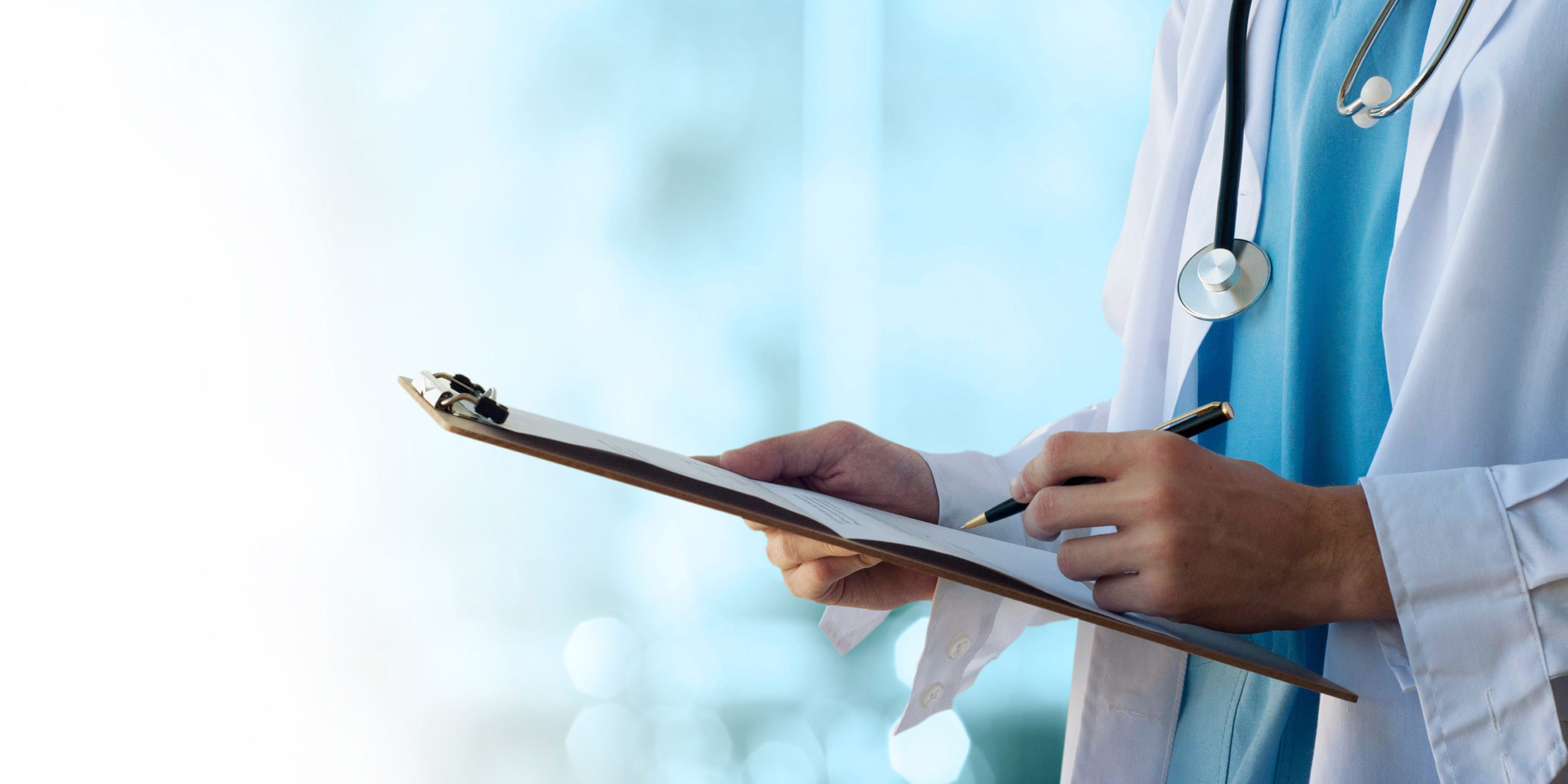
Taking the lean leap in private healthcare
INTERVIEW – A private healthcare group in South Africa has carefully studied the unique challenges it faces and customized its approach to improvement accordingly, embarking on a lean journey to better patient care.
