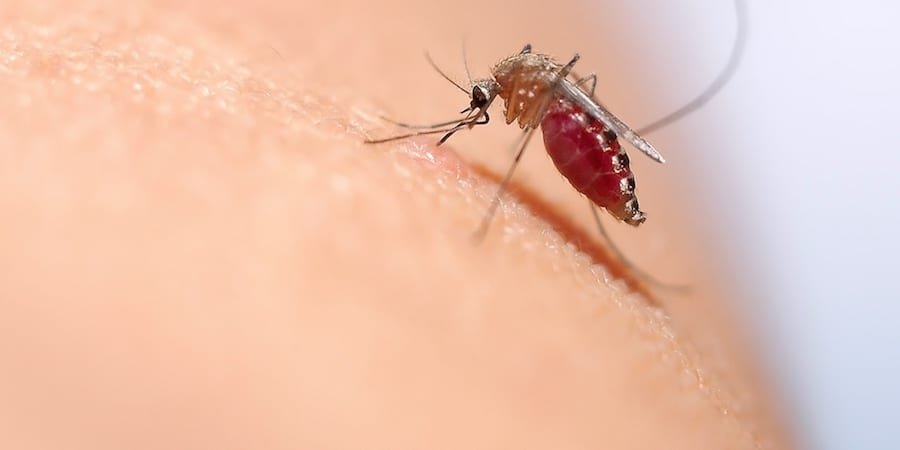
Lean is helping a Brazilian hospital fight dengue fever
FEATURE – By using lean management, the Hospital São Francisco (HSF) near São Paulo, Brazil, has improved its ability to deal with dengue epidemics – treating patients more quickly and efficiently.
Words by: Flávio Battaglia and Tamiris Manzano, Lean Institute Brasil
Every year, dengue affects between 50 and 100 million people worldwide. The incidence of this mosquito-borne viral infection has increased alarmingly since the 1950s: back then, only nine countries recorded cases, while today more than one-hundred do. This includes Brazil, which has had more than seven million cases since 2002.
The infection causes a flu-like illness, which occasionally develops into a potentially fatal complication, which is known as severe dengue. While there is no treatment for dengue or severe dengue, according to the World Health Organization early detection and access to care are enough to lower the death rate to below 1%.
Over the past five years, the Brazilian city of Ribeirão Preto has faced three dengue epidemics – in 2011, 2013, and 2016 – which the 165-bed Hospital São Francisco (HSP) is now learning to deal with using lean thinking to quickly and efficiently care for a growing number of affected patients.
THE FIRST TWO EPIDEMICS, AND THE LESSONS LEARNED
In 2011, shortly after HSF had completed the expansion of its emergency care unit, the first outbreak of dengue occurred. Projections for that year suggested the ER would receive 12,000 patients a month, but the epidemic (which came to represent 32% of the patients the hospital was seeing) had pushed that number to 28,000 by April.
At that time, the hospital wasn't using lean thinking (their journey started in 2012). Instead, they decided to build a House of Dengue right in front of the emergency room, a building exclusively dedicated to caring for dengue patients. Despite the big investment and the many difficulties encountered, the building helped HSF to overcome the first epidemic without registering any deaths, which was a huge cause for celebration.
