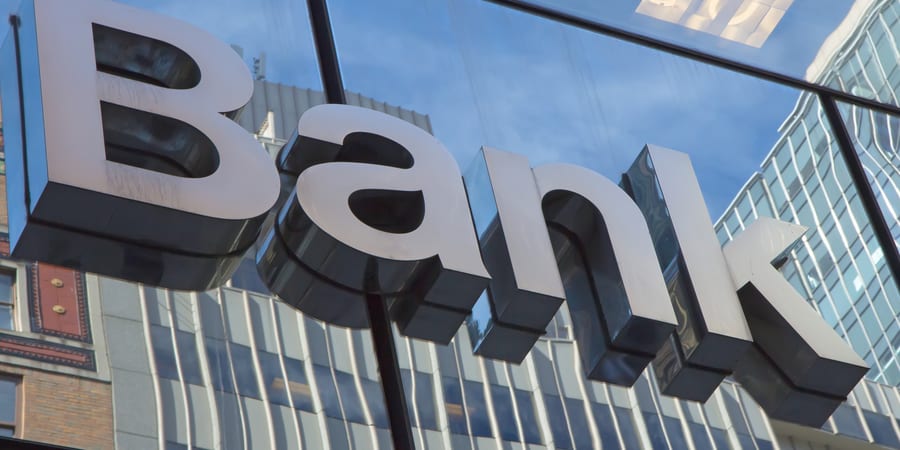
How Banca Nazionale del Lavoro used lean to improve its IT department
INTERVIEW – Planet Lean interviews Silvia Cespa of Italy’s Banca Nazionale del Lavoro, a bank that boasts one of the most advanced IT departments in Europe. How did it get there? Through a six-year transformation towards lean banking.
Interviewee: Silvia Cespa, Lean IT coach, Banca Nazionale del Lavoro
Roberto Priolo: What problems were you facing in the IT department at BNL when you decided to start implementing lean thinking?
Silvia Cespa: Lean was already present in other departments within Banca Nazionale del Lavoro (which is part of BNP Paribas), and when IT had the opportunity to join this initiative, around six years ago, we saw it as a way to potentially improve things. In the end, lean did much more than that. It completely revolutionized the way we work as a department.
RP: What were the big phases in the lean transformation of the IT department at BNL?
SC: We started off with the maintenance teams for a couple of reasons. First of all, it seemed logical because in IT maintenance activities are the ones that most resemble industrial operations. Secondly, we were spending a lot of time and resources to help users with IT applications that constantly caused problems, but we didn’t understand why there were so many issues.
Of course, the problems we were seeing in maintenance were a result of mistakes made in the development phase. So our second move was to work with project teams. People were rushing to complete projects all the time, which often had a negative effect on quality.
We focused a lot on developing people’s capabilities as a way to tackle issues with the development function, but once we went down that path, we realized that most problems related to projects were actually caused by the type of requests the teams received.
We had to think differently, and decided to extend our lean efforts to the people who were requesting a specific service. We analyzed the situation, and found out that many times the function asking for the project teams’ help or for the development of a specific IT feature was unaware of the end user’s actual needs. They didn’t always know what the customer needed, which resulted in requests that the teams found difficult to interpret.
That’s when we introduced ACE Fast, the first big revolution in the world of IT project development at BNL. With ACE Fast, we had business functions work with us to define not what we had to develop, but the problems and needs of the end user that the bank had to solve.
This way we “forced” the business and the IT department to get out of the room and “go and see” the end users. This was the third phase in our journey. At this point the value chain was beginning to work more seamlessly: because we knew what an application was going to be used for, it became easier for us to develop it.
Before long, the problem of how we could develop a product that actually met user needs came up. So we dug deeper.
We had already found out how to maintain an application, how to manage a development project, what we had to develop, so a natural next step was to involve the end user to learn how we had to develop a feature or an application.