Interviewee: Sharon Vasuthevan, Nursing and Quality Executive, Life Healthcare Group
Lean Institute Africa (LIA): What is Life Healthcare’s approach to quality improvement?
Sharon Vasuthevan: We marry the definition of quality improvement of the Health Foundation: “better patient experience and outcomes achieved through transforming provider behavior and organizations, through using a systemic change method and strategies”. We’ve learned that successful quality improvement combines change with a strategy. In other words, you need to carry out improvement (the change itself), but you also need a standard improvement method that relies on the appropriate tools and techniques (the strategy). We do this while taking into account the specific organizational context to achieve better outcomes.
LIA: How did you get started?
SV: From the outset, we understood that we needed to own the quality improvement process. So, in April 2016, we initiated a Proof of Concept (POC) project. The aim was to define the approach that would equip our staff with good methods and tools for seeking improvement opportunities and implementing these projects – aligning them with the company’s strategic pillars (our True North). To complete the POC we took on three pilot projects in a large and busy hospital to test various approaches, including A3 Thinking, Toyota Kata (a pilot of which is pictured below) and the Institute for Healthcare Improvement (IHI) Improvement Model. For all methods, we used the Plan-Do-Study-Act (PDSA) cycle to test improvement recommendations.
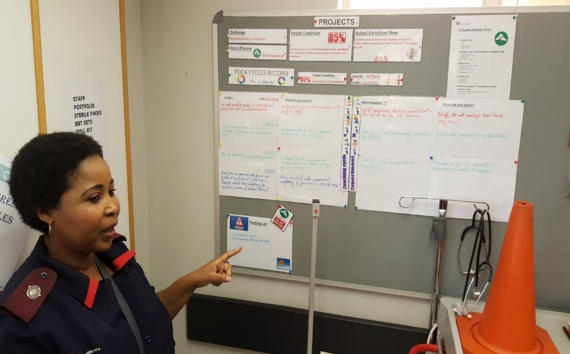
LIA: What came after you took your first steps into lean healthcare?
SV: We were pleased with the initial outcomes of the pilot, and out of this evolved our own scientific method of improvement. We named it iShift (its visual elements are pictured below). This approach includes a tailored adaptation of the three lean management tools: A3 Thinking, Toyota Kata and Healthcare Kaizen. It was important to tailor these so that they fit as best as possible with our unique work culture.
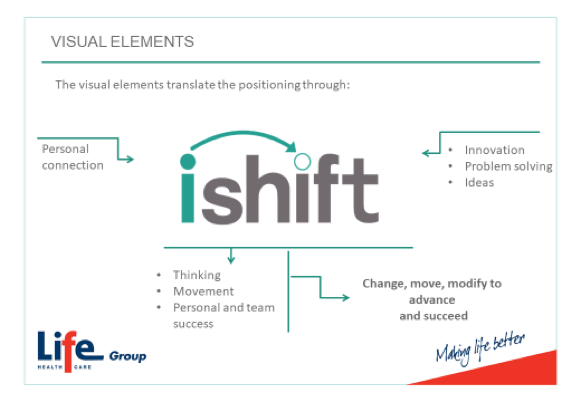
In July 2017, we broadened the scope of our iShift program to include a defined management system. This was based on a customized version of the Lean Transformation Framework. Our management system would fundamentally transform (or shift, if you will) our leadership’s thinking. It moved from a traditional project management approach to one that incorporates, and is based on, a holistic, continuous improvement approach. However, we took care to ensure that Life Healthcare’s unique and owned iShift Management System terminology was used. The purpose of this was to encourage a culture change without overtly referring to what may have been perceived as an external approach (lean management). We felt this would be important in engaging our staff in a meaningful way and garnering their support for this new way of working.
Shifting to a lean approach to improvement and project work was a bold step for us. We’ve entered a new and exciting culture of inclusion – where the ideas and improvements come from the staff doing the actual work, enabling system-wide change.