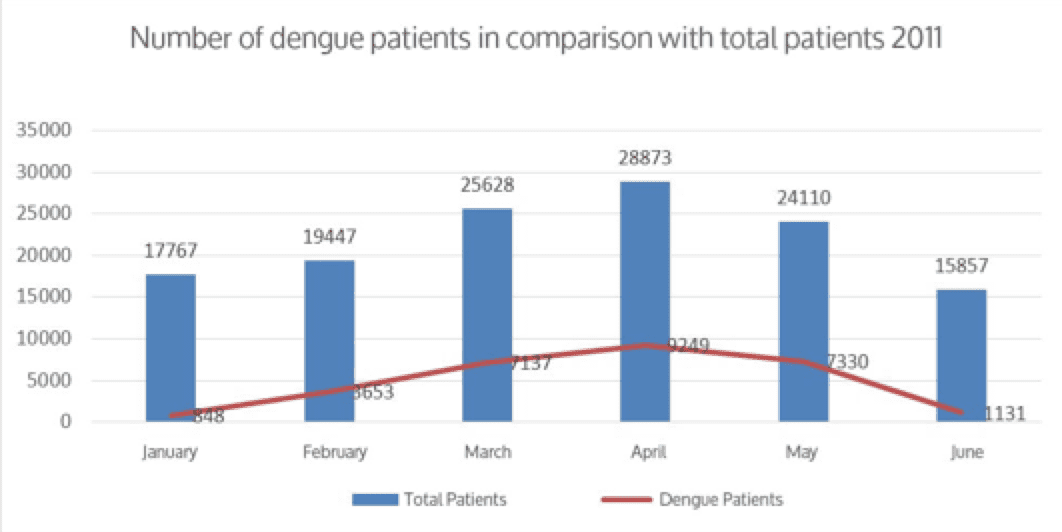
In 2012, the number of dengue cases started to fall rather quickly and the epidemic appeared to be over. Due to the lack of space in the hospital, it was decided that the House of Dengue would be used for other activities that at the time HSF could not accommodate. Unfortunately, the following year Ribeirão Preto suffered a second dengue epidemic: the outbreak increased the total number of ER patients to more than 23,000 in April 2013, with nearly 9,000 of these – 37% – coming to the hospital showing symptoms of the disease.
With the House of Dengue no longer available and most of its professionals not trained to deal with an epidemic (due the turnover of medical staff), difficulties quickly arose. This time, however, things would be different, as HSF had started applying lean thinking.
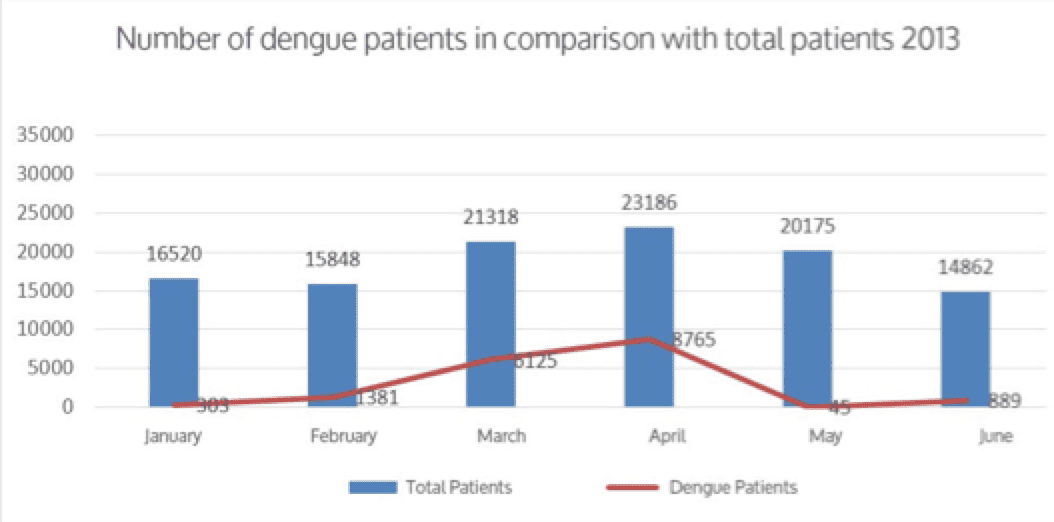
THE ROLE OF LEAN
It had now become clear that dengue outbreaks cause a spike in hospital demand and bring chaos in the provision of care.
