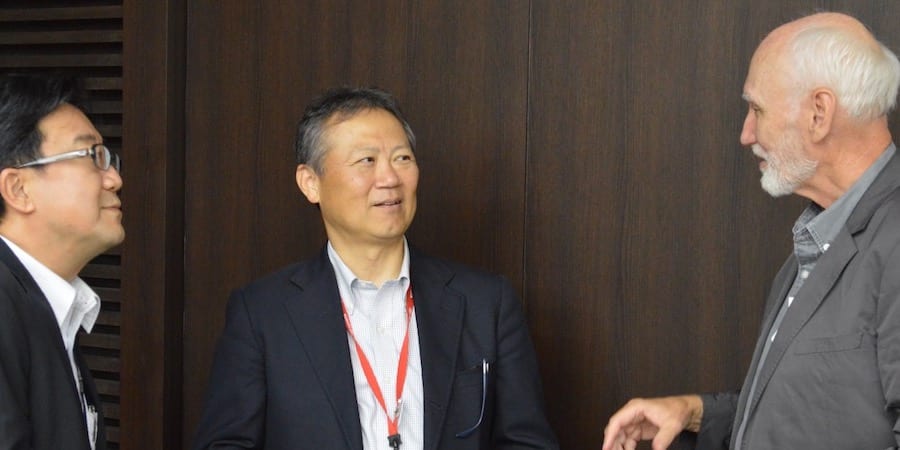
John Shook discusses Toyota and Japan at Nagoya station
INTERVIEW – For its 10th anniversary, the Lean Global Network went to Japan for a study mission. Our editor spoke with John Shook on a Shinkansen platform after four days in Toyota City and Nagoya.
Interviewee: John Shook, Chairman, Lean Global Network
Planet Lean: Why did you decide to come here with a united nations assembly of 40 individuals from 20 countries?
John Shook: A year ago, we came up with the idea to go to Japan for our annual Lean Global Network meeting. We wanted to observe what Toyota is doing and deepen our understanding as a group.
That’s how forty of us “LGNers” ended up in Toyota City for a week. The group was incredibly diverse: some people had worked for Toyota for several years, while others had never visited the company (some had never set foot in Japan). With so many different perspectives, the study tour appeared as a great learning opportunity from the get-go.
Our aim was to do a deep dive into Toyota. Instead of exploring the high-tech side of the story and the work Toyota is doing on next-generation powertrain or autonomous driving, however, we decided to focus specifically on the company’s attempt to go “back to basics”. We wanted to really understand Toyota’s big focus on going back to the fundamentals that began to shape its DNA around 70 years ago.
Toyota’s move towards its original principles came a few years ago at Akio Toyoda’s behest, in response to the recall and financial crises of 2009-2010. It stemmed from the belief that the only way to sustain who Toyota had become – a massive global company producing 60 models – was a return to the fundamentals. To remain successful, Toyota set out to find a way to ensure that the infrastructure and bureaucracy that come with being a large organization would support the work, rather than get in the way. From our visits, it was clear how committed the company is to this new approach.
PL: What does “back to basics” mean at Toyota?
JS: Good question. As with so many terms or concepts, when it comes to Toyota, things often carry deeper or more multi-layered meanings than appears on the surface. In this respect, the “back to basics” idea at Toyota today doesn’t mean merely doing the same things as before. Instead, it means that the fundamentals are re-emerging in different forms to meet new realities. A perfect example of this is TNGA (Toyota New Global Architecture). In Toyota City, we learned a lot about TNGA, both from Masato Katsumata, Chief Engineer of the Camry, and from Toyota suppliers, who told us how they are interfacing with the new approach to bring flexibility in production (by standardizing designs and making assembly easier) and improvements in the appearance of models.
We realized that TNGA is a way of maintaining organizational teamwork effective in the interest of making products that customers want, and in the face of the tremendous complexity resulting from having a growing portfolio of products and a global and diverse supply base. Critically, what TNGA does is adapting Toyota’s original ethos and principles to today’s circumstances. This applies to the Chief Engineer system developed in the 1950s: it serves Toyota well for half a century, but over the past 20 years circumstances changed, making it less effective than it used to be. Indeed, part of what makes Toyota great is its ability to adapt to change.