LIA: You’re now a few years into your transformation. Can you tell us where Life Healthcare is in their lean transformation journey, and how you’ve continued on your path? How do you sustain your improvements?
We focused on developing our own training content to ensure it’s suitable to our specific target audience. We trained front-line staff in the iShift method, focusing on small improvements and standard work (which includes work procedures, tools and templates), as well as a standard visual display.
From there, supported by the Lean Institute Africa, we have trained National, Regional and Hospital management teams in A3 problem solving, project planning, implementation and coaching methods. We have developed our own facilitator who can upskill Life Healthcare’s staff internally. This has helped us to structure well-focused projects in a way that fosters learning and helps us to sustain results. David Mann, a respected author who has written about how to effectively create a Lean Culture in an organization, believes that an effective lean culture is dependent on the following elements in a Daily Management System: leader standard work, visual management, and daily accountability.
To sustain our staff’s good work and continuous improvement, we have therefore developed the following iShift Daily Management System. It includes Mann’s three elements:
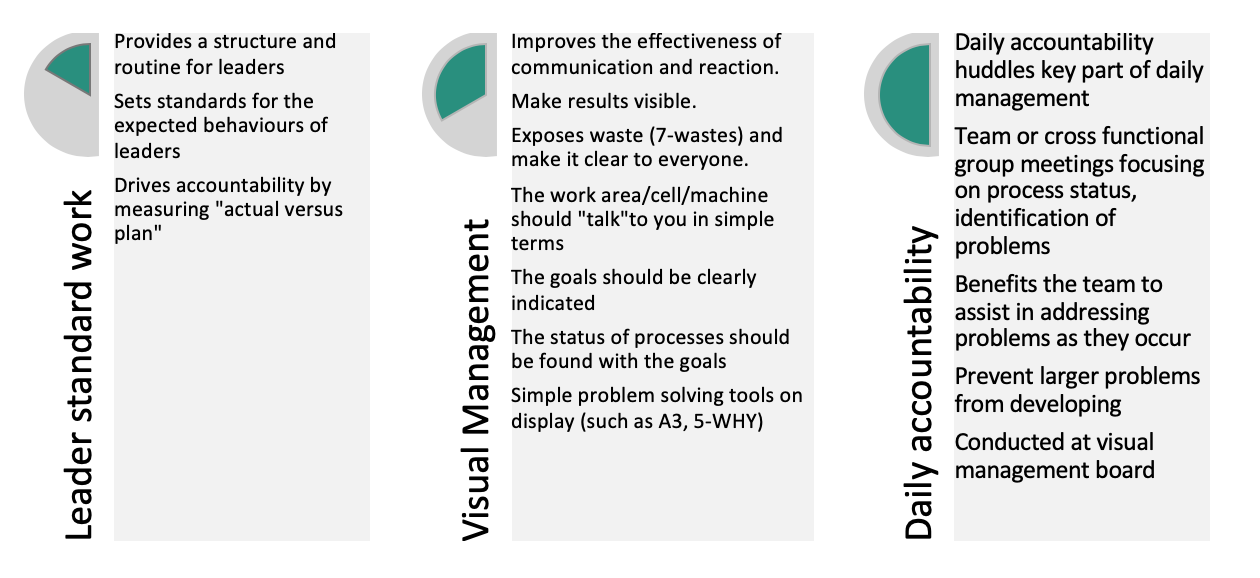
Leader standard work is critical to ensuring that our lean culture prospers. This change demonstrates to employees how their leaders allocate their time every day. It also shifts managers’ focus from being seen as, and being, the primary problem-solvers to empowering all Life Healthcare employees to solve their own problems.