Like for most diseases, prevention and early diagnosis are the most effective countermeasures in the fight against dengue. To speed up the whole process, HSF introduced flow in its operations – from arrival to the emergency room to diagnosis: after traditional screening, dengue patients were now directed to a dedicated care pathway, which includes blood sample collection, a visit by a doctor, and either a prescription or direct discharge with a follow-up visit scheduled.
To quickly identify dengue patients (whether returning for testing or suspected of having contracted the virus) and easily distinguish them from the rest, the hospital asked them to wear an orange bracelet. (The same color is used to identify dengue patients in the IT system.)
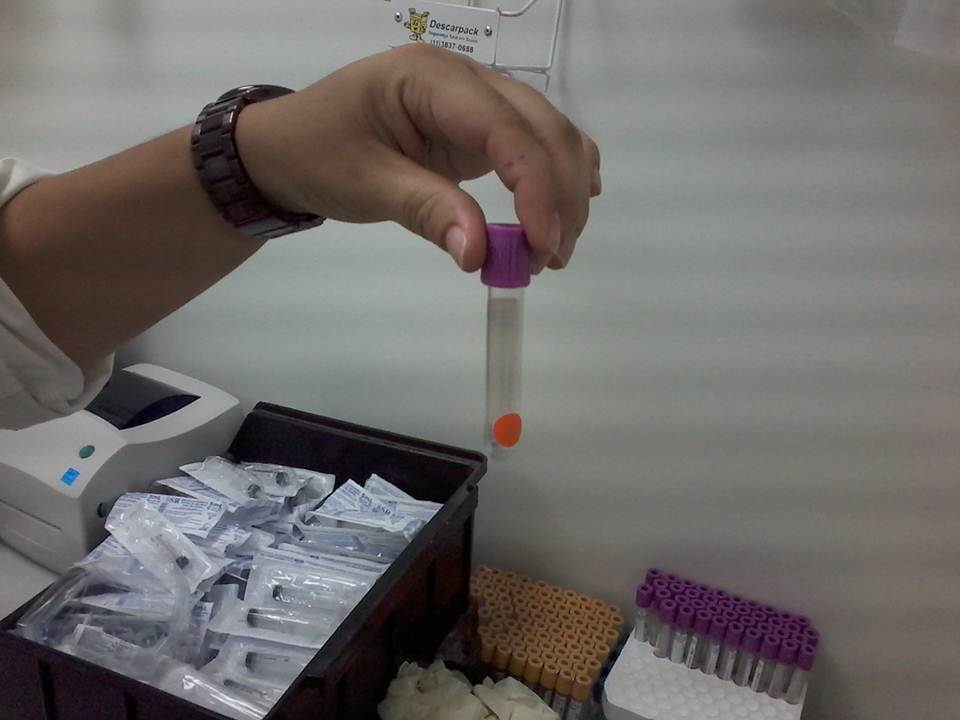
Nurses were given the authority to screen patients independently and send them to the blood-testing unit to collect their sample (carrying out medical exams prior to a visit is not a common practice, but the acuity of the crisis called for it), while all dengue-related tasks for doctors were standardized.
To facilitate staff's access to information and improve the visualization of patients' clinical data, the hospital started using a "dengue card" for every patient, which at each visit gathers all relevant information on tests results, treatment given and potential signs that a patient might have to be readmitted. Efforts were also made to schedule follow-up visits and try to avoid peaks in the number of arrivals by balancing demand (dengue fever lasts from five to seven days, and patients have to return to the hospital every day or two).
Speaking of tests results, these are traditionally performed in a different area of the hospital. To establish continuous flow, however, HSF introduced working cells in the ER tasked with collecting samples, analyzing them and releasing the results in the form of a report – which massively contributed to reducing the "delivery time" of lab results. To accommodate the cells, but also the new flow-based system, the layout of the ER was changed.