That’s when we moved to the latest phase in our transformation. We call it Paper Mockup. We invite users to work with us to understand what they need from an application. This has a double advantage: first of all, users understand how important they are to us, and secondly, we are able to eliminate rework because we are told from the outset what an application should be like. Users are happier, and we are much faster.
Essentially, every time we solved a problem throughout our journey we realized there was another one that needed our attention. That’s how we went deeper into the analysis of our processes and ultimately got where we are today. We have had great results: we have substantially shortened the time needed to prepare for a project, even by 70% in certain cases, and we have also reduced the time and effort related to functional analysis by around 30%.
RP: What can you tell me about hoshin kanri at BNL?
SC: Upon seeing the first results, management got really excited. Not just about the operational improvements we had achieved, but also by how our people had gained back control of their work and by their enthusiasm. It’s like they were reborn.
Management realized there was something to lean, and decided to explore it, and support it, more.
This of course resulted in the implementation of hoshin kanri (it was 2011), which has slowly been eroding the barrier that traditionally sits between top management and the front line. The four KPIs we came up with are the KPIs of the whole organization. They are understood and owned by everybody. That’s where the real change was.
RP: Why do you think this implementation was so successful?
SC: What I see is an organization full of people who want to do well, even when it costs them a lot – working on Saturdays, or until 10 at night. All of this is testament to how committed our team is. People at BNL care for their work and for the business. (Even though they often complain about it, but hey… we are Italian, we like to complain!) At first all we heard was, “We are not Japanese,” whereas now people know that the problems of users are their problems.
RP: How does the role of IT change in a lean organization compared to a traditional business?
SC: By definition, IT facilitates and enables. What changes with lean is that IT becomes an informed and responsible facilitator. The role of IT doesn’t change, but the understanding of its role does.
THE INTERVIEWEE
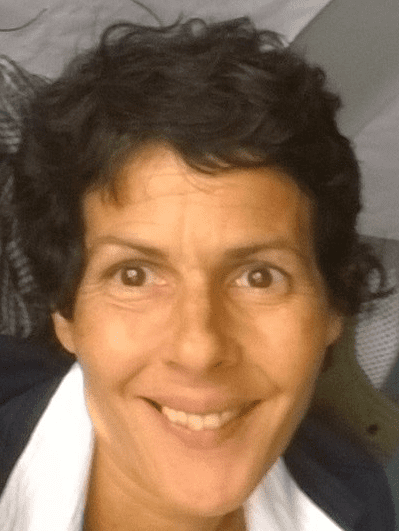
Read more
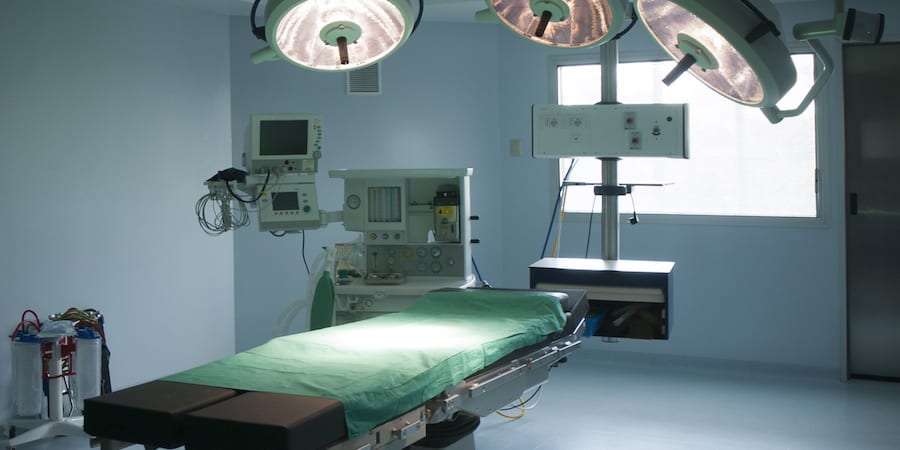
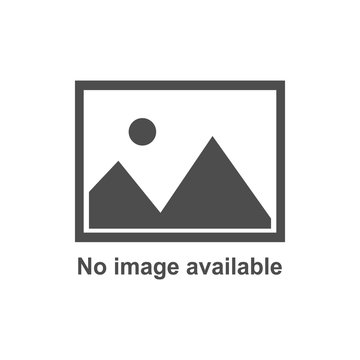
INTERVIEW – At the recent Lean Healthcare Transformation Summit in Brussels, Planet Lean editor Roberto Priolo sat down with John Toussaint to discuss the state of lean thinking in healthcare, its challenges and its opportunities.