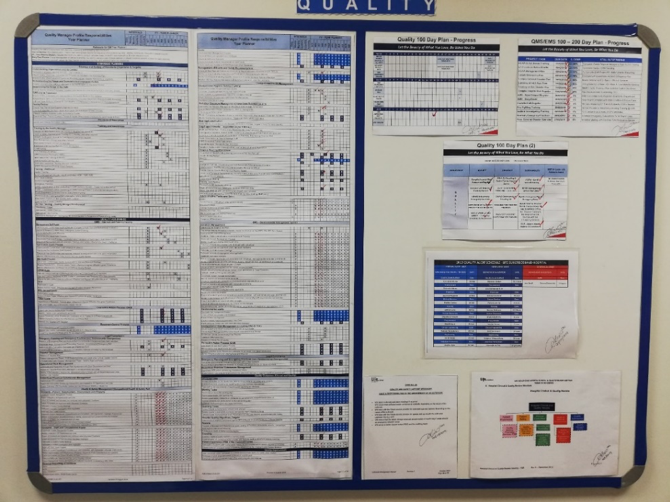
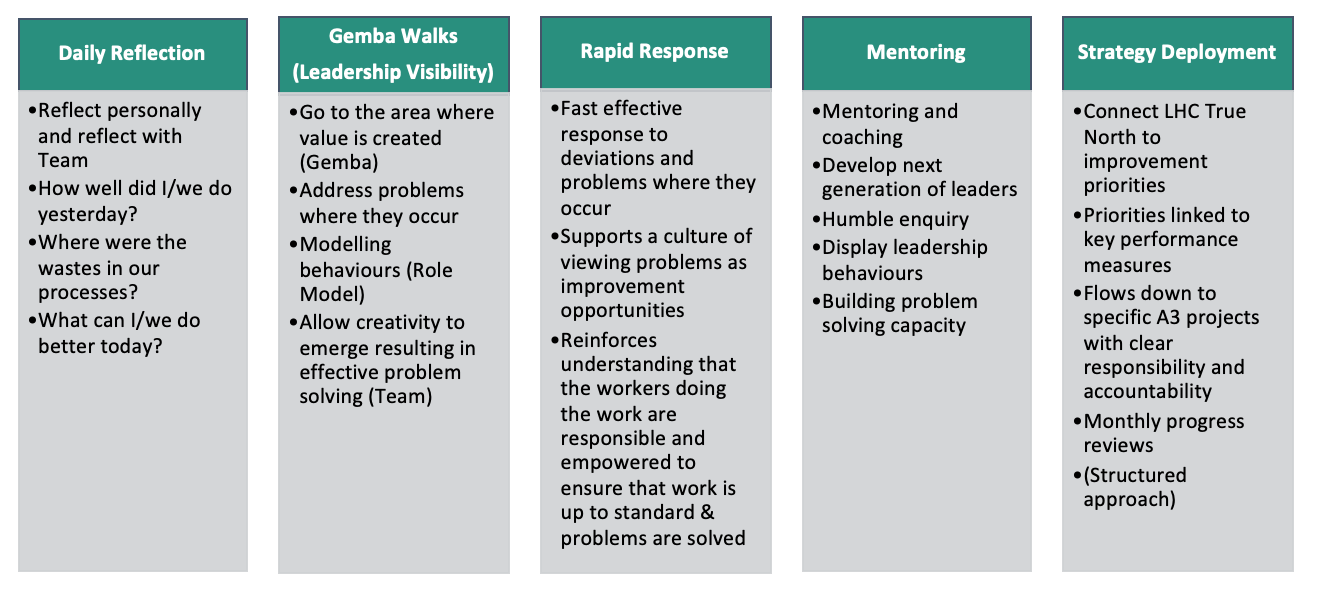
The next success factor in our Lean Management System is Visual Management. The key benefit of the visual display of performance is that it drives actionable improvements. It makes it easy to see problems and quickly implement countermeasures. Visual management boards show key unit-level process indicators that align with system-wide strategic goals, such as improving care quality and patient safety, as well as lowering the cost of care.
