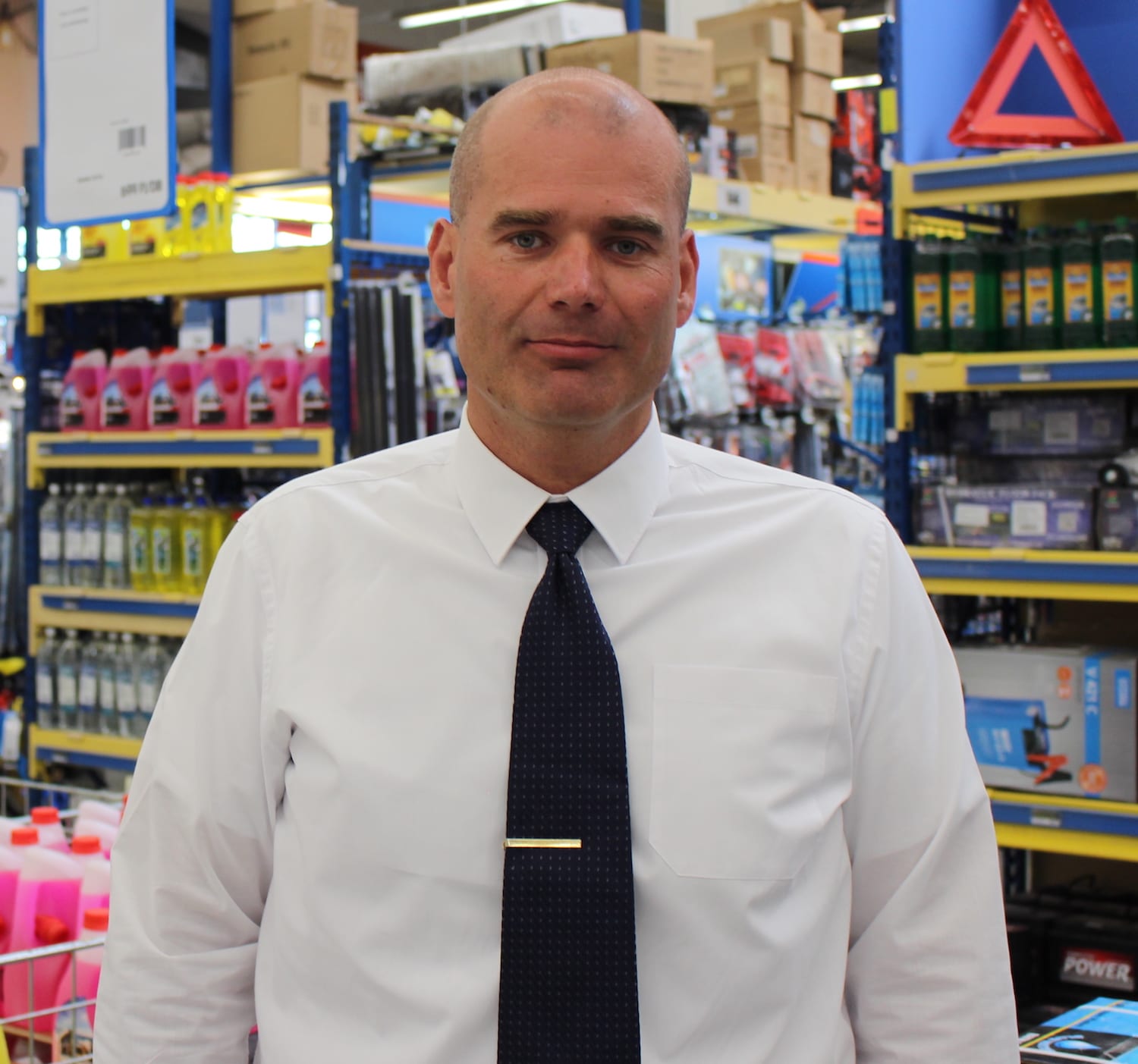
Read more
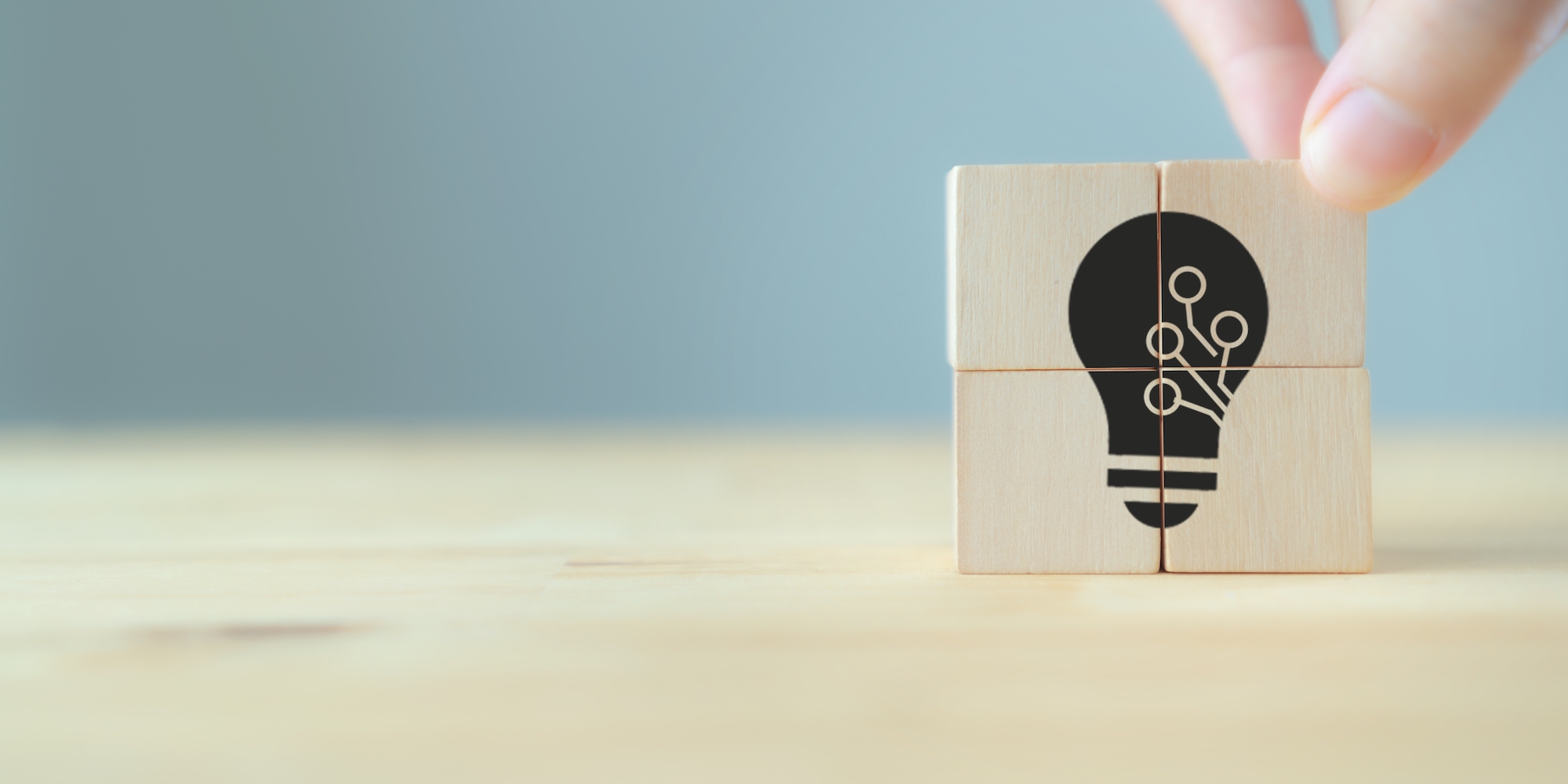
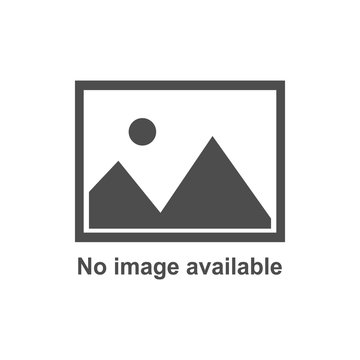
FEATURE – The authors explain why putting value at the heart of customer discussions is key to developing a successful, resilient tech firm.