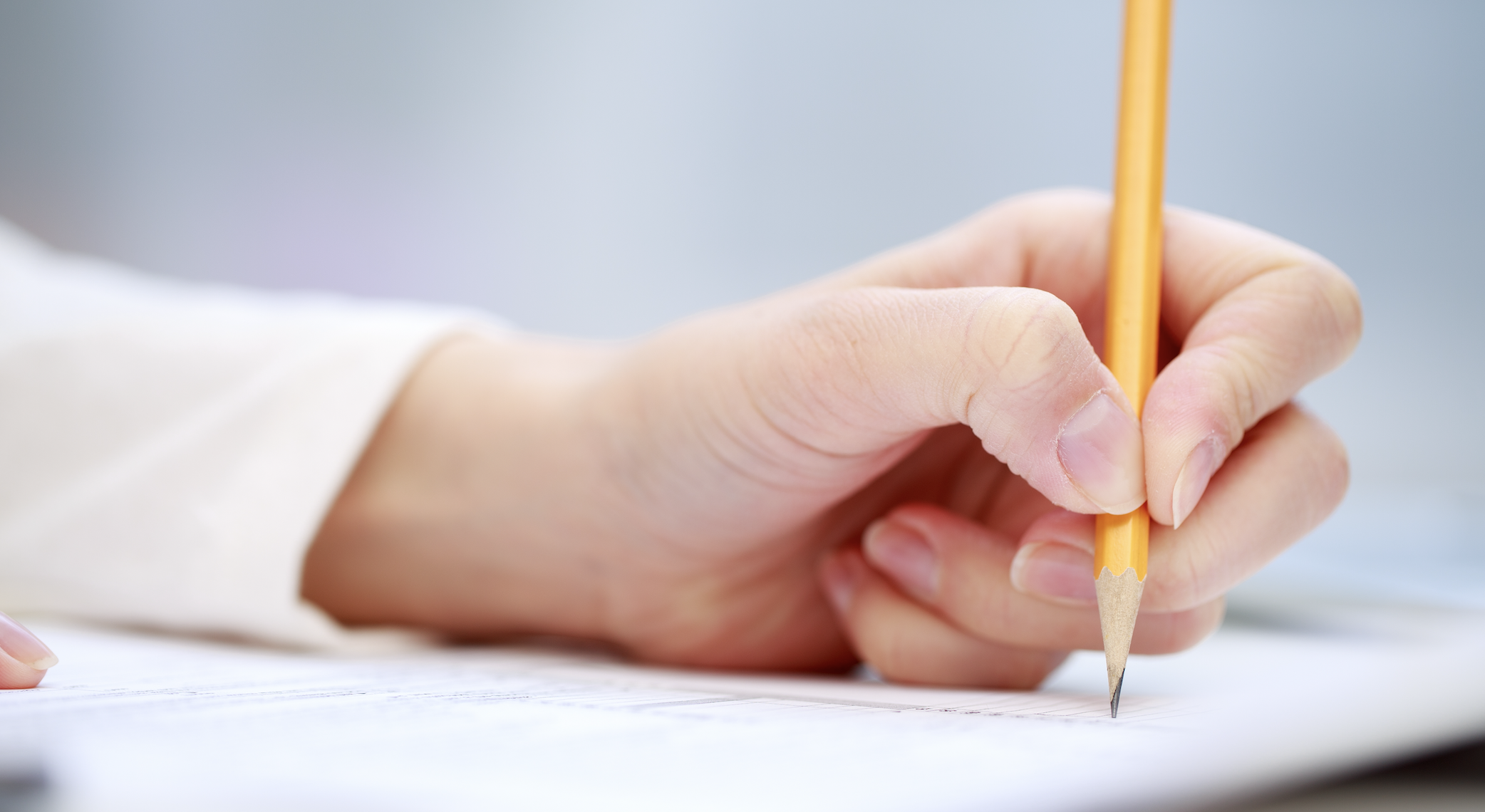
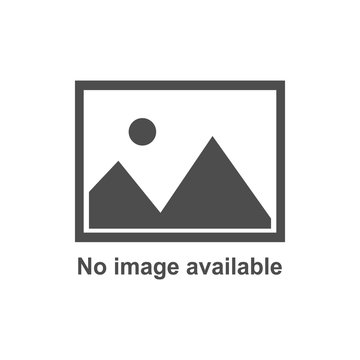
FEATURE – Using her distinctive narrative style, the author breaks down the A3 process to help you understand how it works and how you can tap into its potential.