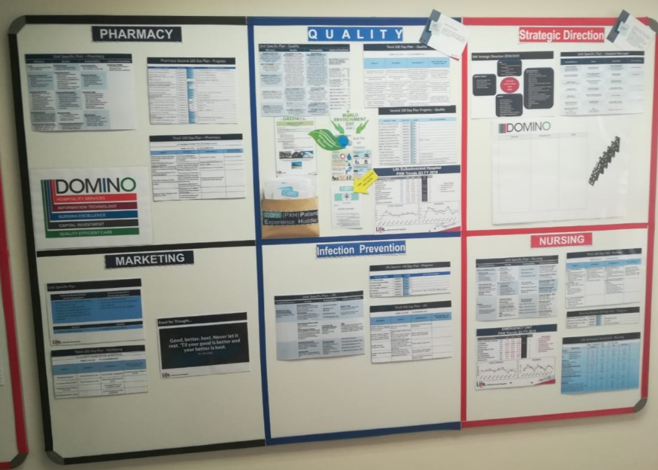
Daily accountability ensures that the focus remains on improving performance, which is shown on the visual management boards in each department. The structure of the daily accountability process is straightforward — a series of four brief meetings to review what happened the previous day and assign actions for improvement, where required. These are fast-paced, stand-up meetings/huddles at the gemba. The format emphasizes quickly resolving or investigating problems with the process. Daily tiered huddles at every level of the organization are an integral element of our daily management system. Their objective is to create alignment across the organization to ultimately achieve our True North. Both result-KPIs and process-KPIs are monitored daily. The result-KPI of an organization tier might be the process-KPI of another tier. Thus, the alignment between organizational levels is maintained in achieving the common Life Healthcare purpose.
- Tier 1: Start of the working shift, led by the team/shift-leader. The idea is to focus on abnormalities experienced during the previous shift, and any expected challenges for the shift ahead. That’s an opportunity to do better.
- Tier 2: Led by department supervisor/unit manager with the team. Night Quality Supervisor with the shift leaders and team members in the nursing units.