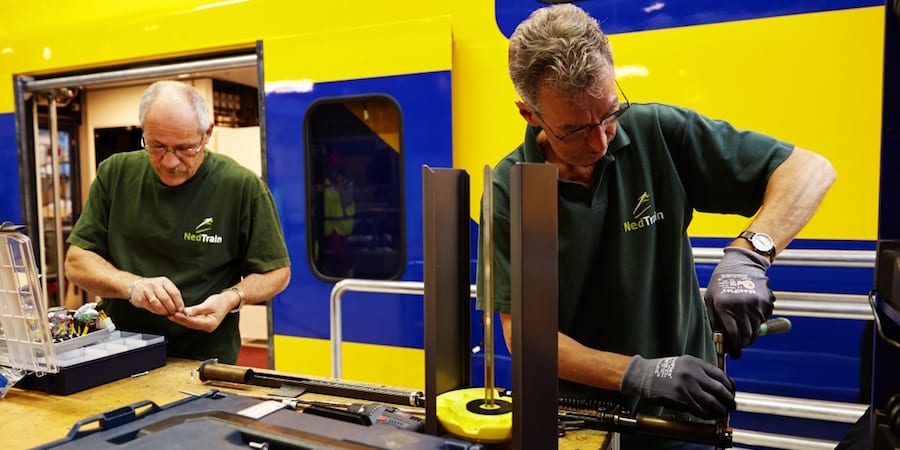
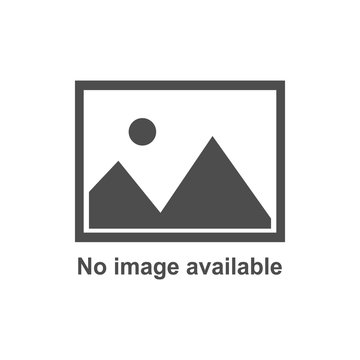
FEATURE – Faced with long lead-times to hire new people and with tens of millions paid in sick leave every year, the HR department of Dutch railway operator NS has turned to lean thinking to set them on the right track for the future.
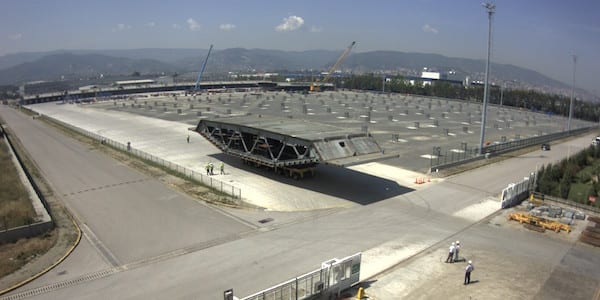
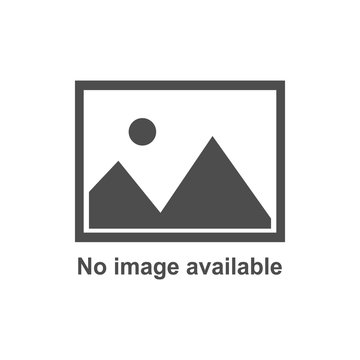
CASE STUDY - A Turkish shipyard and engineering company has found that lean principles and practice are the only way to deliver unique, large construction projects efficiently and successfully.
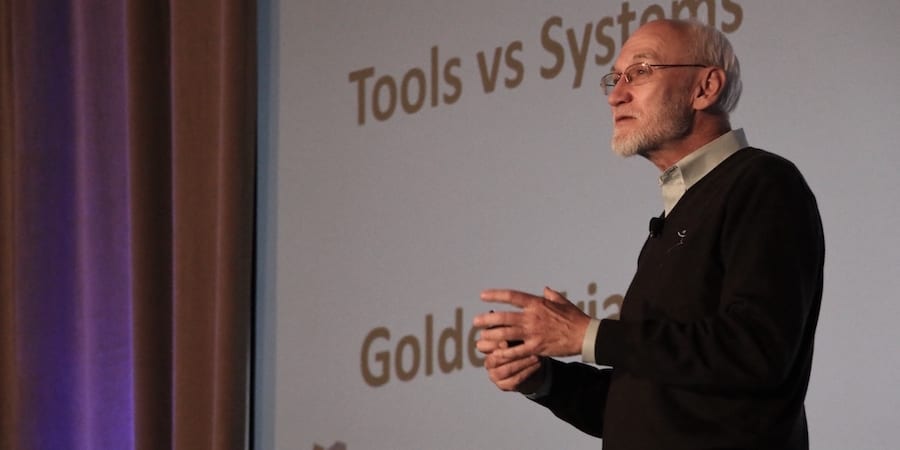
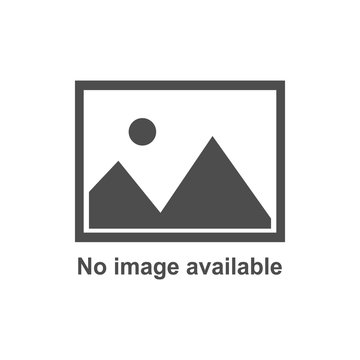
INTERVIEW – In this must-read Q&A, our editor sits down with lean guru John Shook to discuss the meaning of failure, the nature of innovation, and the resilience of our movement.