PL: Did we have to come all the way to Japan to learn these things?
JS: That relates to another recurring theme throughout the week: why go to Japan? Many lean practitioners come here to visit Toyota, but one could very well ask why they bother flying all the way to Far East when there are so many great Toyota plants and examples of lean thinking elsewhere in the world. There are of course reasons lean developed in Toyota City, however, and one might say the spirit of lean is still best seen and felt at its place of birth. As mentioned above, Toyota’s constancy of purpose and tenacious kaizen determination throughout its journey are still extremely inspiring.
We’ve been asking ourselves this question: while lean is not uniquely Japanese, would its “invention” have been possible outside of Japan? Through books, we can understand the political and economic environment that led to the creation of TPS. But what about the basic thinking and behaviors – in other words, the culture – of the Japanese? Have they enabled the invention and sustainment of TPS?
To these two dimensions of lean – Toyota and Japanese culture – we then added a third: humanity. Are there any universal human traits that inform and shape lean thinking?
This is what led the LGN group to travel to Japan. We wanted to learn more and potentially find a way to answer these compelling questions:
- What, if anything, is unique to Toyota about lean thinking and practice?
- What, if anything, is Japanese about lean thinking and practice?
- What, if anything, is universal to humans about lean thinking and practice?
EDITOR’S NOTE
Following my conversation with John on the Shinkansen platform at Nagoya station, we traveled as a group to Tokyo where we were hosted at Professor Taka Fujimoto’s Monozukuri Kaizen Center at Tokyo University. John led the group through a structured reflection of what we had learned using a triad (pictured below). We assessed our thinking before we left (we had all placed a dot inside the triad based on where we thought lean thinking and practice belonged) and noted how our thinking had shifted based on what we learned during the study mission. We found this triangulation to be thought-provoking, as it prevents the tendency toward easy answers to simple dichotomies. Following the triangulation exercise, we reflected more concretely on how to use what we had learned to inspire us, as a network, to new ways of thinking. We see this as useful to stimulate us to consider new and better ways to serve the global lean community going forward.
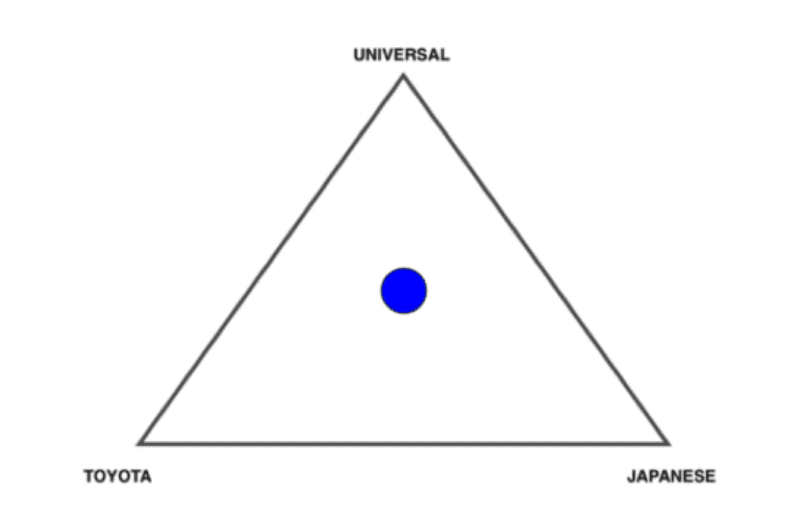
THE INTERVIEWEE
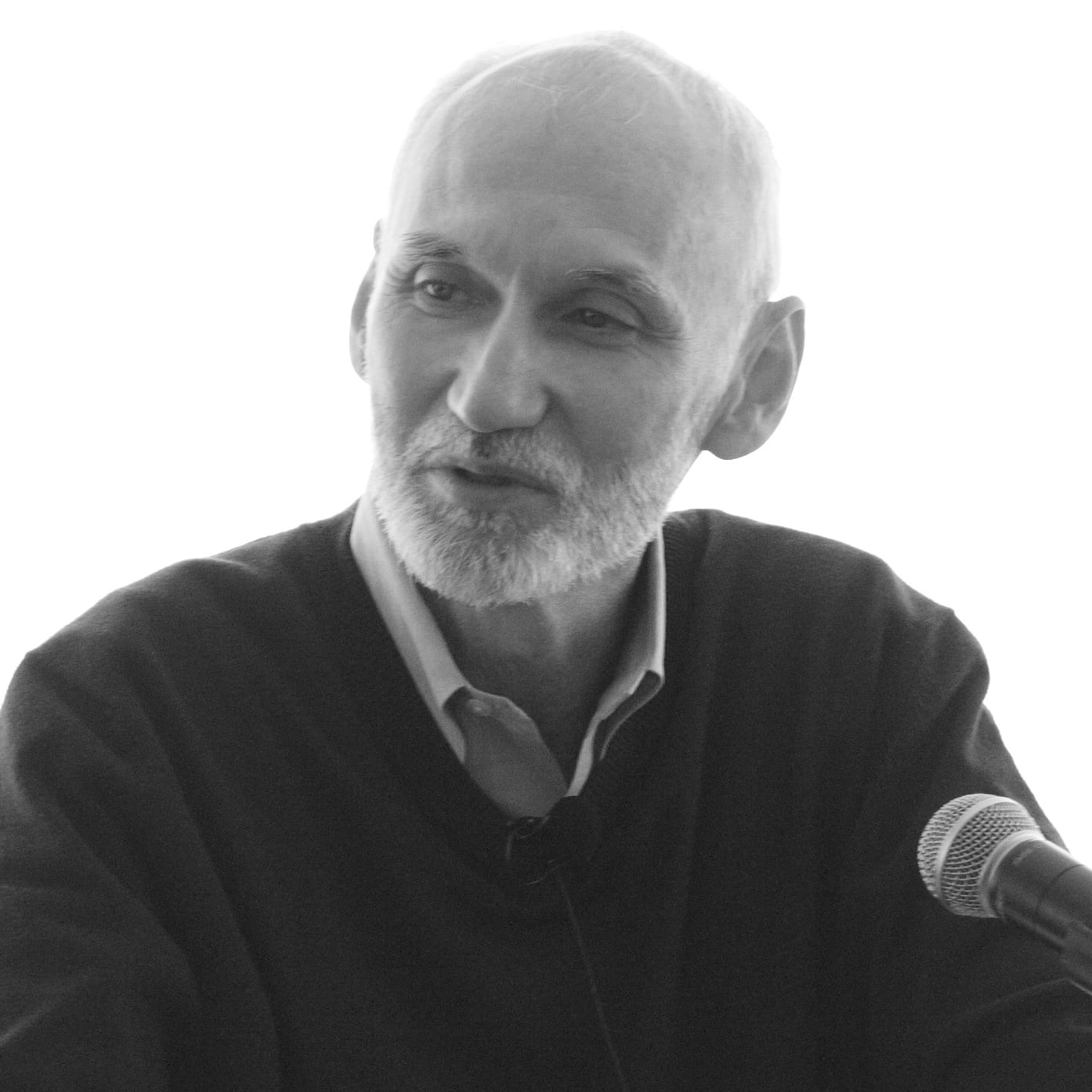
Read more
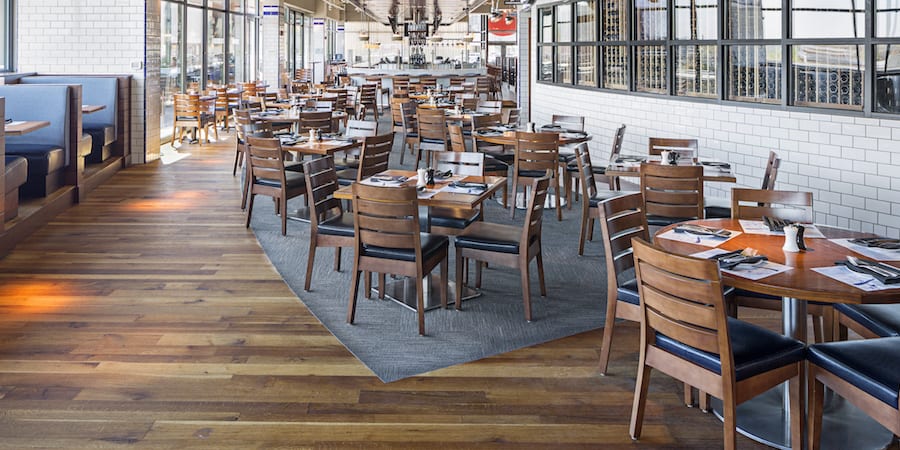
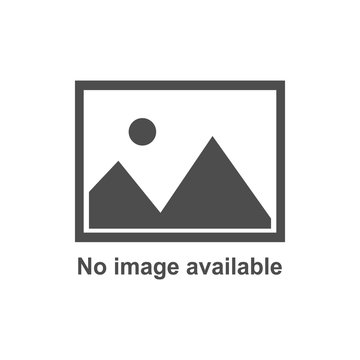
INTERVIEW – An American group of restaurants is experimenting with the application of lean thinking in its kitchens and dining areas. Planet Lean had a word with the chefs to see what’s cooking.