For the hospital, it is important to work with patients to help them familiarize themselves with the risks of dengue and learn how to prevent it: as part of this effort, every dengue patient is now given a bottle of water – hydration plays a big role in recovering from the disease – and posters and boards have been placed on walls around the hospital, explaining what dengue is, how it is transmitted, how it should be treated, what are the warning signs that the infection might be getting worse, and what measures can be taken at home to prevent the disease from spreading. (Educational material also uses video content and Whatsapp messages.) This would not have been possible without lean teaching the hospital to look at the idea of value from the customer's perspective.
However, none of these improvements (which were achieved over time) would have succeeded without the training sessions – both for individuals and groups – that the organization provided to all staff involved in the dengue patients value stream. A big warning sign that staff hadn't received enough training came while monitoring the collection of specific tests for diagnosing dengue (NS1), which recorded several mistakes and deviations from standard. Once these were fixed, the hospital was able to save more than R$65,000 (about $19k) – which covered the investment necessary to distribute the water bottles to dengue patients and to introduce visual management in the ER.
THE THIRD EPIDEMIC
This year Brazil is experiencing the worst dengue epidemic in its history. Historically, dengue epidemics start in January and peak in April. In November 2015, the team in the ER started to notice an increase in the number of suspected cases, which was only possible thanks to the "gemba meetings" the emergency department has introduced in 2014.
To respond to the increase, a multidisciplinary team was established in October 2015 to map out an action plan and prepare for what could (and then turned out to) be an epidemic. This was a multi-functional group, with professionals working across the organization: ER, Hospital Infection Control Service, Intensive Care Unit, Laboratory, Maintenance, Pharmacy, Quality and Continuous Improvement, and Administrative and Technical Managers. Sure enough, in February the number of dengue patients in the emergency room increased almost eightfold compared to December 2015 (in the same month, the percentage of patients visiting the hospital because of dengue grew to 53%).
When the peak of the outbreak occurred towards the end of February, lean was in place and the Hospital São Francisco was now prepared to deal with the crisis: without any major investment, but only by managing its resources in a leaner way, the organization has already managed to care for more dengue patients this year than it has in the 2011 outbreak.
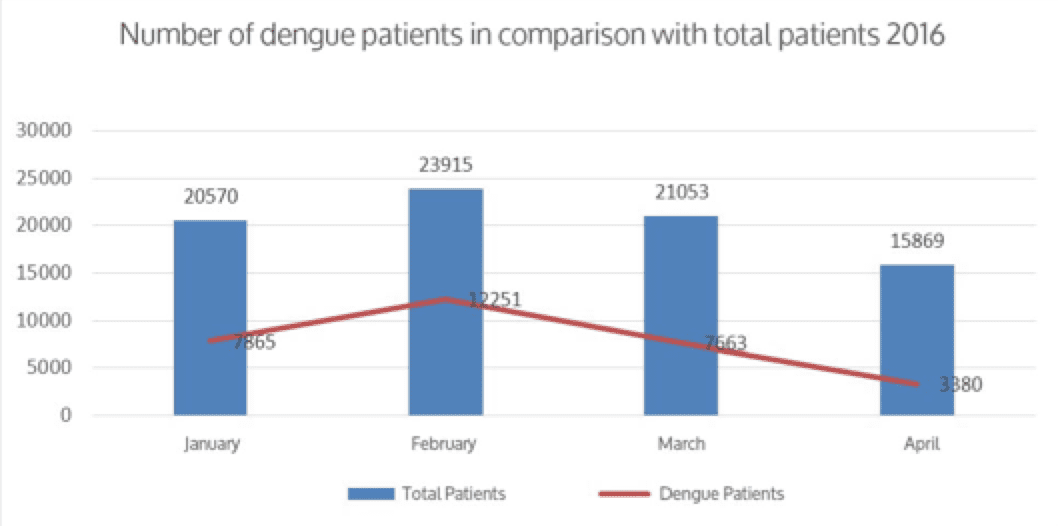
From a financial standpoint, the emergency unit did better during the epidemic than it did at dengue-free times: the average cost per patient was about 40% below the industry standard, while the number of complaints – a quality indicator HSF uses – remained within the standard.