- Tier 3: Led by the function manager or Head of Department with supervisors and support group representatives or staff members. The goal is to identify and visualize gaps in the system, drive team problem-solving, and improve the overall organizational processes.
- Tier 4: Led by each Hospital Manager with the relevant Department Managers. Focused on “run-the-business” as well as “improve-the-business” activities.
LIA: How have Life Healthcare’s patients benefitted from iShift? What about the organization?
VS: Although we still have a long way to go in our lean journey, significant improvement is already evident in better efficiencies and cost savings. Leadership commitment to process improvement is evident in executive participation in rapid improvement exercises, and the integration of iShift tools and techniques into strategic, as well as operational projects. There have been improvements in patient experience, the cost of care and, most importantly, in clinical outcomes.
THE INTERVIEWEE
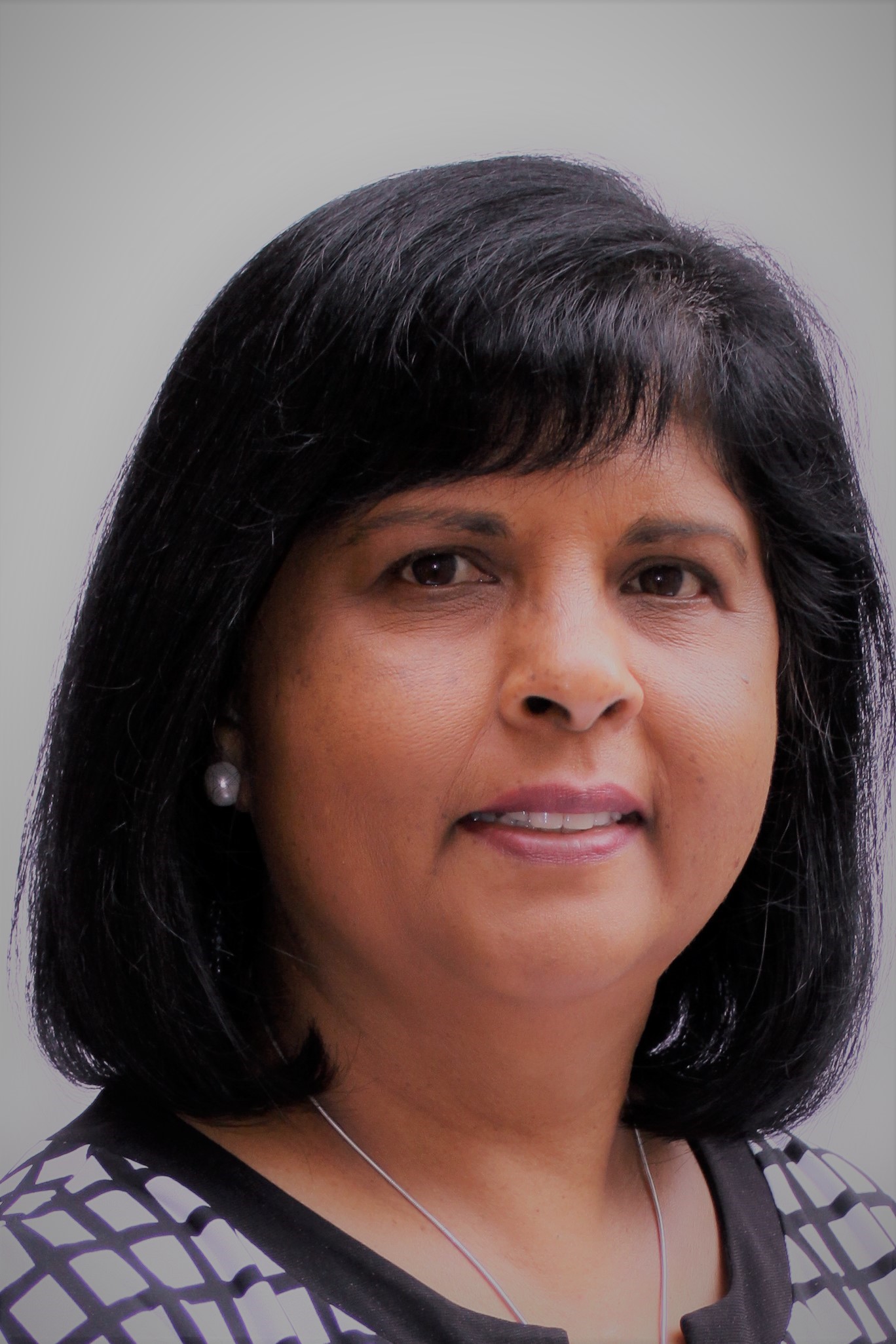
Read more
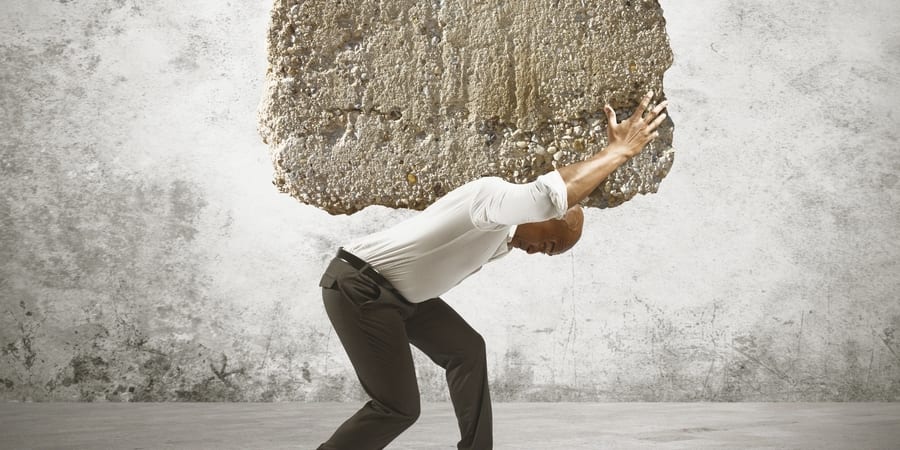
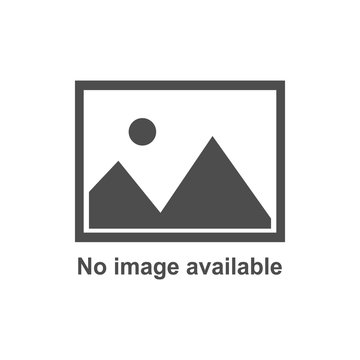
FEATURE - Stressed and overwhelmed by workload? Once again, lean thinking comes to the rescue, offering us a way to approach our work that helps us eliminate waste, save time, and avert breakdowns.