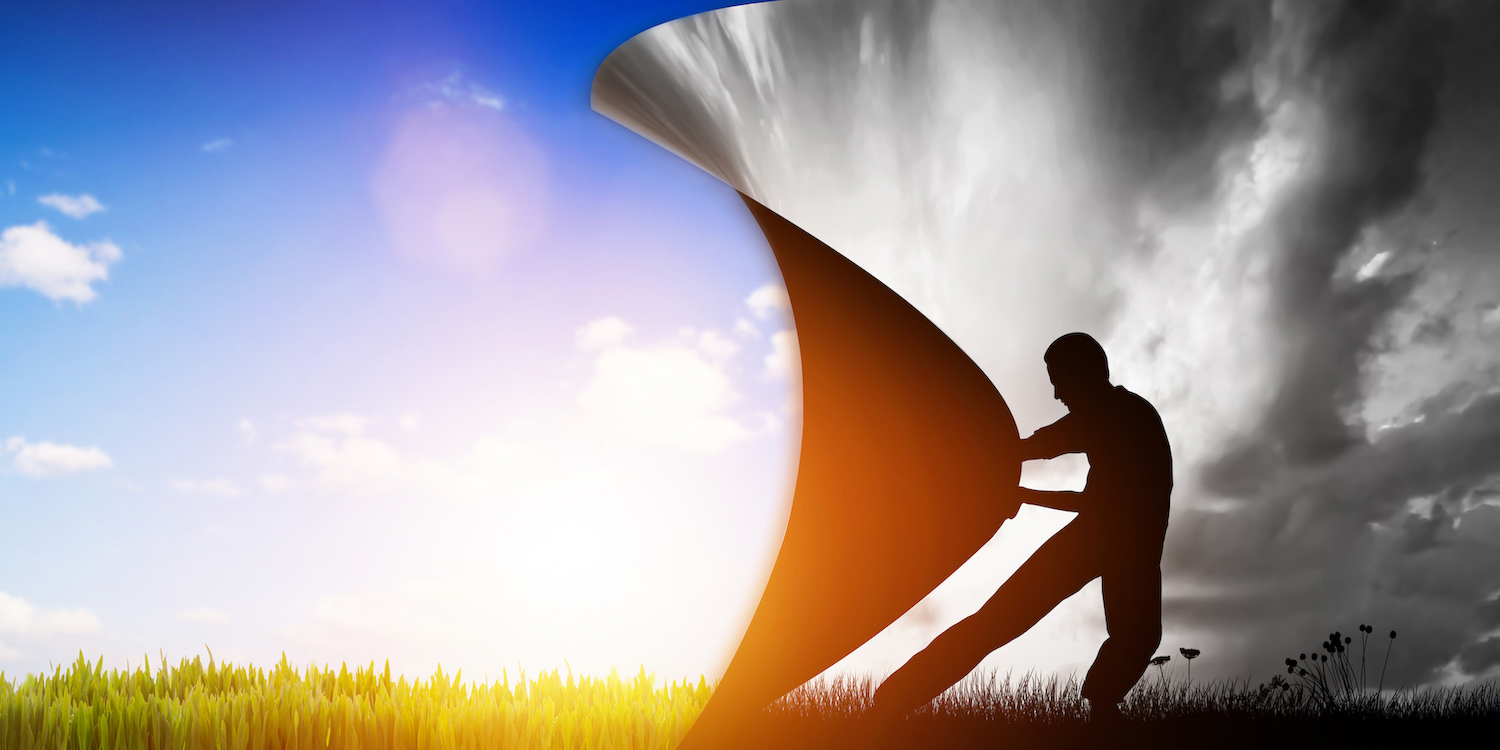
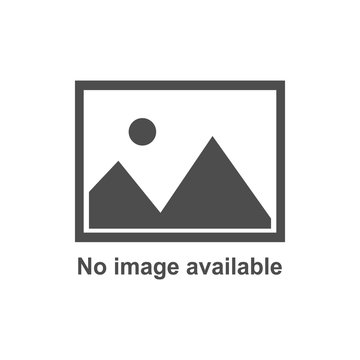
FEATURE – The author discusses how the daily practice of lean thinking develops perseverance and the grit a leader needs to improve an organization.