In the months of January, February and March 2016, the standard cost of emergency care fell sharply thanks to lean thinking.
LOOKING AHEAD
Since the second dengue outbreak and thanks to the implementation of lean thinking, the hospital has become more flexible and adaptive, which is greatly helping at a critical time like this. Hospital staff is determined to become more and more effective in fighting dengue, in collaboration with the population it serves. Hopefully other hospitals in Brazil, and beyond, will join them on this mission.
Our sincere thanks to the São Francisco Hospital staff, especially Dr. Silvia Nunes Szente Fonseca, Elaine C. A. G. Bizerra, Maysa de Souza, Larissa H. J. Sigaki, Arthur Teixeira, and Roberto Chimionato for reviewing this article and for sharing the data provided herein.
This article is also available in Portuguese
THE AUTHORS
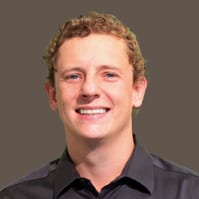
Flávio Battaglia is the Director of Lean Institut Brasil, having spent time with the organization since the year it was founded - 1999. Flávio is an advocate of and expert on lean healthcare.
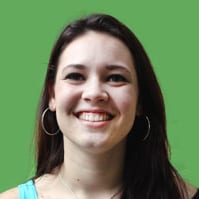
Tamiris Manzano is a translator and she supports Lean Institut Brasil in many of its editorial projects.
Read more
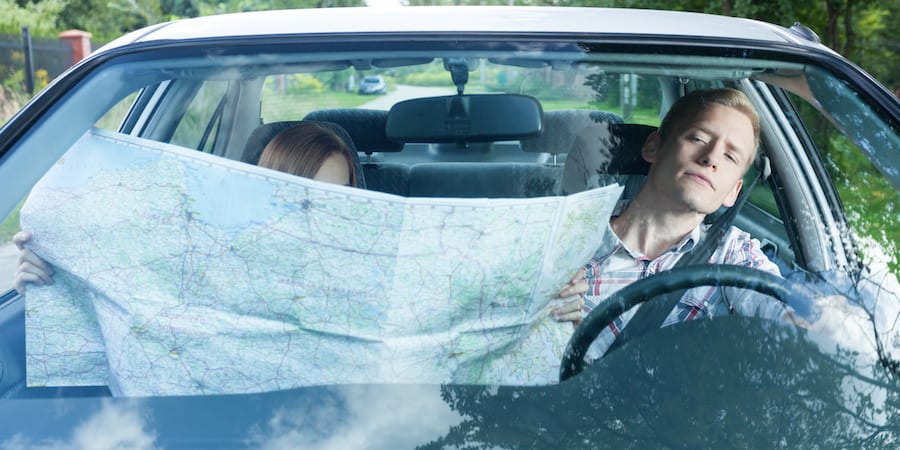
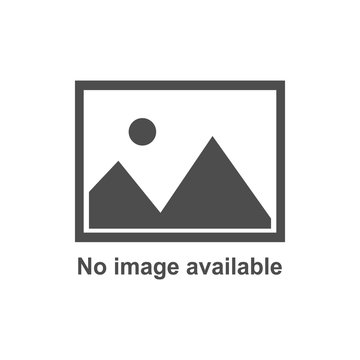
COLUMN – With many of us about to leave for our summer vacations, the importance of planning (a holiday just like a business venture) could not be clearer. But objectives and potential problems should be identified before setting off.