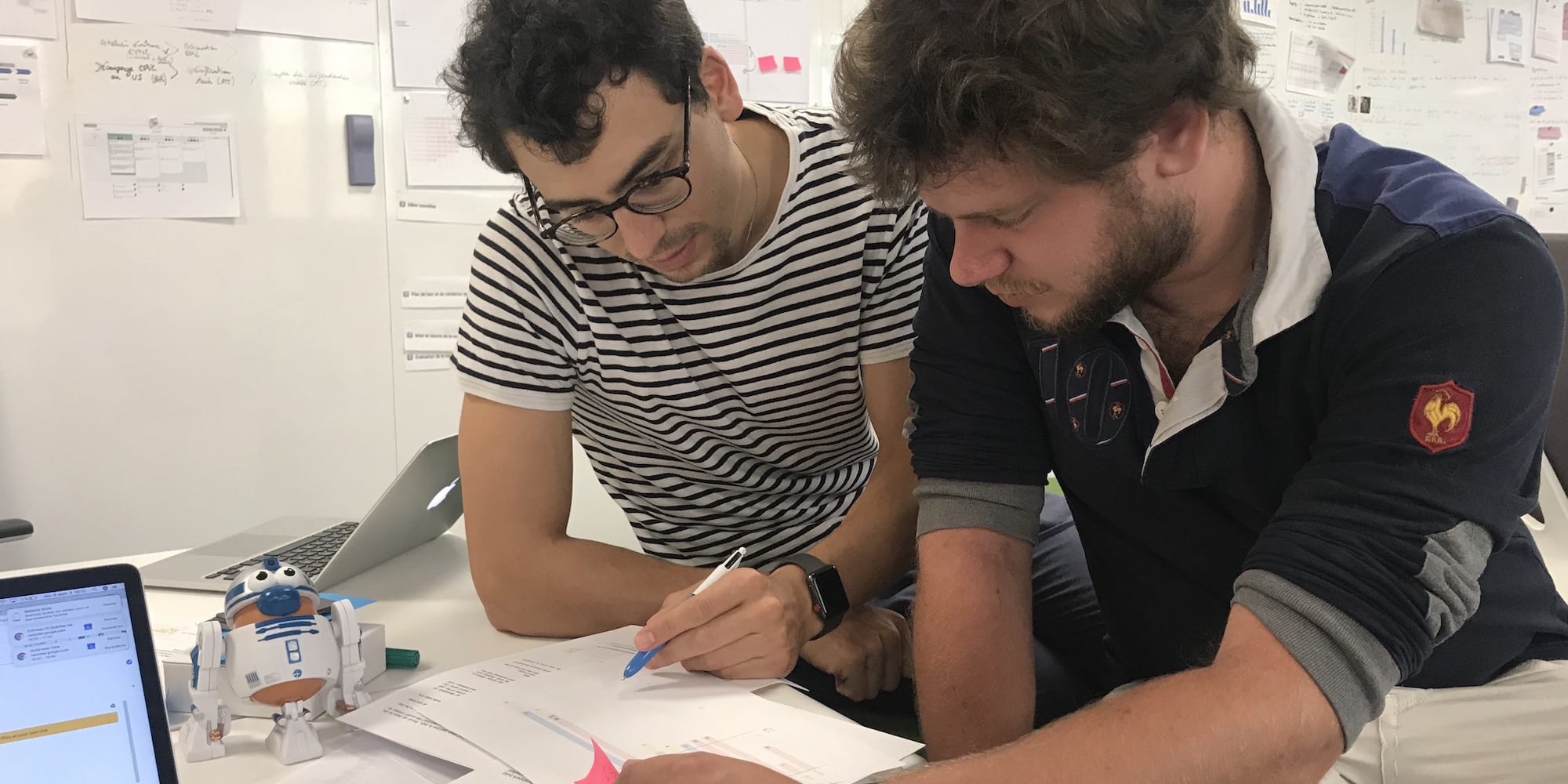
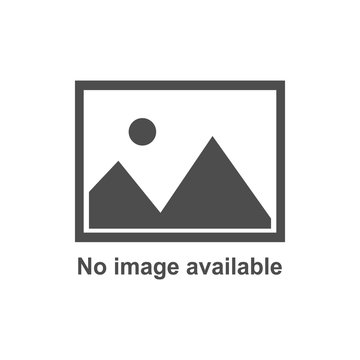
BUILDING BRIDGES – In another article for their series, lean digital company Theodo tells us about their efforts to measure and reduce its lead-time to deliver product features.