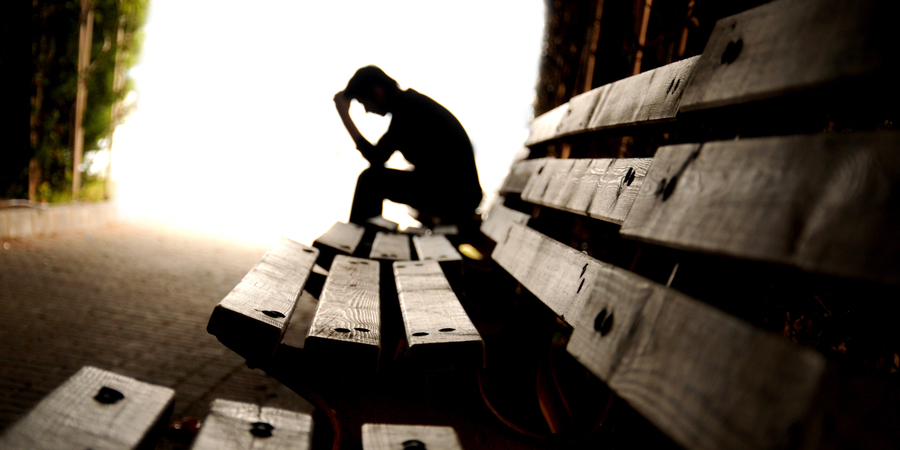
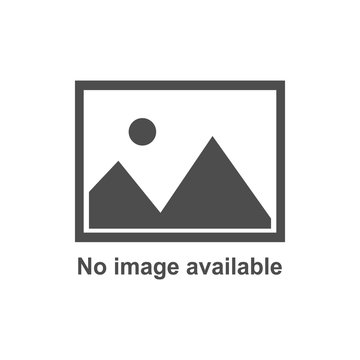
FEATURE – Ahead of the annual lean conference of LEI Polska, the authors reflect on a recent survey they ran with their clients on the key business challenges they face.
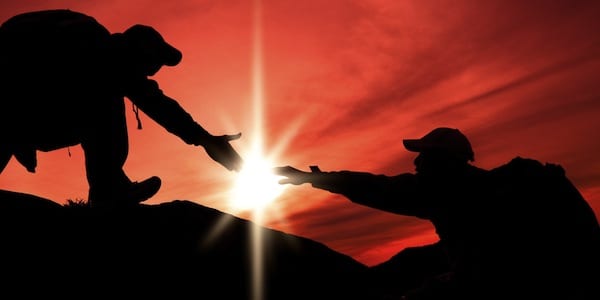
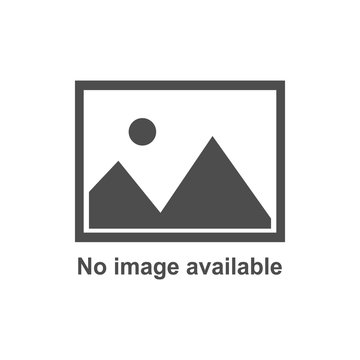
FEATURE - Two weeks ago, the authors shared their thoughts on mindset. In part 2, they discuss how to grasp the true spirit of lean.