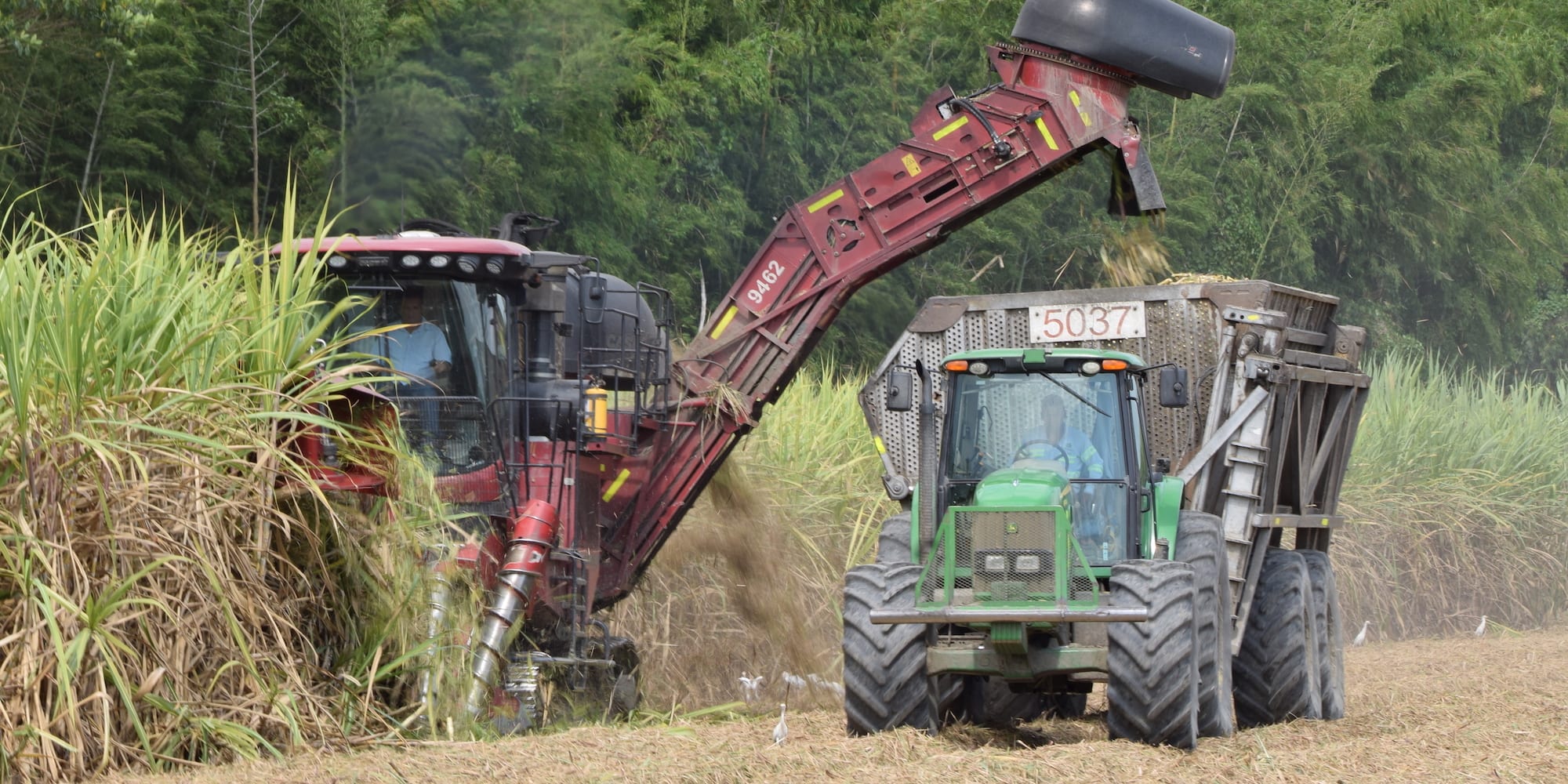
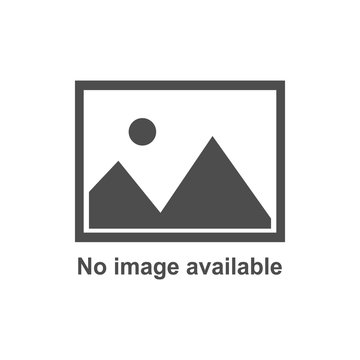
INTERVIEW – This agro-industrial business in Colombia is applying lean thinking to its harvesting process. The harvest manager explains the difficulties and opportunities encountered on the journey so far.