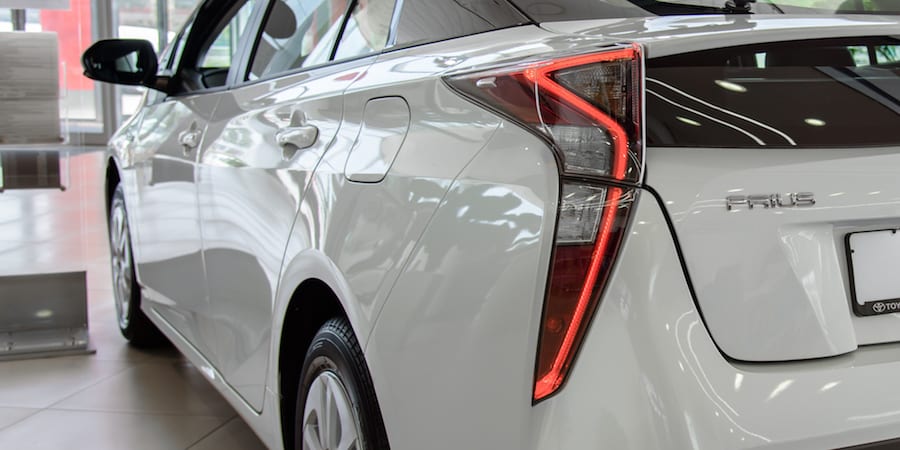
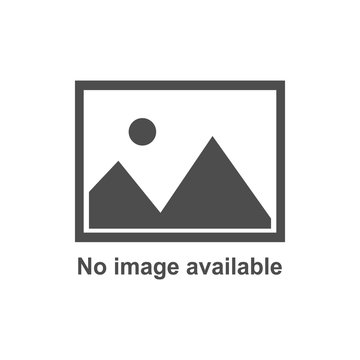
FEATURE – Following a webinar with product development expert Jim Morgan, the author reflects on what the Toyota New Global Architecture and Chief Engineer system can teach us.