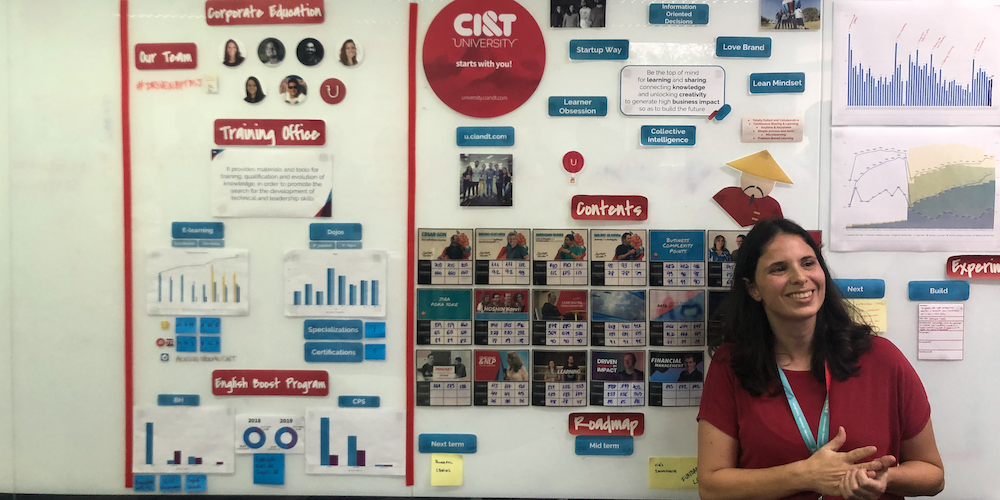
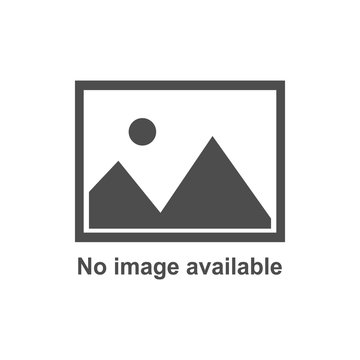
FEATURE – Last month, the Lean Global Network met in Brazil for its annual meeting. As part of it, we visited several amazing gembas. Three of our lean coaches reflect on what we learned.
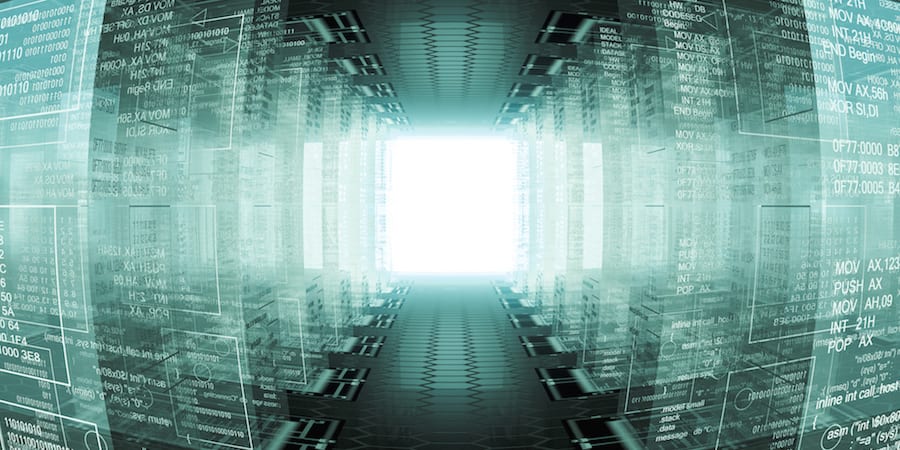
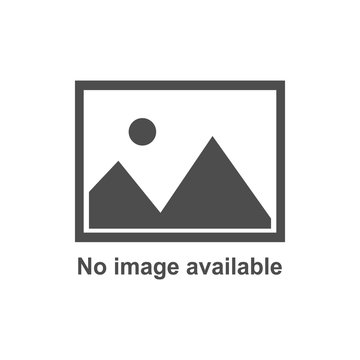
FEATURE – The goal of your digital transformation is not only to develop new technologies and innovative processes, but to turn your people into the kind of "smart creatives" who will lead your firm into the future. Lean will get you there.