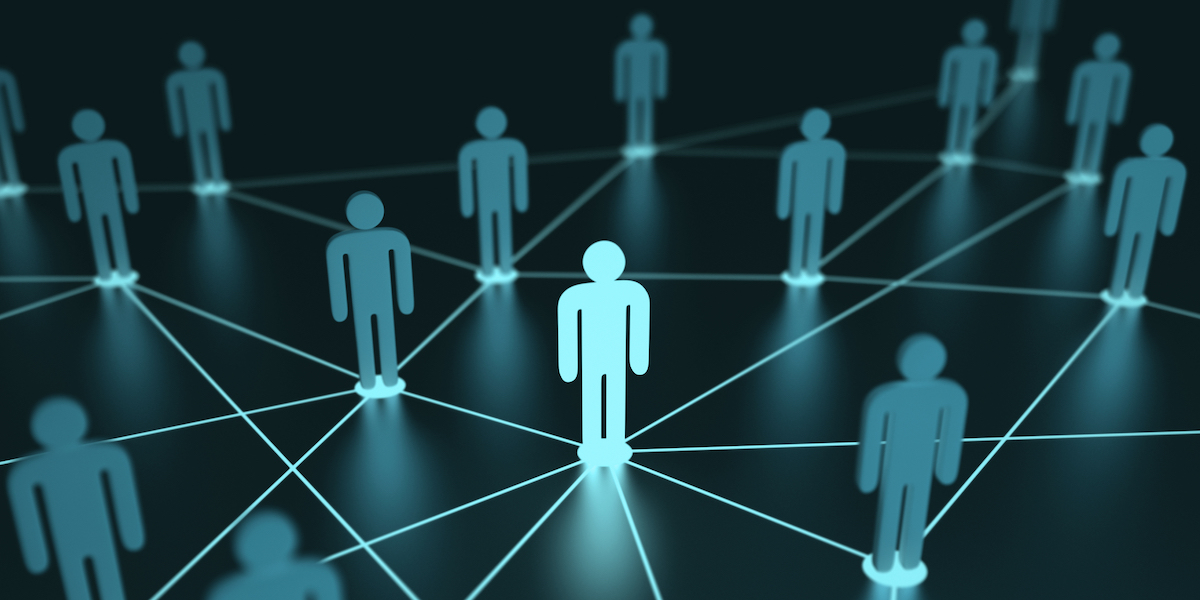
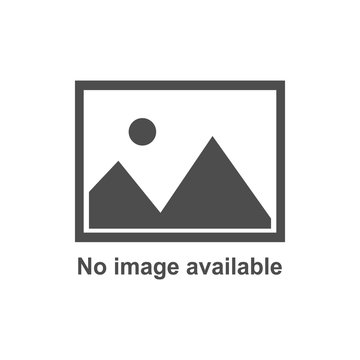
FEATURE – We tend to describe lean as a holistic approach to a transformation, but we won’t be able to truly embrace it until everyone starts to see the organization as a system.
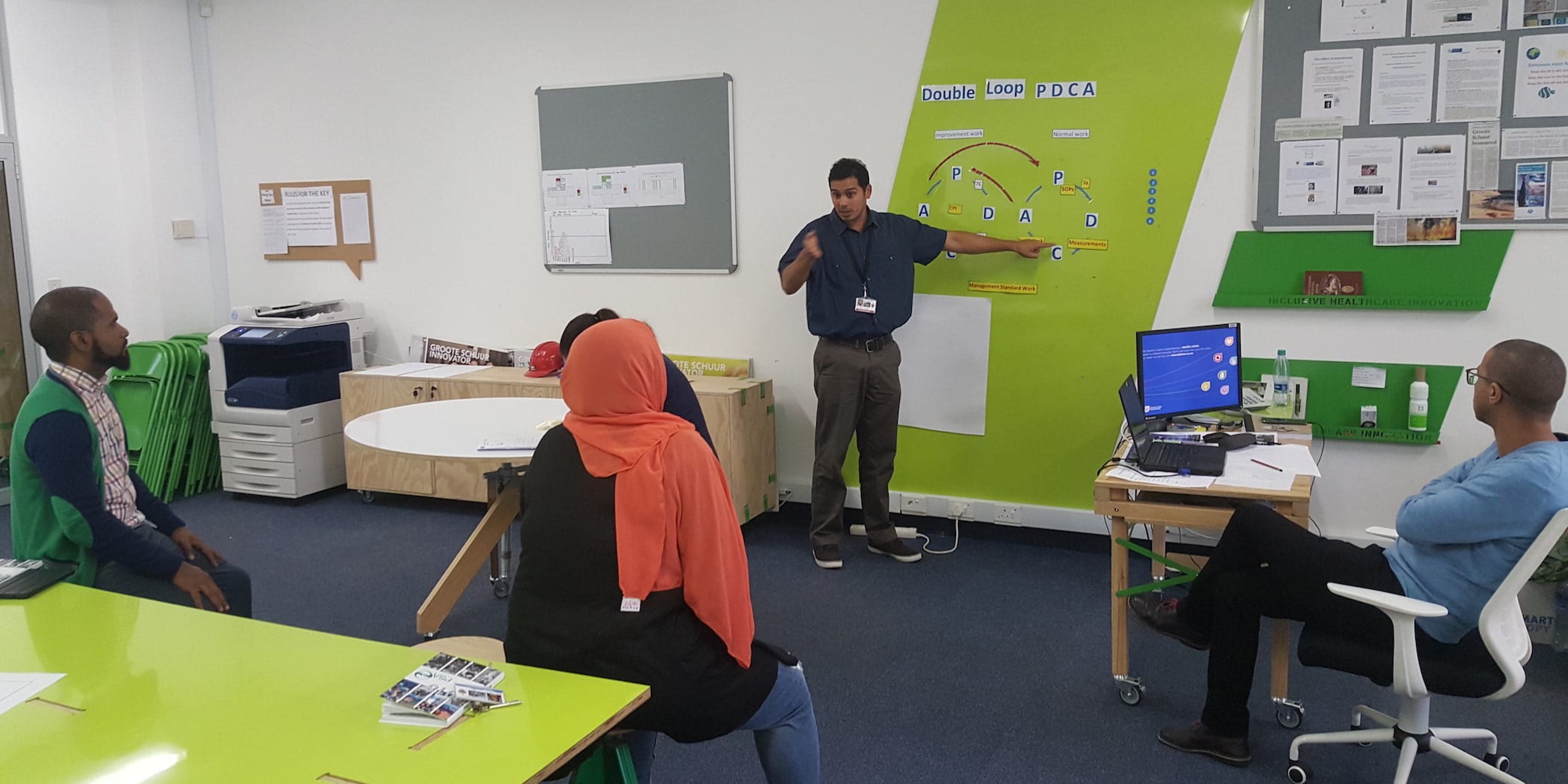
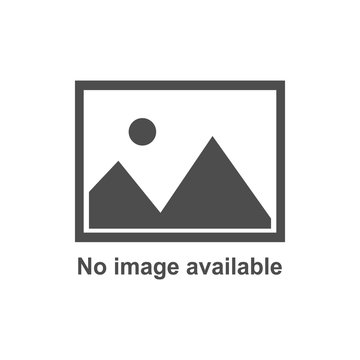
FEATURE – How “Double-Loop PDCA” was discovered due to a problem with implementing a lean daily management system in a South African hospital.