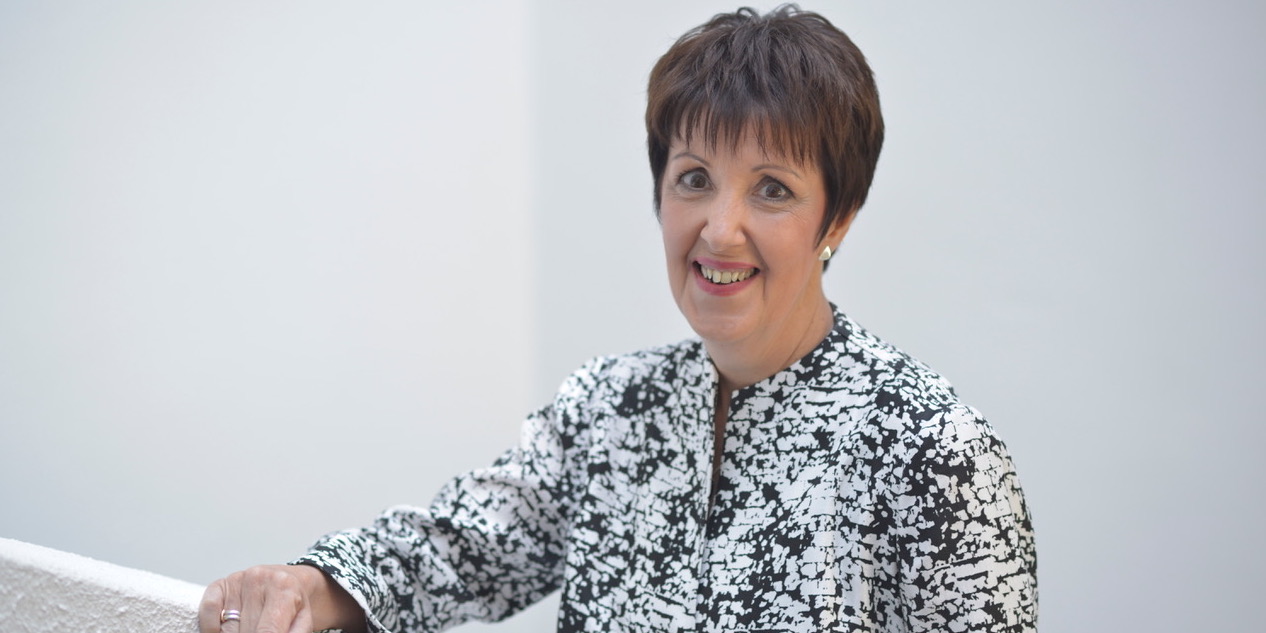
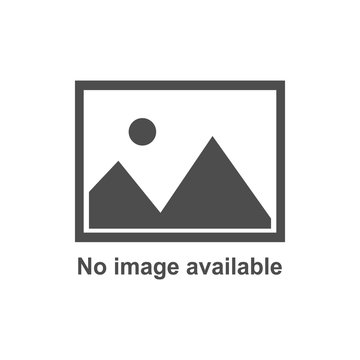
INTERVIEW – Rose Keanly discusses the role of lean in a strategic business transformation in the financial services sector and the dos and don’ts of bringing lean to a large organization.